怎样做好生产质量管理培训讲学.docx
《怎样做好生产质量管理培训讲学.docx》由会员分享,可在线阅读,更多相关《怎样做好生产质量管理培训讲学.docx(9页珍藏版)》请在冰豆网上搜索。
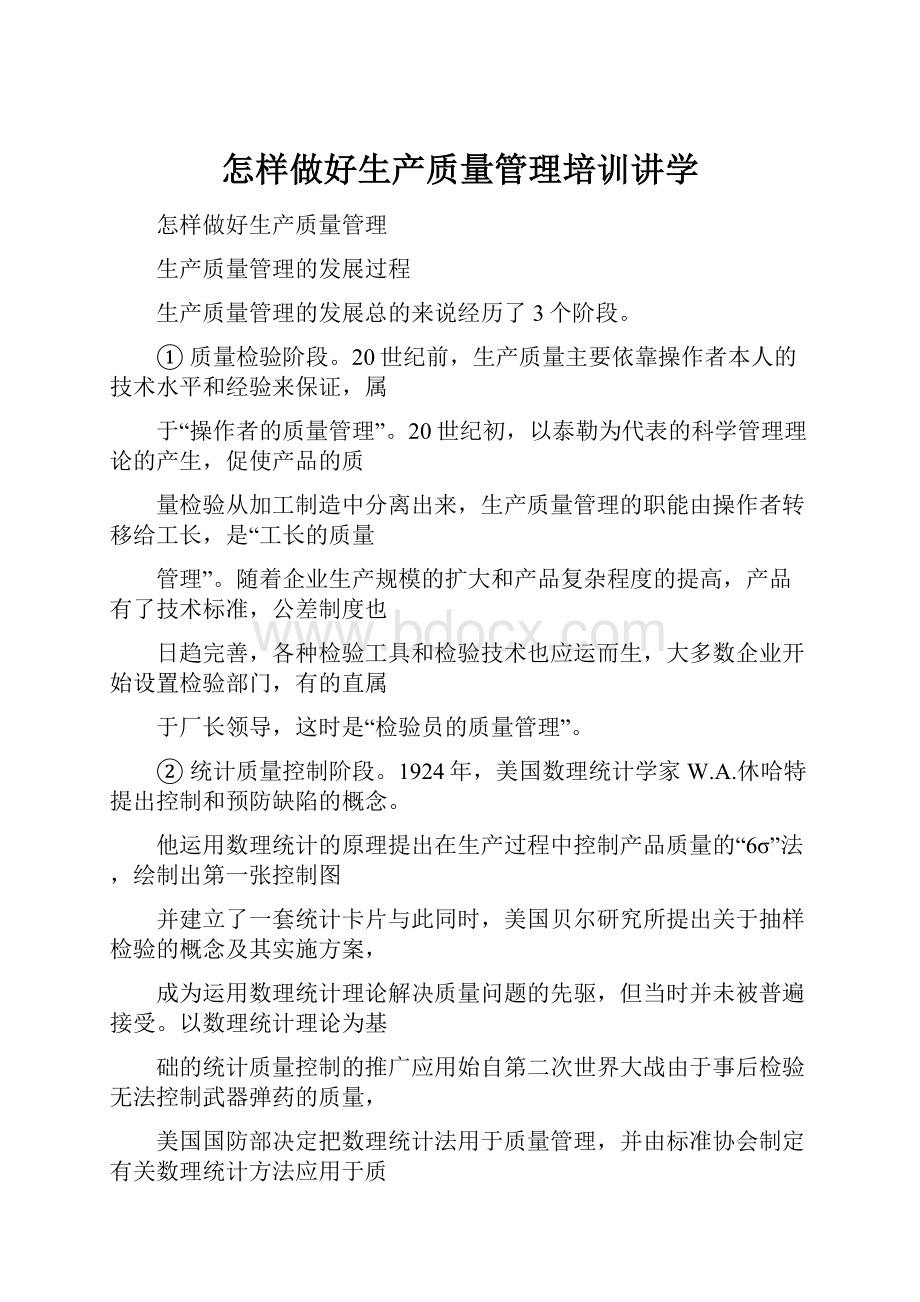
怎样做好生产质量管理培训讲学
怎样做好生产质量管理
生产质量管理的发展过程
生产质量管理的发展总的来说经历了3个阶段。
①质量检验阶段。
20世纪前,生产质量主要依靠操作者本人的技术水平和经验来保证,属
于“操作者的质量管理”。
20世纪初,以泰勒为代表的科学管理理论的产生,促使产品的质
量检验从加工制造中分离出来,生产质量管理的职能由操作者转移给工长,是“工长的质量
管理”。
随着企业生产规模的扩大和产品复杂程度的提高,产品有了技术标准,公差制度也
日趋完善,各种检验工具和检验技术也应运而生,大多数企业开始设置检验部门,有的直属
于厂长领导,这时是“检验员的质量管理”。
②统计质量控制阶段。
1924年,美国数理统计学家W.A.休哈特提出控制和预防缺陷的概念。
他运用数理统计的原理提出在生产过程中控制产品质量的“6σ”法,绘制出第一张控制图
并建立了一套统计卡片与此同时,美国贝尔研究所提出关于抽样检验的概念及其实施方案,
成为运用数理统计理论解决质量问题的先驱,但当时并未被普遍接受。
以数理统计理论为基
础的统计质量控制的推广应用始自第二次世界大战由于事后检验无法控制武器弹药的质量,
美国国防部决定把数理统计法用于质量管理,并由标准协会制定有关数理统计方法应用于质
量管理方面的规划,成立了专门委员会,并于1941~1942年先后公布一批美国战时的质量
管理标准。
③全面质量管理阶段。
20世纪50年代以来,随着生产力的迅速发展和科学技术的日新月异,
人们对产品的质量从注重产品的一般性能发展为注重产品的耐用性、可靠性、安全性、维修
性和经济性等。
在生产技术和企业管理中要求运用系统的观点来研究质量问题。
在管理理论
上也有新的发展,突出重视人的因素,强调依靠企业全体人员的努力来保证质量此外,还有“保
护消费者利益”运动的兴起,企业之间市场竞越来越激烈。
在这种情况下,美国A.V.费根鲍
姆于60年代初提出全面质量管理的概念。
他提出,全面质量管理是“为了能够在最经济的
水平上、并考虑到充分满足顾客要求的条件下进行生产和提供服务,并把企业各部门在研制
质量、维持质量和提高质量方面的活动构成为一体的一种有效体系”。
管理的发展与工业生产技术和管理科学的发展密切相关。
现代关于质量的概念包括对社会
性、经济性和系统性三方面的认识。
①质量的社会性:
质量的好坏不仅从直接的用户,而是从整个社会的角度来评价,尤其关系到
生产安全、环境污染、生态平衡等问题时更是如此。
②质量的经济性:
质量不仅从某些技术指标来考虑,还从制造成本、价格、使用价值和消耗
等几方面来综合评价。
在确定质量水平或目标时,不能脱离社会的条件和需要,不能单纯追
求技术上的先进性,还应考虑使用上的经济合理性,使质量和价格达到合理的平衡。
③质量的系统性:
质量是一个受到设计、制造、使用等因素影响的复杂系统。
例如,汽车是
一个复杂的机械系统,同时又是涉及道路、司机、乘客、货物、交通制度等特点的使用系统。
产品的质量应该达到多维评价的目标。
费根堡姆认为,质量系统是指具有确定质量标准的产
品和为交付使用所必须的管理上和技术上的步骤的网络。
质量管理发展到全面质量管理,是质量管理工作的一次质的飞跃。
统计质量管理着重应用统
计方法控制生产过程质量,发阵预防性管理作用,从而保证产品质量。
然而,产品质量的形
成过程不仅与生产过程有关,还与其他许多过程、许多环节和因素相关联,这不是单纯依靠
统计质量管理所能解决的。
全面质量管理相对更加适应现代化大生产对质量管理整体性、综
合性的客观要求,从过去限于局部性的管理进一步走向全面性、系统性的管理。
为确保生产顺畅,保证产品质量,完善生产流程,确保产品的可追溯性,提高全员积极性,
特制订以下要求:
一、质量检验标准及要求
1、检验标准:
电子产品的通用检验标准,产品特殊检验要求(由工艺技术提供)。
2、检验方法:
依产品的检验及检测标准决定(性能测试要求由工艺技术提供)。
3、检验设备:
检测使用的仪器、工装、治具。
4、检验批次确认:
检验部门将按产品流通卡或物料标示卡上标注的批次分批进行检测,并
对此做好记录
5、产品的库存期不得超过3个月,3个月以上的产品需重新检测处理。
6、完成品及半成品经检验合格出货时需附有出厂检验报告。
二、质量保证
1、抽检人员依照BOM和来料清单对原材料加以抽查,合格后品质人员加盖合格章方可入
库,未抽检,直接入库的产品直接对入库人加以考核。
2、成型物料在成型完成后物流部负责进行标识送检,且标识卡上有相关作业人员的签名。
3、成型物料完成后必须经品质人员抽查确认,抽检标准依照正常生产要求,确认OK后品
质人员必须在标识卡上签名盖章,未经盖章签名,生产有权不予使用,对生产造成的影响由
相关责任单位承担,生产部将此做为质量异常记录。
4、生产上存在因原材料问题造成的生产受阻,或产品质量问题的,生产责任班长需及时出
具书面异常报告给相关部门分析原因,对于发现问题未及时反馈导致的批量问题,考核相应
班组长,并负责对不良品处理,损耗工时财务月底结算时扣除。
5、生产过程的质量控制
5.1、班组必须加强生产过程的产品质量控制管理,相应作业工序悬挂作业指导书,作业指
导书内容与相应工序必须一致,对于非常规产品的生产可悬挂临时作业指导书,在形成量产
时需更新为正式文件,否则做为问题点记录,相关责任人加以考核。
注:
正式文件加受控印章,不可私自涂改,对于有变动的工序需由相应的工艺人员加以更改,
并在更改处签字确认,更改处不可超过3处。
一月之内将更正处改成电子文档(此时限从制
订工艺时开始顺延一个月)。
否则以问题点加以记录,相关人员加以考核。
班长若临时调整
生产工艺,必须通知相应工艺人员,并由工艺担当确认,否则不得私自更改工艺,若有临时
变动的生产工艺或调整的工序(原材料问题或人员的减少增加),工艺必须在相应工艺指导
书上附带动态控制卡注明。
5.2、建立完善的监控体系,在对最终产品质量有影响的关键生产工序上设立专人质控点,
严格做好原始记录和数据统计,监控过程质量。
质控点人员必须定岗定员,作业时标记自己
的记号,此记号必须为可追溯性标记(此标记必须经品质确认通过可以使用,品质留有备档
以便查找),若因特殊原因需更换质控点人员时,必须由品质和工艺对其资格进行确认,生
产不能私自更换质控点人员。
5.3、班组长应及时发现和纠正生产过程的异常状况,确保产品质量的一致性、稳定性,产
品质量如有失控应第一时间查明原因并采取纠正措施,若失控产品已流入下一工序,须将失
控产品放到指定定置区域并采取相应的措施及时处理,相应问题作为质量异常记录。
5.4、质量部人员不定时对产品生产过程质量控制进行巡查,并对生产过程的不符合点进行
问题点记录,且要求相关班组现场当即进行有效整改,对整改结果不符合要求的,考核相应
班长。
5.5、生产上任何人员不可私自更改测试工序,产品必须按工艺指导书要求测试,对于私自
改变测试要求的,质量部人员对问题加以记录,且要求已经测试的所有产品重新测试,损耗
工时由财务在月底结算时扣除,同时考核责任人-20分/次。
5.6、对于生产过程中的不良品处理,后一工序的不良品由相关责任班长具体统计,属前一
工序生产造成的不良品,后一工序可不进行处理,不良品交接给前一工序,由前一工序责任
班组安排人员处理,超出质量目标的不良相关责任人加以考核。
班长做好每天相应的质量异
常记录,每周一上午9:
00前将上周质量异常记录汇总上交生产主管及品质主管。
5.7、生产班长有权对生产过程中存在问题(如原材料问题)进行停产整改,且出具相关的
停产报告并由生产主管签字,经理确认同意方可停产,并对相应责任人进行考核,问题做为
质量异常记录。
5.8、对于未进行品质确认而进行上线使用的物料品质人员有权要求停产,因此而造成的工
时损耗由相关责任部门承担,并负责对异常物料返检,损耗工时参照返检批次的要求,由财
务在月底结算时扣除,因物料未进行抽检而用于产线出现的质量问题做为质量异常记录,相
应班组加以考核。
6、正常产品送检时,当天生产的产品在流通卡上注明生产批次(同一班组生产一批以上的)、
且相关人员签名(班长、包装人员)、送检时间。
未标示品质判定不合格,并记入抽检不合
格记录里。
7、组装过程中
7.1、组装过程的测试合格率不得低于99.8%(加工原因造成的),否则,前一工序的责任
班组负责对未组装的产品重新检测,损耗工时由财务月底结算时扣除,且相应班组进行考核。
7.2、检测人员严格按要求测试,对于私自改变测试要求的,质量部人员发现对问题加以记
录,已经测试的所有产品必须重新测试,损耗工时由财务月底结算时扣除,且相应班组进行
考核。
8、不合格品处理
8.1、品质检验中批次不合格,相关责任班组需对产品进行返检,并进行第二次送检,合格
后方可入库。
8.2、客返的不良品由品质部门进行分类,并按客返不良流程进行处理。
8.3、客户退货的产品由品质部分类,相关部门负责处理,班组对处理的产品及时送验确认,
无问题后方可出货。
9、生产不良品的处理
9.1、生产过程中产生的不良品需要修复,修复完成后的产品需要重新经过质检人员检验,
确认无问题后方可入检。
9.2、需要救治部门维修的产品,由生产交接给救治部维修,救治部维修OK后交接给生产,
生产重新检查处理,要求与正常品生产的要求一致。
生产检测无问题后方可入检,品质人员
对维修品做重点检查,合格后方可入库。
三、现场问题处理
1、设现场巡检人员,巡检人员每两小时对生产现场整体情况进行巡查,并记录问题点,相
关责任人及班长签字确认,找不到责任人由班长承担。
2、对于巡检问题点,相关责任人要求马上整改,巡检人员跟踪确认。
3、巡检问题点每周一上交品质主管,质量部门负责整理汇总并公布张贴。
四、奖罚制度
1、参照产品退货及客诉处理规定
2、因工艺标准不当造成客返或客诉质量事故,由工艺承担。
因班组执行不当,未按要求作
业导致出现的质量问题由班组承担。
3、现场及日常事务考核参照前期考核要求:
日常考核、质量考核、效率考核、物耗及成本
考核。
4、考核细则:
.
4.1、产品抽检质量状况及生产质量异常由质量部在月底加以汇总,并将结果上报公司财务,
财务依此规定对相关责任班组进行工时、工资结算。
4.2、生产部门负责将当月汇总的质量异常记录上报公司财务,财务部依此进行工资结算
4.3若是前一工序作业不当造成的通过目检可以检查出来或用工装可以检测出来的,前工序
责任人给以-10分/1PCS处罚;若是前一工序的原因造成的用目检可以检查出来(用检验工
装无法检测出的),前一工序相关责任人员给以-5分/1PCS处罚,如少件、碎件等。
此项由
生产部门负责监督考核。
4.4对于本月无质量异常的班组,给以相应责任班组全体奖励20分,班长40分。
对于本月
累积A类不合格出现2次(包括内部抽检判定和客户抽检判定)的班组,班组全体考核-5
分,对于A类不合格3次及以上的班组,全体考核-10分/人。
4.5、对于巡检问题点每月超过20个的班组,全体考核-5分/人;对于问题点小于20个的班
组不予以考核;对于本月无任何问题点的班组,全体奖励+10分/人。
此由财务月底进行工
资结算。
注:
各班组人员名单每月底由内勤上报公司财务,财务部门依此进行工资工时结算。
五、相关文件:
1、关于产品退货及客诉处理规定。
2、日常考核、质量考核、效率考核、物耗及成本考核规定。
3、OQC抽检不合格记录一览
4、生产质量异常记录
5、问题点记录