起动机发电机汽车技术资料.docx
《起动机发电机汽车技术资料.docx》由会员分享,可在线阅读,更多相关《起动机发电机汽车技术资料.docx(53页珍藏版)》请在冰豆网上搜索。
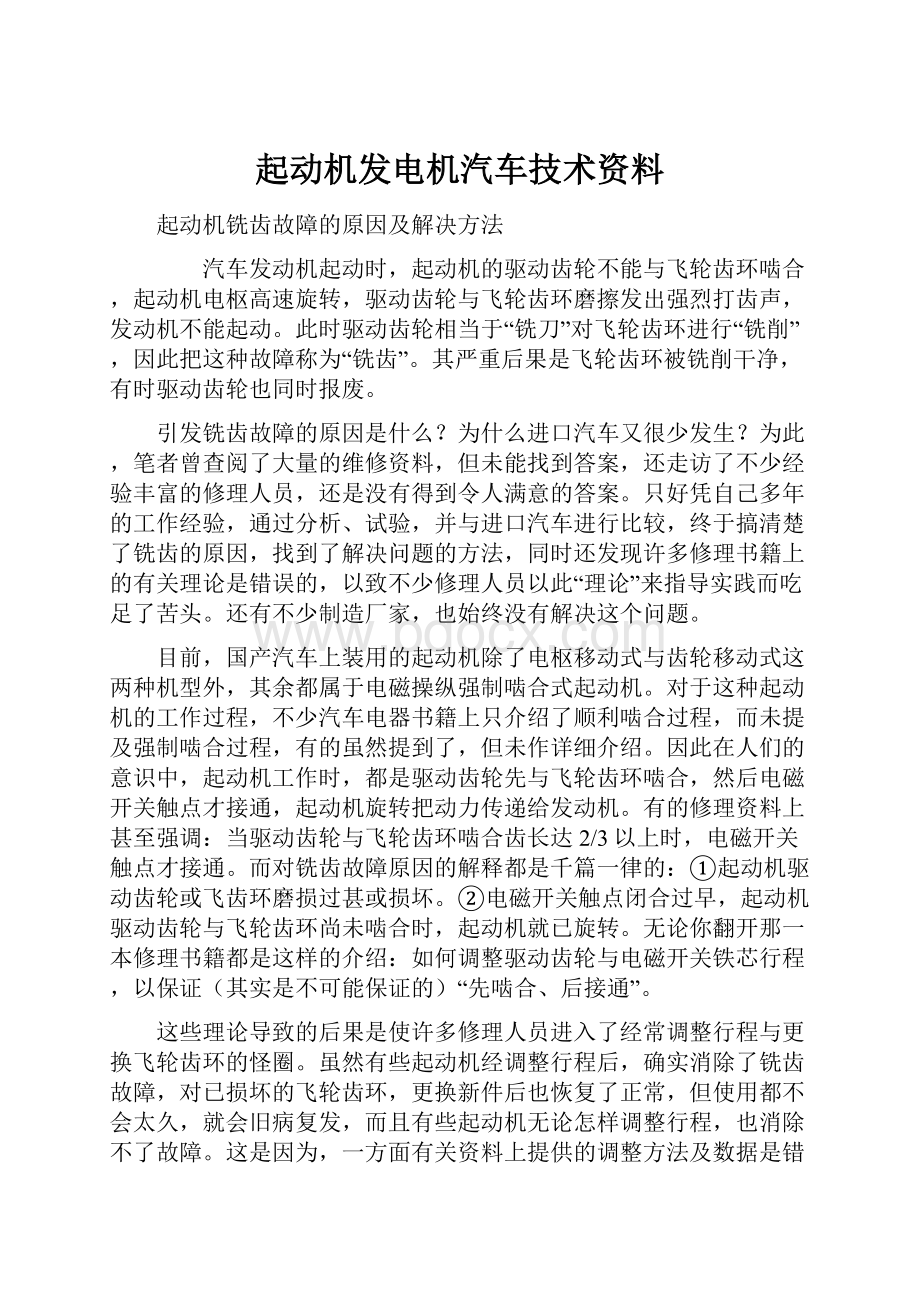
起动机发电机汽车技术资料
起动机铣齿故障的原因及解决方法
汽车发动机起动时,起动机的驱动齿轮不能与飞轮齿环啮合,起动机电枢高速旋转,驱动齿轮与飞轮齿环磨擦发出强烈打齿声,发动机不能起动。
此时驱动齿轮相当于“铣刀”对飞轮齿环进行“铣削”,因此把这种故障称为“铣齿”。
其严重后果是飞轮齿环被铣削干净,有时驱动齿轮也同时报废。
引发铣齿故障的原因是什么?
为什么进口汽车又很少发生?
为此,笔者曾查阅了大量的维修资料,但未能找到答案,还走访了不少经验丰富的修理人员,还是没有得到令人满意的答案。
只好凭自己多年的工作经验,通过分析、试验,并与进口汽车进行比较,终于搞清楚了铣齿的原因,找到了解决问题的方法,同时还发现许多修理书籍上的有关理论是错误的,以致不少修理人员以此“理论”来指导实践而吃足了苦头。
还有不少制造厂家,也始终没有解决这个问题。
目前,国产汽车上装用的起动机除了电枢移动式与齿轮移动式这两种机型外,其余都属于电磁操纵强制啮合式起动机。
对于这种起动机的工作过程,不少汽车电器书籍上只介绍了顺利啮合过程,而未提及强制啮合过程,有的虽然提到了,但未作详细介绍。
因此在人们的意识中,起动机工作时,都是驱动齿轮先与飞轮齿环啮合,然后电磁开关触点才接通,起动机旋转把动力传递给发动机。
有的修理资料上甚至强调:
当驱动齿轮与飞轮齿环啮合齿长达2/3以上时,电磁开关触点才接通。
而对铣齿故障原因的解释都是千篇一律的:
①起动机驱动齿轮或飞齿环磨损过甚或损坏。
②电磁开关触点闭合过早,起动机驱动齿轮与飞轮齿环尚未啮合时,起动机就已旋转。
无论你翻开那一本修理书籍都是这样的介绍:
如何调整驱动齿轮与电磁开关铁芯行程,以保证(其实是不可能保证的)“先啮合、后接通”。
这些理论导致的后果是使许多修理人员进入了经常调整行程与更换飞轮齿环的怪圈。
虽然有些起动机经调整行程后,确实消除了铣齿故障,对已损坏的飞轮齿环,更换新件后也恢复了正常,但使用都不会太久,就会旧病复发,而且有些起动机无论怎样调整行程,也消除不了故障。
这是因为,一方面有关资料上提供的调整方法及数据是错误的,另一方面不知飞轮齿环是如何磨损的,只好坏了以后换新的,再坏再换新的。
这种头痛医头,脚痛医脚,而不能根本解决问题的原因是不知道强制啮合式起动机的强制啮合过程。
其实起动机在工作时,驱动齿轮在向飞轮齿环移动过程中,除了前面讲到的齿轮先啮合后,电磁开关触点才接通的情况,即顺利啮合外,绝大多数情况则是驱动齿轮的齿刚好顶在飞轮齿环上(顶齿),这样转动齿轮已不能向前移动,但拨叉继续移动,从而压缩单向离合器上的啮合弹簧,使两齿端面之间的压力增大,当电磁开关触点接通时,由于驱动齿轮紧紧压在飞轮齿上,使起动机电枢的转动阻力增大,而只能缓慢转动,待转过一定角度后,驱动齿轮滑入飞轮齿环槽中完成啮合过程。
这种在顶齿状态下,电磁开关也要接通,使驱动齿轮强行与飞轮齿环啮合的过程称之为强制啮合。
其关键是靠啮合弹簧的压力,强行降低电枢转速,来求得啮合成功。
从强制啮合过程来看,是电磁开关触点先接通,齿轮后啮合。
那么电磁开关触点接通时间的先后,对是否会造成铣齿故障已无因果关系,也就是说目前那种“都是先啮合,后接通”的理论是错误的。
而“先接通、后啮合”则是强制啮合式起动机的主要特征。
从强制啮合过程可以发现,如果强制啮合的失败,就会发行铣齿故障,即铣齿故障的原因是强制啮合失败所造成的。
强制啮合成功的前提是啮合弹簧必须压紧,使起动机的转动阻力增大,而速缓慢,如果啮合弹簧压得不紧,或弹簧本身压力不够,起动机的初始转速太高,势必会造成铣齿。
从实际情况来看,啮合弹簧压本身压力不够不多见,主要问题都是啮合弹簧未压紧。
而啮合弹簧压不紧的原因只有一个,就是在静止状态下,起动机驱动齿轮与飞轮齿环之间的轴向距离太大,实际测得结果达5mm,有不少甚至超过5mm。
我国标准JB1506-75中规定δ=3mm-5mm,目前所有修理资料也提供这个数据。
笔者不知这个数据是根据什么得出的,但从实际出发,只要能保证发动机在正常运转中,飞轮齿环不碰擦驱动齿轮,δ越小越好。
因为δ越小,起动时驱动齿轮对飞轮齿环的冲击力就越小,飞轮齿环被撞击损坏的可能性就越小。
其次δ越小,在强制啮合情况下,啮合弹簧对驱动齿轮的压力越大,就越容易啮合成功。
例如,一种起动机δ=1mm,另一种起动机δ=5mm,那么后者飞轮齿环受到的冲击力将成倍地大于前者。
这是因为电磁开关线圈刚通电时,铁心有一半在线圈外,受到的电磁吸力还较小,随着铁心向线圈内移动,电磁吸力越来越大,这样铁心的移动过程就是一个加速过程,移动距离越长,铁心的移动速度越快。
而通过拨叉转为驱动齿轮的移动,则是δ越大,驱动齿轮撞击飞轮齿环的速度就越高,冲击力也就越大,飞轮齿环磨损就越快。
磨损后的飞轮齿环与驱动齿轮之间的δ更大,这使啮合弹簧的可压缩距离减小,压力降低,铣齿也就不可避免。
铣齿一旦发生,驱动齿轮对飞轮齿环的破坏极为严重,δ值会进一步加大,从而进入恶性循环。
这就是不少车辆使用一段时间后就发生铣齿故障的原因所在。
从上述可知,造成铣齿的真正原因是驱动齿轮与飞轮齿环之间的轴向距离δ太大。
那么,多大的δ值才合适呢?
几乎不发生铣齿故障的轿车及进口汽车的实际情况来看,这些车辆上的δ值都是保持在1mm-2mm范围内,因此笔者认为δ值以2mm左右为宜,最好控制在2mm以内,但考虑到国内实际情况,如零部件的误差,可将δ值放宽到≤3mm。
值得提醒的是,不要以为功率大的起动机δ值就可以大一些,实际上则恰恰相反,功率越大的起动机,驱动齿轮对飞轮齿环的冲击力就越大因此要求δ值更小,为此呼吁发动机与起动机生产厂应密切配合,严格控制δ这个参数,让以后产的汽车不再频繁发生铣齿故障。
那么对目前大批已发生故障的车辆,又如何来处理呢?
首先,拆下起动机,分别测量飞轮壳上安装面至飞轮齿环端面的距离与起动机上安装面至驱动齿轮端的距离,两者之差就是δ值,也可以分别测量驱动齿轮上的压痕长度与驱动齿轮端面至止推挡圈的距离,两者之差也是δ值。
然后采取以下措施。
a.对可以调整的起动机,如321型、124型、614型等,首先把驱动齿轮的位置调整到满足δ≤3mm,然后把电磁开关铁心压到底,也可通电使铁心吸到底,此时驱动齿轮端面至止推挡圈的距离为0.1mm-1mm,只有同时满足这2项要求,该起动机才算调整完毕,如虽经调整,但δ>3mm,则应采用其它措施。
特别提醒不按目前的修理资料上介绍的方法去调整,因为这些资料上有关“起动机的调整”这一节都是错误的。
这也是为什么装用321型起动机的492汽油机会频繁发生铣齿故障,原因就是调整的方法不准确。
b.对大多数不能调整及上述无法调整到位的起动机,可采用在飞轮齿环下面增加垫圈的方法来缩小δ值。
取下已损坏的飞轮齿环,用铁皮加工几个内外径与飞轮齿环差不多大的垫圈,根据原δ值计算好需要垫多少个垫圈才能满足δ<3mm的要求,然后在飞轮上先装上垫圈,再装上新的飞轮齿环,也可找一根直径与所需垫圈总厚度相同的铁丝,焊成一个圆环,垫在飞轮齿环下面。
c.对飞轮齿环尚未严重损坏,但已发生铣齿故障的汽车,为减小工作量,可车削起动机的安装面,但必须注意车削安装面后,起动机的安装强度会降低。
因此一般车削量不应超过1mm。
全塑型换向器
全塑型换向器是近几年发展起来的一种新型换向器,其结构形式完全不同于压铆式换向器和半塑型换向器。
换向器的换向片是用冷挤工艺将铜管挤压成带有纵向燕尾槽形的铜圈。
压塑成形后,再经过车外圆、铣槽等一系列加工而成。
这种换向器的最大优点是超速性能很好,因此可用于高速工作的减速型起动机。
同时这种换向器的制造工艺比较简单,并可节省大量的铜材,因此是一种很有发展前途的换向器。
它的机械性能和耐热性能主要取决于压塑料的性能。
采用多触点结构插接器提高电流负载能力
随着车用线束控制的发展,要求有传送大电流负载的插接器。
一般情况下,工程师几乎没有别的选择,只有选用大容量插接器,然而这不但不利于整个系统的设计,而且会增加成品成本。
为了降低接触电阻,除了进行表面处理外,只能采取增加插拔力的方法,这将使得插入和拔出时非常困难。
1多触点结构设计
多触点插接器是一种增加了插头、插座之间接触点数量的插接器。
采用插接器多触点结构设计可以达到增加接触的数量,满足传送大电流负载的要求。
多触点结构设计的插座使用“百叶窗式”的接触弹簧条。
弹簧条沿着插座轴向排列,通过“百叶窗”而形成环绕插座周向的多路接触点。
当插头插入该类型插座时,“百叶窗”就变得像弹簧一样,沿其周边紧箍着插头,从而避免某一点(或2点)接触。
将触点设计成“百叶”形状,“百叶”可沿着插座轴向提供相等的接触压力。
当作为插座使用时,可以通过对电流数值的均衡分配,从而提高电源使用效率。
另外,接触点之间的低接触电阻,极大地降低了电压降,使在某一给定电流值下护套内产生的温升值更低。
由于提高电流值而产生负面影响的发热量绝大部分都是通过接触表面散发。
在一般的连接方式中,大致可分为单面和双面接触连接,所产生热量是通过小面积接触面散发出去,多触点结构插接器的温升表现得非常剧烈,其接触面积越大,散热就越快。
多触点结构也有助于避免“热点”现象的出现。
所谓“热点”,就是在某一连接界面中,热量的大部分均通过某一点而散发,该点即成为“热点”。
而多触点结构,不仅增加了接触点的数量,而且极大均衡了接触压力,因此避免了某一点成为“热点”的可能性。
传统的电流信号传递系统中,接触点数量相对较少,只有通过增加插拔力来降低接触电阻,结果造成插拔难度的增加。
而多触点结构插接器在工作时可提供相对低的插入力和拔出力。
另外,在相同的电流负载下,多触点结构插接器所需的工作空间更小。
例如将一个4线插接器改变成多触点结构,即可将其负载增加到双倍。
在多触点结构负荷状态下,4线插接器在达到30℃温升时的负载电流是31A,而传统方式插接器达到同样温升时的负载仅为14.9A。
这意味着选用小型号多触点结构插接器即可承受大电流负载,而且不会降低连接的可靠性和安全性。
2扭式和桥式触点
多触点结构设计成扭式或桥式触点。
对于扭式触点,其“百叶”绕自身轴旋转而产生接触压力,对于桥式触点,仅将其“百叶”预压成简单弧形,因为扭式触点的“百叶”相对于桥式触点的“百叶”更长,所以它适用于大横截面的插头(或插座)。
桥式触点上的“百叶”较短,适用于小横截面的插头(或插座)。
例如扭式触点不能够使用于直径小于7.9mm的插头,而桥式触点能够使用于直径为0.5mm的插头。
这2种结构的触点可以使用带状材料,借助模具加工成所需的形状。
多触点插座安装于插座的护套内,通过采用各种固定机构来保持该插座在恰当的位置。
例如可在小扭式触点上设计沉孔或燕尾槽,在大扭式套管上采用保持环(钢或塑料),在桥式触点上设计沉孔等。
多触点结构设计能够使用于多种类型的和、插接器,包括:
标准圆接触插入式连接器、旋转式连接360°旋转、滑动连接、桶式连接、膨胀式连接。
3多触点结构设计变量
一旦确定用多触点结构来提高插接器电流负载,就必须考虑下面这些变量:
①材料厚度,影响设计的尺寸状况。
②触点表面处理,即电镀或不电镀处理。
例如铍铜合金和镀锡处理来防腐蚀及耐温。
③配合表面的表面处理,粗糙表面减低连接的持久性,而且加大了插拔力。
④材料,材料有不同的特性,比如电传导性,会降低多触点的接触压力。
这些变量将影响连接的持久性、插拔力、电压降和电阻值。
另外,多触点结构还能够在200℃以下的范围内工作(不包括采用电镀使得熔点降低,例如镀锡或锡/铅),也能浸入润滑油或润滑脂中工作(这有助于散热),这都使得多触点结构插接器能够不增加尺寸就可提高其通过的电流负载。
4结论
多触点结构插接器允许应用电流负载的增加而不必增大插接器的尺寸。
插接器通过“百叶窗式”的接触弹簧条,沿着插座的内周边方向形成周边接触压力,极大地提高了插接器的工作性能。
一旦确定用多触点结构设计来提高电流负载能力,还必须考虑选材、材料厚度及表面处理等变量,这些变量将影响持久性、插拔力、电压降和电阻值等性能。
起动机产品行业整体质量状况及主要问题分析
起动机主要故障表现形式:
1)单向离合器失效(打滑、异响)
2)电磁开关故障(触点烧牢、常吸、不吸)
3)定、转子故障
4)转子脱焊
5)轴衬磨损
6)无力、空转等其他故障
近两年来,在国家拖拉机质检中心对送检中心对送检的产品检测中发现,问题较多的为:
1 轴衬磨损,造成后果是起动无力,定、转子相擦,发现晚电机就会烧坏
2 电磁开关故障:
主要吸合无力、粘连,保持线断
3 单向离合器打滑、驱动齿轮内轴衬碎裂、缓冲弹簧质量不稳
4 碳刷磨损
5 工作性能达不到要求
6 换向器等其他故障
在装机使用中主要表现为:
1 起动机不起动工作
2 起动无力
3 铣齿、顶齿
4 起动机空转、打滑
5 未起动齿轮有周期性撞击声
6 起动中有异常机械撞击声
7 单向离合器不回位
为此,我们根据检测结果统计及综合调研情况与主机厂有关人员座谈,对起动机在使用中所反映的问题进行综合分析。
二 主要故障及产生的原因
1 起动机不起动
1)电磁开关损坏
主要表现为吸合线圈断路,短路,造成开关不能吸合,主电路接不通
2)电磁开关接触铜片和触蹼严重烧蚀或调整不当,接不通
3)起动机定、转子绕组烧断、短路或搭铁。
其中定、转子烧,经过我们对有关样机分析,多数是由于轴衬严重磨损,造成电机扫膛所致。
4)换向器严重烧蚀、损坏
5)绝缘碳刷搭铁,碳刷簧折断或失效,碳刷与换向器不能可靠接触
6)整车起动电路故障,如掉线,起动继电器损坏等
7)蓄电池严重亏电或接头脱落,松动等
2 起动无力(起动机运转但不能正常起动发动机)
1)轴衬磨损,造成定、转子相擦,严重将导致电机烧坏(这一点在对检验故障样机及对调研情况分析,故障发生率非常高)
2)换向器有烧蚀或过脏
3)碳刷质量不好,磨损过多或刷簧过软,接触不良
4)电机膛内窜入碳粉或其他杂物
5)定、转子绕组有局部短路
6)单向离合器打滑
7)电枢线与换向器有脱焊
8)蓄电池亏电或容量小,电瓶线过长、过细
9)对初选的起动机与发动机匹配不合理,功率偏小
3 顶齿、铣齿
1)电磁开关的行程调整不当或与驱动机构匹配不好
2)驱动齿轮或飞轮齿圈磨损过甚或损坏
3)电磁开关吸力过小或接触铜片、触点烧毛
4)单向离合器缓冲弹簧质量问题
4 起动无力
1)单向离合器打滑、失效
2)电磁开关与拨叉脱扣或开关动铁芯小顶柱软化失效
5 驱动齿轮周期性撞击飞轮齿圈
主要是电磁开关保持线圈断路,短路或搭铁不良。
由于保持线圈不能保持驱动齿轮与大齿圈的啮合,而吸引线圈又在驱动齿轮进入啮合后被短路而失去吸力,驱动齿轮应在复位弹簧的作用下与齿圈脱开啮合,一但脱开吸引线圈又不短路了,又吸着动铁芯运动推着驱动齿轮再一次进入飞轮齿圈啮合。
当驱动齿轮与飞轮啮合后,吸引线圈又被短路而失去吸力,保持线圈因断路也无吸力保持住啮合,驱动齿轮又被复位(也即接触铜片与触点脱开)脱离啮合。
保持线圈搭铁线被烧断的现象,在实际使用和试验中发生率很高。
6 起动中异响、有“哒哒”噪声
驱动齿轮内小轴衬碎裂,其与飞轮齿圈啮合运转时产生跳动所致。
7 单向离合器不回位
1)电磁开关接触铜片与触点烧粘
2)回位弹簧失效
3)起动线路故障(如起动继电器触点烧结)
根据我们掌握的信息,上述所反映的问题,虽然有个别现象是由主机线路原因,但主要还是起动机自身质量问题,各生产厂应根据市场反映的状况,摸清自家产品的质量问题,逐步加以分析解决。
为什么汽车电压等级要升级?
汽车电压等级的变化深受下列因素的影响:
1 发动机技术
2 车上电器的负荷量
3 汽车技术特别是电子技术的应用发展程度,早期汽车广泛采用6V的电源,但由于汽车发动机压缩比的不断提高,起动机的功率也随之增加,6V电源已经不能满足需要,所以从20世纪50年代开始逐步被12V/14V电源所取代。
随着汽车电子装置比例的增大,汽车对电的需求量增长;此外,电子技术的发展使一些带电的机械装置逐步转变为带机械的电子产品,如电子制动、电动转向、机械阀的电子控制等,这些装置也增加了耗电量。
另外,如果不改变现行的电压标准,功率增大必然导致电流增大,电流增大必然要加大导线的截面积,就要加粗导线,电器件的体积会变大,汽车重量会增加,油耗会增大,有限空间被占用。
选用42V电压作为新的电源标准,简单地说是从发电机输出电压14V的3倍数考虑的,从理论上讲,电压提高3倍数,电流会减少65%,可以更合理地运用在汽车电器系统上;高电压提供了减少导线和部件体积以及重新设计电器系统的可能。
另外是从保证安全的角度考虑,60V以下的电压被认为安全电压,当供电电压大于60V时,由于导线的接头的绝缘材料需大幅增加,因此带来的材料重量增长将会导致在其他方面所获的益处大打折扣。
42V电源的系统的实施,将给整车及发动机等机械部件和电气部件的性能,结构和设计带来深远的影响。
能提高整车的燃油经济性、改善排放,提供更好的驾驶舒适性;促使部件的优化;促使X-by-wire(电子伺服系统)控制的更好的实现。
因此美国与欧洲的汽车制造商和零部件供应商就新一代汽车供电电压标准在1998年共同达成了36V/42V新标准的协议。
起动/发电一体化电压(ISG)集起动与发电于一电机内,取代了传统的起动机和交流发电机,能实现发动机的即起即停。
ISG将在汽车制动时使发动机自动熄火,然后在需要动力时立即重新起动,避免怠速工况,这样能在不影响操作的情况下减少尾气排放。
和ISG系统配合使用的是一个能量再生式制动系统,这个再生式制动系统将使汽车制动时产生的能量,帮助汽车的蓄电池充电,而蓄电池反过来又在汽车起动及加速时提供能源。
实际上这也是一种混合驱动的雏形,它允许发动机经常熄火,必要时再重新快速起动,能在0.2s内使发动机达到怠速工况,可实现低速时由电源直接驱动电机作为汽车的动力源和汽车加速时的动力辅助功能,完全避免怠速工况;当汽车停车灯亮发动机关闭及制动时,施加的制动力使ISG转入发电机状态,电流输入蓄电池,可有效节省怠速与减速时的油耗和降低排放及实现能量回收。
ISG电机的效率可达80%左右,而14V的系统的起动机的效率只70-75%之间,提高了电机的效率。
42V电源系统的应用为发动机的结构改进提供了更大的可能性,并将为新的部件如电控气门的应用创造更好条件。
使用42V电源系统,发动机的一些附件,如转向助力泵、水泵、冷却风扇、空调压缩机和气泵等,可以从发动机中分离出来,直接由新的电源系统驱动,从而减少空转消耗,提高能源利用效率。
此外,减少了发动机的部件数量,改善了设计,起到提高发动机效率的作用。
汽车发动机设计最大的变化是将用无凸轮轴的电磁式电控配气相位机构取代传统的凸轮轴配气相位机构,其优点是在相同排量下,能够提供更大的发动机功率,改善发动机高低速的扭矩特性,降低消耗和有害气体排放,同时降低发动机制造成本。
42V电源系统还可以为发动机系统上诸如为尾气后处理装置的加热器,柴油机微粒捕集器加热器提供能源,有效地降低有害气体排放。
电加热式三效尾气后处理器,可以在原基础上提高加热功率,减少起燃时间,进一步降低冷起动的排放。
蓄电池
1.铅酸蓄电池
铅酸蓄电池也至今已有100多年的历史,广泛用作内烯机汽车的起动动力源。
目前大部分电动车使用的蓄电池均为传统的铅酸蓄电池。
这种蓄电池可靠性好、价格便宜;比功率也基本上能满足电动汽车的动力性要求。
但它有两大缺点:
一是比能量低,所占的质量和体积太大,且一次充电续驶里程较短;另一个是使用寿命短,使用成本过高。
铅酸蓄电池的应用历史最长,也是最成熟,成本最低廉的蓄电池。
当前存在的主要问题是一次充电的续驶里程短,一般约在30-40km,就是快速充电也要4-6H,且比能量只有30W/KG。
为此人们一直探索着如何改进铅酸蓄电池的性能,开发能量效率更高、稳定性更好,电荷容量更大的新电池。
2.镍镉蓄电池
目前,镍镉蓄电池的应用广泛程度仅次于铅酸蓄电池,其比能量可达55wh/kg,比功率超过190w/kg,可快速充电,循环使用寿命是铅酸蓄电池的两倍多,可达到2000多次,但价格为铅酸蓄电池的4-5倍。
它的初期购置成本虽高,但由于其在比能量和使用寿命方面的优势,因此其长期的实际使用成本并不高。
使用中要注意做好回收工作。
以免重金属造成环境污染。
3.镍锌蓄电池
镍锌蓄电池是美国国家能源研究公司(ERC)开发和生产的产品。
厦门蓄电池总厂已与其合作引进了此产品。
新型密封镍锌蓄电池具有高比能量、高比功率和大电流放电的优势。
这种优势使得镍锌蓄电池能够满足电动车辆在一次充电续驶里程、爬坡和加速等方面对能量的需求。
镍锌蓄电池是一极具竞争力的蓄电池,其能量与镍氢蓄电池相当,体积功率已超过镍镉蓄电池,小于镍氢蓄电池。
大电流放电,蓄电池的电压在较大的范围是平衡的,且具有很长的寿命。
4.镍氢蓄电池
镍氢蓄电池是目前人们看好的第二代蓄电池之五,是取代镍镉蓄电池的产品,当然也是取代铅酸蓄电池是产品。
镍氢蓄电池和镍镉蓄电池一样,也属于碱性蓄电池,其特性和镍镉蓄电池相似,不过镍氢蓄电池不含镉、铜,不存在重金属污染问题。
目前生产电动汽车镍氢蓄电池的公司主要是Ovonie公司,它现有80和130Ah两种单元蓄电池,并由此构成30和50kwh两种规格的蓄电池。
其比能量达75-80wh/kg,比功率达160-230W/kg,循环使用寿命超过600次。
这种蓄电池曾装在几种电动汽车上试用,其中一类车一次充电续驶里程为345KM,有一辆车一年中行驶了8万多公里。
由于价格较高,目前尚未大批量生产。
估计随着镍氢蓄电池技术的发展,其比能量可超过80,循环使用寿命可超过2000次,远景价格可降至150美元/kWh。
通用汽车公司已把它作为今后几年电动汽车优先考虑的蓄电池。
5.钠硫蓄电池
钠硫蓄电池也是近期普遍看好的电动汽车用蓄电池,美国福特汽车公司的Minivan电动汽车使用的就是钠硫蓄电池。
它已被美国先进蓄电池联合体列为中期发展的电动汽车蓄电池。
德国ABB公司生产的B240K型钠硫蓄电池,其质量为17.5公斤,蓄电量19.2kwh;比能量达109Wh/kg,循环使用寿命1200次,装车试验时最好的一辆车无故障地行驶了2300公里。
钠硫蓄电池主要存在高温腐蚀严重、蓄电池寿命较短,性能稳定性及使用安全性不太理想等问题。
6.锌空气蓄电池
锌空气蓄电池于1993年始于德国,经过十多年的努力现已基本成熟。
美国的锌空气蓄电池采用的锌粉,配合液体氢氧化钾使锌粉在空气中进行氧化产生电能。
这种蓄电池具有体积小,电荷容量大,质量小,能在宽广的温度范围内正常工作,且无腐蚀,工作安全可靠,成本低廉等优点,是一极有前途的电动车用蓄电池。
锌空气蓄电池的在比能量在200左右。
美国DEMI公司为电动汽车开发的锌空气蓄电池的比能量已达160左右,但它目前尚存在寿命短、比功率小,不能输出大电流及难以充电等缺点。
7飞轮蓄电池 飞轮在真空中旋转,转速可达200000,驱动电机可作电动和发电机来运行。
8.燃料蓄电池被称为质子交换膜燃料蓄电池(PEMFC),它以纯氢为燃料,以空气中氧为氧化剂。
点焊生产的质量控制与检测
点焊作为一种高效、快捷的加工方法,得到越来越广泛的应用。
然而,其可靠性差、焊接强度难检测、生产质量难保证,又限制了它的使用范围。
笔者从事点焊工作多年,下面就点焊质量的控制谈几点看法。
点焊的工作过程为焊炬接触工作、加压、通电、保压及焊炬脱离工件几个步骤,因此,保证其工作过程达到所规定的要求,便可获得牢靠的点焊焊点。
1)在加压、通电过程中,由于焊炬会发红到熔融状态,故要求有一定压力的水进行冷却。
在此过程里,如果未达到要求,往往会出现焊点质量不稳定、焊接脱落现象。
另外,在焊接熔融状态时,两焊炬要有一定的预压力,若生产中未及时调整焊炬的预压力,也不能获得牢固的焊点。
其预压力是靠调整焊