起重机钢结构焊接通用技术条件.docx
《起重机钢结构焊接通用技术条件.docx》由会员分享,可在线阅读,更多相关《起重机钢结构焊接通用技术条件.docx(16页珍藏版)》请在冰豆网上搜索。
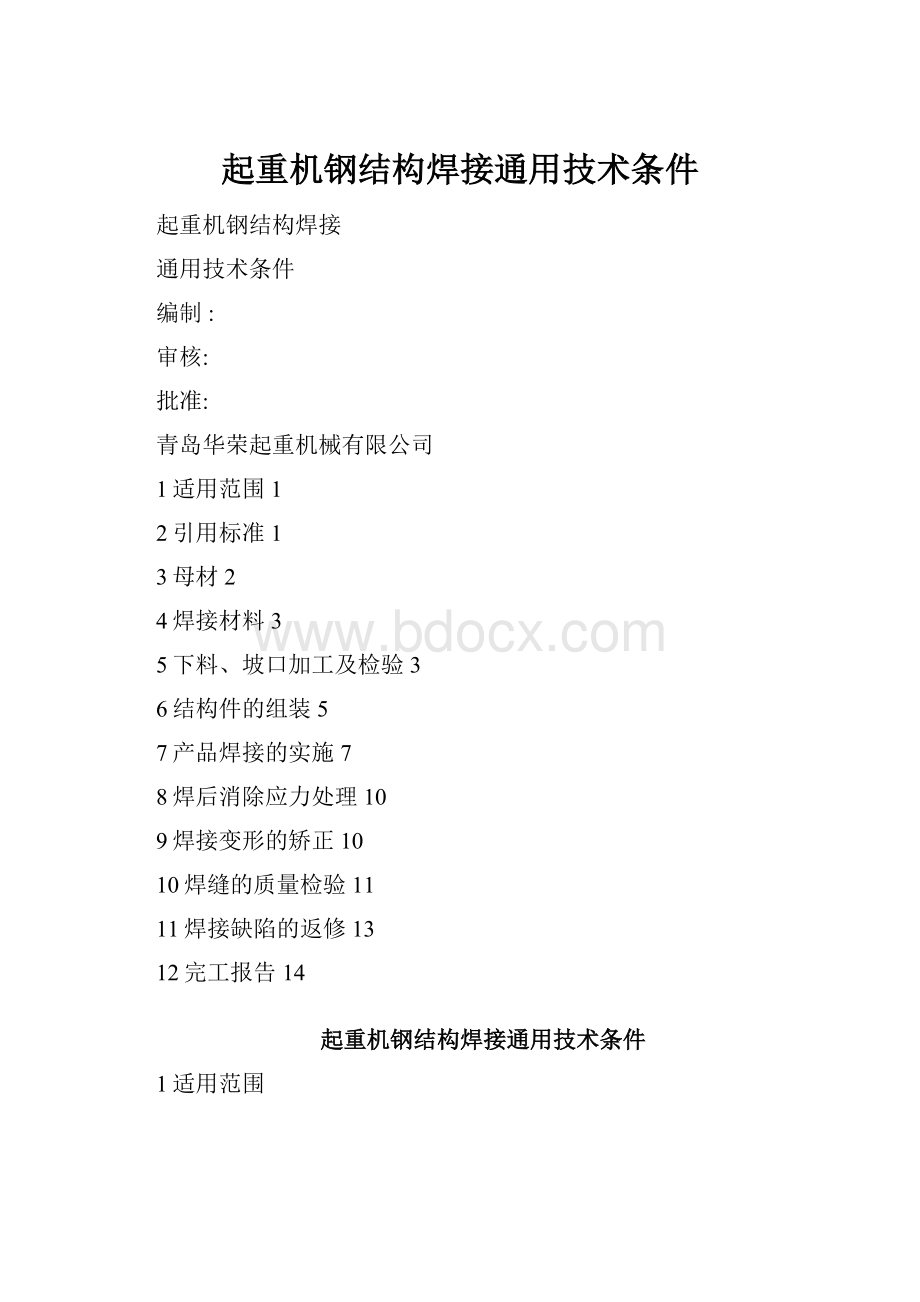
起重机钢结构焊接通用技术条件
起重机钢结构焊接
通用技术条件
编制:
审核:
批准:
青岛华荣起重机械有限公司
1适用范围1
2引用标准1
3母材2
4焊接材料3
5下料、坡口加工及检验3
6结构件的组装5
7产品焊接的实施7
8焊后消除应力处理10
9焊接变形的矫正10
10焊缝的质量检验11
11焊接缺陷的返修13
12完工报告14
起重机钢结构焊接通用技术条件
1适用范围
1.1本技术条件规定了青岛华荣起重机械有限公司生产的碳钢和低合金高强钢起重机钢结构焊条电弧焊、气体保护焊和埋弧焊的技术要求。
1.2本技术条件适用于《特种设备安全监察条例》中规定的起重机械。
对于其它类型的起重设备也可参照执行。
1.3除本技术条件规定外,如有特殊要求应按图样和专用技术条件执行。
2相关标准
GB3811-2008
起重机设计规范
GB6067.1-2010
起重机安全规程第1部分:
总则
GB/T14405-2011
通用桥式起重机
GB/T14406-2011
通用门式起重机
GB/T17495-2009
港口门座起重机
GB/T15361-2009
岸边集装箱起重机
GB/T19683-2005
轨道式集装箱门式起重机
JB/T5000.1-2007
重型机械通用技术条件
第1部分:
产品检验
JB/T5000.2-2007
重型机械通用技术条件
第2部分:
火焰切割件
JB/T5000.3-2007
重型机械通用技术条件
第3部分:
焊接件
JB/T5000.12-2007
重型机械通用技术条件
第12部分:
涂装
JB/T3223-1996
焊接材料质量管理规程
JB/T6061-2007
无损检测焊缝磁粉检测
JB/T6062-2007
无损检测焊缝渗透检测
JB/T10559-2006起重机械无损检测钢焊缝超声检测
GB/T3323-2005金属熔化焊焊接接头射线照相
NBT47014-2011(JBT4708)承压设备焊接工艺评定
NBT47016-2011(JBT4744)承压设备产品焊接试件的力学性能
NBT47015-2011(JBT4709)压力容器焊接规程
GBT19418-2003钢的弧焊接头缺陷质量分级指南
GBT985.1-2008气焊、焊条电弧焊、气体保护焊和高能束焊的推荐坡口
GBT985.2-2008埋弧焊的推荐坡口
TSGQ7001-2006起重机械制造监督检验规则
TSGZ6001-2005特种设备作业人员考核规则
TSGZ6002-2010特种设备焊接操作人员考核细则
3母材
3.1起重机钢结构所用钢种为碳素结构钢或低合金高强钢,其牌号应符合图纸的规定。
如代用,需设计签字同意后才可使用。
3.2母材的规格尺寸应符合采购技术规格书的规定,并按炉(批)号备有质量合格证书,如为复印件,必须加盖销售单位公章。
3.3对于主要受力构件材料,如图纸或相应标准有要求的,须进行复验,其化学成分、机械性能应符合相应标准的规定。
3.4对于母材无质量合格证书,或质量合格证书中未提供某项性能值时,制造厂必须作补充试验,试验合格后方可使用。
3.5各种钢材,包括3》5mm的板材,L902及L902以上的角钢(包括L902),[100及[100以上的槽钢,1120及I120以上的工字钢,^①30的管子,在使用前均须经喷(抛)丸除锈处理。
其除锈质量等级应达到GB/T8923中规定的
Sa21/2级或更高,粗糙度应略低于涂层总厚度的1/3。
预处理后应在规定时间
内涂保养底漆(车间底漆),具体见《涂装技术条件》。
3.6除3.5规定以外规格的钢材,须进行化学处理(酸洗、冲洗、中和、钝化或磷化等),其除锈质量等级应达到JB/T5000.12附录A的有关规定。
3.7锈蚀严重的钢材有下列情况时不得投入使用,或降规格批准使用。
3.7.1钢材表面麻坑深度超过其标准负公差之半时不得投入使用。
3.7.2钢材上有明显锈蚀麻坑时不得用于主要受力构件,以及影响外观的结构件。
3.8钢材变形超标时在下料前必须矫正合格。
4焊接材料
4.1用于钢结构焊接的药皮焊条、焊丝、焊剂应与被焊母材相适应,并应分别
符合GB/T5117、GB/T5118、GB/T5293或GB/T12470的规定。
4.2用于受力结构焊接的药皮焊条应选用碱性低氢型。
4.3焊接材料应具有符合质保要求的质量合格证书,并按JB/T3223的要求进行验收、存放和使用。
5下料、坡口加工及检验
5.1下料和坡口加工
5.1.1焊件下料时应考虑焊接结构件的收缩量与装配间隙。
5.1.2需要机械加工的零件,应在其边缘或厚度留出适当的加工余量。
5.1.3对主要受力构件(主梁、端梁、小车、支腿)的主要零件下料分割前须进行材质标记移植,具体按《产品标识管理规定》执行。
5.1.4焊件下料与开坡口推荐采用机械方法或火焰切割方法,火焰切割件质量
应符合JB/T5000.2的规定。
对于厚度小于20mm以下的非主要结构用板材可以
采用剪床剪切,但必须留出刨边量,以便去掉硬化区,刨边最小深度为5mm。
如零件对角线差或直线度有要求时,应采取气割时留出刨边量,然后通过刨边找方或取直,刨边量根据板厚和刨边长度确定,一般最小为5mm。
5.1.5当采用碳弧气刨开坡口时,应根据母材焊接要求的预热温度进行预热。
碳弧气刨之后,必须仔细清理,消除所有喷溅的熔渣和表面粗糙、咬边和其它缺陷,并呈现金属光泽。
5.1.6当钢板或型钢需要拼接时,拼接方案须经焊接工程师同意,并符合下述要求:
—桥、门式起重机主梁下盖板和腹板横向对接缝位置不得位于跨中左右各
2.5m范围内;
—盖、腹板宽度大于2m时,纵向允许对接,对接板料最小宽度>300mm。
相邻段的拼接位置致少错开300mm。
纵向对按焊缝距离水平加筋位置
应>150mm;
—箱形梁相邻盖腹板横向对接焊缝不允许在梁的同一截面上,其对接焊缝
位置错开200mm以上,T型钢对接焊缝位置与其相邻盖腹板横向对接焊缝位置错开250mm以上;
—横向筋板与盖板或腹板的横向对接焊缝位置错开的距离为:
大筋板150mm以上,小筋板50mm以上;
—筋板宽度B<1.8m,H<2m采用数控一次切割成型,筋板周边不进行刨边加工。
筋板宽度B>1.8m时,由数控切割下料,对接制成;筋板周边必须留余量经刨边加工找方;
—筒体上相邻筒李的纵缝至少错开90°以上;
—起重机轨道拼接时,拼接的最短长度不应小于1.5m。
5.1.7弯曲或卷制的零件,必须保证钢板轧制方向与拆弯线垂直或与卷制方向一致。
5.1.7如为焊接卷筒,筒体母材下料前必须经超声波检测,符合GB/T2970中
I级要求。
7.1.8承重用吊耳板、结构上吊耳板施焊部位面积为1.5倍吊耳板长度X3倍吊耳板宽度处均须进行超声波检测,符合GB/T1970中I级要求。
5.2对坡口的检验
5.2.1坡口尺寸应符合设计图纸或工艺要求。
5.2.2表面不得有任何影响焊接质量的缺陷,若有怀疑时对其进行磁粉检验或液体渗透检验。
磁粉检验时应符合JB/T6061的规定,液体渗透检验符合JB/T6062的规定。
5.3对坡口表面缺陷的修补对坡口表面存在的不合格缺陷应进行修补,修补可以用打磨、机械加工或
缺陷清除后焊补。
当补焊厚度超过5mm时,必要时应进行按超声波检验,评定合格等级应达到JB/T10559中1级焊缝的验收准则要求。
6结构件的组装
6.1结构件的组装应根据设计图样及工艺要求执行。
所使用的工量器具应保证安全、准确,并按要求进行鉴定。
6.2结构件组装前应检查每一零件的几何尺寸和外观质量是否符合设计图纸及工艺要求,对不符合要求的零件不得装配。
6.3对重要的、结构复杂的结构件,为保证整个结构焊接变形控制在设计、标准要求的有效范围内,应严格控制结构件组装及焊接顺序,在装焊工艺中对此应有详细说明。
6.4组装前必须将各待焊处坡口及距离焊接坡口边缘20mm范围内的铁锈、污垢、油腻、毛刺、涂料及熔渣等清除干净。
6.5角焊缝装配时由角焊缝连接的部件必须尽可能贴紧。
根部间隙严禁超过
5mm,但若间隙超过2mm,则角焊缝焊脚尺寸必须按根部间隙值而增加或开设坡口以便达到所要求的焊缝有效厚度。
只有厚度等于或大于75mm的型材或板材、如果在矫直后和装配中、根部不能足够贴紧以满足这一公差的情况除外。
在这种情况下,如采用合适的衬垫,可采用最大根部间隙8mm。
6.6结构件的组装可采用卡箍、夹紧装置等工装或定位方法。
通常定位焊缝应在焊接以前或在接头焊接期间清除掉。
若定位焊缝成为以后正式焊缝的一部分时,则应满足下列要求:
6.6.1定位焊时,对焊工、焊材的要求应与正式焊缝相同。
6.6.2当正式焊缝需要预热时,装配定位焊时也要预热,而且预热要比正式焊
接时预热温度高30C以上。
663定位焊长度为40~60mm。
间距小于400mm。
对于角焊缝,当焊角尺寸K小于或等于6mm时,定位焊缝焊角尺寸应等于0.6K;当焊角尺寸大于6mm时,定位焊缝的焊角尺寸应不大于4mm。
对于厚板零件的定位焊缝长度可适
当增加,可以多层(多道),每层(道)应错开5〜10mm。
4定位焊缝的两端应打磨成倒角,以保证根部完全焊透。
6.6.4对定位焊应进行目视检查,不允许存在裂纹、气孔、缩孔、夹渣、弧坑等缺陷,当发现上述缺陷时应将焊缝打磨掉并移位重焊。
6.7禁止在工件的非焊接区域任意引弧。
6.8结构件组装后应对坡口尺寸、错边量、平直度、整体尺寸等进行检验,合格后方可进行焊接。
6.9一般体积较大,刚性较差易变形的部件,装配时应适当考虑加固措施。
6.10梁的连接板钻孔前应按图纸规定位置装配。
相关零件的配钻孔可采用点装固定或工艺孔连接的方式进行。
6.11凡拆开后需要在工地总装的部件(不能互换的)或零件,应进行编号,并以钢印打出。
编号处禁止涂油漆,要以油漆框出。
6.12构件组装完毕应交检合格后方可进行焊接。
7产品焊接的实施
7.1焊前准备
7.1.1焊工或焊接操作工须按TSGZ6002-2010《特种设备焊接操作人员考核细则》进行培训考试并取得资格证书。
7.1.2焊接之前须按GB6067.1中的相关要求进行焊接工艺评定,并根据评定合格的工艺制订接头的焊接工艺规程指导焊工进行焊接。
7.1.3焊条和焊剂应按工艺或说明书的烘干温度和时间进行烘干,在使用时应
放置在保温筒中随用随取,保温筒温度应保持在100~150C。
7.2焊接要求
7.2.1焊接方法:
要求采用气体保护焊和埋弧焊,当局部进行修补时可采用焊条电弧焊。
7.2.2焊接环境:
在露天焊接时,如遇下雨、下雪、大雾及大风或周围温度低于
-20C等情况下,如未加保护措施并经工艺人员同意,不得进行焊接。
一般情况下,气体保护焊时要求风速不大于2m/s,埋弧焊或焊条电弧焊时要求风速不大于10m/s,相对湿度应不大于90%。
7.2.3焊前预热:
—低碳钢一般无需预热就可进行焊接,但当环境温度低于0C或者厚度较大者,焊前必须按焊接工艺规程要求进行预热和缓冷;
—低合金结构钢的焊接件必须考虑碳当量、构件厚度、焊接接头的拘束度、环境温度以及所使用的焊接材料等确定焊接预热温度,表1给出了推荐的预热
温度。
当采用非低氢焊接材料或焊接方法时应适当降低临界板厚或者适当提高预热温度。
具体构件的预热温度由焊接技术人员根据具体情况结合焊接工艺评定确定;
表1焊接预热温度推荐表
序号
材质
工件厚度(mm)
环境温度Cc)
焊前预热温度(C)
1
20
Q235
/
一般情况不预热
/
35
<16
低于-10
2
Q295
16~24
低于-5
100~150
Q345
25~40
低于0
ZG240~450
>40
<8
低于-10
3
Q390
8~16
低于-5
100~150
16~32
低于0
>32
4
Q420
/
/
100~150
5
Q460
/
/
150~200
—不同材质之间焊接预热温度按焊接性差的选定;
—同种材质而厚度不同时,焊接预热温度按厚度大的选定;
—预热区为焊缝每间侧距焊缝中心不小于29(5为母材厚度),且不小于
75mm。
724焊接时严格按照工艺规定的焊接顺序施焊,以保证焊接结构的应力和变形趋于最小。
7.2.5严禁在构件的非焊接区域以及平台、夹具上引弧,在可能时必须加引弧板和熄弧板。
弓I、熄板接头型式应与母材一致,长度应能保证母材焊缝的完整性。
弓I、熄板须在焊缝冷却后以切割方式去除,并且必须打磨使焊缝两端光滑而与相邻接的部件平齐或留有3mm的高度并与两侧母材进行过渡。
7.2.6对于某些结构件当采用断续焊缝时,焊缝长度、布置应按照图样规定,其长度偏差不得超过-5%或+10%,节距偏差不得超过-20%或+5%。
727在0C以下温度施焊时,严禁对构件和焊缝用重锤敲击。
7.2.8为了控制厚板焊缝中的收缩应力,可对中间焊层用尖头手锤进行锤击,以防止开裂或变形、或同时防止两者。
但严禁对焊缝根部、表面焊层或焊缝边的母材进行锤击。
锤击应小心进行,以防止焊缝金属或母材皱叠或开裂。
729采用气体保护焊施焊时,焊缝宽度不得大于16mm(药芯焊丝①2.4mm,允许立焊位置最大宽度为25.5mm);采用04mm埋弧焊丝施焊时,焊缝宽度不得大于28mm。
7.2.10多层多道焊时道间接头位应错开50mm以上。
7.2.11焊接完成后,应将熔渣、飞溅、焊瘤等彻底清除干净。
但对于低合金钢,当采用埋弧焊时,焊后为保证缓冷,焊剂不要急于回收。
7.2.12采用碳弧气刨清根后应消除所有喷溅的熔渣和表面粗糙、咬边和其它缺陷,并呈现金属光泽。
7.2.13焊工对所焊焊缝自检合格后,应在规定位置打上焊工自己的钢印。
一般打结构外表面距焊缝边缘和端部各50mm位置,采用3/8?
钢印字头。
7.2.14如果图样没有特殊要求,部件焊接完成后,所有部件的外露棱边应进行圆滑处理,半径不小于2mm。
7.2.15临时性附件的拆除要求:
—任何情况下,都不能采用能导致设备表面材料撕裂的方法来拆除临时性附件(例如锤击);
—临时性附件的热切割面距离设备表面至少5mm。
然后,用机械方法(如
角向磨光机打磨)去除剩余部分的材料;
—在构件热处理前拆除临时性附件。
如果由于技术方面原因,在热处理后拆除临时性附件,则需特别注意前两项中的规定;
7.3焊接记录
每完成一项焊接作业(焊接接头、堆焊、返修或补焊),每一作业或者使用同一种焊接工艺规程的一组作业应填写一张产品焊接记录单。
该记录单至少应包括:
—接头、接头组、堆焊、返修或补焊所属产品和部件的名称和图号;
—使用焊接工艺规程的编号;
—焊缝编号;
—使用焊接材料的牌号和批号;
—完成每个工序的焊工或焊接操作工的姓名和钢印号;
—使用焊机的编号;
—焊缝外观及尺寸;
—焊缝无损检测报告编号;
—检验员签名或签章。
8焊后消除应力处理
对于设计图样或工艺上有消应力处理(热处理或振动时效)要求的结构件,在焊接之后应进行消应力处理。
处理规范应根据工件厚度、接头拘束度和结构使用条件结合焊接工艺评定等综合考虑。
热处理可按JB/T6046或JB/T5926执行。
振动时效可按JB/T10375执行。
有密填充内腔的结构件,有热处理之前,应在中间隔板或盖板上适当位置
加工①10mm的孔,使其空腔与外界相通,在盖板上钻的孔,热处理后要进行
焊堵并磨平。
9焊接变形的矫正
对结构件焊接后变形可采用机械方法或火焰局部加热方法进行矫正,但在
热态下禁止在300~500C进行机械矫正和锤击,以免引超脆裂。
采用火焰加热矫正时应注意以下几点:
—对于重要构件,在同一部位不得重复加热;
—不允许在同一断面造成拉、压双向应力的反复矫正;
—受力构件禁止浇水冷却;
—需要进行热处理的构件,应的热处理前进行矫正;
—冷矫正时,变换矫正方向的次数不得超过两次,否则须加热矫正;冷矫正后出现的裂纹,必须焊补后用砂轮磨平,且须参照5.3执行。
—火焰加热矫正时,对于调质钢严禁超过600C,其他钢严禁超过700Co加热过程中,钢材的颜色和相对应的温度,见表2。
表2钢材表面颜色及相应温度
颜色
[温度c
颜色
温度C
颜色
温度C
暗褐色
530~580
樱红色
780~800
暗黄色
1050~1150
赤褐色
580~650
亮樱红色
800~830
亮黄色
1150~1250
暗樱红色
:
650~750
亮红色
830~880
黄白色
1250~1300
深樱红色
750~780
桔红色
880~1050
10焊缝的质量检验
10.1焊缝的等级:
焊缝等级分为1、2、3级
—1级是指重要受拉结构件的焊接接头;
—2级是指一般受拉结构件的焊接接头;
—3级是指受压结构件的焊接接头;
10.2焊缝内部缺陷的检验应符合下列要求:
—1级焊缝应进行100%检验。
采用超声波检验时其评定合格等级应达到JB/T10559中1级焊缝的验收准则要求。
采用射线检验时应达到GB/T3323的规定,其评定等级不应低于H级;
—2级焊缝可根据具体情况进行抽检,采用超声波检验时其评定合格等级应达到JB/T10559中2级焊缝的验收准则要求。
采用射线检验时应达到GB/T3323的规定,其评定等级不应低于皿级;
—3级焊缝可根据具体情况进行抽检,采用超声波检验时其评定合格等级应达到JB/T10559中3级焊缝的验收准则要求,射线检验不作规定。
10.3有下列要求情况之一时应进行表面探伤:
—外观检查怀疑有裂纹;
—设计文件规定;
—检验人员认为有必要时。
磁粉探伤应符合JB/T6061的规定;渗透探伤应符珍贵JB/T60162的规定。
10.4焊接卷筒体的环向对按焊缝和纵向对接焊缝外观检查合格后应进行无损检测。
对环向对接焊缝至少进行50%检验,用射线检测时不应低于GB/T3323缺陷分级中的H级,用超声波检测时不应低于JB/T10559中1级焊缝验收准则要求。
纵向焊缝进行20%检验,但至少要保证各筒节两端各160mm范围内进行检验,用射线检测时不低于GB/T3323缺陷分级中的皿级,用超声波检测时不应低于JB/T10559中3级焊缝验收准则要求。
卷筒轴与法兰、筒体与法兰之间焊缝应进行磁粉或渗透探伤,并符合10.3中相关标准的规定。
10.5弧焊接头的缺陷质量分级应符合下列规定:
—1级弧焊接头的缺陷质量分级应符合GB/T19418的B级;
—2级弧焊接头的缺陷质量分级应符合GB/T19418的C级;
—3级弧焊接头的缺陷质量分级应符合GB/T19418的D级
10.6主要受力结构件的隐蔽件在封闭前,必须经过制造地所在特种设备监督检验人员检查合格后方可起家入下道工序。
10.7钢结构组焊成型后几何尺寸符合相关标准或设计要求。
未注尺寸公差与形位公差按JB/T5000.3执行。
10.8结构件的气密性试验、煤油或肥皂水渗漏试验可参照JB/T4735执行。
10.9焊缝无损检测人员应取得相应的无损检测资格;报告编制人员和签发人员应持有相应无损检测方法的H级或H级以上资格证书。
无损检测外包须选择有
资格的无损检测单位。
10.10焊接质量检验人员应在金属结构制造、检验和测试方面经过培训并取得相应资质。
检验人员应至少完成下列工作任务:
—应证实相关材料符合规程要求;
—应审核操作过程中焊接程序符合焊接技术规程规定的要求;
—检验生产所用焊接设备、监视和测量装置符合规定有要求;
—检验焊缝尺寸、长度和位置符合焊接技术规程或图样的要求;
—应采用合适的量具测量焊缝的尺寸和外形。
应采用强光、放大镜以及其他有助于这种检验的手段目测检验焊缝、母材上裂纹以及其他缺陷。
11焊接缺陷的返修
—对需要焊接返修的缺陷应当分析产生的原因,提出纠正措施,按评定合格的焊接工艺编制返修工艺文件;
—返修前需将缺陷清除干净,必要时可采用表面检测确认;
—待返修部位应制备坡口,坡口形状与尺寸要防止产生焊接缺陷和便于焊工操作;
—如需预热,预热温度应较原焊缝适当提高;—返修焊缝质量要求与原焊缝相同;—当一条焊缝返修长度超过该条焊缝的五分之一,且补焊厚度超过三分之一时则不允许补焊,应将该条焊缝全部铲掉重焊;
—焊瘤,超标凸起,或余高过大时必须清除过量的焊缝金属;
—超标的焊缝凹陷或弧坑,焊缝尺寸不足,咬边时必须对表面进行后,并补充焊缝金属;
—发现不完全熔合,过量的焊缝气孔,或夹渣时必须清除不合格部分并重新焊接;
—发现焊缝或母材的裂纹时必须用磁粉检查、液体渗透检查或其他可靠的方法确定裂纹的范围;然后清除裂纹及裂纹两端的50mm的完好金属重新焊接;
—当母材开错孔位时除了由于结构或其他原因必须焊接修复外,开错位置的冲孔或钻孔可以保留孔洞或以螺栓填满;
—同一部位的返修、补焊次数以两次为限,超次返修应办理相关审批手续。
12完工报告
完工报告应当包括以下内容
—母材和焊材质量证明书(原件或复印件,若为复印件,必须加盖经销商公章);
—母材和焊材的复验报告(若设计、标准或顾客要求);
—焊接工艺评定报告(WPQR)和焊接工艺规程(WPS)清单;
—焊工或焊接操作工姓名及钢印一览表;
—重大设计变更;
—主要受力构件焊缝布置图;
—焊接记录;
—结构几何尺寸记录;
—消应力处理报告(若有);
—外包有资无损检测单位及无损检测人员清单(若有);
—焊缝无损检测报告;
—焊缝返修记录和检验结果报告(若有);
—不合格品处理报告(若有)。