IE相关英文缩写解释.docx
《IE相关英文缩写解释.docx》由会员分享,可在线阅读,更多相关《IE相关英文缩写解释.docx(27页珍藏版)》请在冰豆网上搜索。
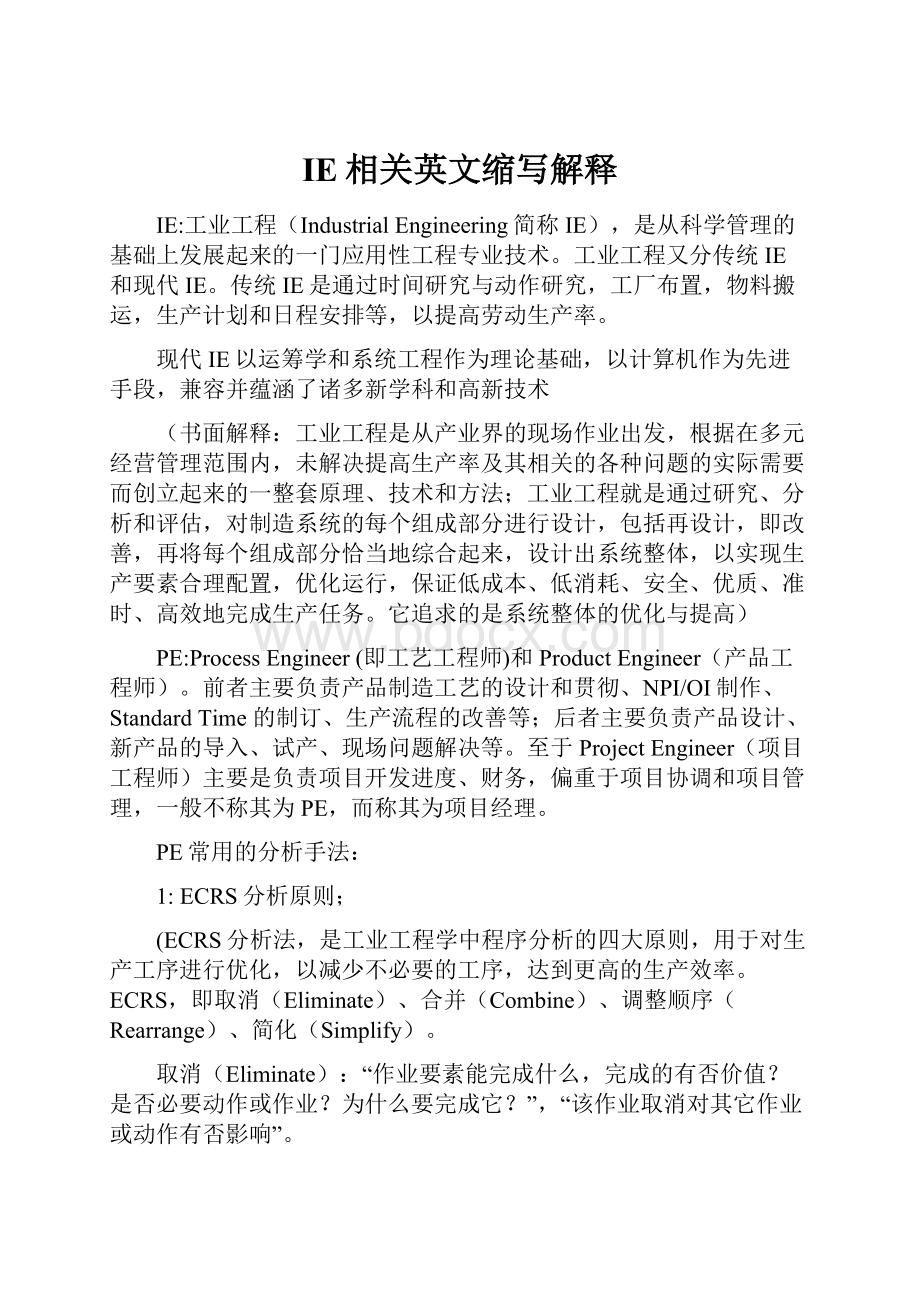
IE相关英文缩写解释
IE:
工业工程(IndustrialEngineering简称IE),是从科学管理的基础上发展起来的一门应用性工程专业技术。
工业工程又分传统IE和现代IE。
传统IE是通过时间研究与动作研究,工厂布置,物料搬运,生产计划和日程安排等,以提高劳动生产率。
现代IE以运筹学和系统工程作为理论基础,以计算机作为先进手段,兼容并蕴涵了诸多新学科和高新技术
(书面解释:
工业工程是从产业界的现场作业出发,根据在多元经营管理范围内,未解决提高生产率及其相关的各种问题的实际需要而创立起来的一整套原理、技术和方法;工业工程就是通过研究、分析和评估,对制造系统的每个组成部分进行设计,包括再设计,即改善,再将每个组成部分恰当地综合起来,设计出系统整体,以实现生产要素合理配置,优化运行,保证低成本、低消耗、安全、优质、准时、高效地完成生产任务。
它追求的是系统整体的优化与提高)
PE:
ProcessEngineer(即工艺工程师)和ProductEngineer(产品工程师)。
前者主要负责产品制造工艺的设计和贯彻、NPI/OI制作、StandardTime的制订、生产流程的改善等;后者主要负责产品设计、新产品的导入、试产、现场问题解决等。
至于ProjectEngineer(项目工程师)主要是负责项目开发进度、财务,偏重于项目协调和项目管理,一般不称其为PE,而称其为项目经理。
PE常用的分析手法:
1:
ECRS分析原则;
(ECRS分析法,是工业工程学中程序分析的四大原则,用于对生产工序进行优化,以减少不必要的工序,达到更高的生产效率。
ECRS,即取消(Eliminate)、合并(Combine)、调整顺序(Rearrange)、简化(Simplify)。
取消(Eliminate):
“作业要素能完成什么,完成的有否价值?
是否必要动作或作业?
为什么要完成它?
”,“该作业取消对其它作业或动作有否影响”。
合并(Combine):
如果工作或动作不能取消,则考虑能否可与其他工作合并,或部分动作或工作合并到其它可合并的动作或作业中。
重排(Rearrange):
对工作的顺序进行重新排列。
简化(Simplify):
指工作内容和步骤的简化,亦指动作的简化,能量的节省。
在进行5W1H分析的基础上,可以寻找工序流程的改善方向,构思新的工作方法,以取代现行的工作方法。
运用ECRS四原则,即取消、合并、重组和简化的原则,可以帮助人们找到更好的效能和更佳的工序方法。
)
2:
5W2H改善方法;
(5W2H分析法又叫七问分析法,是二战中美国陆军兵器修理部首创。
简单、方便,易于理解、使用,富有启发意义,广泛用于企业管理和技术活动,对于决策和执行性的活动措施也非常有帮助,也有助于弥补考虑问题的疏漏。
发明者用五个以W开头的英语单词和两个以H开头的英语单词进行设问,发现解决问题的线索,寻找发明5W2H分析法思路,进行设计构思,从而搞出新的发明项目,这就叫做5W2H法。
(1)WHAT——是什么?
目的是什么?
做什么工作?
(2)WHY——为什么要做?
可不可以不做?
有没有替代方案?
(3)WHO——谁?
由谁来做?
(4)WHEN——何时?
什么时间做?
什么时机最适宜?
(5)WHERE——何处?
在哪里做?
(6)HOW——怎么做?
如何提高效率?
如何实施?
方法是什么?
(7)HOWMUCH——多少?
做到什么程度?
数量如何?
质量水平如何?
费用产出如何?
)
3:
WHY-WHY分析方法;
•(所谓why-why分析,是将发现的现象使用系统化的思考模式,由应有状态或4M(人、机械、材料、方法)的关系筛选出引起现象的因素,再以筛选出的因素为基本,一面仔细观察、调查现场、现物,一面追求真正的原因,并且研究再发防止对策。
•简言之,对发现的现象连续进行多次思考“为什么(why)”的动作,并验证要因是否成立,然后对真因作有效对策的方法称为“WHY-WHY分析”。
)
4:
五大现象分析
(作业、搬运、检验、贮存、等待
A.作业指原材料、零件、半成品依照生产的目的受到物理、化学、机械或被人为变更状态。
记号:
用大圆形作为加工记号。
如碰上加工又要做检查时,则加工的大圆记号内加上检查的方型记号例:
……指加工的第3工序.加工中同时检查(外侧为主要工序).
B.搬运指材料、零件、半成品、成品从某一位置被子移动至另一位置。
记号:
约为加工的大圆记号的1/2大小的小圆,内侧可注明搬运的机器或工具。
……指用卡车搬运。
有时因与大圆的记号不易区别,也有使用箭头记号(或)
C.检查指材料、零件、半成品或成品的品质特性或数量用方法加以检测,并将其结果与基准比较作为判别合格或不合格。
记号:
……品质检查……数量检查……品质与数量的检查
D.停滞指材料、零件、半成品或成品在某一位置滞留或存储。
)
5:
8D
(8D又称团队导向问题解决方法、8D问题求解法(8DProblemSolving)是福特公司处理问题的一种方法,亦适用于制程能力指数低於其应有值时有关问题的解决,它提供了一套符合逻辑的解决问题的方法,同时对於统计制程管制与实际的品质提升架起了一座桥梁。
8D是解决问题的8条基本准则或称8个工作步骤,但在实际应用中却有9个步骤:
D0:
征兆紧急反应措施
D1:
小组成立
D2:
问题说明
D3:
实施并验证临时措施
D4:
确定并验证根本原因
D5:
选择和验证永久纠正措施
D6:
实施永久纠正措施
D7:
预防再发生
D8:
小组祝贺
D0:
征兆紧急反应措施
目的:
主要是为了看此类问题是否需要用8D来解决,如果问题太小,或是不适合用8D来解决的问题,例如价格,经费等等,这一步是针对问题发生时候的紧急反应。
关键要点:
判断问题的类型、大小、范畴等等。
与D3不同,D0是针对问题发生的反应,而D3是针对产品或服务问题本身的暂时应对措施。
D1:
小组成立
目的:
成立一个小组,小组成员具备工艺/产品的知识,有配给的时间并授予了权限,同时应具有所要求的能解决问题和实施纠正措施的技术素质。
小组必须有一个指导和小组长。
关键要点:
成员资格,具备工艺、产品的知识;目标;分工;程序;小组建设
D2:
问题说明
目的:
用量化的术语详细说明与该问题有关的内/外部顾客抱怨,如什么、地点、时间、程度、频率等。
“什么东西出了什么问题”
方法:
质量风险评定,FMEA分析,5W3H
关键要点:
收集和组织所有有关数据以说明问题;问题说明是所描述问题的特别有用的数据的总结;审核现有数据,识别问题、确定范围;细分问题,将复杂问题细分为单个问题;问题定义,找到和顾客所确认问题一致的说明,“什么东西出了什么问题”,而原因又未知风险等级。
D3:
实施并验证临时措施
目的:
保证在永久纠正措施实施前,将问题与内外部顾客隔离。
(原为唯一可选步骤,但发展至今都需采用)
方法:
FMEA、DOE、PPM
关键要点:
评价紧急响应措施;找出和选择最佳“临时抑制措施”;决策;实施,并作好记录;验证(DOE、PPM分析、控制图等)
D4:
确定并验证根本原因
目的:
用统计工具列出可以用来解释问题起因的所有潜在原因,将问题说明中提到的造成偏差的一系列事件或环境或原因相互隔离测试并确定产生问题的根本原因。
方法:
FMEA、PPM、DOE、控制图、5why法
关键要点:
评估可能原因列表中的每一个原因;原因可否使问题排除;验证;控制计划
D5:
选择并验证永久纠正措施
目的:
在生产前测试方案,并对方案进行评审以确定所选的校正措施能够解决客户问题,同时对其它过程不会有不良影响。
方法:
FMEA
关键要点:
重新审视小组成员资格;决策,选择最佳措施;重新评估临时措施,如必要重新选择;验证;管理层承诺执行永久纠正措施;控制计划
D6:
实施永久纠正措施
目的:
制定一个实施永久措施的计划,确定过程控制方法并纳入文件,以确保根本原因的消除。
在生产中应用该措施时应监督其长期效果。
方法:
防错、统计控制
关键要点:
重新审视小组成员;执行永久纠正措施,废除临时措施;利用故障的可测量性确认故障已经排除;控制计划、工艺文件修改
D7:
预防再发生
目的:
修改现有的管理系统、操作系统、工作惯例、设计与规程以防止这一问题与所有类似问题重复发生。
关键要点:
选择预防措施;验证有效性;决策;组织、人员、设备、环境、材料、文件重新确定
D8:
小组祝贺
目的:
承认小组的集体努力,对小组工作进行总结并祝贺。
关键要点:
有选择的保留重要文档;流览小组工作,将心得形成文件;了解小组对解决问题的集体力量,及对解决问题作出的贡献;必要的物质、精神奖励。
)
ME:
可称设备工程师,但比设备工程师的工作范围更广泛。
工欲善其事,必先利其器。
在构成生产的五大要素(人、机、料、法、环,即4M1E)中,机器是第二大要素,这就是ME的事务,包括:
机器、设备、仪器、工具、模具、治具等等这些硬件的维护保养、点检校准、加工能力鉴定等
PIE:
是PE&IE的整合缩写哟,就是(ProcessEngineer"生产制造工程)"&(industryEngineer"工业工程)",主要服务于生产
PIE(ProcessIntegrationEngineer生产制造工程)
PIE=PE+IE
PE=产品工程,保证产品质量,PE主要负责制程工程这一块的事情,要有很强的动手的能力,纯理论的在厂里是混不下去的。
工作内容主要包括:
新产品导入新产品试产之指导试产报告制程异常处理制程巡线流程整合现场改善SOP/SIP制作损失工时确认当然,每个厂对每个职位的定义并不完全一样,以上供参考
IE=工业工程,安排生产
精益生产:
精益生产是通过系统结构、人员组织、运行方式和市场供求等方面的变革,使生产系统能很快适应用户需求不断变化,并能使生产过程中一切无用、多余的东西被精简,最终达到包括市场供销在内的生产的各方面最好结果的一种生产管理方式。
与传统的大生产方式不同,其特色是“多品种”,“小批量”。
首先不同的企业在行业特点上不尽相同,就拿流程行业和离散行业来说,流程行业,比如化工,医药,金属等,一般偏好设备管理,如TPM(TotalProductiveMaintenance),因为在流程型行业需要运用到一系列的特定设备,这些设备的状况极大的影响着产品的质量;而离散行业,比如机械,电子等,LAYOUT,生产线的排布,以及工序都是影响生产效率和质量的重要因素,因此离散行业注重标准化,JIT(JustInTime),看板以及零库存
KPI:
关键绩效指标(KPI:
KeyPerformanceIndicator)是通过对组织内部流程的输入端、输出端的关键参数进行设置、取样、计算、分析,衡量流程绩效的一种目标式量化管理指标,是把企业的战略目标分解为可操作的工作目标的工具,是企业绩效管理的基础。
KPI可以使部门主管明确部门的主要责任,并以此为基础,明确部门人员的业绩衡量指标。
建立明确的切实可行的KPI体系,是做好绩效管理的关键。
关键绩效指标是用于衡量工作人员工作绩效表现的量化指标,是绩效计划的重要组成部分。
KPI法符合一个重要的管理原理--“二八原理”。
在一个企业的价值创造过程中,存在着“80/20”的规律,即20%的骨干人员创造企业80%的价值;而且在每一位员工身上“八二原理”同样适用,即80%的工作任务是由20%的关键行为完成的。
因此,必须抓住20%的关键行为,对之进行分析和衡量,这样就能抓住业绩评价的重心
OEE:
设备综合效率是OverallEquipmentEffectiveness,简称OEE。
一般,每一个生产设备都有自己的理论产能,要实现这一理论产能必须保证没有任何干扰和质量损耗。
它是一种严格的机器总体性能的衡量手段,提示时间浪费存在于哪里,统计各种时间浪费的目的在于实现改进(OEE是一个独立的测量工具,它用来表现实际的生产能力相对于理论产能的比率)
OPE:
人员综合效率是OverallPlantEfficiency,简称OPE。
是衡量以人为主的工厂效率及质量的综合指标,在知名制造型企业被广泛使用,即是一个监控平台,也是一个考核各个部门业绩的指标。
UPPH:
UPPH=unitsPerHourPerPerson,单位人时产能,是公司作为衡量员工工作绩效的重要指标
UPPH计算方式如下:
UPPH=工作量/(投入时间*投入人力)。
(投入时间以小时计算)
TPM:
TPM是英文TotalProductiveMaintenance的缩略语,中文译名叫全员生产维护,又译为全员生产保全。
是以提高设备综合效率为目标,以全系统的预防维修为过程,全体人员参与为基础的设备保养和维修管理体系。
TPM强调五大要素,即:
——TPM致力于设备综合效率最大化的目标;
——TPM在设备一生建立彻底的预防维修体制;
——TPM由各个部门共同推行;
——TPM涉及每个雇员,从最高管理者到现场工人;
——TPM通过动机管理,即自主的小组活动来推进。
(PM)
SMT:
SMT是表面组装技术(表面贴装技术)(SurfaceMountTechnology的缩写),称为表面贴装或表面安装技术。
是目前电子组装行业里最流行的一种技术和工艺。
它是一种将无引脚或短引线表面组装元器件(简称SMC/SMD,中文称片状元器件)安装在印制电路板(PrintedCircuitBoard,PCB)的表面或其它基板的表面上,通过回流焊或浸焊等方法加以焊接组装的电路装连技术
TPS:
事务处理系统即:
Transactionprocessingsystems(TPS),是在数据(信息)发生处将它们记录下来,通过OLTP产生新的信息,将信息保存到数据库中供其他信息系统使用,提高事务处理效率并保证其正确性。
事务处理系统对于组织降低业务成本,提高信息准确度和提升业务服务水平等方面有积极意义。
JIT:
准时制生产方式(JustInTime简称JIT),又称作无库存生产方式(stocklessproduction),零库存(zeroinventories),一个流(one-pieceflow)或者超级市场生产方式(supermarketproduction)
PTS:
既定时间标准设定(PredeterminedTimeStandards,PTS)法是作业测定中常用的一种方法。
这种方法比标准要素法更进了一步,它是将构成工作单元的动作分解成若干个基本动作,对这些基本动作进行详细观测,然后做成基本动作的标准时间表。
当要确定实际工作时间时,只要把工作任务分解成这些基本动作,从基本动作的标准时间表上查出各基本动作的标准时间,将其加合就可以得到工作的正常时间,然后再加上宽放时间,就可以得到标准工作时间。
PTS法有好几种,根据基本动作的分类与使用时间单位的不同而不同。
使用最广泛的一种是MTM法(MethodsofTimeMeasurement)。
使用PTS法制定工作标准的步骤:
1、将工作或工作单元分解成基本动作;
2、决定调节因素,以便选择合适的表格值,调节因素包括:
重量、距离、物体尺寸,以及动作的难度等;
3、合计动作的标准时间,得出工作的正常时间;
4、在正常时间上加上宽放时间,得出标准工作时间
MOD:
1.预定时间系统法的一种(PTS-Predeterminedtimesystem),1966年由澳大利亚的海特博士创立﹐mod法即模特排时法﹐(modulararrangementofpredeterminedtimestandard)
2.定义:
正常的人手指动作一次的时间
(相当移动的距离为2.5cm)就是1MOD;
1MOD=0.129秒
3.mod法共有21个动作﹕
A:
上肢移动动作
M1---手指移动﹐参考距离为2.5cm
M2---手腕移动﹐参考距离为5cm
M3---小臂移动﹐参考距离为15cm
M4---大臂移动﹐参考距离为30cm
M5---伸直手﹐参考距离为45cm
B:
终结动作﹕即移动动作最后要达到的目的动作
G0---无意识碰﹑接触
G1---简单地抓
G3---复杂﹑准确地抓
P0---简单地放
P2---较复杂(大概位置)地放入﹑嵌入﹑贴上等P5---组装﹑放入﹑嵌入﹑贴上等
C:
其它动作
F3---足踏板动作
W5---走步动作
L1---重量因素(有效重时2—6千克﹐每增加4千克则加1mod)
E2---目视
R2---校正
D3---判断﹑反应
A4---按下
C4---旋转
B17---弯体动作
S30---起身坐下
MOST:
所谓标准工时,是指依据规定的作业条件,通过标准作业方法进行作业时所需的时间。
标准工时在企业有着广泛的应用。
传统标准工时计算方法中,最常见的是直接观测法与PTS法。
直接观测法需要用秒表对多个观测对象进行10-40次观测,去除异常值后再进行计算,耗时长,得出的数值误差大,且不能在作业前进行设定。
PTS法将构成工作单元的动作分解成若干个基本动作,对这些基本动作进行详细观测,然后做成基本动作的标准时间表。
掌握此方法可以在作业前就进行设定工时,且误差小。
MOST法是从PTS法中的MTM法演化来的一种方法。
与其他方法相比,MOST法是简单且经济性能极佳的方法,有着分析时间短、掌握速度快、适用范围广的特点。
其中最大的优势是分析时间短。
假设MOST法分析时间为1的话,以往的PTS法需要30-50倍的时间来分析,分析用纸也是MOST法的十多倍用量。
MOST将动作分成三类,分别是普通移动动作、控制动作、工具使用动作。
(1)普通移动动作构成代号是:
ABG/ABP/A。
各符号含义如下:
A:
代表手/脚的移动距离(横向位移),如伸手,走两步。
B:
代表躯体动作(纵向位移),如蹲下、起身、弯腰。
G:
代表抓取动作,表示抓取物品大小、重量、有无障碍等。
P:
代表定位,指物品在放置时的控制幅度,如对准某点放置、修正方向等。
于是此普通动作有:
弯腰(B)后,走几步伸手(A)抓取一定重量的物品(G),站直(B),走几步伸手(A)将物品放在指定位置(P),最后手收回(A)。
(2)控制动作构成代号是:
ABG/MXI/A。
这里面A、B、G与普通动作的A、B、G含义一样,不同的是MXI。
M:
代表所有用手引导的物体在受控制的途径上移动或动作,如用手拉下手啤机手柄。
X:
代表身体部位以外设备、机械作业时间,如将两个零件配合放上超声波模,按下超声波机按钮开关,超声完成后取出零件。
此时等待超声波机下压的时间就是X。
I:
代表对象物体方向修正。
小的方向修正可以包含在P数值或M数值内,但复杂的方向修正则必须单独给出一个I数值,如对准两条边贴贴纸,有多个针脚的电子元件插入多孔的线路板等。
于是控制动作有:
无身体动作(B),伸手(A)抓住手柄(G),摇动手柄2圈(M)到手柄的指定刻度(I),等待机器运行X秒(X),最后收回手(A)。
(3)工具使用动作构成代号是:
ABG/ABP/(动作模式)/ABP/A。
这里面A、B、G、P与普通动作的含义一样,只有在动作模式一栏,有以下划分:
F代表拧紧,L代表松开,C代表切断,S代表表面处理,M代表测量,R代表记录,T代表思考。
于是工具使用动作有:
无身体动作(B),伸手(A)抓取螺丝刀(G),无身体动作(B),手抓着螺丝刀移动(A)到螺丝位置(P),拧紧螺丝(F),无身体动作(B),手抓着螺丝刀移动(A),将螺丝刀放回到工具盒(P),最后手收回(A)。
至此,MOST所有动作介绍完毕。
动作的大小由TMU值表示。
TMU值只是一个时间单位,1TMU等于0.036秒。
MOST有详细的数值对照表,规定了多大的动作用多大的TMU值。
此数值对照表我们在这里就不一一介绍了。
PMC:
PMC即Productionmaterialcontrol的缩写。
是指对生产的计划与生产进度,以及物料的计划、跟踪、收发、存储、使用等各方面的监督与管理和呆滞料的预防处理工作。
PMC部主要有两方面的工作内容。
即PC(生产计划、生产进度的管理)与MC(物料的计划、采购、跟踪、收发、存储、使用等各方面的监督与管理,以及呆废料的预防与处理工作)。
MRP:
物资需求计划(MaterialRequirementPlanning,MRP)即指根据产品结构各层次物品的从属和数量关系,以每个物品为计划对象,以完工时期为时间基准倒排计划,按提前期长短区别各个物品下达计划时间的先后顺序,是一种工业制造企业内物资计划管理模式。
MRP是根据市场需求预测和顾客订单制定产品的生产计划,然后基于产品生成进度计划,组成产品的材料结构表和库存状况,通过计算机计算所需物料的需求量和需求时间,从而确定材料的加工进度和订货日程的一种实用技术。
VSM:
VSM,即价值流程图(ValueStreamMapping,VSM),是丰田精益制造生产系统框架下的一种用来描述物流和信息流的形象化工具。
它运用精益制造的工具和技术来帮助企业理解和精简生产流程。
价值流程图的目的是为了辨识和减少生产过程中的浪费。
浪费在这里被定义为不能够为终端产品提供增值的任何活动,并经常用于说明生产过程中所减少的“浪费”总量。
VSM可以作为管理人员、工程师、生产制造人员、流程规划人员、供应商以及顾客发现浪费、寻找浪费根源的起点。
从这点来说,VSM还是一项沟通工具。
但是,VSM往往被用作战略工具、变革管理工具。
P/Q:
产品数量(P-Q)分析是一个很简单但是非常有用的工具。
它可以用来对生产的产品按照数量进行分类,然后根据分类结果对生产车间进行布局优化。
在组装作业中,可以使用产品数量分析按照物料清单分析零部件的通用性和消耗数量。
零部件的通用性是判断不同的产品是否可以混流生产的一个评估标准,而零部件的消耗量判断如何组织零部件的供应很有帮助。
没有进行产品数量分析的公司,通常会认为他们的生产不是重复性的,很难利用精益工具进行优化。
实际上,产品数量分析能够找出表面上没有规律的市场需求,使得生产型企业能够重新组织生产线,来满足客户的实际需求。
EPE:
EveryPartEvery生产批量大小,如每3天才切换不同型号,那么EPE相当于3天的生产数量,若每天生产200片,则EPE(生产批量)=600片
C/0:
ChangeOverTime切换时间,切换时间是从生产A型号的最后一个成品结束到生产B型号的首件合格品的时间长度
C/T:
CycleTime,某工序完成第N个产品到完成第N+1个产品的时间间隔,包括增值时间和非增值时间。
VAT:
ValueAddedTime,增值时间,客户认为有价值的工序时间,及客户愿意为该工序所花的买单。
L/T:
LeadTime,周期时间,一个产品走完一道工序或者价值流所花的全部时间。
通常情况下VAT<C/T<L/T
WIP:
WorkingInProcess,ERP中指在制品或流水线,又称车间生产管理。
WIP(workinproduct)指的就是工作中心在制品区。
为工作中心提供原材料、完成产品、半成品的存储货位。
在会计核算科目中一般以【WIP物料】出现。
CELL线:
cellline(cell拉)源自日本son