实用工艺过程危险有害因素的分析报告.docx
《实用工艺过程危险有害因素的分析报告.docx》由会员分享,可在线阅读,更多相关《实用工艺过程危险有害因素的分析报告.docx(104页珍藏版)》请在冰豆网上搜索。
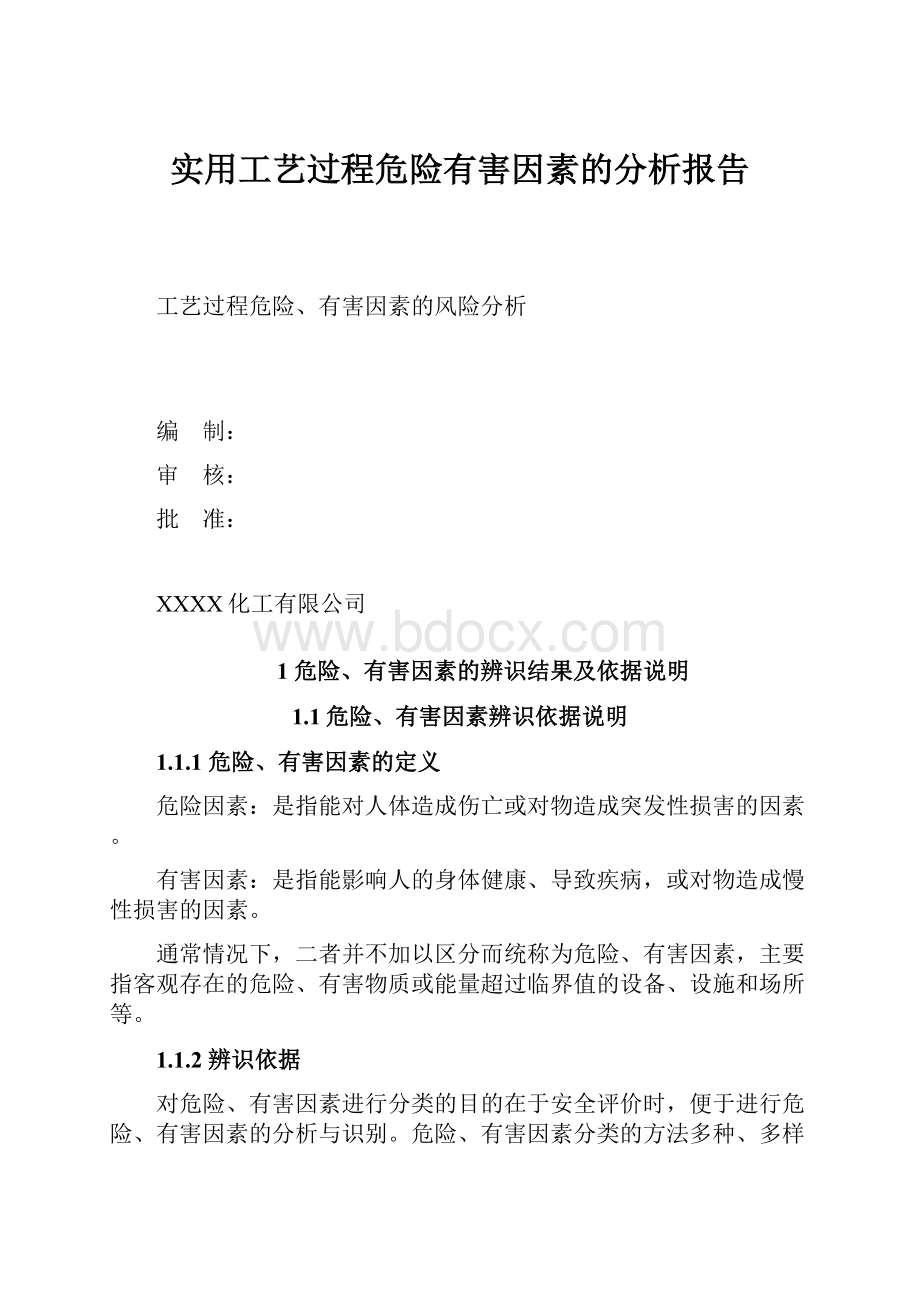
实用工艺过程危险有害因素的分析报告
工艺过程危险、有害因素的风险分析
编 制:
审 核:
批 准:
XXXX化工有限公司
1危险、有害因素的辨识结果及依据说明
1.1危险、有害因素辨识依据说明
1.1.1危险、有害因素的定义
危险因素:
是指能对人体造成伤亡或对物造成突发性损害的因素。
有害因素:
是指能影响人的身体健康、导致疾病,或对物造成慢性损害的因素。
通常情况下,二者并不加以区分而统称为危险、有害因素,主要指客观存在的危险、有害物质或能量超过临界值的设备、设施和场所等。
1.1.2辨识依据
对危险、有害因素进行分类的目的在于安全评价时,便于进行危险、有害因素的分析与识别。
危险、有害因素分类的方法多种、多样,参照《企业职工伤亡事故分类》(GB6441-1986)分类标准作为危险、有害因素辨识依据。
1.2物料的危险有害因素辨识结果
工艺过程涉及的主要物料有产品氧气、液氧、氮气、液氮、液氩、氩气,原料为空气。
各物质理化性质及危险特性见附录。
工艺过程所涉及到的物料按其危险、有害特性来分,可分为下述几类:
(1)根据《危险化学品目录(2015年版)》属危险化学品物质有:
氧气、液氧、氮气、液氮、氩气、液氩。
(2)根据《危险化学品目录(2015年版)》工艺过程无剧毒化学品物质。
(3)根据《高毒物品目录》(2003版)工艺过程无高毒物品。
(4)根据《中华人民共和国监控化学品管理条例》(国务院令第190号)工艺过程无监控化学品。
(5)根据《易制毒化学品分类目录》工艺过程无易制毒化学品。
(6)按照HG20660-2000毒性危害分级划分:
压缩空气、氧气、液氧、氮气、液氮、氩气、液氩属轻度危害物质。
(7)根据《建筑设计防火规范》(GB50016-2014):
压缩空气、氧气、液氧火灾危险性为乙类;氮气、液氮、氩气、液氩火灾危险性为戊类。
(8)按照《压力容器中化学介质毒性危害和爆炸危险程度分类》(HG20660-2000)工艺过程无爆炸性介质。
(9)根据《危险货物品名表》(GB12268-2012),工艺过程无第8类腐蚀性物品。
主要危险、有害物质危险特性见表1-1。
表1-1主要危险、有害物质危险特性
类别
序号
名称
主要危
险特性
火灾
危险性
UN号
产品
1
氧气
助燃
乙
1072
2
液氧
助燃
乙
1073
3
氮气
不燃
戊
1046
4
液氮
不燃
戊
1977
5
氩气
不燃
戊
1006
6
液氩
不燃
戊
1951
1.3生产过程的危险有害因素辨识结果
1.3.1生产工艺过程中危险有害因素辨识分析
(1)空气过滤、压缩、预冷、净化单元
净化是除去空气中的水份、二氧化碳、乙炔、乙烯、丙烯等碳氢化合物,如果使用过期、失效的分子筛或切换程序有误,同时分子筛出口的分析仪表出现问题,会造成乙炔等碳氢化合物进入系统,碳氢化合物在液氧中积聚且液氧没有达到安全排放量,在主冷位置容易发生爆炸。
乙炔在液氧中溶解度很低,因而易析出、积聚。
乙炔的爆炸敏感度很大,最小引燃能只有0.019mJ。
乙炔的爆炸范围宽、危险性大,是上述物质中危险性最大的。
乙炔在液氧中与氧反应能发生爆炸(乙炔在无氧情况下分解爆炸;乙炔于氧气中的燃烧爆炸;固体乙炔析出,液氧、碳氢化合物固态析出,在系统中形成爆炸性混合物,在冲击摩擦或静电等引爆源下引起爆炸)。
分子筛再生时使用高温氮气(最高温度290℃),加温用蒸汽、高温氮气泄漏会造成人员灼烫,人员进入高浓度氮气环境会造成窒息,再生效果不佳会降低分子筛性能,使危害气体进入系统,有造成爆炸事故的可能。
(2)空分精馏单元
如果自动调节系统失灵或事故状态下不及时泄压,超过设备、管道承载能力有可能会发生爆炸。
当空分装置发生氧气泄漏或检修时未置换或置换不彻底,如作业环境附近有油脂等极易发生火灾事故。
空分装置使用的透平油和润滑油及其分解产物泄漏遇富氧或泄漏的氧会发生火灾、爆炸。
(3)其他
空分制氧装置中的液氧、液氮、液氩属低温产品,如果输送这些产品的泵、阀门、管道因故障或人为失误导致泄漏,接触到操作人员身体,有造成人体冻伤的可能;
高压气体泄漏会产生噪声伤害,氧气排空、泄漏,液氧泄漏会造成富氧区,人员吸入会造成氧中毒,氮气、氩气排空、泄漏,液氮、液氩泄漏会造成缺氧区,人员在缺氧会造成窒息;如氧气、液氧输送管道内有电焊渣等,固体杂物与管道摩擦有造成火灾、爆炸的可能。
1.3.2主要设备和设施危险有害因素辨识分析
(1)空气过滤、压缩、预冷、净化单元
该单元主要设备有空气过滤器、空气压缩机、空冷塔、冷冻水泵、冷水机组、循环水泵、分子筛、再生蒸汽加热器等。
空气压缩机高速旋转,产生噪声,对人体和环境造成伤害。
空气压缩机因电线老化,绝缘失效、短路、超载等有造成人员触电伤害的可能。
空气压缩机电机、联轴器、旋转部位,因防护不当或失效,操作人员,检修人员检修(包括衣物、长发)发生卷入、碰撞、碾绞等机械伤害。
空气压缩机、空气过滤器设备高大,检修人员巡检、检修时,其梯子、护栏、平台失稳或损坏(工、器具、结构体等下落)会造成高处坠落和物体打击伤害。
空气压缩机内压力0.625MPa,压缩机故障或操作不当超载运行,会引发爆炸事故。
冷冻水泵、冷水机组、循环水泵运行中产生噪声对人体和环境造成噪声伤害。
冷冻水泵、冷水机组、循环水泵、空冷塔其电线老化、短路、绝缘不良,电机故障等会造成触电伤害。
冷冻水泵、冷水机组、循环水泵的旋转部位,联轴器,防护不当或失效,易产生卷入等机械伤害。
冷水机组、双级空冷塔等高大设备,检修人员巡检、检修时,操作因梯子、护栏、平台损坏或失稳(工、器具、组装件等下落)会造成高处坠落和物体打击伤害。
再生蒸汽加热器、再生电加热器的水蒸汽,在1.0MPa压力下,其温度达190℃。
蒸汽一旦泄漏,易造成人体灼烫伤害。
再生电加热器,因电器原件老化、电线老化、绝缘不良、短路等易造成触电伤害。
(2)空分精馏单元
该单元主要设备包括主换热器、过冷器、主冷凝蒸发器、中压塔、低压塔、纯氮塔、透平膨胀机、液体膨胀机等。
透平膨胀机,其高速旋转会产生噪声,对人体和环境造成噪声危害,易发生卷入等机械伤害。
主换热器、过冷器、主冷凝蒸发器、中压塔、低压塔是压力容器,如安全附件失效,压力自动调节系统失灵,会造成容器超压失控,引起容器爆炸伤害。
空分装置发生液氧外泄与可燃物形成爆炸体系,可发生塔外爆炸,空分装置氧气外泄、或氧气罐内检修时置换不净,遇明火,高温和可燃物易发生火灾伤害。
检修中冷箱封盖忘关或栅栏式盖子损坏、未设围栏等,人容易掉进松散珍珠砂中会造成窒息伤害或死亡。
(3)氧气、氮气压缩单元
该单元主要设备有氧压机、氮压机等。
氧压机、氮压机高速旋转,产生噪声,对人体和环境造成伤害。
氧压机、氮压机因电线老化,绝缘失效、短路、超载等有造成人员触电伤害的可能。
氧压机、氮压机电机、联轴器、旋转部位,因防护不当或失效,操作人员,检修人员检修(包括衣物、长发)发生卷入、碰撞、碾绞等机械伤害。
氧压机、氮压机设备高大,检修人员巡检、检修时,其梯子、护栏、平台失稳或损坏(工、器具、结构体等下落)会造成高处坠落和物体打击伤害。
氧压机、氮压机内压力2.3MPa,压缩机故障或操作不当超载运行,会引发爆炸事故。
氧压机在运行中,如发生气缸温度高;活塞环、气封、密闭件材质存在问题;运行中发生机械磨损;气缸内带入杂物等故障,若处理不及时,可损坏氧压机,严重时也可发生气缸爆炸。
氧压机运行中如发生泄漏,泄漏的氧气进入油箱,是极其危险的,往往造成重大火灾、爆炸事故。
(4)其他
压力容器自动调节系统失控,造成设备超压,有造成容器爆炸可能。
压缩机、泵运运行中产生噪声,对人体和环境造成噪声危害。
用电设备电机故障,电源线老化,绝缘失效,短路等易造成触电伤害。
压缩机、泵等设备转动部位防护不当,或失效,易会造成卷入等机械伤害。
低温设备故障泄露,液体产品有造成人员冻伤的可能。
工艺过程温度最低为-190℃,如果设备材料防冷脆措施不当有造成设备破裂,物料泄漏的危险。
1.3.3特种设备危险有害因素辨识分析
工艺过程涉及到的特种设备有:
压力容器、压力管道、桥式起重机、气瓶。
(1)压力容器
压力容器质量不好或在生产过程中如果安全附件损坏、失效或不全有造成容器超压,严重时会造成容器破裂,破裂产生的碎片四处飞散,人员防护不当有造成人员伤害的危险,容器破裂物料泄漏,液氧、氧气泄漏遇可燃物有发生火灾的危险,氮、氩泄漏现场通风不好有造成人员窒息的危险,另外还有冻伤等危险。
(2)压力管道
压力管道质量不好、安全附件不全、失效或损坏有造成管道破裂的危险;管道破裂物料泄漏,氧泄漏遇可燃物会造成火灾,人员氧中毒,氮氩泄漏有造成人员窒息危险,液化气体泄漏有造成人员冻伤的危险;压缩气体泄漏会产生噪声,蒸汽泄漏会造成灼烫伤害。
(3)桥式起重机
桥式起重机属起重机械,提升物料、设备时如固定不好等操作不当有造成起重伤害的危险,维护不当,钢丝绳等长时间使用质量变差,起重重物时超负荷使用有造成起重伤害的危险。
(4)气瓶
氧气瓶、氮气瓶、氩气瓶不合格会有爆炸危险。
氧气瓶在充装过程中,如果操作失误或有油脂类等杂质进入瓶内,或钢瓶本身质量缺陷及腐蚀毁损,或充装过快等因素引起破裂,会造成火灾、爆炸等危险。
(5)其他
以上各特种设备操作属特种作业,操作人员如无操作证或操作证过期,违规上岗,也会因操作不熟练或违规操作造成事故。
1.4物料贮存、装卸、输送过程危险、有害因素分析
1.4.1储运、装卸、输送工艺过程危险有害因素分析
(1)液氧储存
液氧储罐
来自空分装置的过冷液氧通过管道进入液氧储槽。
该过程存在的危险、有害因素是:
如液氧储罐投入使用前,未清理或清理不彻底有造成火灾爆炸事故的危险;
液位显示不准有造成储罐储存超量,液氧泄漏有造成火灾、爆炸、人员中毒、冻伤的可能;
液氧储罐液氧中乙炔量超标,有造成火灾爆炸的危险;如果阀门、管道及储罐因故障或人为失误导致泄漏,接触到操作人员身体,有造成人体冻伤的可能;
液氧泄漏会造成周围富氧,人员吸入高浓度富氧空气会造成氧中毒。
如因各种原因造成液氧储槽压力升高,超过空分装置压力会造成液氧返回空分装置,造成事故。
工艺过程液态储罐为平底罐,如液化气体长时间储存,内部物料温度逐步升高,一旦超过沸点就会起压,使储罐成为受压容器,导致焊缝损坏,物料泄漏,有造成火灾、爆炸,人员冻伤的危险。
液氧灌装
当液氧外卖时采用槽车运输,该过程存在的危险、有害因素是:
车辆进入乙类场所时如未戴阻火器有引发火灾爆炸的可能,车辆行使、中转过程中如司机精力不集中,疲劳驾驶,超速行驶,车辆超载有造成人员车辆伤害的可能。
槽车安全附件不全或失灵有造成事故的危险;
如果首次投入使用的槽车清理不彻底,未采取预冷措施,有造成事故的危险;
槽车充装量超过要求量有造成事故的危险;装卸用接头混用有造成事故的危险;
如果装车时,不接静电接地线及时将产生的静电引入大地,可造成静电积聚并放电,有引发火灾爆炸的危险;
装车过程中如果发生液氧泄漏,现场操作人员又穿着化纤衣物或衣物上沾染有油脂,或现场环境中存在可燃性物质,就可能导致燃爆事故,同时,运输液氧的槽(罐)车属移动式压力容器,如果超量充装或超压有爆炸的危险。
槽车充装时未熄火、充装其他物质的槽车运输液氧也有造成事故的危险。
液氧汽化
液氧气化体积膨胀,控制不好有造成汽化器破裂的危险;
汽化器选择不当、液氧输送速度太快,造成氧气携带液氧,液氧进入氧气管道后,液氧汽化体积膨胀会造成输出氧气压力升高,有造成管道破裂的危险;
液氧气化中液氧等会造成管道冷脆。
管道
输送物料的管道,如果管架间距大,会造成管道下坠,严重时会造成管道折断,管道排空阀泄漏,管道设计不合理,如无防膨胀措施、管道与电缆共同、平行敷设、管道防静电措施不当或无防静电措施等都有造成火灾爆炸、人员冻伤、中毒窒息的危险。
液氧管道保温层损坏或未保温,人员接触管道有造成冻伤的危险;
夏季气温升高,液氧挥发速度加快,有造成管道超压破裂的危险。
如氧气、液氧输送管道内有电焊渣等且氧气、液氧中有乙炔等,固体杂物与管道摩擦有造成火灾、爆炸的可能。
输氧管道及管件有油脂、溶剂和橡胶等可燃物质,急开或速闭阀门,易发生着火灾、爆炸。
(2)氧气储存
氧气储存实际是缓冲过程,该过程存在的危险、有害因素是:
当氧气管网压力高时向氧气球罐输送氧气,由于球罐压力表失灵有可能发生球罐超压破裂;
在向氧气球罐或向管网输送氧气时,阀门切换失误,有造成输送管道破裂的危险。
关于管道的其他危险有害因素见“
(1)
管道”。
(3)液氮储存
液氮储罐
来自空分装置的过冷液氮用真空管道通入液氮储罐。
该过程存在的危险、有害因素是:
液氮属低温产品,如果泵、阀门、管道及储罐因故障或人为失误导致泄漏,接触到操作人员身体,有造成人体冻伤的可能;
氮气泄漏会对人员产生噪声伤害,氮气排空、泄漏,液氮泄漏会造成缺氧区,人员进入缺氧环境有造成造成窒息的可能;
泵等机械设备对人员还存在机械伤害、噪声危害
液位显示不准有造成储罐储存超量的危险,液体储罐使用过程中夹层真空度低,会影响储罐隔热效果,有造成储罐超压的危险;
如因各种原因造成液氮储槽压力升高,超过空分装置压力会造成液氮返回空分装置,造成事故。
液氮灌装
当液氮外卖时采用槽车运输,该过程存在的危险、有害因素是:
车辆进入乙类场所时如未戴阻火器有引发火灾爆炸的可能,车辆行使、中转过程中如司机精力不集中,疲劳驾驶,超速行驶,车辆超载有造成人员车辆伤害的可能。
槽车安全附件不全或失灵有造成事故的危险;
如果首次投入使用的槽车清理不彻底,未采取预冷措施,有造成事故的危险;
槽车充装量超过要求量有造成事故的危险;
装卸用接头混用有造成事故的危险;
运输液氮的槽(罐)车属移动式压力容器,如果超量充装或超压有爆炸的危险。
液氮汽化
液氮气化体积膨胀,控制不好有造成汽化器破裂的危险;
汽化器选择不当、液氮输送速度太快,造成氮气携带液氮,液氮进入氮气管道后,液氮汽化体积膨胀会造成输出氮气压力升高,有造成管道破裂的危险。
管道
输送物料的管道,如果管架间距大,会造成管道下坠,严重时会造成管道折断,管道排空阀泄漏,管道设计不合理,如无防膨胀措施有造成管道破裂,人员冻伤、窒息的危险。
液氮管道保温层损坏或未保温,人员接触管道有造成冻伤的危险;
夏季气温升高,液氮挥发速度加快,有造成管道超压破裂的危险。
(4)氮气储存
氮气储存实际是缓冲过程,该过程存在的危险、有害因素是:
当氮气管网压力高时向氮气球罐输送氮气,该过程有发生球罐超压破裂的危险;当管网压力低时,向管网输出氮气,该过程有造成管道破裂的危险;在向氮气球罐或向管网输送氮气时,阀门切换失误,有造成输送管道破裂的危险。
关于管道的其他危险有害因素见“(3)
管道”。
(5)液氩储存
液氩储存与液氮储存危险有害因素相近,见“(3)液氮储存”。
(6)氩气储存
氩气储存危险有害因素见“(4)氮气储存”。
(7)管道系统
工艺过程有氧气管道、氮气管道、氩气管道,其危险、有害因素分析如下:
超压的物料进入管道有造成管道破裂的危险;
氧气管道防静电措施不当或无防静电措施有造成火灾、爆炸的危险;
如果氧气进入输送氮、氩的管道或氮、氩进入其他气体的输送管道有造成火灾爆炸的危险。
管道管件选材不合理、管道设计不合规、管道安装不规范、管道验收不规范都要造成事故的危险。
低温管道保温层损坏或未保温,人员接触管道有造成冻伤的危险;
夏季气温升高,液氧挥发速度加快,有造成管道超压破裂的危险。
如氧气、液氧输送管道内有电焊渣等且氧气、液氧中有乙炔等,固体杂物与管道摩擦有造成火灾、爆炸的可能。
输氧管道及管件有油脂、溶剂和橡胶等可燃物质,急开或速闭阀门,易发生着火灾、爆炸。
埋地管道防腐蚀措施不当或无防腐蚀措施,时间久了管道受腐蚀管壁变薄,承压能力降低,有造成管道破裂的危险。
1.4.2储运设备存在的危险、有害因素分析
泵类
泵类无安全装置或安全装置不全,当运转时人员的衣物等被绞入会造成人员机械伤害;
其运转时产生噪声,人员长时间在噪声场所工作,会产生噪声伤害;
液氧泵的选型不当,有造成火灾爆炸的可能;
如无防静电、漏电措施或防静电、漏电措施不当有造成火灾爆炸的可能;人员接触带电体会造成触电伤害;
泵密封不好造成液氧、液氮、液氩泄漏有造成火灾爆炸、人员冻伤、窒息的危险。
储罐
a、液态储槽
储槽制作不按相关程序进行,造成储存质量不合格,如果绝热层未达到规范要求就投入使用,会使储槽隔热效果不好,液空挥发产生气体,体积膨胀、安全阀、压力表失灵,造成储槽压力升高,当超过储罐承压时要造成储罐破裂的危险;罐与其他设备及管线连接处如密封不严,可能造成物料泄漏,液空泄漏会造成火灾、爆炸,人员冻伤的危险,阀门等附件如有缺陷,人员误操作,可造成液氧泄漏,有造成人员冻伤、发生火灾爆炸的可能。
工艺过程液空储罐较大,基础制作不好,发生下沉,有造成储罐倾斜物料泄漏,发生火灾、爆炸,人员冻伤的危险;
b、气体球罐
球罐属压力容器如果设计、制造、安装不按相关程序进行,造成质量不合格,投入使用后有发生破裂的危险。
球罐安全附件不全或失效当超压时,有造成容器破裂的危险。
夏季气温高如果不采取降温措施,气温升高压力升高,如果安全附件失效,有造成容器破裂的危险;
球罐长时间使用,受空气腐蚀等,会造成罐壁变薄,承压能力下降,当达到一定程度时,有发生容器破裂的危险。
未定期对球罐安全附件进行检验,造成安全附件失效有造成容器破裂的危险。
电器设备
工艺过程生产过程中使用电器设备,如电气线路由于短路、负荷过载、接地电阻值大、导线绝缘损坏、漏电等会造成过热而引发火灾。
管道
管道危险有害因素分析见1.4.1。
1.5公用系统辅助设施危险有害因素分析
公用系统包括变配电、供蒸汽、制冷、循环水等,存在的危险有害因素如下。
(1)电气系统
电气系统危险、危害因素分为两类:
一类是自然灾害如雷击;
另一类是电气设备本身和运行过程中不安全因素导致的危险、危害。
电气系统如绝缘不良、违章操作、防雷措施不当等原因,有发生触电的危险。
短路、过电压、接触不良等原因,可产生电气火花、电弧或过热,可能发生电气火灾事故。
电工高处作业过程时,如违章操作、防护品使用不当等原因不当易造成高处坠落事故。
(2)供热系统
工艺过程的蒸汽管道如超压,管道爆裂有造成人员灼烫的危险。
(3)给排水系统
工艺过程循环水池及消防水池如防护不当,人员意外掉落废水池,可能发生淹溺危险。
循环水池泵的机械运动带有危险性,如果人员违章、防护不当或机械故障等原因会产生机械伤害事故。
(4)制冷系统
制冷系统的温度较低,系统中的低温液体泄漏,如果人员违章、躲闪不及易发生低温伤害。
制冷机组的运转部件有一定的危险性,如人员违章或防护设施不当,有产生机械伤害的危险。
1.6工艺过程所涉及的危险、有害因素及其分布
1.6.1工艺过程可能造成爆炸、火灾、中毒、灼烫事故的危险、有害因素及其分布
工艺过程可能造成爆炸、火灾、中毒、灼烫危险、有害因素分布见表1-2。
表1-2爆炸、火灾、中毒、灼烫危险、有害因素分布表
序号
危险、有害因素
涉及的物质、设备设施或原因
主要分布区域
备注
1
爆炸
碳氢化合物在液氧中积聚
空分装置、罐区
2
容器爆炸
压力容器、压力管道
空分装置、罐区
3
火灾
氧遇可燃物等
空分装置、罐区
4
中毒、窒息
氧、氮、氩含量过高
空分装置、罐区
5
灼烫
蒸汽,高温设备、管道表面
空分装置
1.6.2工艺过程可能造成作业人员伤亡的其它危险、有害因素及其分布
工艺过程可能造成的其他的作业人员伤亡的危险、有害因素有噪声、触电、机械伤害、高处坠落、物体打击、冻伤、淹溺、起重伤害等。
表1-3其他危险、有害因素分布表
序号
危险、有害因素
涉及的物质、设备设施或原因
主要分布区域
备注
1
机械伤害
设备旋转或振动部位防护设施不全
空分装置、罐区、循环水等
2
触电
电器、变配电设施、用电设备、发电机等
空分装置、罐区、循环水、变电所等
3
振动和噪声
减震、降噪设施不良,带压气体泄漏
空分装置、罐区、循环水等
4
起重伤害
桥式起重机
泵房
5
物体打击
活动物体坠落或飞散物接触人员
空分装置、罐区等
6
车辆伤害
运输机动车辆伤害人员
厂区
7
高处坠落
高处作业引起
空分装置、罐区等
8
淹溺
人员坠落入水池
循环水冷却塔水池
9
冻伤
冷冻机、低温液体
冷冻机、罐区、空分装置
1.7危险化学品重大危险源辨识
1.7.1按照《危险化学品重大危险源辨识》(GB18218-2009)辨识
(1)危险化学品重大危险源辨识依据
重大危险源,是指长期地或临时地生产、加工、搬运、使用或贮存危险物质,且危险物质的数量等于或超过临界量的单元。
重大危险源的辨识依据,是物质的危险特性及其数量。
重大危险源分为生产场所重大危险源和贮存区重大危险源两种。
根据国家标准《危险化学品重大危险源辨识》(GB18218-2009)的规定,对该项目危险物质的主要生产场所、贮存区进行危险化学品重大危险源辨识。
重大危险源是以《危险化学品重大危险源辨识》(GB18218-2009)中规定的危险物质品名及其临界量来确定的。
①当单元内存在的危险物质为单一品种,且物质的数量等于或超过相应的临界量时,则该单元定为重大危险源。
②当单元内存在的危险物质为多品种时,则按以下算式进行计算,若满足该算式,则定为重大危险源。
q1/Q1+q2/Q2+…+qn/Qn≥1
式中:
为每种物质实际存量(t),
Q1、Q2…Qn为与各种危险物相对应的临界量(t)。
(2)危险化学品重大危险源辨识
根据《危险化学品重大危险源辨识》(GB18218-2009)标准,工艺过程无危险化学品重大危险源辨识物质,所以未构成重大危险源。
2)重大危险源辨识分析
对照《危险化学品重大危险源辨识》(GB18218-2009)中危险物质名称及其临界量标准,本项目的氧属于重大危险源物质。
公司有400m3氧气球罐1个,储存氧气17.1t;500m3液氧贮槽3个,每个贮槽可储存液氧484.5t。
表1-4危险物质临界量表
物质名称
临界量(吨)
实际量(吨)
备注
液氧
200
1470.6
计算如下:
1470.6/200=7.353>1
因此,该公司构成重大危险源。
根据《危险化学品重大危险源辨识》(GBl8218-2009)标准规定,公司构成重大危险源。
重大危险源区域设有监控装置,已进行登记备案,并进行重大危险源的专项评估,取得重大危险源备案证明。
其重大危险源的管理符合相关安全生产法律、法规及标准规定要求。
3)重大危险源分级
(1)分级指标
采用单元内各种危险化学品实际存在(在线)量与其在《危险化学品重大危险源辨识》(GB18218)中规定的临界量比值,经校正系数校正后的比值之和R作为分级指标。
(2)R的计算方法
式中:
q1,q2,…,qn—每种危险化学品