车工实训总结报告三篇.docx
《车工实训总结报告三篇.docx》由会员分享,可在线阅读,更多相关《车工实训总结报告三篇.docx(14页珍藏版)》请在冰豆网上搜索。
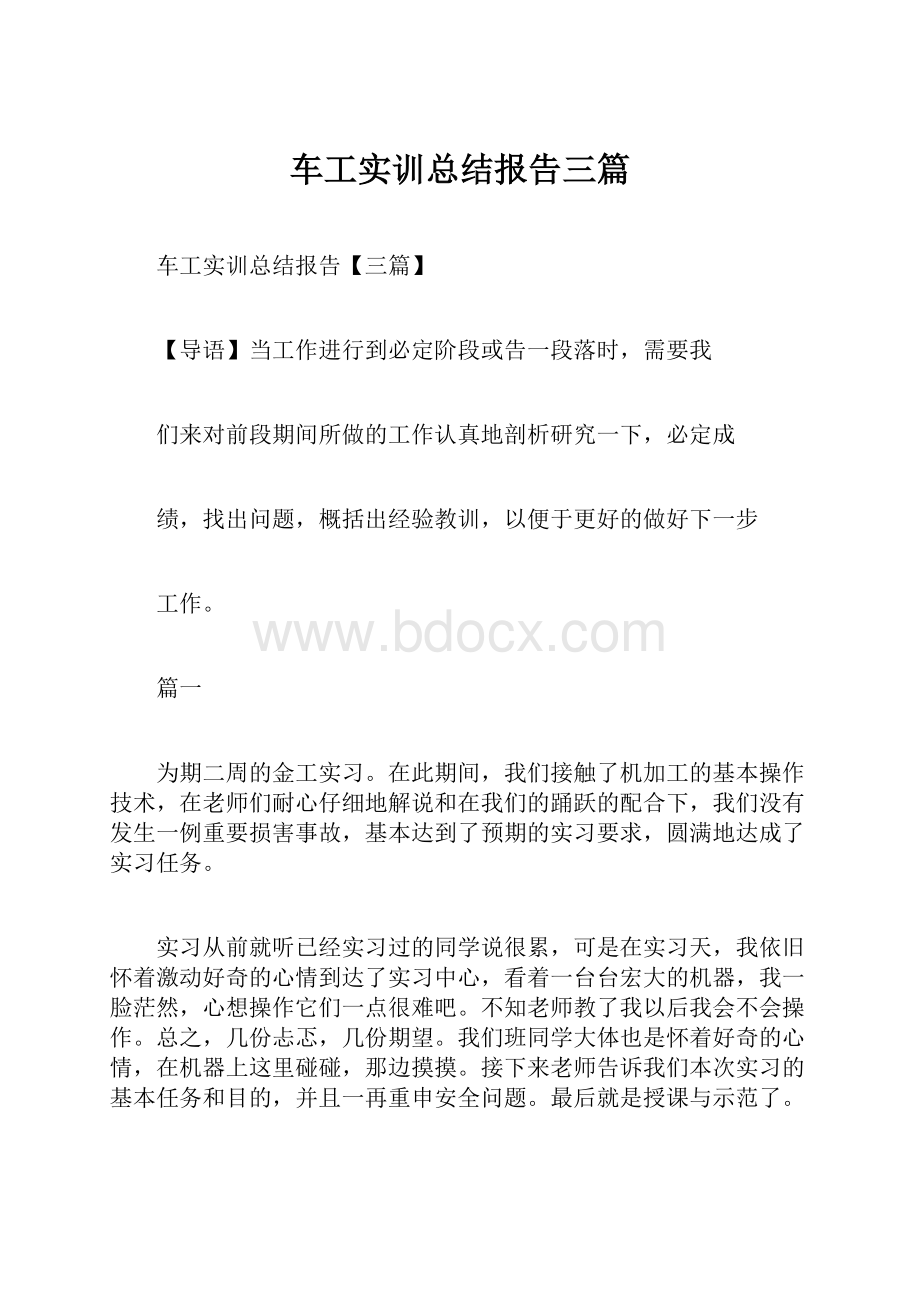
车工实训总结报告三篇
车工实训总结报告【三篇】
【导语】当工作进行到必定阶段或告一段落时,需要我
们来对前段期间所做的工作认真地剖析研究一下,必定成
绩,找出问题,概括出经验教训,以便于更好的做好下一步
工作。
篇一
为期二周的金工实习。
在此期间,我们接触了机加工的基本操作技术,在老师们耐心仔细地解说和在我们的踊跃的配合下,我们没有发生一例重要损害事故,基本达到了预期的实习要求,圆满地达成了实习任务。
实习从前就听已经实习过的同学说很累,可是在实习天,我依旧怀着激动好奇的心情到达了实习中心,看着一台台宏大的机器,我一脸茫然,心想操作它们一点很难吧。
不知老师教了我以后我会不会操作。
总之,几份忐忑,几份期望。
我们班同学大体也是怀着好奇的心情,在机器上这里碰碰,那边摸摸。
接下来老师告诉我们本次实习的基本任务和目的,并且一再重申安全问题。
最后就是授课与示范了。
我们主要学习车工,一进操作室看到车床就知道操作应当不简单,结果老师也说了车工是最难的。
我当时就告诉自
己,我的着手能力原来就不强,必定要认真听!
车床是利用工件的旋转和刀具的直线和曲线运动来加工工件的,就其工
作的基本内容来说,能够车削外圆。
内圆、端面、切断、切槽、内外圆锥、各样螺纹及滚花和成形面等。
经过老师的介绍,我知道了车刀的安装一定注意以下几点:
,车刀夹在刀架上的伸出长度应当尽量短,以增强其刚
性。
第二,车刀底下的垫片数目应尽量少,并放齐整。
第三,车刀刀尖应于车床主轴中心等高。
工件的安装:
,伸出不可以太长,影响装夹刚性。
第二,装夹一定坚固靠谱,防备工件飞出伤人,必需时用加力杆。
第三,装夹毛坯工件时注意找正佳紧。
同时还有切削三因素、切削用量选择、手动车外圆,端面,阶台的方法。
最后老师也相同的讲了实习任务,并且介绍了加工这个零件的工艺步骤,我认真的听着,惟恐遗漏一点点。
最后就是在操作机器上是演示了,相同我也很认真的看着。
老师的任务达成了,接下来就轮到我们自己操作了,我们三人一组,要每人都加工一个简单的零件。
刚开始的时候我们对机床的熟习度不够,致使我们加工起来不单很慢,并且常常犯错,应为机加工零件对零件的精度要求很高的,一不当心就出废品,就得又从头做,加工的时间长了慢慢的对机床也有些熟习了,加工起来速度就显然
的快了,并且精度也显然提升了许多。
终于在次日下午就
加工出了三个合格的零件。
后边三天老师给我们的任务是加工一个更难的零件,而
且精度要求也更高,由于前面的基础,我们加工的速度快了
许多,但应为精度要并且精度要求也更高,由于前面的基础,
我们加工的速度求较高,因此仍是常常出废品。
经过努力,
在我们仔细的加工下仍是达成了任务,成功做出了零件。
应为机加工都是站着的,因此二周下来我们都很累的,
但过得很充分,在这二周里我们仍是学会了好多东西。
1.认识机械制造工艺知识和新工艺、新技术、新设施在机械制造中的应用,培育、提升和增强了我们的工程实践能力、创新意识和创新能力。
2.机加实习培育和锻炼了我们,提升了我们的整体综合素质,使我们不只对机加实习的重要意义有了更深层次的认识,并且提升了我们的实践着手能力。
使我们更好的理论与实质相联合,稳固了我们的所学的知识。
3.我们同时也学到老师的敬业、谨慎精神。
有的老师会一次又一次地给同学演示怎样操作,直到同学真实清楚。
实习过程中我们也弘扬了团结互帮的精神男同学帮助女同学、着手能力强的同学帮助着手能力衰的同学,大家互相帮助互相学习,既学会了怎样合作又增强了同学间的友情。
4.在实习过程中我们获得的劳动成就。
这些以前让人难
致使信的小零件,居然是自己亲手加工而成,这类骄傲感、
成就感是难以用语言来表达的。
机加实习让久在讲堂的我亲身的感觉到作为一名工人
的苦与乐,同时查验了自己所学的知识。
机加实习更让我深
深地领会到人生的意义。
劳动不单对自然世界进行改造,也对一个人的思想进行
改造。
经过这周的机加实习,在这方面我也深有领会。
1、劳动是最荣耀的,只去实践才能领会劳动的酸楚和
乐趣。
2、坚韧不拔,认真耐心。
3、认真负责,注意安全。
4、只需付出就会有收获。
实践是真谛的查验标准,经过一礼拜的金工实习,我了
解到好多工作知识,也获得意志上锻炼,有酸楚也有快乐,
这是我大学生活中的又一笔可贵的财产,对我此后的学习和
工作将有很大的影响。
很快我们就要步入社会,面对就业了,就业单位不会像
老师那样点点滴滴仔细入微地把要做的工作告诉我们,的是
需要我们自己去察看、学习。
不具备这项能力就难以胜任未
来的挑战。
跟着科学的迅猛发展,新技术的宽泛应用,会有
好多领域是我们不曾接触过的,只有敢于去试试才能有所突
破,有所创新。
就像我们接触到的车工,固然它的危险性很大,可是要求每个同学都要去操作并且要做出成品,这样就锻炼了大家敢于试试的勇气。
一周的金工实习带给我们的,不全部是我们所接触到的那些操作技术,也不只是是经过几项工种所要求我们锻炼的几种能力,的则需要我们每一个人在实习结束后依据自己的状况去感悟,去反省,勤时自勉,有所收获,使此次实习达到了他的真实目的。
篇二
车工实习结束了,但带给我的感觉却永久的留在了我的心底。
重要的是安全老师告诉我们的从前发生的近似事件,我真的有点惧怕,很多人也和我有相同的感觉。
老师看出了这一点,就告诉我们,只需依据正确的方法,掌握要领,是不会发惹祸故的,于是我理解了,规范的操作,是安全的重要保证!
一、车工安全知识
1、上班穿工作服,女生戴工作帽,并将长挽入帽内。
2、工作时一定精力集中,禁止私自走开机床。
3、工件和车刀需装夹坚固,免得工件和车刀飞出伤人。
4、工件旋转时,禁止丈量工件。
5、工件安装好后,三爪扳手一定顺手取下,免得不注
意开动车床,免得扳手飞出伤人。
6、上班禁止串岗,坚持各自工作岗位二车床实践知识
老师先初步示范了一下操作方法,并加工了一部分,而后就让我们开始加工,在此时老师们教的特别认真,不断地在人群中穿越,随时指正我们在操作中的错误,纠正手型,耐心的一遍遍的剖析我们做的砂型的的优弊端。
固然时间只有短短的几日,可是师傅们倒是尽其的努力,在这样有限的时间里多教给我们一点东西,希望我们能真的有所收获,而不是空手而归。
车床加工中一个很重要的方面就是要选择正确的刀,一开始我们要把所给圆柱的端面车平,就要用偏车刀来加工,而后就是切槽,这时就要换用切槽刀。
切槽刀的刀头宽度较小,有一条主切削刀和两条副切削刀,它的刀头较小,简单折断,故应用小切削用量。
切槽的时候采纳左右借刀法。
切完槽,就要加工螺纹了,这对我们这类素来没有使用过车床的人来说,真是个考验。
我不断的转动横向和纵向的
控制手柄,谨小慎微的加工,搞了整整一个下午,还算满意,可是比起老师拿给我们看的样本仍是差了许多,并且在加工
的时候我的手还被飞出来的热的铁屑烫伤了,不论怎么说,一句话,仍是不娴熟。
但看着自己加工出来的工件,内心真的很快乐。
车工实习是一门实践基础课,是机械类各专业学生学习工程资料及机械制造基础等课程必不行少的先修课,是非机
类有关专业教课计划中重要的实践教课环节。
鉴于此,同学们一定赐予这门课以足够的重视,充足的利用这一个月的时间,好好的提升一下自己的着手能力。
我校的工程训练中心固然存在诸如:
设施数目有限、师资力量相对单薄等缺点,可是学校经过有效的组织,化短为长,使同学们分期分批的实习,达到了理想的成效。
光阴老是急忙而逝,很快几日就这样过去了。
大学毕业后,我们就要步入社会,面对就业了,就业单位不会像老师那样点点滴滴仔细入微地把要做的工作告诉我们,的是需要我们自己去察看、学习、总结。
不具备这项能力就难以胜任将来的挑战。
跟着科学的迅猛发展,新技术的宽泛应用,会有好多领域是我们不曾接触过的,只有敢于去试试才能有所打破,有所创新。
几日的车工实习带给我们的,不全部是我们所接触到的那些操作技术,也不只是是经过几项工种所要求我们锻炼的几种能力,的则需要我们每一个人在实习结束后依据自己的状况去感悟,去反省,勤时自勉,有所收获,使此次实习达到了他的真实目的。
篇三
一、实习目的:
1、认识车床及有关安全知识。
2、熟习车床的基本操作方法。
3、读懂图纸并实质感觉操作的各个步骤。
二、实习要求:
按图纸要求做一个锉刀手柄.
三、实习内容:
(一)车工理论
1.什么是车工?
操作机床并在机床上加工机械产品的工人或工种。
2.车削的观点。
经过工件的旋转运动和刀具的进给运动来改变工件毛
坯尺寸大小,形状要求的一种冷加工切削方法。
3.什么是主运动?
工件的旋转是主运动。
4.什么是协助运动?
刀具的进给运动是协助运动。
5.车床的型号标准。
CW6140-1000,750
此中,C示车床类型W示特征代号(全能)6:
构成代号1:
型号代码一般车床40:
主参数同意加工直径的1/10400毫米
(mm)1000:
加工长度
6.车床的加工范围。
车外圆、车端面、车内孔、车圆锥、钻孔、铰孔、钻中
心孔、车特型面、切槽、切断、车削各样不一样的螺纹、滚花、
冷绕弹簧等。
7.车床的重要构成部分。
主轴变速箱、走刀箱、拖板箱、
刀架、挂轮箱、尾架、拖板、三杆、床身、附件
8.车床的运动系统主运动:
电动机→皮带轮→床头变速箱→主轴→卡盘→工件做旋转运动
协助运动:
电动机→皮带轮→床头变速箱→光杆或丝杆→拖板箱→拖板→刀架→车刀作纵横两个方向的直线运动或车削各样螺纹
9.车床的养护:
润滑:
上班加润滑油.检查:
上班空转2-3
分钟.防砸:
不一样意在车床上敲打.泊车变速:
改变速度,一定
停下机床.文明生产:
下班打扫机床和环境卫生.封闭电源:
保证安全.
(二)安全操作规程:
1.工作时穿工作服,女生要戴帽子并把头发卷入帽子内.
禁止带手套操作
2.工作时一定精力集中,不一样意私自走开机床或做与车削没关的工作。
手和身体不可以凑近旋转的工件和车床零件。
3.工件和车刀一定装坚固,不一样意用手去停旋转的卡盘.
4.车床动工时不一样意丈量工件长度.也不可以用手摸工
件。
5.工件夹好后要顺手把卡盘扳手取下,免得飞出伤人.
6.工作时禁止串岗,走开自己的工作岗位.
7.禁止开车变换转速.
8.车削时,小刀架应放在适合地点,免得与转盘相撞发
惹祸故.
9.用专用铁钩消除铁屑,不一样意直接消除。
10.违反安全规定,教师要赐予责备教育.不听教育,多
次违反的报院系赐予必需的办理,实习成绩记为零.
(三)加工工艺:
锉刀手柄的加工工艺
序号加工步骤加工内容加工工具
1车外圆下料160~170mm115mm×Φ30+°外圆车刀、游
标卡尺
2车台阶划线定位30,70,75,80,11530mm×Φ2210mm×Φ1790°外圆车刀游标卡尺
3车圆弧圆弧R=35mm圆弧R=105mm圆弧车刀圆弧样板游
标卡尺
4整形用锉刀修整砂布抛光锉刀、砂布、游标卡尺四、车工心得领会:
金工实习是一门实践性的技术基础课,是理工科学生学
习工艺知识、培育工程意识、提升综合素质的重要实践必修
课。
经过本次短暂的金工实习的实质操作与练习,我收获颇
多。
车工是在车床上利用工件的旋转和刀具的挪动来加工
各样展转体的表面。
第一是老师让我们小构成员一人一台车
床各自去熟习车床。
而后给我们现场解说,让我们认识到卧
式车床的构成结构和其用途,车刀的种类,常用的刀具资料,刀具资料的基天性能,车刀的构成和主要几何角度,学会了
车刀的安装,三爪自安心卡盘安装工件的方法。
接着老师给我们示范了车床的操作方法及示范坯料车断面。
最后就是让我们开始自己独立练习操作,固然开始操作技术不怎么娴熟,但经过几次的练习及小构成员间的互相
学习,最后我们终于成功了,看着自己辛辛苦苦做出的工件,我们内心都万分惊喜,很有成就感,同时也领会到了工程技术人员,工人们的不简单。
经过车工实习,我们熟习了有关车工及车工工艺方面的基本知识,掌握了必定的基本操作技术。
此次实习使我理解
了“只需我们肯努力,勇于战胜各样困难,不怕苦,不怕累,认真地去实践,并坚韧不拔,最后我们必定能成功”。
【车工实训总结报告【三篇】】,工作总结。