普通气动滑阀作业指导书.docx
《普通气动滑阀作业指导书.docx》由会员分享,可在线阅读,更多相关《普通气动滑阀作业指导书.docx(13页珍藏版)》请在冰豆网上搜索。
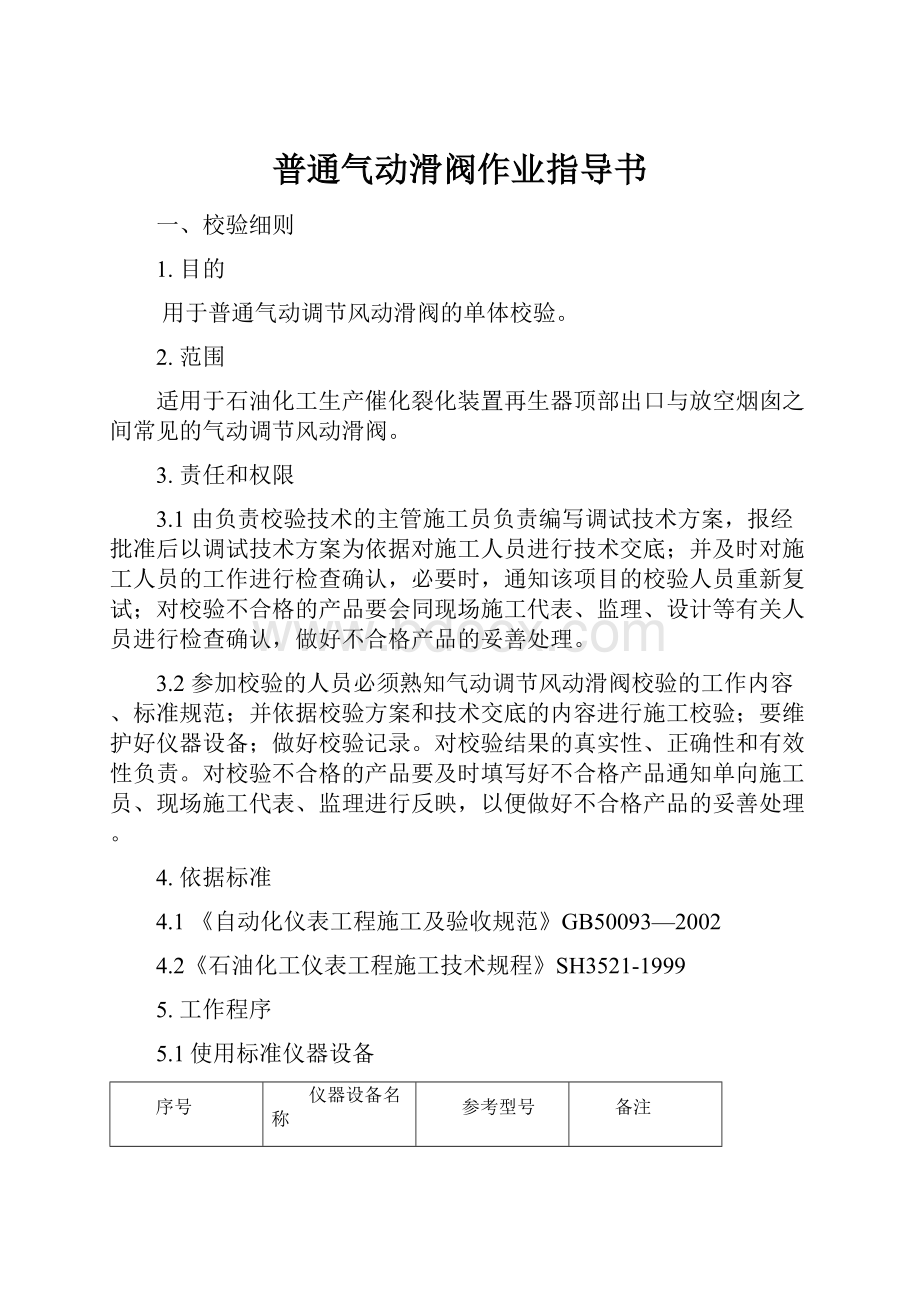
普通气动滑阀作业指导书
一、校验细则
1.目的
用于普通气动调节风动滑阀的单体校验。
2.范围
适用于石油化工生产催化裂化装置再生器顶部出口与放空烟囱之间常见的气动调节风动滑阀。
3.责任和权限
3.1由负责校验技术的主管施工员负责编写调试技术方案,报经批准后以调试技术方案为依据对施工人员进行技术交底;并及时对施工人员的工作进行检查确认,必要时,通知该项目的校验人员重新复试;对校验不合格的产品要会同现场施工代表、监理、设计等有关人员进行检查确认,做好不合格产品的妥善处理。
3.2参加校验的人员必须熟知气动调节风动滑阀校验的工作内容、标准规范;并依据校验方案和技术交底的内容进行施工校验;要维护好仪器设备;做好校验记录。
对校验结果的真实性、正确性和有效性负责。
对校验不合格的产品要及时填写好不合格产品通知单向施工员、现场施工代表、监理进行反映,以便做好不合格产品的妥善处理。
4.依据标准
4.1《自动化仪表工程施工及验收规范》GB50093—2002
4.2《石油化工仪表工程施工技术规程》SH3521-1999
5.工作程序
5.1使用标准仪器设备
序号
仪器设备名称
参考型号
备注
1
仪表空气发生装置
可用空气压缩机
2
台式标准压力表
精度和规格符合规范
3
千分尺
0.01,10mm
4
气动定值器
5.2校验环境要求
5.2.1有具备良好环境(10℃≤环境温度≦30℃、相对湿度≯80%、)的仪表校验间,(也可对已安装完善的气动调节风动滑阀进行就地校验)。
5.2.2有外供气源(0.6MPa的动力风)或有移动式无油空气压缩机、过虑器、干燥器、稳压器等设备组成的仪表空气发生装置提供气源(0.6MPa动力风)。
要求气源应清洁干燥,气源压力应稳定,波动值允许误差小于额定值的±10%。
5.2.4喷雾润滑器、减速箱油液面符合要求。
5.2.5所用标准仪器应具备有效的检定合格证书,其基本误差的绝对值不宜超过被校表基本误差的绝对值的1/3。
5.3校验前的准备工作
5.3.1由负责校验技术的主管施工员对参加校验的施工人员进行技术方案交底。
5.3.2参加校验的施工人员详细了解气动调节风动滑阀使用说明书,掌握气动调节风动滑阀调试的校验方法,明确气动调节风动滑阀校验的特殊要求和规定。
5.3.3准备好符合要求的校验仪器、设备及必要的使用工具。
5.3.4气动调节风动滑阀自身具备校验条件。
5.4气动调节风动滑阀的调校方法及步骤
5.4.1极限开关的调整(原理图见图1)
图1极限开关原理图
1)在使用风动马达操作前,应按下列步骤调整极限开关:
开阀及限位量的调整
a.关闭动力风。
b.用手轮将阀板打开到阀杆上的凸圈与密封圈接触的位置,记录极限开关上操纵快开阀的凸轮上的齿轮轴转动方向。
c.返回阀板,使阀杆凸圈与密封圈离开约3mm,作为阀板缓冲余隙。
d.保持阀板在此位置,将极限开关的中心顶丝拧入约6mm,即螺丝槽底与齿轮箱面齐平位置,使龊轮与计算齿轮脱离,齿轮轴不再转动。
e.用与(b)中所记录的同样方向转动该齿轮轴,直到凸轮转90°并推开联杆。
f.回拧中心顶丝到原位(尽头位置),使龆轮与计数齿轮重新啮合,开阀调整即完毕。
调整关阀极限位置的步骤与调整开阀极限位置的步骤完全相同,仅只是“挡键”或其它机械限位装置代替了“密封圈”,但是这两个步骤必须单独进行;即当一端调整完毕后,再以同样的步骤进行另一端的调整。
必须特别注意,当中心顶丝拧入时,绝对不能再动手轮,否则调整就失去了准确性,则必须按上述步骤重新调整。
每次调整极限开关时都应按照上述步骤进行。
调整完毕后,应用手轮反复开关阀板,并检查凸轮是否按原定的位置瞬时转动90度,当凸轮转动90度时,阀杆凸圈或阀板是否与密封圈或档键等的保持一定的间隙(3mm)。
5.4.2指挥阀的调整:
指挥阀的调整应在极限开关调整后进行。
①.调整活塞左端的调节螺栓、使活塞完全关闭两个出气孔时,膜片正好处于自由状态,即活塞的调节螺栓端面此时刚好轻轻抵住膜片螺栓端部,以保证指挥阀有较好的特性。
调整前应打开顶盖,取下膜片、使活塞大概处于活塞套的中间位置而关闭两个出气孔。
然后送入小量的动力风。
移动活塞,使右端的出气孔微微打开,风动马达也轻轻启动,用深度游标尺测量活塞右端至压紧螺母端面的距离C1。
往左慢慢移动活塞左端至压紧螺母端面的尺寸C2此时可计算出C的值为:
C=1/2(C1+C2)
移动活塞,保证C的尺寸后,再测量出左端的尺寸b,应使b=a,如不等,可通过调整调节螺栓的伸出长度来达到,然后用螺母锁紧(此项应关闭动力风进行)。
②.调节螺母的调整
装上膜片、顶盖、弹簧、调节螺母(调节螺栓未拧紧)。
顶盖通入60kPa的信号风压,并送入动力风。
此时风动马达开始转动,向里调节调整螺栓,
压力至风动马达开始启动,此信号压力P1为上行程风压,然后逐渐减少顶盖内的信号压力,使风动马达反转,此时信号压力P2为下行程风压,应反复调整螺母使1/2(P1+P2)=60kPa。
③.指挥阀上下行程出气口开度相等的调整:
指挥阀上下行程出气口开度是控制风动马达转速的部位,应要调整一致。
a.测定上下行程出气口的度:
先将指挥阀顶盖内通往60kPa的信号压力,然后开启动力风,再逐渐增加信号压力,使风动马达开始启动,测量出活塞端部与调整螺母端部尺寸S1,再增加信号压力至120kPa,再如上位置测出S2。
S1-S2=上行程出气口开度。
b.测定下行程出气口开度:
减少顶盖内通入的信号压力,使风动马达反向启动,再如上述测出S3尺寸,再把信号压力降至0,测出S4尺寸,则S4-S3为下行程出气口开度。
若上下行程出气口开度不等,则应调整活塞上的调节螺栓,上行出气口开度小可增加调节螺栓的长度,下行出气口开度小可减小调节螺栓的长度。
5.4.3定位器和变送器传动部分的调整(调整时关闭动力风):
①调整塔齿轮Z8、Z9与空心轴上轮Z7和蜗杆轴上齿轮Z10的传动间隙。
(见图2)
图4.4.4.1—3定位器和阀位变送器的传动机构示意图
图2
先松开塔齿轮支架上的紧固螺栓,移动支架,使齿轮Z7与Z8和齿轮Z9与Z10的齿侧间隙为0.2~0.3mm,然后上紧紧固螺栓。
②凸轮中点位置的调整:
手动阀门至阀杆行程的中点位置后不动,松开凸轮轴端上的锁紧螺钉,转动凸轮,使凸轮上有效转角330度的中间位置即165度位置对准定位器和阀位变送器的滚轮,然后上紧螺钉。
5.4.4行程的调整:
为了使定位器输入信号压力由20kPa变到100kPa时(也可由100kPa变到20kPa)凸轮的转角和阀杆行程达到对应要求的数值,需要调整定位器中的反馈弹簧的工作圈数,其原理是当弹簧2的工作圈数增加时,它的刚度减少,因为增加工作圈数的弹簧2的拉力就要降低,凸轮转角必须增加△ф,才能达到需要的反馈量,亦即弹簧的拉力增大到可以使波纹管回到平衡位置的数值。
这样弹簧2的工作圈数增加时,凸轮转角增大,阀杆行程增加。
反之,当弹簧2的工作圈数减少时,它的刚度增大,因为减少工作圈数与未减少工作圈数的两个弹簧2,当它们变形后的长度相同时,减少工作圈数的弹簧2的拉力就要增大,凸轮的转角减少△ф就能达到需要的反馈量,即弹簧2的拉力减少到使波纹管1可以回到平衡位置的数值,这样当弹簧2的工作圈数减少时,凸轮的转角减少,阀杆行程减少。
总之,通过增加或减少弹簧2的工作圈数,就可以使阀杆的行程达到要求的数值。
5.4.5特殊调整:
①作用调整:
传动及自动控制部分可以很方便的从正作用改为反作用。
所谓正作用亦称气关式,即气动调节信号的压力增加时,阀关;所谓反作用也称气开式,即气动调节信号的压力增加时,阀开。
在改变正或反作用时,仅需将凸轮反装或正装,并相应地对调节气动指挥阀及风动马达动力风管线走向即可。
设计选用单动滑阀为反作用,双动滑阀为正作用。
②范围调整:
假如发生阀在全开或全关的位置,而气动调节信号的压力并不是在相应的范围内时,则应调节定位器内反馈拉伸弹簧2的有效圈数及调整放大杆4的平行度。
气动调节信号正常的压力变化范围80kPa,±0.3kPa。
不管杠杆10与放大杆4的平行度偏向哪一个方向,都会影响气动调节信号的压力范围;同时对特定的行程,主要的是准确地固定反馈拉伸弹簧2的有效圈数,以保证80kPa的变化范围与阀杆的行程相对应。
假如弹簧的有效圈数比计算圈数小则将使变化范围减小,圈数多,则将使范围增大。
因此,增多圈数可使范围增大,减小有效圈数可使范围缩小。
③定位器(阀位变送器)的零位调整:
调整零位最方便是在阀杆位于全行程中间位置进行。
当通入动力风后,传动及自动控制部分可能将阀杆移动到超越或不到予定的中间位置,这就表明需要调整定位器的零位,调整方法如下:
a.将气动调节信号的压力保持在60kPa,然后在弹簧2与平行板联接处用人工压缩或拉伸反馈弹簧2(见图3)的方法,以决定调节的方向。
假如将弹簧压缩而阀杆向中间位置移动,则表示需要增加弹簧的予拉力;相反,假如将弹簧拉伸而阀杆向中间位置移动,则表示需要减小弹簧的予拉力。
图4.4.4.1-3定位器工作原理
1-波纹管2-反馈弹簧3-平衡板4-放大杆5-挡板6-喷咀
7-放大器8-反馈波纹管9-放大弹簧10-杠杆
图3
b.增加弹簧的予拉力:
退出锁紧螺母,正转调整螺钉,而增加弹簧
的予拉力,并观查阀杆动向及最后位置,直到在气动调节信号的压力保持在60kPa时,阀杆位于中间位置为止。
如果减小弹簧的予拉力,则反转调整螺钉以减小弹簧的予拉力,则反转调整螺钉以减小弹簧的予拉力,并观查阀杆最后停留的位置,直到气动调节信号的压力保持60kPa时,阀杆位于中间位置为止。
c、拧紧锁紧螺母,以保持予拉力。
d、改变气动调节信号的压力,以观查整个操作系统是否正常,即阀杆位置的变化是否与气动调节信号压力的变动成比例。
5.4.6以上调整完毕,需做如下试验:
5.4.6.1、全开及全关时间试验;
将气动调节信号从20KPa升高到100KPa(或从100Kpa下降到20Kpa),阀板应在45秒钟内从全开到全关(或从全关到全开)。
5.4.6.2、准确度试验;
1)在阀杆行程从全开中间全关过程中,将气动调节信号每升高8KPa的阶跃信号,阀杆移动的位置不应超过全行程的1%,并保持位置稳定,阀位变送器的输出压力应与定位器调节信号的压力一致,其误差应在1%以内。
2)在阀杆行程从全关全开过程中,将气动调节信号每升高8KPa的阶跃信号,阀杆移动的位置不应超过全行程的1%,并保持位置稳定,阀位变送器的输出压力应与定位器调节信号的压力一致,其误差应在1%以内。
5.4.6.3、灵敏度试验;
除气动信号在最小(20KPa)和最大(100KPa)两点外,在全行程内每升高或降低1/400(既2KPa)的阶跃信号,阀杆应启动并移动全行程的1/400。
5.4.6.4、稳定性试验;
此试验前,用气动调节信号指挥,风动马达操作,将滑阀往复开动几次后再进行试验。
要求试验每次3个循环,试验5次,每次间隔时间为:
第1、2次连续试验,第2次与第3次试验间隔时间为2小时,第3次与第4次试验间隔时间为4小时,第4次与第5次试验间隔时间为24小时。
方法如下:
在全行程范围内分别施加0%、25%、50%、75%、100%五个点的信号,阀板每移动一档而达到停止位置时,所发生的衰减振荡不超过3次。
5.5技术指标要求:
校验后的气动调节风动滑阀技术指标必须保证:
1)灵敏度需达到1/400;
2)准确度需达到1/100;
3)具有良好的稳定性;
4)全行程时间应小于45秒;
5)其它各项指标应符合生产厂生产的技术指标要求;
6)保证的起动灵敏、全行程无迟滞、喘振等现象。
5.4.9注意事项:
1)所用气源必须符合要求;
2)喷雾润滑油面不低于1/3;
3)减速箱液面正常;
4)试验项目先后顺序正确。
5)带手动轮的校验时,一定要把调节阀打到自动位置再进行。
4)调节阀试验调整完毕,必须放净试验用水,并用空气吹干,然后,把阀门进出口封闭,置于室内或棚屋内保存。
对高压阀的密封面应加装特殊保护。
6.安全措施
6.1搬运仪器设备应小心轻放,防止摔坏仪器及砸伤人。
6.2仪表校验使用临时电源应加装漏电保护器。
6.3现场校验滑阀应注意周围环境,仪器摆放要稳固。
并严格执行校验方法步骤,防止风动马达损坏。
附此类阀校验记录表格见J603
SH3503-J603
调节阀、执行器、
开关阀调校记录
工程名称:
单元名称:
仪表名称
仪表型号
仪表位号
制造厂
精确度
出厂编号
行程
允许误差
输入信号
规格
PN=
DN=
di=
作用形式
标准表名称、
编号、精度
阀门定位器
型号
作用方向
气源
MPa
输入
输出
阀体强度试验
试验介质
试验压力
MPa
kPa
膜头气密性试验
试验介质
试验压力
MPa
kPa
阀芯、阀座
泄露量试验
试验介质
阀门出入口压差
MPa
实测值
ml/min
允许值
ml/min
全行程时间(S)
开阀
关阀
被校刻度
带阀门定位器
不带阀门定位器
0
50%
100%
0%
50%
100%
输入信号(mA)
标准行程(mm)
实测行程
(mm)
正
反
误差
(mm)
正
反
回差(mm)
调校结果
备注:
技术负责人:
质量检查员:
调校人:
年月日