H型钢轧机方案.docx
《H型钢轧机方案.docx》由会员分享,可在线阅读,更多相关《H型钢轧机方案.docx(12页珍藏版)》请在冰豆网上搜索。
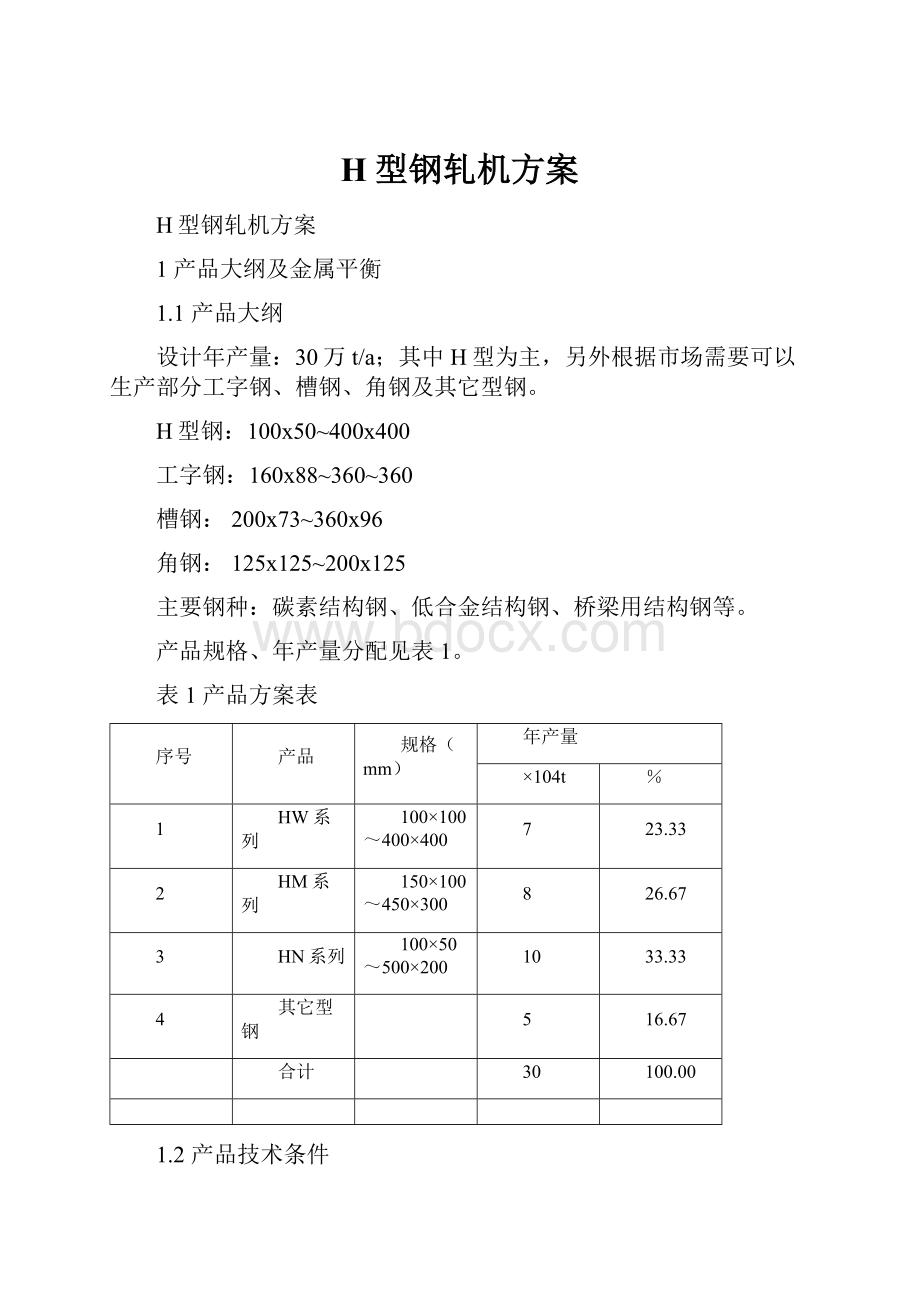
H型钢轧机方案
H型钢轧机方案
1产品大纲及金属平衡
1.1产品大纲
设计年产量:
30万t/a;其中H型为主,另外根据市场需要可以生产部分工字钢、槽钢、角钢及其它型钢。
H型钢:
100x50~400x400
工字钢:
160x88~360~360
槽钢:
200x73~360x96
角钢:
125x125~200x125
主要钢种:
碳素结构钢、低合金结构钢、桥梁用结构钢等。
产品规格、年产量分配见表1。
表1产品方案表
序号
产品
规格(mm)
年产量
×104t
%
1
HW系列
100×100~400×400
7
23.33
2
HM系列
150×100~450×300
8
26.67
3
HN系列
100×50~500×200
10
33.33
4
其它型钢
5
16.67
合计
30
100.00
1.2产品技术条件
H型钢按GB/T11263-2005标准,定尺长度为6~24m,产品堆垛后用钢线捆扎,每捆最大外形尺寸为1100×700mm,每捆最大重量为10t。
1.3原料
所用原料为合格连铸方坯、矩形坯、异型坯,连铸坯年需要量为31.6万t。
方坯规格:
160x160x10000~12000mm
矩形坯规格:
180x250x10000x12000mm
连铸异型坯规格为:
400mm×280×80mm,长度10000~12000
连铸坯符合相应标准要求
异型坯的腹板和翼缘的高度及厚度公差:
<±1.5%;
长度公差:
最大±20mm
重量公差:
最大±1.5%
弯曲度:
≯10mm/m,11m长的坯料最大弯曲度为100mm
不得有明显的扭转
铸坯内部缺陷:
钢坯应无内部缺陷、气孔和缩孔,硫和碳偏析及非金属夹杂物必须分不均匀。
1.4金属平衡
车间年产量30万t,综合成材率为95%,年需要原料31.6万
吨,金属平衡见表2。
表2金属平衡表
原料
氧化损失
切头、切废
轧废
精整损失
成品
年产量(t)
316000
4740
9480
948
948
300000
比例(%)
100
1.5
3
0.3
0.3
95
2生产工艺
2.1工艺流程简述
经清理、检查确认合格的坯料通过起重机吊到上料台架,台架移至入炉辊道,经称重、测长后由钢坯托入机送入步进梁式加热炉内进行加热。
钢坯加热到出炉温度后,由钢坯托出机将钢坯托至出炉辊道,由出炉辊道将钢坯送至高压水除鳞装置清除表面氧化铁皮。
之后,钢坯在二辊可逆开坯机上往复轧制7~11道次后,送至切舌头热锯切除轧件头、尾端“舌头”。
切除“舌头”的轧件移至粗轧机组输入辊道,由辊道将轧件送入万能粗轧机组往返轧制3~5次,然后进入万能精轧机组轧制1次,轧成最后成品,轧件上冷床前经热锯分段,满足冷床冷却要求进入步进式冷床进行冷却。
H型钢在冷床上直立冷却后,由辊道送至变节距辊式矫直机进行长尺矫直,经成排台架成排后,由冷锯机切成6~24m定尺。
切成定尺的轧件经人工目测检查后,进入堆垛台架堆垛,经打捆、称重、标牌后进入成品台架,由成品跨吊车吊运入库、发货。
在检查台上目检发现的表面质量和弯曲度不合格的钢材则运往不合格钢材清理区。
不合格钢材清理区包括一台冷锯机、一台压力矫直机、一组移送台架和称重装置。
冷锯机用于表面质量不合格产品的改尺,压力矫直机用于弯曲度超过公差的不合格产品的补充矫直。
在移送台架上还可以进行人工砂轮修磨。
改尺或补矫后的轧件,由辊道并称重后运送移送台架收集。
工艺流程简图:
3主要设备选型
3.1轧机组成
3.1.1开坯机
轧辊直径:
Φ850/750mm,最大辊环直径1100mm
辊身长度:
2300mm,
主传动电机:
由一台3500KW交流电机驱动,交—交变频调速
开坯机为两辊水平轧机,坯料送至轧机前后,根据轧制程序表进入相应的轧槽可逆轧制,并通过翻钢装置将轧件夹紧进行翻转。
一般轧制5-7道次(最多9道次)。
开坯机特点如下:
(1)辊系快速整体更换不需吊车,采甩轧辊牵引小车和横移台车结合的换辊方式,导卫横梁安装在轧机轴承座上,更换轧辊时,导卫及横梁随辊系整套从牌坊窗口中拖出,一次换辊时间仅为20min;
(2)上轧辊为液压式平衡装置,电动压下,压下量480mm,压下速度60mm/s,正常轧制时下辊固定,上辊压下。
换品种和使用较小直径的轧辊时,下轧辊用垫片组调节其水平度;
(3)上下轧辊轴向定位由操作侧的液压锁紧装置实现,下轧辊可手动轴向调节,调节量±5mm;
(4)机前、机后均设有带翻钢钩的推床,可以在任何道次移钢或翻钢。
3.1.2万能轧机机组(UR-E-UF)
1)万能粗轧机UR:
水平辊直径:
Φ1120/940mm
水平辊辊身长80-800mm
立辊直径:
Φ740/640mm
立辊辊身长285mm
电机功率:
3500KW,交—交变频调速
2)轧边机
轧辊直径:
Φ800/680mm
辊身长度1200mm,
电机功率1500KW
3)万能精轧机UF:
水平辊直径:
Φ1120/940mm
水平辊辊身长80-800mm
立辊直径:
Φ740/640mm
立辊辊身长285mm
电机功率:
2500KW,交—交变频调速
万能轧机全部采用紧凑型易更换式轧机,这种紧凑型轧机共三架,通过采用三架轧机串列可逆式布置,组成了生产H型钢的核心单元。
典型的这种串列可逆机组的布置形式有二架万能轧机组成,中间是一架轧边机,第一架(万能粗轧机UR)采用X轧法,第三架(万能精轧机UF)采用H轧法,形成X-H轧法。
第二架(轧边机E)。
轧制H型钢时,万能轧机作为万能机架使用,带有两个水平辊和两个立辊,对轧件的腹板和翼缘四面碾压。
轧制普通型钢时,万能轧机转换成两辊机架,即不带立辊,只带有两个水平辊,对轧件进行轧制。
万能轧机前后有对中导卫的升降辊道,可保证轧件正确进入轧机。
三架轧机的辊系和轴承座同步更换,更换平台在轧线外侧,换辊时间最长只用20min。
传动侧的牌坊,通过液压方式,由张力螺杆锁定,操作侧的牌坊为“可拉出”式,轧件导卫固定在水平轧机的轴承座上。
由于换辊时辊系不必通过牌坊口移出,因此,牌坊口做得非常小,仅能装下轧辊轴承,与传统的宽牌坊口轧机相比,轧辊轴承座结构的紧凑,使得水平机架的刚度提高了70%,立式机架提高了30%,而且轧机由液压压下调整取代了电动调整,变得更加灵活简单。
液压压下调整技术有以下特点:
(1)在负荷状态下进行调整;
(2)可进行精细调整,精度进一步得到改善;
(3)轧辊、轴承和牌坊都带有过负荷保护装置;
(4)堆钢时在轧辊工作处不卷钢;
(5)轧辊自动校对零位置;
(6)消除了换辊后的轧辊弹跳现象
(7)运用了AGC及液压辊缝调节系统。
3.2轧线主要辅助工艺设备
3.2.1步进梁式加热炉1座
型式:
端进侧出料步进式加热炉
加热能力为80t/h。
装炉设备将坯料从装炉辊道移至炉内合适位置,然后每一支坯在炉内以合适步距前进直到钢坯被放置到出炉辊道上面。
加热炉分三段:
预热段、加热段、均热段,钢坯出炉温度为1250℃左右。
3.2.2高压水除鳞装置1套
高压水除磷装置由输入导卫、运输辊道和除鳞箱组成,主要功能是去除出炉钢坯表面的氧化铁皮。
泵站工作压力:
22Mpa
喷嘴工作压力:
20Mpa
输入侧由水帘及双层链式帘封闭,输出侧则由双层链式帘封闭,高压水管接扁平式喷嘴,电控装置的启停通过热金属检测器控制。
3.2.3锯机
车间整个生产线共设有4台锯机,开坯机后热锯一台,主要用于切头、去尾;冷床前热锯一台,除用于切头、去尾外,主要用于分段和取样;收集床区域有冷锯两台,一台移动,一台固定,用于定尺锯切。
锯片直径:
Φ1800/1650mm
锯片厚度:
12mm。
锯片旋转线速度:
130-141m/s
进锯速度:
10-300mm/s
其特点如下:
(1)驱动电机斜置在锯机底座上,通过伞齿轮及主传动轴带动锯片,锯片由液压装置锁紧在传动轴上。
锯片进锯由液压驱动,进锯速度根据锯切阻力由比例阀调节。
当轧件断面较大、锯切阻力高时,进锯速度慢,反之,进锯速度块。
(2)锯机带有轧件夹紧装置,在上下及前后4个方向夹持轧件,锯切时不会产生振动,保证了锯切精度,提高了锯机寿命。
(3)为了提高产品的定尺率,根据轧件轧出的长度和定尺长度,在分段热锯和冷锯上选择锯切方式,控制移动锯和定尺机的位置,实现最佳锯切,提高产品的定尺率。
3.2.4步进式冷床1座
型式:
步进梁式,带有输入、输出、翻立及翻倒装置
输入、输出辊道中心距:
17m
冷床宽度:
60m
步进梁水平行程:
400/520/650mm
步进梁垂直行程:
230mm
冷床的下床温度:
80℃
冷床由固定梁和步进梁组成,步进梁的水平和垂直行程分别由液压缸单独驱动,且二者同步运动。
轧件通过冷床下的强制喷水雾化,提高了冷却效果;通过开/关冷却水管和采用水压控制,冷却速度能够得到调节。
所有的轧件均被送到冷床上的固定位置,由移钢机构将轧件从步进梁上翻出并移至冷床的输出辊道上。
3.2.5变节距矫直机1台
型式:
九辊悬臂式,节距可调
矫直辊直径:
Φ650-820mm
最大矫直速度:
6m/s,咬入速度1.5 m/s
辊子数量:
9个
节距范围:
1100~1400mm
采用长尺(相当于冷床长度)在线矫直工艺,先矫直后定尺锯切。
矫直辊通过液压锁紧螺母固定在矫直辊轴上,为了覆盖所有的产品范围,矫直机在水平方向上有一个固定的但不一样的间距。
所有的矫直辊都由电机单独传动。
矫直机人口侧设有喂钢装置,矫直辊下侧设有氧化铁皮处理系统,上侧设有一套换辊吊车,矫直机旁边设有一套矫直辊快速更换装置。
3.2.6其它设备
包括定尺机、码垛机、打捆机、收集台架、辊道、液压站、稀油站、加热炉周围及轧机前后等辅助设备。
4车间工作制度及轧机年工作小时
本车间采用4班3运转连续工作制,节假日不停产,实行轮休。
轧机年工作小时为6500h,见表3。
表3轧机年工作时间分析表
日历
时间
计划检修
规定
工作时间
停工时间
额定工作时间
大修或中修
小修
交接班及换辊
事故及其他
d
h
d
h
d
h
d
h
h
h
d
365
8760
20
480
15
360
330
7920
495
925
6500
轧机年工作小时说明如下:
(1)设备大修或中修:
每年1次,每次平均占用20天;
(2)小修:
每月2次,每次年均15小时;
(3)班前准备:
每班0.5小时,按每年工作330天,共计495小时;
(4)事故及其他停机时间:
925小时。
5车间工艺平面布置
车间由原料跨、主轧跨、成品跨(一、二)、轧辊加工间、电气室等组成。
见附图。
6车间工艺特点及装备水平
6.1异型坯轧制
用异型坯直接轧制是二十世纪八十年代末、九十年代国际先进技术,与过去用板坯、矩形坯轧制技术相比,开坯机的轧制道次可以减少,轧制温度可以提高100℃,轧制力降低30%,综合能耗降低20%。
6.2开轭式机架,快速换辊技术
二十世纪八十年代、九十年代初,国际上出现了开轭式结构的万能轧机,这种结构型式的轧机采用辊系换辊,换辊时间仅20~30分钟,与过去的闭口式机架、预应力机架及紧凑式机架相比,机架数量减少,设备投资少,换辊时间短。
6.3长尺冷却、矫直
采用长尺冷却-长尺矫直-冷锯锯切工艺,锯切质量和精度高,矫直质量好,成品的头尾平直,提高了产品的精度和成材率。
6.4三机架可逆连轧技术
增加万能轧机道次可以提高H型钢的质量,但影响轧机的产量,过去常用的方法是采用两组万能粗轧机跟踪布置方式解决产量和质量的矛盾。
但是加大了设备间距,增加了厂房和投资。
二十世纪七十年代末,出现了万能-轧边-万能布置的三机架可逆连轧机,这种轧机布置组成,既增加了万能道次又缩短了设备间距,优点是产量适中,占地少,投资省。
串列可逆连轧机中采用X-H轧制方法,较过去的轧机减少了轧机机架数量、轧辊及导卫,使得设备生产费用大大降低。
6.5厚度控制
厚度控制,由于立辊的参与而使变形机理复杂。
1991年投产的英国拉肯比(Lackenby)厂首次采用了,在上水平辊和左、右两侧立辊的压下和轴承座间设置了液压,同时控制三个辊缝,从而可以生产高精度产品。
此外,在万能轧机设置了上轧辊动态轴向调整。
轧机调零后,可以测量和存储上探头到上辊轴及下探头到下辊轴的距离。
轧制过程中立辊如失去平衡而引起上辊或下辊的窜动,上辊会与下辊同步调整,从而保证上、下腹板对中并控制腹板和翼缘的尺寸。
6.6生产线的自动化水平
先进的1级和2级自动化系统负责设备和过程在线功能控制,可实现下列功能:
(1)机械设备各种动作的顺序控制;
(2)材料跟踪;
(3)主传动装置速度控制;
(4)闭环控制功能;
(5)设定值计算功能,如辊缝自动控制;
(6)过程参数记录。
建立在PLC和微处理器基础上的系统,可自动控制可逆式轧机区的设备。
1级自动化系统负责系统的动作控制,确保达到最佳的动态特性和很高的响应速度。
执行元件的设定既可通过查表(操作人员可以修改),也可通过2级自动化系统来完成。
2级自动化系统借助于孔型设计计算程序,可计算轧机轧制程序,并提供给与1级自动化系统相连的轧机设定装置。
可利用在轧机以“道次与道次”和“轧件与轧件”模式工作时从现场获得的检测结果,对模型进行修正;而且可以在“离线”模式下运行,并显示运行结果。
1级和2级系统可完全控制轧机的自动化运行,其中包括液压辊缝控制、厚度自动控制、截面控制系统、孔型设计计算/自适应等控制功能。
7主要技术经济指标
主要技术经济指标见表5。
表5技术经济指标
序号
指标名称
单位
数量
备注
1
年产量
t
300000
2
钢坯年需要量
t
316000
3
轧机组成
架
4
其中:
开坯轧机
架
1
万能轧机
架
2
轧边机
架
1
4
车间工艺设备总重量
t
5600
其中:
工艺操作设备
t
4900
起重运输设备
t
700
5
车间设备总装机容量
kW
28000
6
主厂房建筑面积
m2
48300
7
额定年工作时间
h
6500
8
货物周转量
642000
输入
t
320000
输出
t
322000
9
每吨产品消耗指标
连铸坯
t
1.053
燃料
GJ
1.3
电
kWh
110
补充水
m3
1
压缩空气
Nm3
8
轧辊
kg
2.5
耐火材料
kg
0.5
润滑材料
kg
0.148
10
全厂劳动定员
人
350