ECMN10线路板外层制作能力指南.docx
《ECMN10线路板外层制作能力指南.docx》由会员分享,可在线阅读,更多相关《ECMN10线路板外层制作能力指南.docx(51页珍藏版)》请在冰豆网上搜索。
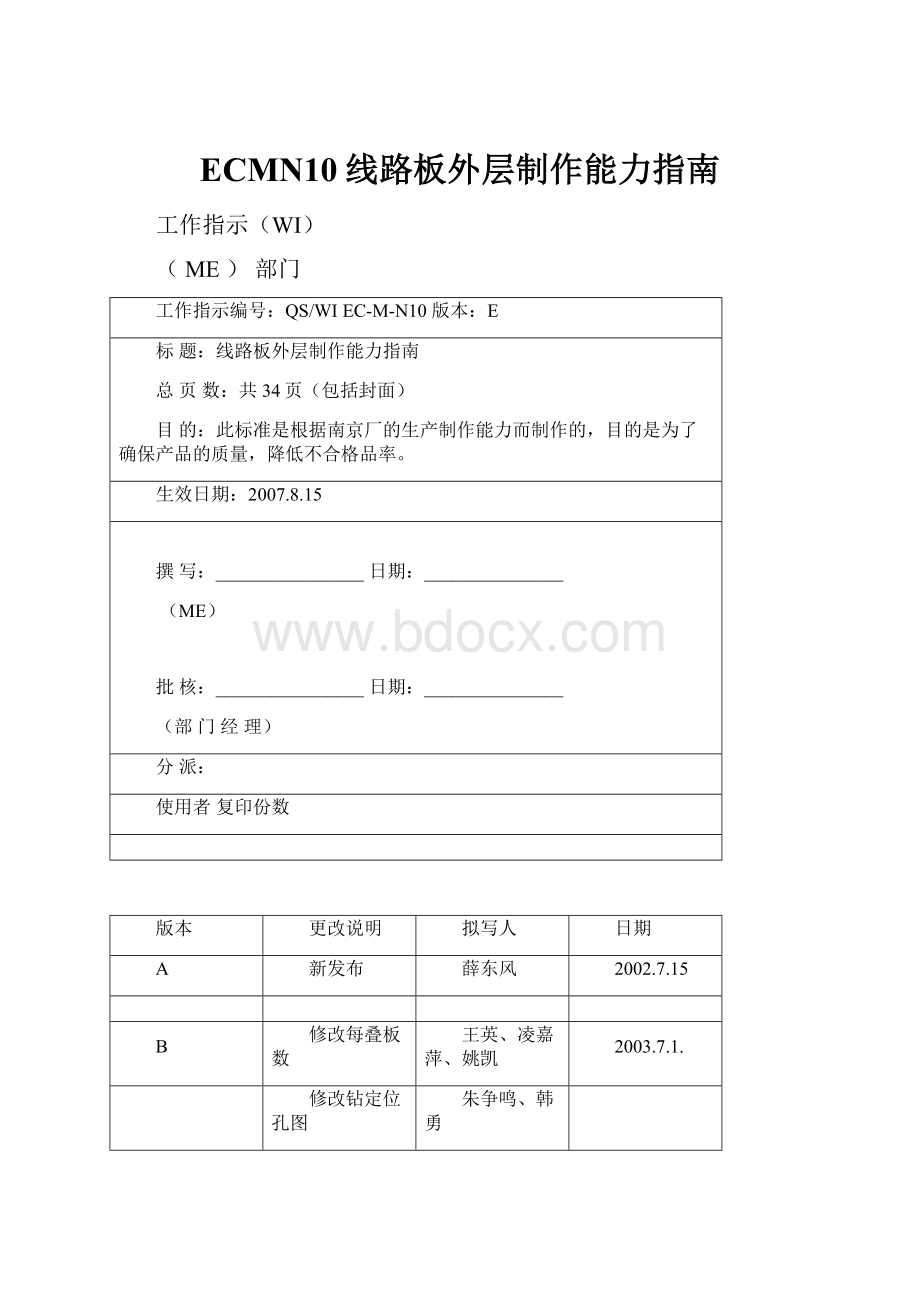
ECMN10线路板外层制作能力指南
工作指示(WI)
(ME)部门
工作指示编号:
QS/WIEC-M-N10版本:
E
标题:
线路板外层制作能力指南
总页数:
共34页(包括封面)
目的:
此标准是根据南京厂的生产制作能力而制作的,目的是为了确保产品的质量,降低不合格品率。
生效日期:
2007.8.15
撰写:
________________日期:
_______________
(ME)
批核:
________________日期:
_______________
(部门经理)
分派:
使用者复印份数
版本
更改说明
拟写人
日期
A
新发布
薛东风
2002.7.15
B
修改每叠板数
王英、凌嘉萍、姚凯
2003.7.1.
修改钻定位孔图
朱争鸣、韩勇
修改外形误差
修改每叠板数
C
修改各工序制程能力
凌嘉萍、王英、姚凯
2006.1.1
韩勇、奚兰玉
D
完善各工序制程能力
凌嘉萍、王英、姚凯
2006.6.22
黄海银、胡家宝、
王俊
D/1
修改绿油挡点制作
胡家宝
2007.4.30
E
增加荣信电镀线制程能力
黄海银、王俊
2007.8.15
增加喷锡制程能力
增加东台钻机制程能力
增加凯码电测机制程能力
E/1
修改槽长小于2倍槽宽坑槽制作方法
王俊、孙刚
2008.9.3
修改半金属化孔/槽制作方法
修改外形铣圆制作方法
增加层压涨缩板钻带调整方法
增加跳步钻孔的要求
增加外形香港V槽机的制程能力
绿油挡点的修改
张平
2009.12.28
E/2
修改二钻铜位开窗要求
孙刚
2010.5.4
修改钻孔叠板数
完善半金属化孔/槽制作方法
目录
1.介绍……………………………………………………………………………………第4页
2.切板……………………………………………………………………………………第4页
3.钻孔……………………………………………………………………………………第6页
4.去毛刺………………………………………………………………………………第11页
5.化学沉铜/孔处理……………………………………………………………………第12页
6.全板电镀……………………………………………………………………………第12页
7.图形转移……………………………………………………………………………第12页
8.图形电镀……………………………………………………………………………第13页
9.退菲林/蚀刻/退锡…………………………………………………………………第14页
10.绿油…………………………………………………………………………………第15页
11.零件符号印刷………………………………………………………………………第20页
12.喷锡…………………………………………………………………………………第20页
13.外形加工……………………………………………………………………………第20页
14.电测试………………………………………………………………………………第31页
15.防氧化………………………………………………………………………………第33页
16.附录:
PCB制作流程………………………………………………………………第33页
1.介绍
这是外层制作能力指南,除非特殊情况,生产过程将遵循此标准进行。
此标准是根据南京厂的生产制作能力而制作的,目的是为了确保产品的质量,降低不合格品率。
任何生产计划偏离了此标准,需提前通知工程部,工程部有责任会同PE、QA等有关部门认真分析研究做出决定以满足工程上与生产上的需要。
2.切板
2.1自动磨边机切削量为2mm,开料图需按拼板尺寸放大2mm切板,保证磨边后尺寸符合拼板尺寸。
2.2覆铜板有纵横向之分,在设计印制线路板时应注意方向的选择,避免印制线路板在加工时或之后产生翘曲、尺寸收缩及机械强度转变等问题。
(一般字符的竖方向为板的纵方向)
A
若线路板是长方形的,较长之方向应与纵方向同向
B
排孔、方孔最好如左图所示
C
若线路板外围有凹凸时,其凹凸处最好如左图所示,以减少如折断等可能造成的损坏。
2.3拼板图尺寸应与干膜尺寸相匹配,保证干膜掩孔并遵循板料纵横向原则。
则板长方向为干膜尺寸+3mm;板宽方向可参照以下尺寸并可根据拼板尺寸作相应调整。
厂家
规格
开料
方式
板宽
板长及适合干膜
16″
18″
19″
20″
21″
22″
23″
24″
408
460
485
511
536
562
587
612
南亚
、
松下
33.5″×48.5″
3×3
280
/
/
/
/
/
/
/
3×2
280
2×2
423
/
36.5″×48.5″
3×3
306
/
/
/
/
/
/
/
3×2
306
2×2
460
/
40.5″×48.5″
3×3
340
/
/
/
/
/
/
/
3×2
340
2×2
511
/
/
/
42.5″×48.5″
3×3
357
/
/
/
/
/
/
/
3×2
357
2×2
530
/
/
/
/
建滔
37″×49″
3×3
310
/
/
/
/
/
/
/
3×2
310
2×2
467
/
41″×49″
3×3
344
/
/
/
/
/
/
/
3×2
344
2×2
518
/
/
/
/
43″×49″
3×3
361
/
/
/
/
/
/
/
3×2
361
2×2
530
/
/
/
/
注:
“/”为不可取尺寸或不符合板料纵横向原则。
3.钻孔
3.1最大的板料尺寸
HITACHI6L-180E:
470×690mm
6L-210E:
530×690mm
6Ne210E:
530×690mm
6Ni210E:
530×690mm
东台DT7600:
550×700mm
3.2最大/最小钻孔
最小孔径:
0.2mm
最大孔径:
6.35mm
3.3叠板数(层数≤6层)
最小孔径
板厚(mm)
叠板数
(块)
φ0.2
φ0.25
φ0.3
φ0.35
φ0.4
φ0.45
φ0.5
φ0.55
≥φ0.6
1
≤1.6
≤1.6
≤3.2
≤3.2
≤4.0
≤4.0
≤4.0
≤5.0
≤5.0
2
≤0.8
≤1.0
≤1.8
≤1.8
≤2.0
≤2.0
≤2.4
≤2.4
≤2.4
3
≤0.5
≤0.5
≤1.6
≤1.6
≤1.6
≤1.6
≤1.6
≤1.6
≤1.6
4
/
/
≤0.9
≤0.9
≤1.2
≤1.2
≤1.2
≤1.2
≤1.2
5
/
/
/
/
/
/
≤1.0
≤1.0
≤1.0
注:
1)使用新野鼎泰0.4/0.45mm新钻咀和研一钻咀,对含有最小普通钻咀≥0.4mm、最小坑槽钻咀≥0.7mm的1.5mm板厚的(客户对孔粗无要求)双面板料号可叠四钻孔
2)若坑槽钻有下列情况时,请按下表设置叠板数
最小孔径
板厚(mm)
叠板数
(块)
≤φ0.65坑槽钻
如钻制方形槽时坑槽钻≤φ0.8
1
≤3.2
≤3.2
2
≤1.6
≤1.8
3
≤1.1
≤1.2
4
≤0.8
≤0.9
3)层数>6层,叠板数根据正常叠板数减1,最少叠板数为1块。
4)多层板板厚按中值计算
3.4孔的最大位置误差(综合)
第一次钻孔叠一块0.05mm
叠二块及以上0.08mm
二次钻孔0.127mm
3.5孔的最大直径误差
直径d≤3.175+0.000mm
-0.0254mm
直径d>3.1750.0254mm
3.6两个直径为d的孔相隔的最小距离为X
如图:
d为任何值时,x≥0.254mm
3.7叠钻坑槽误差:
(单位:
mm)
公差值
坑槽长宽比
坑槽长度<2D
坑槽长度≥2D
坑槽宽度公差
0.05
0.05
坑槽长度公差
0.15
0.127
3.8最小的坑槽宽:
0.5mm;坑槽长度小于2倍坑槽宽度时会产生的角度偏差(使用坑槽钻及坑槽参数)
3.9如遇坑槽长度<2D的坑槽CAM制作人员应先与客户确认能否改为圆孔或加长到≥2D,以提高钻机产能,避免不良品产生。
3.10坑槽钻直径:
0.5mm-2.1mm,>2.1mm坑槽可用普通钻嘴加工。
PE编制钻孔程序时对坑槽长度大于2倍坑槽宽度,范围在0.5mm-2.0mm内的所有钻嘴直径应加0.01mm;对坑槽长度小于2倍坑槽宽度,范围在0.5mm-2.0mm内的所有钻嘴直径应加0.005mm;对2.05-2.5mm的坑槽不必区分槽长是否大于或小于2倍坑槽宽度,所应用的钻咀直径加0.005mm,以便直接读取坑槽钻孔参数。
3.11定位孔位置如图:
(单位:
mm)
多层板定位孔位置图,锣边后应保留备用定位孔
双面板定位孔位置图
3.12半金属孔/槽制作
1)对拼板间距大且板厚≦1.2mm的图号可以采用铣加工的方式制作半金属化槽/孔,即图电制作完后交外形工序预铣,将半金属化槽/孔制作出后蚀刻将孔内翻起的金属毛刺去除。
2)对板厚超过1.2mm以上或拼板间距小只能采用V槽加工半金属化槽/孔的图号,图电制作完后交钻孔工序进行半金属化槽/孔两侧钻孔截铜,钻完后蚀刻将孔内翻起的金属毛刺去除
注:
半金属孔/槽制作流程:
正常流程制作至图形电镀→钻孔/外形→蚀刻→后工序按流程正常制作。
如有特殊情况可与ME沟通。
3.13沉头孔深度误差:
0.2mm
沉孔角度为1650,钻嘴直径应≥3.2mm沉孔角度为900,钻嘴直径应≥2.8mm
3.14钻制腰形孔后孔内留有铜丝需用钻嘴去除
3.15二次钻孔位置上:
为防止干膜图形偏移造成二钻孔位与PAD开窗无法重合,PE设计二钻铜位开窗尺寸时要求小于该处二钻钻咀直径0.2mm。
如二面均为基材,预留扩孔盘单边尺寸一般应设计为大于要求孔径0.2mm,如遇特殊情况最小不能低于0.127mm(如下图)。
如一面为铜箔一面为基材,钻孔时铜箔面必须向上放置,以减少钻孔毛剌;
如二面均有铜箔,则将铜箔面朝一个面的孔挑出分开编写钻孔程序,保持钻孔时铜箔面必须向上这一放置原则。
3.16二次扩孔流程:
蚀刻→绿油→二次钻孔→外形加工
3.17外定位孔与单元内的孔最小距离为12.7mm,防止钻机铜压脚碰撞销钉后受损。
3.18钻制直径>4.5mm的孔时为减少切削阻力,延长主轴寿命可采用二种方法加工:
A扩孔钻孔法,从4.5mm开始每隔0.5mm一支钻嘴递增,直至达到要求的孔径。
B预钻孔法,在所需钻孔位置上事先钻制几个小孔,再用要求孔径钻嘴钻孔。
3.19钻嘴直径补偿标准(单位:
mm)
孔类型
补偿值
板类型
NPTH
PTH
防氧化板
/
0.1
喷锡板
/
0.15
注:
1)最小孔径公差±0.05mm;
2)如果客户标注的公差不是对称分布,则需将其调整为中值,例如:
客户要求孔径公差为1.0+0.2/-0,则调整为1.1±0.1,然后按上表给出补偿尺寸。
3.20钻坑槽补偿标准(单位:
mm)
坑槽长宽比
补偿值
补偿项目
坑槽长度<2D
坑槽长度≥2D
PTH
NPTH
PTH/NPTH
槽长补偿
直径≤3.15补偿0.075
直径≤3.15补偿0.075
不做补偿
注:
1)以上仅作为参考,按以上要求试板,合格后批量生产。
2)如遇坑槽长度<2D的坑槽应先与客户确认能否加长到≥2D,以减少我司编程工作量。
3.21方形槽制作
A对于方形槽一般采用铣加工,特殊情况可采用钻孔加工(PE需与ME协商确认)。
1)加工顺序:
A槽→B槽→C槽→D槽,原则为先钻宽方向再钻长方向。
2)方形槽钻孔时,钻嘴选用标准应为:
钻嘴直径<槽宽/2,如客户对内R角有要求时,最大钻嘴直径<槽宽/2+0.1mm,以避免当C槽钻完后D槽受侧向力影响而变形。
3)如槽长小于2倍的钻孔直径则按3.20进行补偿。
B对于方形槽内R角<0.4mm先用钻嘴钻制出内R角再采用铣加工或直接采用冲加工,以提高钻孔产能。
3.22T型槽及L型槽的加工
3.22.1T型槽加工,首先先在两槽相交处各打一个板上最小孔,然后PE在编钻带时,先钻小坑槽,后再钻大坑槽,A槽补偿同3.20坑槽补偿标准,B槽补偿在3.20坑槽补偿的基础上槽长加大0.025mm。
对于B型槽加工方向如T型槽图中箭头所示。
3.22.2L型槽加工,首先先在两槽相交处各打一个板上最小孔,然后PE在编钻带时,先钻小坑槽,后再钻大坑槽,钻孔补偿同3.20坑槽补偿标准。
槽加工方向如L型槽图中箭头所示
B槽
B槽
A槽
A槽
3.23如为方便客户分板而钻制的工艺邮票孔,如3.6图中X应≥0.5mm,以减少因孔距较近导致真空吸力减弱而产生的塞孔现象。
3.24层压涨缩板钻带调整方法
A层压提供料号实际的涨缩值,PE人员根据涨缩量调整钻带。
B当料号需调整的行(列)为1时,PE人员根据涨缩量计算涨缩系数按比例对钻带进行缩放处理。
C当料号需调整的行(列)为偶数时,PE人员根据涨缩量÷行(列)数得出行(列)的调整量。
调整时位于中心线的第1行(列)在原位置上移动1/2调整量,由内向外第2行(列)在原位置上移动3/2调整量,第3行(列)在原位置上移动5/2调整量,依次类推。
(如图1)
D当料号需调整的行(列)为>1的奇数时,PE人员根据涨缩量÷[行(列)数-1]得出行(列)的调整量。
调整时位于中间的行(列)或单元位置不做调整。
位于中间的行(列)旁的第1行(列)在原位置上移动1/2调整量,由内向外第2行(列)在原位置上移动3/2调整量,第3行(列)在原位置上移动5/2调整量,依次类推。
(如图2、3)
第2行
第1行
第1行
第2行
涨缩板的调整如下,见示意图:
第第第第
2112
列列列列
X轴涨时,左右四列向外移动(图1)
如X、Y轴均涨,正中间不移,其它套装按图示移动(图3)
备注:
如板缩按相反方向移动
3.25输出CEM-3板料料号钻孔程序时,需在钻孔程序头加入1.05mm直径以下钻咀钻孔参数(坑槽钻咀参数不变),使钻机读取程序时自动加载CEM-3板料钻孔参数,减少操作人员操作失误造成的品质问题。
(CEM-3板料钻孔参数见钻孔工序工作指示)
4.除毛刺
4.1最大板宽:
24″(610mm);
4.2最小板尺寸:
8″×8″(200×200mm)
4.3板料厚:
0.5-3.0mm
5.化学沉铜/孔处理
5.1板料尺寸:
宽×长:
A″×24″(A×610mm)(宽超过18”,产能降低50%)
宽×长:
12″×13″(300×325mm)(最小)
板厚:
0.2-3.0mm
5.2化学沉铜最小孔径为0.25mm
5.3最小背光8.0
5.4要求钻孔粗糙度为≤1.4mil(35um)
5.5最大厚径比6:
1
6.全板电镀
6.1板料尺寸:
板长最大:
610mm
板长最小:
406mm
拼板长度越接近610mm,电镀均匀性越好
板宽最小:
300mm
以保证电镀时有2个夹点,以防1个夹点出现接触不良
电镀缸最大有效尺寸:
90″×24″(2286×610mm)
板厚:
0.8-2.5mm(0.8mm以下不建议)
6.2全板铜厚孔壁厚度7-12um
7.图形转移
7.1最大板:
20×24
最小板料尺寸:
250×330mm(自动贴膜机要求)
7.2板料厚:
0.4-3.0mm
7.3对位菲林遮光区的宽度要求比板边至少大5mm
7.4所有印刷定位孔、V槽定位孔等为不镀通孔(即都需掩孔)
7.5单元外的所有图形或孔边,均需在距板边3mm以内
7.6粘贴的干菲林要宽于干菲林需覆盖的部位及小于板宽3mm
7.7单元的边与板边的最小空间不少于10mm(或单元内需电镀部位与板边最小空间大于10mm),以便于曝光时开天窗
7.8生产菲林最小线宽/线距0.125/0.125mm,应考虑蚀刻后线宽减少值及客户要求的完成线宽、线距值等因素来相应作出菲林补偿。
(极限为0.1mm,品质会有很大下降)
干膜制版后线宽/间距变化最大±0.01mm
7.9如果成品锡圈要求是nmm,则
底铜厚
菲林锡圈(min)
制版后锡圈(min)
0.5oz
n+0.13mm
n+0.03mm
1oz
n+0.135mm
n+0.035mm
2oz
n+0.15mm
n+0.05mm
如客户允许,焊盘(VIA孔)都应设计为水滴状,以减少破孔机会。
7.10最小的栅格:
0.2mm(隔离盘线宽也按此设计)
7.11对于要遮盖≤6.25mm的圆孔,最小的菲林掩孔盘直径,单边至少应大于孔径0.254mm,不允许单面掩孔;一面有盘,一面无盘的单面孔,无盘面菲林盘比孔径小0.2mm,否则采用二次扩孔方法。
7.12板厚大于1.0mm的板可用菲林掩小于Φ6.25mm的圆孔,Φ4×10mm的槽孔;板厚小于1.0mm的板可用菲林覆盖小于Φ4.0mm的圆孔,Φ3×6mm的槽孔。
7.13图形外四边应有菲林对准标识,标识焊盘为环宽0.1mm.绿油对位标识为圆铜位需印绿油且绿油曝光菲林开最小窗口,以便检查对位准确性。
干膜对位
0.1mm的锡圈
绿油对位
8.图形电镀
8.1最大板料尺寸:
板长最大:
610mm(大线)660mm(荣信线)
板长最小:
406mm
板宽最小:
300mm
电镀缸最大有效尺寸:
144″×24″(3658×610mm)(大线)
80″×26″(2032×660mm)(荣信线)
板厚:
0.8-2.5mm(0.8mm以下不建议)
8.2板边的最小距离:
10mm
板边留给夹具的最小距离为12mm
8.3电镀铜整流柜最大800A(单面),最小100A(单面),电镀锡整流柜最大600A(单面),最小100A(单面),一缸板毛坯面积应≥1.4m2
8.4计算电镀面积时,需计算孔壁面积(按专用计算公式算)
8.5需用2个以上夹具夹板,板宽度不小于300mm(2个夹具中心距离为6″)
8.6如果线路图形的密度(不包括边框导电部分)≤20%,需增加辅助图形进行电镀,即“假铜位”,如果有条件,把铜位放到可分割出来的地方,如无法增加假Cu位,则通知ME确定电镀方式
8.6.1拼板及线路密度的原则
A拼板时最小拼板尺寸:
12"×16";
B如遇特殊情况无法保证最小拼板,请至少保证拼板宽方向≥12";
C如线路密度(不包括边框导电部分)≤20%,或图形中有孤立线条存在需增加辅助图形进行电镀。
8.6.2样板电镀电流密度参考表格(批量生产板或为转批的试流板以电流纸为准)
下表中的线路面积以面积较小的面计算
尺寸
线路面积
大线电流密度(ASF)
荣信线电流密度(ASF)
全板
图形
镀锡
全板
图形
镀锡
<300mm
<30%
26
20
13
26
20
13
>30%
26
22
13
26
22
13
300-400mm
<30%
26
18
13
26
18
13
30%-50%
24
20
13
24
20
13
>50%
24
22
13
24
22
13
>400mm
<30%
20
20
13
20
20
13
30%-50%
20
22
13
20
22
13
>50%
20
24
13
20
24
13
双循环板(厚径比≥6:
1或最小孔径0.2mm)
12
12
13
12
12
13
线宽或间距小于0.1mm的板
24
20
13
24
18
13
有孤立线条的板
24
20
13
24
18
13
B
A
8.7除非客户提出特殊的厚度要求,图形电镀一般加厚到≥20um(孔壁厚度)
D
C
厚径比<5:
1,孔径≥0.4mm,均镀性>80%
厚径比>5:
1,孔径<0.4mm,均镀性>70%
F
E
均镀性=(C+D)/2
(A+B+E+F+)/4
8.8图形内有线宽/间距≤0.15mm部分,应避免将其拼版在靠近边框处
8.9拼版单元边离导电框除去0.40mm+铣刀直径外,多余部分应增加辅助图形进行电镀且辅助图形密度应与生产板图形密度相近
8.10后工序铜厚减少量(出货铜厚应考虑后序的减少,在图电时适当增加)
WF前处理:
0.4-0.6um/次;OSP前处理:
0.7-1.5um/次
AOI前处理:
0.8-1.2um/次;喷咀前处理:
0.8-1.5um/次
注:
正常情况下前处理过一次
9.退菲林/蚀刻/退锡
9.1最大板宽:
610mm最小板宽:
150mm
最大板厚:
3.2mm最小板厚:
0.4mm
9.2表示底层铜的厚度和图形电镀方法的标记将被加在线路板两面任何一面板边的空白处,例如:
“1/2安士”表示所采用之底铜每Ft2重量1/2安士,最好采用蚀刻字方法(包括其它文字符号)
9.3在板两面的板边空白处会加上适当的标记以表示是防氧化“Cu106”、喷锡“SCL”
9.4蚀刻后,线宽要减少,由于受板的尺寸、板的边以及线路分布的影响很大,很难找到一个确定数据,线宽减少按以下的参考数据估计:
铜厚(安士)
估计线宽减少(mm)
0.5
0.03-0.05
1
0.05-0.07
2
0.08-0.