半导体企业生产线管理的十大基本原则.docx
《半导体企业生产线管理的十大基本原则.docx》由会员分享,可在线阅读,更多相关《半导体企业生产线管理的十大基本原则.docx(6页珍藏版)》请在冰豆网上搜索。
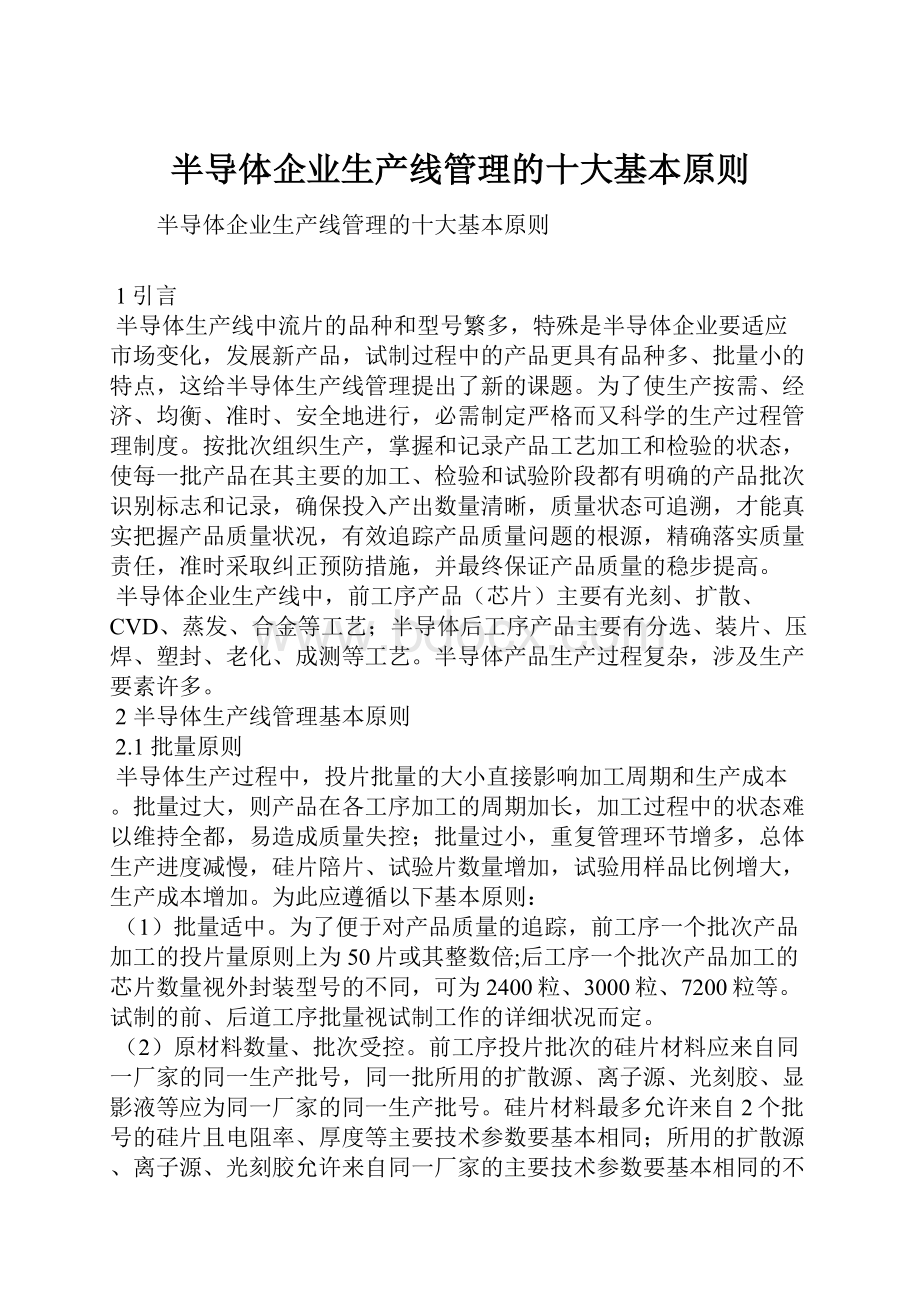
半导体企业生产线管理的十大基本原则
半导体企业生产线管理的十大基本原则
1引言
半导体生产线中流片的品种和型号繁多,特殊是半导体企业要适应市场变化,发展新产品,试制过程中的产品更具有品种多、批量小的特点,这给半导体生产线管理提出了新的课题。
为了使生产按需、经济、均衡、准时、安全地进行,必需制定严格而又科学的生产过程管理制度。
按批次组织生产,掌握和记录产品工艺加工和检验的状态,使每一批产品在其主要的加工、检验和试验阶段都有明确的产品批次识别标志和记录,确保投入产出数量清晰,质量状态可追溯,才能真实把握产品质量状况,有效追踪产品质量问题的根源,精确落实质量责任,准时采取纠正预防措施,并最终保证产品质量的稳步提高。
半导体企业生产线中,前工序产品(芯片)主要有光刻、扩散、CVD、蒸发、合金等工艺;半导体后工序产品主要有分选、装片、压焊、塑封、老化、成测等工艺。
半导体产品生产过程复杂,涉及生产要素许多。
2半导体生产线管理基本原则
2.1批量原则
半导体生产过程中,投片批量的大小直接影响加工周期和生产成本。
批量过大,则产品在各工序加工的周期加长,加工过程中的状态难以维持全都,易造成质量失控;批量过小,重复管理环节增多,总体生产进度减慢,硅片陪片、试验片数量增加,试验用样品比例增大,生产成本增加。
为此应遵循以下基本原则:
(1)批量适中。
为了便于对产品质量的追踪,前工序一个批次产品加工的投片量原则上为50片或其整数倍;后工序一个批次产品加工的芯片数量视外封装型号的不同,可为2400粒、3000粒、7200粒等。
试制的前、后道工序批量视试制工作的详细状况而定。
(2)原材料数量、批次受控。
前工序投片批次的硅片材料应来自同一厂家的同一生产批号,同一批所用的扩散源、离子源、光刻胶、显影液等应为同一厂家的同一生产批号。
硅片材料最多允许来自2个批号的硅片且电阻率、厚度等主要技术参数要基本相同;所用的扩散源、离子源、光刻胶允许来自同一厂家的主要技术参数要基本相同的不同生产批号产品,并在领料单和产品工艺流程卡中注明各个批号材料及数量等。
后工序封装用的芯片、金丝、环氧树脂等材料应来自同一厂家的同一生产批号;芯片最多允许来自2个批号的同一产品;金丝、环氧树脂等材料最多允许来自同一厂家不同生产批号且理化性能全都的相应材料,并在领料单和工艺流程卡中注明各个批号材料及数量。
(3)一批产品中使用不同批次同种原材料时,应确保可追溯。
2.2批号原则
产品批号应遵循以下基本原则:
(1)产品批号编制唯一。
各工序在加工或检验的同一批产品应具有唯一的产品批号,不允很多批产品用一个批号,也不允许一产品有多个批号。
(2)产品批号分类编制。
依据半导体产品功能,产品批号分为底压系列晶体管、中压系列晶体管、高压系列晶体管、可控硅、放电管、二极管和功率集成电路等,分别进行产品批号编制,(光电器件产品按颜色、封装形式、光强等分类进行产品批号编制)。
批号基本规则是一位字母(表示产品品种)+该产品代号+年月四位代码+二位序列号。
(3)产品批号给出方法。
已生产定型产品的批号由前、后工序生产部门的调度员依据产品批号分类编制原则给出;新品试制产品的批号及其分流批号由技术中心主管工艺师会同有关生产部门调度员或生产线线长给出。
2.3转移与分批原则
转移与分批原则应遵循的基本原则:
(1)整批转移,物卡同传,记录完整。
产品在按批次完成全部本工序的工艺加工和检验并填写完整相应的原始记录和“工艺流程卡”后,方可转移至下一工序;操作员或检验员必需同时收到上一工序已完工或检验的产品和“工艺流程卡”,并核对物、卡的数量、状态状况无误后,方可开头工作。
“工艺流程卡”要求填写完整齐全、规范合格,并随对应的已完成工艺加工和检验的产品批一起流出半导体生产线。
(2)分拆子批原则。
已经生产定型的产品遇特别状况而不能以一个完整批转移出本工序时,可由班长持“工艺流程卡”向生产调度员或生产线线长申请分子批转移,调度员或线长同意后将该批分拆成多个子批,并给出各个子批批号转移;试制新品因试验工艺须分拆子批时,由项目负责人打算,并报生产调度员或线长登记,给出分流子批批号。
对每个子批应赐予一个与其它子批互不重复而又与原母批批号有渊源关系的子批批号,子批批号具有唯一性。
前、后工序子批批号均在原母批批号后面增加一个连字符和一位阿拉伯数字组成,数字表示子批顺序号。
2.4暂存原则
半导体产品在加工、检验中,需临时存放时,为保障生产有序进行,保证产品质量,需要对产品进行合格标志、有效标识与合理贮存,因此,应遵循以下基本规则:
(1)标志规范。
产品应按工艺具体规范的要求,在适当位置形成正式的产品标志。
(2)标识正确。
产品的状态标识按批次进行,除“工艺流程卡”外,还可用标签的形式记录产品的型号、批号、数量、工序等(在加工、待检、待判、合格、不合格),填写标识的人员与日期等相关产品识别内容。
产品状况发生变化时,应准时更换产品的标识。
在制品的标识由该批次操作员或检验员完成;出工序的标识由班长完成;出生产线的标识由调度员或线长完成。
(3)贮存受控。
依据不同的状态,产品贮存按批次将在制品与对应的状态标识签一起存放在不同的既定位置。
后工序的产品应装专用周转盒,放置在温度20~25℃,湿度≤RH65%,1000级净化受控环境中;前工序产品应装在专用传递盒中,放置在温度20~25℃,湿度≤RH65%,100级净化受控环境中。
2.5返工原则
通过把握返工产品的质量状态,有效掌握返工过程并做精确记录,保证不因返工而造成产品的批次性质量问题存在。
返工应遵循的基本原则:
(1)集中完成。
任一批次产品在同一工序的返工应集中在一起完成,以保证同次返工的状态全都。
(2)掌握返工次数。
一般状况下,后工序产品在一个工序上只允许最多返工二次;前工序产品在光刻工序上允许返工一次,前工序产品在扩散、CVD、蒸发溅射和合金工序因热效应,一般不进行返工。
(3)批次性返工的掌握。
后工序批次性不合格(整批不合格、工序合格品率明显底于其目标合格品率或出现较大质量问题)的产品批,须通过不格品评审程序,然后打算是否可作为返工批向下转移。
对于批次性返工,调度员或线长应组织技术人员制订相应方案并报生产部部长签字同意后才能进行。
前工序批次性不合格,一般不返工。
(4)返工批号的掌握。
返工批的投片批号由调度员或线长给出。
返工批的批号编制为:
在原投片批号后+连字符加+BX(X为一位返工序号)。
2.6记录原则
生产过程中的“工艺流程卡”等工艺原始记录是产品质量追踪的主要依据。
此外,质量分析、生产计划、原材料预备、成品率统计分析、成本核算等工作也都要以产品生产的这些原始工艺数据为基础。
因此,记录应遵循以下基本原则:
(1)记录准时精确,唯一对应。
每一个批号、子批批号、返工批号的产品都必需对应其唯一的“工艺流程卡”及填写齐全的加工、检验相关原始记录,既不允许合并不同批次的记录,也不允许同一批次产品有多份同种记录。
(2)记录不得重复。
各子批、返工批在前步母批中已完成和记录了的工序内容,在其后续批次的“工艺流程卡”中不再重复记录,只需记录后续操作的有关内容。
(3)子批、返工批的追踪掌握。
在确定子批或返工批后,生产调度员或线长应在原母批产品的“工艺流程卡”相应备注栏内注明各有关分批的状况和去向(包括子批批号或返工批批号及其数量)。
当产品正式批次(原母批和各子批)及其全部的返工批的在线加工与检验全部完成后,调度员或线长应依次序将已填写完整齐全的全部这些批次的“工艺流程卡”汇总装订在一起作为该批“工艺流程卡”。
2.7时间原则
产品的生产既要保证质量,又要保证时间进度,因此应遵循以下时间基本原则:
(1)生产预备时间。
前工序任一批次产品的原材料应在3周内预备就绪;后工序任一批次产品的原材料应在2周内预备就绪。
生产部门调度员或线长、计划供应部原材料计划员和新产品项目负责人之间应经常交换原材料供需信息,使原材料预备能做到提前计划,准时供应,原材料不到位时不进行生产或试制。
(2)生产过程时间。
前工序任一批次产品加工和检验,应在1。
5个月内完成;后工序任一批次产品加工和检验,应在1个月内完成。
每一道工序加工和检验时间应不超过计划用时的1倍(设备故障除外),否则,班长应准时了解状况并报调度员或线长,作出相应处理。
调度员或线长应每天把握各工序生产状况,绘制生产进度表。
(3)问题处理时间,因管理、原材料、工艺或操作等原因,前工序在2个月内或后工序在1。
5个月内投产批的产品未能流出工艺线时,生产调度员或线长应准时提交报告,交本生产部部长和计划部部长,在1周之内,由每周生产联席会议争论,拿出解决方法。
2.8调度原则
调度员或线长是生产线管理工作的关键和灵魂,其工作状况对生产管理的效果产生直接影响。
生产调度员或线长应遵守的基本规则:
(1)日常调度。
依据生产部门实际状况,按“批量原则”分批投片;按“批号原则”给出产品批次号;按“分批原则”、“返工原则”给出子批批号、返工批号。
(2)调度单管理。
调度员或线长以“生产调度单”按批次发布调度指令,生产过程中以“工艺流程卡”为路线进行生产管理。
每一个投片批次均有唯一的“生产调度单”,随对应的“工艺流程卡”下发。
调度员或线长应准时建立清楚的调度台帐,依序给出调度单编号,保证前批与后批、子批与母批、正式批与返工批间的批号关系正确,产品数量精确。
调度单编号由一位英语字母和六位阿拉伯数字组成。
其中英语字母代表品种,前四位数字为年月,后二位数码为该类产品的投片顺序号。
(3)特别状况下的调度。
产品设计、工艺文件不齐全,原材料预备不足或不合格,不得将该批产品投入生产线加工。
特别状况,须有本生产部部长或更高一级领导书面同意的文字材料。
2.9归档原则
半导体生产过程中的原始凭证和记录应准时、有效归档,这对于产品质量问题追踪查询和统计、核算、计划等管理工作非常重要。
(1)“工艺流程卡”的归档。
“工艺流程卡”要求填写完整齐全、规范合格。
一个批次若分作多个子批或有返工批时,应将同一母批的全部子批和返工批的“工艺流程卡”依序整理汇总,作为这个整批次“工艺流程卡”的资料。
前、后工序已全部完成工艺加工、检验的“工艺流程卡”,每天由本部门生产调度员或线长收集一次,暂存在本部门资料库,每月一次集中交技术中心资料室,并办理交接手续。
若核对存在问题,资料管理员不能接受。
该调度员或线长应在3个工作日内组织完成出现问题的整改,并重新交收归档。
(2)“生产调度单”的归档。
每月第一周的第二个工作日,调度员或线长应将上月开出的全部“生产调度单”底联交计划部归档,办理交接手续。
交接中应核对“生产调度单”的完整性和编号的连续性,如有问题,调度员或线长应在3个工作日完成整改并重新送交归档。
2.10计算机辅助管理原则
半导体器件制造业属高科技范畴,生产线所用的设备、仪器大多数是带计算机掌握的,因此要利用计算机进行辅助管理,以保证产品的质量。
为此应遵循计算机辅助管理原则:
(1)程序、数据备份原则。
生产过程中的程序、数据应备份一份放技术中心资料室保管,备份一份放生产部留存。
(2)程序建立、更改原则。
生产过程中的程序由产品项目负责人编制,生产部门主管工程师审核,总工程师批准。
在生产过程中,若程序须更改,要由调度员或线长提出,工序工程师拟定,生产部门主管工程师审核,总工程师批准,并填写“程序更改通知单”后方可更改。
更改通知书每月由调度员或线长汇总送交技术中心资料室归档。
(3)数据、图片建立原则。
生产过程中,分析测试所记录的数据、所拍摄的图片,应即时存入相应工序的子目录下,并记录日期、操作员等要素,不得删除或更改。
重要数据和图片应设置密码。
为保全起见,可再另存备份。
这些数据和图片应每月刻录进光盘一次,由调度员或线长交技术中心资料室保存。