电动客车项目可研报告.docx
《电动客车项目可研报告.docx》由会员分享,可在线阅读,更多相关《电动客车项目可研报告.docx(14页珍藏版)》请在冰豆网上搜索。
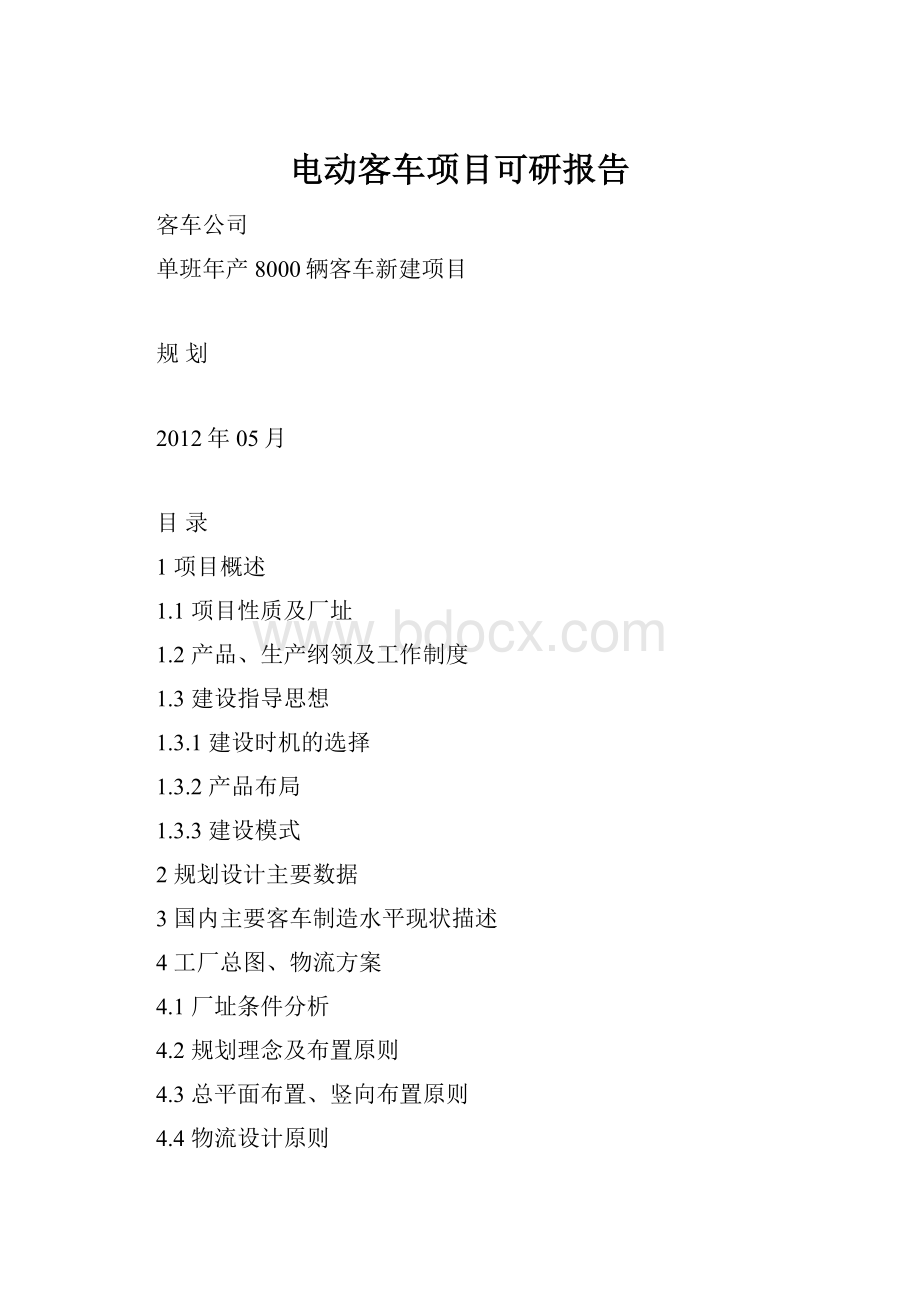
电动客车项目可研报告
客车公司
单班年产8000辆客车新建项目
规划
2012年05月
目录
1项目概述
1.1项目性质及厂址
1.2产品、生产纲领及工作制度
1.3建设指导思想
1.3.1建设时机的选择
1.3.2产品布局
1.3.3建设模式
2规划设计主要数据
3国内主要客车制造水平现状描述
4工厂总图、物流方案
4.1厂址条件分析
4.2规划理念及布置原则
4.3总平面布置、竖向布置原则
4.4物流设计原则
5制造技术方案
5.1准备车间
5.2焊装车间
5.3涂装车间
5.4总装车间
6采用的主要环保、节能措施
7存在的主要问题和建议
8对有关工作进度的设想
附表:
投资估算表
附图:
厂区总体规划布置图(共计五个方案)
1项目概述
1.1项目性质及厂址位置
本项目属于新建项目。
1.2产品、生产纲领及工作制度
全年工作250d,按单班年产8000辆各类客车设计,具体如下:
7m以下轻型客车,1500辆/白班,为冲焊结构车身。
7~9m中型客车,4000辆/白班,为冲压骨架蒙皮结构。
9~12m大型客车,2500辆/白班,为型材骨架蒙皮结构。
为了拓宽产品型谱,增加13.7m的大型客车。
考虑到这类产品的市场容量较小,各生产线只考虑其通过性即可。
当市场上产品供不应求时,只需要通过季节性加开4h工作制的第二班,顺利实现增产4000辆的目的。
1.3建设指导思想
1.3.1建设时机的选择
我国客车行业已经保持了连续20年的快速发展(年均市场增长率约15%),近几年国家又陆续出台了西部大开发、振兴东北老工业基地、全国统筹城乡综合配套改革实验等重大政策,对促进客车市场的进一步发展还在起着深远的影响。
客观地分析,目前呈现愈演愈烈态势的全球性经济发展放缓,国内CPI偏高,GDP有所下调,为节能降耗,为拉动内需,需积极的加大公共交通工具的投入,尤其是新能源客车项目,将得到国家与地方政府的大力支持;
本项目在当前宏观形势下,积极努力通过与国际知名品牌客车集团合资合作。
筹化新的客车产品布局、引进适销对路的产品型谱及开发新能源客车;引进先进生产设备和工艺、利用当前建设成本相对低廉等手段,提升企业的核心竞争力,在2014年年底前建成投产,是比较恰当、稳妥的。
1.3.2产品布局
合资公司在产品技术、生产、销售、采购、研发、组织机构等诸方面各自形成体系、完全独立运行。
合资公司将会拥有客车产品技术使用权,其中、轻型客车产品及新能源技术具有明显优势,应把发展6m~9m中、轻型客车产品作为重点,把发展9m~12m大型、高档、豪华客车放其次位置,作为产品系列及市场补充。
1.3.3建设模式
1.3.3.1一次建成,提高效益
一是符合汽车产业发展政策,即70%以上的客车市场应该由2-3家企业控制,其他企业作为补充;二是形成经济规模,提高效益。
为此,本项目拟一次建成、投产。
1.3.3.2集约利用土地,精益建设
本项目拟定的新厂址,地块条件不太理想,因此在确保设计方案合理的前提下,尽量减少零星建筑物数量,组建大型联合厂房,提高土地集约程度。
工厂设计中贯彻精益思想,以先进适用技术为依托,细心删除冗余功能,注重提升节能、环保和消防水平。
1.3.3.3资金筹措
自筹资金与银行借贷
2规划设想主要数据
建设占地面积:
39.600hm2=594亩
建设使用面积:
32.5000hm2=489亩
总建筑面积:
89700m2=134.57亩
建设投资(估算):
38000万元(未计建设期利息)
其中工程费用(估算):
31000万元
建设周期:
18个月
3国内主要客车制造水平现状描述
3.1下料工艺
均采用轮番方式组织生产。
顶盖及左右侧围板多为卷料,采用开卷纵横剪切机组下料,少数厂家也有采用定尺料的,但成本相对较高。
其它钢板下料采用剪板机。
型材下料采用卧式半自动带锯机,型材弯管件采用液压弯管机成型,摇臂钻钻孔。
小型冲压件多采用1000kN以下开式可倾压力机,薄板折弯件采用液压板料压力机成形。
车间内部运输采用电动平板车和吊钩桥式起重机。
冲压件的模具主要采用简易钢模。
3.2焊装工艺
根据产品工艺的不同,车身焊装线的上线方式主要分为工艺托架上线方式(无底架总成,到总装车间再将车身扣合到三类底盘上)、底架总成上线方式(主要为承载式车身结构,少数为带有副车架的非承载式车身结构)、三类底盘上线方式。
焊装线的输送方式多样化,有轨道工艺小车、垂直地面链、板式输送机和机动辊床滑撬输送线等。
蒙皮件主要采用机械或电热张拉机张拉、单面点焊机焊接工艺。
其中顶盖蒙皮还有采用大型龙门式自动多点焊机的。
车身骨架合装均采用柔性合装专机装配。
个别厂家将顶盖蒙皮及左/右侧围蒙皮的开机剪切下料机组与张拉点焊机组紧凑布置在一起,以求降低大型蒙皮件的运输距离和难度。
3.3涂装工艺
均采用三涂层工艺。
前处理一种是采用整体喷浸结合的生产方式,蒙皮后的车身通过程控输送机进行工序输送。
一种是采用骨架构件前处理工艺,骨架总成不再进行前处理。
国内仅有沈飞日野和厦门金旅两家采用了整车前处理电泳工艺,其他所有国内厂家均考虑到生产成本问题而没有采用。
喷漆及烘干少数厂家采用转运车和滑撬输送系统相结合的生产方式,多数厂家采用转运车和垂直地面链的生产方式。
至今为止,没有一家国内厂家采用水性漆中涂和面漆工艺的。
3.4总装工艺
从装配方式上,分为A:
合装工艺,车身和底盘分别进入总装车间,在总装车间合装;B:
非合装工艺,车身底盘在焊装车间完成连接,经涂装后整车进入总装车间;C:
车身由涂装车间运入,在总装车间完成前桥、后桥、动力总成等总成下装工作。
此种装配方式一般用于承载式车身的结构形式。
从运输方式上,主要分为工艺轨道小车式、单边板式带式、人工推送式。
从玻璃安装、涂胶工艺方法上,主要分为工作台式、固定升降台式、移动式升降台和手工涂胶式。
4工厂总图、物流方案
4.1厂址条件分析
作为单班年产8000辆客车的生产基地,几乎无法组织生产,厂房布置、道路网形成及物流运输组织将十分困难,因此需要大量的规划与设计;市政七通一平,工业园区规划与环评等问题需要尽快落实;
4.2规划理念及布置原则
4.2.1总平面布置的原则
以生产物流为龙头,力争使供应物流、生产物流、销售物流合理,且使人流物流分开;结合市政规划要求,使厂区功能分区明确合理;注意节约用地;满足各项规范的要求;注意风向朝向的影响;注重工厂的绿化及美化。
4.2.2规划理念
整体布局体现物流第一的理念,四大工艺首尾相接并尽量布置在1个厂区内;总平面布置结合实际满足各方面要求且经济、合理、实用,总平规划方案尽量考虑的细致、周到、全面、可行。
物流、人流分开各行其门,不迂回交叉,型材、外协件、成品车各行其道。
4.3总平面布置、竖向布置原则
4.3.1总平面布置
略
4.3.5总图主要数据
表4-1总图主要数据表(方案1)
序
号
项目
单位
数据
备注
一期
二期
合计
1
建设占地面积
hm2
39.600
39.600
2
建设使用面积
hm2
32.5000
32.5000
3
建构筑物占地面积
m2
85000
85000
4
堆场面积
m2
76000
76000
5
建筑密度
%
49.00
6
道路面积
m2
56000
56000
其中试车跑道13288平米
7
总建筑面积
168000
168000
8
容积率
0.516
9
绿化面积
m2
58000
58000
10
绿地率
%
18.00
11
办公及生活设施用地面积
m2
1500
1500
含在建设使用面积内
12
办公生活用地占总面积比率
%
0.46
0.46
13
围墙长度
m
2600
2600
注:
其余方案总图主要数据仅供参考。
5工厂制造技术方案
5.1准备车间
5.1.1车间任务
承担轻型及中、大型客车车身冲压件的钢板、卷料的存放,钢板的剪切、下料、冲压成型、折弯成型,钣金成形及车架厚杂件成形等。
卷料的开卷校平剪切。
车身骨架的型材存放、型材下料、弯管成形、摇臂钻钻孔。
毛坯、冲压件及模具的存放等任务。
本车间属于批量生产性质。
5.1.2设计原则
7m以下轻客的冲压线全部搬迁利用原有冲压线。
根据车间生产特点采用轮番方式组织生产。
原材料运入采用汽车。
卷料下料采用开卷纵横剪切机组(客车顶盖及左右侧围板)。
钢板下料采用剪板机,钢板材料利用率按70%计。
型材下料采用卧式半自动带锯机,型材弯管件采用液压弯管机成型,摇臂钻钻孔。
型材材料利用率按90%计。
车架厚板冲压杂件采用四柱万能液压机(Y32-500)成形。
小型冲压件采用开式可倾压力机(1000kN以下)。
薄板折弯件采用液压板料压力机(W67Y-100/3200)成形。
车间内部运输采用电动平板车和吊钩桥式起重机。
车间工艺布置充分考虑工艺流程合理性。
尽量做到工艺流程短捷顺畅。
冲压后的废料装入废料箱后,采用叉车运输到全厂废料地集中处理。
中客及大客冲压件的模具全部采用简易钢模。
主要工艺说明:
前围上蒙皮工艺过程:
钢板采用剪板机剪片料→液压机压型→修边钻孔→零件存放→焊接车间。
5.2焊装车间
5.2.1车间任务
车间任务:
承担轻型及中、大型客车车身的焊装、调整、修磨等任务(生产线考虑13.7m客车的通过性);构件前处理工段设置在焊装车间。
生产性质:
本车间为批量生产性质。
产品特点:
7m以下客车车身全部由薄板冲压件焊装而成;7~9m客车车身为骨架蒙皮结构,其中骨架由薄板、中厚板焊接而成;12m及以上客车车身为骨架蒙皮结构,其骨架由型材(矩形管)焊接而成。
5.2.2工艺方案
5.2.2.1焊装工段
根据生产纲领和车身结构特点,焊装车间设置4条客车车身焊装线,其中7m以下客车焊装线1条、7~9m客车焊装线2条、12m以上客车焊装线1条。
所有客车车身采用脱壳式生产,客车底盘不通过焊装车间。
对于7~9m客车及12m以上客车,采用客车六面体合装设备将六大片骨架合装成车身骨架。
侧中蒙皮及顶蒙皮采用机械张拉机;蒙皮焊接采用单面点焊机焊接。
车身骨架焊接采用弧焊或点焊工艺,采用合理的焊接顺序和焊接参数,尽可能减小骨架焊接变形。
车身焊装线采用轨道小车人工推送;分总成骨架等大中总成上线采用天车吊运,其余中小总成件上线采用人工搬运;车身总成下线通过工艺小车推送到涂装车间;厂房内其他大工件的传送采用天车配合简易吊具吊运,小件、冲压件、蒙皮等装在轮式工位器具或专用小车内用叉车或人工送到各工位。
对于7m以下客车,设置车身主焊线(含车门装配及打磨调整)、地板总成焊装线、左右侧围总成焊装线、前/后围总成焊装线等主要生产线。
焊接工艺以点焊为主。
采用电动葫芦输送工件。
车身总成及分总成采用检具、样架和量具进行检测,确保车身总成质量。
由于焊装车间生产过程产生大量焊接烟尘,通过加强焊装车间厂房的全室通风换气,改善车间作业环境。
5.2.2.2前处理工段
前处理工段的生产性质为间歇式生产。
所有客车的骨架构件均通过分类组挂通过每一个前处理工序。
工艺采用间歇式方式,通过程控行车进行工序间输送。
采用低温磷化工艺,前处理槽全部为敞开式结构。
烘干室采用热风循环的烘干方式,设置电动对开门,间歇式操作。
5.3涂装车间
5.3.1车间任务
涂装车间主要承担客车车身的涂装任务,主要包括车身焊接总成的漆前预清理;车身焊接总成的涂密封胶、喷涂车底防震隔热胶及发泡、喷涂底漆、中涂、面漆和彩漆等工作。
涂装车间的生性质为间歇式生产。
5.3.2设计原则
对于7m以下的轻客,因其品质要求较高,专门配备一台脱脂一体室和一台喷淋一体室进行前处理后,再进入到9m以下车型的涂装线。
中型及大型客车产品仅进行骨架构件前处理,不再进行车身整体前处理。
涂装车间采用抽屉式布置方式,结合车型的长短进行喷漆室及烘干室的设计:
7m以下轻客及7~9m中客设置一条涂装线;9m以上大客设置一条调涂装线;考虑到长13.7m客车的生产需要,为其单独配置1台喷漆室及1台烘干室专门通过此车型。
车身采用三涂层涂装工艺,即工件涂底漆、中涂、面漆。
采用改性丙烯酸烘烤漆涂装工艺,其涂层的耐腐蚀性、装饰性达到国际先进水平。
车身总成在涂装车间进行手工预清理、打磨、刮腻子,喷胶及发泡、喷涂底漆、中涂、面漆、彩漆。
涂装车间工序间运输采用转运车、工艺车与垂直地面链相结合的运输方式。
喷漆室、烘干室内采用垂直地面链输送。
其他工位采用人工退送。
涂装与焊装、总装车间的运输采用转运车与工艺车相结合的运输方式。
喷漆室采用上送风、下排风的水旋式喷漆室,送风为经过初、中过滤的空调风,含漆渣废水经漆泥处理装置处理后排至厂区污水处理站处理后排放。
烘干室采用热风循环的烘干室,设置电动对开门,间歇式操作。
烘干热源采用天燃气,油漆烘干室配置直接燃烧废气处理装置,余热回用。
采用工位设置的调漆系统。
喷漆室、调漆间设置CO2自动消防系统,集中控制。
对于易产生噪音的各种涂装设备,采取防噪音措施。
空调装置设置在空调平台上。
设备排风装置(风机)设置在独立的排风平台上,并设置隔音室,车间内噪音控制在85dB以下。
为保证产品涂装质量,车间内设有检查工位、返修工位。
5.4总装车间
5.4.1车间任务
本车间承担7m-13.7m客车内饰材料下料、分总成分装和客车装配、检测及调整返修等工作,同时承担部分底盘装配工作。
5.4.2设计原则
所有产品均采用车身与底盘合装的装配工艺。
为适应7m以下轻客、7~9m中巴及9~12m大客不同长度的车身,提高装配线生产效率,便于物流管理,总装车间设置3条客车装配线,均采用单边板式带输送形式。
其中大客装配线通过调整车位间距,可以实现超长度客车的装配生产。
设置1条底盘装配线,完成三段式底盘装配。
另设置一条三类底盘改制线,以满足客户的个性化需求。
新增1条整车检测线,设置在检测返修间内。
6采用的主要环保、节能措施
6.1主要环保措施
准备车间的压力机和剪板机在设备安装时加弹簧-黏滞阻尼隔震器减震。
焊装车间和总装车间的焊接烟尘,采用单机除尘器与全室换气相结合的方式治理。
焊装车间的弧焊工作量很大,全部采用烟尘发生量较小的半自动CO2弧焊机,从根源上减少焊接烟尘的产生。
涂装车间产生的脱脂、磷化、打磨废水排放至污水处理站进行处理、喷漆废水经过漆泥处理装置处理后排放至污水处理站进行处理。
喷漆产生的喷漆废气通过水旋式喷漆室处理后,通过一定高度烟囱集中排放到大气中。
烘干废气通过直燃装置进行净化处理后排放到厂房外。
总装车间在装配线整车下线处、测速试验台、整车返修区汽车冷启动及加速时会有大量尾气排出。
治理措施是:
在装配线整车下线处设1套尾气随行排放装置,在返修区增设轴流风机排风装置,将汽车尾气排出厂房。
在测速试验台处,设计1套排烟系统,将尾气排出厂房外。
空压机设置在独立的空压机站房,做隔声处理,空压机机体密闭隔声,空压机吸气管上自带空气消声过滤器,做独立基础减震降噪。
水泵加减震垫,采用软连接等进行防噪。
车间产生的金属废料全部由废品收购公司回收利用;废磷化渣、废漆渣及污水处理产生的污泥送环保部门指定的有资质的危险废物处理单位处理(厂内设置危险固体废物仓库和垃圾场);工业垃圾全部送城市指定垃圾场。
是否采用中水回用技术,请贵公司确定。
6.2主要节能措施
准备车间蒙皮件采用卷料,提高材料利用率。
焊装车间点焊机及空压站所需冷却水循环使用。
烘干室采用废气燃烧后的余热回收利用技术来预热烘干废气。
设计所采用的各类设备均为高效节能型设备,如节电电机以及节能型灯具等,并且设备负荷率为85%以上,提高能源利用率。
热工设备选用节能型,设备除带有温度、压力控制系统外,还带有节能型保温材料,使设备表面的温度不超过50℃。
是否采用中水回用技术,请贵公司确定。
是否采用雨水回收再利用技术,请贵公司确定。
生产厂房采用屋面采光带、办公楼采用大开间布局,以提高自然光的利用效率。
采用低损耗节能的户内成套变电所,干式变压器,靠近负荷中心布置。
变电所低压侧并联电容器进行无功动态补偿,使10kV侧功率因数补偿到0.90以上。
采用高光效长寿命节能光源和开启式节能灯具。
走廊采用节能灯,声、光控制。
电能计量作到三级计量,利于企业考核,节约能源。
管道热膨胀尽量利用自然补偿,长直线管段采用方形补偿器补偿。
热水管道采用岩棉制品保温,镀锌铁皮保护层。
直埋不保温管道采用环氧煤沥青特加强防腐
为了节约用水,采用节能型陶瓷芯龙头、冲便器安装延时自闭阀。
给水系统采用优质管材、管件(包括管接头、弯头、三通和四通)及附件(包括法兰、阀门和水龙头),防止跑、冒、滴、漏,减少输送过程的水资源损耗。
7存在的主要问题和建议
首先进入厂区路面无法通过大型车辆和设备,四大车间及其配套设施将会被分割的非常零碎,严重影响产品性能;