论文PCB质量管理及主要品质缺陷分析.docx
《论文PCB质量管理及主要品质缺陷分析.docx》由会员分享,可在线阅读,更多相关《论文PCB质量管理及主要品质缺陷分析.docx(12页珍藏版)》请在冰豆网上搜索。
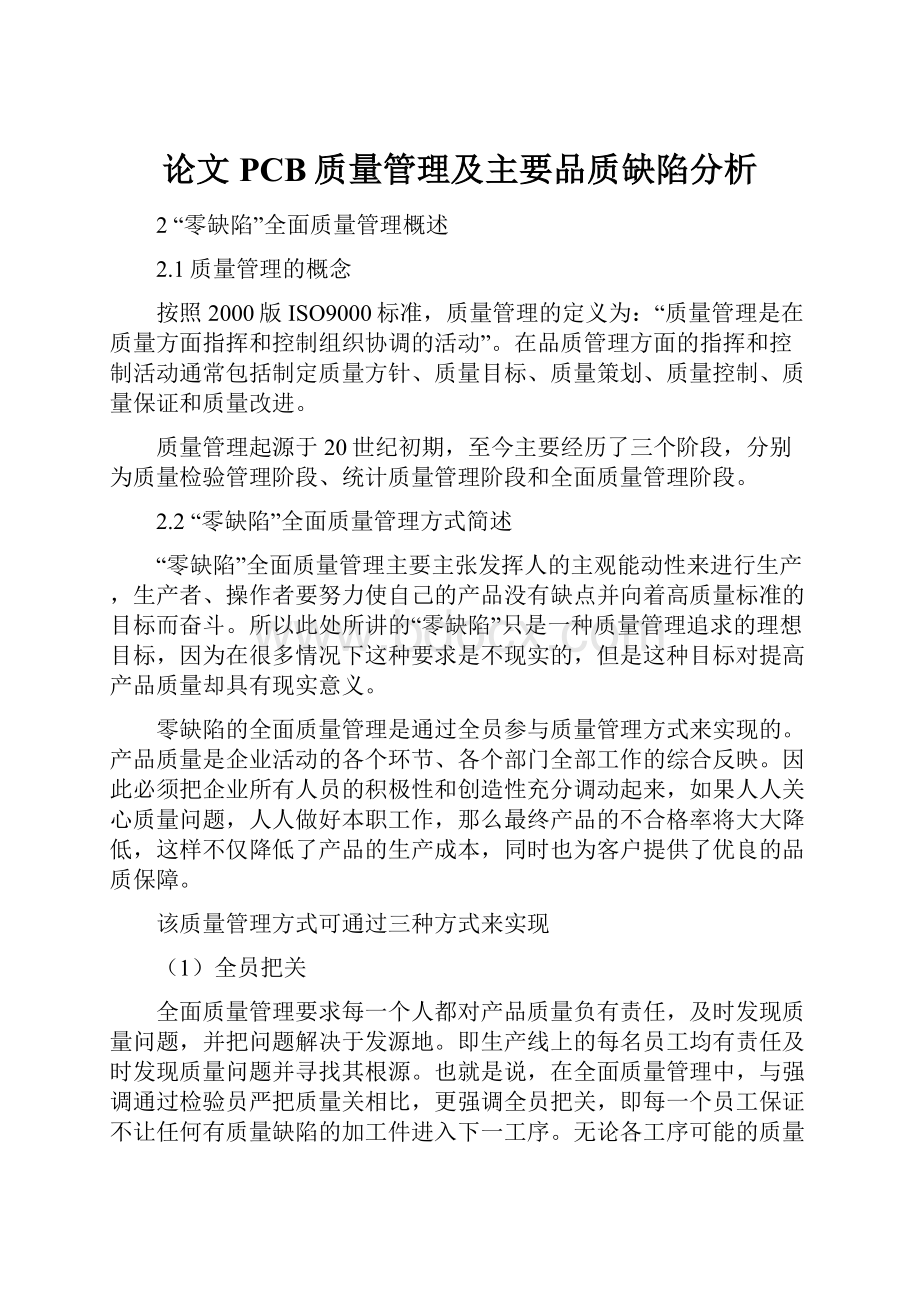
论文PCB质量管理及主要品质缺陷分析
2“零缺陷”全面质量管理概述
2.1质量管理的概念
按照2000版ISO9000标准,质量管理的定义为:
“质量管理是在质量方面指挥和控制组织协调的活动”。
在品质管理方面的指挥和控制活动通常包括制定质量方针、质量目标、质量策划、质量控制、质量保证和质量改进。
质量管理起源于20世纪初期,至今主要经历了三个阶段,分别为质量检验管理阶段、统计质量管理阶段和全面质量管理阶段。
2.2“零缺陷”全面质量管理方式简述
“零缺陷”全面质量管理主要主张发挥人的主观能动性来进行生产,生产者、操作者要努力使自己的产品没有缺点并向着高质量标准的目标而奋斗。
所以此处所讲的“零缺陷”只是一种质量管理追求的理想目标,因为在很多情况下这种要求是不现实的,但是这种目标对提高产品质量却具有现实意义。
零缺陷的全面质量管理是通过全员参与质量管理方式来实现的。
产品质量是企业活动的各个环节、各个部门全部工作的综合反映。
因此必须把企业所有人员的积极性和创造性充分调动起来,如果人人关心质量问题,人人做好本职工作,那么最终产品的不合格率将大大降低,这样不仅降低了产品的生产成本,同时也为客户提供了优良的品质保障。
该质量管理方式可通过三种方式来实现
(1)全员把关
全面质量管理要求每一个人都对产品质量负有责任,及时发现质量问题,并把问题解决于发源地。
即生产线上的每名员工均有责任及时发现质量问题并寻找其根源。
也就是说,在全面质量管理中,与强调通过检验员严把质量关相比,更强调全员把关,即每一个员工保证不让任何有质量缺陷的加工件进入下一工序。
无论各工序可能的质量问题有多少,这种方法都会使企业的产品合格率大大提高。
同时,这种方法还会减少检验员的数目,从而降低鉴定成本。
(2)QC小组
QC小组是由一些基层管理人员及一般员工组成,能够发现、分析并最终解决生产和质量问题。
这是因为许多员工如果被允许参与改进他们所进行的工作,这些员工往往会表现出更大的兴趣和成就感。
一般要求QC小组成员都是自愿加入的,并且小组的成员应定期进行讨论、研究等活动,以分析、解决产品质量问题。
QC小组可以是在同一个班组内建立,也可以跨班组建立。
QC小组可以定期或不定期向公司提出质量改进意见,而且企业管理人员应对这些意见或建议给予高度重视,因为往往这些群众意见中的某一条可行性建议,就可以使公司通过质量改进而提高产品合格率或降低成本,从而获得更大的收益。
同时QC小组还可以成为研发人力资源、调动广大员工积极性和创造性的一种重要途径[2]。
(3)质量教育
既然产品的质量决定于企业全体员工,要求全员参与质量管理,就必须不断地对全体人员进行质量教育,让他们在思想上重视质量问题。
进行质量教育时要让每位员工了解与各自工作内容相关的环节的工作,以便使每位员工均认识到自己这一环节的工作如果出现问题会在哪些方面影响相关环节的工作。
也就是应该使每位员工都要找到自己的“顾客”。
例如一条生产线上某一工序的人应该把下一工序的工人看做自己的“顾客”,每个人都应该尽量满足自己的“顾客”的需求。
“零缺陷”全面质量管理思想强调全企业所有工作人员齐心协力、循序渐进、精益求精地进行产品质量控制。
如果利用这几种全员参与的质量管理方式相结合进行产品质量管理,相信所生产产品的品质与“零缺陷”目标的距离将大大缩短。
3主要品质缺陷分析
由于印制电路板的制程复杂,工序繁琐,导致其制造过程中出现的品质缺陷较多,严重影响最终产品质量。
为了降低PCB不合格率,使其在生产过程中的品质缺陷问题得到有效控制,现对PCB主要制造工序中的主要品质缺陷做简要分析,以便在实际生产中解决各缺陷问题提供必要的理论依据。
3.1层压工序主要缺陷分析
(1)分层:
分层是指基材的层间或导电箔与基材之间部分发生分离现象。
分层直接影响印制板的可靠性。
明显的分层不用显微镜剖析,而用肉眼就可以直接观察,也就是通常说的气泡。
多层板层压后分层产生原因
a.铜箔或导体铜表面在层压前处理不当,如没有除油、粗化或黑化棕化不均匀。
b.半固化片表面不清洁。
c.半固化片存放时间过长。
d.压制温度,加压工艺控制不正常,气泡未被完全排除。
(2)层间错位:
层间错位是指层与层之间连接盘中心的偏移。
层间错位产生原因
a.内层材料的热膨胀,粘结片的树脂流动。
b.层压中的热收缩。
c.层压材料和模板的热胀系数相差大。
(3)夹杂:
夹杂是指层压板内有没被蚀刻的金属箔或其他异物。
层间夹杂产生原因
a.工作人员操作不当。
b.层压环境灰尘或悬浮颗粒过多。
c.蚀刻工艺控制参数设置异常或蚀刻工艺不得当。
(4)空洞:
层压板的空洞通常是很小的,在实际中对于两层导体之间板厚为0.254mm的情况下,空洞最大允许直径为0.076mm。
层压空洞通常出现内层导线的边缘或焊盘上下面,当钻孔后,这个空洞很可能呈现在孔壁上一般情况下外层焊盘和导线之下允许有直径小于0.076mm的空洞。
但孔壁上层压板空洞,由于孔金属化空洞内存有气体或其他杂质,焊接时的热冲击,破坏了孔金属化,将影响印制板的可靠性。
层压板空洞产生原因
a.半固化片化学挥发物过多。
b.树脂系统含水分过高,工作室内湿度大。
c.压制模具不便于排气。
3.2钻孔工序主要缺陷分析
(1)钉头:
由于钻孔在多层印制板内层导线焊盘上的铜箔向外倾斜的状况叫钉头(如图1所示)。
多数的标准中没有一个明确的尺寸要求,但对军用多层印制电路板最大允许钉头大小是铜箔厚度的50%,钉头的存在,也就说明了这块多层印制电路板的钻孔质量大大下降,钉头的存在也伴有环氧树脂腻污存在。
(2)树脂腻污:
钻孔后,多层印制板内层导体铜环上有环氧树脂涂层,使孔内铜环不能充分暴露,这通常叫树脂腻污,也有资料称之为胶渣(如图2所示)。
由于树脂腻污严重影响了孔壁金属与内层铜环的链接,所以,多层印制板不允许有树脂腻污存在。
钉头与树脂腻污产生的原因
由于印制板基材的导热率比金属低,钻孔时产生大量的切屑热,绝大部分热量传递给钻头,使其达到很高的温度,除切屑热外,钻头与孔壁的钻擦也产生热量,这就加速了钻头的磨损,当用磨损的钻头钻孔时就容易使内层焊盘的铜产生钉头,造成孔壁的凹凸不平。
更严重的是,由于钻孔时产生的热量,使环氧树脂受热软化,软化的树脂粘在钻头上,在钻头进刀或退刀时容易使已经暴露的铜环涂抹上一层环氧树脂。
由此可见,这种缺陷与使用的印制板材料玻璃化温度、钻头材料与几何尺寸、钻孔操作工艺等有关系[3]。
(3)
焊盘撕裂:
所谓焊盘撕裂是指钻孔时产生了多层印制板内层焊盘撕断或裂开。
焊盘撕裂产生的原因
在产生较大的钉头同时,往往也容易产生这种缺陷,但主要是由于磨损钻头钻孔产生较大的切屑力,在层压板与铜箔之间抗剥强度较低的情况下,更容易产生内层焊盘撕裂。
(4)毛刺:
钻孔后孔周围印制板两表面铜箔突起叫毛刺。
目前现有的刷板设备可以去除大部分毛刺,但极其细小的毛刺刷板设备可能去除不彻底。
并有可能使毛刺导向孔内,使孔径变小。
严重时为了去除毛刺,造成孔周围的铜箔损坏,使孔壁与铜接触不良,有时可达到一圈而断开。
毛刺产生的原因
当钻头顶角磨顿时,可使印制板两面铜箔其毛刺,如果印制板与上下两面的垫板没有压紧,钻孔后也要产生毛刺。
毛刺倒向孔内,影响孔金属化可靠性。
3.3孔金属化工序主要缺陷分析
(1)电镀空洞:
是指在金属化孔壁上沉积的金属层中露出基材的洞状区域。
电镀空洞产生原因
a.金属化孔之前孔壁清洁处理不好,活化处理时孔壁有附着颗粒和气泡,使该处没有活化从而导致该处的化学沉铜不能进行,造成最终产品的空洞。
b.图形电镀锡铅合金时局部由于附着物和气泡在孔壁上,蚀刻时,将没有镀上锡铅的部位的铜腐蚀掉就形成了空洞。
(2)瘤状物:
是指在电镀过程中孔壁表面形成的金属瘤状凸起(如图3所示)。
瘤状物产生原因
a.钻孔孔壁极不光滑,有严重玻璃纤维突出。
b.电镀液内有颗粒被镀涂在镀层里,或者使用电流密度过大。
c.光亮镀铜的添加剂比例失调。
(3)
裂缝或拐角开裂:
这种裂痕是指在120℃下将被测试验板烘4个小时,在288℃下浮浸焊锡10秒后,再制备显微试样,在200倍以下显微效果下能观察到的裂缝(如图4所示)。
值得注意的是,不应该在高于200的放大倍数下检查是否有裂缝,由于镀层与底层之间结合部分在制备样品时总有一定的变化,把正常的结合间隙认为是电镀裂缝则是不合理的。
要判断是否为真正的镀层裂缝和拐角开裂是很重要的,因为这种开裂最终导致电路故障,影响整板的可靠性。
孔金属化裂缝或拐角开裂产生原因
当印制板受热后,环氧玻璃布在Z方向上玻璃化温度(Tg≈120~140℃)以下的膨胀系数为6~9×10-5,当温度在Tg以上时膨胀系数为2.5×10-4,而铜膨胀系数在20℃时为1.7×10-5,在230℃时为1.8×10-5。
由此可见,当印制电路板与元器件组装时,在焊接265℃进行热冲击时,两种材料膨胀系数不同,而产生不同的力作用于金属化孔上,特别是在金属化孔拐角处受力最大,当镀铜层的韧性不能满足受力产生形变的要求时,则会发生开裂。
要克服这种缺陷,除材料外,必须严格控制点镀铜层的质量。
3.4蚀刻工序主要缺陷分析
(1)侧蚀:
由于蚀刻而在导线侧面上形成的凹槽,并以该凹槽深度的程度来描述侧蚀程度(如图5所示)。
造成侧蚀后使焊盘尺寸发生变化,导线变得很细,对于普通印制板导体侧蚀量不应该超过金属的总厚度,而精密的细线条对侧蚀要严格控制。
侧蚀现象是时刻中不可避免的,只能设法减少,但不能消除。
侧蚀量大产生原因
a.铜箔厚度过大。
b.蚀刻液不是在最佳工作状态进行蚀刻。
c.延长了蚀刻时间。
(2)“铜箔残足”:
所谓铜箔残足是指在所形成线路的铜箔根部存在的蚀刻不足而产生的铜箔残留(如图6所示)。
“铜箔残足”产生原因
a.电镀铜箔制造时,是以1000ASF的高电流密度快速镀得的ED铜箔,是以柱状组织快速向上成长。
起始时颗粒较细,结束时则毛面棱线的颗粒就较大,并还有额外粗糙后处理所加镀的铜瘤与耐热的黄铜层。
再加上高温压合时其棱线的踏入树脂中,因而很不容易彻底蚀刻透。
b.向上的板面会有水池(内层)或水沟(外层)效应,再加上一铜二铜镀得太厚,与锡铅层的屋檐效应等共同挞伐之下,板边角密线路区,经常造成蚀刻不彻底的短路情形。
3.5不同类型短路的特征及成因
(1)基铜短路
其特征是在两条线路之间形成短路的铜面明显低于线路铜面,可能是单个的短路,也可能的大量的短路。
形成原因是在蚀刻的退膜工序,干膜没有被完全褪掉或者是因为干膜屑粘贴在板面上,在蚀刻时导致基铜没有被蚀去而形成。
(2)
电镀短路
特征是形成短路的铜面和线路的铜面是等高的,可能以单独的短路出现,也可能以大量的短路出现。
形成的原因是因为在电镀时时间太长或溶液搅拌剧烈导致干膜破裂,而在干膜应覆盖的区域镀上了铜和锡铅合金,经过蚀刻工序后便形成了短路。
(3)细线短路
特点是在两条导线之间有一条很细的铜线形成短路,细线的宽度为0.025~0.075mm。
成因只要是在曝光时环境控制不好,例如头发丝或其他的细小纤维落在板面上,造成曝光时有细小的干膜没有曝光,在电镀时刻完成后就形成了短路。
细线短路也有可能是重复性短路。
但不会多,因为生产部门每曝光一定的板会清洁曝光玻璃。
(4)凹坑短路
其特点是在形成线路缺陷区域可以明显看到有一个小凹坑,而这一短路就是因为小凹坑所导致。
原因是在多层板被压制时形成凹坑或基材有凹坑,因为凹坑的存在,在贴干膜时造成干膜和铜面之间有空隙,因此在图形电镀时凹坑处也被电镀了,蚀刻结束后就形成短路现象。
(5)蚀刻不足
通常在大块的无铜区域可以看到或多或少的像云块一样的铜,厚度较小,在观察线路区域,所形成的短路比较长,呈连续性,短路的铜面也比线路面低,原因是在蚀刻时药水的浓度太低或设定的蚀刻速度太快、时间太短造成的。
(6)刮擦短路
其特点是沿着一条铜线(不一定是直线)有较多的短路,短路也是因为这条铜线造成的,并且沿某一方向有擦刮的痕迹。
原因是因为在曝光之后、电镀之前干膜被机械或人为原因刮破或擦伤(在电镀之前发现仍可返工),经过电镀、蚀刻完成后即形成短路。
3.6不同类型开路的特征及成因
(1)重复性开路
特点是在几乎每一片板的同一个地方出现同样的开路,呈多次重复的现象,并且曝光底片的编号是相同的。
其形成原因是曝光底片上与板子开路相同的位置有缺陷,这种情况下曝光底片必须报废,并且要加强曝光时第一和最后一片板的AOI检测,确保第一片板无误后才可曝光。
(2)缺口开路
这种开路的特点是在一条导线上有一个缺口,并且因缺口导致剩下的线宽不足正常线宽的1/2或等于1/2,通常位置固定,呈多次重复现象。
其形成的原因也是因为曝光底片上有缺损,因此板子相同的位置导线也有一个缺口。
消除的办法是换新的曝光底片,并且加强曝光过程中的AOI检测。
(3)真空开路
在某一区域,有多条导线呈现愈来愈细的现象(逐渐变细),有的形成开路,有的没有开路,但因为导线太细(小于客户要求的最小线宽)而不得不报废。
导致这种缺陷的原因是因为曝光用的底片和干膜接触不够紧密,中间有空气,也就是曝光台闭合后抽真空不好,真空度达不到要求,从而导致曝光时导线变细或开路。
(4)刮擦开路
其特点是能够明显地看到导线被外力刮擦的痕迹,也因此造成开路。
原因是因为操作不当(例如拿板方法错误不小心等)或机器的原因而将导线擦伤从而形成开路。
由于外层线路缺陷问题的产生原因比较复杂,很多种情况都有可能,此处并未一一列举,但大多数缺陷都出现在覆铜板、菲林片、干膜等物料上,或是在曝光、显影、蚀刻等工序出现异常。
4结论
对于企业来说,尽量减少品质缺陷问题的发生减少生产过程产品的报废率,无疑是降低生产成本、使生产效益最大化的最行之有效的办法。
在此,就本文所述“零缺陷”质量管理方式的具体实施办法做几点简单建议:
(1)多开展对于员工质量观念教育的活动,而且教育的方式不能仅仅局限于开培训课程,可以将一个班组或一个部门所有成员组织在一起进行各种团队游戏,这样不仅可以让员工们在工作之余愉悦心情,使公司建立良好的企业文化,更主要的是还可以让大家知道团队合作的重要性,增强班组及部门的凝聚力,在工作中只有大家齐心协力共同努力参与到质量管理中去才能生产出高质量的产品。
(2)开通员工参与的沟通渠道,让员工能够将自己的意见或建议及时向有关领导或管理人员反映。
例如才公司内开设一些总经理信箱或在公司网站开设沟通窗口,并积极鼓励引导全体员工参与到质量改善或其他合理化建议提议中去,同时配以合理的奖励制度,所提建议或意见一经采纳,将予以一定额度的资金奖励或作为升职参考项等等。
(3)开展多样化的质量活动,例如组织同一车间两个班组进行互检活动或同一班组内不同岗位员工互检活动。
并对检查出的品质问题进行分析,找出解决方案。
以调动员工参与质量管理的积极性,减少问题的出现。
(4)积极建立执行激励制度,对在质量工作中成绩突出的员工或团队,要给予积极的奖励(包括物质奖励和精神奖励),激发更多的员工参与质量工作行列中。
致谢
本论文是在系主任王金来老师的悉心指导下完成的,因本人缺乏经验、学识有限,曾多次找王主任帮助修改论文,从选题方向到论文的格式细节,王主任以其广博的知识、丰富的经验和清晰的思路,对我进行耐心的指导,使我能够顺利的完成论文写作。
故借此论文完成之际,对王主任表示深深的感谢。
同时,在这里我还要感谢梅州博敏电子股份有限公司给我机会在PCB生产车间实习,让我更加深入透彻地了解了PCB生产工艺,使我的理论知识在实践中得到了升华,并顺利完成毕业论文。
并且在这里我还要感谢学校对我的栽培,感谢所有老师对我的谆谆教诲,以及系里给我们推荐优良的就业机会。
参考文献
[1]张怀武,何为,林金堵.现代印制电路原理与工艺[M].北京:
机械工业出版社,2009.1~2.
[2]刘树华,鲁建厦,王家尧.精益生产[M].北京:
机械工业出版社,2009.249~264.
[3]殷春喜.多层板金属化孔互连缺陷研究[EB/OL].