外圆表面的车削加工.docx
《外圆表面的车削加工.docx》由会员分享,可在线阅读,更多相关《外圆表面的车削加工.docx(14页珍藏版)》请在冰豆网上搜索。
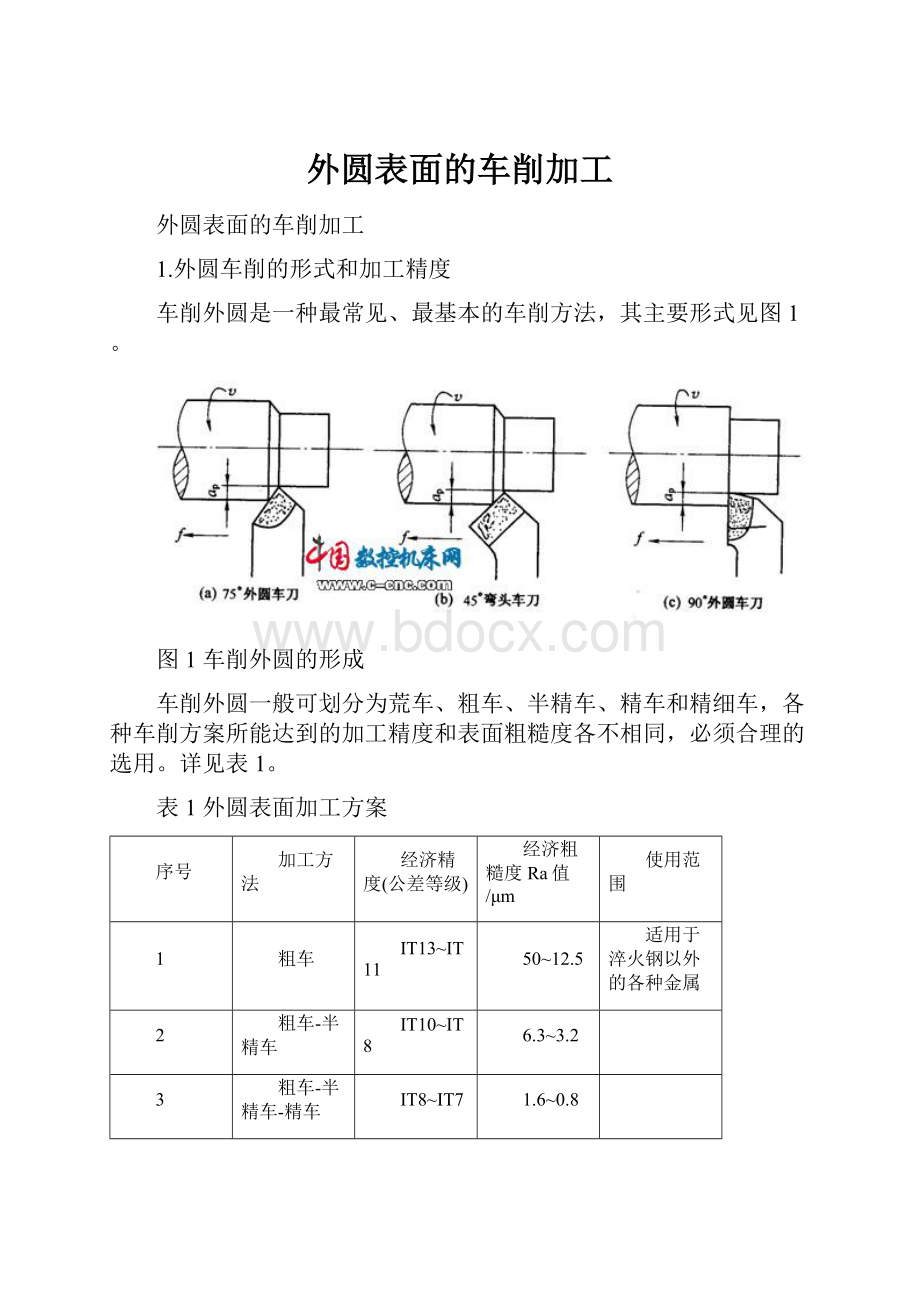
外圆表面的车削加工
外圆表面的车削加工
1.外圆车削的形式和加工精度
车削外圆是一种最常见、最基本的车削方法,其主要形式见图1。
图1车削外圆的形成
车削外圆一般可划分为荒车、粗车、半精车、精车和精细车,各种车削方案所能达到的加工精度和表面粗糙度各不相同,必须合理的选用。
详见表1。
表1外圆表面加工方案
序号
加工方法
经济精度(公差等级)
经济粗糙度Ra值/μm
使用范围
1
粗车
IT13~IT11
50~12.5
适用于淬火钢以外的各种金属
2
粗车-半精车
IT10~IT8
6.3~3.2
3
粗车-半精车-精车
IT8~IT7
1.6~0.8
4
粗车-半精车-精车-滚压
IT8~IT7
0.2~0.0255
5
粗车-半精车-磨削
IT8~IT7
0.8~0.4
主要用于淬火钢,也可用于未淬火钢,但不适用于有色金属
6
粗车-半精车-粗磨-精磨
IT7~IT6
0.4~0.1
7
粗车-半精车-粗磨-精磨-超精加工(或轮式超精磨)
IT5
0.1~0.012(或Rz0.1)
8
粗车-半精车-精车-精细车(金刚车)
IT7~IT6
0.4~0.025
主要用于要求较高的有色金属
9
粗车-半精车-粗磨-精磨-超精磨(或镜面磨)
IT5以上
0.025~0.006(或Rz0.1)
极高精度的外圆加工
10
粗车-半精车-粗磨-精磨-研磨
IT5以上
0.1~0.012 (或Rz0.1)
2.外圆车削工件的装夹方法
外圆车削加工时,最常见的工件装夹方法见表2。
表2最常见的车削装夹方法
名称
装夹简图
装夹特点
应用
三爪卡盘
三个卡爪可同时
移动,自动定心,
装夹迅速方便
长径比小于4,截面为圆形,六方体的中、小型工件加工
四爪卡盘
四个卡爪都可单独移动,装夹工件需要找正
长径比小于4,截面为方形、椭圆形的较大、较重的工件
花盘
盘面上多通槽和T形槽,使用螺钉、压板装夹,装夹前需找正
形状不规则的工件、孔或外圆与定位基面垂直的工件的加工
双顶尖
定心正确,装夹稳定
长径比为4~15的实心轴类零件加工
双顶尖中心架
支爪可调,增加工件刚性
长径比大于15的细长轴工件粗加工
一夹一顶跟刀架
支爪随刀具一起运动,无接刀痕
长径比大于15的细长轴工件半精加工、精加工
心轴
能保证外圆、端面对内孔的位置精度
以孔为定位基准的套类零件的加工
3.车刀的结构形式
车刀按结构不同可分为整体式、焊接式、机夹重磨式和机夹可转位式等几种。
整体式车刀是将车刀的切削部分与夹持部分用同一中材料制成,如尺寸不大的高速钢车刀常用这种结构。
焊接式车刀是在碳钢刀杆(常用45钢)上根据刀片的形状和尺寸铣出刀槽后将硬质合金刀片钎焊在刀槽中,然后刃磨出所需的几何参数。
焊接式车刀结构简单、紧凑、刚性好、灵活性大,可根据切削要求较方便地刃磨出所需角度,故应用广泛。
但经高温钎焊的硬质合金刀片,易产生应力和裂纹,切削性能有所下降,并且刀杆不能重复使用,浪费较大。
机夹重磨式车刀的刀片与刀杆是两个可拆的独立元件,切削时靠夹紧元件将它们紧固在一起,由于避免了因焊接产生的缺陷,可提高刀具的切削性能,并且刀杆可多次使用。
机夹可转位式车刀是将压制有合理几何参数、断屑槽、并有几个切削刃的多边形刀片,用机械夹固的方法,装夹在标准刀杆上,以实现切削的一种刀具结构。
当刀片的一个切削刃磨钝后,松开夹紧元件,把刀片转位换成另一新切削刃,便可继续使用。
与焊接式车刀相比,机夹可转位式车刀具有切削效率高,刀片使用寿命长,刀具消耗费用低等优点。
可转位车刀的刀杆可重复使用,节省了刀杆材料。
刀杆和刀片可实现标准化、系列化,有利用刀具的管理工作。
图2为常见车刀的结构示意图。
图2常用车刀结构示意图
4.外圆车刀的选择和装夹
外圆车刀应根据外圆表面加工方案选择。
粗车外圆要求外圆粗车刀强度高,能在切削深度大或走刀速度快的情况下保持刀头坚固。
精车外圆要求外圆车刀刀刃锋利、光洁。
如图1所示,主偏角Кr=75°外圆车刀刀头强度高,生产中常选用为外圆粗车刀;
主偏角Кr=45°弯头车刀,使用方便,还可以车端面和倒角,但因其副偏角К'r大,工件表面加工粗糙,不适于精加工;主偏角Кr=90°的外圆车刀可用粗车或精车,还可车削有垂直台阶的外圆和细长轴。
车刀在刀架上的安装高度,一般应使刀尖在与工件旋转轴线等高的地方.安装时可用尾架顶尖作为标准,或在工件端面车一印痕,就可知道轴线位置,把车刀调整安装好。
车刀在刀架上的位置,一般应垂直于工件旋转轴线,否则会引起主偏角Кr变化,还可能使刀尖扎入工件已加工表面或影响表面粗糙度质量。
5.车床
(1)车床的用途 车床主要用于加工零件的各种回转表面,如内外圆柱表面,内外圆锥表面,成形回转表面和回转体的端面等,有些车床还能车削螺纹表面。
由于大多数机器零件都具有回转表面,并且大部分需要用车床来加工,因此,车床是一般机器制造厂中应用最广泛的一类机床,约占机床总数的35%~50%。
在车床上,除使用车刀进行加工之外,还可以使用各种孔加工刀具(如钻头、铰刀、镗刀等)进行孔加工,或者使用螺纹刀具(丝锥、板牙)进行内、外螺纹加工。
(2)车床的运动
①工件的旋转运动 是车床的主运动,其特点是速度较高,消耗功率较大。
②刀具的直线移动 是车床的进给运动,是使毛坯上新的金属层被不断投入切削,以便切削出整个加工表面。
上述运动是车床形成加工表面形状所需的表面成形运动。
车床上车削螺纹时,工件的旋转运动和刀具的直线移动则形成螺旋运动,是一种复合成形运动。
(3)车床的分类 为适应不同的加工要求,车床分为很多种类。
按其结构和用途不同,可分为:
卧式车床(图3)、立式车床(图4)、转塔车床、回轮车床、落地车床、液压仿形及多刀自动和半自动车床、各种专用车床(如曲轴车床、凸轮车床等)、数控车床和车削加工中心等。
1、11—床腿2—进给箱3—主轴箱4—床鞍5—中滑板6—刀架
7—回转盘8—小滑板9—尾架10—床身12—光杠13—丝杠14—溜板箱
图3CA6140型卧式车床
图4立式车床
6.CA6140型卧式车床
(1)机床的工艺范围及其组成 CA6140型卧式车床的工艺范围很广,能适用于各种回转表面的加工,如车削内外圆柱面、圆锥面、环槽及成形回转面;车削端面及各种常用螺纹;还可以进行钻孔、扩孔、铰孔、滚花、攻螺纹和套螺纹等工作。
其加工的典型表面见图5。
图5CA6140型卧式车床加工的典型表面
CA6140型卧式车床的通用性较强,但机床的结构复杂且自动化程度低,加工过程中辅助时间较长,适用于单件、小批量生产及修理车间。
CA6140型卧式车床的布局及组成见图3。
图6CA6140型卧式车床的传动系统图
(2)机床的传动系统 图6为CA6140型卧式车床的传动系统图。
图中左上方的方框内表示机床的主轴箱,框中是从主电动机到车床主轴的主运动传动链。
传达链中的滑移齿轮变速机构,可使主轴得到不同的转速;片式摩擦离合器换向机构,可使主轴得到正、反向转速。
左下方框表示进给箱,右下方框表示溜板箱。
从主轴箱中下半部分传动件,到左外侧的挂轮机构、进给箱中的传动件、丝杆或光杠以及溜板箱中的传动件,构成了从主轴到刀架的进给传动链。
进给换向机构位于主轴箱下部,用于切削左旋或右旋螺纹,挂轮或进给箱中的变换机构,用来决定将运动传给丝杠还是光杠。
若传给丝杠,则经过丝杠和溜板箱中的开合螺母,把运动传给刀架,实现切削螺纹传动链;若传给光杠,则通过光杠和溜板箱中的转换机构传给刀架,形成机动进给传动链。
溜板箱中的转换机构用来确定是纵向进给或是横向进给。
①主运动传动链 运动由主电动机经V带轮传动副Ф130mm/Ф230mm传至主轴箱中的轴Ⅰ,轴Ⅰ上装有双向多片摩擦离合器M1,使主轴正转、反转或停止。
主运动传动链的传动路线表达式为
由传动路线表达式可以看出,主轴可获得2×3×[(2×2)+1]=30级正转转速,由于轴Ⅲ至轴Ⅴ间的两组双联滑移齿轮变速组的4种传动比为
其中u2=u3,所以实际只有3种不同的传动比,因此主轴只能获得
2×3×[(2×2-1)+1]=24级正转转速。
同理主轴可获得3×[(2×2-1)+1]=12级反转转速。
主轴反转时,轴Ⅰ-Ⅱ间传动比的值大于正转时传动比的值,所以反转转速大于正转转速。
主轴反转一般不用于切削,而是用于车削螺纹时,切削完一刀后,使车刀沿螺旋线退回,以免下一次切削时“乱扣”。
转速高,可节省辅助时间。
②车削螺纹传动链 CA6140型车床能够车削米制、英制、模数制和径节制四种标准螺纹,还能够车削大导程、非标准和较精密的螺纹,这些螺纹可以是左旋的也可以是右旋的。
车削螺纹传动链的作用,就是要得到上述各种螺纹的导程。
表3各种标准螺纹的螺距参数及其与螺距、导程的换算关系
螺纹种类
螺距参数
螺距/mm
导程/mm
米制
螺距P/mm
P=P
L=KP
模数制
模数m/mm
Pm=πm
Lm=KPm=Kπm
英制
每英寸牙数a(牙/in)
Pa=25.4/a
La=KPa=25.4K/a
径节制
径节DP(牙/in)
PDP=25.4π/DP
LDP=KPDP=25.4Kπ/DP
不同标准的螺纹用不同的参数表示其螺距,表3列出了米制、英制、模数制和径节制四种螺纹的螺距参数及其与螺距P、导程L之间的换算关系。
车削螺纹时,必须保证主轴每转一转,刀具准确地移动被加工螺纹的一个导程
LI,其运动平衡式为
注:
表中K为螺纹线数
式中 u——从主轴到丝杠之间的总传动比;
L丝——机床丝杠的导程(CA6140型车床L丝=12mm);
LI——被加工螺纹的导程(mm)。
在这个平衡式中,通过改变传动链中的传动比u,就可以得到要加工的螺纹导程。
CA6140型车床车削上述各种螺纹时传动路线表达式为
其中u基是轴ⅩⅢ和轴ⅩⅣ之间变速机构的8种传动比,即:
上述变速机构是获得各种螺纹的基本机构,称为基本螺距机构或称基本组。
u倍是轴ⅩⅤ和轴ⅩⅦ之间变速机构的4种传动比,即:
上述4种传动比按倍数关系排列。
用于扩大机床车削螺纹导程的种数。
这个变速机构称为增倍机构或增倍组。
在加工正常螺纹导程时,主轴Ⅵ直接传动轴Ⅸ,其间传动比
,此时能加工的最大螺纹导程L=12mm。
如果需要车削导程更大的螺纹时,可将轴Ⅸ的滑移齿轮58向右移动,使之与轴Ⅷ上的齿轮26啮合,从主轴Ⅵ至轴Ⅸ间的传动比为
这表明,当车削螺纹传动链其它部分不变时,只做上述调整,便可使螺纹导程比正常导程相应地扩大4倍或16倍。
通常把上述传动机构称之为扩大螺距机构。
在CA6140型车床上,通过扩大螺距机构所能车削的最大米制螺纹导程为192mm。
必须指出,扩大螺距机构的传动比u扩是由主运动传动链中背轮机构齿轮的啮合位置所确定的,而背轮机构一定的齿轮啮合位置,又对应一定的主轴转速,因此,主轴转速一定时,螺纹导程可能扩大的倍数是确定的。
具体地说,主轴转速是10~32r/min时,导程可扩大16倍;主轴转速是40~125r/min时,导程可扩大4倍;主轴转速更高时,导程不能扩大。
这也正好符合大导程螺纹只能在低速时车削的实际需要。
当需要车削非标准螺纹和精密螺纹时,需将进结箱中的齿式离合器M3、M4和M5全部接合上,此时,轴ⅩⅡ、ⅩⅣ、ⅩⅦ和丝杠ⅩⅧ联成一体,运动由挂轮直接传给丝杠,被加工螺纹的导程L工可通过选配挂轮来实现,因此可以车削任意导程的非标准螺纹。
同时,由于传动链大大地缩短,减少了传动件制造和装配误差对螺纹螺距精度的影响,若选用高精度的齿轮做为挂轮,则可加工精密螺纹。
挂轮换置公式为:
③纵向和横向机动进给传动链 纵向进给一般用于外圆车削,而横向进给用于端面车削。
为了减少丝杠的磨损和便于操纵,机动进给是由光杠经溜板箱传动的,其传动路线表达式为:
CA6140型车床纵向机动进给量有64级。
其中,当进给运动由主轴经正常螺距米制螺纹传动路线时,可获得范围为0.08~1.22mm/r32级正常进给量;当进给运动由主轴经正常螺距英制螺纹传动路线时,可获得0.86~1.59mm/r8级较大进给量;若接通扩大螺距机构,选用米制螺纹传动路线,并使u倍=1/8,可获得0.028~0.054mm/r8级用于高速精车的细进给量;而接通扩大螺距机构,采用英制螺纹传动路线,并适当调整增倍机构,可获得范围为1.71~6.33mm/r16级供强力切削或宽刃精车之用的加大进给量。
分析可知,当主轴箱及进给箱中的传动路线相同时,所得到的横向机动进给量级数与纵向相同,且横向进给量f横=1/2f纵。
这是因为横向进给经常用于切槽或切断,容易产生振动,切削条件差,故使用较小进给量。
④刀架快速移动传动链 刀架的快速移动是由装在溜板箱内的快速电动机(0.25kw,2800r/min)驱动的。
按下快速移动按钮,启动快速电动机后,由溜板箱中的双向离合器M8和M9控制其纵、横双向快速移动。
刀架快速移动时,可不必脱开机动进给传动链,在齿轮56与轴之间装有超越离合器M6,可保证光杠和快速电机同时传给轴运动而不相互干涉。