管道制作方案.docx
《管道制作方案.docx》由会员分享,可在线阅读,更多相关《管道制作方案.docx(59页珍藏版)》请在冰豆网上搜索。
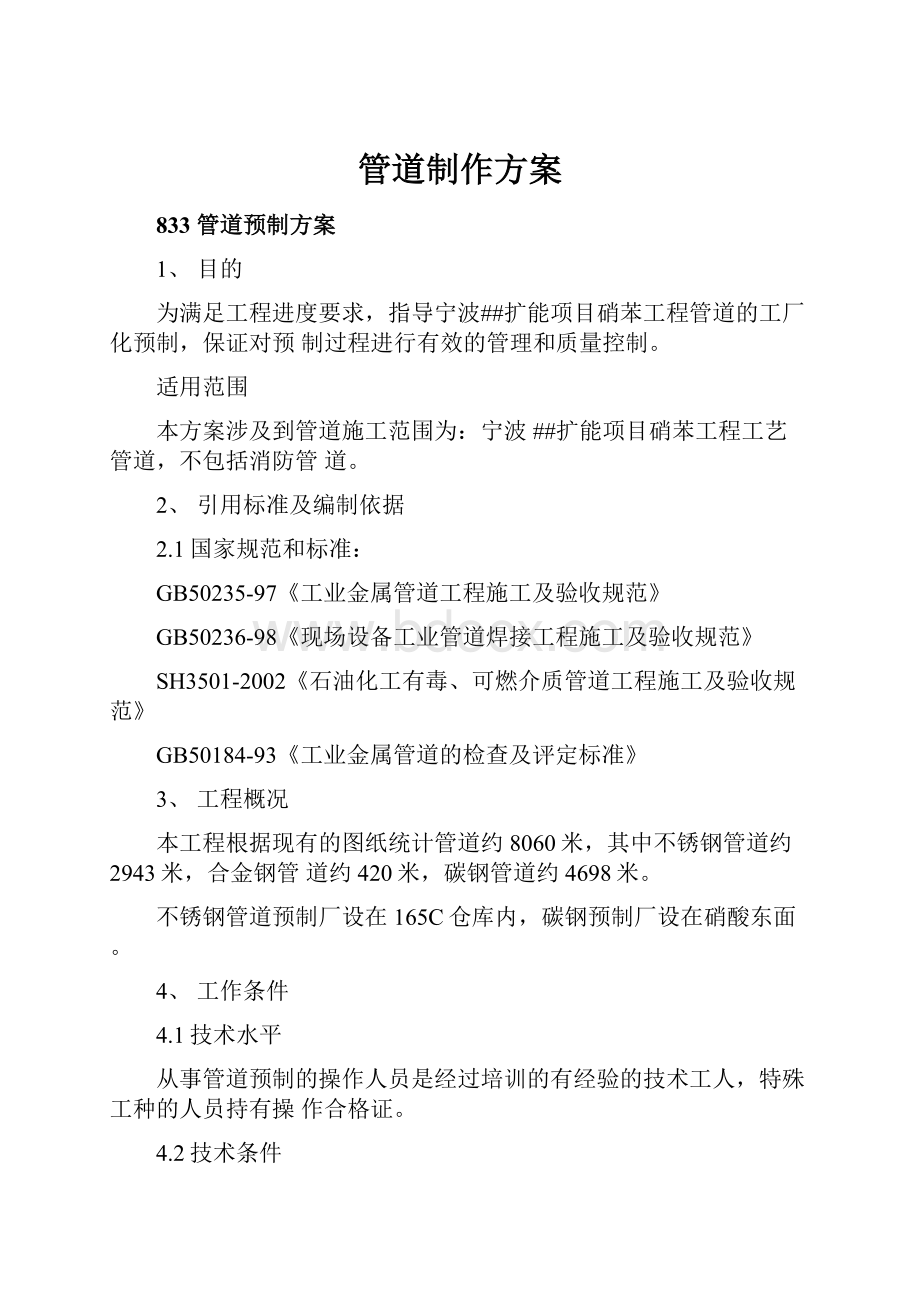
管道制作方案
833管道预制方案
1、目的
为满足工程进度要求,指导宁波##扩能项目硝苯工程管道的工厂化预制,保证对预制过程进行有效的管理和质量控制。
适用范围
本方案涉及到管道施工范围为:
宁波##扩能项目硝苯工程工艺管道,不包括消防管道。
2、引用标准及编制依据
2.1国家规范和标准:
GB50235-97《工业金属管道工程施工及验收规范》
GB50236-98《现场设备工业管道焊接工程施工及验收规范》
SH3501-2002《石油化工有毒、可燃介质管道工程施工及验收规范》
GB50184-93《工业金属管道的检查及评定标准》
3、工程概况
本工程根据现有的图纸统计管道约8060米,其中不锈钢管道约2943米,合金钢管道约420米,碳钢管道约4698米。
不锈钢管道预制厂设在165C仓库内,碳钢预制厂设在硝酸东面。
4、工作条件
4.1技术水平
从事管道预制的操作人员是经过培训的有经验的技术工人,特殊工种的人员持有操作合格证。
4.2技术条件
4.2.1技术文件
(1)用于工厂化预制的管道轴测图
(2)相关的施工技术文件(作业指导书、工艺规程)和管理程序
(3)施工技术交底卡
(4)管材及配件尺寸标准
4.2.2质量控制文件
(1)材料合格证或验收报告
(2)操作工序交接单
(3)管道预制件的符合性检查表
(4)焊口跟踪图及跟踪单
(5)检验报告(RTPT、VT)
423预制材料
(1)根据预制进度计划合理领用预制材料。
(2)领用的材料必须具有产品合格证或复验报告。
(3)原材料的领用、贮存和发放按本项目投标文件《甲供材料管理程序》执行。
4.2.4预制场地、预制设备和工机具
(1)预制场地应有良好的通风状态和卫生环境。
(2)预制车间的设备加工能力须满足预制的操作要求,并具有良好的操作性能。
(3)预制车间的工机具应齐全,并有专门的堆放场所和进行专人管理。
(4)配制一台3M无油空压机及相应的管线布置,用于管道预制件的管内吹扫。
5、操作流程
5.1碳钢管道工作流程见附录1
5.1不锈钢管道工作流程见附录2。
6预制加工图绘制
6.2任务分配及资料收集
根据施工计划和现场施工提出的需求计划,经预制厂负责人确认后,根据技术员资源状况,合理分配任务,提出进度要求。
技术员在绘制预制加工图时要依据以下资料:
(1)工艺流程图;
(2)带有管线材料表的轴测图;
(3)管道平(剖)面图及局部透视图;
(4)设备平面布置图;
(5)设计说明书和施工技术条件(或设计指定的标准及规范)。
6.3预制段划分
6.3.1表示说明
(1)预制段指两安装焊口之间在预制厂预制的连续部分,标记表示:
XXX-XXX-XXX-GD—
LNF
L――管道轴测图的图号
N分段号,用英文字母表示
F——管道介质流向,用箭头表示
(2)焊口号编制以一张预制图为单位连续编制。
预制焊口与安装焊口分别以不同的字母来表示,用“SWn”表示预制焊口,“FWn”表示安装焊口,n代表阿拉
伯数字。
如:
SW1、SW2、SW3、SW5分别表示1、2、3、5号焊口为预制焊口,要在预制车间内完成;FW4、FW6表示4、6号焊口为安装焊口,不在预制车间内完成,而由现场组装时焊接。
(3)定长管段指两焊口之间需要定长加工的管段,标记表示:
管道的公称尺寸一一定长管道长度(+100)――材料特性
(4)定长管道长度指两焊口间管段长度,如有(+100)表示可调整管段,其预留长度100mm如不是可调整段表示时不加(+100)。
6.3.2预制深度
(1)为了尽可能多在预制车间内完成管道的制作,结合平面图在考虑方便运输与安装的前提下,尽量扩大预制深度。
(2)对于搬运中容易受损的部件如大尺寸阀门等,不宜在预制车间内与管道连接。
6.3.3预制管段划分
(1)焊口设置必须注意:
结合平面图支架位置,焊口应离开支吊架边缘至少100mm;
焊口不能设在穿墙或穿楼板套管内,且应尽可能离开墙面或楼板面200mm(最低不得小于100mm)以上;
安装焊口(即分段的连接点)的位置应尽量设在便于现场操作的部位。
(2)当两不同管线的连接点为焊口时,则该点为安装焊口
(3)当两不同管线以直管或弯管连接时,该焊口的编号应排在下游管段上(以介质流向确定)。
(4)当两不同管线在三通处连接时,则该焊口的编号设在支管上。
(5)轴测图上标注的设计长度包括了管道元件的长度,定长管道长度标注要减去管道元件长度,定长管道长度包含了焊口的宽度,其在坡口加工时进行消除。
(6)设置调整段
为了防止因土建、设备安装和焊接时所产生的误差,须在管道的x、y、z三个方
向上设置调整段,即在三个不同方向的长度上增加一段可供调节的余量。
设置调整段时,宜将几张图所组成的管系综合起来统一考虑,在不同方向的管段
上选择适当部位设置调整段,以尽量减少现场切割的工作量。
调整段上必须设安装焊口。
调整余量的长度一般为100mm。
预制图上在定长管段长度后面用(+100)来表示。
6.4审核批准
审核批准由预制厂负责人负责,审核时要对以下内容进行检查:
(1)是否与现场申请的管线一致
(2)预制管段的设置是否合理
(3)预制焊口和安装焊口设置是否合理
(4)可调整段设置是否合理
6.5填写身份卡
身份卡包括了每根管道的基本信息,预制过程中资料记录的查询信息及过程参与人的确认,一份身份卡对应一根管道。
此处填写的内容包括管道基本信息和预制管道材料的尺寸、规格型号、数量等。
6.6制作配料单
每根管线制作一份配料单,配料单包括项目号、管线号、预制管道材料的尺寸、规格型号、数量、配料人、领发料人签字,制作好的配料单成批发给材料员进行配料,填写完整的配料单暂保存在材料管理处,以备材料员查询。
7、操作程序及技术要求
7.1下料切割
7.1.1—张等轴图附1份下料尺寸表,应由技术人员负责编制,在确认每一段下料尺寸时,应精确计算,主要考虑预制段尺寸和下料段尺寸之间的差异,下料段尺寸应去除弯头、三通、大小头等管配件的理论尺寸以及规范规定的焊口组对间隙;法兰、垫片的厚度以及其它配件(如阀门、过滤器等)的理论尺寸。
如有煨弯,则应认真计算弯管段的下料尺寸(包括弯管作业时所需的超长)。
7.1.2调整段的下料尺寸包括下料段的尺寸加调整余量,调整余量在三维图上已给出。
如未给出,则由图纸转换人员根据情况来确定余量长度。
调整余量长度一般为50〜
100mm
7.1.3在按下料表进行下料时,操作人员应考虑到切割造成的误差:
(1)
热切割产生的热影响区
(2)
切口粗糙误差
(3)
其它缺陷
7.1.4钢管切割之前应进行原有标记移植。
7.1.5不锈钢管在使用砂轮切割时,应使用专用砂轮片。
7.1.6管子切口质量应符合下列规定:
(1)切口表面应平整,无裂痕、重皮、毛刺、凹凸、缩口、熔渣、氧化物、铁屑等缺陷或杂物。
(2)切口端面倾斜偏差不应大于管子外径的1%且不得超过3m(如执行的标准不同时,按相应标准执行)。
7.1.7下料完成后,操作人员应在下料表上签字,并随下料段一起交下一道工序。
7.2配料
配料应由专职材料员负责,原则上按等轴图进行管配件配料。
7.2.1配料工作应根据预制周计划和材料到货情况按等轴图进行配制。
7.2.2可按每张等轴图用专用箱子分开配放,也可几张或几十张图张一起配好,并在箱子上贴上配好的材料清单。
7.2.3预制人员领用(或专送)时,领用者应按材料清单进行复查并在清单上签字确认,清单一式两份,领用者和材料员各保管一份。
7.3坡口加工
坡口加工可在和管子下料同时进行,也可单独进行。
7.3.1管子、管件的坡口型式和尺寸应符合相应的图纸和设计文件的要求,当设计无规
定时,按GB50235-97规范附录B第B.0.1条规定确定。
7.3.2不同壁厚管道组对时,当内壁错边量超过设计规定或外壁错边量大于3mm寸,应
进行修整。
修整尺寸应符合设计文件要求或按GB50235-97规范图5.0.8条焊件坡口型式规定执行。
7.3.3管道坡口加工一般采用机械方法,如用热加工方法加工坡口后,则应去除坡口表面的氧化皮,熔渣及影响接头质量的表面层,并应将凹凸不平处打磨平整。
7.3.4无论用哪一种方法,坡口加工完毕后,均应去除油污、水分、铁锈等杂物。
7.4弯管及焊口组对
7.4.1焊口组对时,应对坡口及其内外表面10mn范围内进行清理,去除油污、油漆、铁锈、毛刺等杂物。
7.4.2对于不锈钢管组对用的台架、支承架等,应用衬垫材料进行隔离。
7.4.3组对后,应保持管子的平直。
7.4.4对于焊接时易产生变形的簿壁管,组对时,应使用专用夹具进行固定。
7.4.5厚壁大口径管道组对时,如采用定位板进行定位,定位板的材质应和母材相同或相似。
取下定位板时,应用砂轮机磨削,且防止损伤母材。
7.4.6焊口组对时,应做到内壁平齐,内壁错边量不宜超过壁厚的10%且不大于2mm
7.4.7不等厚管道组成件组对时,应按规范要求进行修整后再进行组对。
7.4.8所有组对好的焊接接头尺寸应满足设计文件或图纸的要求。
7.5不锈钢管道焊缝的表面处理
如设计文件的规定或执行的标准有要求,应对所有的不锈钢管焊缝的外表面进行处理,去除表面氧化层,达到金属母材本色。
7.6管道预制件的标记
7.6.1对所有管道预制件进行标记,按管道预制图上的管段编号进行。
7.6.2标记为临时性标记,可用记号笔或油漆进行。
7.6.3标记应清晰,且能保持较长时间,至少应保持到该管段安装完毕。
7.7管道预制件清洁
对于预制好的管段进行清洁度检查,管内不得有焊渣、油迹、石子等外来物,如有杂物,应用擦洗或压空吹扫的办法来进行清除,清洁过的预制管段应及时采取相应的保护措施。
7.8预制件的符合性检查
应根据设计文件要求,对管道预制件进行符合性检查(按比例),主要内容如下:
7.8.1确认使用材料的规格、型号、材质正确无误。
7.8.2确认管道预制段的尺寸符合图纸要求。
7.8.3确认焊缝的外观质量和无损检验满足设计文件要求。
7.8.4工序交接清单签字完毕。
7.8.5如需要,按每张等轴图填写好材料质保书(炉批号)跟踪表。
7.8.6填写好管道预制件符合性检查记录。
说明:
工序交接单由各工序操作人员负责检查确认,预制件的符合性检查记录由质量
检查人员负责填写并签字确认。
7.9管道预制件的包装保护
7.9.1对于小口径的管道预制件的管端用聚乙烯管帽进行封口,如管帽较松时,可用胶粘带固定在管子上。
7.9.2对于大口径的管道预制件的管端用清洁的无毛白布或聚乙烯塑料布包扎并用胶粘带固定,或者采用塑料管帽进行封堵。
7.9.3法兰面一般用胶合板进行包装,包装方法可用尼龙绳(镀锌铁丝)通过法兰螺栓
孔和盖板上预先钻好的孔绑扎固定。
7.9.4如果设计有要求,对整个不锈钢预制件用聚乙烯薄膜包裹起来。
7.10管道预制件的堆放和领用
管道预制件的堆放和领用参照投标文件物项管理类。
8、设备、工机具配置
设备、工机具配置见本项目施工组织设计施工设备和工机具配置计划管道机具配置计划。
9、安全事项
安全事项按本项目施工组织设计HSE方案的要求执行。
10、附录
10.1碳钢管道预制厂工作流程图(附录1)。
10.2不锈钢管道预制厂工作流程图(附录2)。
附录
碳钢管道预制厂工作流程方框图
图纸*任务单►班组仓库领料材料检验
素材
喷砂
附录二
不锈钢管道预制厂工作流程方框图
放线下料
余料标识移植
切割坡口
存放待用
对
弯
*任务单
•班组
仓库领料
材料检验
返修
建帐登记
焊缝酸洗
编号
符合性
检查
密圭寸
堆场・
预制件
存放
G”
发放
领料单
—?
?
资料
存档
834管道安装方案
1、目的
为保证本项目管道安装工程的施工质量和满足工程进度要求。
2、适用范围
本方案适用于宁波##扩能项目硝苯工程工艺管道安装工程的施工,不包含消防管道及
工艺管道的防腐、保温。
3、编制依据
GB50235-97《工业金属管道工程施工及验收规范》
SH3501-2002《石油化工有毒、可燃介质管道工程施工及验收规范》
GB50236-98《现场设备工业管道焊接工程施工及验收规范》
GB50184-93《工业金属管道的检查及评定标准》
4、工程概况
见管道预制方案。
5、工作内容及操作流程
&主要施工方法及步骤
6.1管道安装前的施工准备
6.1.1管道施工应具备下列条件方可开工:
(1)技术资料满足施工要求,施工图纸已会审。
(2)施工方案已经批准,开工前必须进行详细的技术交底和HSE交底。
(3)材料、施工人员、工机具满足施工和HSE要求,施工环境符合要求,并能保证连续施工。
(4)管道安装前,设备安装已基本完成,需配管的设备已精平完毕并有工序交接卡。
6.1.2施工要求
(1)管道施工应按设计图纸要求进行,如发现施工图与实际情况不符时,管道工程技术人员应及时向监理、业主提出,不得自行更改,设计修改或材料代用须书面报经业主批准。
(2)施工人员必须了解CNF编制的相关施工程序及业主指定的技术标准、规范,熟悉施工技术要求和图纸,在施工中严格执行。
(3)要求熟悉施工现场,合理布置电、气焊机具、材料堆放场、制作场和运输通道等。
6.1.3材料验收
(1)管道组成件及管道支承件应具有制造厂的质量证明书。
(2)按设计要求核对材料的规格、材质、型号,材料不合格者不得使用。
(3)合金钢管道组成件应采用光谱分析或其他方法对材质进行复查,并应做标记。
(4)材料外观检查:
无裂纹、缩孔、夹渣、折迭、重皮等缺陷,所有管道直径及壁厚偏
差均不得超出相关标准的规定(普通管道外径偏差允许值为土10%DN壁厚偏差为
+12%-10%)。
(5)管子、管件的几何尺寸及光洁度应符合各类管道的设计规定要求。
法兰密封面平整、
光洁、不得有毛刺及经向沟槽。
螺栓、螺母的螺纹完整,无伤痕、无毛刺等缺陷,
配合良好。
垫片无折损、皱纹等缺陷。
(6)阀门在验收时应进行外观检查,阀门的外观质量应符合产品标准的要求,不得有裂纹、氧化皮、粘砂、疏松等影响强度的缺陷。
(7)管道支、吊架所用的弹簧,外观构造、尺寸和材质应符合设计规定要求;支吊架弹簧应有制造厂的合格证。
(8)材料验收时要填写管件检查验收记录、钢管检查验收(效验性)记录。
6.2管道安装
6.2.1管道安装按下列程序进行:
检查先决条件|」预制管段的运输及现场存放支吊架制作安装
管道无损检测,—管道焊接管道安装
622管道安装的先决条件
(1)管道安装应在建筑物、构筑物施工基本完成,有关配管的设备及支、吊架已就位、
固定、找平后进行。
(2)材料已经检验合格,且有合格证书。
(3)阀门已经按规范要求进行了检验或试验,检验(试验)记录齐全。
(4)管道预制已完成,并经检验合格。
(5)管道安装前,对各系统,各区段需用的阀门、仪表配件等按设计图纸,分段组件编
号,认真核实实物和施工记录无误。
6.2.3预制管段的运输及现场存放
应按照周计划对需要的预制管段运输至安装现场。
管段运输时应注意保护预制管段和油漆不被损坏,并且要注意管端的保护装置在安装之前应保持完好。
管段运至现场后要妥善保管,防止管段被污染。
不锈钢管段运输及现场存放应置于垫木或其他不对不锈钢产生污染的材料上,并防止与车身和其他碳钢部件直接接触。
不锈钢
管段吊装时要用尼龙吊装带。
预制管段的运输的要求及控制方法详见《质量计划》
6.2.4支、吊架制作安装
制作安装管道支、吊架,按设计要求制作安装,支吊架制安和管道安装同时进行。
管道支、吊架制作安装按照本项目投标文件《管道支吊架制作安装方案》执行。
6.2.5管道安装
(1)检查各部件的质量情况,不符和要求的及时处理,防止把不合格的部件用于系统中。
(2)不锈钢管道吊装时应使用尼龙吊装带,禁止用钢丝绳直接吊装不锈钢管段。
(3)连接各部件、法兰、阀门,焊接并经检查合格。
(4)管道使用的阀门、仪表等,安装前根据设计要求进行强度和密封试验,调试合格。
不合格的产品严禁安装。
符合安装要求的产品应附有合格证书。
(5)管道安装前,应按图纸进行测量放线,确认现场实际与图纸是否一致,无误后再进行安装。
(6)管道安装时,应对照管道预制分段图进行。
对留有调整段的,应按现场实际进行测
量,根据实测尺寸切割所需的调整尺寸。
(7)管段切割及坡口加工时,不锈钢管应使用专用工具(砂轮片、锉刀等),不可与碳钢管混用。
(8)管段安装前应检查管道内部清洁度,如发现管内有污垢,应先进行吹扫或用其他方法将管内清理干净,方可对管段进行组对、焊接。
(9)管道安装同时填写管道施工检查记录。
626管道焊接
管道焊接按本项目投标文件《管道焊接方案》执行。
在管道焊接完成后,根据设计和规范要求及时对焊缝进行无损检测及热处理(根据需要)。
7、管道安装技术要求
7.1管道材料的接收、储存和检查、试验
7.1.1碳钢、不锈钢管道材料接收、储存要求
(1)到货的管材、管件运至二级仓库后,要有规律地摆放。
不锈钢及管件要采取防渗碳
措施,且保持堆放场地清洁。
不锈钢管材及管件、碳钢管材及管件、塑料管材及管件不得堆放一起。
室外保存的管材应储存在较高位置,并用木方垫好同时对各种管材、管件要有明显标识,对要求涂刷色标的管件、管材,要按规定执行。
对无标识
或标识不清的管材、管件严禁使用。
(2)对到货管材、管件等材料在使用前严格核对其规格、材质、型号、同时进行外观检查。
(3)管材的表面质量应达到:
内外表面应光滑,表面的局部缺陷应予清除,清除后外径或壁厚不得超出规定的负偏差值。
清洁无针孔、裂纹、夹渣、折叠、皱皮和腐蚀等缺陷。
管子的腐蚀和凹陷不超过壁厚负偏差值。
7.1.2管道附件检验
(1)对弯头、异径管、三通、法兰、盲板及紧固件等进行检查,其尺寸偏差应符合现行标准,材质应符合设计要求。
(2)法兰密封面应平整光洁,不得有毛刺及径向划痕,法兰螺纹部分完整无损伤,凹凸法兰应能自然嵌合,凸面高度不得低于凹槽的深度。
(3)石棉、橡胶、塑料等非金属材料垫片应质地柔和,无老化变质或分层现象。
表面不得有折损、皱纹等缺陷。
(4)金属垫片的加工尺寸、精度、光洁度及硬度应符合要求,表面应无裂纹、毛刺、凹凸槽径向划痕及锈斑等缺陷。
(5)包金属及缠绕式垫片不应有径向划痕、松散等缺陷。
螺栓与螺母的螺纹应完整,无划痕、毛刺等缺陷,螺栓与螺母应无松动、卡涩现象。
7.2管道坡口加工方法及要求
721管道(素材)依据技术人员已转化的预制单线图纸进行划线、切割下料后进行坡口加工。
坡口加工的管段应放置在加工台上(车间预制)进行坡口打磨;在现场进行坡口加工时,管段下面应加垫道木或其它可垫物。
不锈钢管道进行坡口打磨时应防止与碳钢接触产生渗碳并使用专用加工工具。
严禁不锈钢与碳钢材料直接接触。
7.2.2碳钢管道坡口加工可采用机械方法或半机械方法,用角向磨光机(或砂轮机)加工;管子口径大于150mm寸,可采用氧气、乙炔火焰热加工。
不锈钢管道的坡口加工可采用坡口机加工或等离子弧热加工方法。
采用热加工方法加工坡口后,必须除去坡口表面的氧化皮、熔渣及影响焊接质量的表面层,并应将管子端面的凹凸不平处打磨平整。
不锈钢切割或打磨时应使用专用砂轮片,不得与碳钢砂轮片混用。
7.2.3坡口加工的形式和尺寸要求:
坡口形式已由焊接WP舔口PQF确定,应严格执行。
7.2.4管子切割应符合下列规定:
(1)切割表面应平整、无裂纹、皱皮、毛刺、凹凸缩口、熔渣、氧化物、切屑等杂物。
(2)切割端面倾斜偏差不应大于管子外径1%且不得超过3mm
(3)管道的坡向、坡度应符合设计要求,管子对口应检查平直度,在距坡口中心200mm处测量,允许偏差为1mm/m全长允许偏差不超过10mm
(4)管段现场下料切割前应首先对管段单线图进行审核,主要审核:
图号、管线号、管段号及材质是否与设计相符。
管段分段、现场安装预留口是否合理,并应对管段预制尺寸进行必要的现场复测。
现场尺寸复测应用细钢丝或足够长的钢卷尺而不要用粉线,以提高测量准确度,测量后确定预制下料的实际尺寸。
管道支、吊架规格型号是否正确。
7.3管道组对要求
7.3.1焊口组对时,应对坡口及其内外表面20mm范围内进行清理,去除油圬、油漆、
铁锈、毛刺等杂物。
732对于不锈钢管组对用的台架、支承架等,应用衬垫材料进行隔离。
733除设计规定需进行冷拉伸或冷压缩的管道外,管道不得进行强行组对。
组对后,应
保持管子的平直。
7.3.4对于焊接时易产生变形的簿壁管,组对时,应使用专用夹具进行固定。
7.3.5厚壁大口径管道组对时,如采用定位板进行定位,定位板的材质应和母材相同或相似。
取下定位板时,应用砂轮机磨削,且防止损伤母材。
7.3.6焊口组对时,应做到内壁平齐,内壁错边量不宜超过壁厚的10%,且不大于2mm。
7.3.7管子对口后应垫置牢固,避免焊接过程中产生变形,管道连接时不得强力组对。
7.4管道安装要求
7.4.1管子、管件及阀门等已按设计要求核对无误并具有产品合格证和质保证书,内部已经
清理干净,不存杂物。
7.4.2管道的坡向、坡度应符合设计要求。
法兰连接时应保持平行,其偏差不大于法兰外径的1.5/1000,且不大于2mm绝对不得用强紧螺栓的方法消除歪斜。
法兰连接面应保持同轴,其螺栓孔中心偏差一般不超过孔径的5%并保证螺栓能自由穿入,
法兰连接应使用同一规格、同一材质的螺栓。
安装方向应一致,紧固螺栓应对称、均匀、松紧适度,紧固后外露长度不大于1-2螺距。
7.4.3管道的坡度,可用支座下的金属垫板(垫板要焊接牢固)调整,吊架用吊杆螺栓调整。
7.4.4合金钢管道(包括不锈钢管道)不应焊接临时支撑物,如有必要时应符合焊接的有关规定。
7.4.5与设备连接的管道,安装前必须将管道内部清理干净,其固定焊口一般离设备300mm
7.4.6当设计或设备制造厂无规定时,对不容许承受附加外力的传动设备,在设备法兰与管道连接前,应在自由状态下进行组对、焊接,法兰的平行度和同轴度偏差应在规范允许的偏差之内。
7.4.7管道安装时,应同时进行支、吊架的固定和调整工作。
支、吊架位置应正确,安装应牢固,管子和支撑面接触良好。
7.4.8无热位移管道的管道吊架,其吊杆应垂直安装。
有热位移管道的管道吊架,其吊点
应在位移相反方向,按位移的1/2偏位安装。
749固定支架和限位支架应严格按设计要求安装,固定支架应在补偿装置预拉伸或预压缩前固定。
7.4.10弹簧支、吊架的弹簧安装高度,应按设计文件规定进行调整。
弹簧应调整至冷态值,并做好记录。
弹簧支架的限位板,应保留到试车前拆除。
7.4.11管道预制件安装前应完成的有关工序,如探伤、热处理、清洗等已经进行完毕,并符合要求。
7.4.12管道安装的允许偏差应符合--附录1规定。
7.4.13管道焊接:
按