汽车维修的作用1解读.docx
《汽车维修的作用1解读.docx》由会员分享,可在线阅读,更多相关《汽车维修的作用1解读.docx(20页珍藏版)》请在冰豆网上搜索。
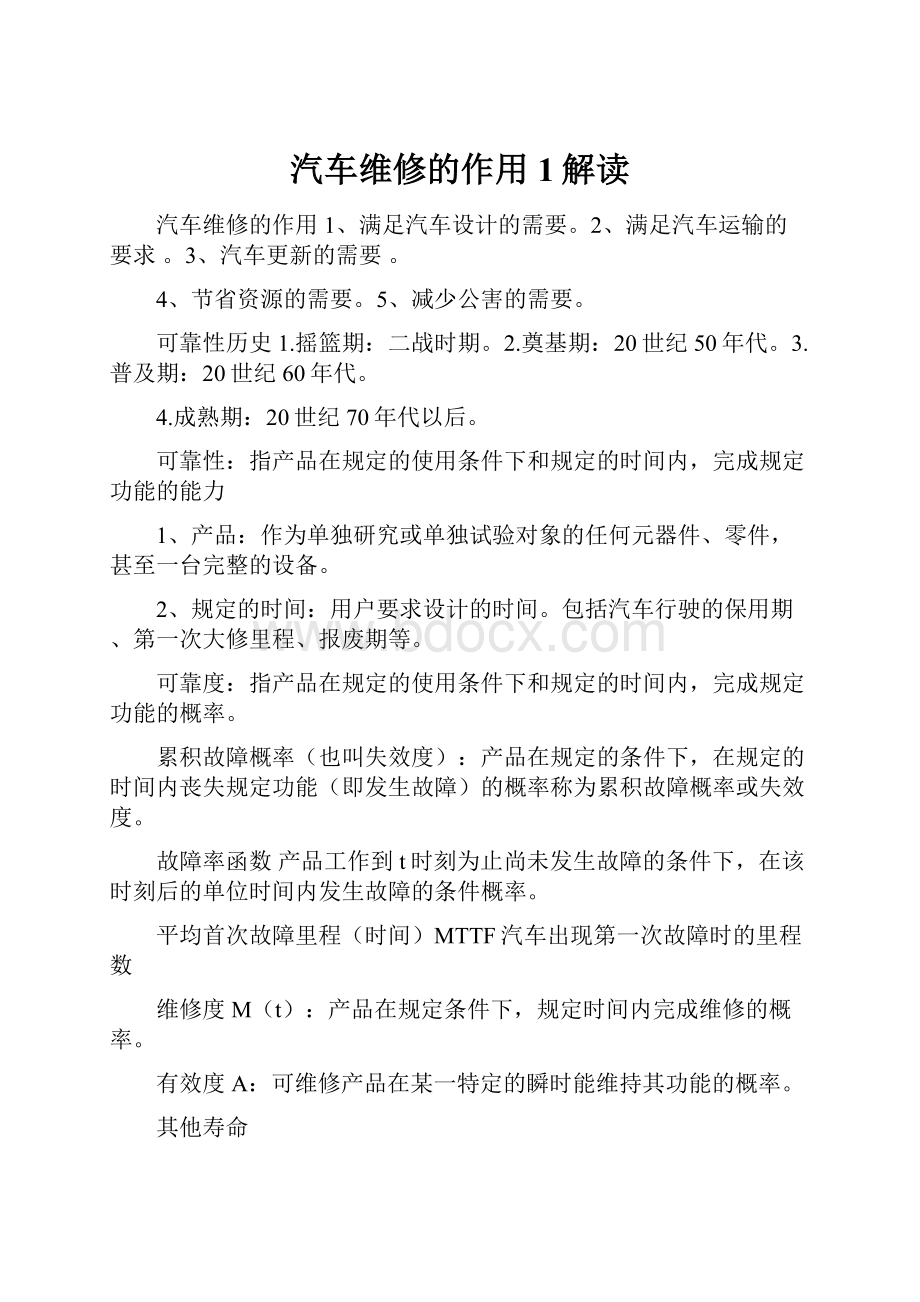
汽车维修的作用1解读
汽车维修的作用1、满足汽车设计的需要。
2、满足汽车运输的要求。
3、汽车更新的需要。
4、节省资源的需要。
5、减少公害的需要。
可靠性历史1.摇篮期:
二战时期。
2.奠基期:
20世纪50年代。
3.普及期:
20世纪60年代。
4.成熟期:
20世纪70年代以后。
可靠性:
指产品在规定的使用条件下和规定的时间内,完成规定功能的能力
1、产品:
作为单独研究或单独试验对象的任何元器件、零件,甚至一台完整的设备。
2、规定的时间:
用户要求设计的时间。
包括汽车行驶的保用期、第一次大修里程、报废期等。
可靠度:
指产品在规定的使用条件下和规定的时间内,完成规定功能的概率。
累积故障概率(也叫失效度):
产品在规定的条件下,在规定的时间内丧失规定功能(即发生故障)的概率称为累积故障概率或失效度。
故障率函数产品工作到t时刻为止尚未发生故障的条件下,在该时刻后的单位时间内发生故障的条件概率。
平均首次故障里程(时间)MTTF汽车出现第一次故障时的里程数
维修度M(t):
产品在规定条件下,规定时间内完成维修的概率。
有效度A:
可维修产品在某一特定的瞬时能维持其功能的概率。
其他寿命
①特征寿命:
可靠度R(t)=e-1=36.8%的可靠寿命称为特征寿命,记为η,亦即累积故障概念F(t)=63.2%时的寿命。
②中位寿命:
可靠度R(t)=50%的可靠寿命称为中位寿命,记为t0.5
③额定寿命:
可靠度R(t)=90%的可靠寿命称为的额定寿命,记为t0.9。
汽车故障:
指汽车在规定的使用条件下和规定的时间内,不能完成规定功能的现象。
2、分类
(1)按故障模式分:
a.损坏型故障b.退化型故障c.松脱型故障d.失调型故障e.功能失效型故障f.堵塞与渗漏型故障
(2)按故障危害程度分:
•a、致命故障(ε1=100)
•i)涉及人身安全,可能导致人身伤亡。
•ii)引起主要总成报废,造成重大经济损失。
•iii)不符合制动、排放、噪声等法规要求。
•b、严重故障(ε2=10)
•i)导致整车性能显著下降。
•ii)造成主要零件损坏。
•iii)用随车工具,备件在30min内不能修复。
•C、一般故障(ε3=1)
•i)造成停驶。
•ii)不会导致主要零件损坏。
•iii)用随车工具,备件在30min内可以修复。
•d、轻微故障(ε4=0.2)
•i)不会导致停驶和正常使用。
•ii)不需要更换零件。
•iii)5min内能轻易排除
典型故障率曲线(浴盆曲线):
1、早期故障期A、2、偶然故障期B、3、耗损故障期C
汽车故障的分布规律:
指数分布、正态分布、对数正态分布、威布尔分布
威布尔分布是基于最弱环模型为物理背景导出的一种分布函数
通常用以下几个寿命来评价产品的可靠性:
•a.B10寿命:
累积失效概率F(t)=10%时的寿命。
•b.特征寿命:
累积失效概率F(t)=63.2%时的寿命。
•c.中位寿命(也叫B50寿命):
累积失效概率F(t)=50%时的寿命。
可靠性试验的目的
•a.为研制新产品、发现其弱点以改进设计;
•b.为确认零件的设计任务书;
•c.为接受产品和保证产品质量;
•d.为审查制造工艺的好坏。
可靠性试验的分类
•a.寿命试验b.临界试验c.环境试验d.使用试验
使用可靠性数据的采集方法:
①对现场人员分发报表,定期返回、②组织专门测定可靠性的人员进行可靠性试验。
数据采集时应注意的事项
1)采集范围:
在每一份数据的收集报告中,产品对象范围要明确统一。
2)制定异常工作的标准:
要尽可能制订出明确的故障判别标准。
3)时间的记录:
时间主要指工作时间。
有的还要考虑运输、储存、停机时间等。
4)使用条件:
主要包括使用场合、气候、使用工况(载荷、车速)及运转形式等。
5)维修条件:
包括维修人员的水平、维修制度、设备条件以及修理水平等。
6)取样方法:
可靠性数据应在母体中随机取样进行调查,既不要仅调查发生事故的产品,也不要把毛病特大特多的除外。
汽车可靠性数据的分析-图分析法
•1、概率纸原理、2、图分析法、
(2)描点(3)配置直线(4)图估计
(1)形状参数m的图估计。
2)尺度参数t0的图估计。
3)特征寿命η的图估计。
4)位置参数r的图估计。
5)平均寿命μ的图估计。
6)方差σ2的图估计、7)可靠度函数R(t)的图估计。
8)可靠寿命tR的图估计。
)
综合评判法利用模糊数学的原理,把定性的因素变成定量的指标。
1、确定因素集U;2、确定评语集V;3、确定评价矩阵R;4、确定权重向量(或系数)A;
5、进行矩阵乘法运算;6、归一处理;7、计算总分。
汽车技术状况的定义:
定量测得的表征某一时刻汽车外观和性能的参数值的总和。
表征汽车技术状况的参数分为两大类:
①结构参数:
②技术状况参数:
汽车完好技术状况:
指汽车完全符合技术文件规定要求的状况,即技术状况的各种参数值,都完全符合技术文件的规定。
汽车不良技术状况:
汽车不符合技术文件规定的任一要求的状况。
汽车的工作能力:
汽车按技术文件规定的使用性能指标,执行规定功能的能力。
汽车故障:
指汽车部分或完全丧失工作能力的现象。
汽车技术状况变化的外观症状:
1)汽车动力性变差。
接近大修里程的汽车,其加速时间将增加25%~35%,动力将下降25%以上(有效功率和有效转矩低于原设计规定的75%)。
2)汽车燃料消耗量和润滑油消耗量显著增加。
如接近大修里程的汽车,其燃料消耗量将增加15%以上。
3)汽车制动性能变差。
4)汽车操纵稳定性能变差。
5)汽车排放和噪声超标。
6)汽车在行驶中出现异响和异常振动,存在引起交通事故和机械事故的隐患。
7)汽车的可靠性变差,使汽车因故障停驶的时间增加
汽车技术状况变化的类型:
(1)渐进性:
(2)突发性:
汽车失效的主要原因
1、汽车零件的耗损。
2、使用条件对汽车技术状况的影响。
(1)道路条件。
(2)运行条件。
(3)运输条件。
(4)气候条件。
(5)维修水平。
汽车失效类型1、磨损。
2、腐蚀。
3、老化。
4、疲劳断裂。
5、变形。
汽车零件的摩擦:
两物体相对运动使其接触表面间产生运动阻力的现象称为摩擦。
1)按运动状态分
①静摩擦:
②动摩擦:
2)按运动方式分:
1滑动摩擦:
②滚动摩擦:
3)按润滑情况分:
①固体摩擦(干摩擦)、②流体摩擦、③边界摩擦、④混合摩擦(a.流体摩擦。
b.半流体摩擦。
c.边界摩擦。
d.半固体摩擦。
e.固体摩擦(干摩擦))
汽车零件的磨损:
零件摩擦表面的金属在相对运动过程中不断损失的现象
分类:
1)磨料磨损:
摩擦表面间存在的硬质颗粒引起的磨损,称为磨料磨损
磨料磨损机理:
微量切削为主的假说、以疲劳破坏为主的假说、以压痕为主的假说
影响因素:
①零件表面的硬度。
②磨料的硬度。
③磨料的粒度。
④磨料在摩擦表面间经过的距离和速度。
⑤磨料与金属表面间的相互作用力。
2)疲劳磨损:
两零件接触表面在交变载荷作用下,零件表层因疲劳而产生物质耗损的现象,称为疲劳磨损。
失效机理:
疲劳磨损是疲劳和摩擦共同作用的结果,其失效过程分为两个阶段:
1劳核心裂纹的形成;②疲劳裂纹的发展③材料微粒的脱落,在零件表面形成点状或片状凹坑。
影响因素:
①零件的材质、②零件表面的硬度、③金属表面渗碳层厚度、④零件表面粗糙度⑤润滑油质量、⑥装配精度
粘着磨损:
当金属表面的油膜被破坏,摩擦表面间直接接触而发生粘着作用,使一个零件表面的金属转移到另一个零件表面引起的磨损,称为粘着磨损。
失效机理:
①冷粘着:
金属原子之间互相扩散,吸引引起的。
由于表面存在微观不平,表面的接触发生在微凸体处,在一定载荷作用下,接触点处发生塑性变形,使其表面膜被破坏,两摩擦表面金属直接接触形成粘结点(即固相焊合)。
②热粘着:
当摩擦副在高的滑动速度,大接触应力的工作条件下,摩擦副表面实际接触的微凸体,因大量的摩擦热而产生熔化和熔合,相互粘接在一起,又在相对运动中被撕裂,严重时造成相对运动停止(由于局部压力大、温度升高、产生熔化而引起的)。
影响因素:
①摩擦副的材料特性的影响、②润滑油的影响、③零件表面性质、④运动速度和负荷的影响、
氧化磨损:
零件摩擦表面微凸体上的氧化膜由于摩擦遭到破坏而脱落,而在另一次摩擦接触前又形成新的氧化膜,这种氧化膜不断被除去,又反复形成的过程称为氧化磨损。
微动磨损:
零件的嵌合部位,静配合处,在力或振动作用下产生的,由静配合变成动配合,而产生微小的滑动,此时表面上产生大量的微小氧化物磨损粉末,由此造成的磨损称为微动磨损。
影响因素:
①零件振动:
振动幅度的大小,振动频率对磨损量都会产生影响。
②配合副的材质:
铝-铝、铝-钢配合都容易产生微动磨损。
③空气含量(主要氧气和腐蚀气体的含量)对磨损量也会产生影响。
减少磨损的措施
(1)正确选择材料:
配合副材料尽量选不同,如一硬一软不易磨损。
(2)正确选择配合副。
(3)进行表面强化。
如材质达不到设计要求时,则要改进其表面性能。
(4)改善工作环境:
不要超载,减轻载荷。
(5)结构设计合理:
润滑条件得到改善,避免应力集中。
(6)提高加工质量:
如提高表面粗糙度,提高装配质量等。
气缸的磨损特点:
a.高度方向的磨损:
b.直径(圆周)方向的磨损
影响因素:
a.磨料的影响、b.工作气体压力的影响、c.工作温度和润滑油粘度的影响、d.腐蚀的影响
综合分析:
高度方向的磨损原因:
•磨料压力润滑腐蚀
•上部多上部大上部坏上部重
•下部少下部小下部好下部轻
直径方向的磨损原因:
•a.磨料:
对着进气门位置的磨料多,磨损就大。
•b.润滑:
对着进气门位置受可燃混合气冲刷、润滑条件差,磨损大。
•c.腐蚀:
对着进气门位置温度低、腐蚀就大,磨损也大。
零件磨损量的测定方法:
(1)直接测量法、①表面测量法②称重法③刻痕法④快速磨损法
(2)间接测量法、①光电比色法、②光谱分析法、③同位素法
汽车零件的腐蚀与气蚀
1、零件的腐蚀:
金属零件受周围介质作用而引起的损坏叫做零件的腐蚀。
按腐蚀机理可分为化学腐蚀和电化学腐蚀。
(1)化学腐蚀:
金属零件与介质直接发生化学反应而引起的损坏称为化学腐蚀。
(2)电化学腐蚀:
金属与介质发生电化学作用而有电流产生的腐蚀。
(3)预防方法:
①改变金属本身的成分。
2面覆盖,即对金属表面进行改性,表面进行强化,如电镀(镀铬、镀锡)等。
3计合理,如提高零件表面粗糙度等
2、零件的气蚀(也叫穴蚀)
当零件与液体接触并有相对运动时,零件的表面出现的一种破坏现象,称为穴蚀。
特点是在局部区域出现麻点、针孔,严重时呈聚集的蜂窝状的孔穴群。
(2)影响因素及防止措施
①结构影响a.缸套壁厚,适当增加缸套壁厚,加中间支撑,减轻缸套的振动。
b.活塞结构。
②修理装配质量的影响a.缸套倾斜的影响。
b.位置偏差的影响。
c.活塞-缸套装配间隙的影响,尽可能减小活塞-气缸间隙,有利于减轻缸套的振动。
4冷却系结构及冷却液特性方面的影响。
a.冷却液温度的影响。
b.冷却液性质的影响。
c.冷却系结构的影响。
④柴油机工作过程粗暴,易产生压力,加快穴蚀。
汽车零件的疲劳断裂:
零件在反复多次的应力或能量负荷循环后才发生断裂的现象叫做零件的疲劳断裂。
(1)按断裂后的表面特征分:
塑性断裂、脆性断裂
(2)按断口的微观特征分:
晶间断裂、穿晶断裂
(3)按零件承受载荷的性质分:
机械断裂、疲劳断裂
(4)按应力循环次数分
①高周疲劳断裂:
应力循环次数Nf≥104次。
②低周疲劳断裂:
应力循环次数Nf≤104次。
疲劳断裂的失效机理
(1)疲劳裂纹核心策源地的形成。
(2)疲劳裂纹的扩展。
(3)疲劳断裂。
脆性材料的断口呈粗糙的“晶粒”状结构或呈放射线,塑性材料的断口具有纤维状结构,在零件表面有剪切唇。
提高汽车零件抗疲劳断裂的方法
(1)延缓疲劳裂纹萌生时间。
(2)降低疲劳裂纹扩展的速率。
(3)提高疲劳裂纹门槛值长度
疲劳断裂与疲劳磨损的区别
(1)损伤形式不同:
疲劳断裂是突然断裂,疲劳磨损是金属一块一块脱落。
(2)受力情况不同:
疲劳断裂主要受拉、压应力反复作用,疲劳磨损主要受油楔力反复作用。
(3)表面变形不同:
疲劳断裂属于非塑性变形,疲劳磨损伴随有塑性变形。
(4)初始裂纹不同:
疲劳断裂初始裂纹在表面,疲劳磨损初始裂纹在表面下0.15~0.25mm处。
汽车零件的变形:
零件在使用过程中,由于承载或内部应力的作用,使零件的尺寸和形状改变的现象称为零件的变形。
类型:
(1)弹性变形失效、
(2)塑性变形失效、(3)蠕变变形失效
2气缸变形的后果a.气缸轴线不垂直于曲轴轴线。
b.曲轴轴线不平行于凸轮轴线。
c.气缸体上下平面不平行。
d.曲轴主轴承座孔的不同轴度。
e.曲轴轴线不垂直于端面
①变速变形规律:
和受力有关,变形情况比较复杂。
a、长度方向(X方向)合力的作用,对端面形成扭矩。
b、宽度方向(Y方向)合力的作用,对端面形成扭矩。
c、高度方向(Z方向)即自重的作用形成扭矩,处于又弯又扭的复杂变形状态。
汽车零件变形的影响因素:
(1)内应力:
热应力、相变应力
(2)外载荷的影响:
①设计原因、②使用原因、③维修原因(3)温度的影响(4)零件变形的内因①空位②位错③扩散
电子元器件的损伤1)影响因素
(1)温度:
高温是造成电子元器件过热损坏的重要原因。
(2)湿度:
湿度增加,会使电子产品的绝缘性能下降,加速老化。
(3)电源电压的波动:
瞬间过电压对电子元器件的危害很大
2)电子元件的损伤及其故障特点
(1)元件击穿
(2)元件老化(3)连接故障
工程塑料的损伤1)工程塑料的特点
(1)物理性质:
密度小;
(2)机械性能①抗拉强度低;
3弹性模量小
3)工程塑料的损伤
(1)老化
(2)疲劳破坏(3)磨损(4)刮痕(5)龟裂
橡胶制品的损伤1)轮胎2)胶管3)油封件4)减振橡胶
数据收集记录单的主要内容应包括:
(1)使用单位名称;
(2)记录对象;(3)时间;(4)使用条件;(5)故障内容;(6)维修状况;(7)现场人员分析。
注意事项1)明确研究对象;2)规定故障含义;3)统一时间单位;4)说明使用条件;
4)反映维修状况;6)掌握取样原则
预防性维修:
定时拆修、定时报废、视情维修、状态监控维修
可靠性为中心的维修策略特点:
1)生产的复杂性继续增加;2)自动化程度加速;3)即时生产系统出现;4)产品标准和服务质量要求提高;5)视情维修、以可靠性为中心的维修和计算机辅助维修管理方式被普遍采用
汽车维修执行的是四级保养制度。
分为:
例行保养:
清洁、检查、补给;一级保养:
紧固、润滑;二级保养:
检查、调整;三级保养:
部分总成解体;
四类修理:
大修、小修、总成大修和零件修复
影响维修性的主要因素
(1)汽车的总体布局和结构设计。
(2)部件和连接件的折装。
(3)维修作业的程序。
(4)可达性。
(5)检测性。
(6)无维修设计
有效度是指汽车(总成、子系统)在某一时刻,能维持正常功能的概率
有效度指标:
固有有效度、可达有效度、工作有效度
国外汽车维修标准化工作的特点
(1)涉及新技术领域,如电子、计算机以及通讯技术在汽车检测维修领域的应用。
(2)汽车安全设施与技术方面,如乘员安全、维修人员安全、环境影响。
(3)环境保护,如汽车排放、噪声、电磁干扰、清洗等。
(4)汽车检测及维修技术要求的细化。
(5)日本和美国将涉及汽车安全、环境以及注册的有关要求以国家法的形式予以颁布
(6)有的国家标准工作由标准化协会直接规划、组织、协调制定、修订和出版,国家或标准化协会仅负责带有普遍性的根本性法规。
(7)国际标准化机构(ISO)国际道路车辆标准化专业委员会ISO/TC22制定的有关道路车辆互换性和安全性是制定汽车维修检测标准的基础,各国的其他相关标准是以其作为基础,进行细化和补充。
(8)目前,国外标准中针对具体的某一类汽车检测设备的技术标准、测试标准和维修设备技术标准还很少。
按维护周期分类1、日常维护作业:
每天都要进行以清洁和减次为主的作业,每行驶100~200km进行一次,由驾驶员完成,其中心内容:
清洁、补给(润滑油、燃油、冷却水、轮胎气压等)和安全检视。
2、一级维护作业:
每行驶2000~3000km进行一次(即10~20个工作日进行一次)以润滑和紧固为中心内容,由专业维修工负责执行。
3、二级维护作业:
每行驶1~1.5万km进行一次,以检验和调整为中心内容,规定:
车辆在二级维护前,必须先进行检测诊断和技术评定。
4、二级附加作业:
第二次二级维护后附加的作业。
车辆行驶状态分类1、初驶车维护作业(初驶车包括新车、大修后出厂的车)。
2、行驶车维护作业(包括定程维护、分级维护)。
3、停驶车维护作业(停驶车是指停驶1周以上的车)
按作业性质分类1打扫、清洗和外表养护作业。
2、检查与紧固作业3、检验与调整作业:
用设备和仪器上检测线进行的作业。
4、电气作业:
对电气设备进行的作业。
5、润滑作业:
对润滑系统进行的作业。
6、轮胎作业:
轮胎充气、清理、轮胎换位及更换内外胎。
7、加注作业:
检查油箱,加油、检查水箱状况,并加注冷却液。
置信水平(1-):
是指技术状况参数的实际变化率低于或等于极限变化率的概率
汽车维护作业里程的确定1、紧固作业里程的确定
(1)研究的必要性:
①直接影响到汽车的安全性,可靠性和经济性。
②影响汽车的使用寿命。
③影响维修费用。
(2)确定方法:
①抽样调查②统计、分析
2、检验、调整作业里程的确定:
(1)抽样、调查。
(2)观察记录
在组织汽车维护工艺时,应考虑以下几个原则:
1)工艺过程的组织应符合车辆运行的工作制度;
2)能合理利用维护工艺设备和生产面积;
3)能有效地完成规定的维护工作内容,保证维护质量;
4)工艺过程的组织应保证维护作业的劳动生产率高,成本低。
汽车维护作业的组织形式按专业分工程度不同,分为:
全能工段式(
(1)固定工位作业、
(2)平行交叉作业)、专业工段式(
(1)尽头式工段、
(2)直通式工段)
统筹法:
用流线图科学安排组织生产并进行计划管理的一种组织方法,在国外也叫网络法。
流线图:
按各个工序的时间,顺序标出的箭头图就叫流线图。
工序:
指一项需要人力、物力、财力才能完成的生产过程叫工序
就车修理法(也叫原车原件修理法):
进行修理作业时,要求被修复的主要零件和总成装回原车的修理方法。
缺点:
影响生产过程的连续性、不能流水线生产。
停厂日长、必须等修理周期最长的总成修竣后方能装配汽车,因此大修周期较长。
总成互换修理法:
用储备的完好总成替换汽车上的不可用总成的修理方法。
周转总成:
预先储备的汽车总成,用来替换维修中的不可用总成。
优点:
保证汽车修理的连续性缩短停厂车日。
适合大规模生产、流水线作业。
缺点:
需要备用总成、成本高。
破坏原车原貌。
混装修理法:
进行修理作业时,不要求被修复零件和总成全部装回原车的修理方法。
修理费时的件采用互换修理法,其它件采用就车修理法
汽车修理生产中采用两种作业组织方式
1、固定工位作业法:
在一个工作位置完成全部修理工作。
优点:
节省工作面积、适合生产规模小、车型复杂的修理企业。
不受连续性限制。
缺点:
劳动强度大,要求工人技术全面,不易提高其熟练程度。
不适合大规模作业,难于使用专用设备。
2、流水作业法:
汽车在生产线的各个工位上按确定的工艺顺序和节拍进行修理的方法。
流水作业法又可分为连续流水作业和间断流水作业两种。
优点:
劳动强度小、专业化程度高、
工效高、适合于单一车型、生产规模较大的修理企业。
缺点:
设备投资大、占地面积大
不适合于生产规模小、车型复杂的修理企业;
修理生产的组织方式有:
综合作业法和专业分工作业法。
(1)综合作业法:
由一个作业组承修一辆汽车的大部分修理工作。
是适用于固
定工位作业法的一种劳动组织形式。
特点:
需要全能的修理工人,修理周期长,成本高,一般只适用于生产规模小、车型复杂的修理企业。
(2)专业分工作业法:
将汽车修理作业按工种、部位、总成、组合件或工序由一个或几个专业组专门负责进行的。
既适用于固定工位作业法,也适用于流水作业法。
特点:
便于采用专用工艺装备,能保证修理质量,提高工效,易于提高工人的操作技术水平,修理周期短,一般适用于承修车辆多、车型较单一的修理企业。
汽车的检验接收
1、为了有效地组织修理生产,承修企业应掌握送修车辆的情况。
2、确定承修车辆的技术状况与装备的齐备程度。
3、检验送修汽车以进一步了解汽车各部的技术状况。
汽车及总成的解体
1、合理组织拆卸作业及安排工艺顺序。
2、正确使用拆装工具和设备。
3、注意零件间的相互位置关系以防止拆卸错乱。
4、其他应注意的问题。
汽车及零件的清洗:
1、汽车外部清洗、
(1)清洗的分类①按水温分类:
冷水清洗、热水清洗。
②按水压分类:
低压清洗(洗车身,压力为0.2~0.4Mpa)、高压清洗(洗底盘,压力为1.8~2.5MPa)③按执行方式分类:
人工清洗、机械清洗。
(2)清洗设备简介:
底盘清洗设备、车身清洗设备、滚刷设备、助设备
汽车零件清洗:
(1)油污的清洗①碱水除油a.除油机理、c.影响因素
清洗液温度,80~90℃为好。
机械搅拌。
喷洗压力。
②有机溶剂除油
(2)积炭的清除:
清除方法:
1)机械清除:
用金属刷子或刮刀清除,这种方法劳动量较大,不能将积碳完全清除,容易损伤表面。
2)化学清除:
退碳剂浸泡→炭层膨胀→变软→清除。
3)熔盐清除法:
将零件放在温度为(400±10)℃的65%的氢氧化钠、30%的硝酸钠和5%的氯化钠溶液中进行处理,使积碳沉积物充分氧化钠;
(3)水垢的清除;与冷却水接触的地方易形水垢,水垢的成分取决于所用冷却液的成分,可以是碳酸钙、硫酸钙、硅酸钙的沉积物或是它们的混合物。
零件的检验分类:
根据零件的技术状况,分为可用零件,需修零件和不可用零件三种
技术条件的内容:
①零件可能产生的缺陷。
②缺陷的特征和检验方法,并用简图标明缺陷的部位。
③零件的性能(包括零件的尺寸、材料、热处理性能等)。
④零件的使用极限及允许值(包括极限磨损寸尺,容许磨损尺寸和容许变形量或相对位置偏差)。
⑤零件的报废条件。
⑥零件的修理方法。
(3)确定零件容许磨损量,极限磨损尺寸的传统方法:
①经验统计法、②试验研究法、③计算分析法
汽车零件检验方法分类:
1、外观检验:
具有显著裂纹、变形或磨损的零件。
2、几何尺寸测量。
3、零件形位公差测量。
4、零件内部组织缺陷的检验。
5、高速旋转组件的平衡
汽车零件形位误差的检验:
1、圆度、圆柱度误差的检测:
常用两点法测量。
2、平行度误差和垂直度误差的检测3、同轴度误差的检测、4、平面度误差的检测、5、圆跳动的检测、6、直线度误差的检测
汽车零件隐蔽缺陷的检验:
1、荧光探伤、2、磁力探伤(纵向磁化探伤、环形磁化探伤、联合磁化探伤)3、超声波探伤:
(1)穿透式探伤
(2)反射式探伤4、水压试验、5、射线探伤(
(1)X光探伤
(2)γ射线探伤)
不平衡的原因:
①材质不均匀(如有气焰、砂眼等)。
②加工误差引起的轴线偏离等。
③装配误差(不同轴等)。
④使用中磨损、变形引起的。
汽车零件的平衡方法:
静平衡(减重法和加重法)、动平衡(加重法和减重法)、组合件的平衡:
指曲轴、飞轮及离合器组合件,将它们装配一起进行动平衡试验。
汽车总成装配的一般技术要求
(1)配合副的配合特性。
(2)主要联接件的紧固力矩及其均匀性。
(3)各零件工作表面和轴线间的相互位置。
(4)旋转件的平衡要求。
(5)高速运动件的质量要求。
(6)密封性、清洁度和调整要求。
总成磨合的目的:
1、加大承载面积。
2、提高零件表面的质量、耐磨性、疲劳强度和抗腐蚀性能。
3、发现装