生产运作管理笔记整理.docx
《生产运作管理笔记整理.docx》由会员分享,可在线阅读,更多相关《生产运作管理笔记整理.docx(32页珍藏版)》请在冰豆网上搜索。
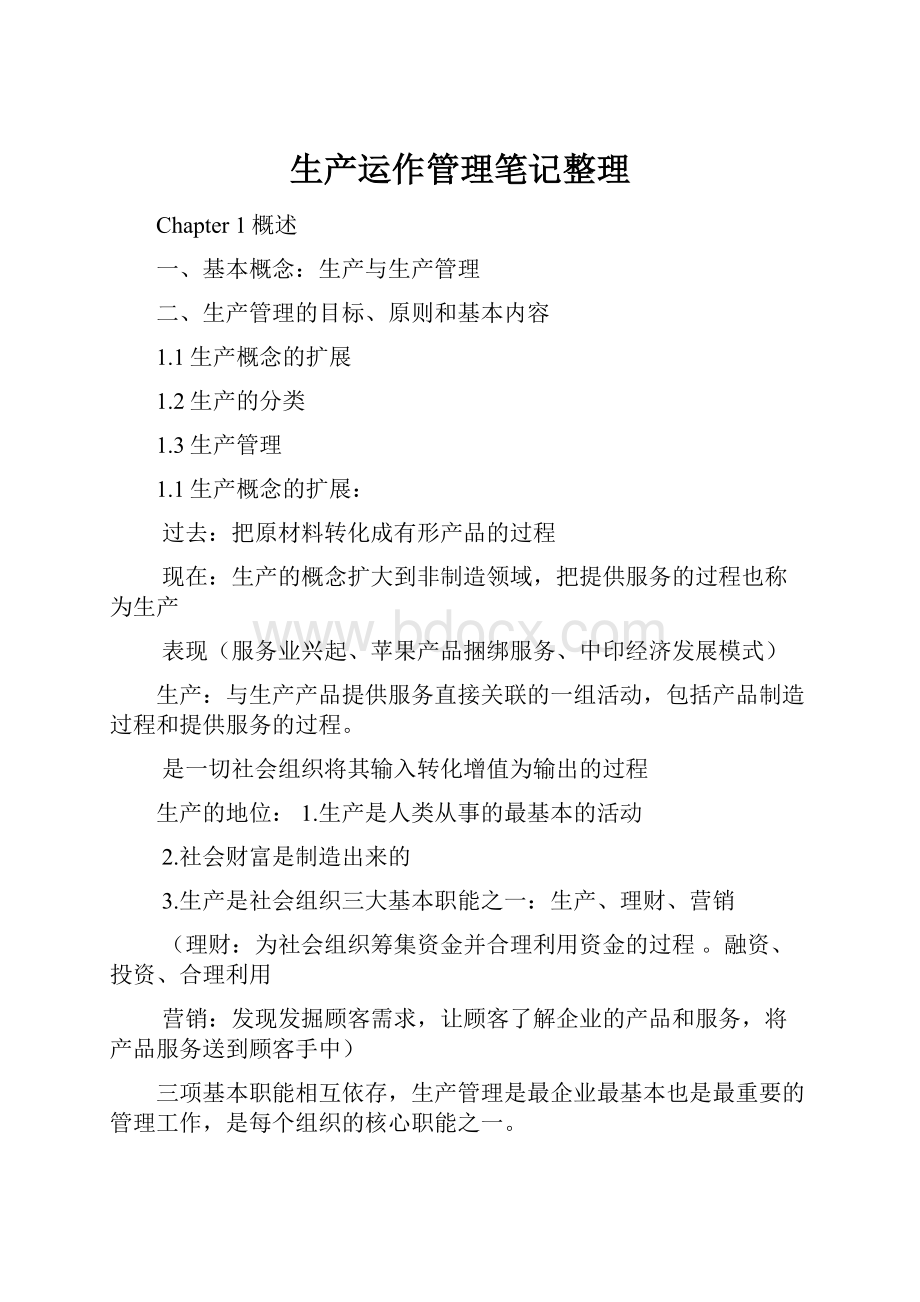
生产运作管理笔记整理
Chapter1概述
一、基本概念:
生产与生产管理
二、生产管理的目标、原则和基本内容
1.1生产概念的扩展
1.2生产的分类
1.3生产管理
1.1生产概念的扩展:
过去:
把原材料转化成有形产品的过程
现在:
生产的概念扩大到非制造领域,把提供服务的过程也称为生产
表现(服务业兴起、苹果产品捆绑服务、中印经济发展模式)
生产:
与生产产品提供服务直接关联的一组活动,包括产品制造过程和提供服务的过程。
是一切社会组织将其输入转化增值为输出的过程
生产的地位:
1.生产是人类从事的最基本的活动
2.社会财富是制造出来的
3.生产是社会组织三大基本职能之一:
生产、理财、营销
(理财:
为社会组织筹集资金并合理利用资金的过程。
融资、投资、合理利用
营销:
发现发掘顾客需求,让顾客了解企业的产品和服务,将产品服务送到顾客手中)
三项基本职能相互依存,生产管理是最企业最基本也是最重要的管理工作,是每个组织的核心职能之一。
社会组织其他职能:
会计、采购、公共关系、维修、人力资源管理、研究与开发。
。
。
生产系统:
人和设施构成的,达到生产目标的系统
狭义的生产系统:
企业内部的生产运作系统
广义的生产系统:
由合作企业组成的系统
1.2生产的分类
制造型生产:
按工艺过程特点:
流程式生产(工艺过程连续:
造纸、食品、冶金)特点
加工装配式生产(工艺过程离散:
计算机、汽车)特点
按满足需求的方式:
备货型生产MTS(家用电器)
订货型生产MTO(船舶、大型锅炉)
两者比较提前期
按生产的重复程度:
大量生产
成批生产
单件生产
特点比较
提高效率的方法:
减少零件变化:
推行三花:
产品系列化、零部件标准化、零部件通用化
提高生产系统的柔性:
数控机床、成组技术
服务型生产:
生产过程中存在客户投入的
针对已知客户需求量身定做的无形活动分类
Ps(任何组织提供的产品实际上都是产品+服务,只不过比例不同)
服务型生产与制造型生产的比较
1.3生产管理:
对生产所涉及的资源进行计划、组织和控制的过程
计划:
需求预测确定品种和产量设置交货期编制生产计划
编制物料需求计划编制生产作业计划人员班次安排统计生产进展
组织:
空间组织
时间组织
合理组织生产要素,充分利用资源
控制:
接受订货控制投料控制生产进度控制
库存控制成本控制
如何才能投入/产出max:
合理配置企业资源、高效管理业务流程、产品服务最大程度满足顾客需求
生产的三大决策:
生产什么、如何生产、用什么生产
OEM
ODM
OBM
附加值微笑曲线
二、生产管理的目标、原则和基本内容
生产管理三大功能:
产品开发((产品设计(需求系统结构)产品发展(项目成本工艺))
流程设计与管理(流程设计库存系统生产控制运作优化)
供应链管理(战略供应链设计供应链管理)
生产管理的目标:
高效、灵活、准时、清洁地生产合格产品或提供满意服务
竞争要素:
时间质量成本服务柔性
供需协调供需不匹配流程分析
生产运作管理课程的作用:
战胜低效率
找到运营平衡点
评估拟定的流程再造和新技术
Chapter2运作战略
运作战略的提出
运作战略的构造
运作战略的四个阶段
小结
运作战略:
一项长期规划,最有效利用企业关键资源,支持企业企业长期和总体竞争战略
一种总体决策模式,在市场需求和运作资源间协调
竞争战略:
企业在特定商务环境下,通过与众不同的竞争方式取得优势的竞争。
波特三大竞争战略:
全面成本领先战略(有效运营规模经济减少生产分销成本)
差异化(独特产品高质量新产品高端市场广告)
集中焦点(特定产品满足特定需求特定市场)
绩效目标:
成本:
生产制造劳动力原料能源机器管理物流存货
质量:
一致性、表现性、可靠性、耐用性、名牌(内部外部顾客满意度故障率)
交付期:
按时按量送达新产品推出频率
柔性:
对产品数量和种类改变的反应能力(新产品推出时间)
服务:
售前销售售后
环保
运营战略:
为运营决策指明远景及总体方向的蓝图。
它来源与公司战略,支持公司竞争战略
包括企业绩效目标和决策领域
运作战略的构造:
构建核心竞争力:
以顾客为中心的运作:
I=P(价格)-C(成本)
顾客价值V=功能F/成本C(质量、成本、交货期、柔性、服务)
以产品为中心的运作:
P=C+I
订单资格要素
订单赢得要素
运作战略的四个部分:
与之不同的能力客观的数字语言表述目标达到目标的指南策略选择
运作效力的四个阶段:
内部中立(纠正最差的问题,停止妨碍组织)
外部中立(采用最佳实践,与竞争者一样好)
内部支持(连接战略与运营,在行业中显然是最好的)
外部支持(提供一个运营优势重新定义行业期望值)
Chapter3生产管理需求预测
1.为什么要做需求预测
2.需求预测方法
3.预测误差与监控
对未来可能发生的事情的估计和预测
是运作管理的需要
意义:
为下一步计划做准备,是营销、生产、人力资源的基础
预测主要步骤
影响因素:
经济状况产品特征过去需求
计划的广告、价格折扣或营销策略竞争对手行动
需求预测衡量标准:
稳定性(反应稳定需求的能力)
响应性(反应变化需求的能力)
需求预测方法:
定量预测方法:
简单移动平均(时间
加权移动平均序列
一次指数平滑平滑)
时间序列分解模型(加法、乘法)
因果模型
定兴预测方法:
德尔菲法
部门主管集体讨论法
销售人员意见汇总法
顾客期望法
时间序列的构成:
趋势成分季节成分周期成分随机成分
预测误差与监控:
预测精度:
预测误差
平均绝对偏差
平均平方误差
平均预测误差
平均绝对百分误差
预测监控:
跟踪信号
Chapter4新产品开发
复合基础观:
普通资源的创造性复合使用,较少注重品牌
资源基础观:
占有有价值的核心资源,注重品牌
设计阶段成本决定因素高,实际成本占有少
新产品开发压力:
费用高
成功率低,风险大
时间长,回报下降
新产品开发过程:
现象:
1无潜在用户和需求
2不能满足需求或功能过剩
3沟通不够
新产品开发现象:
技术推动能生产出的产品
市场拉动能卖得出的产品
跨职能合作:
既生产得出又卖的出
并行工程:
串行设计特点“各部分缺乏沟通,开发周期长可制造性和可装配性差成本高
制造业环境变化:
产品生命周期缩短,交货期成为主要竞争因素,用户需求多样化
多品种小批量生产比例增大
并行设计要考虑的因素:
功能可制造性可装配性质量保证可靠性顾客满意环境保护
并行工程的主要内容:
过程重构
功能重构
构建技术支持环境
(三要素:
协作过程技术)
集成产品开发团队
过程管理
Chapter5流程能力与流程选择
流程概述流程能力流程选择
流程:
一组将输入转化为输出的相互关联联系的活动
六要素:
输入输出活动活动的相互作用顾客价值
企业流程:
经营流程管理流程业务流程
特点:
目的性动态性整体性层次性
业务流程:
一组跨职能部门的,与其他流程相辅相成的任务或活动逻辑序列
(举例、关键指标、订单业务流程)
竞争力基础:
生产能力:
企业的设施设备在一定时间内,在合理的技术组织下,能生产出的一定种类的最大数量。
但实际上,由于计划损失(维修,交接,转产),有效能力会低一些。
能力利用率=实际产出/设计能力
产品同质时用产出,不同质时用投入
能力利用率=实际所用时间/可用时间
能力效率=实际产出/有效能力
生产率:
产出/投入
单要素生产率(劳动生产率(数量/工时),机器生产率,资本生产率,能量生产率)
多要素生产率(产出(数量)/总成本(元))
总生产能力:
出发点:
客户需求
要素:
质量,成本,速度,柔性,服务,环保
瓶颈,面包生产
流程图符号
工序或任务检查
库存区或等待队列延迟
决策点物流、顾客留、信息流
工艺流程的分类:
线性流程:
大量生产,连续生产(高度标准化自动化,低成本低柔性)
间歇性流程:
成批生产
项目流程:
独特产品的生产
Chapter6选址与设施布置
选址:
影响选址因素:
投资,成本,劳动力市场原材料交通文化法律税收
选址内容:
选择地区选址地点评价决策
选址评价:
量本利分析法(固定成本和可变成本)
评分法(简单,最低门槛,加权)
线性规划法(运输问题不考)
选址的定量模型
例:
录像带制作选址
1.按大小排列,求x按x坐标大小排列
2.按顺序依次累加权数与坐标无关
3.得出最终值除于2为中间值
4.第一次超过中间值的权数对应的坐标值就是所求坐标
直角距离minisum选址问题
Minisum目标函数寻求整个设施选址的总和最小,目的是优化整体或平均性能。
被称为网络上的中值问题
Minimax目标由已存在设施的单个成本最大的组分组成,目标是优化最坏情况。
被称为网络上的中心问题
F=f1+f2
F1=∑w{x-c}
F2=∑w{y-c}
厂区平面布置:
运输短,灵活,有效的面积利用,工作环境,发展余地
物料运作图作业相关图(不考)
车间平面布置:
按一定原则,正确确定车间内部各组成单位及工作地,设备之间的相互位置。
生产组织形式:
工艺专业化:
机群式
对象专业化:
产品式,流水线式
成组单元布置
固定式布置
间歇式布置-工艺专业化
从至表试验法
作业相关图法和选址模型
仓库布置方法
线性规划法p161
计算机辅助布置(构建型,改进型n(n-1)/2)
从至表试验法:
1.把移动次数与移动成本对应相乘
2.把相互运输的两种设备成本相加
3.选择前n-1大的成本关联的设备
4.有n!
种可能,试算法计算
仓库布置:
线性布置:
流水生产
劳动对象按照一定的工艺路线,顺利通过各个工作地,并按统一的速度连续完成工序作业的生产过程
特点:
工艺流程封闭;工作地专业化程度高;生产具有明确的节奏;高度连续性
优点:
生产率高,周期短,成本低,质量高,便于管理
缺点:
人的创造性、单次投资大、缺乏柔性
装配线平衡
装配线是流水生产组织最为广泛的一种。
需要做到在确定节拍的情况下给工人分配工作。
平衡目的、原则
装配线平衡的步骤:
1.确定流水线的节拍r=计划有效工作时间/实际出产合格数量(大于工序最大,小于工序和)
2.计算最小工作地数Smin=[∑ti/r]把每一道工序时间相加除于节拍,向数值大方向取整
3.组织工作地数4.计算评价指标
三轮车工序练习
装配线的摆放
Chapter7年度生产计划
计划管理
生产能力
MTS企业年度生产计划的制定
计划管理:
计划是管理的首要职能
计划是组织的前提,是指挥的依据,是协调的工具,是控制的标准。
计划管理过程(PDCA):
制定计划执行计划检查计划完成情况改进
计划的层次:
长期计划:
战略层
中期计划:
战术层
短期计划:
作业层
年度生产计划:
是一个中期计划,处理的对象以产品级为主。
企业从三方面来制定综合计划:
产品族,劳动力,时间
计划期限的平衡:
1.有限的决策点数减少计划的复杂性
2,当需求预测出现季节性波动时,灵活调整生产率和劳动力水平。
年度生产计划的层次:
厂级生产计划:
产品级
车间生产计划:
零件级
班组生产计划:
工序级
生产计划指标体系:
产品品种、数量、质量、产值、出产期
制定生产计划的一般步骤:
确定目标
评估当前条件
预测未来的环境条件
确定计划方案
实施计划评价结果
生产能力:
企业的设施与设备,在一定时期内,在先进合理的技术组织条件下,所能生产一定种类产品的最大数量。
代表产品:
结构、工艺具有代表性,产量较大
假定产品:
实际上并不存在的产品,是为了结构与工艺差异大的产品有一个统一的计量途径
2.生产能力的计算
M=Fe*S/t计划期内单台有效工作时间*台数/产品台额
3.能力与负荷的平衡
目的:
衡量生产计划的可能性
工时平衡:
负荷=计划产量*单位产品台时定额与能力=设备年有效工作时数比较
3.MTS企业年度生产计划
制定程序:
确定每时期需求→每时期能力→确定库存策略
确定正常工作时间、加班时间,库存维持、缺货等成本方案进行成本计算
a处理非均匀需求的策略
1.改变库存水平(优:
将内部生产与外部需求隔开,维持内部生产均衡;
充分利用设备和人力;利于产品质量稳定;利于生产管理)
(缺:
库存大,占用资金多)
2.改变生产率(增减劳动人数,加班,临时工,转包外购)
(优:
市场适应性好;库存费用低)
(缺:
生产不均匀;不利于产品质量稳定;要经常调整设备和人力)
3.混合策略
B.产品生产进度的安排方法
均匀需求(全年计划平均分配或均匀递增分配)
非均匀需求(混合策略)
Chapter8库存分析与控制
库存的基本概念与分类库存分析与控制多周期库存模型单周期库存模型
库存:
暂时闲置的用于将来目的的资源
目的:
预防不确定性
为了生产和采购的的规模积极性
弥补需求或供应中遇到的变化
运输产生的库存
功能:
快速满足顾客需求,缩短交货期
稳定生产需求防止缺货
形成经济规模,防止价格上涨或者价格折扣
保证生产与运作的正常运行
弊端:
占用大量资金增加企业费用支出腐烂变质的损失掩盖了缺陷
库存分类:
库存形态库存形成方式:
周期库存安全库存在途库存
库存控制:
单周期&多周期(一次性订货(一年只订一次)和重复性订货)
确定型&随机型
独立需求&相关需求(独立性需求需要预测,相关需求可以精确预测)
ABC分类:
意大利经济学家帕累托提出,二八原则,重点管理法
通过对物料的分类,找出其中占用大量资金的少量物料加以重点管理和控制
(A类:
品种数占10%-20%资金占用75%-80%)
ABC分析方法:
数据统计作图分类
应用:
对A类项目:
经常预测估价、盘点
立即更新库存记录
经常审查需求量、订货量和安全库存
密切跟踪并催货,减少提前期
对B类项目:
类似A但要求不那么频繁
对C类项目:
计算机自动控制,简单维护库存记录和订货技术
较大的订货批量和安全库存
不需要经常清点,准确性要求较低
库存分析与控制:
目的:
防止超储和缺货,在合理成本范围内达到满意的服务水平
问题:
多久检查一次库存量
何时提出补充订货
每次订货量是多少
典型策略:
定量订货系统
定期订货系统
最大最小系统
1.定量订货系统
订货点和订货量固定不变,连续检查库存,当库存量下降到订货点时就发出订货,每次按相同的订货量Q来补充库存,A类物资可采用此法控制
2.定期订货系统
按预先确定的周期检查库存水平并随后提出订货,将库存补充到预定的目标水平
3.最大最小系统
按预先确定的周期检查库存水平,当订货量小于最小库存水平时提出订货,大于最大库存水平时,不提出订货。
多周期库存模型
1.与库存有关的费用分析(随库存增加而增加的费用,减少的费用,年库存总费用)
2.经济订货批量:
订货批量是消耗一次订货费用采购某种产品的数量
经济订货批量是按照库存总费用最小的原则确定出的订货批量
经济订货批量模型:
年维持费用:
1/2*Q*H
年订货费用:
(D/Q)*S
年总费用:
1/2Q*C*h+(D/Q)*S+C*D
当1/2QH=(D/Q)*S时为最优订货批量
Q²=2DS/HEOQ=。
。
。
订货点:
D/一年*提前期
经济生产批量EPQ
年总费用:
CD+1/2QCh+D/Q*S
最优解Q*=EPQ:
根号2DSp/(p-r)H
一定要记住*2
报童问题:
易变质产品的库存控制问题
机会成本
超储成本
期望损失最小法
期望损失=机会成本*缺货数*缺货概率+超储成本*库存数*库存成本
期望利润最大法
期望利润=你懂得-。
-
边际分析法:
如果增加一个产品订货能使期望收益大于期望成本,那么就应该在原订货量的基础上追加一个产品的订货。
P(D*)累计概率分布函数P(D)需求量大于D的概率
Cu做乘子正累加(机会成本)
Co倒累加(超储成本)
Prob[Y>=D*]:
Co/Co+Cu后查标准正态分布求z
D*=均值+标准差*z
机票
Chapter9制造资源计划
MRP的产生与发展
MRP的处理过程
1.MRP的产生与发展
订货点法的缺陷MRP的产生与基本思想
MRP和订货点系统的比较
订货点法的缺陷:
:
订货点订货期量
(只适合需求比较稳定的物料,实际中需求不均匀,一要要一批)
需求预测-盲目性(不得不保持较大的安全库存)
高库存与低服务水平-需要的没有,不需要的太多
形成块状需求:
平均库存水平高,占用资金
这些缺陷都是因为它没有按照各种物料真正需用的时间来确定订货日期
MRP的诞生:
物料需求计划,最早由美国IBM公司oelicky博士设计
主要思想:
打破产品品种台套之间界限,把企业生产过程中涉及的所有产品在逻辑上视为相同物料。
把所有物料分成独立需求和相关需求。
根据产品需求时间和数量进行展开,按时段确定不同时段各种物料的需求。
围绕物料转化组织制造资源,实时按需要准时生产
以物料为中心组织生产
MRP处理的是相关需求
将产品制造过程看作是从成品到原材料的一系列订货过程
MRP提出了解决物料转化过程中的关键问题:
何时需要需要什么需要多少
它不仅在数量上解决了缺料问题,更关键的是从时间上解决了缺料问题
MRP的发展阶段:
1.MRP-物料需求计算器(开环,没有反馈)
2.闭环MRP(能力需求计划,信息反馈,计划调整)
3.MRPⅡ(加财务)
4.ERP(供应链,现代信息技术,流程式制造业)
MRP的处理过程:
准备MRP处理所需的各种输入,将MPS作为确认的生产订单下达传给MRP
根据产品的BOM,从第0层项目起,逐层处理各个项目直至最低层
输入:
主生产计划MPS
(确定需求,计算净需求,确定MPS量,计算待分配量,MPS的滚动)
物料清单BOM(产品结构文件,表示了产品的组成和结构信息)
物料分为自制项目和采购项目
库存状态文件
常用的批量策略:
逐批确定法
固定批量
*最大零件周期收益(MPG)
输出信息:
主报告:
关于生产和库存的计划与控制的报告
二级报告:
业绩控制,例外情况等
系统更新:
信息变化:
MPS的滚动,其他关于物流,设备,人员等的变动信息
再生系统:
定期集中更新生成计划
净变系统:
随时修正计划
Chapter10作业计划与控制
基本概念
两台机器的排序问题
相同零件不同移动方式下加工周期的计算
排序:
将不同工作任务安排一个执行顺序,使预定目标最优化
工件:
服务对象
机器:
服务者
作业计划:
除排序外还要确定开工完工时间
流水车间排序问题的基本特征:
每个工件的加工路线都一样,加工顺序也一样
单间车间排序问题特征:
每个工件加工路线独特,工件没有一定的流向
表示方法:
n(工件数)/m(机器数)/A(车间类型)/B(目标函数)
两台机器的排序问题
~含义:
n个工件都必须经过机器1,机器2的加工,工艺路线是一致的
~最长流程时间
~n/2/F/Fmax问题的算法:
Johnson算法:
最短时间出现在M1上,往前排,
最短时间出现在M2上,往后排
相同零件,不同移动方式下加工周期的计算
包括:
顺序移动方式:
一批零件在上道工序全部加工完毕后才整批转移到下道工序继续加工。
优:
设备利用率高,移动次数少缺:
加工周期长T=n∑ti(常用于单件或成批生产过程)
平行移动方式:
每个零件前道工序完成后立即转移到下道工序T=∑ti+(n-1)t1
优:
加工周期短缺:
设备利用率低;移动次数多(常用于装配流水线,大量生产)
平行顺序移动方式:
要求:
每道工序连续进行加工
各道工序尽可能平行加工
T=n∑ti-(n-1)∑min{tj,tj+1}
Chapter11精益生产与流程重构
无库存生产方式的实质准时生产制组织无库存生产的方法
无库存生产方式的实质
1.不断消除浪费,进行永无休止的改进
2.它是一种理想的生产方式
3.它是一种综合的管理技术
准时生产制
JIT的基本概念:
日本丰田公司在50年代初提出
基本思想:
严格按用户需求生产产品
按必要的时间、数量,生产必要的产品
数量上不多不少,时间上不早不晚
生产方式特征:
后工序提取零部件
小批量生产、传送
用最后的装配工序来调整平衡全部生产
推进式系统和牵引式系统
推进式系统:
有一个集中的计划与控制系统,各车间、各工作地按计划生产,并将加工完的零部件送到后续工序。
(如MRP)难以做到准时生产
牵引式系统:
从产品装配出发,每个车间,每道工序按照当时需求向前一工序提出要求,以此来驱动生产。
(产品装配-提取零部件-补充零部件)可以实现准时生产。
看板系统:
实现准时生产的一种工具。
又称传票卡,起传递信息的作用,分为
移动看板:
在前后两道工序间移动,用于提取零件
生产看板:
用于指挥工作地的生产,它规定要生产的零件和数量,在工作地和出口处往返。
组织无库存生产的条件(牵引式生产系统+看板管理方式)
1.计划平准化:
生产率=市场需求率
生产频率:
单位时间内进行同一产品生产的次数
2.减少调整准备时间(尽可能在机器运行时进行调整准备,人员培训,设备改造)
3.建立无库存的制造单元(把库房搬进厂房,设备重新排序,U形布置)
4.准时采购(消除采购过程的浪费,供应厂家的质量,五因素)
5.从根源上保证质量(减少废品,事前预防,全面质量管理,设备预防性维修)
6.设计易生产、易装配的产品(模块化设计,通用件,标准件,生产自动化)
Chapter12工程项目计划与进度控制
工程项目管理的目标、内容和方法
网络图
网络时间参数的计算
工程项目:
在规定时间内,由专门组织起来的人员共同完成的、有明确目标的一次性工作。
(单件生产)
项目管理:
对工程项目进行计划、组织和控制。
目标:
质量成本进度
内容:
立项建设运行
方法:
甘特图网络计划技术
网络计划技术步骤:
1.项目分解
2.确定各种活动之间相互关系
3.估计活动所需时间
4.绘制网络图
5.计算网络参数,确定关键路线
6.网络优化
7.监控
8.调整
网络图:
由结点和箭线组成,用于表示工程项目的作业构成及其相互关系
箭线型网络图:
双代号网络图,箭线表作业
结点型网络图:
单代号网络图,结点表作业
一些练习和注意事项
网络时间参数的计算
作业时间:
在一定的技术组织条件下,为完成一项作业所需的时间
单一时间估计法:
有同类作业的时间参考资料
三种时间估计法:
最乐观时间a最可能时间m最悲观时间b
平均时间:
t=(a+4m+b)/6
方差:
α^2=[(b-a)/6]^2
节点时间参数计算:
规则和练习
作业时差