物料管理的问题与对策.docx
《物料管理的问题与对策.docx》由会员分享,可在线阅读,更多相关《物料管理的问题与对策.docx(35页珍藏版)》请在冰豆网上搜索。
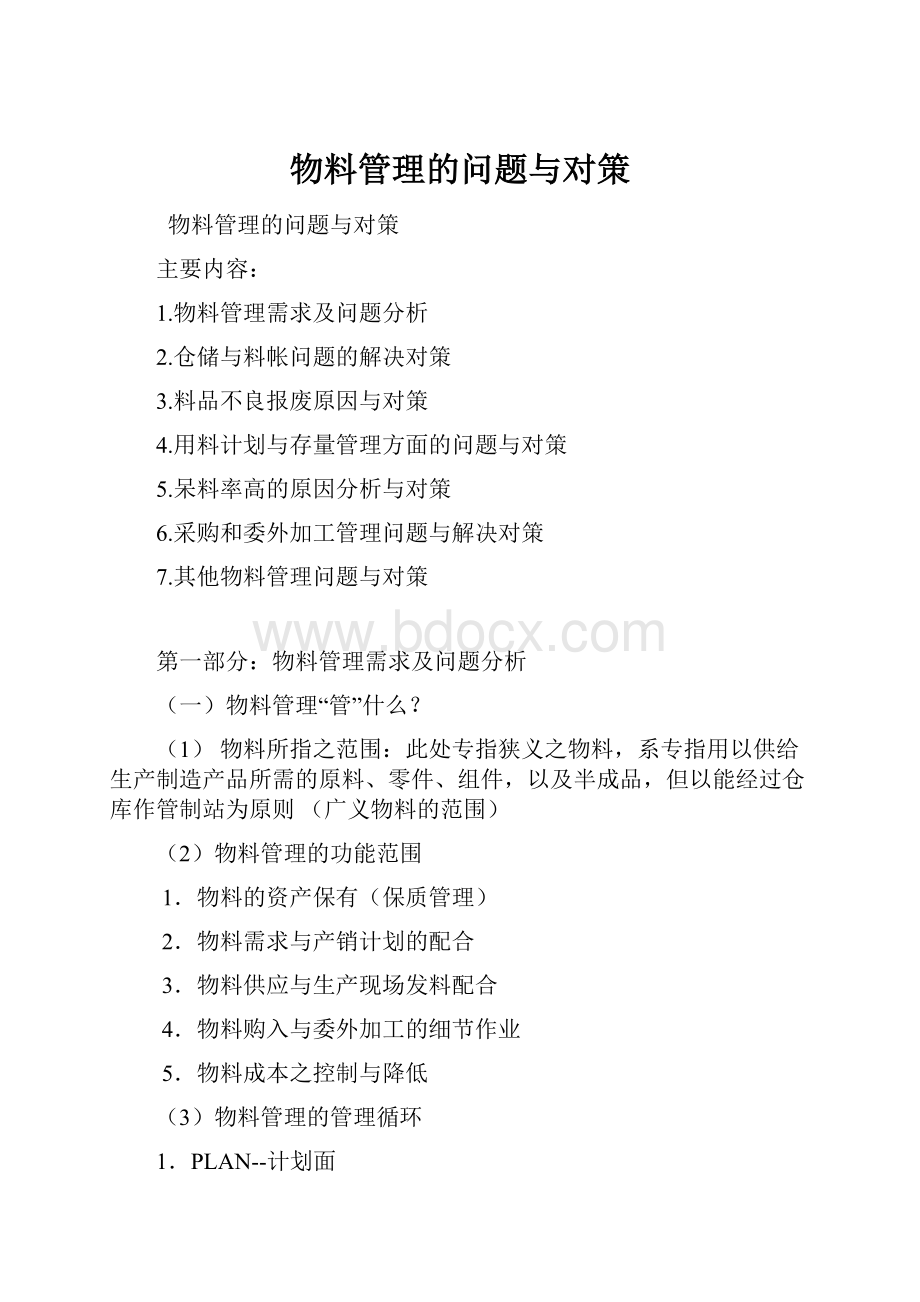
物料管理的问题与对策
物料管理的问题与对策
主要内容:
1.物料管理需求及问题分析
2.仓储与料帐问题的解决对策
3.料品不良报废原因与对策
4.用料计划与存量管理方面的问题与对策
5.呆料率高的原因分析与对策
6.采购和委外加工管理问题与解决对策
7.其他物料管理问题与对策
第一部分:
物料管理需求及问题分析
(一)物料管理“管”什么?
(1)物料所指之范围:
此处专指狭义之物料,系专指用以供给生产制造产品所需的原料、零件、组件,以及半成品,但以能经过仓库作管制站为原则(广义物料的范围)
(2)物料管理的功能范围
1.物料的资产保有(保质管理)
2.物料需求与产销计划的配合
3.物料供应与生产现场发料配合
4.物料购入与委外加工的细节作业
5.物料成本之控制与降低
(3)物料管理的管理循环
1.PLAN--计划面
*拟订切实的物料存量计划,尤指存量水准作为管理基准
*进行仓储规划
*做好用料需求计划(以生产计划或订单排程为基础,减少无效库存)
*依据DPS做出“备料计划”
2.DO--实施面
*依据存量管理或MRP进行请购订购等
*进行进料检验等
*惊醒料品入库及帐务报表编制工作
*仓库整理及盘点
*依据生产指令,进行备料发料作业
*执行其他出入库作业
3.CHECK--查核面
*查核低于安全存量或依据MRP展开后不足的料品,提示采取行动
*比照近期生产进度需求,分析缺料的可能性
*查核应进料而未进料状况,或因生产进度变更从而进料期必须修正的料品,提示稽催
*查核料品采购价格、品质、数量短少之差异所在,以利研拟对策
4.ACTION--对策行动面
*针对无法如期进料之料品,修订原定进度排程
*针对紧急需求,到供应商处进行“现地跟催”
*针对来料不良状况,对协作厂商进行辅导
*针对紧急缺料部分,研拟替代料品对策
(二)物料管理的重要性
1.物料成本占制造成本的最大比率,对利润的影响也最大。
*一般在装配业与一般加工业其物料成本经常占总制造成本的50%以上,个别行业可达90%,如面粉加工业等。
就重点管理的原则而言,物料成本管理为绝对的重点,是企业经营成败的关键。
2.没有适时、适量、适品供料,就没有生产力可言。
*制造业的中心思想就是生产力(运用管理手段与技巧,使资金、人才、设备与物料,能妥善有效运用,提高绩效创造利润,这就是生产力),
*没有合适的物料及时供应,生产力就低落,交期延迟,造成损失。
3.物料积存常是企业财务最大负担。
*存货与资金积压几乎是同义语,大部分工厂至少都有半个月以上甚至数个月的物料库存,,为此而积压的资金必然会产生如存款利息、投资收益等机会损失。
4.物料的赔损,消蚀应有的利润。
*包括呆料、报废等
(三)物料管理的目标
1、适品/适量/适时供应生产所需,使产销顺利-以最少的库存达到产销需求,抑制停工待料
2、防止呆料/死藏品之发生-抑制直接浪费
3、提高用料周转率,提升财务运营绩效,减少财务负担及成本
4、控制及降低物料成本,确保或提高利润-含最小仓储成本在内
5、确保企业资产之数量及价值-资产确保
(四)高阶经营者对物料管理的需求
1、产销顺畅方面
*不要因停工待料而导致交货期延误
*不要因缺料而影响营业接单
2、生产方面
*不要因待料,而浪费人员/机台生产力
*不要因材料问题而生产排程混乱、生产效率低落
3.成本控制方面
*用料成本要严密控制
*不要因材料不良、在制程中重制重修,造成人工及其他材料浪费
*呆料废料是最大浪费
4.经营风险方面
*呆料风险要尽量减少
*因缺料而延误交期,使客户迟疑,是经营最大风险
(五)中阶主管对物料管理的需求
1、使部门业务(工作)顺利
*缺料/材料不良,造成一切工作不顺利
*为了紧急处理缺料/不良料问题,一切工作都混乱掉
2、减少自己管理困扰
*不要因材料原因而导致工作绩效不良,引起上级指责
*部属工作不顺,使自己忙于“救火”,造成困扰
*部门业绩达不到目标
(六)营业部门的需求
1、不要因为缺料待工而延误订单交期
2、不要因为料品品质问题而造成客户抱怨
3、不要因为成本高而导致竞争力低落
(七)基层人员的需求
1、工作顺利方面
*最好每个分派的工作都有适当的供料,使自己的工作顺利进行
*由于缺料或不良,导致工作调来调去,麻烦又没成就感
2、不要因材料问题而冤枉受责
*不良料品导致制程品质不良
*不良料品导致多余加工或检查
(八)物料管理常见缺失及后果
1.料帐不准
--不管是〖安全存量法〗还是〖MRP法〗都会有困扰
--帐高于物-未及购备,停工待料交期延误
--帐低于物-多买,变成呆料
--更多的管理稽核与调整工作
2.料品不良报废多
--报废品损失
--不良品混入,到现场影响投产效率
--来不及顺畅供应投产-停工待料交期延误
3.呆料比率高
--潜在的废料损失
--仓库管理效率低,占用Space
4、库存积压,周转率低
--资金运用的停滞~不利经营;---经营风险增加
5、仓储备料时间长
--生产线待料,损失工时生产力
--仓储人力工时浪费
6、停工待料损失工时多
--现场人机迄生产力损失
--交期延误
(九)一般物料管理系统架构
第二部分仓储与料帐问题的解决对策
(一)料帐不准的主要原因
1、由于传票表单流程方面的缺失
--表单缺损
--表单输入打错
--填入内容有错
2、由于储位与料号方面的缺失
--储位少,另放他处
--一料多号或一号多料
3、由于包装容器方面的缺失
--关键料项未用标准容器
--零星库存不易检查
4、帐务人员的缺失
--没有及时入帐
--出入库数量没有核对
--无单作业
--缺乏料帐稽核的努力
5、仓库设施的问题
--仓库与现场未隔离或隔离而不落实,易遭盗失
--储位不足,随便放置
6、缺乏严密可行的料帐管理工具
--缺乏储位库存卡比较
--手工帐无法对应多料项
--零星库存无法管控
(二)解决料帐不准的主要对策
1做好储位管理—不会取错放错记错帐
2做好料帐系统---建构正确无误的料帐核心
3出入库管理流程之严密化---出入库凭证不会“进来垃圾出去的还是垃圾”
4运用辅助性的盘点手段
5运用辅助管理工具---例如标准容器、条码标签等
6电脑化系统之运用
7自动仓储之运用
(三)仓储管理的范围
1、仓储规划与储位管理
---使不同类的生产用料、呆料、不良品得以区分,使仓储更具有生产效益。
集中人力管好活料之原则。
---原物料库存
A生产用主料区B生产用辅料区
C耗材区D废料区
E进料检验区G备料区(现场备料区)
H呆料待处理区I工具庶务用品库存
2、物料先进先出管理
---防止废料不良品发生
---配合设计变更,优先消耗呆滞旧料
3、料帐管理---及时准确登帐,日清日毕
4、库存管理资讯提供---库存量、呆料等统计
5、盘点与调整管理
---配合财务作业需求
---及时调整,避免资讯提供错误
---发掘仓储料帐管理上的缺失
(四)仓储管理的原则
1、基本功能原则
---数量确保之原则
---品质确保之原则
---易于寻找之原则
---善用仓储空间之原则
2、扩充机能原则
---协助存量管制的功能
---协助警示异常处理的功能
---快速备料减少工时损失的功能
---协助警示缺料的功能
---提高盘点效率
(五)仓储整顿与盘点
1、仓储整顿的方向
---使呆料浮现
---使料帐更易稽核
---使先进先出更具体落实
---使仓储空间更充分有效的利用
---使仓储管理更具有“生产”效益(理念)
---不良品的浮现与隔离
2、仓储整顿的具体作法
---呆料移仓
---同料项的储位并邻
---不良品的标示、移仓
---容器的实装化
---料帐的复核
---空储位的再运用合并
3、仓储整顿的时机
---常时盘点时(每日或周定时执行、略盘原则、有针对性原则、差异严重的进行仓储整顿之调整)
---循环盘点时(制定储位料区轮流盘点Schedule,依时间表每月定时执行预定盘点料项,每料项每月至少盘点一次,盘赢亏要深入追踪)
---特殊时机
例如:
设变、OEM订单料项整顿
4、盘点的目的
---会计决算用
---料帐调整用
---稽核仓储管理问题
---提升仓储管理效率,解决经营有关困扰
(六)料帐管理的基本理念(方法)
1、料帐管理程序
A建立管理卡、帐
B设定出入库凭单传票及流程
落实出入库异动作业
C提示管理用报表
D采取对策措施
E料帐稽核
2、库存管制卡之运用原则
A新建卡—新料项产生或年度盘点完成时
B旧卡换新卡—旧卡填完转入新卡时
C与料帐调整同步处理(异动发生制原则而非凭证发生制)
D维持卡号独一性—连续编号、严密管制
E与事物之完全关联—卡必有料、料必有卡
F副卡之使用时机
3、建立严密的出入库管理流程
A设计导入适宜的出入库凭据表单
B设计导入适宜的出入库流程及登帐流程
手工表单的适正联数、审签流程等
C登帐前的表单复查、确认
D及时登帐
--料帐卡同步作业
--帐卡作业“今日事,今日毕”
--On-line方式的电脑登帐
4、其他提升料帐准确性之手段
A标准容器的运用
B料帐稽核
C料帐管理电脑化作业
D批次仓储法之运用(或采用两段式仓储法)
E自动仓储
F特别功能报表(呆料分析表、安全存量警示表)
(七)备料管理不良之改善
1、备料管理不良的一般现象
A备料时间长
B欠料补料的困扰
C成本无法控制
2、原因分析及对策
A仓储规划不佳:
储位混乱,一品料多位且远隔,不容易寻找,搬运道路狭窄或阻塞
B搬运设备落后
C储位标示管理不佳,新人员找不到
D未建立事前备料制度
E运用批次仓储的做法
F善用“缺料分析报告”
思考题
1、公司是否已明文订定“物料管理制度准则”?
这些制度在“管”哪些物料?
用什么“工具”去管?
该工具是否能够很“扎实”地“管理”它?
2、谁都知道PDCA管理循环,贵部门对物料的管理,进行了哪些“PDCA”的工作?
请分类列出作为部门内部讨论,以求得共识。
3、请您尝试列出贵部门在PDCA管理各阶段的检核要点,明示它的目的、可能发生的问题、注意要点等。
最好制成表格供您工作参考。
4、我的料帐放置在哪里?
谁在管?
为什么由他管?
他在何时做登帐处理的动作?
他还要提供什么资料给哪些部门?
5、如何严密管制“库存管制卡”的启用与转换?
为什么要控制?
6、针对料帐的应用,我公司具有哪些库存管理资讯报表?
7、我们是否用到“循环盘点”“常时盘点”?
如何运用?
如何去查核他是否落实执行?
8、缺料分析应该何时由何部门执行?
根据什么去进行分析?
缺料明细提出后,由谁主持拟订解决对策?
9、我们是否已经执行投产前备料的工作?
依据什么去备料?
有哪些困扰?
10、公司领发料的依据是什么?
标准投产的料由谁来主导?
超损耗领料如何处理?
如何查核管制?
第三部分.料品不良报废原因与对策
(一)料品不良报废原因
1、仓储环境管理不佳
2、仓储搬运之问题
---搬运设备器材之损伤
---搬运人员之失慎
3、未执行先进先出管理
4、工程设计变更之管制不佳
5、存量计划策略之失误
6、进料管理把关不严
(二)主要解决对策方向
1.仓储环境整顿
---依料品特性存放适合环境之仓库
2.仓库内存放及搬运工具改善
A通道合理化
B存放料品方式-料架,标准容器,栈板,堆叠箱
C搬运工具-叉车,多层标准台车
---减少因搬运而产生之破损/不良
3.储位实施先进先出管理
---库存卡之颜色管理
---定期移仓,以MRP法防治呆料之产生
4.--MRP的精髓-适品,适量,适时
--订单\批次变更及时处理
5.运用仓储整顿
--及时发掘呆料/不请料,予以处理
6.做好进料品质管理
--做好供料厂商制程能力掌控
--进料检验的落实执行-检验标准、抽样检验方法
第四部分用料计划与存量管理方面的问题与对策
(一)、库存积压主要原因
1、错误的采购决策-判断失误、非理性采购
2、景气变化与市场变化
3、营业预测的偏失
--销售预测模式/方法粗糙
4、不适宜的存量管理模式
例如:
安全存量法的基准设定失误
不宜用安全存量法而偏执采用
5,MRP系统资讯偏差或执行不落实
例如:
料帐不准
6、售后服务需求的特殊影响
(二)提升销售预测准确性的关键
1、提升销售预测者的正确心态
2、提供预测者有效资讯协助预测
--主要客户的近月平均(各别产品)销售量资讯
--作出趋势分析
3、建立正确的销售预测模式
--正确表格/合宜栏位
--运用异状稽核,减少基础资讯错误
--运用“客户盘点”作佐证
(三)必须选用适宜存量管制模式
僵化勉强使用一种量管制模式是错误的看法(包括管理成本高)
1,如必需的法
2,复仓法(二个箱柜系统)
3、安全存量法
4、定量订购法
5、定期订购法)
6,MRP法(材料需求计划)
7,即时看板方式-使库存为零的方法
(1)ABC与存量管制模式之选择
1,ABC分类
A类料品—高价/变化大无法掌握
B类料品—中价/需求较稳定/领引计时长
C类料品—低价/领引计时短/市售标准品
2,ABC分析与存量模式之策略
A类料品—无库存/严格依需求管控
B类料品—安全存量/自动管制/例外管理
C类料品—低成本管理法
(2)A/R法的选择与运用
1,A/R法的适用条件
纯OEM委托订单生产
高单价料品(一类)
流行类产品,几乎无重复性
2,A/R法的程序
订单承接
依订单需求建立BOM
依BOM与生产批量,展算各料品需用量及需用时日
依需用量采购/托外加工
(3)复仓法的选择与运用
1、适用范围
低单价料品(C类)
市售标准品(低价)
不易计量与控制之料品
2、复仓法的原理
目视管理
低成本管理
现场主义
(4)安全存量法之选择运用
1、安全存量法的原理(如下图)
2、安全存量法具体程序
A、设定料项安全存量基准
依LeadTime/期中平均使用量
订购点/最低安全存量
B、设立料项管控制度/流程
入出库登帐
料帐管制簿/电脑帐/库存管制卡
C、低于安全存量基准即提示请购
3、安全存量法适用料项性质
A通用性很高的料项
B生产计划稳定,产品变化不多,或者产品变化多但是用料却很一致(如棉纺织业)的料项
C存料价值中等(B类)
D产品生命周期长,存料比较不易过时者
E领引时间很长的料项
(5)定量订购法
1、特征
A不需要具备变动的意识即可实施管制
B需要量变动较为剧烈的料项不适用此法
C采购费用实施成本为最低
D使自动订购系统成为可能
E使事务作业更平均化
F库存量难免较多
2、适用范围
A耗用量比较固定的料项
B购备期短,易保管的物品
C单价较低的料项
(6)定期订购法
1、特征
A订购时间—以一定时间为频率
B订购量—依据生产计划和需求预测计算
C订购作业—事务手续有烦琐的倾向
D库存量—一般会使库存量减少
2、适用范围
A高单价的一类料品
B购备期比较长的料品
C通用性小,易腐化的料品
D需求变动大,较不安定的料品
E可以实施预测的料品
(7)MRP法之运用件
1、适用条件
A多项料品组成—产品的加工装配业
B不同产品间有共用某些料品
C产品寿命周期短,经常设计变化(ECN)
D呆料管理成为重点
E要求大幅压低用料库存
F要求停工待料降为最低,又不能积料太多
2,MRP的系统架构
A、计划面
主排程生产计划
用料结构(BOM)与用料需求展开(MRP)
B、执行面
库存料帐管理
库存有效数管理
采购作业与托工加工作业
C、控制面
细排程(DPS)与缺料分析
备料管理与发料管制
D、分析面例如:
用料成本差异分析
MRP核心与周转流程(如下图)
MRP与采购,制造作业关联图(如下图)
MRP运作流程(如下图)
3、主排程计划的复核
A与产能负荷的复核
(尤其大制程生产线的产能/负荷限制)
B与用料领引时间的复核
C与生产工具的复核
(例如:
模具数/模具CycleTime)
4、用料需求展开
A毛需求量与需用时段
毛需求量=排程量Ⅹ标准单位用量Ⅹ(1+损耗率)
B净需求量与需用时段
有效存量=现在库存量-制令指派未领量+已订购未交量
净需求量=毛需求量-有效存量=毛需求量-有效存量
5,MRP对物料管理的贡献
基本理念架构
适品–依BOM
适量–有效存量管制
适时–依排程估定应进料日期
减少原物料积压提高用料周转率
抑减呆料发生机率
依照BOM及生产批算出用料需求
已经关连到订单生产批变化
配合排程减少停工待料损失
包括生产批的排程变化
(八)丰田看板方式
1、适用目标
--库存量(几近)为零(含在制品)
--后制程不急用之物料,绝不生产(供应),但后制程需用之物料,前制程应立即供应
2、适用条件
--高价料品
--极低批量柔性生产(使了制造混合)且订单变化很大
--产品规格多,用料结构复杂
3、看板方式要点
A后制程向前制程"领料"
B前制程仅做"补充"后制程来领的量
C把供料厂商当做本厂的"前制程"
--供料厂商只补充“被领用”的量
--因此不会有“库存”,甚至不必“仓库”
D把生产批量细分化/微小化
--依每批批量估定“需料”
--每批的排程时段为“日”,甚至为“小时”
E以"看板"(最小批量)为领料/请制基准
第五部分呆料率高的原因分析与对策
(一)呆料比率高的原因
1、设计变更,管理失常
---FIFO管理不落实
---ECN时间差,或资讯流有误(物控,采购,IQC等)
---设计错误的牺牲品
2、采用不适宜的存量管理模式
---采用安全存量管理模式
---安全存量基准不适宜
---料帐不准,使MRP不能落实
3、销售预测、生产计划、订单管理之缺失(预测方式错误、取消订单没有与客户约定限制等)
4、呆料管理松懈或方法不对
5、未积极有效处理呆料(不甘心呆料处理的损失,等待“转机”;或主管、幕僚偷懒松懈)
(二)防治及解决呆料的对策
1,运用严密的ECN管理消除呆料
A与ECN同步的呆料移出,处理
---ECN通知--副联给生管采购关联旧料发掘
---移出呆料区---呆料及早处理
B运用电脑化BOM关联处理,找出呆料
---—使用档的建立--见企业资源规划资料查询
---ECN登录时的料项用途查询
---无用途的旧料移出呆料待处理区
2、设置呆料区并严密管理
必要性
---使其与活料分离管理
---特别警示
---再处理的严密稽催
B呆料来源
---ECN的结果
---时间性呆料、不良品呆料
---仓储整顿的结果
---订单变更的后遗症
3,运用MRP方式从根本上消除呆源
MRP可以杜绝呆料的理由
---BOM与ECN同步,旧料不会列入依赖性需求
---电脑化MRP展开,减少手工错误
---依定单展开用料需求,不必要的不购入
B严密管制订单变更
---订单缩减、规格变更应立即处理
---由电脑展算缩减量的BOM依赖性需求,提出异常报表
---依异常报表紧急处理“已请购”和“已订购”的料项
---已入库的料项移至呆料区
4、提升预测准确性抑减呆料
预测购料的必要性
---产销提前期短,而材料购备期长,只好以预测方式购料
---供应商姿态高无法配合MRP,只好预测订购
如果预测不准,通用性低的物料就变成呆料
B解决对策
---以特别方式(特别条款)分批进料
---同业互通机制
---提升销售预测准确度
5、其他方式抑减呆料
A运用批次仓储法
B运用仓储整顿法
C及时调整安全存量基准和材料购备期
D设置呆料处理的幕僚团队
---由精英幕僚组成,相关权责主管参与
---定期报告
---区分原因、责任者、防治方式
---提出有效处理对策
---专案追踪处理成效
(三)呆料处理的大方向
1、呆料处理管制---就是定期提出呆料分析表,由高阶幕僚组成处理决策小组,决议处理对策,包括何部门、何人主办、在何时以前完成完成时要提出报告,作为“呆料处理绩效”。
2、参考方法
A与友厂换料
B退予原供应商
C再加工变成次级品
D回炉重制成新规格品
E再加工转作成其他规格的料项
F设法当作替代料
G转作补助能源材料
H报废
第六部分采购和委外加工管理问题与解决对策
(一)停工待料原因分析
1,未运用MRP用料需求规划模式
---分批生产则分批提前进料;分批连续生产则一次性提前进料
2、安全存量及基准资料失去灵敏性
3,BOM没有作到及时有效(ECN缺失)
4、料帐不准
5、采购能力不足
A采购事务流程缺失
B托工管理缺失
C供应商能力问题
(二)抑减停工待料之对策
1。
提升料帐准确性是第一要务
---大部分企业都以"料帐资讯"作为采购需求的根据(包括MRP法和安全存量法)
2。
运用缺料分析法
---作好MRP,使各料项的进料日配合排程在派工前作好缺料分析,建立DPS时也已经作好缺料分析,以使DPS更加顺畅。
。
3.以MRP模式彻底防治停工待料
A传统存量管理模式容易停工待料
---一\R法连安全存量都不设置
---复仓法对投产需求不敏感
---安全存量法仍假定依过去经验的推算,对未曾用过的料无参考资料,对突增的订单无法因应
BMRP的防治架构
---严密的BOM展开(独立或依赖性需求)
---ECN已经与BOM完全整合
---用料需求已估算领引计时,MRP展开直接连接请购,订购,领发料等作业
---订单增量、规格变更便于及时处理
---排程的可行性复核
4、运