参考文献综述.docx
《参考文献综述.docx》由会员分享,可在线阅读,更多相关《参考文献综述.docx(10页珍藏版)》请在冰豆网上搜索。
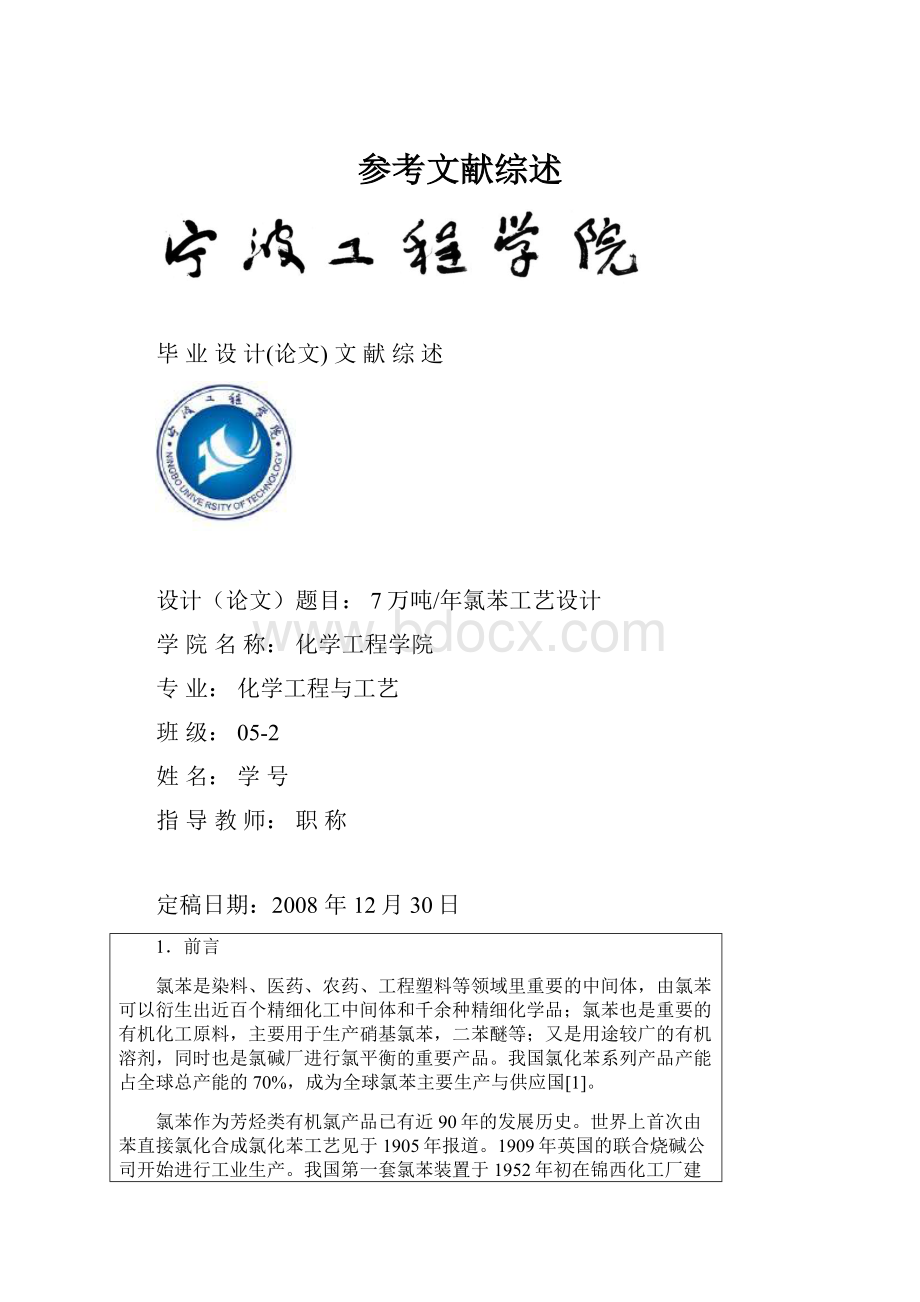
参考文献综述
毕业设计(论文)文献综述
设计(论文)题目:
7万吨/年氯苯工艺设计
学院名称:
化学工程学院
专业:
化学工程与工艺
班级:
05-2
姓名:
学号
指导教师:
职称
定稿日期:
2008年12月30日
1.前言
氯苯是染料、医药、农药、工程塑料等领域里重要的中间体,由氯苯可以衍生出近百个精细化工中间体和千余种精细化学品;氯苯也是重要的有机化工原料,主要用于生产硝基氯苯,二苯醚等;又是用途较广的有机溶剂,同时也是氯碱厂进行氯平衡的重要产品。
我国氯化苯系列产品产能占全球总产能的70%,成为全球氯苯主要生产与供应国[1]。
氯苯作为芳烃类有机氯产品已有近90年的发展历史。
世界上首次由苯直接氯化合成氯化苯工艺见于1905年报道。
1909年英国的联合烧碱公司开始进行工业生产。
我国第一套氯苯装置于1952年初在锦西化工厂建成投产,采用以低温间歇氯化法。
随着氯苯技术逐步发展,六十年代开始我国氯苯的生产工艺逐渐改进为高温连续法。
该法大大简化了操作程序,降低了能耗,改善了环境,生产能力也随之提高,至八十年代我国已有万吨以上装置三套,九十年代中期我国氯苯生产装置总能力已超过了10万吨[2]。
2000年后我国氯苯生产能力迅速发展,至2006年我国氯苯生产能力可达50万吨,2008年国内氯苯年产能已达55.5万吨[3]。
目前全国生产氯苯的厂家近20多家,生产能力在5万t/a以上的有南京化工厂、锦西化工总厂、扬州农药厂、渤海化工集团公司天津化工厂、河南开普化工股份有限公司、太原化学工业集团公司、江苏化工农药集团公司等[4]。
基于氯苯是重要的有机中间体,而与它相关的化学品的开发又是具有很大发展潜力的,因此氯化苯的投入生产将有助于上下游产品的开发,极大程度地促进化学品的市场销售,推动国民经济的发展。
2主体部分
2.1氯苯的理化性质
氯苯分子式C6H5Cl,无色透明液体,具有不愉快的苦杏仁味,分子量112.56g/mol,20℃闪点28℃,熔点-45.2℃,沸点132.2℃,不溶于水,溶于乙醇、乙醚、氯仿、二硫化碳、苯等多数有机溶剂,危险标记7(易燃液体)。
2.2氯苯生产工艺技术
2.2.1工艺技术路线比较[5][6]
1)氧化氯化法
将苯蒸汽与氯化氢在200℃—250℃一同通过Cu2+催化剂,氯化氢被空气中的氧气氧化成氯气,随即与苯反应,其总方程为:
苯的转化率约10%,氯苯的收率约90%,得到的氯苯可用气相水解法制取苯酚。
2)酸催化的次氯酸的氯化
次卤酸不易离解成卤素正离子X+,而是一种比分子态卤素更不活泼的卤化剂,但在强酸存在下,可使芳烃卤化;采用该卤化剂,可使反应在水介质中进行,对合成有实际意义。
酸催化下用次氯酸氯化反应中,其氯化历程可表示如下:
因此,在酸催化下,HOCl成为非常强的卤化剂是由于生成高度极化的络合物
,
是氯化反应的反应剂。
带正电荷的中间络合物的存在,可以从反应不显示氢同位素效应而得到证明。
在酸度超过1mol••L-1时,反应速度随酸度的增大而迅速加快,许多烃在二噁烷作溶剂时的反应动力学证明了这点,并发现氯化银能进一步催化这类反应。
但对于高活泼的化合物如苯酞,反应速度与芳烃无关:
3)沸腾氯化法
该方法的原理:
以FeCl3为催化剂,苯和氯气反应的氯化反应生成氯化苯,总反应式为:
然后氯化反应热使氯化液沸腾,使一部分的苯和氯苯蒸发汽化,经过塔顶的石墨冷凝器使大部分的苯蒸汽和氯苯蒸汽冷凝下来,最后再进行分离提纯。
将以上三种工艺流程相比,氧化氯化法是不会生成多氯代苯,并且原料费用少;缺点是腐蚀性强,对设备材质要求很高。
这种方法从1971年起已被淘汰。
沸腾氯化法优点是具有较小的空间阻碍,并且该反应可以在水的介质中反应,但是缺点是由于在生产中使用的一些溶剂比如二噁烷具有极强的毒性,在工业化生产中不可采用,很容易对环境及人类带来危害。
用沸腾氯化法生产氯苯的主要优点是生产能力大,在相同的氯化深度下二氯化苯的生成量较少,这是由于减少了返混的缘故。
因此,可以看出沸腾氯化法最有优点。
由于现在技术的不断发展更新,氯苯的生产工艺不断的改进,这样可以有效的减少生产的成本,增加最后的产率[7]。
2.3氯苯反应机理
2.3.1氯苯的生产原理
苯环的结构决定了苯环的卤代为亲电取代反应,反应催化剂为Fecl3,其反应历程为:
(1)铁与氯反应生成三氯化铁
(2)三氯化铁与氯作用生成具有催化作用的路易斯酸
(3)氯正离子对苯的芳核发生亲电攻击生成中间络合物
(4)中间络合物脱去质子而得到核上取代的氯化物
(5)副反应为氯苯氯化生成二氯苯
2.3.2氯苯的生产
生产的操作过程如下:
将经过固体食盐干燥的苯和氯气,按苯氯比约为4:
1的比例,送入充满铁环填料的氯化器底部,部分氯气和铁环反应生成FeCl3并溶解于苯中,保持反应器温度在75-80℃,使其在沸腾状态下进行反应。
氯化液溢出流入液封槽,经冷却后进入贮罐,控制氯化液比重在0.935-0.950,此时温控为15℃,将氯化产物水洗、中和,送往蒸馏分离,蒸出的苯循环利用。
出产品氯苯外,得到的混合二氯苯还可以进一步分离;反应器的顶部逸出的苯蒸汽和氯化氢气体,经冷凝回收苯,再以水吸收得到副产盐酸[8]。
1-转子流量剂;2-氯化器;3-液封槽;1-酸水排放口;2-苯及氯气出口;3-炉条;
4,5-管式石墨冷却器;6-酸苯分离器;4-填料铁圈;5-壳钢衬耐酸砖;6-氯化液出口;
7-氯化液冷却器7-挡板;8-气体出口
图2-1苯的沸腾氯化流程图图2-2沸腾氯化器
2.3.3工艺流程图
图2-3氯苯生产的工艺流程图
2.3.4工艺参数的选择与影响[9]
1)反应温度的选择
苯的氯化是放热反应,随着反应的进行,热量增多,温度升高,可以加快反应速度,但苯的初馏点气79.5℃,沸点80.1℃,温度升高,使得苯蒸发而损失;随着热量的不断积累,温度高于100℃以上,将会出现苯的炭化现象,炭化物履盖于铁环上,遮盖了催化剂表面的活性中心,形成催化剂结焦现象而失去活性,使反应受阻乃至停顿[6]。
同时,温度过高会使铁环过热,发生熔结,特别是旧铁环(即使用过一段时间变薄的铁环)在高温时极易发生熔结,严重时烧结在一起,使催化剂比表面减少,产生催化剂老化现象,失去活性。
所以,苯的氯化反应过程中,要保证催化剂活性充分发挥,就必须保持适宜温度,即及时取走过量反应热,来保证氯化反应正常迅速地进行。
氯苯生产中采取过量苯的蒸发取走反应热,使氯化温度保持在75~85℃之间,苯以沸腾的汽液相参与反应,不仅催化剂活性充分发挥,且由于是汽—汽、汽—液混合反应,使反应速度得以加快。
若反应温度较低,则催化剂的活性难以充分发挥,反应速度缓慢,通入的氯气不能完全参加反应,会产生系统中氯气过剩的现象,给反应带来危害。
2)氯气过量的影响
在共价键形成的双原子分子,Cl-Cl键的键能较小,也就是氯分子最易发生共价键断裂而形成游离基Cl·。
苯的氯化过程中温度低时,产生氯气过剩现象,过剩的氯游离于系统之中。
氯化反应及三氯化铁的生成过程都是放热反应,系统中的游离氯,受热时获得热量有可能足以使Cl-Cl键断裂生成游离基Cl·。
链锁反应在极短的时间内会放出极大的能量,当系统中气相的氢、氧和氯的含量达到爆炸范围时,链锁反应放出的能量达到一定程度能引起爆炸,也会使氢和氧发生爆鸣反应。
使爆炸更加猛烈。
此时系统中还有易燃物—苯存在,就会发生燃烧,这些现象在氯苯生产中发生过多次。
所以,苯的氯化反应,前期必须使反应温度较快地升至70℃以上,使催化剂的活性能尽快发挥,氯气能进入完全反应阶段,减少系统中氯的过剩量,以保证苯的氯化反应速度和反应的安全。
3)原料纯度的影响
在苯的氯化反应中,一般不希望原料中含有其他杂质,最有害的苯中含有硫化物。
噻吩在反应中生成不容于苯的黑色沉淀,这种物质会包住三氯化铁的表面,使催化剂失效,此外,噻吩在反应生成的氯化物能在氯化液的精馏过程中分解出氯化氢,对设备造成腐蚀噻吩或含氢≤0.01%。
此外在有机原料中还部希望含有水分。
因为水与反应生成的氯化氢作用生成盐酸,它对催化剂三氯化铁的溶解度,大大超过有机物对三氯化铁的溶解度,导致催化剂离开反应区,使氯化反应速度变慢。
研究表明:
当苯中含有0.2%水分时,苯中所含三氯化铁被提取入盐酸层,氯化反应不再进行苯中三氯化铁的最低浓度是0.01%;溶于水中的氯化氢还能设备剧烈腐蚀。
苯中的水分可采用恒沸蒸馏或干燥剂出去。
4)催化剂的选择
对活性较低的芳烃的卤化,一般要加入金属卤化物做催化剂。
选用最经济的催化剂FeCl3,但实际加入的“催化剂”是废铁屑、铁镟丝或废铁管。
在氯化时,金属铁和氧化铁与氯反应而生成真正的催化剂FeCl3,有人指出苯中如果含有2×10-3的水(质量分数),就会使FeCl3溶解而失去活性。
因此要求苯和氯气都充分干燥,使含水的质量分数低于4×10-4(按质量计)。
2.4氯苯生产中的三废污染及其处理
氯化苯生产过程中排放的“三废”有废水、废气、废渣,它们都是一些含苯类的有害物质,对人体及周围环境影响很大,也是氯碱行业中比较大的污染源。
及时有效地处理“三废”是氯化苯生产技术发展的重点[10]。
2.4.1废水处理
废水处理是氯化苯生产过程中“三废治理”的最重要部分。
生产过程中主要产生下面五部分废水,其总量约为每吨氯化苯产生0.2t~0.6t废水,其中含苯200-2500mg/l,氯化苯100-500mg/l,含二氯苯微量,酸碱性在pH=1~8左右。
水洗产生的废水处理方法:
①将这部分废水送到副产盐酸工段,做废酸回收。
也可以提高其HCl的浓度,作为销售废酸。
②将水洗缸中的废水进人回收池中,用泵送到污水处理站进行酸碱中和,待pH合格后排放[11-12]。
2.4.2废气处理
在氯化苯生产中,每生产1t氯化苯约排放含苯、氯化苯、HCl等废气约6~7m3。
如果将这部分气体排放到大气中,将会严重污染环境,必须对其进行处理。
处理方法:
(1)苯经氯化反应产生的尾气经过单塔、总塔、二级低温喷淋吸收塔可使尾气中含苯降5~10g/m3。
尾气中HCl的吸收是通过加水在绝热吸收塔内吸收制成28%~31%的副产盐酸,但是副产盐酸中不同程度地带有少量的苯,必须对其进行回收,否则对用户造成二次污染,具体方法简述如下:
在副产盐酸进入盐酸贮槽之前设计一组酸苯分离器,夹带苯的副产酸从酸苯分离器的顶部进人,根据酸与苯互不相溶氯化苯。
(2)氯化反应的尾气中带有一定量的氯气,如果超过标准排放到大气将会污染环境,腐蚀设备。
可采用以下方法进行净化:
盐酸吸收后的尾气经过一个碱吸收塔,用液碱进行循环喷淋,使尾气中氯气与碱生成次氯酸钠,次氯酸钠可回收利用。
(3)各类贮槽排放的废气采用活性炭吸附的方法进行吸收[13-15]。
2.4.3废渣处理
氯化苯生产过程中产生的废渣主要是一些含有多氯苯的物质和碳化物并且含有少量的苯、一氯苯和二氯苯。
这些物质不仅对环境造成污染,而且其中的苯、一氯苯、二氯苯这些有用物质也白白地流失,使苯耗提高,成本增加。
故必须对其进行处理,具体处理方法有以下几种:
①填埋法,一种比较理想的处理方法,能最大限度地降低污。
②焚烧法该法在处理效果上不太理想,虽然焚烧能减少废渣的污染,但是废渣在燃烧时产生氯气,必须用足够的烃类燃料来消耗它,另外如果废渣燃烧不充分,会产生一些致癌物质,所以不应采用此法。
③干馏法,利用氢气直接加热,将废渣中的苯和氯苯及二氯苯等有机物加热到一定温度,使之挥发成气体从废渣中逸出,其有效成份经过冷凝,中和被回收,不凝气经吸收塔吸收HCI后排到大气中[10]。
2.5氯苯的生产现状和市场情况
2007年国内氯化苯产量将增长,我国氯化苯总产量将突破45万吨,开工率达到90%。
2008年6月以来,长期稳定运行的国内氯苯市场行情强势上扬,价格由每吨7200元涨至8000元,达到近两年来的高位,且有望继续上涨。
究其原因,主要是受上游原料提价和下游需求强劲的拉动[17]。
长期低位持稳的氯化苯市场此次强势上扬,主要源自两个方面:
上游焦化苯市场近期价格强势推高,某些区域甚至高达8300元,并限制发货,造成了氯化苯企业成本大幅增加,并影响到开工率,由此导致氯化苯生产企业被动上调出厂价格。
此外,近期氯化苯下游主要消费产品硝基氯苯价格猛涨,突破历史高位。
截至5月底,与去年同期相比,硝基氯苯价格涨幅达130%,邻硝基氯苯涨幅达131%,而氯化苯涨幅只有16%,形成了强烈反差。
随着下游利润空间的增大,造成近期氯化苯市场需求的增量,这也是此次氯化苯行情上扬的重要原因之一。
除上述因素以外,近期氯化苯市场价格强势上扬,还受到宏观经济环境、国际原油市场石油苯走势等外在因素的影响。
今年国内石油苯的价格涨幅达27%,目前执行价格10700元。
这对近两年一直与其保持2000元左右价差的焦化苯来说,拓宽了价格上升空间,未来将带动焦化苯市场价格进一步上扬。
因此,氯化苯市场仍然面临着成本进一步提高的可能,后市行情将继续处于上升通道[3]。
3.总结
1)氯苯为无色透明的液体,易挥发、易燃,空气中爆炸极限为1.83%~9.23%(体积)。
可溶于大多数有机溶剂,不溶于水。
氯苯主要用于生产硝基氯苯。
2)我国氯化苯系列产品产能占全球总产能的一半以上,成为全球氯苯主要生产与供应国。
近几年来,我国氯苯产能产量达历史新高,但美国、西欧和日本氯化苯市场的需求呈下降态势。
3)氯苯的生产方法有氧化氯化法、酸催化的次氯酸的氯化、沸腾氯化法三种。
由于氧化氯化法腐蚀性强,对设备材质要求很高;酸催化的次氯酸的氯化法使用的溶剂毒性较大,很容易对环境及人类带来危害。
因此,目前生产氯苯的工厂都是采用沸腾氯化法。
4)沸腾氯化法生产时一般以三氯化铁为催化剂,反应温度在75℃~85℃之间,并且在苯的氯化反应前期必须使反应温度较快地升至70℃以上,使催化剂的活性能尽快发挥,氯气能进入完全反应阶段,减少系统中氯的过剩量,以保证苯的氯化反应速度和反应的安全。
同时要求原料中含噻吩或水必须控制在小于0.01%。
5)生产过程中产生的废水可用作生产副产盐酸;废气在回收部分苯后,用碱吸收废气中的盐酸;废渣可以用填埋法、焚烧法将其进行无害化处置。
4.参考文献
[1]申玉海.氯苯生产装置简介[J].中国氯碱,1994,(3):
17-18
[2]钱松.我国氯苯的市场分析[J].精细化工原料及中间体,2007,(4):
43-44
[3]刘永明.氯化苯价格进入上行通道[J].中国高新技术产业导报,2008,(D06):
1
[4]刘永明.氯化苯市场喜忧并存[N].中国化工报.,2007,(003)
[5]黄璐,王保国.化工设计.北京:
化学工业出版社,2001
[6]蒋登高,张亚东,周彩容.精细有机合成反应及工艺[M].北京:
化学工业出版社,2001
[7]严戌生.清洁生产在氯苯生产中的应用[J].中国氯碱,2001,(11):
38-39
[8]王刚,刘爽.氯苯生产工艺的优化[J].中国氯碱,2008,(05):
20-21
[9]傅先元.氯苯生产中苯流失的分析与对策[J].中国氯碱,2005,(4):
40-41
[10]司明德.氯苯生产中氯化工艺分析[J].山西化工,1994,
(2):
12-14
[11]张再喜.氯苯生产中的几个技术问题[J].中国氯碱,2002,(5):
19-20
[12]张文革.氯苯生产中的三废污染及其处理[J].化工生产与技术,1998,
(1):
44-50
[13]徐军,徐建如,贾峰,任晓峰.氯化苯生产水洗酸的回收利用[J].中国氯碱.2005,(12):
37-38
[14]C.Seignez,N.Adler,C.Thoeni,M.Stettler,P.Péringer,C.Holliger.Steady-stateandtransient-stateperformanceofabiotricklingfiltertreatingchlorobenzene-containingwastegas.AppliedMicrobiologyandBiotechnology[J].ApplMicrobiolBiotechnol,2004,65
(1):
33-37
[15]张海鹏.一氯苯生产中氯化尾气的处理方法[J].中国氯碱,2004,(4):
37-38
[16]LIUQiang,DENGYu-heng.Improvementoftricklingbiofilterpurificationperformanceontreatingchlorobenzeneinwastegasesusingsurfactant[J].Journalofshanghaiuniversity,2007,11(6):
607-612