套印准确及套印精度的控制.docx
《套印准确及套印精度的控制.docx》由会员分享,可在线阅读,更多相关《套印准确及套印精度的控制.docx(14页珍藏版)》请在冰豆网上搜索。
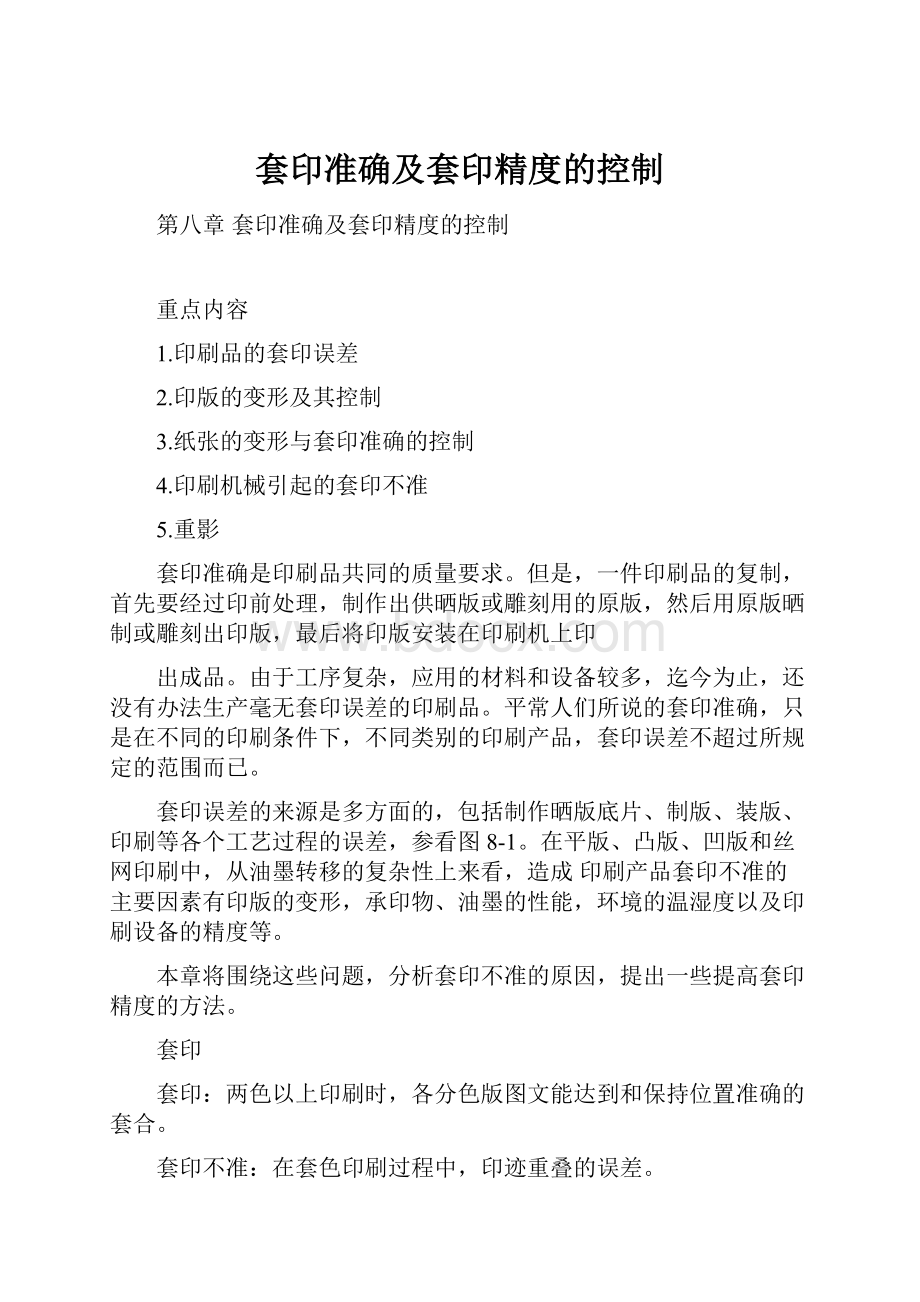
套印准确及套印精度的控制
第八章套印准确及套印精度的控制
重点内容
1.印刷品的套印误差
2.印版的变形及其控制
3.纸张的变形与套印准确的控制
4.印刷机械引起的套印不准
5.重影
套印准确是印刷品共同的质量要求。
但是,一件印刷品的复制,首先要经过印前处理,制作出供晒版或雕刻用的原版,然后用原版晒制或雕刻出印版,最后将印版安装在印刷机上印
出成品。
由于工序复杂,应用的材料和设备较多,迄今为止,还没有办法生产毫无套印误差的印刷品。
平常人们所说的套印准确,只是在不同的印刷条件下,不同类别的印刷产品,套印误差不超过所规定的范围而已。
套印误差的来源是多方面的,包括制作晒版底片、制版、装版、印刷等各个工艺过程的误差,参看图8-1。
在平版、凸版、凹版和丝网印刷中,从油墨转移的复杂性上来看,造成印刷产品套印不准的主要因素有印版的变形,承印物、油墨的性能,环境的温湿度以及印刷设备的精度等。
本章将围绕这些问题,分析套印不准的原因,提出一些提高套印精度的方法。
套印
套印:
两色以上印刷时,各分色版图文能达到和保持位置准确的套合。
套印不准:
在套色印刷过程中,印迹重叠的误差。
套印不准原因的鱼骨图
套印误差多方面,包括底片、制版、装版、印刷等各个工艺过程的误差,参看图8-1。
造成套印不准的主要因素有印版变形,承印物、油墨的性能,环境的温湿度以及印刷设备的精度等。
第一节印刷品的套印误差
一、印刷品套印精度的要求
1.凹印套印精度(允差)(CY/T6-91)
精细印刷品允差一般印刷品允差
部位四开对开全开四开对开全开
主体<0.10<0.15<0.20<0.20<0.30<0.50
一般<0.15<0.20<0.30<0.30<0.40<0.60
主体部位指画面反映主题的部分,如图案、文字、标志
CY/T6-91分类
精细印刷品:
使用高质量原辅材料经精细制版和印刷的印刷品。
一般印刷品:
除上述以外符合相应质量标准的印刷品。
2.平印套印精度(允差)
CY/T5-1999
多色版图像轮廓及位置应准确套合
精细印刷品的套印允许误差≤0.10mm;
一般印刷品的套印允许误差≤0.20mm。
CY/T5-1999分类
(与CY/T6-91相同)
精细印刷品:
使用高质量原辅材料经精细制版和印刷的印刷品。
一般印刷品:
除上述外的符合相应质量要求的印刷品。
3.凸印套印精度(允差)
CY/T4-91
印刷书页中各版面正、反套印准确,其套印允差为:
精细产品小于1.5毫米,
一般产品小于2.5毫米。
CY/T4-91分类
精细产品:
用高质量原辅材料精细加工印制的书刊印刷品。
一般产品:
除上述以外的符合相应质量标准的书刊印刷品。
4.报纸套印精度(允差)
GB/T14705-93
印刷各版幅面,正反套印允差“上下”“左右”不大于2mm。
产品种类双色产品多色产品
主体部位一般部位允差
≤1mm≤0.5mm≤0.7mm
5.柔印套印精度(允差)
纸张印刷品塑料印刷品纸箱印刷品
精细印刷品主要部位:
0.2主要部位:
0.2
<次要部位:
0.3次要部位:
0.31.5
一般印刷品主要部位:
0.3主要部位:
0.3
<次要部位:
0.5次要部位:
0.52
GB/T17497-1998
二、印刷品套印误差的变化规律
套印误差为正态分布
特点:
调准后1.小误差出现多;2.大误差出现少;3.标准误差
S=1/n∑(xd-xi)2(8-2)
三、印刷机的套印误差
印刷机的套印误差
1.续纸套印误差----输纸造成纸张在滚筒上位置差别
2.传纸套印误差----传纸造成纸张在滚筒上位置差别
单色机四色印刷误差
单色机四色印刷:
四次续纸、四次印刷
若,续纸误差0.05mm,则,套印误差0.05mm
印刷机印刷精度(套印精度)取决于续纸,每次续纸误差相同
四色机印刷误差
一次续纸,一个续纸误差,第一色与最后一色无续纸误差
三次传纸,多次交接,传纸误差各不相同
若传纸误差0.03mm,实际套印误差
S1,4=(0.032+0.032+0.032)1/2=0.00271/2=0.052mm
四、定位标记
定位标记:
测定套印准确程度的标记
作用:
检查印刷品上下、左右、斜线方向套印情况
发排时标定印版底片上,印刷后同纸边一起裁掉
印张套印状况
叼口辨认印刷的方向。
前后套印不准多发生在纸尾,叼口部位不发生
左右套印不准,严重的一边是侧挡规对面。
第二节印版的变形及其控制
弯曲变形与拉伸变形
平面印版,安装到滚筒上,发生弯曲变形
紧固时发生拉伸变形
为了提高印刷品的套印精度,必须对印版的这两种变形进行控制。
一、印版的弯曲变形
内层(滚筒面)缩短,外层(图文面)伸长,中间层长度不变,即“中性层”
印版中性层长度等于变形前印版的长度,外层变形最严重
利用系数与伸长量
设印版长度L,厚度b,印版滚筒半径R
K=L/2π(R+b/2)
K印版利用系数,0.6~0.9。
印版版面绝对伸长量ΔL1
ΔL1=[2π(R+b)-2π(R+b/2)]·K=bL/(2R+b)
相对伸长率
ΔL1/L=b/(2R+b)
当b一定时,R小,伸长大
当R一定时,b大,伸长大
多层金属版镀层过厚会绷裂
柔性版、凸版厚,变形量大
高速印刷机滚筒半径小,为控制印版弯曲变形,采用薄版。
二、印版的拉伸变形
张力作用,印版拉伸变形
摩擦力存在,从A、B点到C点,印版各断面轴向应力递减,拉伸变形也递减
A点和B点拉伸变形最大,C点没有变形
印版局部过量变形(靠近A、B)。
三、印版的其它变形
套印不准,要调节印版位置,不正常敲击或拉动印版,产生其它形式变形,甚至使印版断裂
印版轴向移动时,先撤消印版张紧力
印版周向移动时,拉动印版的一端就必须把另一端的张力撤除
四、印刷定位系统
定位系统也叫规位系统,利用定位销和定位孔配合,保证印版在印刷机上获得准确的定位
制版和装版的定位系统。
制版定位系统的定位孔和定位销的排布位置如图8-9所示
装版定位系统定位孔和观察孔排布位置如图8-10所示。
第三节纸张的变形
一、纸张含水量与纸张的变形
纸张的含水量:
纸张含水的重量与该纸张重量之比(百分比)
纸张具有很强的亲水能力
对水有毛细吸附作用
纸张是吸水性很强的材料
水分来源:
纸张接触时吸收水分,从潮湿空气中吸水,向干燥空气中排水
纸张吸水膨胀,尺寸和面积增加,机械强度降低
纸张脱水收缩,尺寸和面积缩小,僵硬发脆
纸张的变形
纸张敏弹性变形有利。
印刷压力作用下被压缩,良好接触,提高油墨转移率。
纸张滞弹性变形对印刷影响不大,不予考虑。
塑性变形引起纸张形状、尺寸变化
1.温度对纸张含水量的影响
一定湿度,温度升高,含水量线性下降
温度变化±5℃,纸张含水量变化±0.15%。
含水量变化超±0.1%影响套印精度
平衡含水量
平衡含水量:
空气中,水蒸气压和纸张中水蒸气压相平衡
印刷车间的温度变化不超过±3℃。
2.相对湿度对纸张含水量的影响
湿度增大,含水量增加,纸张膨胀
不同纸张,同样湿度下含水量不相同,产生的变形量也不相同
(参见表8-1)
3.温度和相对湿度与纸张变形的关系
运输储存,纸张可能发生吸湿或解湿
吸湿纸垛形成“荷叶边”,(a)
解湿纸垛形成紧边,(b)
正、反两面含水不均,纸张卷曲,(c)
纸张含水量与伸长率的关系
干燥纤维完全润湿,直径增加25%~30%,长度增加1%~2%
吸水,纵丝缕纸宽度伸长大,长度伸长小
横丝缕纸长度伸长大,宽度伸长小
荷叶边或紧边纸进印刷机,无法定位
二、纸张的滞后效应和调湿处理
1.纸张的滞后效应
含水量高(解湿)纸张和含水量低(吸湿)同样湿度达到平衡,那么,高含水量纸张含水量仍高
一旦吸湿,即使再回到原来湿度环境,含水量也提高。
2.纸张的调湿处理
(1)调湿目的
①降低对水敏感程度,减少变形----润湿液,边吸湿边解湿
纸张反复吸湿、解湿,水分变化越来越小(滞后效应)
②降低静电,防电击火灾----中和离子
(2)调湿方法
①自然调湿法
纸张吊晾在车间,纸张含水量与车间的湿度平衡。
纸张调湿一般是吸湿过程,吸湿时间较长。
调湿方法
②强迫调湿法
将纸张吊晾在晾纸机或晾纸间的圆形晾纸机架上,再吹送调温调湿的空气。
吹送空气温度比印刷车间高10~15℃,相对湿度比印刷车间高10%~20%
套印精度不高,吊晾2~3天
套印精度较高,吊晾3~5天
纸张吹松,空气充分接触,只需2~3h
印刷过程中纸张含水量的变化
(1)
A:
未调湿,含水低,车间吸湿,滞后效应,含水仍低,印刷中大量吸水,变形大,套印不准
B:
自然调湿,印刷前,含水已到一定水平;印刷开始,少量吸湿,变形较小
印刷过程中张含水量的变化
(2)
C:
强迫调湿,含水较高,车间解湿,滞后效应,含水仍高,印刷中边吸湿边解湿,含水量几乎不变,变形很小。
第四节印刷机械引起的套印不准
一、纸张的定位与套印不准
1.定位与递纸
纸张前端到达前规时,前规落下定位
纸张碰到前规停止前进,侧规纸张拉到定位位置
定位后,递纸牙把纸张叼起来,前规抬起,纸张被递给压印滚筒上叼纸牙
2.影响套印不准因素
(1)前规、侧规磨损
纸张位置变化,套印不准
(2)纸张精度
纸张尺寸精度和垂直度。
不成直角,纸张会倾斜,图像倾斜。
(3)堆码不齐
产生位置误差
二、叼纸牙叼力和交接关系对套印的影响
1.叼纸牙叼力与套印
叼纸牙叼力不均匀,纸张的直线尺寸均被改变,印刷品必生局部套印不准
2.叼纸牙交接关系与套印
单色印刷机,从递纸到印完一色,两次交接
多色机印刷,交接次数多
交接过程中,可能造成叼口位置改变,套印不准。
递纸牙垫、给纸铁台与压印滚筒三者保持一定距离,叼牙高度一致。
纸张叼口不出现波浪形,叼口尺寸合适。
三、印刷压力、纸张剥离张力与套印不准的关系
1.印刷压力与纸张的变形
较大印刷压力,宽度和拖梢两角的长度有微量扩展,所谓扇形变形,套印不准,拖梢部分严重
压力大,变形大,同一批每色压力应一致
纸张纵向丝缕和滚筒轴向平行,同一批丝缕方相同
2.剥离张力与纸张的变形
剥离张力:
纸张克服油墨粘着力,离开印版或橡皮布的作用力。
由叼纸牙施加
剥离张力大,纸张变形增加,纸张被拉长,套印精度下降
第五节滚筒衬垫厚度对图文尺寸的影响
一、滚筒半径与图文尺寸的关系
1.设:
三滚筒半径相同,为R,L排列
假定图文分布1/4周
角速度相同,同时转过90º
印版图文与承印物印迹同为1/2πR
图文印迹不变
2.压印滚筒半径R-a1
转过90º
印版图文长度1/2πR
承印物印迹长度1/2πR-1/2πa1
承印物印迹缩短了1/2πa1
3.印版滚筒半径R-a2
转过90º
印版图文长度1/2πR-1/2πa2
承印物印迹长度1/2πR
承印物印迹伸长了1/2πa2
二、印版衬垫增减与图文尺寸的关系
传动比1∶1,等角速度转动,印刷角α(印版图文包角,)相等
α=L版/R版=L橡/R橡=L压/R压
印版转到橡皮布图文宽
L橡=L版·R橡/R版
橡皮布到承印物图文
L压=L橡·R压/R橡
L压=L版·R压/R版
承印物上图文宽度与印版和压印两滚筒的半径、印版上的图文宽度有关,而与橡皮滚筒无关
橡皮滚筒仅起转印图文的作用,如半径小,印迹短,再转印变长
橡皮滚筒过大过小,图文变形,网点扩大
结论
1.印版滚筒衬垫增加,承印物上图文宽度比印版上原有图文宽度减小
2.利用增减印版滚筒包衬厚度,适当控制印刷图文长度变化
3.滚筒系统直径的关系受滚筒配置理论制约,包衬厚度可调范围一般很小。
第六节重影
重影
1.定义:
重影又叫双影,指印刷的线条旁边出现的浅线条或印刷网点旁边出现的侧影
2.重影危害
重影使细线条发粗,原来的网点变成一粒半或两粒,整个印刷品的图文模糊,清晰度明显下降。
一、重影的产生与类别
1.产生
平版印刷,P、B之间微小位移,对应质点不重合
橡皮布上一次转移剩余墨层,不能与本次转移墨层完全重合,本次墨层深迹,剩余墨层浅迹,深浅墨迹,同时出现,形成重影
2.重影类型
重影类型:
纵向、横向和A、B重影
纵向重影,也叫上下重影:
网点虚影在原网点上、下端
横向重影,也叫来去重影:
网点虚影在原网点的左右侧
A、B重影
A、B重影:
多色胶印湿压湿,前一纸张留在后一色橡皮布上墨迹不重合,后印纸张网点旁边出现虚影。
有的在原网点上、下侧,有的在原网点左右侧。
二、产生重影的原因与排除方法
1.纵向重影
(2)配合间隙过大
滚筒轴颈与轴套、偏心套与墙板孔的配合间隙过大,运转中产生振动,角速度不均匀,每次不能在相同位置接触,出现重影
排除:
滚筒轴套配合间隙0.01~0.02mm
(2)侧隙及径向跳动量过大
滚筒齿轮侧隙及径向跳动量过大。
齿轮磨损,齿厚减小,侧隙增大,运转不均匀,产生滚筒间瞬时相对位移,出现重影。
排除:
更换磨损严重齿轮或轴承调;适当缩小中心距,减小侧隙
(3)滚筒包衬不当
滚筒包衬不当,压力过大,表面线速度不一致,过量挤压,橡皮布变形位移,出现重影
排除:
采取正确合理的包衬
(4)交接不准
多色胶印机各机组相互交接不准。
先印印迹转移到后色橡皮布表面,墨迹发生位移,引起重影
排除:
滚筒间交接位置精确,不能松动或磨损
2.横向重影
(1)叼纸牙轴轴向串动
叼纸牙轴串动,传纸不准,纸张位移,产生重影
排除:
调整轴两头紧圈和轴套端面间隙
(2)滚筒轴向位移
滚筒轴向位移,墨迹转移不重合,产生重影
排除:
轴向串动量不超过0.03mm,调整止推轴承
3.A、B重影
机器原因,倍径传纸滚筒两咬牙精度不够。
A、B两组纸网点不在后印橡皮布上重合,产生A、B重影。
A、B重影以此得名
工艺问题,牙垫磨损,精度下降。