自动铣削机动力装置设计论文本科论文.docx
《自动铣削机动力装置设计论文本科论文.docx》由会员分享,可在线阅读,更多相关《自动铣削机动力装置设计论文本科论文.docx(28页珍藏版)》请在冰豆网上搜索。
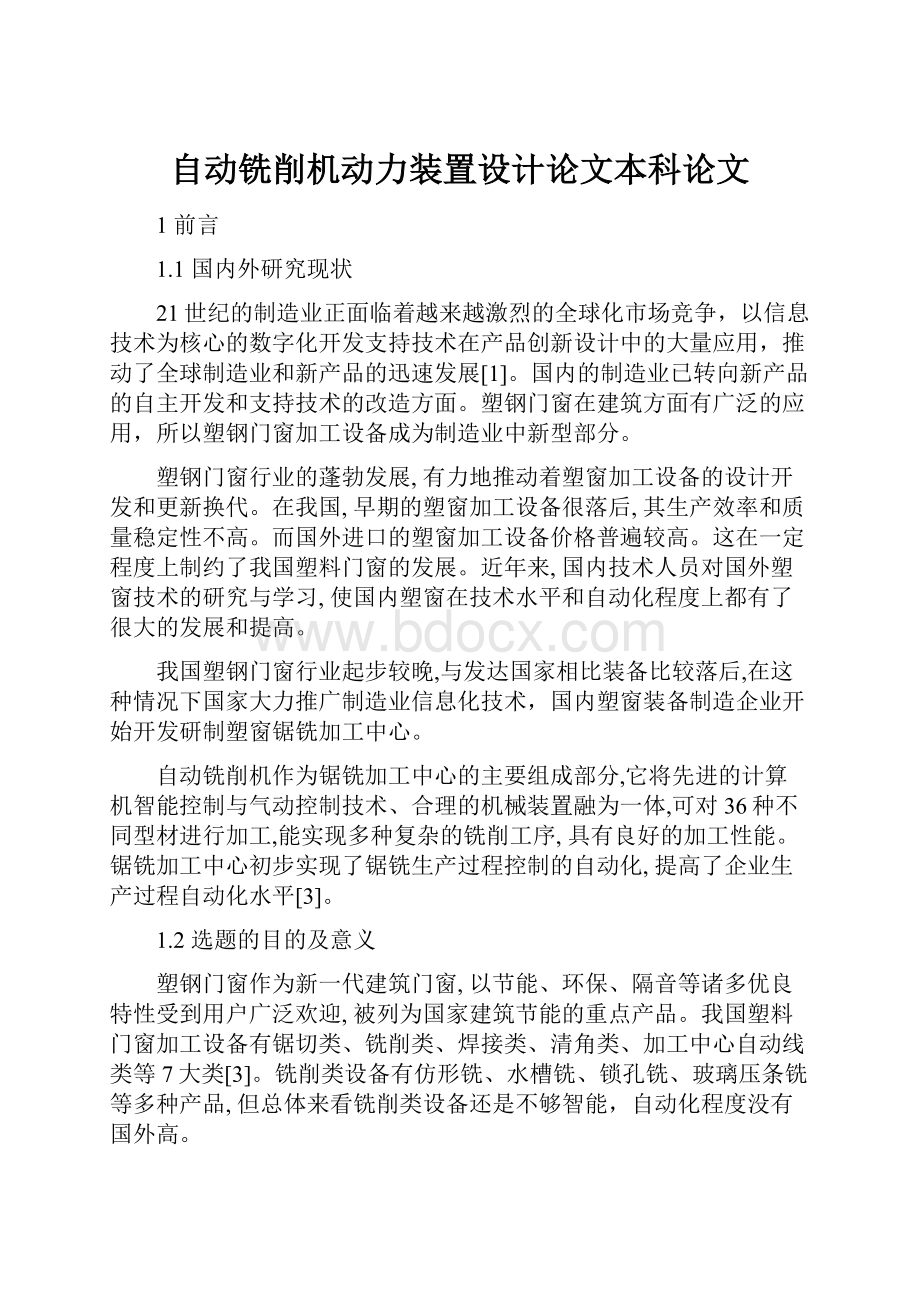
自动铣削机动力装置设计论文本科论文
1前言
1.1国内外研究现状
21世纪的制造业正面临着越来越激烈的全球化市场竞争,以信息技术为核心的数字化开发支持技术在产品创新设计中的大量应用,推动了全球制造业和新产品的迅速发展[1]。
国内的制造业已转向新产品的自主开发和支持技术的改造方面。
塑钢门窗在建筑方面有广泛的应用,所以塑钢门窗加工设备成为制造业中新型部分。
塑钢门窗行业的蓬勃发展,有力地推动着塑窗加工设备的设计开发和更新换代。
在我国,早期的塑窗加工设备很落后,其生产效率和质量稳定性不高。
而国外进口的塑窗加工设备价格普遍较高。
这在一定程度上制约了我国塑料门窗的发展。
近年来,国内技术人员对国外塑窗技术的研究与学习,使国内塑窗在技术水平和自动化程度上都有了很大的发展和提高。
我国塑钢门窗行业起步较晚,与发达国家相比装备比较落后,在这种情况下国家大力推广制造业信息化技术,国内塑窗装备制造企业开始开发研制塑窗锯铣加工中心。
自动铣削机作为锯铣加工中心的主要组成部分,它将先进的计算机智能控制与气动控制技术、合理的机械装置融为一体,可对36种不同型材进行加工,能实现多种复杂的铣削工序,具有良好的加工性能。
锯铣加工中心初步实现了锯铣生产过程控制的自动化,提高了企业生产过程自动化水平[3]。
1.2选题的目的及意义
塑钢门窗作为新一代建筑门窗,以节能、环保、隔音等诸多优良特性受到用户广泛欢迎,被列为国家建筑节能的重点产品。
我国塑料门窗加工设备有锯切类、铣削类、焊接类、清角类、加工中心自动线类等7大类[3]。
铣削类设备有仿形铣、水槽铣、锁孔铣、玻璃压条铣等多种产品,但总体来看铣削类设备还是不够智能,自动化程度没有国外高。
自动铣削机动力装置设计在设计方面需要采用跨越式思维模式,需要创新,从中可以巩固和加强大学里所学的知识,同时提高自己的创新能力和运用知识的能力,为以后工作打下良好的基础。
2设计内容和方案
2.1设计内容
塑窗自动铣削机作为锯铣加工中心主要单元,将信息技术、自动化技术、气动控制技术等与制造技术相结合,可自动高速加工36种不同型材,并将多种复杂的铣削工序集中在一台设备上自动实现,具有良好的柔性加工性能[3]。
本次以自动铣削机动力装置设计为毕业设计主要内容,要求实现多种型材的排水孔、通风孔、铰链孔、门窗锁孔、滑轮孔以及其他各种五金件安装孔、槽的加工,其孔、槽既可为规则形状亦可为异形。
锯铣加工中心由电脑控制台、自动输料台、送料机械手、自动铣削机、自动锯切机、锯后输送和收尘等几大部分组成。
图2.1为加工中心各组成单元配置图。
图2.1加工中心各组成单元配置
1—送料机械手2—主控柜3—自动铣削机4—废料输送5—收尘设备
6—锯后输送7—自动锯切机8—电脑控制台9—自动送料台
自动铣削机的重要部分是动力装置,设计要求满足一下参数:
(1)自动铣床能够实现25×25~120×120截面铝塑型材的规则及异型孔槽的铣削;
(2)铣刀直径为
(3)可以铣削铝合金及塑料门窗型材;
(4)要求设计方案合理,结构紧凑、工作可靠、质量达到行业标准。
2.2设计方案
2.2.1自动铣削机装置
自动铣削装置,见图由2.2两个伺服电动机驱动,通过滚珠丝杠控制其上下和左右运动,调整刀具相对于型材的位置。
刀具则在进给驱动气缸的作用下,快进后进行切削。
这一设计得到很高的精度和生产效率。
图2.2自动铣削装置
1-铣削装置支架2—铣刀头3—气缸4—电动机5—滚珠丝杠
6—上下移动伺服电动机
此自动铣削装置安装14把刀具可实现在型材截面内多方向的进给。
切削加工采用两种方式进行,通过气缸直接进给或配合送料机械手进行小孔及排水槽等的加工,另一方式则为送料机械手与铣削装置支架带动刀具的伺服进给实现较大孔或异形孔、槽的加工。
这种结构设计方式具有明显的柔性加工性能及其他一些优点,具体表现在:
(1)在型材同一截面内可进行多方向的孔、槽加工,满足用户多方面需要;
(2)自动铣削装置的两个伺服轴配合送料机械手的纵向伺服进给,可实现各种规则及异形孔、槽的加工;
(3)滚珠丝杠及工作头进给气缸较大的行程范围配合送料机械手的自动识别系统,可加工36种不同规格的型材;
(4)具有较高的加工精度和加工效率。
因刀具位置或轨迹由伺服系统控制,且根据需要,某几把刀可同时加工;
(5)进给采用带磁性开关的气缸进行控制,不污染环境,成本较低[3]。
2.2.2气动控制
设计时考虑塑钢门窗应在清洁的环境中生产,而气动控制相对液压控制有不污染环境、成本较低等许多优点,且切削PVC塑料切削力较小,故夹紧和切削进给均采用了气动控制,其原理图见图2.3。
图2.3刀具进给及夹紧机构气动控制系统
1、2—液压阀3—刀具进给气缸4—调速接头5—垂直夹紧上气缸
6—垂直夹紧气缸7—水平夹紧气缸
气动系统主要由气源处理器、电磁阀、压力继电器、气缸及各种气路接头等组成,气缸速度全部由调速接头4调整,可调整行程。
当型材固定好以后,由气缸带着刀具进给以及铣削。
2.3最优方案确定
2.3.1电机
电机都采用交流伺服电机,交流伺服电机有以下特点:
(a)、自动调整
(b)、高速高响应
(c)、低振动
(d)、当信号电压为零时无自转现象,位置精度非常准确
2.3.2进给传动系统
进给传动系统选择滚珠丝杠,因为滚珠丝杠有以下特点:
(a)传动效率高。
滚珠丝杠副的传动效率很高,可达92%~98%,是普通丝杠的2~4倍。
(b)摩擦力小。
因为动、静摩擦系数相差小,因而传动灵敏,运动平稳、低速不容易产生爬行,随动精度和定位精度高。
(c)使用寿命长。
滚珠丝杠采用优质合金制造,表面粗糙度小,其滚道表面淬火硬度可达60HRC~62HRC。
另外,因为是滚动摩擦,磨损更小。
(d)经预紧后可以消除轴向间隙,提高了系统的刚度。
(e)反向运动时无空行程,可以提高轴向运动精度。
(f)不能自锁,有可逆性。
2.3.3动力装置
动力装置采用气动,气动有以下特点:
(a)、气动装置结构简单、轻便、安装维护简单。
压力等级低、故使用安全。
(b)、工作介质是取之不尽的空气、空气本身不花钱。
排气处理简单,不污染环境,成本低。
3主要结构设计
3.1主传动系统设计
机床的主传动系统是用来实现机床主运动的,它应具有一定的转速和一定的变速范围,以便采用不同材料的刀具,加工不同材料、不同尺寸、不同要求的工件,并能方便地进行开、停、变速、换向和制动等。
3.1.1选铣刀
根据设计要求,实现多种型材的排水孔、通风孔、铰链孔、门窗锁孔、滑轮孔以及其他各种五金件安装孔、槽的加工,其孔、槽既可为规则形状亦可为异形,从要求我们可以知道主要是铣削沟槽与工件上各种形状的孔,能满足要求的铣刀是立铣刀。
由于本课题中铝塑型材锯铣加工中心的切削材料主要是铝塑型材,对加工刀具的要求不高,可以用高速钢,所选铣刀如图3.1。
图3.1直柄立铣刀
名称
基本尺寸d1(mm)
基本尺寸d2(mm)
基准型L1(mm)
长型L1(mm)
基准型L2(mm)
长型L2(mm)
齿数
高速钢直柄立铣刀
5
5
6
47
55
58
63
13
24
4
6
6
6
57
57
68
68
13
24
4
7
8
10
60
57
74
68
16
30
4
8
8
10
63
66
82
80
19
38
4
表3.1所选铣刀的参数
高速钢直柄立铣刀的螺旋角30°~40°,主前角20°,主后角20°~25°,副后角8°。
(a)铣削速度
在该刀具材料下铣削硬度比较低的材料一般的铣削速度为:
15~35(m/min),因为我们要达到一个比较高的加工表面的粗糙度,所以我们选择比较高的的一个速度,暂定为35(m/min)。
(b)进给量f
(3.1)
:
铣刀每分钟进给量(毫米/分);
z:
铣刀齿数;一般fz的范围是:
0.05~0.15(mm/z)。
所以进给量f的范围是:
0.2~0.6(mm/z)。
(c)铣削深度
半精加工铣削深度ap的范围是:
0.5~2(mm),对于硬度比较低的铝合金材料铣削深度ap的范围可以取为:
0.5~4(mm)。
3.1.2选电机
(a)高速钢直柄立铣刀铣削铝合金的计算
(3.2)
表3.2各种铣刀加工不同材料的CF值
铣刀
名称
切削系数Cf值
钢料
可锻铸铁
青铜
灰铸铁
铝镁合金
端铣刀
808
490
368
490
177
立铣刀
669
294
222
294
167
三面刃铣刀
670
294
221
294
167
表3.3高速钢铣刀切削力修正系数kF值
前角γ0
5ο
10ο
15ο
20ο
kF
1.08
1.0
0.92
0.85
表3.3铣削时各分力与圆周力的比值
铣削条件
比值
不对称铣
立铣
ae=0.05d0(mm)
af=0.1~0.2(mm/z)
逆铣
顺铣
FH/FZ
FV/FZ
Fa/FZ
1.0~1.2
0.2~0.3
0.35~0.4
0.8~0.9
0.75~0.8
0.35~0.4
由以上表我们可以知道CF=167,kF=0.85,因为d0=5~8,所以我们取d0=8,那么ae=0.05d0=0.4,af=fz=0.2,Z=4,ap=4,将以上各值代入式3.2中,我们可得最大铣削力为:
(N)
(b)计算电机功率
(3.3)
我们已经知道FZ=54.2,V是最大切削速度为35,弹性联轴器η=0.99~0.995,我们选η=0.99,将以上代入式3.3中,可得:
(c)计算电机转速
(3.4)
当V=35,d0=5时,n取最大值,把V、d0代入式3.4中,可得:
(r/min)
(d)电机选型
知道电机功率不小于1.9KW,转速不小于2229r/min。
我们可以选电机为:
表3.4GSH电机性能参数
型号规格
额定电压(v)
额定功率(KW)
基准频率(Hz)
同步转速(r/min)
最高转速(r/min)
额定电流(A)
额定转矩(N.m)
GSH-2.2-06A42
220/380
2.2
100
6000
9000
10.45/
6.05
3.502
所选电机的尺寸如下图3.2:
表3.5电机尺寸
型号
A
B
C
GSHA42
375
65
225
图3.2GSH-2.2-06A42的尺寸图
3.1.3联轴器的选型
由于转速比较高,尺寸比较小,我就选择了胀紧套联接单向膜片联轴器,此联轴器的特点是:
(a)结构简单;
(b)传递力矩大;
(c)吸收振动;
(d)拆装方便;
(e)使用寿命长;
(f)可补偿轴的角度偏差、偏心、轴向窜动。
表3.6胀紧套联接单向膜片联轴器
型号
d(mm)
D(mm)
L(mm)
A(mm)
B(mm)
DMA02
10-32
82
95
6.6
26
图3.3胀紧套联接单向膜片联轴器
3.1.4胀紧套的选择
根据要求以及联轴器的型号,我们选用Z1型胀紧连接套:
表3.7Z1型胀紧连接套
d×D(mm)
L(mm)
l(mm)
25×30
6.3
5.3
图3.4Z1型胀紧连接套尺寸图
3.1.5弹簧夹头的选择
根据铣刀选择的弹簧夹头为ER卡簧。
表3.8ER卡簧
型号
D(mm)
L(mm)
d(mm)
ER32
32
40
3~20
图3.5ER卡簧
3.1.6主轴的设计
主轴的设计取决于安装的刀具,安装铣刀需要用弹簧夹头,所以主轴前端设计成空心的,用来安装弹簧夹头,后端与联轴器联接,设计尺寸如图3.6。
图3.6主轴
3.2进给传动系统设计
进给传动系统我选择伺服电机带动滚珠丝杠,其特点:
1.摩擦损失小,传动效率;2.运动平稳,灵敏度高,低速时无爬行;3.轴向刚度高,反向定位精度高;4.磨损小,寿命长,维护简单;5.同步性好;6.有专业的厂家生产。
对于滚珠丝杠的安装我们选用了一端固定一段自由安装的形式。
图3.7滚珠丝杠安装示意
3.2.1电机的选型
对带动丝杠上下移动的电机要求不高,因为它只管带着刀架上下移动,切削时不用移动,这样的电机功率可以小,转速可以小,然而带着丝杠水平移动的电机,切削时也要配合移动。
所以电机按水平电机选择。
我们先假设电机的额定功率为2KW、额定转速为1000r/min,丝杠的螺距是6mm,那么丝杠的进给速度V1=1000×6=6m/min,丝杠主轴受力有以下公式:
(3.5)
(3.6)
(3.7)
根据式3.6
=9550×
=19100(N·mm)
根据式3.7Fx=Fz÷4=54.2÷4=13.55
式3.5中f=0.15、dz=35把以上数据代入式3.5中,可得:
丝杠功率P1=Fm×V1=177.26×6=1.06(KW)
弹性联轴器的效率η=0.99~0.995,角接触球轴承的效率η=0.99,用两个角接触球轴承,所以电机最大功率:
=1.09
因为P2=1.09<2,所以电机的额定功率为2KW,额定转速为1000r/min是符合的。
表3.9电机性能参数
型号
相数及线电压(V)
额定功率(KW)
额定转速(RPM)
最高转速(RPM)
额定转矩(N·m)
最大转矩(N·m)
额定电流(A)
转子惯量(Kg·cm2)
电机长度L(mm)
130L2M19N
3-220
2.0
1000
1300
19
57
9.3
44
313
图3.8电机尺寸图
3.2.2联轴器的选择
这也选胀紧套联接单向膜片联轴器如图3.3,所选型号如下表3.10:
表3.10胀紧套联接单向膜片联轴器
型号
d(mm)
D(mm)
L(mm)
A(mm)
B(mm)
DMA01
10-22
68
90
6.1
26
3.2.3丝杠轴的设计
初步确定轴的最小尺寸,选取轴的材料为45钢,调质处理,根据下列公式:
dmin=A0
(3.8)
取A0为120,P1=1.06,n=1000代入式3.8中则:
dmin=120×
=12(mm)
以下图3.9是我设计的丝杠轴,最小直径是22mm,符合要求,前端与胀紧套联接单向膜片联轴器联接,中间有螺纹的安装一个小圆螺母为了固定轴承,后端安装轴承。
丝杠直径为35mm,丝杠长度设计成400mm。
图3.9丝杠轴
3.2.4胀紧套的选择
配合联轴器选择Z1型胀紧连接套如图3.4:
表3.11Z1型胀紧连接套
d×D(mm)
L(mm)
l(mm)
22×26
6.3
5.3
3.2.5轴承的选择
由于在此处主要受轴向力,角接触球轴承能承受一定的径向力和较大的轴向力,所以我们选择了角接触球轴承,在这受两个方向的轴向力所以要成对使用角接触球轴承(小端面对小端面)。
4主要零件选择
4.1丝杠的选择
此课题选的是滚珠丝杠,型号是W3506:
表4.1滚珠丝杠单位:
mm
型号
直径D0
螺距l
D1
D2
D3
D4
T
L
额定动载荷(N)
额定静载荷(N)
W3506
35
6
55
65
96
82
12
60
2500
11600
图4.1滚珠丝杠
4.2气缸的选择
4.2.1控制铣刀的气缸的选择
选择气缸好坏直接决定切削的质量,所以必须严格选择气缸,气缸的输出力、缸径和使用压力的关系有
F1=η×A1×P(4.1)
式中F1—气缸的输出力,(N);
η—负载率;
A1—受压面积,(mm2);
P—使用压力,(MPa)。
根据查表可知,运动工况时η<0.5,P在0.15~1之间,假设先选个缸径为40mm的,它的受压面积是1260mm2,取η=0.3,P=0.15,A1=1260代入式4.1可得
F1=0.3×1260×0.15=56.7>54.2,所以此气缸合理可用。
表4.2气缸
型号
缸径(mm)
行程(mm)
MBB40-200
40
200
4.2.2平衡气缸的选择
同理取η=0.3,P=0.15,选个缸径为100mm的,它的受压面积是7850mm2,取η=0.3,P=0.8,A1=7850代入4.1可得F1=0.4×7850×0.8=2512>2000(通过估算竖直丝杠所受最大轴向载荷),所以此气缸合理可用。
表4.3气缸
型号
缸径(mm)
行程(mm)
MBB100-400
100
400
4.3导轨以及导轨滑块的选择
4.3.1导轨的选择
这里我们选线性导轨,它的结构简单、安装方便。
线性导轨又称滑轨、线性滑轨,用于直线往复运动场合,拥有比直线轴承更高的额定负载,同时可以承担一定的扭矩,可在高负载的情况下实现高精度的直线运动。
图4.2线性滑轨
表4.4线性导轨单位:
mm
型号
H1
D×h×d
E
P
W1
H2
MSA25LS
22
11×9×7
20
60
23
6.5
MSA20LS
18
9.5×8.5×6
20
60
20
5
MSA15S
15
7.5×5.3×4.5
20
60
15
4.2
4.3.2导轨滑块的选择
导轨滑块与导轨是配合的,导轨确定了导轨滑块也就确定了,如图4.1:
表4.5导轨滑块单位:
mm
型号
H
d1
T
B
C
W
K
W2
L
L1
N
G
S×l
MSA25LS
40
3.3
10
35
50
48
5.8
12.5
100.6
78
10
12
M6×8
MSA20LS
30
3.3
8
32
50
44
5.8
12
88.8
67.2
5
12
M5×6
MSA15S
28
3.3
7.2
26
26
34
3.2
9.5
56.3
39.3
8.3
7
M4×5
5主要零件的校核
5.1丝杠的校核
所选滚珠丝杠的型号是W3506,它的额定动载荷是2500N,额定静载荷是11600N。
5.1.1计算最大动载荷C
选用滚珠丝杠副的直径D0时,必须保证在一定轴向负载作用下,丝杠在回转100万转后,在它的滚道上不产生点蚀现象。
这个轴向负载的最大值即称为该滚珠丝杠能承受的最大动负载C,可用下式计算:
(5.1)
式中L—寿命,以106转为一单位,L=
(5.2)
n—丝杠转速,(r/min)
T—为使用寿命,(h)对于数控机床取T=15000h;
fw—运转系数,见表5.1。
表5.1运转系数
运转状态
运转系数
无冲击运转
1.0~1.2
一般运转
1.2~1.5
有冲击运转
1.5~2.5
把n=1000,T=15000代入式5.2,可得:
(h)
把Fm=177.26,fw=1.2,L=900代入式5.1,可得:
(N)
这样C=20545.1.2刚度验算
滚珠丝杠副的轴向变形会影响进给系统的定位精度及运动的平稳性,因此考虑丝杠的拉伸或压缩变形量δ,先用下式计算受工作负载Fm的作用引起的导程l的变化量Δl,再计算滚珠丝杠总长度上的拉伸和压缩量δ。
(5.3)
式中Δl—在工作负载Fm作用下引起每一导程的变化量,(mm);
Fm—工作负载;
l—滚珠丝杠的导程,(mm);
E—材料弹性模数,对钢E=20.6×104(N/mm2);
F—滚珠丝杠截面积(按内径确定)(mm2);
d1—内径,(mm)d1=D0+2e-2R(5.4)
D0—丝杠公称直径,D0=35mm;
e—偏心距,e=0.056mm;
R—滚道半径,R=2.064mm。
“+”号用于拉伸,“-”号用于压缩。
再计算丝杠总长度上拉伸或压缩的变形量δ(mm):
(5.5)
式中L—滚珠丝杠在支承间的受力长度,(mm)。
先根据式5.4可得:
d1=35+2×0.056-2×2.064=30.984(mm)
由式5.3有
再根据式5.5有
这么小的变形量符合刚度要求。
5.1.3稳定性检验
对已选定尺寸的丝杠在给定的支承条件下,承受最大轴向负载时,应验算其有没有产生纵向弯曲(失稳)的危险。
产生失稳的临界负载Fk可用下式计算:
(5.6)
式中E—材料弹性模数,对钢E=20.6×104(N/mm2);
I—截面惯性矩(mm4),丝杠截面惯性矩I=πd14/64(d1为丝杠内径);
L—滚珠丝杠在支承间的受力长度,(mm);
fz—丝杠的支撑长度系数。
见表5.2。
.
表5.2丝杠的支撑长度系数
方式
一端固定一端自由
两端简支
一端固定一端简支
两端固定
fz
0.25
1.00
2.00
4.00
先求I,I=3.14×30.9844/64=4.5×104(mm4);
这里丝杠是一端固定一端简支,fz=2.00,根据式5.6有
(N)
临界负载FK与最大工作负载Fm之比称为稳定性安全系数nK;nK=FK/Fm>[nK]则丝杠不会失稳,[nK]为许用稳定性安全系数,一般取[nK]=2.5~4。
nK=1.1×106/177.26=6200远大于[nK],所以稳定性很好。
5.1.4滚珠丝杠副的寿命计算
滚珠丝杠副的寿命,主要是指疲劳寿命。
在工程计算中,采用“额定疲劳寿命”这一概念,它指一批尺寸、规格、精度相同的滚珠丝杠,在相同的条件下回转,其中90%不发生疲劳剥落的情况下运转的总转数。
也可以总回转时间或总走行距离来表示,寿命计算公式如下:
(5.7)
(5.8)
式中L1—额定疲劳寿命,(r);
Lt—寿命时间,(h);
C0—额定动载荷,(N),C0=2500N;
Fm—轴向载荷,(N),Fm=177.26N;
fww—运转系数,fww=1.2;
n—丝杠转速,(r/min),n=1000r/min。
由式5.7可得
(r)
由式5.8可得
(h)
Lt>20000h,所以符合。
5.2轴承的校核
本轴承主要是解决其寿命问题,因此对本设计中的角接触球轴承进行校核,其主要参数:
额定动