车间现状改善及设施布局设计重点讲义资料.docx
《车间现状改善及设施布局设计重点讲义资料.docx》由会员分享,可在线阅读,更多相关《车间现状改善及设施布局设计重点讲义资料.docx(27页珍藏版)》请在冰豆网上搜索。
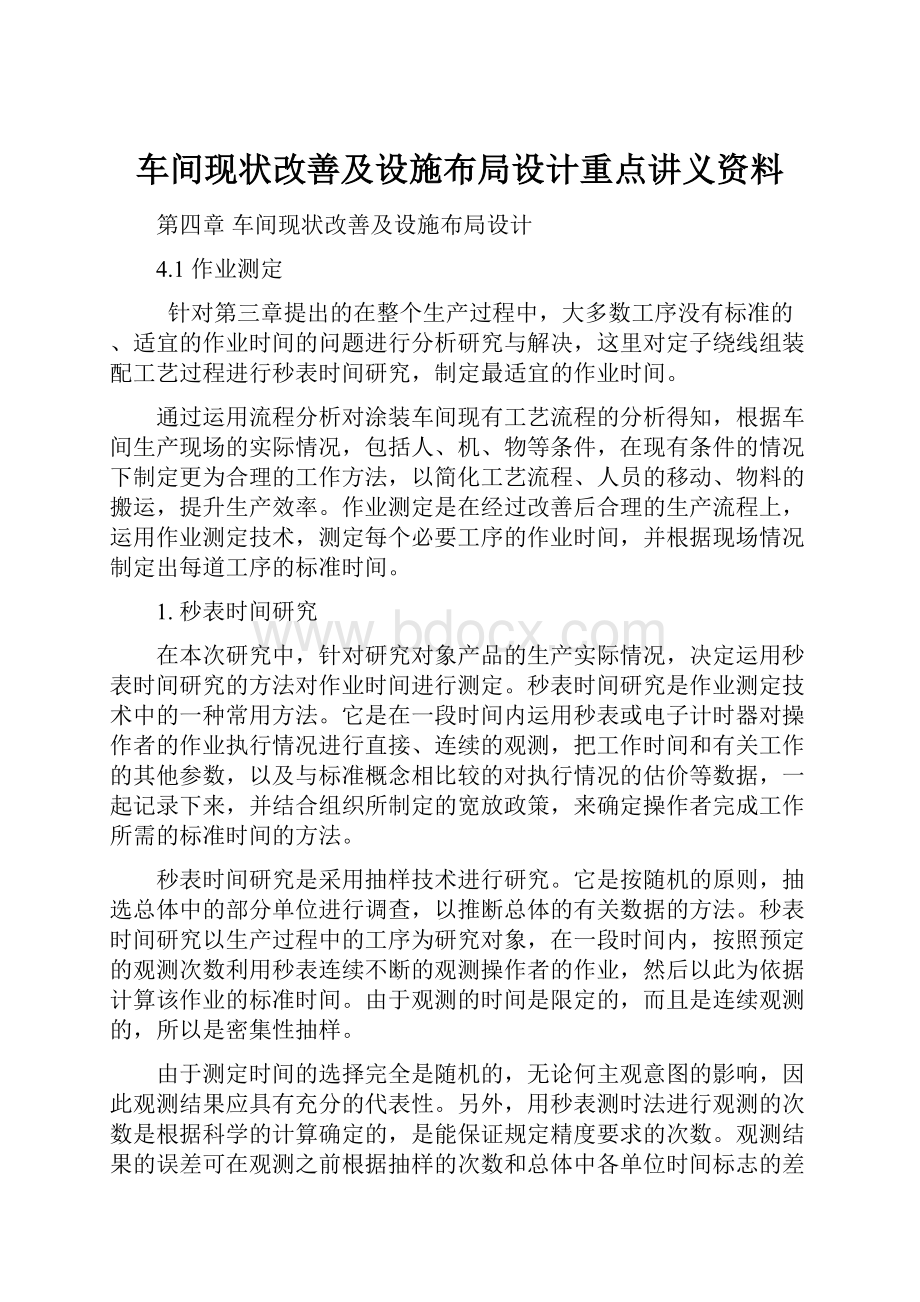
车间现状改善及设施布局设计重点讲义资料
第四章车间现状改善及设施布局设计
4.1作业测定
针对第三章提出的在整个生产过程中,大多数工序没有标准的、适宜的作业时间的问题进行分析研究与解决,这里对定子绕线组装配工艺过程进行秒表时间研究,制定最适宜的作业时间。
通过运用流程分析对涂装车间现有工艺流程的分析得知,根据车间生产现场的实际情况,包括人、机、物等条件,在现有条件的情况下制定更为合理的工作方法,以简化工艺流程、人员的移动、物料的搬运,提升生产效率。
作业测定是在经过改善后合理的生产流程上,运用作业测定技术,测定每个必要工序的作业时间,并根据现场情况制定出每道工序的标准时间。
1.秒表时间研究
在本次研究中,针对研究对象产品的生产实际情况,决定运用秒表时间研究的方法对作业时间进行测定。
秒表时间研究是作业测定技术中的一种常用方法。
它是在一段时间内运用秒表或电子计时器对操作者的作业执行情况进行直接、连续的观测,把工作时间和有关工作的其他参数,以及与标准概念相比较的对执行情况的估价等数据,一起记录下来,并结合组织所制定的宽放政策,来确定操作者完成工作所需的标准时间的方法。
秒表时间研究是采用抽样技术进行研究。
它是按随机的原则,抽选总体中的部分单位进行调查,以推断总体的有关数据的方法。
秒表时间研究以生产过程中的工序为研究对象,在一段时间内,按照预定的观测次数利用秒表连续不断的观测操作者的作业,然后以此为依据计算该作业的标准时间。
由于观测的时间是限定的,而且是连续观测的,所以是密集性抽样。
由于测定时间的选择完全是随机的,无论何主观意图的影响,因此观测结果应具有充分的代表性。
另外,用秒表测时法进行观测的次数是根据科学的计算确定的,是能保证规定精度要求的次数。
观测结果的误差可在观测之前根据抽样的次数和总体中各单位时间标志的差异程度,事先通过计算,将其控制在一定范围之内,因此计算结果比较可靠。
使用秒表时间研究方法进行时间研究时必须具有以下工具:
(1)秒表
(2)记录板
(3)时间研究表格
(4)计算器、测量工具、摄影、录像设备或计时机等
近年来发展的各种数据收集站,将数据的采集,汇总与打印的功能结合在一起,可自动安排采样过程。
收集数据时只需按有关的键即可在屏幕上自动显示,有编辑功能与统计汇总功能,并将数据传输到其他计算机上,这就大大提高了时间研究的精度与效率。
2.秒表时间研究的过程
(1)、确定观测次数
秒表时间研究是一个抽样观测的过程,为了得到科学的时间标准,需要有足够的样本容量。
样本愈大,得到的结果愈准确。
但样本过大,时间和精力大量耗费,也是不必要的。
因此科学地确定观测次数,尤为重要。
一般的说,作业比较稳定、观测人员训练有素、经验丰富、被观测对象较多,则观测次数可少些,否则观测次数就要多些。
在选择观测次数时,精度与费用之间呈相反变化趋势,要在二者之间做出最优的决策。
一般情况下,采用误差界限法确定观测的次数。
该法是基于假定所有观测时间值的变化均属于正常波动,实用上可视观测值呈正态分布,在异常值已经剔除后,仍有相当的观测值样本数。
设
是样本数为n时样本均值的标准差(平均数的标准误),
为总体标准差,则:
(3-1)
要计算平均数的标准误,需知道总体标准差(
)的值。
实际工作中一般得不到这个数值,因而必须对它进行估计。
一般就以样木的标准差(S)代替总体标准差(
),当样本足够大时,可用式(3-2)计算:
(3-2)
当样本容量为
(保证一定精度要求时应观测的次数)时,样本均值的标准差
为:
(3-3)
此时,时间研究人员应决定置信水准(或可靠度)及精准度(误差界限),一般取可靠度为95%,精确度为5%(样本均值与总体均值之间的误差范围控制在±5%以内),则:
(3-4)
式中。
0.05为精确度。
将式(3-3)代入式(3-4)式得:
则:
(3-5)
当样本数量较少时,可改用下式:
(3-6)
同理根据不同情况的误差控制范围,都可运用上述式子计算出应观测的次数。
为了工作改善而进行时间研究,可根据作业周期确定观测次数,具体见表4-4所示。
表4-4观测次数确定标准
作业周期/min
0.1
0.25
0.5
0.75
1.0
2.0
5.0
10.0
20.0
40.0
40.0以上
观测次数
200
100
60
40
30
20
15
10
8
5
3
由上表和原始测时表可知,电机定子绕线组装配工艺的观测次数为10次。
(2)、测时
在车间测得秒表时间研究作业(1.绕线2.下线3.成形并绝缘包扎4.嵌线5.接线6.去毛刺整形7.定子圧形)的时间如下表所示:
测时
次数
绕线
下线
成形并绝缘包扎
嵌线
接线
去毛刺整形
定子圧形
1
12.15
12.13
11.31
44.3
15.5
12.5
15.0
2
12.17
12.17
11.53
44.1
15.5
12.6
15.3
3
12.14
12.13
11.22
44.2
15.4
12.4
15.3
4
12.19
12.12
11.43
44.3
15.6
12.5
15.5
5
12.10
12.13
11.23
44.1
15.3
12.6
15.4
6
12.25
12.12
11.32
44.5
15.4
12.4
15.4
7
12.16
12.15
11.37
44.2
15.5
12.5
15.5
8
12.15
12.14
11.35
43.8
15.5
12.3
15.5
9
12.14
12.12
11.31
44.3
15.5
12.5
15.3
10
12.16
12.13
11.41
44.2
15.3
12.4
15.7
∑
121.61
121.34
113.48
443
154.5
124.7
153.9
12.16
12.13
11.34
44.3
15.45
12.47
15.39
(3)剔除异常值并计算各单元实际操作时间
剔除异常值
假设对某一操作单元观测n次所得时间为∑则均值为:
标准偏差为:
正常值为
之内的数值,超过者即为异常值。
偏差上限为
,偏差下限为
,在上限与下限之间均视为正常值,凡不在这个区域内的数值即为异常值,应予以剔除。
根据正态分布的原理,在正常情况下,若计算同一分布的抽样数值,其99.7%的数据应在均值正负三倍标准偏差区域内。
以绕线工序为例,共有十组数据,如表4-5所示,
=12.16
由
可求得
0.04
偏差上限UCL=
=12.28,偏差下限LCL=
=12.04,十组数据全部符合要求;
同理可得,
下线工序
0.015,UCL=12.18,LCL=12.09,十组数据全部符合要求;
成形并绝缘包扎工序
0.09,UCL=11.64.LCL=11.06,十组数据全部符合要求;
嵌线工序
0.17,UCL=44.54,LCL=43.86,十组数据全部符合要求;
接线工序
0.09,UCL=15.72,LCL=15.18,十组数据全部符合要求;
去毛刺整形工序
0.09,UCL=12.73,LCL=12.20,十组数据全部符合要求;
定子圧形工序
0.18,UCL=15.93,LCL=14.85,十组数据全部符合要求。
计算各单位的实际操作时间
异常值提出后,运用剩余的合格数据分别求个单元观测时间的算数平均值,即为该单元的实际操作时间。
由于各个工序所测得的时间都符合要求,故实际操作时间如上表求得的算数平均值。
(4)计算正常时间
正常时间是指以正常速度完成一项作业或操作单元所需的时间,不能直接将上述时间认为是操作者以正常速度操作所需的时间,必须对操作者的作业进行评定,并以此对观测时间进行修正,使操作所需的时间变为不快不慢的正常时间。
为了更好的进行作业评定,尽量减少研究人员的主观影响,通常采用评定方法进行评定。
平准化法是应用最广泛的方法。
由罗莱、曼纳特和斯太基门德等人在西屋法基础上进行改进,发展为平准化评定系统。
此法将熟练、努力、工作环境、一致性四个因素作为衡量工作的主要评定因素,每个因素又分为超佳、优、良、平均、可、欠佳六个高低程度的等级。
称为熟练系数、努力系数、工作环境系数、一致性系数、表3-6即为评定因素及等级。
表4-5评定因素及等级
1 熟练系数
2 努力系数
超佳
A1
+0.15
超佳
A1
+0.13
A2
+0.13
A2
+0.12
优
B1
+0.11
优
B1
+0.10
B2
+0.08
B2
+0.08
良
C1
+0.06
良
C1
+0.05
C2
+0.03
C2
+0.02
平均
D
0.00
平均
D
0.00
可
E1
-0.05
可
E1
-0.04
E2
-0.10
E2
-0.08
欠佳
F1
-0.16
欠佳
F1
-0.12
F2
-0.22
F2
-0.17
3 工作环境系数
4 一致性系数
理想
A
+0.06
理想
A
+0.04
优
B
+0.04
优
B
+0.03
良
C
+0.02
良
C
+0.01
平均
D
0.00
平均
D
0.00
可
E
-0.03
可
E
-0.02
欠佳
F
-0.07
欠佳
F
-0.04
运用平准化法进行作业测定,其评定的系数的计算为:
评定系数=1+熟练系数+努力系数+工作环境系数+一致性系数
每个工序的评定系数如下表所示。
表4-6评定系数统计表
工序号
工序名称
熟悉系数
努力系数
工作环境系数
一致性系数
评定系数
1
绕线
0.08
0.03
0.02
0.01
1.14
2
下线
0.06
0.05
0.02
0.01
1.14
3
成形并绝缘包扎
0.06
0.05
0.02
0.01
1.14
4
嵌线
0.06
0.02
-0.03
-0.02
1.03
5
接线
-0.05
0.05
0.02
0.03
1.10
6
去毛刺整形
0.03
0.08
0
0.01
1.12
7
定子圧形
0.06
0.02
0.02
0.01
1.11
正常时间=观测时间*评定系数
表4-7工序正常时间
正常时间
绕线
下线
成形并绝缘包扎
嵌线
接线
去毛刺整形
定子圧形
T/min
13.86
13.83
12.94
45.53
17.00
13.97
17.08
(5)确定宽放时间及标准时间
正常时间并未考虑操作者个人需要和各种不可避免的延迟因素所耽误的时间。
根据前文分析以及现场调查得出,此处宽放率为14%,其中私事宽5%,疲劳宽放4%,延迟宽放3%,政策宽放2%。
标准时间=正常时间+宽放时间=正常时间*(1+宽放率)
过以上参数的计算,将标准时间录入表4-7中的工时统计表中。
表4-8工时统计表
工序号
工序
人力(人)
产出单位(台)
测量工时(min)
评比系数
宽放率
标准工时
(min)
1
绕线
2
1
12.15
1.14
15%
15.94
2
下线
2
1
12.12
1.16
15%
15.91
3
成形并绝缘包扎
1
1
11.33
1.14
15%
14.87
4
嵌线
2
1
44.07
1.03
15%
52.19
5
接线
2
1
15.49
0.02
15%
19.54
6
去毛刺整形
1
1
12.56
1.12
15%
16.06
7
定子圧形
1
1
15.40
1.11
15%
19.65
4.2生产线生产现状的改善
这里将对第三章提出的生产线的工艺流程不够完善的问题行一下分析改进:
1.根据找出最经济的移动方法和减少搬运次数的基本原则对转子的焊接到精车的搬运过程进行改善。
将精车区的位置与精磨区的位置交换,交换后,焊接区距机加工区即精车工序的距离大大缩短,减少了搬运的距离,电机移动找到了经济的方法。
另外,由于搬运距离缩短,并且焊接的过程需要等待,因此,搬运工作可取消专门的搬运工人,改由精车的工人来完成,以提高工作效率,降低成本。
2.根据尽可能取消不必要的工序和安排最佳的顺序两项基本原则对转子精车后的光滑度以及后续精磨和精铣工序的过程进行分析改善。
由于95%的精车后的电机光滑度检验都不能一次性达到标准的要求,需要运回机加工区再继续进行精磨和精铣的工序后再进行第二次的光滑度检验,才能符合要求。
因此,可将第一次的光滑度检验工序取消,直接进行精磨和精铣的工序,然后再运到检验区进行光滑度检验。
这样不仅不会降低电机光滑度符合标准的合格率,同时还可以减少2次不必要的搬运过程和一次重复性的检验过程。
另外,由于减少了2次搬运,也会相应的减少搬运的员工人数和其他员工的劳动负荷,降低了产品的成本也能提高产品的质量。
3.根据使各工序尽可能经济化的原则,对喷漆和上铭牌两道工序进行必要的改善。
由于等待一组喷漆电机干透后才能进行上铭牌的工序,并且,每组喷漆等待漆干的时间较长,大约需要60—80分钟时间。
在这段等待的期问,喷漆和上铭牌两组工人都将处于等待,除去喷漆和上铭牌的工作时间外,单纯等待时间大约每组30分钟。
造成了时间上和人员上浪费,因此,将其中一组员工取消,只保留一组。
在喷漆后等待的时间里,就可以由这同一组员工完成下面的上铭牌的工作,从而大大提高了劳动效率。
通过以上几个方面的分析改进,减少了整个生产过程的操作步骤,节约了车间的空间,缩短了搬运距离,改进后的车间布局及搬运路线图如图4-1所示。
图4-1改进后车间路线图
改进后的工艺流程是:
拿起压装转子—至压装操作台—穿铜条—储存至十个—运至焊接区—焊接—等待—运至机加工区—精车—精铣—精磨—运至检验区—检验光滑度—运至储存区—储存—等待—运至装配区—装配—运至喷漆区—喷漆—上铭牌。
改善后的工艺程序图如下图4-2所示。
图4-2改善后转子工艺程序图
图4-3为改善前后转子装配工艺流程比较图,从中可以看出改善效果的效果。
(1)改善后转子装配程序由原来的27个主要流程减少为改善后的21个流程。
(2)改善后的转子装配过程中的搬运过程由改善前的12次搬运减少为改善后的7次,总路线同时得到缩减。
(3)改善前的等待过程由原来的3次减少为改善后的2次,缩短了单个产品的生产周期。
通过以上的分析改进,转子的装配过程有了明显的改善,其装配工序降低了6个工序,更明显的是,其搬运路线得到了很大的缩减,使得在搬运过程中的时间减少,并且路线的减少使得整个车间的布局有了很大的改善,从而使整个电机的生产成本大大降低了,效率有了明显的提高。
图4-3改善前后转子装配的工艺流程图
4.2车间现存问题的改善
4.2.1精车转子工序的人-机作业分析
1.针对第三章提出的车间内人机作业普遍不合理的现象,这里利用人机作业的方法对精车转子工序进行人员数及机器数的重新分配和改善
选定转子的精加工这一工序过程进行人机作业分析,该工序多为两人一机、三人一机的配置,这里以两人一机的情况进行分析改进。
通过仔细的观察和记录,其作业时间如下表4-1所示:
4-1人-机作业时间表
序号
动作分解
测量时间(s)
评比
放宽率
工时(s)
人
机
1
取未加工的转子
5
1.00
1.08
5.4
2
用夹具加好
12
1.00
1.08
12.96
3
测量转子的尺寸
10
1.00
1.08
10.8
4
精车转子
48
1.00
1.08
51.84
5
再次测量转子的尺寸
15
1.00
1.08
16.2
6
取下转子
14
1.00
1.08
15.12
7
摆放好卸下的转子
8
1.00
1.08
8.64
总计(s)
120.96
69.12
51.84
根据现有两人操作一台设备的作业方式,以人——机作业图来研究工作人员及设备的利用率。
从表4-1中可以看出,作业人员的利用率只有28.54%,而空闲时间比率却达71.46%,显然作业人员的利用率很低,人员在作业过程中有过多的等待时间,其人-机作业分析图如图4-4所示。
4-4精车转子现行人-机作业分析图
作业名称:
精加工
机器名称:
车床
操作者:
研究者:
方法:
现行方法
机器号码:
日期:
人
车床
操作
时间
操作
时间
取未加工的转子
5
空闲
5
用夹具夹好
12
空闲
12
测量转子的尺寸
10
空闲
10
空闲
48
精车转子
48
再次测量转子的尺寸
15
空闲
15
取下轴
14
空闲
14
摆放好卸下的转子
8
空闲
8
代表空闲代表工作时间单位:
秒
统计
工人
机器
空闲时间
48
74
工作时间
74
48
周程
122
122
利用率
30.32%
69.68%
2.精车转子的问题的分析
由图中可见,工作中车床2/3的时间没有工作,这是由于当工人操作时,机床处于停止工作的状态;机床工作时工人则无事可做。
工人将工件夹紧在机床台面上和加工后松开夹具、取下零件是必须在机床停止时才能进行的,但加工前后的测量可以在机床工作过程中同时进行。
因此要缩短工作周期,应尽量利用机器工作的时间进行手工操作。
这意味着工作人员在其空闲时间内可以再操作一台车床。
于是可以增加一台机床由一名工作人员操作,另一名工作人员专门负责检查的工作,这样就变成了一个工作人员操作两台机器。
改进后,精车转子的人机作业分析图如下图4-5所示。
4-5精车转子改良后人-机作业分析图
作业名称:
精加工
机器名称:
车床
操作者:
研究者:
方法:
现行方法
机器号码:
日期:
工作人员
车床1
车床2
内容说明
时间/s
状态
内容说明
时间/s
状态
内容说明
时间/s
状态
取未加工的转子
5
空闲
5
精车转子
19
将转子装到车床1
12
装未加工的转子
14
开动车床1
2
关闭车床2
2
精车转子
48
卸下加工好的转子
16
卸下加工好的转子
14
摆放好卸下的转子
8
空闲
13
取未加工的转子
5
将装转子到车床2
12
装未加工的转子
12
开动车床2
2
空闲
5
精车转子
29
关闭车床1
2
卸下加工好的转子
16
卸下加工好的转子
14
摆放好卸下的转子
8
空闲
8
统计
工作人员
空闲时间:
5s操作时间:
86s周程时间:
91利用率:
94.51%
车床1
空闲时间:
13s操作时间:
86s周程时间:
91利用率:
94.51%
车床2
空闲时间:
13s操作时间:
86s周程时间:
91利用率:
94.51%
3.对精车转子进行人机作业分析后的改进结果
通过上面的分析改进(见图4-5),整个精车加工转子的周程时间由原来的122s提高到了91s,提高了31s,使得整个生产周期有了很大的降低,虽然工作人员的工作时间由原来的74s变为86s,但其空闲时间却降低到了5s,是原来工作人员空闲时间的9倍,时间利用率由原来的28.54%变为现在的为94.51%,时间利用率有了很大的提高;其次,车床1和车床2的工作时间都是86s,空闲时间都是5s,工作效率都是94.51%。
工作人员的时间利用率提高了近3倍,即在相同的时间内精车转子的数量是原来的3倍,这样就大大降低了生产成本,提高了其生产效率,生产效率提高了将近33%。
4.2.2定子下线及接线工序的双手作业分析
针对第三章提出的作业人员的双手负荷不平衡的问题,这里通过方法研究中的双手作业分析的方法,对定子下线及接线的工序进行分析与改善,使作业人员的双手负荷趋于平衡,以减轻工作人员的疲劳状况和提高双手的作业效率。
1.下线工序的双手作业分析
(1)工序现状
记录现行方法下线的双手作业过程如图4-6所示。
由图可知,双手负荷不平衡,左手大部分时间处于空闲状态,右手的工作量明显大于左手。
图4-6下线工序现行双手作业图
工作:
下线
开始:
双手空闲
结束:
完成下线工作
左手操作
右手操作
内容描述
操作符号
操作符号
内容描述
等待
■
■
移至铜线
等待
■
■
拿起铜线
等待
■
■
移至工作台
等待
■
■
移至绝缘纸
等待
■
■
拿起绝缘纸
等待
■
■
移至工作台
持住
■
■
用绝缘纸将铜丝包好
等待
■
■
至固定条
等待
■
■
拿起固定条
等待
■
■
至工作台
放入固定条
■
■
持住
等待
■
■
至铁盒
等待
■
■
拿起铁盒
等待
■
■
至工作台
放入盒中
■
■
持住
等待
■
■
取出固定条
等待
■
■
调整位置
总计
2
1
14
7
8
2
(2)双手作业的分析
通过对下线工序的进一步分析后,可以发现工作人员的双手操作比较随意,左手80%的时间基本上处于空闲状态,而其右手却一直处于工作状态。
通过分析后可以发现,右手主要负责拿铜条、绝缘纸和固定条等至工作台和包装铜条、取出固定条的工作,如果在右手拿取铜条的同时左手去拿绝缘纸