化工原理课程设计苯甲苯精馏塔设计.docx
《化工原理课程设计苯甲苯精馏塔设计.docx》由会员分享,可在线阅读,更多相关《化工原理课程设计苯甲苯精馏塔设计.docx(28页珍藏版)》请在冰豆网上搜索。
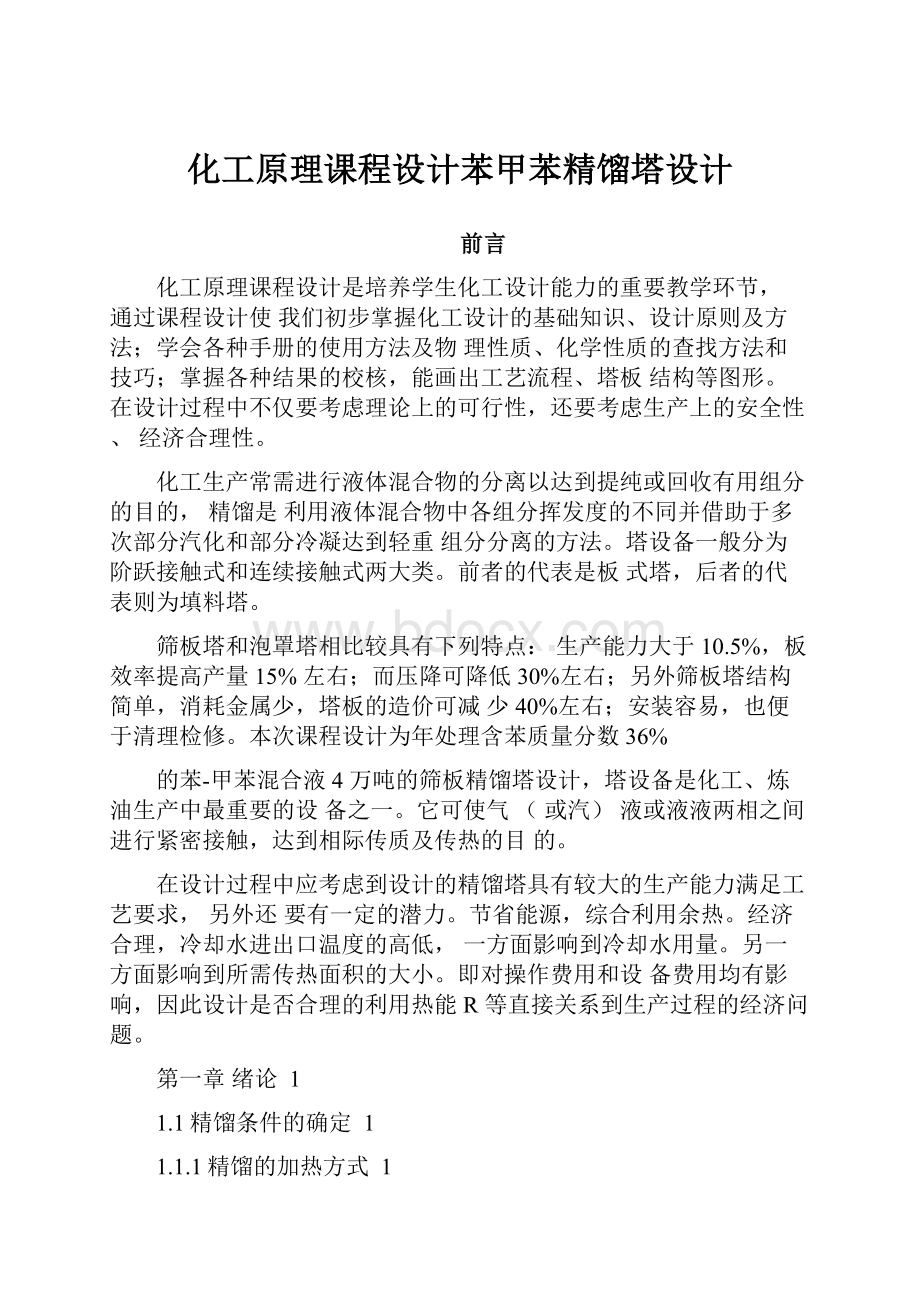
化工原理课程设计苯甲苯精馏塔设计
前言
化工原理课程设计是培养学生化工设计能力的重要教学环节,通过课程设计使我们初步掌握化工设计的基础知识、设计原则及方法;学会各种手册的使用方法及物理性质、化学性质的查找方法和技巧;掌握各种结果的校核,能画出工艺流程、塔板结构等图形。
在设计过程中不仅要考虑理论上的可行性,还要考虑生产上的安全性、经济合理性。
化工生产常需进行液体混合物的分离以达到提纯或回收有用组分的目的,精馏是利用液体混合物中各组分挥发度的不同并借助于多次部分汽化和部分冷凝达到轻重组分分离的方法。
塔设备一般分为阶跃接触式和连续接触式两大类。
前者的代表是板式塔,后者的代表则为填料塔。
筛板塔和泡罩塔相比较具有下列特点:
生产能力大于10.5%,板效率提高产量15%左右;而压降可降低30%左右;另外筛板塔结构简单,消耗金属少,塔板的造价可减少40%左右;安装容易,也便于清理检修。
本次课程设计为年处理含苯质量分数36%
的苯-甲苯混合液4万吨的筛板精馏塔设计,塔设备是化工、炼油生产中最重要的设备之一。
它可使气(或汽)液或液液两相之间进行紧密接触,达到相际传质及传热的目的。
在设计过程中应考虑到设计的精馏塔具有较大的生产能力满足工艺要求,另外还要有一定的潜力。
节省能源,综合利用余热。
经济合理,冷却水进出口温度的高低,一方面影响到冷却水用量。
另一方面影响到所需传热面积的大小。
即对操作费用和设备费用均有影响,因此设计是否合理的利用热能R等直接关系到生产过程的经济问题。
第一章绪论1
1.1精馏条件的确定1
1.1.1精馏的加热方式1
1.1.2精馏的进料状态1
1.1.3精馏的操作压力1
1.2确定设计方案1
1.2.1工艺和操作的要求2
1.2.2满足经济上的要求2
1.2.3保证安全生产2
第二章设计计算2
2.1设计方案的确定2
2.2精馏塔的物料衡算2
2.2.1原料液进料量、塔顶、塔底摩尔分率2
2.2.2原料液及塔顶、塔底产品的平均摩尔质量3
2.2.3物料衡算3
2.3塔板计算3
2.3.1理论板数NT的求取3
2.3.2全塔效率的计算4
2.3.3求实际板数4
2.3.4有效塔高的计算4
2.4精馏塔的工艺条件及有关物性数据的计算.4
2.4.1操作压力的计算4
2.4.2操作温度的计算5
2.4.3平均摩尔质量的计算5
2.4.4平均密度的计算6
2.4.5液体平均表面张力的计算7
2.4.6液体平均黏度的计算8
2.4.7气液负荷计算8
2.5塔径的计算8
2.6塔板主要工艺尺寸的计算9
2.6.1溢流装置计算9
2.6.2塔板布置11
2.7筛板的流体力学验算塔板压降.12
2.7.1精馏段筛板的流体力学验算塔板压降12
2.7.2提馏段筛板的流体力学验算塔板压降13
2.8塔板负荷性能图14
2.81精馏段塔板负荷性能图14
2.82提馏段塔板负荷性能图15
第三章设计结果一览表错误!
未定义书签
第四章板式塔结构17
4.1塔顶空间18
4.2塔底空间18
4.3人孔18
4.4塔高18
第五章致谢19
第一章绪论
1.1精馏条件的确定
本精馏方案适用于工业生产中苯-甲苯溶液二元物系中进行苯的提纯。
精馏塔苯塔的产品要求纯度很高,而且要求塔顶、塔底产品同时合格,普通的精馏温度控制远远达不到这个要求。
故在实际生产过程控制中只有采用灵敏板控制才能达到要求。
故苯塔采用温差控制。
1.1.1精馏的加热方式
蒸馏釜的加热方式通常采用间接蒸汽加热,设置再沸器。
有时也可采用直接蒸汽加热。
然而,直接蒸汽加热,由于蒸汽的不断通入,对塔底溶液起了稀释作用,在塔底易挥发物损失量相同的情况下,塔底残液中易挥发组分的浓度应较低,因而塔板数稍有增加。
采用直接蒸汽加热时,加热蒸汽的压力要高于釜中的压力,以便克服蒸汽喷出小孔的阻力及釜中液柱静压力。
1.1.2精馏的进料状态
进料状态直接影响到进料线(q线)、操作线和平衡关系的相对位置,对整个塔的热量衡算也有很大的影响。
和泡点进料相比:
若采用冷进料,在分离要求一定的条件下所需理论板数少,不需预热器,但塔釜热负荷(一般需采用直接蒸汽加热)从总热量看基本平衡,但进料温度波动较大,操作不易控制;若采用露点进料,则在分离要求一定的条件下,所需理论板数多,进料前预热器负荷大,能耗大,同时精馏段与提馏段上升蒸汽量变化较大,操作不易控制,受外界条件影响大。
泡点进料介于二者之间,最大的优点在于受外界干扰小,塔内精馏段、提馏段上升蒸汽量变化较小,便于设计、制造和操作控制。
故此设计采用泡点进料。
1.1.3精馏的操作压力
精馏操作在常压下进行,因为苯沸点低,适合于在常压下操作而不需要进行减压操作或加压操作。
同时苯物系在高温下不易发生分解、聚合等变质反应且为液体(不是混合气体)。
所以,不必要用加压或减压精馏。
另一方面,加压或减压精馏能量消耗大,在常压下能操作的物系一般不用加压或减压精馏。
1.2确定设计方案
确定设计方案总的原则是在可能的条件下,尽量采用科学技术上的最新成就,使生产达到技术上最先进、经济上最合理的要求,符合优质、高产、安全、低消耗的原则。
为此,必须具体考虑如下几点:
1.2.1工艺和操作的要求
所设计出来的流程和设备,首先必须保证产品达到任务规定的要求,而且质量要稳定,这就要求各流体流量和压头稳定,入塔料液的温度和状态稳定,从而需要采取相应的措施。
其次所定的设计方案需要有一定的操作弹性,各处流量应能在一定范围内进行调节,必要时传热量也可进行调整。
因此,在必要的位置上要装置调节阀门,在管路中安装备用支线。
计算传热面积和选取操作指标时,也应考虑到生产上的可能波动。
再其次,要考虑必需装置的仪表(如温度计、压强计,流量计等)及其装置的位置,以便能通过这些仪表来观测生产过程是否正常,从而帮助找出不正常的原因,以便采取相应措施。
1.2.2满足经济上的要求
要节省热能和电能的消耗,减少设备及基建费用。
如前所述在蒸馏过程中如能适当地利用塔顶、塔底的废热,就能节约很多生蒸汽和冷却水,也能减少电能消耗。
又如冷却水出口温度的高低,一方面影响到冷却水用量,另方面也影响到所需传热面积的大小,即对操作费和设备费都有影响。
同样,回流比的大小对操作费和设备费也有很大影响。
1.2.3保证安全生产
例如苯属有毒物料,不能让其蒸汽弥漫车间。
又如,塔是指定在常压下操作的,塔内压力过大或塔骤冷而产生真空,都会使塔受到破坏,因而需要安全装置。
以上三项原则在生产中都是同样重要的。
但在化工原理课程设计中,对第一个原则应作较多的考虑,对第二个原则只作定性的考虑,而对第三个原则只要求作一般的考虑。
第二章设计计算
2.1设计方案的确定
本设计采用连续精馏流程,饱和液体进料。
塔顶上升蒸汽采用全凝器冷凝,冷凝液在泡点下一部分回流至塔内,其余部分经产品冷却器冷却后送至储罐。
该物系属于易分离物系,最小回流比比较小,故操作回流比取最小回流比的2倍。
塔釜采用饱和蒸汽间接加热,塔底产品冷却后送至储罐。
2.2精馏塔的物料衡算
2.2.1原料液进料量、塔顶、塔底摩尔分率
生产能力)进料量:
F=85000t/年
苯的摩尔质量MA=78.11Kg/mol
2.2.3物料衡算
原料处理量
850000002
F1.37102kmol/h
85.96127200
总物料衡算苯物料衡算联立解得:
F=D+W=137kmol/h
0.44F0.983D0.024W
D=59.43Kmol/h
W=77.57Kmol/h
2.3塔板计算
2.3.1理论板数NT的求取
(1)相对挥发度的求取
查温度-组成图得td=80℃tw=92.6℃(由表2)当取td=80℃时
当取td=92.6℃时
PA146.004kp,PB58.94kp
(2)最小回流比的求取
由于是饱和液体进料,有q=1,q线为一垂直线,故xPxF0.44,根据相平衡方
程有
最小回流比为
对于平衡曲线不正常情况下,取回流比R=(1.1-2)Rmin
R=1.5Rmin=2.16
(3)精馏塔的气、液相负荷
(4)操作线方程
精馏段操作线方程提馏段操作线方程
(5)逐板法求理论板数计算过程如下
相平衡方程
2.5x
11.5x
变形得:
2.51.5y
精馏段操作线方程
提馏段操作线方程
用精馏段操作线和相平衡方程进行逐板计算:
故精馏段理论板数n=7
用提馏段操作线和相平衡方程继续逐板计算:
故提馏段理论板数n=8(不包括再沸器)
2.3.2全塔效率的计算
由td=80℃tw=92.6℃
计算出tm=93.5℃根据表6分别查得苯、甲苯在平均温度下的粘度
内差法计算出A0.271mPaS,B0.278mPaS平均粘度由公式,得
根据奥康奈尔(O`connell)公式计算全塔效率ET
2.3.3求实际板数
精馏段实际板层数
提馏段实际板层数
全塔共有塔板28块,进料板在第14块板。
2.3.4有效塔高的计算
精馏段有效塔高
提馏段有效塔高
在精馏段和提馏段各设人孔一个,高度为600mm,
故有效塔高Z4.85.60.6211.6m
2.4精馏塔的工艺条件及有关物性数据的计算
2.4.1操作压力的计算
塔顶操作压力P=101.3kPa
每层塔板压降△P=0.7kPa
进料板压力PF=101.3+0.7×13=110.4kPa
塔底操作压力Pw=101.3+0.71×5=111.8kPa
精馏段平均压力Pm1=(101.3+110.4)/2=105.85kPa
提馏段平均压力Pm2=(110.4+111.8)/2=111.1kPa
2.4.2操作温度的计算
塔顶温度tD80℃
进料板温度tF92.6℃
塔底温度tW107℃
精馏段平均温度tm1=(80+92.6)/2=86.3℃
提馏段平均温度tm2=(92.6+107)/2=99.8℃
2.4.3平均摩尔质量的计算
塔顶平均摩尔质量计算
由由XDy10.983带入相平衡方程,得x1=0.959
进料板平均摩尔质量计算
由上面理论板的算法,得yF=0.654,xF=0.43
塔底平均摩尔质量计算
由xW=0.01,由相平衡方程,得yW=0.026
Ml,W0.0178.11(10.01)92.1391.99(kg/kmol)
精馏段平均摩尔质量
提馏段平均摩尔质量
2.4.4平均密度的计算
①气相平均密度计算
由理想气体状态方程计算,精馏段的平均气相密度即
RTM
VmPMVM8.31405.8865.3802.6763.152.86(kg/m)
提馏段的平均气相密度
②液相平均密度计算
液相平均密度依下式计算,
aAaB
LmLALB
由tD=80℃,查手册得
A815kg/m3
B810kg/m3
塔顶液相的质量分率
求得
0.98
得L,D
814.9kg/m3
由tf=92.06℃,
查共线图得
A800.9kg/m3
3
B797.63kg/m3
求得A
10.39
L,Fm800.09
m
塔顶液相的质量分率
0.4378.110.39
0.4378.1110.4392.13
0.61得L,Fm800kg/m3
797.63L,Fm
c.塔底液相平均密度的计算
由tw=107℃,
3
A783.96kg/m3
B783.3kg/m3
塔顶液相的质量分率
0.0178.11
0.0178.1110.0192.13
0.085
10.08510.085得
L,W783.96783.3
3
L,Wm730kg/m3
精馏段液相平均密度为
Lm
814.9800
2
3
807.45kg/m3
提馏段液相平均密度为
2.4.5液体平均表面张力的计算
由公式:
n
LmxLL
L1
a.塔顶液相平均表面张力的计算
由tD=80℃,查手册A21.27(mN/m)
b.进料板液相平均表面张力的计算
由tF=92.06℃,查共线图得
A19.75(mN/m)B20.42(mN/m)
c.塔底液相平均表面张力的计算
由tw=107℃,查共线图得
A18.02(mN/m)B18.87(mN/m)
21.69(mN/m)
精馏段液相平均表面张力为
21.2820.13
Lm
20.21(mN/m)
提馏段液相平均表面张力为
2.4.6液体平均黏度的计算
由公式:
Lmxii及查手册得
塔顶液相平均黏度的计算
由tD=80℃,查共线图得
a.进料板液相平均黏度的计算由tF=92.06℃,查共线图得
b.塔底液相平均黏度的计算由tw=107℃,查共线图得
精馏段液相平均黏度为
提馏段液相平均黏度为
2.4.7气液负荷计算
精馏段:
提馏段:
2.5塔径的计算
塔板间距HT的选定很重要,它与塔高、塔径、物系性质、分离效率、塔的操作弹性,以及塔的安装、检修等都有关。
可参照下表所示经验关系选取。
表2.1板间距与塔径关系
塔径DT,m
0.3~0.5
0.5~0.8
0.8~1.6
1.6~2.4
2.4~4.0
板间距HT,mm
200~300
250~350
300~450
350~600
400~600
对精馏段:
初选板间距HT0.40m,取板上液层高度hL0.06m,
HThL0.400.060.34m;
查史密斯关联图得C20=0.070;依式
校正物系表面张力为
可取安全系数为0.7,则(安全系数0.6—0.8),
按标准塔径圆整为1.6m,则空塔气速0.73m/s。
对提馏段:
初选板间距HT0.40m,取板上液层高度hL0.06m,
故HLhT0.034m;
查史密斯关联图得C20=0.065;依式
校正物系表面张力为19.58mN/m时
可取安全系数为0.7,则(安全系数0.6—0.8),故
按标准,塔径圆整为2.0m,则空塔气速0.46m/s。
将精馏段和提溜段相比较可以知道二者的塔径不一致,根据塔径的选择规定,对于相差不大的二塔径取二者中较大的,因此在设计塔的时候塔径取2m。
2.6塔板主要工艺尺寸的计算
2.6.1溢流装置计算
精馏段
因塔径D=2m,可选用单溢流弓形降液管,采用平行受液盘。
对精馏段各项计算如下:
a)溢流堰长lw:
单溢流区lw=(0.6~0.8)D,取堰长为lw=0.60D=0.60×2.0=1.2m
b)出口堰高hw:
查液流收缩系数计算图可以
图2.1液流收缩系数计算图
查得E=1.04,则
故hwhLhOW0.060.0140.046m
c)降液管的宽度Wd与降液管的面积Af:
由lw/D0.06查弓形降液管的宽度与面积图
图2.2弓形降液管的宽度与面积
Wd/D
0.124,
Af/AT0.056
Wd0.124D0.1241.20.198m,
利用
3600AfH
Lh
T计算液体在降液管中停留时间以检验降液管面积,
即
3600AfHTLh
12.56S(大于5s,符合要求)
d)降液管底隙高度h0:
取液体通过降液管底隙的流速uo0.08m/s(0.07---0.25m/s)依式
满足条件,故降液管底隙高度设计合理
e)受液盘采用平行形受液盘,不设进堰口,深度为60mm
提馏段
因塔径D=2m,可选用单溢流弓形降液管,采用平行受液盘。
对精馏段各项计
算如下:
a)溢流堰长lw:
单溢流区lW=(0.6~0.8)D,取堰长lw为0.60D=0.60×2.0=1.2mb)出口堰高hW:
hWhLhOW
查液流收缩系数计算图可以得到液流收缩系数E查得E=1.04,则
故hwhLhOW0.060.0140.046m
c)降液管的宽度Wd与降液管的面积Af:
由
lw/D0.60查弓形降液管的宽度与面积图可得
Wd0.124D0.1241.20.198m,
利用3600AfHT计算液体在降液管中停留时间以检验降液管面积,
d)降液管底隙高度h0:
取液体通过降液管底隙的流速00.01m/s(0.07---0.25m/s)满足条件,故降液管底隙高度设计合理
e)受液盘
采用平行形受液盘,不设进堰口,深度为60mm
2.6.2塔板布置
a)塔板的分块
因D≥1200mm,故塔板采用分块式。
塔极分为4块。
对精馏段:
取边缘区宽度
由于小塔边缘区宽度取30—50mm所以这里取Wc0.04m安定区宽度
由于D=1.2m<1.5m故
b)开孔区面积
计算开孔区面积
D2D
RWc0.040.96mxWdWs10.1980.070.73m
2c2,2ds
筛孔数n与开孔率:
本例所处理是物系无腐蚀性,可选用3mm碳钢板,取筛板直径d05mm,筛孔
按正三角形排列取孔中心距t为t4520mm
则每层板上的开孔面积A0为
气体通过筛孔的气速为:
2.7筛板的流体力学验算塔板压降
2.7.1精馏段筛板的流体力学验算塔板压降
(1)干板阻力hg计算。
干板阻力由下式计算:
由d053
1.67,查筛板塔汽液负荷因子曲线图
图2.3
得C00.84
故hc1V
u0
2
1
2.8610.35
0.027m液柱
c2gL
C0
29.81
807.450.84
(2)气体通过液层的阻力
hl计算。
气体通过液层的阻力hL由下式计算,即
查充气系数关联图得0.62。
故h1hL0.580.060.0372m液柱。
(3)液体表面张力的阻力计算。
液体表面张力所产生的阻力h由下式计算,即:
气体通过每层塔板的液柱高度hp按下式计算:
气体通过每层塔板的压降为:
(2)液面落差对于筛板塔,液面落差很小,且本设计的塔径和液流量均不大,故可忽略液面落差的影响。
(3)溢流液泛为防止塔内发生液泛,降液管内液层高Hd应服从下式所表示的关系,即:
塔板不设进口堰则
苯—甲苯物系属一般物系,取0.5,则:
所以设计中不会发生液泛现象
(4)雾沫夹带雾沫夹带按下式计算:
故液沫夹带量v在允许的范围内。
(5)漏液对筛板塔,漏液点气速可由以下公式计算:
稳定系数为
故在本设计中无明显漏液。
2.7.2提馏段筛板的流体力学验算塔板压降
(1)干板阻力计算。
干板阻力由下式计算:
由d0531.67,查筛板塔汽液负荷因子曲线图得
(2)气体通过液层的阻力计算。
查充气系数关联图得0.68。
故h1hL0.680.060.04m液柱。
(3)液体表面张力的阻力h计算。
液体表面张力所产生的阻力h由下式计算,即:
气体通过每层塔板的液柱高度hp按下式计算:
hphchlh0.0310.040.01040.072m液柱气体通过每层塔板的压降为:
(2)液面落差对于筛板塔,液面落差很小,且本设计的塔径和液流量均不大,故可忽略液面落差的影响。
(3)溢流液泛为防止塔内发生液泛,降液管内液层高应服从下式所表示的关系,即:
塔板不设进口堰则
苯—甲苯物系属一般物系,取0.5,则:
所以设计中不会发生液泛现象
(4)雾沫夹带雾沫夹带按下式计算:
故液沫夹带量v在允许的范围内。
(5)漏液对筛板塔,漏液点气速可由以下公式计算:
稳定系数为故在本设计中无明显漏液。
2.8塔板负荷性能图
2.81精馏段塔板负荷性能图
(1)
漏液线
得:
整理得:
在操作范围内,任取几个Ls值,依上式计算出VS值,计算结果列于下表
表2.2漏液线计算结果
Ls/(m3/s)
0.003
0.004
0.005
0.006
0.01
Vs/(m3/s)
1.22
1.24
1.254
1.27
1.32
由上表数据即可作出漏液线1
(2)雾沫夹带线
以v0.1kg液/kg气为限,求VsLs关系如下:
在操作范围内,任取几个Ls值,依上式计算出VS值,计算结果列于下表
表2.3雾沫夹带线计算结果
Ls/(m3/s)
0.003
0.004
0.005
0.006
0.01
Vs/(m3/s)
4.001
3.89
3.79
3.696
3.361
由上表数据即可作出液沫夹带线2
(3)液相负荷下限线
对于平直堰,取堰上液层高度how0.06m作为最小液体负荷标准
据此可作出与气体流量无关的垂直液相负荷下限线3
(4)液相负荷上限线
以0.4s作为液体在降液管中停留时间的下限
据此可作出与气体流量无关的垂直液相负荷上限线4。
(5)液泛线
由E=1.04,lw1.2.得:
已算出h2.03103m液柱,
HT0.4m,hW0.046m,0.5
代入整理得:
22/32Vs211.5880.3L2s/35950L2s
在操作范围内,任取几个Ls值,依上式计算出Vs值,计算结果列于表2.4
表2.4
Ls/(m3/s)
0.003
0.004
0.005
0.006
0.01
图2.4
精馏段
Vs/(m3/s)
9.74
9.46
9.13
8.81
7.18
负荷性
能图
2.82提馏段塔板负荷性能图
(1)
漏液线
整理得:
表2.5漏液线计算结果
Ls/(m3/s)
0.003
0.004
0.005
0.006
0.01
Vs/(m3/s)
0.92
0.92
0.93
0.94
0.80
由上表数据即可作出漏液线1
(