夹具设计英文文献翻译讲课稿.docx
《夹具设计英文文献翻译讲课稿.docx》由会员分享,可在线阅读,更多相关《夹具设计英文文献翻译讲课稿.docx(8页珍藏版)》请在冰豆网上搜索。
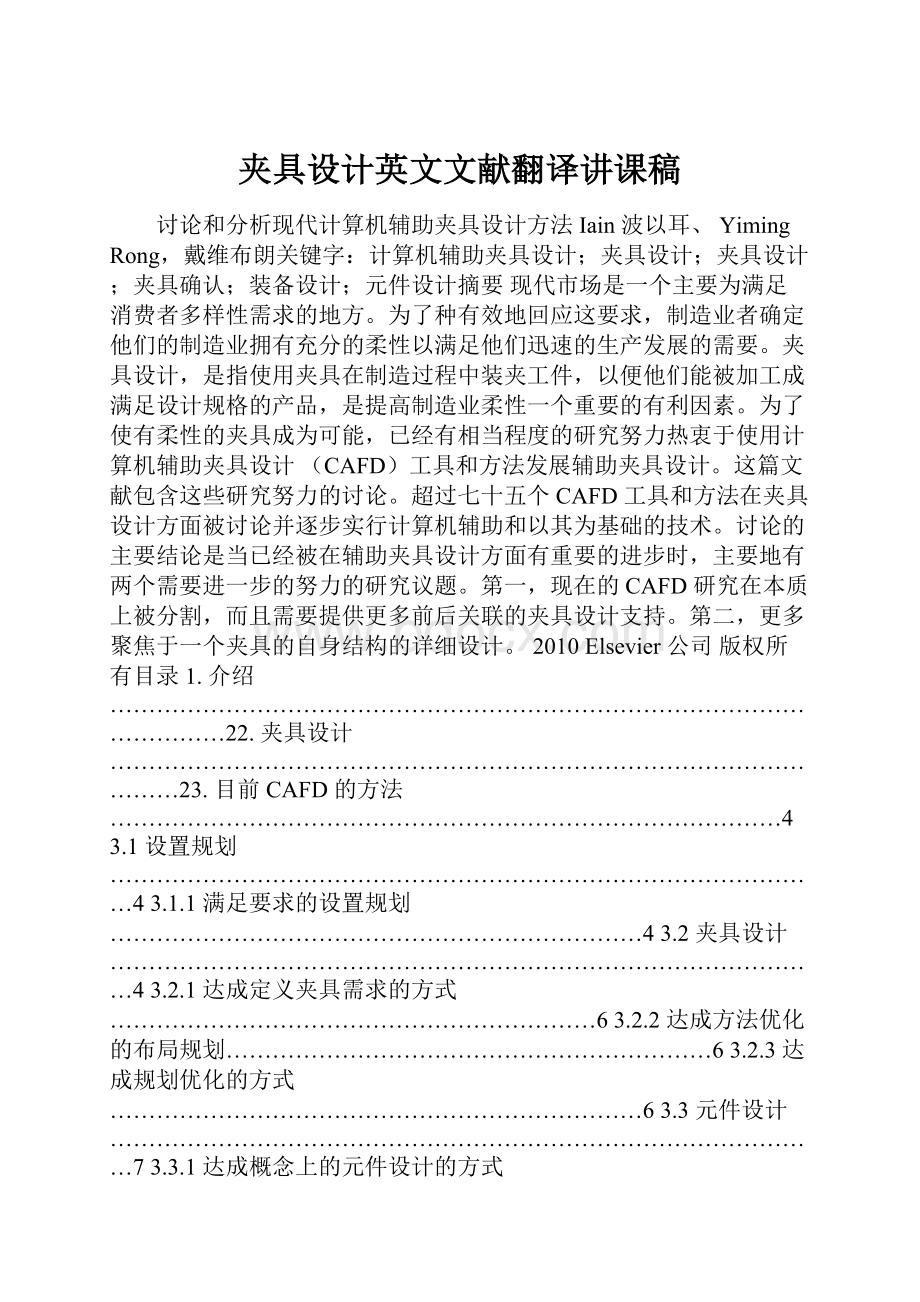
夹具设计英文文献翻译讲课稿
讨论和分析现代计算机辅助夹具设计方法Iain波以耳、YimingRong,戴维布朗关键字:
计算机辅助夹具设计;夹具设计;夹具设计;夹具确认;装备设计;元件设计摘要现代市场是一个主要为满足消费者多样性需求的地方。
为了种有效地回应这要求,制造业者确定他们的制造业拥有充分的柔性以满足他们迅速的生产发展的需要。
夹具设计,是指使用夹具在制造过程中装夹工件,以便他们能被加工成满足设计规格的产品,是提高制造业柔性一个重要的有利因素。
为了使有柔性的夹具成为可能,已经有相当程度的研究努力热衷于使用计算机辅助夹具设计(CAFD)工具和方法发展辅助夹具设计。
这篇文献包含这些研究努力的讨论。
超过七十五个CAFD工具和方法在夹具设计方面被讨论并逐步实行计算机辅助和以其为基础的技术。
讨论的主要结论是当已经被在辅助夹具设计方面有重要的进步时,主要地有两个需要进一步的努力的研究议题。
第一,现在的CAFD研究在本质上被分割,而且需要提供更多前后关联的夹具设计支持。
第二,更多聚焦于一个夹具的自身结构的详细设计。
2010Elsevier公司版权所有目录1.介绍……………………………………………………………………………………………22.夹具设计………………………………………………………………………………………23.目前CAFD的方法……………………………………………………………………………43.1设置规划…………………………………………………………………………………43.1.1满足要求的设置规划……………………………………………………………43.2夹具设计…………………………………………………………………………………43.2.1达成定义夹具需求的方式………………………………………………………63.2.2达成方法优化的布局规划………………………………………………………63.2.3达成规划优化的方式……………………………………………………………63.3元件设计…………………………………………………………………………………73.3.1达成概念上的元件设计的方式…………………………………………………73.3.2达成详细的元件设计的方式……………………………………………………73.4确认………………………………………………………………………………………83.4.1达成约束需求确认的方式………………………………………………………83.4.2达成公差需求确认的方式………………………………………………………83.4.3达成碰撞检测需求确认的方式…………………………………………………83.4.4达成可用性和供应的方式需求确认……………………………………………93.5夹具数据的表现…………………………………………………………………………94.CAFD研究的分析………………………………………………………………………………94.1CAFD研究的被分割的性质……………………………………………………………94.2有效地辅助元件设计…………………………………………………………………104.3综合地明确地叙述夹具需求……………………………………………………………104.4确认CAFD研究输出……………………………………………………………………105.结论……………………………………………………………………………………………10参考文献…………………………………………………………………………………………101.介绍制造业企业的主要担心是发展设计和在短时间范围里生产多种高质量产品的能力。
一种新产品在其他竞争者之前快速进入市场内,是一个能够起到保护、增加市场较高占用额和利润的决定性的因素。
由于对多样性的消费者渴求,已经造成对制造业者需要发展有柔性的制造业的要求,现在产品的一届生产是产品发展中达成一个迅速的大量生产的转机。
一些因素对达成有柔性的制造业的组织能力有影响,其中之一,在生产期间,夹具使用在对哪一个工件进行过生产的机制操作后进入产品之内被装配的个别的部份。
夹具在生产期间要快速、准确、安全地定位工件,使机器制造部份满足设计规格。
现代制造业中准确性促进许多不同的产品以通常的部份为特色达到普遍的部份的可互换性。
夹具的费用占制造业系统的总计费用的10-20〔1。
这些费用不仅包括夹具产品、装配,运转,也包括它们的设计。
因此为了减少夹具与设计费用,有两种方法已经被采用实现这一目标。
一是专注于发展有柔性的夹具系统,例如使用适当地新型材料装夹工件〔2和发展商业模组夹具系统。
然而,有柔性的夹具重要标准是它没有处理设计夹具的困难。
要解决这一个问题,第二个研究方法是发展单一化夹具设计程序的辅助计算机的夹具设计(CAFD)制度,它就是在这文献里面被讨论的研究方法。
第2节描述主要时期和使用夹具设计程序的需求的广泛多样性。
后来在第3节研究努力哪一已经在技术的发展之上集中焦点的概观,而且提供用工具工作为了辅助设计程序的个第别时期。
4节讨论这些努力识别现在CAFD研究的缝隙,最后报纸藉由为将来的CAFD研究提出一些潜在的方向总结。
在进行之前,已经有夹具研究的早先讨论值得注意,最近毕和张〔1,Pehlivan和Summers〔3.毕和张当提供关于CAFD研究的一些细节的时候,容易在有柔性的夹具系统的发展和Pehlivan与Summers之上集中和在夹具设计里面的在数据整合之上重合。
这篇论文的价值是它提供现在CAFD技术和工具和他们如何提供横跨整个的夹具设计程序的支持的深入讨论和批评。
2.夹具设计这一个区段概括说明夹具的主要特征,相关夹具设计程序对研究努力不利将会在第3和4节被分别地检讨和批评。
机床上有一个支持夹紧工件夹具装置〔45.图1是一个工件正确地固定在它的夹具体上的典型例子。
螺栓在加工期间,如此支撑夹紧夹具体工件,固定工件位置。
定位系统有自己的辅助单元和连络工件的定位器。
定位组件有一个螺栓,—辅助单元和一个连络工件,而且产生一个定位力量防止螺栓的松动。
制造这样典型地夹具的设计程序有四个阶段:
装备设计,夹具设计,元件设计,和确认,例如在图2中的说明这是适用于Kangetal的论点的〔6.在装置规划和加工工件信息,为每个装置分析决定机构的数量要求,完成所有必要的加工操作和适当的定位基准。
工件的手动操作代表一个设置相结合的过程可以执行一个无需改变位置或定位工件操作。
要为产生每种装备一个夹具夹具计划单元设计,和运行确认阶段。
在夹具规划,包含设置生成满足要求的夹具和生成的布局规划,它代表了对这些要求解决方案的第一步。
这种布局计划的细节将建立与夹具的定位和夹紧装置的工件表面接触,加上表面的定位和夹紧点位置。
定位点的数量和位置,必须使工件加工过程中的6度自由(图3)有足够的的约束7,有各种各样的方便概念定位点布局,如3-2-1定位的原则4。
在第三阶段,产生合适的元件设计(即定位和夹紧装置)和夹具随后在验证阶段测试,以确保它满足夹具的设计过程中要求。
因为它们产生和元件设计前,采取设置和夹具计划的核查,这是值得注意的地方。
夹具的要求虽然没有显示Kangetal。
6通常设计夹具阶段可以划分为六类表1。
“公差”的要求与确保有足够“支撑”是最基本的要求同时和保证工件夹具可以物理支持;的定位误差的工件定位准确;同样的“夹紧”的要求集中维护这个精度夹具中工件与受加工的力量;“购买力”的要求与保障夹具代表的值例如在从材料、操作和装配、拆卸成本。
“可用性”的“碰撞检测”要求专注于确保夹具与加工路径、工件、甚至本身不碰撞。
要求与夹具相关工程学有关,包括例如需要确保一个固定以防止不正确特征嵌入一个工件和芯片脱落的误差分析那里的夹具协助去除工件加工的误差。
有很多设计的情况下这些要求是有冲突的。
举个例子一个重夹具在安定方面可能是有利的但是成本由于材料成本的增加和可用性因为体重增加可能会阻碍手工处理效果不好。
这种冲突增加夹具的设计的复杂性并对此需要研究综述CAFD第3节。
3.目前CAFD的方法这部分描述了当前的CAFD的研究成果重点介绍了在他们支持的四阶段夹具设计的方表式。
2总结研究成果提供了一个基于设计阶段他们的支持该夹具的要求他们寻求地址要求是写给很大程度上的深度而普通文本程度在自然界的深度较小以及他们潜在的技术对主要的基础。
第3.1-3.4部分分别描述了不同方案支持设置规划、夹具规划、元件设计、验证。
此外第3.5节讨论了对于CAFD代表夹具的信息研究成果。
3.1设置规划设置规划涉及识别加工方法一种个别的装备定义能在没有必须用手改变工件的位置或定方位的工件上被以机器制造的特征。
其后,设计程序的剩余阶段把重心集中在为保护工件的每种装备发展夹具。
从夹具的观点关键输出安装规划阶段是识别各类要求设置、定位基准例如主要的表面将用于工件在夹具定位。
在关键任务设置规划或分组加工的功能可以在一个单一工件设置。
加工特征量可以定义为被切削工具典型的例子包括孔、槽、表面和内表面8。
这些特征聚类成独立的设置是依赖于许多因素包括公差之间的依赖关系的能力特点机床将被用来创造特点、方向刀具的加工方法和特征优先顺序和一批技术已经开发支持设置规划。
虽然基于矩阵的技术和神经网络也被使用,但是图论和启发式推理是最普遍的技术用于支持设置规划。
3.1.1满足要求的设置规划使用图论方法确定和代表机构已经是一个特别常用的方法。
9-11。
图由两个的元素组:
顶点它代表的工件特点、和边缘它代表之间存在的关系特点和安装识别。
它们的自然能变化例如在Sarma和赖特9考虑特征加工之间的优先级关系显著而皇和张10聚焦于公差之间存在关系的特点。
考虑到这些边缘误差加权依照大小该图形法也可以更方便地识别装置能最大限度地通过紧公差减少宽容堆误差的分组机构。
然而比较了不同类型的大小宽容对方,这可能证明问题的难度,因此黄12的因素包括使用公差13作为一种手段为促进这样的比喻,黄、刘14为迎合一个各种各样的公差类型和多个公差要求被联系在一起的产生同一套的特点。
虽然有些方法采用杂乱的图协助建立识别111516张和林。
17使用有利于指导图的决心和显式表达式特色应被用作定位基准图4除了安装识别和次序。
同样鉴定机构等问题提炼通过考虑机床能力提供一个两个阶段的设置规划过程。
在启发式推理的形式中经验知识也被用来帮助安装计划。
其常用的原因是夹具设计效率是依赖于设计经验18。
支持设置规划一般都是举行这样的知识经验的形式导出启发式规则被采纳19。
例如Gologlu20采用启发式规则几何推理来支持特征聚类、特征加工的优先级和定位基准的选择。
在这样一个启发式方法焦点往往落在涉及的物理本质特征与用于创建加工工艺规则21、22。
虽然有些技术包括精度特征的考虑23在图形的基础技术24,他们的深度小于分析发现。
同样25的运动学方法已经被比较深入的应用于分析方法的影响。
然而值得注意基础的方法的是常常是有着经验来提高他们的整体效能16。
基于矩阵的方法也被用来支持设置规划在这一过程中产生的特征矩阵定义集群以及随后的26特征矩阵确定优先次序概述即可加工特点进而对大量的成本优化指标如机床成本随时间变化等等。
通过混合遗传退火算法考虑机床的动态变化的能力。
通过应用演算法Hebbal和梅塔27初始特征矩阵生成一个基于组合机床为每个特征识别方法可考虑面孔和特征定位公差。
另外使用神经网络的规划支持设置也被研究。
神经网络的互联网络进行简单的元素在互联是“学”的一组实例数据。
一旦受过教育的这些网络可以产生新问题的解决方案给网络。
28明、麦使用神经网络方法在具有优先级工具方法和容差关系输入一组Kohonen自组织神经网络业务为单个特征在装备上。
3.2夹具设计夹具设计涉及到综合的定义从夹具要求支撑、精度、夹紧承受能力相适应、碰撞预防和可用性的要求列于表1创造一个夹具布局方案。
布局方案的第一部分是夹具解决工件在指定位置的定位和夹紧。
许多布局规划的方法特征进行验证特别是关于夹紧的要求。
通常这个验证包括反馈回路的组成部分旨在优化布局方案就这些要求。
现在技术用于支持夹具规划讨论对夹具的要求方面的定义、布局规划、布局优化。
3.2.1.达成定义夹具需求的方式综合夹具定义的要求已经受到了有限的关注主要专注于个性化需求的定义在支撑、夹紧、及精度的要求。
例如张在17中对形位公差定义的特征进行了分析来源,确定工件公差允许公差在每一个精度要求的分解。
定位精度是允许点组成的多种因素诸如定位元件精度、机床精度、工件变形的定位等等。
公差要求这些分解的精度可以继续满足夹具设计:
例如定位元件的公差在开发元件设计阶段不能超过规定定位元件精度。
在一个类似的个性化的设计夹紧力实现夹紧元件要求也受了关注29、30。
在31中要求通过提供一个初始分解要求而随后通过一系列的分析和交互的夹具设计精炼而出。
3233韩特等人还关注于功能要求驱动夹具设计但他们主要关注约束限制要求。
3.2.2.达成方法优化的布局规划规划关心的是识别的定位原理它定义了数量和总布置的定位和夹紧点对工件表面的接触就且表面坐标位置在接触发生。
为优化规划使用探讨基于经验知识的重用。
除了以优化为基础的方法20、34、35那些讨论在性质上有类似处在章节3.1使用基于实例的推理。
先前的问题要解决使用特定知识是一个通用的解决问题的推理技术。
该方法应用于布局规划、布局规划得到的工件检索计划183637。
通过典型工件相似特征根据他们的分类、公差、特点等索引工件零件族。
38林佑升及黄采取类似的零件分类方法但使用神经网络恢复布局规划。
进一步的研究也试图验证布局规划和必要的修复。
例如罗伊、廖39完成工件变形分析如果太大变形则采用启发式规则重新定位和夹紧位置和考验。
3.2.3.达成规划优化的方式在布局方案优选是常见的CAFD和发生对工件的稳定性和变形都是约束的要求。
基于典型稳定性优化布局方案确保一个侧重于满足运动学形封闭约束一套接触无穷小的部分完全约束运动、加强这与优化对某种形式的稳定性基础条件例如最小化的力量在定位或夹紧点40-42。
Wu和Chan43集中在优化稳定性测量稳定性在3.4节讨论使用遗传算法GA这是一个经常用于变形技术基础的优化。
Gas是一个进化算法的例子常用于解决优化问题这是自于生物的演化。
应用气体支持夹具规划、潜在的规划设计方案以二进制字符串编码、测试、评估和受生物改性通过复制、突变、和交叉产生改进方案直到达到最佳状态。
工件表面通常使用有限元变形测试分析在这一过程打造了一系列潜在的节点定位和夹紧代表接触点例如由Kashyap执行和DeVries44。
套接触点编码和测试以及开发新的的遗传算法用于工件变形加工、夹紧力引起的接触点集直到达到最佳而不是使用节点4546。
一些CAFD方法使用几何数据如空间坐标的遗传算法它能提供改进的准确性就像他们占了物理距离节点之间存在4748。
伪梯度技术49也被用来实现优化5051。
52进行对比遗传算法和伪梯度优化效果得出这样一个结论:
前者提供了高质量的优化他们的能力来寻找全球性的解决方案而伪梯度技术倾向聚集在当地方案。
更正确的说,超过专注于夹具为个别的部份设计,Kong和Ceglarek53定义一个来确认夹具的工作空间供一个家庭的部分基于个人配置的夹具定位布局为每个部分的方法。
该方法利用普罗斯分析确定初步工作空间布局受到的夹具优化配置然而一个给定的零件叠加在确定最佳定位点,为一个装配的部分可组装在一个可重构装配工装夹具。
这个建立在早期工作由李54通过简化计算的要求尝试的优化算法。
3.3.元件设计元件设计包括定义的概念和详细的定位和夹紧单元之间的夹具连同他们底座相连图5。
这些元件由一种定位和夹接触工件和本身是绑在一个结构性支撑依次连接底座上。
这些结构支持服务等多种功能例如提供定位和夹紧单元具有足够的硬度能承受和应用加工夹具夹紧力从而导致部分特征设计获得了公差并允许夹具和定位器与工件在合适的位置。
单元件设计一般都很少受到前所未有的关注夹具规划与验证但大量的技术已经被用于支持两个概念和详细的单元的设计。
3.3.1.达成概念上的元件设计的方式概念化设计已聚焦的类型及数量的元素应该包含一个元件以及他们的总体布局。
有各种不同的定位器夹子结构性支撑要素每个可以更适合于一些夹具的问题比其他的要大。
随着两个设置规划和夹具布局规划、基于规则的方法也支持采用概念设计元件其中启发式规则是用来选择元素的首选单位必须建立在回应因素例如工件接触特征表面类型、表面纹理等和加工操作在安装3555,58。
除了使用启发式规则作为一种手段产生概念设计、Kumar59使用归纳推理技术建立决策树规则从这种夹具可通过的检查每一个决策树的道路。
神经网络方法也被用来支持概念元件设计。
Kumar等人60使用遗传算法结合神经网络方法中神经网络的训练给你们一组精选的先前的设计问题及其解决方法。
遗传算法产生一个可能的解决方案采用神经网络评价既而引导遗传算法对其求解。
38林及黄也使用神经网络在一个简化的基于实例推理CBR方法中他们的元件设计夹具的问题是由以他们的几何结构和神经网络用于发现类似的工件上工作时。
相反王和Rong37和波以耳31使用传统的CBR方法检索单位夹具的功能需求的基础上形成的检索然后经改良和修改在详细设计单元。
3.3.2.达成详细的元件设计的方式很多的执行概念设计也进行详细的设计包括主导技术规则、几何、和行为的基础但不是所有的系统。
详细的定义设计涉及到单位根据他们的尺寸、材料模型等等。
几何特别是高度夹紧定位代理单位扮演着个体的设计在目标是选择与装配单元的元素定义合适的行动提供一个单位高度的关键角色6162。
63开发了一种基于系统几何尺寸的各个元素之间的关系中形成的主要维度的元素通常是它们所要求的高度通过参数化密度的关系。
这是一个关系有着知识库如何不同的元素可配置形成一个单一的整体。
同样64使用几何约束推理来协助用户指定的元素组合形成单个单位的互动的方法。
另外基于规则的方法也被用于定义详细的单位工件夹具布局和信息例如定位和夹紧位置在使用的设计规则推理来选择和装配适当大小的因素32,55,56。
相反65采用进化算法的发展途径的单位在规划和单元设计同时发生直到达到一个令人满意的解决办法。
一般情况下基于规则和几何方法并不能明确地考虑所需的强度设计单位在他们。
然而实现其功能因此必须能承受加工、夹紧力满足强加于这样的零件设计公差能。
为了解决这一问题很多行为单元设计驱动方法已有聚焦于确保有足够的强度。
塞西尔66提出了一些初步的工作来防止失效尺寸皮带夹由应力性骨折但不考虑公差结构单元或支援。
Hurtado和Melkote67开发一个模型的合成夹具结构简单式柔性加工夹具及尺寸均能达到确定刚度和稳定性为目标通过考虑工件夹具、工件刚度矩阵并且扩大为模块化夹具68。
波以耳31也考虑刚度要求更复杂的单元设计在基于实例推理的方法。
在得到了一个概念设计提供正确的类型的功能该设计的物理结构则是利用动态选择适应适应策略直到它提供了正确的水平的刚度。
3.4.确认验证了聚焦于确保夹具设计按他们的设定计划、布局规划和支撑单元满足夹具的要求。
要注意表2显示大部分的CAFD执行一些类型的验证方法但在这段评论重点将对那些在验证研究成果的一个主要特色的工作。
验证发生与公差、夹紧、碰撞检测、可用性、和售价的要求见表1。
显式验证对这种身体要求不是通常认为是一个重大验证给出其紧密耦合任务的过程设计夹具。
约束验证需求受到了大部分研究的关注其次是宽容和碰撞检测验证需求。
相比之下购买力和可用性的工作验证需求吸引了小的焦点。
3.4.1.达成约束需求确.