90吨LF炉工程设计说明书.docx
《90吨LF炉工程设计说明书.docx》由会员分享,可在线阅读,更多相关《90吨LF炉工程设计说明书.docx(53页珍藏版)》请在冰豆网上搜索。
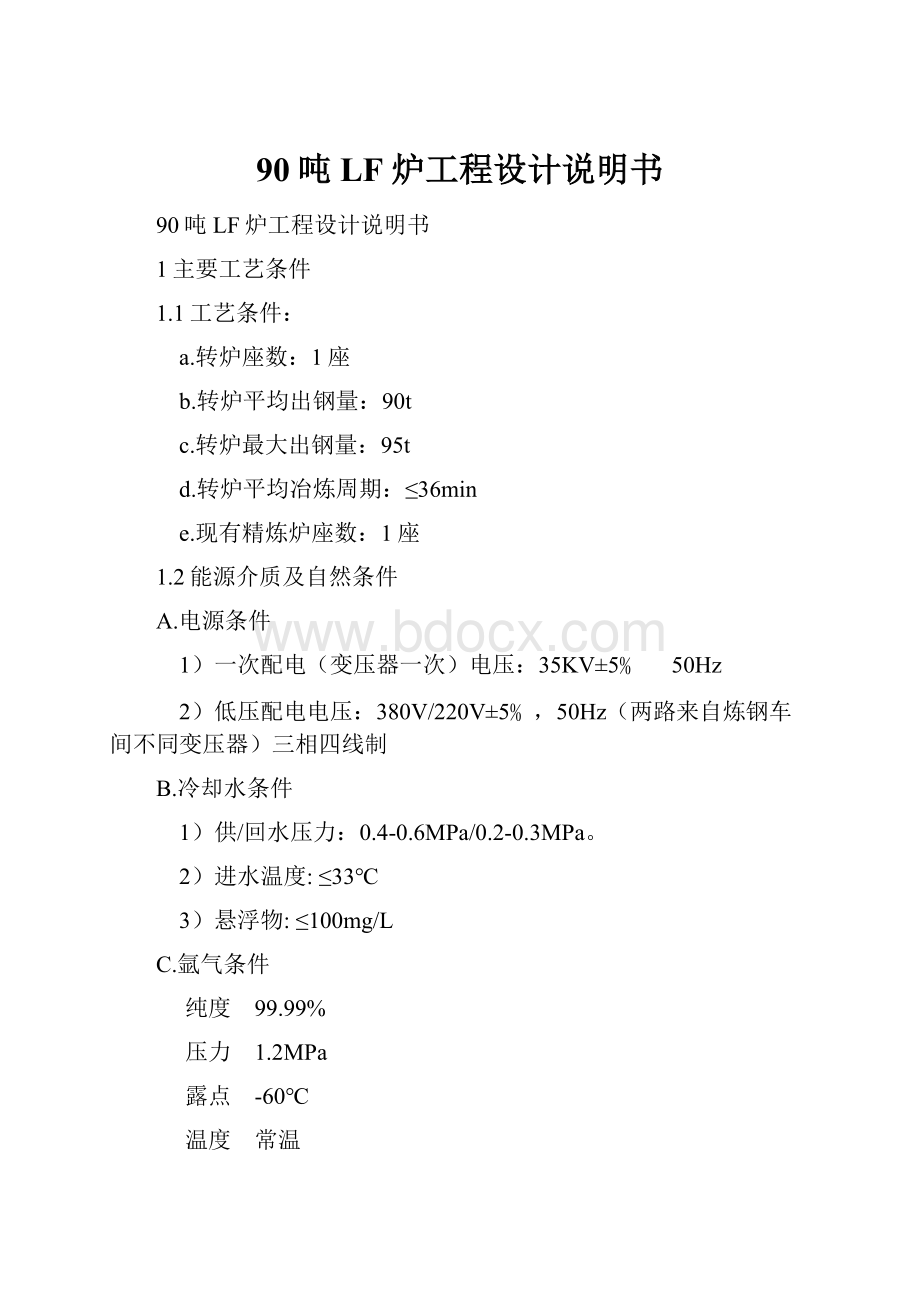
90吨LF炉工程设计说明书
90吨LF炉工程设计说明书
1主要工艺条件
1.1工艺条件:
a.转炉座数:
1座
b.转炉平均出钢量:
90t
c.转炉最大出钢量:
95t
d.转炉平均冶炼周期:
≤36min
e.现有精炼炉座数:
1座
1.2能源介质及自然条件
A.电源条件
1)一次配电(变压器一次)电压:
35KV±5﹪ 50Hz
2)低压配电电压:
380V/220V±5﹪,50Hz(两路来自炼钢车间不同变压器)三相四线制
B.冷却水条件
1)供/回水压力:
0.4-0.6MPa/0.2-0.3MPa。
2)进水温度:
≤33℃
3)悬浮物:
≤100mg/L
C.氩气条件
纯度 99.99%
压力 1.2MPa
露点 -60℃
温度 常温
D.压缩空气条件
压力 0.3—0.6MPa
含油 ≤20mg/m3
露点 10℃
温度 常温
1.3LF炉的产品大纲及产量
1)90t-LF精炼炉拟精炼的产品
拟精炼品种:
焊条钢 H08 20%
优质碳素钢45-72A、82B 30%
铆螺钢ML35 25%
弹簧钢60Si2Mn 55SiMnVB 5%
焊丝钢ER50-6E 20%
2)精炼炉生产能力计算
(1)
平均每炉处理钢水量:
90t
(2)
平均每炉处理周期:
36min
(3)
LF炉座数:
1座
(4)
精炼炉年作业率:
85%
(5)
转炉、精炼、连铸配合率:
90%
经计算:
Q1=365×24×60/36×90×85%×90%=1005000t/y
故单台精炼炉年生产能力为1005000t。
1.4LF炉生产周期
LF炉采用双钢包车三工位工作时下表中括号内的时间不累积计算。
序号
项 目
工序时间(min)
工序累积时间(min)
1
钢包吊至包车上
(~2.0)
0.0
2
连接吹氩管、试气
1.0
1.0
3
包车开至加热工位
1.5
2.5
4
炉盖和电极下落到位
1.0
3.5
5
测温取样确定加热制度及成分微调
2.0
5.5
6
加渣料及合金料
(2.5)
5.5
7
送电加热精炼(6.0+5.0+1.0+11.5∽16.0)
23.5—28.0
29.0-33.5
8
测温取样
1.0
30.0-34.5
9
炉盖、电极升起
1.5
31.5-36.0
10
包车开出加热工位
(1.5)
31.5-36.0
11
喂丝
(2.0)
31.5-36.0
12
加保温剂
(1.0)
31.5-36.0
13
软吹氩及气洗
(5.0—10.0)
31.5-36.0
14
断开吹氩管及吊出钢包
(2.0)
31.5-36.0
15
合 计
31.5-36.0
1.5精炼炉工艺布置
重钢公司拟新建的90t-LF钢包精炼炉布置在(C)--(D)跨和(D)--(E)跨16#--22#柱之间。
该精炼炉采用单车双工位纵轨布置.散装料系统、变压器室、主控室位于二层平台;液压室、氩气室位于一层。
高压配电室(35KV)及谐波补偿装置室位于二层平台。
2备组成及功能说明
2.1备主要功能
LF钢包精炼炉能取代初炼炉进行还原操作,可对钢液实施升温、脱氧、脱硫、合金微调,采用吹氩搅拌,使钢液成份、温度均匀,质量(纯净度)提高,具体的功能为:
----电弧加热提温
----钢水成份微调
----脱硫、脱氧、去除夹杂
----均匀钢水成份和温度
----改变夹杂物形态
----作为转炉、连铸机之间的缓冲设备,保证转炉、连铸匹配生产,实现多炉连浇。
2.2设备的主要技术参数
序号
名 称
单位
参数
备注
1
钢包
钢包额定容量
t
95
自由空间高度
mm
600
90t钢水
钢包耳轴中心距
mm
4250
2
钢包车
行走速度
m/min
2-20
定位精度
mm
±10
最大载重量
t
180
驱动方式
机械式
交流变频调速
3
加热装置
电极直径
mm
φ400
超高功率石墨电极
电极分布园直径
mm
φ710
电极最大行程
mm
2700
初定
电极升降速度
m/min
升5/降4
MAX.
4
钢水升温速率
℃/min
≥4
强化≥5℃/min
5
电炉变压器
额定容量
KVA
18000
一次电压
KV
35
二次电压
V
335-295-235
11级(前5级恒功率,后6级恒电流)
二次额定电流
KA
35.23
调压方式
ABB有载调压
冷却方式
强迫油循环水冷
出线方式
内封侧出线
6
短网阻抗
阻抗
mΩ
≤2.6
三相不平衡系数
%
≤4
7
液压系统
工作压力
Mpa
12
工作介质
水-乙二醇
电极升降调节
电液-比例
油箱材质
不锈钢
耐腐蚀
8
氩气系统
供气压力
Mpa
1.2
可调压力及流量,一个钢包两个底吹氩点
工作压力
Mpa
0.5-1.0
耗量
NL/min
450
9
冷却水系统
工作压力
Mpa
0.4-0.6
回水压力
Mpa
0.2-0.3
耗量
m3/h
~320
进/回水温度
℃
≤32/55
10
加热炉盖
提升高度
mm
650
有效高度400mm
提升方法
г型架一液压缸
裙边高度
mm
~300
11
合金加料装置
料仓数量
8
料仓容积
m3
6×6m3+2×10m3
给料方式
震动给料
VVVF
受料斗容积
m3
1.5
2.3钢包车及拖缆
钢包车本体由四个钢板组焊成的矩形梁构成框形车架,上面设有两个耳轴支座用于支撑钢包,下部装有主、从两组车轮(共四个车轮),车轮直径约ф900。
钢包车用电机驱动,约30KW电机直联双出轴齿轮减速机后通过联轴器分别与两个主动轮相连接,结构简单、可靠。
电动机和减速器通过安装座直接固定于车架横梁上,刚性好,减速机齿轮面采用中硬齿轮面。
钢包车运行调速采用变频调速。
为了保证钢包车的平稳运行,在车的前后端对应于每个车轮装有四个轨道清理装置,随着钢包车的运行清理掉钢轨上可能落上的杂物。
钢包车动力电源、钢包底吹氩搅拌的氩气管道及电缆均由拖缆提供。
其结构是在钢包车的外侧上方(±0.00以上)固定一根工字钢轨(用户自备)。
电缆及氩气软管通过若干个吊架悬挂于工字钢轨上,吊架与工字钢轨之间设有滚轮,从而保证了钢包车运行过程中拖缆装置收放自如。
设防护屏的目的是为了很有效地保护电缆免受高温钢包的热幅射,提高电缆的使用寿命。
钢包车的定位采用接近开关(远离加热工位)定位,使得钢包车可平稳启动和制动,无惯性冲击。
除钢包车控制系统设有制动单元外,钢包车本身也设软制动单元,以便于在事故状态下将钢包车拖出。
钢包车设吹氩操作平台。
钢包车坐包标高设计考虑予留VD。
技术规格:
最大载重量:
180t
运行速度:
2∽20m/min(无级可调)
驱动方式:
机械式、变频调速(VVVF)
2.4加热基架及导向轮装置
加热基架是精炼炉的基础构件,其分为上、下两层,分别安装电极升降立柱、炉盖升降立柱及其对应的导向轮装置。
导向滚轮组用于电极升降机构及炉盖升降机构定位导向,共由二组滚轮组成,对应电极升降立柱和炉盖升降立柱上下各设一组,分别安装在独立基架的上下层。
导向滚轮的设计考虑到安装、使用、维护及立柱升降的平稳和电磁场的影响等因素,设计时考虑其有较大的调整行程,并要求其调整方便、可靠及足够大的轮距,以确保升降立柱的运行平稳,达到稳定电弧燃烧。
导向滚轮与电极升降立柱导轨之间的间隙调整是通过简单、可靠、实用的方法调整来实现,以保证立柱与导向轮的接触良好。
技术参数:
主导向滚轮组直径 Φ300mm
辅导向滚轮组直径 Φ220mm
导向滚轮组间距 ≥2000mm
导向滚轮组数 2套8组
2.5 “密封”式水冷炉盖装置
水冷炉盖为密排管式结构,水冷炉盖用无缝锅炉钢管和特制的等直径弯头组焊而成,以保证水冷为均流无死点,提高水冷效果。
在结构上炉盖本体侧壁体成柱形,顶部是锥形面,下大上小以保证刚性,顶中心部分是一倒锥形水冷环,用以承放耐火材料中心盖,中心盖上开有与三相电极相对应的三个电极孔(耐火材料中心盖用户自备)。
在炉盖的内侧设有“V”字型挂渣钉,以便于耐材打结和冶炼过程中自动挂渣。
在炉盖本体上除三个电极孔外,根据工艺要求还设有合金加料孔以及相应的密封盖,根据冶炼要求打开相应的孔盖进行操作(汽缸带动)。
孔盖的作用是防止高温烟气溢出,同时在炉盖的侧壁(侧部开口-水冷倾斜向上)设有一人工观察工作孔(汽缸带动),在冶炼过程中,根据需要可打开孔盖进行观察和其它工艺操作,同时在炉盖的顶部设有一检修平台和护栏,以便于电极横臂检修、电极的更换及接长等。
炉盖下“密封”装置采用独特的凹形设计,既保证了良好的炉内还原气氛,同时又确保了良好的集烟效果。
炉盖在使用时,内部须打结有50~80mm的耐材(用户自备并打结)以提高炉盖的使用寿命和热效率。
技术参数:
炉盖直径:
∽Ф3050mm(初定)
炉盖高度:
∽1180mm(初定)
下“密封”罩高度:
300mm(初定)
炉盖寿命:
≥3000炉次
2.6 炉盖提升机构
炉盖提升机构由炉盖升降油缸及Γ型架组成.油缸安装在Г型架立柱下端,并远离高温区及强磁场,炉盖的升降由升降油缸来实现。
Γ型架既承担了炉盖升降负荷,同时又作为水冷炉盖的冷却水进回水路,使冷却水水路得到极大简化。
在使用过程中,确保无事故点和热停炉及工艺的正常进行。
Γ型架与水冷炉盖的联接处,即Γ型架端部采用独特的“牛头”设计,“牛头”即可以上下摆动,又可以左右调整,使得炉盖的安装、维修变得异常方便实用。
油缸的主要密封采用原装进口件。
技术参数:
炉盖提升高度:
650mm
炉盖提升力:
≥20×104N
炉盖升降同步精度:
≤±15mm
2.7电极升降机构
为确保导电横臂升降平稳和电弧燃烧稳定,电极升降立柱结构设计除考虑电极横臂及电缆和电极的负荷外,同时更应考虑电磁力的作用。
故电极升降立柱必须具备足够的强度和刚性(较1#精炼炉加强),电极升降立柱是用钢板焊接成的异形构件,内腔装设立柱升降油缸,立柱外表与导向滚轮接触面均经精加工和热处理。
立柱上平面与横臂联接处二者之间设有环形绝缘,确保无爬弧现象。
电极横臂与立柱联接处设有一水冷托架,托架一方面可满足导电横臂在立柱上的前后及左右方向调整,同时也保证维护及检修的方便性。
所配铜——钢复合导电横臂采用最优的结构设计及空间布置即保证了结构的强度和刚性,更主要的考虑二次电流的供电特性,从而减少等效电抗值,降低三相不平衡度,在保证相间不短路的条件下,极大的缩小了电极分布圆直径。
电极夹放缸的结构采用双活塞设计,另外,将电极夹放缸置于横臂内部,一方面避开高温区,另一方面避开强磁场区,电极夹放缸不设水冷。
另外,电极夹放机构的电极夹紧力在确定时留有很大的裕度(夹紧力可调),以确保电极与锻造精加工的紫铜电极夹头接触良好,延长易损件的使用寿命,降低生产运行成本。
立柱升降油缸的主要密封采用原装进口件
技术参数:
电极直径:
Ф400mm,超高功率石墨电极(用户自备)
电极分布园直径:
Ф710mm
夹紧力:
≥15.1~19.7×104N(可调)
电极行程:
2700mm(初定)
电极升降速度:
4.5/3(5/4.5)m/min(自动/手动)
2.8 二次短网系统
二次短网系统是指变压器二次侧向钢包炉输送电能的大电流线路,由水冷挠性补偿器、导电铜管、大截面水冷电缆等组成。
由于钢包炉在冶炼时,所需功率大,二次电流通常都在数万安培之上,所以能耗、阻抗、三相不平衡系数及功率因数在短网结构设计时显得尤为重要。
技术参数:
阻抗:
Z≤2.6 mΩ
三相不平衡系数:
≤4.0%
功率因数 cosφ=0.83
2.9精炼炉变压器
钢包精炼炉变压器用于钢液加热提温,既要保证较高的升温速度,又要确保钢包包衬使用寿命,钢包精炼炉必需采用低电压大电流操作。
变压器由变压器本体、油枕、开关操作箱、小车、高压套管、释压器、ABB进口有载调压开关、油水冷却器、低压导电排等组成。
性能值:
阻抗电压8%,空载电流1%。
变压器过载能力:
+20%,2h
二次绕组:
采用先进的线圈绕组结构,使得附加损耗小,抗短路能力强。
器身压紧:
所有线圈整体组装真空气相干燥处理,线圈压紧采用专用特制弹簧油缸压紧,使其在运行中始终处于压紧状态。
变压器铁芯材料采用日本产品(型号Z10-0.3)。
变压器和有载开关分别配有重瓦斯、轻瓦斯、释压器等保护功能。
储油箱内衬橡皮囊,使油与空气隔绝以保护变压器油。
变压器带有远传测温装置输出4-20mA信号,在主控室通过数显仪可观察油温。
变压器生产厂家确定前须得到甲方的认可。
技术参数:
额定容量:
18MVA,+20%,2h
一次电压:
35KV,50HZ
二次电压:
335—295—235,共设十一档,前五档恒功率,后六档恒电流
二次额定电流:
35.23KA
调压方式:
三相同步有载电动(原装进口ABB开关)
出线方式:
内封侧出线
冷却方式:
板式强油循环水冷(OFWF)外附变压器器身。
2.10双线喂丝机
喂线技术的核心是将比较轻、易氧化、易挥发的合金元素制成包芯线或实心线快速输入钢液,在钢液深处熔化溶解,从而达到脱氧、脱硫、改变夹杂物形态,实现成份微调等冶金目的。
技术参数:
喂线规格 Φ8~Φ13
喂线速度 1~6m/s
2.11水冷系统
水冷系统分二个部分:
一部分其主要冷却部位有水冷电缆、导电横臂、电极夹头、短网等,第二部分主要为:
水冷炉盖本体及炉盖下“密封”装置等。
水冷系统每路水都设有压力、温度检测元件,当进水压力过低,回水温度过高时,都有声光指示和报警。
炉盖总回水装有电磁流量开关,用于检测及漏水报警。
水冷胶管采用活联结;水冷分配器前增设过滤网及检修放水阀。
技术规格:
进水压力:
0.4-0.6Mpa, 回水压力:
0.2-0.3Mpa
进/回水温度:
≤33/55℃, 耗量:
320m3/h
(变压器用水量约为80m3/h,设备用水量约为240m3/h)
水质要求符合标准《GB10067.1-88》对水质的一般要求
2.12合金加料系统
自动加料系统主要由储料仓装置、称量给料装置、皮带送料及密封装置、钟式料罐、储料仓支撑架和检修平台装置等组成。
储料仓装置主要包括料仓、高低料位检测装置、手动插板阀及振动给料器等,料仓主要由型钢和钢板焊接而成,呈倒锥形布置,上大下小。
侧面分别设有低料位检测装置,主要用于料位检测和报警。
在料仓的下端设有一个人工手动插板阀,以备检修振动给料器时关闭料仓。
料仓下端出口处设有一个振动给料器,可将料仓的物料快速准确地送到称量料斗中。
称量给料装置主要包括称量料仓、称量传感器和振动给料器等。
称量料仓是由钢板和型钢焊接而成,称量装置主要依据工艺要求,准确计量拟加炉内的物料。
振动给料器则将计量准确的物料送到皮带送料装置上。
物料通过皮带送料装置,经过溜管进入炉内。
皮带送料及密封装置是将称量准确的物料在无污染的条件下快速准确地送至炉内,以满足正常生产之需求。
为了避免皮带在送料过程中皮带跑偏,故在设计时,皮带送料的支撑辊制作成槽形,且在两侧设有皮带跑偏的机械限位装置。
同时为避免皮带打滑,在皮带支撑主动辊一侧设有皮带张紧轮,以保证皮带与主动辊之间有足够的摩擦力。
钟式料罐是由钢板制作而成,上大下小。
它是将各种物料通过起吊设备(行车)运到料仓的容器。
储料仓支撑架和检修平台装置是由钢板和型钢组焊而成,是储料仓装置及检修的基础构件,故要求其有较好的强度和稳定性。
振动给料器采用变频控制调速,其控制有两种控制方式,一种由PLC控制,实现生产自动化,另外一种在主控室内计算机操作站手动控制,加料系统工作时,称重传感器的输出为PLC可识别的4-20mmA信号,并可在主控室实时显示。
加料粒度:
≤80mm
加料系统工作时,整个系统为全封闭式
技术参数:
储料仓 6m3×6+10m3×2
钟式料罐 2m3
加料能力 45t/h
加料时间 <2.5min
称量精度 ≤0.5%
2.13电极存放及联接装置
电极连接可在炉子上完成,也可单独在平台的电极联接储存装置上完成,该过程均由人工来实现。
2.14气动系统
气动系统主要用于各工作气缸动作的完成与控制。
本系统主要由阀架、气动三联件及电磁阀等组成,其用气点为合金加料插板阀及炉门启闭等。
主要技术参数:
压力:
0.4-0.6Mpa
耗量:
1.2Nm3/min
2.15氩气系统
本系统按氩气流量的不同级别按指令自动控制,也可手动调节,系统除了设定工作压力(依据实际工况而定)外,同时又设有测漏及高压旁吹等级别,可以实现自动调节氩气流量,并记录氩气耗量的瞬时值及累积值,也可由计算机控制。
系统出现异常情况时有事故声光报警,过压、欠压也有报警。
精炼过程中氩气流量大小、变化斜率等可按时间设段,以满足不同的工艺要求。
调节与测量功能由PLC自动完成,组成完整的自控系统,也可以转为手动控制。
整套系统装在一个柜体内。
功能:
1)压力调节:
0.20~1.0Mpa(视工艺要求确定)
2)流量测量、调节漏气检查,高压旁吹
3)事故自动诊断和报警
技术参数:
供气压力:
1.2MPa
工作压力:
0.3~1.0MPa
氩气流量:
450Nl/min(max)×2、40Nl/min(min)
氩气纯度:
99.99%
2.16 液压系统
本台90t_LF钢包精炼炉液压系统,由泵站、阀站、蓄能器等部分组成,供电极升降、水冷炉盖升降、电极夹放等液压装置所用。
柱塞泵选用恒压变量柱塞泵(力士乐),共二套,一用一备。
液压介质为阻燃水-乙二醇。
为使系统在高效、节能状态下运行,以及在设备失电状态下能自动将三相电极和炉盖提升,使钢包车具有移动条件,系统配有蓄能装置。
三相电极升降调节采用电液比例阀(力士乐),其它控制回路采用进口(力士乐)滑阀,使系统达到无泄漏运行。
考虑到当地的气温条件,液压装置配备有冷却装置。
液压站设在变压器室下面。
考虑到工作介质有较强的腐蚀性,液压箱、管道采用不锈钢材质。
液压泵装置
·液压泵装置是由二台排量140ML的恒压变量泵及电机等组成,控制形式为一用一备。
·恒压变量泵的驱动功率约为37KW,可满足液压系统的工作压力要求。
·每台泵装置设有压力保护功能和压力油过滤器,以保证向液压系统输入高精度工作介质。
·液压泵装置设有单向阀、高压球芯截止阀等液压件。
测压点,测压软管等液压附件,确保正确使用维护。
·液压泵装置设有压力继电器,用于采集系统压力。
油箱总成
·依据精炼炉炉况、工作缸数量、缸径和行程,可计算出需约2.8m3的不锈钢油箱。
·油箱设有液位计和液位发讯器,用于对低液位、超低液位、高液位、超高液位进行报警和发讯。
同时还可参与系统PLC控制。
·油箱设有两个温度控制器,用于对低温度、超低温度、高温度、超高温度、进行报警和发讯。
同时也可参与系统PLC控制。
·油箱配有循环过滤冷却系统,30分钟可将油箱的油液按照控制要求过滤[7μ]冷却一次,以满足液压系统对油液的要求。
备用油源蓄能器装置
此蓄能器装置主要功能为满足事故状态下钢包车开出并将电极及炉盖提升,同时也起到了平衡液压压力作用。
此蓄能器装置配有8个100L皮囊蓄能器并分为两组,每台蓄能器配有压力保护和切断卸荷功能,可向系统输入(210--240)L工作介质。
精炼炉阀站
·电极升降控制系统。
电极升降采用了3台电液比例阀(力士乐),分别对三相电极升降进行自动控制。
·炉盖升降系统采用DN10三位四通电液阀(力士乐)并备有双单向节流阀。
炉盖升降控制系统还具有液压锁功能。
·电极松开控制系统采用DN6二位四能电磁阀(力士乐)控制,结构简单动作可靠。
主要技术参数:
系统工作压力:
12MPa
主泵电机容量:
2×37KW(一用一备)
泵工作压力:
16MPa
泵流量:
140L/min
蓄能器形式:
皮囊式
额定压力:
21MPa
工作压力:
12MPa
蓄能器容积:
800L
系统油箱容积:
2800L
系统油箱材质:
不锈钢
系统工作介质:
水一乙二醇
2.17大烟罩除尘装置
大烟罩除尘装置共由活动烟罩、固定烟罩、驱动装置、滑线装置及侧封板装置、电动风量调节阀和限位装置等组成。
活动烟罩位于精炼炉设备正上方,其是由钢板焊制而成,内侧设有耐火隔热层,两侧各设两组车轮,其中一组为主动轮,且车轮轨面标高有一定的高度差,以方便烟罩的拆装。
固定烟罩位于设备靠近变压器侧,其结构同活动烟罩,且位于活动烟罩的下方,为了满足电极升降行程及强磁场工况条件,固定烟罩内部离横臂最高点需保持一个合理的空间高度。
为了方便工艺操作和减少除尘风量,故在除尘烟罩的四周均设有侧封板,侧封板由型钢和钢板组焊而成,内侧辅设有隔热耐火层。
为方便工艺操作,在操作平台一侧的侧封板上设有一工艺操作孔门。
该孔门既可以实现相关的工艺操作,也可以方便炉前观察。
驱动装置安装在活动烟罩的两侧,共计两套。
每套各设一组主动轮,以实现活动烟罩的运动,满足工艺操作及电极更换。
滑线装置为驱动装置的提供动力电源。
技术参数:
烟尘捕捉率 ≥98%
活动烟罩运行速度 ∽12m/min
2.18 高压系统
设备名称 数量 安装位置
进线PT柜 1面 高压室
真空开关柜 1面 高压室
保护柜 1面 高压室
整流电源柜 1面 高压室
高压系统主要用于90tLF精炼炉变压器一次侧电源合闸和分断。
进线PT柜包括隔离开关,主要用来隔离电源,便于安全检修。
另外进线PT柜还包括电压互感器、电流表、电压表、三相有功功率表、无功功率表、有功电度表及无功电度表等测量仪表。
真空开关柜包括断路器手车、电流互感器,断路器采用CD10-Ⅱ型直流电磁操动机构,可以方便地进行远距离操作,完成变压器电源的接通和分断;真空断路器合闸回路,采用防跳装置,克服了真空触头反复合、分导致的电弧重燃,有效的延长了触头寿命。
滤波系统安装有氧化锌避雷器及R-L-C吸收装置,能有效防止操作过电压和浪涌过电压对变压器和电压互感器绝缘可能造成的危害。
整流电源柜内配备整流变压器、三相桥式整流模块、滤波装置等,为高压控制回路、