冲压课程设计.docx
《冲压课程设计.docx》由会员分享,可在线阅读,更多相关《冲压课程设计.docx(24页珍藏版)》请在冰豆网上搜索。
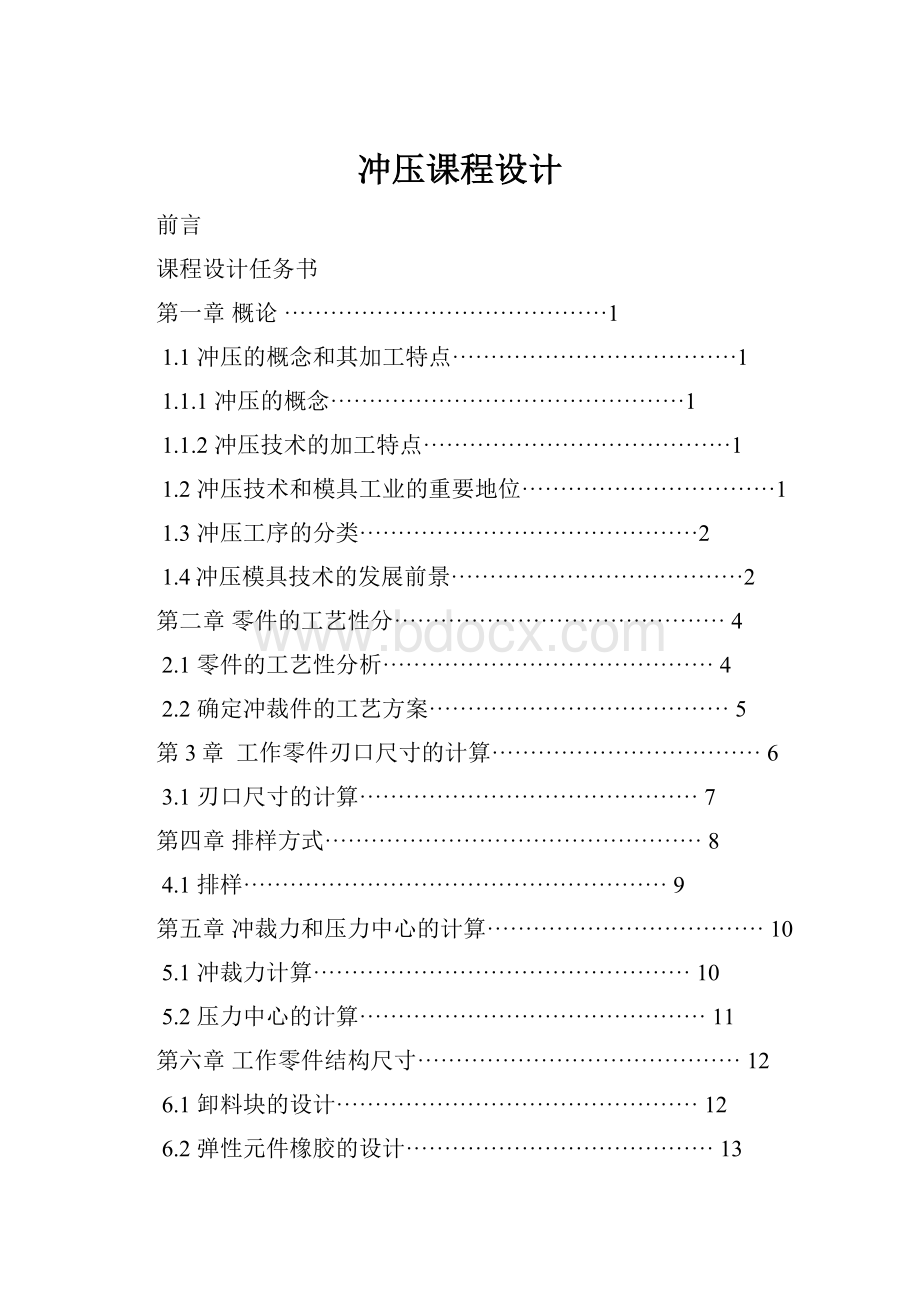
冲压课程设计
前言
课程设计任务书
第一章概论··········································1
1.1冲压的概念和其加工特点·····································1
1.1.1冲压的概念··············································1
1.1.2冲压技术的加工特点········································1
1.2冲压技术和模具工业的重要地位·································1
1.3冲压工序的分类············································2
1.4冲压模具技术的发展前景······································2
第二章零件的工艺性分···········································4
2.1零件的工艺性分析···········································4
2.2确定冲裁件的工艺方案·······································5
第3章工作零件刃口尺寸的计算···································6
3.1刃口尺寸的计算············································7
第四章排样方式·················································8
4.1排样·······················································9
第五章冲裁力和压力中心的计算····································10
5.1冲裁力计算·················································10
5.2压力中心的计算·············································11
第六章工作零件结构尺寸··········································12
6.1卸料块的设计···············································12
6.2弹性元件橡胶的设计········································13
6.3落料凹模板尺寸············································14
6.4凸凹模的设计··············································15
6.5冲孔凸模的设计············································16
第七章模架及其它零件的设计·····································17
7.1上下模座···················································17
7.2模柄·······················································18
第八章总结·····················································19
参考文献·························································21
前言
冲压是利用安装在冲压设备(主要是压力机)上的模具对材料施加压力,使其产生分离或塑性变形,从而获得所需零件(俗称冲压或冲压件)的一种压力加工方法。
冲压通常是在常温下对材料进行变形加工,且主要采用板料来加工成所需零件,所以也叫冷冲压或板料冲压。
冲压是材料压力加工或塑性加工的主要方法之一,隶属于材料成型工程。
冲压所使用的模具称为冲压模具,简称冲模。
冲模是将材料(金属或非金属)批量加工成所需冲件的专用工具。
冲模在冲压中至关重要,没有符合要求的冲模,批量冲压生产就难以进行;没有先进的冲模,先进的冲压工艺就无法实现。
冲压工艺与模具、冲压设备和冲压材料构成冲压加工的三要素,只有它们相互结合才能得出冲压件。
与机械加工及塑件加工的其它方法相比,冲压加工无论在技术方面还是经济方面都具有许多独特的优点。
主要表现如下。
(1)冲压加工的生产效率高,且操作方便,易于实现机械化和自动化。
(2)冲压时由于模具保证了冲压件的尺寸与形状精度,且一般不压件的表面质量,而模具的寿命一般较长,所以冲压的质量稳定,互换性好,具有“一模一样”的特征。
(3)冲压可加工出尺寸范围较大、形状较复杂的零件,如小到钟表的秒表,大到汽车纵梁、覆盖件等,加工冲压时材料的冷变形硬化效应,冲压的强度和刚度均较高。
(4)冲压一般没有切屑碎料生成,材料的消耗较少,且不需要其它加热设备,因为是一种省料,节能的加工方法,冲压件的成本较低。
由于冲压加工的零件种类繁多,各类零件的形状、尺寸和精度要求又各不相同,因而生产中采用的冲压工艺方法也是各种各样的。
概括起来,可分为分离工序和成形工序两大类:
分离工序是指将坯料沿一定的轮廓线分离而获得一定形状、尺寸和断面质量的冲压(俗称冲压件)的工序;成形工序是指使坯料在不破坏的条件下产生塑性变形而获得一定形状和尺寸的冲压件的工序。
上述两类工序,按基本变形方式不同又可分为冲裁、弯曲、拉伸和成形四种基本工序,每种基本工序还包括有多种单一工序。
在实际生产中,当冲压件的生产批量较大、尺寸较少而公差要求较小时,若用分散的单一工序来冲压是不经济甚至难于达到要求。
这时在工艺上多采用集中的方案,即把两种或两种以上的单一工序集中在一副模具内完成,称为组合的方法不同。
复合冲压—在压力机的一次工作行程中,在模具的同一个工位上同时完成两种或两种以上不同单一工序的一种组合方式。
级进冲压—在压力机上的一次工作行程中,按照一定的顺序在同一模具的不同工位上完成两种或两种以上不同单一工序的一种组合方式。
复合-级进—在一副冲模上包括复合和级进两种方式的组合工序。
冲模的结构类型也很多。
通常按工序性质可分为冲裁模、弯曲模、拉伸模和成形模等;按工序的组合方式可分为单工序模、复合模和级进模等。
但不论何种类型的冲模,都可看成是由上模和下模两部分组成,上模被固定在压力机工作台或垫板上,是冲模的固定部分。
工作时,坯料在下模面上通过定位零件定位,压力机滑块带动上模下压,在模具工作零件(即凸模、凹模)的作用下坯料便产生分离或塑性变形,从而获得所需形状与尺寸的冲件。
上模回升时,模具的卸料与出件装置将冲件或废料从凸、凹模上卸下或推、顶出来,以便进行下一次冲压循环。
此设计针对所给的零件进行了一套冷冲压模具的设计,其中设计内容为分析零件的冲裁工艺性(材料、工件结构形状、尺寸精度),拟定零件的冲压工艺方案及模具结构,排样,裁板,计算冲压工序压力,选用压力机及确定压力中心,计算凸凹模刃口尺寸,主要零部件设计和加工工艺编制,压力机的校核。
《冲压工艺及模具设计》课程设计任务书
设计题目:
“垫片”零件冲压工艺及模具设计
内容及任务:
一、设计的主要技术参数:
见产品图
二、设计任务:
完成该产品的冲压工艺方案、设计说明书、模具装配图及工作零件图。
三、设计工作量
1、制订冲压工艺方案
2、模具总装图1张,凸模及凹模零件图2张
3、设计说明书1份,20页左右
四、设计要求
1、图纸用CAD绘制并交纸质图及电子档
2、本任务书应与说明书、图纸一同装订成册,并加封面,装入资料袋中,否则不接收
3、设计必须认真仔细,允许讨论,但严禁抄袭、复制或复印。
名称:
垫片
批量:
大批量
材料:
10号钢
厚度:
0.5mm
第一章概论
1.1冲压的概念和其加工特点
1.1.1冲压的概念
冲压:
是利用安装在压力机上的冲模对材料施加压力,使其产生分离或塑性变形,从而获得所需零件的一种冲压加工方法。
1.1.2冲压技术的加工特点
冲压加工是一种先进的金属加工方法,与其他加工方法(切削)比较,它有以下特点:
1、采用冲压加工方法,在压床简单冲压下,可以得到壁薄、重量轻、刚性好、表面质量高、形状复杂、用其他加工方法难以加工的工件。
如汽车的前顶盖、车门等薄壳零件。
2、冲压件的尺寸精度是由模具保证的,制出的零件一般不进一步加工,可直接用来装配,而且有一定精度,具有互换性。
因此,冲压加工的尺寸稳定、互换性好。
3、在耗材不大的情况下,能得到强度高、足够刚性而重量轻、外表光滑美观的零件,因此,工件的成本较低。
4、冲压加工一般不需要加热毛坯,也不像切削加工那样,大量切削金属,所以它不但节能,而且节约金属。
操作简单,劳动强度低,材料利用率高(一般为70%~85%)。
5、生产率高,冲床冲一次一般可得一个零件,而冲床一分钟的行程少则多次,多则几百次。
同时,生产出的毛坯和零件形状规则,便于实现机械化和自动化。
最近几年发展起来的简易冲模、组合模具、锌基合金冲模等为单件大批量生产创造了条件,因此,产品造价成本低。
1.2冲压技术和模具工业的重要地位
冲压模具是大批生产同形产品的工具,是工业生产的主要工艺装备。
冲压模具工业是国民经济的基础工业。
冲压模具可保证冲压产品的尺寸精度,使产品质量稳定,而且在加工中不破坏产品表面。
用冲压模具生产零部件可以采用冶金厂大量生产的廉价的轧制钢板或钢带为坯料,且在生产中不需加热,具有生产效率高、质量好、重量。
轻、成本低且节约能源和原材料等一系列优点,是其他加工方法所不能比拟的。
使用模具已成为当代工业生产的重要手段和工艺发展方向。
现代制造工业的发展和技术水平的提高,很大程度上取决于模具工业的发展。
目前,工业生产中普遍采用模具成形工艺方法,以提高产品的生产率和质量。
1.3冲压工序的分类
1、根据工艺性质分:
分离工序、成形工序。
分离工序:
指坯料在模具刃口作用下,沿一定的轮廓线分离而获得冲件的加工方法。
成形工序:
指坯料在模具压力作用下,使坯料产生塑性变形,但不产生分离而获得具有一定形状和尺寸的冲件的加工方法。
2、根据工序组合程度分:
单工序、复合工序、连续工序。
1.4冲压模具技术的发展前景
现代模具工业有“不衰亡工业”之称。
世界模具市场总体上供不应求,市场需求量维持在600亿至650亿美元,同时,我国的模具产业也迎来了新一轮的发展机遇。
近几年,我国模具产业总产值保持13%的年增长率(据不完全统计,2004年国内模具进口总值达到600多亿,同时,有近200个亿的出口),到2005年模具产值预计为600亿元,模具及模具标准件出口将从现在的每年9000多万美元增长到2005年的2亿美元左右。
单就汽车产业而言,一个型号的汽车所需模具达几千副,价值上亿元,而当汽车更换车型时约有80%的模具需要更换。
2003年我国汽车产销量均突破400万辆,预计2004年产销量各突破500万辆,轿车产量将达到260万辆。
另外,电子和通讯产品对模具的需求也非常大,在发达国家往往占到模具市场总量的20%之多。
目前,中国17000多个模具生产厂点,从业人数约50多万。
1999年中国模具工业总产值已达245亿元人民币。
工业总产值中企业自产自用的约占三分之二,作为商品销售的约占三分之一。
在模具工业的总产值中,冲压模具约占50%,塑料模具约占33%,压铸模具约占6%,其它各类模具约占11%。
第二章零件的工艺性分析
2.1零件的工艺分析
零件图
名称:
垫片
批量:
大批量
材料:
10号钢
厚度:
0.5mm
该零件的外形规则结构对称,适用于普通冲压加工,材料为10号钢,厚度t=0.5mm,零件无特殊要要求,按IT=14级选取。
其公差查《互换性与测量技术基础》P18页得到如下图:
零件公差图
2.2、确定冲裁工艺方案
该工件包括落料冲孔两个基本工序,可有以下几种方案
方案一:
先落料后冲孔,采用单工序模生产。
方案二:
先冲孔后落料,采用级进模生产。
方案三:
冲孔落料同时进行,采用复合膜生产
各方案的特点比较如下:
方案一:
膜结构简单制造方便,但需要两道工序,两幅模具,成本相对较高,生产效率低,在第一道工序完成后进入第二道工序,必然会增加误差,使工件精度降低,达不到要求,故不选用。
方案二:
级进模能满足生产效率高的要求,但其难以保证内部的相对精度,故不选用。
方案三:
复合膜适用于生产效率高,精度高,结构形状简单的工件,其最窄的距离为4,而工件厚度为t=0.5mm,能满足a
1.5t的要求。
故选用此方案
第3章工作零件刃口尺寸的计算
3.1、刃口尺寸的计算
根据冲裁件结构的不同,刃口尺寸的计算方法如下:
落料如图a为工件图,图b为冲裁该工件所用落料凹模刃口的轮廓图,图中虚线表示凹模刃口磨损后尺寸的变化情况
冲裁件结构图
(a)(b)
落料时应以凹模为基准件来配作凸模。
从图b中可以看出,凹模磨损后刃口尺寸有变大、变小和不变三种情况:
1)凹模磨损后变大的尺寸(图中A
和A
),按一般落料凹模尺寸公式计算,系数x课本44页表3-5得0.5代入公式得:
2)凹模磨损后变小的尺寸(图中B
和B
),按一般冲孔凸模尺寸公式计算,因它在凹模上相当于冲孔凸模尺寸,系数x都为0.5,即:
3)凹模磨损后无变化的尺寸(图中C),即:
凹模刃口尺寸按凸模实际尺寸配置,保证双面间隙值为
第四章排样方式
4.1、排样
1可采用以下两种排样方式
1)少废料排样
2)无废料排样
由于该工件结构比较简单,无论采用一方案还是二方案都能满足要求。
相比而言少废料排样材料利用率低,但无废料排样会加快模具的磨损,使模具寿命减少,并直接影响工件的断面质量,所以采用少废排样即一方案。
查冲压模具与制造表搭边值如下:
根据制件的厚度和排样方法得到如下:
搭边值工件间
,沿边
排样方式结构图(横排)
排样方式结构图(纵排)
2条料宽度的确定
采用有侧压装置,条料宽度公差查下表:
条料宽度偏差
(单位mm)
条料宽度b
材料厚度t
~1
1~2
2~3
3~5
~50
50~100
100~150
150~220
220~300
-0.4
-0.5
-0.6
-0.7
-0.8
-0.5
-0.6
-0.7
-0.8
-0.9
-0.7
-0.8
-0.9
-1.0
-1.1
-0.9
-1.0
-1.1
-1.2
-1.3
条料宽度:
条料的步距:
一个步距内材料利用率
为:
第五章冲裁力和压力中心的计算
5.1、冲裁力的计算
通常说的冲裁力是指冲裁力的最大值,它是选用压力机和设计模具的重要依据之一。
平刃口冲裁模的冲裁力F一般按下式计算:
式中F——冲裁力(N)
L——冲裁周边长度(mm)
t——材料厚度(mm)
——材料抗剪强度(MPa)查表的
K——系数
系数K是考虑到实际生产中,模具间隙值的波动和不均匀、刃口的磨损、板料力学性能和厚度波动等因素的影响而给出的修正系数,一般取K=1.3
、
、
——卸料力、推件力、顶件力系数,见下表
料厚
K卸
K推
K顶
钢
0.1
>0.1~0.5
>0.5~2.5
>2.5~6.5
>6.5
0.065~0.075
0.045~0.055
0.04~0.05
0.03~0.04
0.02~0.03
0.1
0.063
0.055
0.045
0.025
0.14
0.08
0.06
0.05
0.03
铝、铝合金、纯铜、黄铜
0.025~0.080.02~0.06
0.3~0.07
0.03~0.09
表2-8卸料力、推件力和顶件力系数注:
卸料力系数K卸在冲多孔、大搭边和轮廓复杂说取上限值。
卸料力
推件力
顶件力
式中F——冲裁力(N);
n——同时梗塞在凹模内的工件(或废料)数;n=h/t
h——凹模洞口的直壁高度(mm);
t——材料厚度(mm);
卸料力
推件力
顶件力
根据模具结构,总的冲压力为
压力机公称压力的确定:
对于冲裁工序,压力机的公称压力应大于或等于冲裁时总压力的1.11.3倍,即
根据冷冲压模具设计指导书p210页初选压力机为:
开式双柱可倾压力机J23-25
5.2、压力中心的计算
模具压力中心是诸冲压合力作用点的位置,为了确保压力机和模具正常工作,应使冲模的压力中心与压力机滑块的中心相重合。
否则,会使冲模和压力机滑块产生偏心载荷,使滑块和导轨间产生过大磨损,模具导向零件加速磨损,降低了模具和压力机的使用寿命。
模具的压力中心,可按以下原则来确定
(1)对称零件的单个冲裁件,冲模的压力中心为冲裁的几何中心。
(2)工件形状相同且分布对称时,冲模的压力中心与零件的对称中心相重合。
(3)各分力对某坐标轴的力矩之代数和等于诸力的合力对该轴的力矩。
求出合力作用点的坐标位置0,0(x=0,y=0),即为所求模具的压力中心。
由于该零件是一个矩形图形,属于对称中心零件,所以该零件的压力中心在图形的几何中心O处。
如图
压力中心结构图
第六章工作零件结构尺寸
6.1、卸料板的设计
卸料装置一般是弹性的,其基本零件是卸料板、卸料螺钉和弹性元件(弹簧或橡胶)组成,弹性卸料板的平面外形尺寸等于或稍大于凹模板尺寸,厚度取凹模厚度的0.6~0.8倍。
卸料螺钉一般采用标准的阶梯形螺钉,其数量按卸料板形状与大小确定,卸料板为圆形时常用3~4个,为矩形时一般用4~6个。
卸料螺钉的直径大小可选8~12mm,各卸料螺钉的长度应一致,以保证卸料板水平和均匀卸料。
弹性卸料装置依靠弹簧或橡皮的弹力来卸料,卸较力不太大,但冲压时可兼起压料的作用。
6.2、弹性元件橡胶的设计
(1)橡胶的形状及数量
由于橡胶允许承受的载荷较大,安装灵活方便,因而是冲裁模中常见的弹性元件。
假设数量为n=1
(2)确定橡胶的自由高度
其中:
卸料板工作行程
为凸凹模凹进卸料板的深度,取1mm
为凸凹模冲载后进入凹模的深度3mm
t为材料厚度0.5mm
其中:
橡胶工作行程
为凸凹模修磨量,取5.5mm
综合上述,
(3)确定橡胶的预压缩量
(4)橡胶的装模高度约为:
6.3、落料凹模板尺寸
凹模厚度:
(其计算结果大于或等于15mm)其中b——冲压件最大外形尺寸:
k——系数,考虑板材厚度的影响,其值可查表3—15.
考虑到推件块的安装空间和运动空间,凹模的实际厚度应增加取
凹模壁厚:
(其计算结果大于或等于30~40mm)
实际取C=30mm
凹模长度:
取
凹模宽度:
取B=150mm
所以,凹模轮廓尺寸为
,为了保证螺孔间、螺孔与销钉孔之间的强度和模具的寿命,一般开的孔与孔之间的距离、销孔与螺纹孔之间的距离不应小于5mm,螺纹孔与凹模刃口间的距离取大于两倍孔径值。
凹模结构图如下图所示:
凹模结构图
6.4、凸凹模的设计
凸凹模的内、外缘均为刃口,内、外缘之间的壁厚取决于冲裁件的尺寸,为保证凸凹模的强度,凸凹模应有一定的壁厚。
凸凹模总长L:
其中
为凸凹模固定板厚度,
为橡胶安装高度,
为弹性卸料板厚度。
其结构如图所示:
`
凸凹模结构图
6.5、冲孔凸模的设计
因为凸摸为内孔凸模,选用直通式凸模,与凸模固定板采用H7/m6配合。
凸模材料应选Cr12,热处理58~62HRC。
凸模的长度根据模具的具体结构确定,长度根据磨损量及固定板、凹模的厚度等来决定的即:
其中
为凸模固定板厚度,
为冲孔凸模固定板,
为落料凸模。
其结构如图所示:
冲孔凸模结构图
第七章模架及其它零件的设计
7.1、上下模座
模座分带导柱和不带导柱两种,根据生产规模和生产要求确定是否带导柱的模座。
本模具采用中间导柱、导套来保证模具上、下模的精确导向。
滑动导柱、导套都是圆柱形的,其加工方便,可采用车床加工,装配容易。
导柱的长度应保证上模座最底位置时(闭合状态),导柱上端面与上模座顶面的距离17mm。
而下模座底面与导柱底面的距离为4mm。
导柱的下部与下模座导柱孔采用H7/r6的过盈配合,导套的外径与上模座导套孔采用H7/r6的过盈配合。
导套的长度,需要保证冲压时导柱一定要进入导套10mm以上。
导柱与导套之间采用H5/h5的间隙配合,导柱与导套均采用T10A材料,热处理硬度渗碳淬硬55~60HRC。
导柱的直径、长度分别为:
导柱:
d/mm×L/mm分别为φ35×230;
导套:
d/mm×L/mm×Dmm分别为φ35×125×48,
模座的的尺寸L/mm×B/mm为315mm×200mm。
模座的厚度应为凹模厚度的1.5~2倍上模座的厚度为35,上垫板厚度取12,凸模固定板厚度取18,凸凹模固定板取22mm,卸料板取18mm,下模座的厚度为35mm。
7.2、模柄
本模具采用带台阶的压入式模柄。
查表2——35得到模柄尺寸如下
、
第八章总结
在大学的学习过程中,课程设计是一个重要的环节。
是我们步入社会与实际工作的一次极好的演示,我十分有幸把课程设计和实际工作有机的结合起来。
经过一学期对模具整体结构和细节的学习与了解,为了更进一步的了解模具制造和加工,利用所学模具知识设计一套简单的垫片冲孔落料复合模具,来巩固所学模具知识。
此次的课程设计是我们从大学毕业走向未来工作的重要一步,从最初的计算、绘图直到完成设计,期间查找资料、老师们的指导与同学的交流,每一个过程都是对自己能力的一次检验和充实。
不但是我更进一步理解和懂得了解以前学到的知识而且还把以前课本上学到的知识连接在一起。
系统的掌握了产品零件的成型工艺分析,模具结构设计的基本方法和步骤,非标准零件的设计基本方法。
使我更进一步地学习和巩固了综合应用、模具课程设计以及相关的理论基础和专业知识。
此次课程设计是对我专业知识和专业基础知识一次实际检验和巩固,课程设计收获很多,提高自己的绘图能力。
学会了正确运用技术标准和资料,培养了认真负责、踏实细致的工作作风和严谨的科学态度,强化了质量意识和时间观念,形成了从业的基本职业素质。
但是课程设计也暴露出自己专业基础的很多不足之处,比如缺乏综合应用专业知识的能力,对材料的不了解。
这次实践是自己大学所学的一次大的检阅,使我明白自己知识还很浅薄。
虽然马上要毕业了,但是自己的求学之路还很长,以后更应在工作中学习,努力使自己成为一个对社会有所贡献的人。
参考文献
[1]翁其金,徐新成冲压工艺与模具设计:
机械工业出版社。
[2]王芳.冷冲压模具设计指导[M].北京:
机械工业出版社,1998。
[3]王新华,袁联富.冲模结构图册[M].北京:
机械工业出版社