冲压模具设计制造规范.docx
《冲压模具设计制造规范.docx》由会员分享,可在线阅读,更多相关《冲压模具设计制造规范.docx(17页珍藏版)》请在冰豆网上搜索。
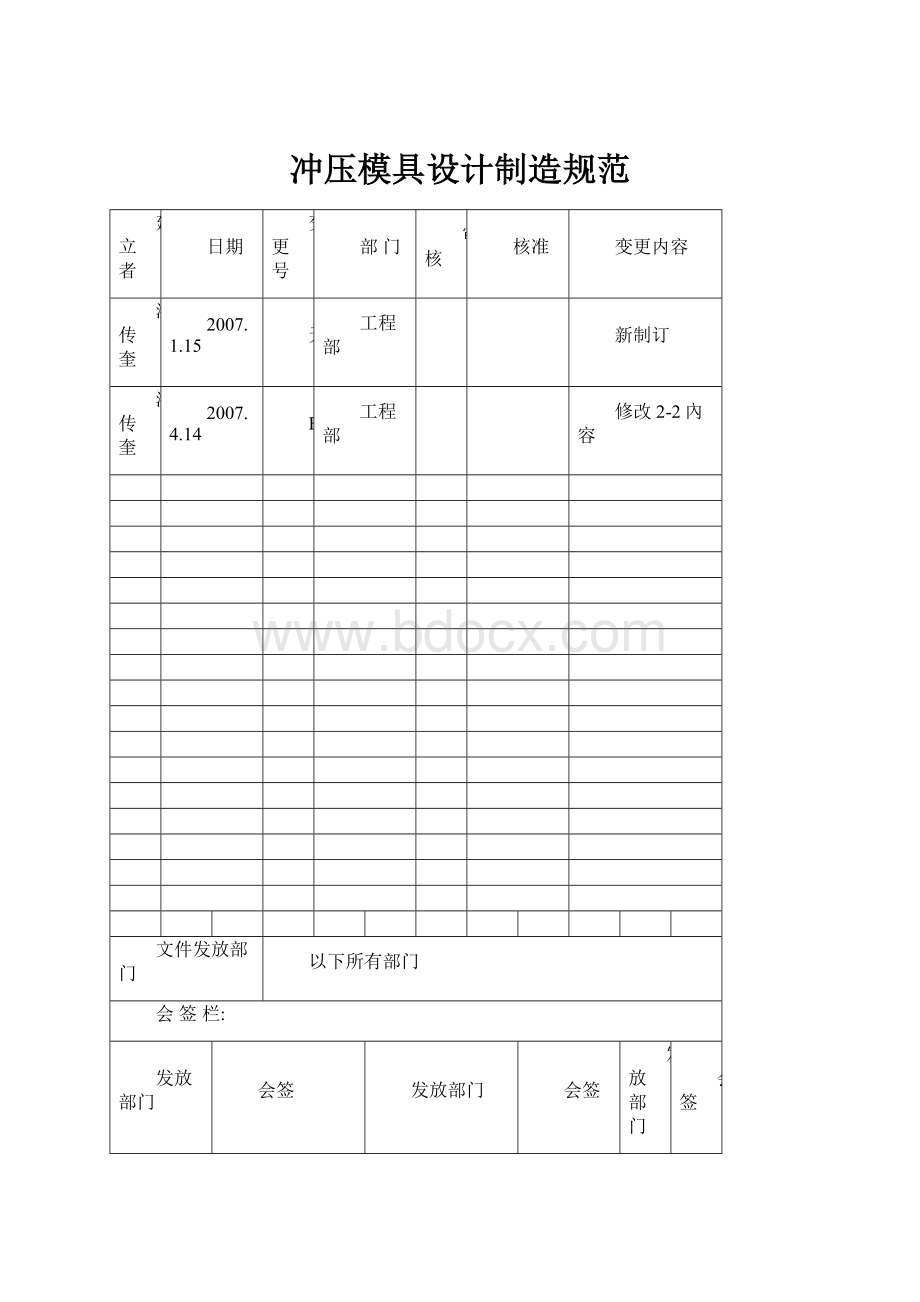
冲压模具设计制造规范
建立者
日期
变更号
部门
审核
核准
变更内容
潘传奎
2007.1.15
无
工程部
新制订
潘传奎
2007.4.14
B
工程部
修改2-2內容
文件发放部门
以下所有部门
会签栏:
发放部门
会签
发放部门
会签
发放部门
会签
工程部
一.目的:
统一公司模具设计规范,更好地配合加工单位,适应快速作业的需要。
二.范围:
适用于本公司所有部门之作业。
三.权责:
由各个部门编写文件之人员负责执行此规范。
四.内容:
1.开模前相关作业程序:
1-1程序说明:
新项目提出开模时,模具工程师必须先向业务或此项目负责人确认此项目预估的量能会有多少,之后再依照此量能特性加以分析,以最快速、经济、合理之要求达成最佳化冲压模具状态,以确保后续之量产能力。
模具开发前期制作冲压模具工程设计制作分析,此分析用意在于预见模具开发可能产生之问题点,将其整理以及早发现及早修正的形态为目的,其次安排各工程图面的合理性(包含单工程模具工程图面以及连续模料带图面)、考虑模具结构设计的安全以及正确性……等,另外依照评估后模具形式决定模具材质以及热处理特性,再规范定义各配件的使用时机,明确规划出最佳化模具的形式。
在模具制作期间,模具开发进度的掌控往往是造成一个新的项目是否有办法如期成行的一个重要症结点。
试模时实际的状况记录于试模检讨记录中,藉由实际的问题记录以及改善确认方式此套新开发的模具运行无误有量产能力,最后确认每个单件皆符合RD所设计的规范要求后,签认模具移交单以做模具验收的标准,而针对以上叙述以下用流程图加以说明:
预估产量之确定冲压模具级数及作业分类原则
冲压模具工程设计制作分析DesignForManufactureReport
工程图以及料带图面确定工程模:
各工程工序图
连续模:
料带图
模具结构确定各工程模具结构图
模具开发进度掌控模具开发进度表
试模检讨改善报告试模检讨改善记录
全尺寸检验FAIReport&CpkReport
模具验收确认模具验收办法
2.冲压模具级数、寿命定义及模具组织架构:
2-1冲压模具级数定义:
各类冲压模具依照不同程度产能之要求,定义出三种级数冲压模具结构尺寸以及相关规定之设计形态,分别为每个月产能在50K以下少量产能型态的模具(定义为一般产能模具)50K~100K之间中产能型态之模具(定义为中产能模具)以及每个月100K
以上产量之模具(定义为高产能模具),定义各级数产能模具如下表所示:
月产能
定义
级数
100K以上
高产能模具
A
50K-100K
中产能模具
B
50K以下
低产能模具
C
2-2冲压模具寿命定义:
由于模具在冲压过程中有一定的磨损、变形,为了保证产品的质量,冲压一定次数后就必须有一次模具保养,根据本厂内多年的现场统计,总结模具保养规律如下:
模具种类
修模寿命(万次)
模具保养次数
模具总寿命(万次)
复合模\下料模
3—5
(根据不同的材质决定)
10
30—50
(根据不同的材质决定)
冲孔模
8—10
(根据不同的材质决定)
10
80-100
(根据不同的材质决定)
成型模
3—5
(根据不同的材质决定)
20
60-100
(根据不同的材质决定)
连续模
8—10
(根据不同的材质决定)
10
80-200
(根据不同的材质决定)
2-3冲压模具结构分类:
冲压类模具可分为下料形式、冲孔形式、折弯形式、连续模具等,其模具结构、板材尺寸、模具材质规范如以下所示。
2-3-1冲压模具类型:
(A)下复合下料模具结构:
零件代号
零件名称
零件代号
零件名称
UP
上模座
DS
下脱板
UB
上垫板
LB
下夹板
PH
上夹板
LP
下模座
PS
脱料板
B2
下垫块
DU
上模板
B1
下扥板
DE
下模板
PUNCH
冲头
(B)冲孔模具结构:
零件代号
零件名称
零件代号
零件名称
UP
上模座
LB
下垫板
UB
上垫板
LP
下模座
PH
上夹板
B2
下垫块
PP
止当板
B1
下扥板
PS
脱料板
PUNCH
冲头
DE
下模板
(C)折弯模(内脱式折弯模结构):
零件代号
零件名称
零件代号
零件名称
UP
上模座
DE
下模板
UB
上垫板
LB
下夹板
PH
上夹板
LP
下模座
DU
上模板
B2
下垫块
PS
脱料块
B1
下扥板
X3
档料块
EJ
下顶板
DS
内脱板
(D)折弯模(滑块式折弯模结构):
零件代号
零件名称
零件代号
零件名称
UP
上模座
LP
下模座
UB
上垫板
B2
下垫块
UE
上模板
B1
下扥板
DS
下脱板
PUNCH
冲头
LB
下垫板
2-3-2冲压模具模板长宽尺寸:
(A)宽度以及长度决定
模板长度≒(展开长度+3mmx2)+(内导柱直径x2)+展开比例分配x2
模板宽度≒(展开宽度+3mmx2)+(内导柱直径x2)+展开比例分配x2
(B)宽度以及长度决定
模座长度≒模板长度+展开比例分配
模座宽度≒模板宽度+展开比例分配
(C)展开比例分配:
展开长度<50mm----35mm
50mm<展开长度<150mm----40mm
150mm<展开长度<300mm----50mm
300mm<展开长度<550mm----60mm
550mm<展开长度------------------70~80mm
2-3-3模具等级与材质对应表:
模具等级
模板名称
A
B
C
上模座
A3
A3
A3
上垫板
D2
D2
D2
上夹板
A3(冲头处割入块),快拆式
A3
A3
止当板
D2
D2
D2
上脱板
SLD(冲头处割入块),快拆式
SLD
SLD
下模板
SLD(刀口加SKH-9入块),入块为快拆式
SLD(刀口加SKH-9入块)
SLD
下垫板
D2
D2
D2
下模座
A3
A3
A3
下垫脚
A3
A3
A3
3.模具设计分析:
开发期之模具工程设计制作分析,其目的在汇整模具开发问题以提供RD人员机
构设计修改之依据且能有效缩短开模检讨会议的时间。
3-1设计分析方向:
新产品开模前针对成品图面进行模具分析作业分析内容有以下几点:
1.模具在设计与制作加工上的困难处。
2.因后制程影响之质量变量。
3.更佳的设计建议方式提出(模具设计或是成品设计)。
3-2分析档案的制作DesignForManufacture(DFMReport):
1.成品图本身的展开后干涉之提出。
2.因原素材特性所产生制作之变异之提出(如撕裂、抽引高度不足)。
3.实际实验数据提出辅佐验证。
4.模具设计制作上加工或生产困难之处。
5.因冲压加工制程有可能影响之质量变量。
6.因后加工制程影响之质量变量。
7.认为有更佳的设计建议方式提出(模具设计或是成品设计)。
4.模具设计要求:
4-1设计前期确认:
1.客户指定并承认产品的毛边方向和压毛边的位置。
2.在模具设计以前,必须由设计主管确认料带布置或工序图布置。
4-2基本设计要求:
4-2-1基本设计规范要求:
(A)所有定位孔一般皆应该设计在废料或者是可去除的部分。
(B)工程模或是连续模之脱料板皆必须具有对料片或料带完全整平的功能,防
止冲切时造成定位会成形不良。
(C)一般的模具设计应设计有防呆装置确保组模不会颠倒或者在不正确的位置
安装。
(D)废料的排出应该在设计检讨时明确地定义。
(E)冲孔、抽引、折弯等设计尽量要做成可以在冲压机床内可移换或可调整,以便
尽可能地减少修模试模停机时间。
(F)当产品在成型部位有冲孔,则冲孔应该在成型后进行。
以确保客户对孔的相对位置的管控。
(G)设计考虑应该在潜在可能的高维修率的部位加入硬化钢的衬套和入块,以
防止为了修整一个孔而研磨整个模块/板。
(H)模座应该设置吊孔以便安全方便地搬移和架模。
(I)所有的模块和垫板都应该标示有详细的编号,材资和硬度。
(J)拉伸成型时,必须有硬作入块和衬套.
4-2-2改善成形性基本设计要求:
(A)为了使折弯材料预变形,减少折弯时的阻力以及防止折弯时所产生的拉料变
形,为使折弯尺寸更准确,可适时增加压线设计。
(B)为减小折弯时的回弹,使折弯尺寸更准确减小折弯所产生的拉料变形,可适时增加折弯压筋入子设计。
(C)在产品要求剪切无毛刺时,可利用压毛边方式倒去除冲切时所产生之毛刺。
(D)对于字模的装夹方式为了便于快速拆卸更换,字模皆需采用打入子的结构方
式,并且需设计有防呆装置以免导致字体图形方向错误。
(E)根据产品的要求不同,莎拉孔一般有深莎拉和浅莎拉两种分别,此部分需确认无误后进行设计。
(F)若产品折弯处要求不可有刮伤状态时折弯刀可使用滚轮机构方式进行设计。
(G)产品中常遇到之凸点之定位方式,可在模具内部设计打凸点冲头定位方式进行设计。
(H)模具设计中反折压平一般采用上压式以及侧推式(以及其它的设计方式),模具之设计模式需与设计主管讨论确定后可进行设计。
(I)模具设计卷缘成形一般采用上压式以及测推式(以及其它的设计方式),模具之设计模式需与设计主管讨论确认后可进行设计。
(J)一般攻牙成形各部分尺寸之表准请参照下表,若有特殊抽牙状况请与设计主管讨论确认后可进行设计。
公称尺寸M
螺距P
板厚T
预冲孔d
抽牙冲子d1
冲模孔D
M3
0.5
0.6
1.5
2.7
3.5
0.8
3.7
1
3.9
1.2
4.2
0.8
4.6
M4
0.7
1.8
3.6
1
4.8
1.2
5.1
1.5
5.5
#6-32
0.8
1.8
3.1
4.1
1
4.3
1.2
4.6
1.5
5
4-2-3模具结构特性基本设计要求:
(A)弹簧长度选择需保证在开模状态时弹簧的预压量2~4mm。
(B)连续模带料部分再最后一站剪切或剪断成形,产品要求外观或手可触摸处
均无毛边时可进行预剪装置机构设计。
(C)折弯刀固定方式需用铣削孔沉入方式固定,铣槽深度根据其产品折弯高度
而定,夹板槽深5~8mm以上,且须精铣加工。
(D)使用切断成形设计时先剪切后折刀口为一个料厚,斜度1.5度,目的是减
少冲头同切口之间的接触面,以便减少摩擦,且为了保证刀口强度防止崩
刃,冲头切口底部直2mm,冲头折弯边高度需有1.5T。
(E)对于连续模设计时外导柱之导柱安装于下模,而导套则安装于上模。
对于
工程模和自动化线(ROBOT)而言,则把外导柱安装于上模而把导套安装于下模,导套可高于成品10mm,导柱依实际闭模高度设计。
若为翘翘板结构模具则外导柱需选用无钢珠导柱。
(F)单边冲切冲头必须设计有靠刀形式。
(G)若冲压材料为铝材、铜材等软质材料或表面有外观需求时需使用铁氟龙材
质顶料销。
(H)共享板(零)件线孔需做在对产品尺寸无直接影响的板(零)件上,例如
复合模公母模共享时做在公模上。
(I)滑块固定方式形式规范如下:
1.用于中小型滑块,依靠滑块的垂直边限位。
2.用于以共享方式加工的大型滑块﹐限位块采用入块形式
3.用于需快速装卸的大中型滑块﹐依靠滑块底部的限位板限位
4.适用于需要滑块在接触料片前先复位的场合﹐靠滑块中的顶料销作用﹐先将滑块复位﹐顶料销长度通常为7mm﹐浮出端面2.0mm﹐选用红色扁线弹簧。
5.适用于要求中间垂直p上下运动﹐左右滑块水平运动的块合﹐中间滑块依靠内导柱导向﹐左右滑块用等高套筒限位﹐等高套筒长度取夹板厚度加0.5mm。
(J)在连续模设计中,为使材料送料精准,使用节距定位来保证材料的送料步距。
且节距定位有切舌式以及侧刃定位两种形式,除非设计上之必要否则皆需使用侧刃定位方式设计。
(K)为防止模具在空打时打坏零件,如字模、压线印以及一些特殊模具力的不平衡状况时,必须设计限位柱以承受力量。
(L)侧推成形模具成形时,外定位需采用浮升定位的方式。
(M)选用两用浮升销不仅要考虑材料的厚度,还要考虑模具的大小(优先取大)
(N)内定位销与产品间隙为单边0.02~0.03MM,外定位块与产品间隙为0.05MM,且内定位销必须有对称顶料销D,顶料销与内定位保持实际距离5.0MM;若无内定位销时,外定位块与工件间隙应为0.03MM.内定位脱料板让位割单+0.05MM,外定位销脱料板让位钻单+0.5MM,外定块脱料板让位割单+0.05MM(但压毛边的外定位间隙割单+0.15MM),三个非工作面割单+0.5MM,外定位的数量最少6支(一般取8支)且有防呆。
(O)为防止导正销将材料带起,在导正销两旁均匀放置顶料销以便脱料,顶料销与导正销距离L不可过长,弹力应力求一致,避免工件变形。
(P)连续模具必须要设置导料架引导材料。
(Q)内导柱导正可提高模具精度,节约模具成本,且便于模具组立。
但须注意若是使用
ROBOT线机械手冲压时,请考虑机械手的台升高度是否大于内导柱凸出高。
(R)在产品上铆合螺帽时,为了保证螺帽的定位稳定和成形以后产品质量,在设计模具时都要为螺帽设计专用的定位装置。
(S)在模具设计时对其模具零件与模板之间的间隙如下表所示。
上模座
上垫板
上夹板
止挡板
脱料板
上模板
下模板
内脱板
下夹板
下垫板
下模座
冲头
X
X
0.005
0.5
0.01
X
5%t直2.0锥1度(下模刀口)
X
X
1
1.5
固定入块
X
X
X
X
0.005
X
0.005
X
X
X
X
活动入块
X
X
X
X
X
X
0.01
X
X
X
X
浮升块
X
X
X
X
X
X
0.015
X
X
X
X
浮升引导销
X
X
X
X
X
X
0.015
X
X
X
X
浮升两用销
X
X
X
X
X
X
0.015
X
X
X
X
顶料销
X
X
X
X
X
X
0.05
X
X
X
X
顶杆
X
1
1
X
X
X
X
X
X
1
1
合销
0.01
0.1
0.01
X
X
0.01
0.01
X
0.01
0.1
0.005
辅助导柱
X
X
0.01
1
0.008
0.008
0.008
0.008
0.01
X
X
辅助导套
X
X
X
X
0.008
X
0.008
X
X
X
X
外导套
Фd+0.12(压入式)
外导柱
Фd-0.008~-0.005
等高套筒
0.5
0.5
0.5
0.5
X
X
X
0.5
0.5
0.5
0.5
(本资料素材和资料部分来自网络,仅供参考。
请预览后才下载,期待您的好评与关注!
)