转炉钢渣处理的工艺方法doc.docx
《转炉钢渣处理的工艺方法doc.docx》由会员分享,可在线阅读,更多相关《转炉钢渣处理的工艺方法doc.docx(42页珍藏版)》请在冰豆网上搜索。
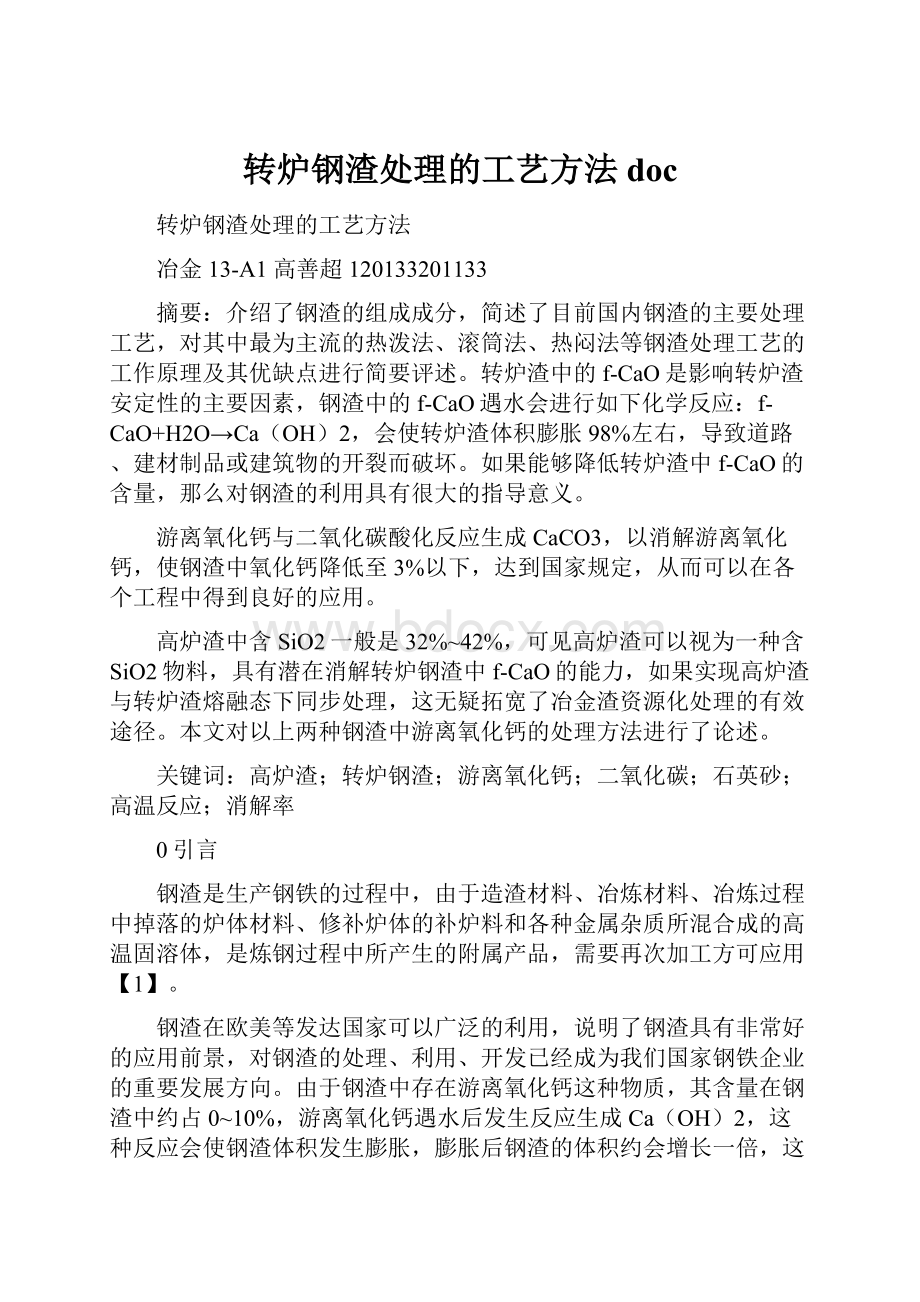
转炉钢渣处理的工艺方法doc
转炉钢渣处理的工艺方法
冶金13-A1高善超120133201133
摘要:
介绍了钢渣的组成成分,简述了目前国内钢渣的主要处理工艺,对其中最为主流的热泼法、滚筒法、热闷法等钢渣处理工艺的工作原理及其优缺点进行简要评述。
转炉渣中的f-CaO是影响转炉渣安定性的主要因素,钢渣中的f-CaO遇水会进行如下化学反应:
f-CaO+H2O→Ca(OH)2,会使转炉渣体积膨胀98%左右,导致道路、建材制品或建筑物的开裂而破坏。
如果能够降低转炉渣中f-CaO的含量,那么对钢渣的利用具有很大的指导意义。
游离氧化钙与二氧化碳酸化反应生成CaCO3,以消解游离氧化钙,使钢渣中氧化钙降低至3%以下,达到国家规定,从而可以在各个工程中得到良好的应用。
高炉渣中含SiO2一般是32%~42%,可见高炉渣可以视为一种含SiO2物料,具有潜在消解转炉钢渣中f-CaO的能力,如果实现高炉渣与转炉渣熔融态下同步处理,这无疑拓宽了冶金渣资源化处理的有效途径。
本文对以上两种钢渣中游离氧化钙的处理方法进行了论述。
关键词:
高炉渣;转炉钢渣;游离氧化钙;二氧化碳;石英砂;高温反应;消解率
0引言
钢渣是生产钢铁的过程中,由于造渣材料、冶炼材料、冶炼过程中掉落的炉体材料、修补炉体的补炉料和各种金属杂质所混合成的高温固溶体,是炼钢过程中所产生的附属产品,需要再次加工方可应用【1】。
钢渣在欧美等发达国家可以广泛的利用,说明了钢渣具有非常好的应用前景,对钢渣的处理、利用、开发已经成为我们国家钢铁企业的重要发展方向。
由于钢渣中存在游离氧化钙这种物质,其含量在钢渣中约占0~10%,游离氧化钙遇水后发生反应生成Ca(OH)2,这种反应会使钢渣体积发生膨胀,膨胀后钢渣的体积约会增长一倍,这种情况制约了钢渣的使用方向,使其很难在建材与道路工程中加以使用。
由于我国正处于高速发展中,各项基础设施建设需要建设,其中高速公路的发展快速,如果可以将处理后的钢渣应用其中,代替其他岩土材料,可以降低建设成本,降低其他材料的消耗,有效的处理了堆积巨大的废弃钢渣,达到实际的经济效益【1-2】。
因此对钢渣进行合理的处理并应用已经成为我国钢铁企业重要的发展方向之一。
1.高炉渣的组成及用途
1.1高炉渣的化学组分
高炉渣是冶炼生铁时从高炉中排出的废渣。
高炉冶炼时,从炉顶加人铁矿石、燃料(焦炭)以及助熔剂等,当炉内温度达到1300~1500℃时,物料熔化变成液相,在液相中浮在铁水上的熔渣,通过排渣口排出,这就是高炉渣。
高炉渣是由CaO、MgO、Al2O3、SiO2、MnO、Fe2O3等组成的硅酸盐和铝酸盐。
SiO2、MnO、CaO和MgO是高炉渣的主要成分,它们在高炉渣中占95%以上。
由于矿石品位和冶炼生铁品种不同,高炉渣的化学成分变动较大。
高炉矿渣属于硅酸盐质材料,它的化学组成与天然岩石和硅酸盐水泥相似。
因此,可以代替天然岩石和作为水泥生产原料等使用。
1.2高炉渣的矿相成分
高炉渣是在铁矿石提取冶金过程中矿石脉石、焦炭灰分、熔剂等形成的硅酸盐熔体,其化学成分主要是Ca、Si、Al、Mg等的氧化物,矿物组成主要是硅酸二钙(2CaO·SiO2)、假硅灰石(CaO·SiO2)、钙铝黄长石(2CaO·Al2O3·SiO2)、钙镁黄长石(2CaO·MgO·SiO2)、硅长石(CaO·Al2O3·2SiO2)、钙镁橄榄石(CaO·MgO·SiO2)、镁蔷薇辉石(3CaO·MgO·2SiO2)及镁方柱石(2CaO·MgO·2SiO2)等。
多数情况下高炉渣可视为CaO-SiO2-Al2O3的伪三元系,其中,SiO2和Al2O3主要来自脉石和焦炭中的灰分,CaO和MgO主要来自熔剂[24]。
高炉终渣温度一般与铁水相当或略高于铁水,在1400~1550℃之间。
1.3高炉渣的性质
高炉渣冷却方式不同,得到的炉渣性能不同。
(1)水渣高炉熔渣在大量冷却水的作用下急冷形成的海绵状浮石类物质。
在急冷过程中,熔渣中的绝大部分化合物来不及形成稳定化合物,而以玻璃体状态将热能转化为化学能封存其内,从而构成了潜在的化学活性。
(2)重矿渣高温熔渣在空气中自然冷却或淋少量水慢速冷却而形成的致密块渣。
重矿渣的物理性质与天然碎石相近,其块渣容重大多在1900kg/m3以上,其抗压性、稳定性、抗冻性、抗冲击能力(韧性)均符合工程要求,可以代替碎石用于各种建筑工程中。
(3)膨珠膨珠大多呈球形,粒径与生产工艺和生产设备密切相关。
膨珠表面有釉化玻璃质光泽,珠内有微孔,孔径大的350~400μm,其堆积密度为400~1200kg/m3。
1.4高炉渣处理方法
目前国内外在生产上应用的高炉渣处理方法基本上是水淬法和干渣法。
由于干渣处理环境污染较为严重,且资源利用率低,现在已很少使用,一般只在事故处理时,设置干渣坑或渣罐出渣[3]。
目前,高炉渣处理主要采用水淬法。
按水渣的脱水方式,水淬法主要有如下方法。
(1)转鼓脱水法:
经水淬或机械粒化后的水渣流到转鼓脱水器进行脱水,前者为INBA法(因巴法),后者为TYNA法(图拉法)。
图拉法在我国已获得国家发明专利,专利名称为冶金熔渣粒化装置,专利权人为中冶集团包头钢铁设计研究总院,为俄罗斯与我国共同发明。
(2)渣池过滤法:
渣水混合物流入沉渣池,采用抓斗吊车抓渣,渣池内的水则通过渣池底部或侧面的过滤层进行排水。
底滤式加反冲洗装置,一般称为OCP法(底滤法)。
(3)脱水槽法:
水淬后的渣浆经渣浆泵输送到脱水槽内进行脱水,这种方法就是通常所说的RASA法(拉萨法)。
我国大多数高炉采用的是深水底滤法(OCP),西方国家大部分采用因巴法(INBA)。
2.转炉渣的结构
2.1转炉渣的化学成分
转炉钢渣是转炉炼钢产生的一种废渣,是出炉状态温度高达1400℃以上的液体,化学成分CaO含量为40%~60%,SiO2含量为13%~20%,主要矿物相是硅酸三钙(C3S)、硅酸二钙(C2S)、钙铁橄榄石、游离氧化钙(f-CaO)、游离氧化镁等。
由于游离氧化钙(f-CaO)、游离MgO等有害成分含量高,冷却处理后的钢渣中含有大量结晶粗大、结构致密的f-CaO和离MgO,这些f-CaO和游离MgO遇水后会在很长时间内持续水化并发生体积膨胀,导致钢渣利用时长期安定性极差,严重制约了钢渣的安全利用。
2.2转炉渣的矿相成分
钢渣中矿物成分主要为硅酸二钙(C2S)、硅酸三钙(C3S)、铁酸钙或者铁酸二(CaO·Fe2O3/2CaO·Fe2O3)、RO相、尖晶石相、橄榄石(CaO·RO·SiO2)等,其中游离氧化钙(fCaO)和C2S、C3S为主要成分,总量在50%以上[4]。
钢渣具有较高的碱度时,其碱度R>3,钢渣中矿物成分含量依次为C3S,C2S、RO相、2CaO·Fe2O3、fCaO。
钢渣具有较低的碱度时,钢渣中矿物成分含量依次为C2S,RO相、2CaO·Fe2O3、C3S、f-CaO。
钢渣的碱度R<1.5时,在钢渣中还可能有钙镁橄榄石、镁蔷薇辉石、黄长石等矿物的出现[5-6]。
2.3转炉渣中的f-CaO
转炉渣的膨胀机理是渣中的f-CaO在水化过程中遇水生成Ca(OH)2后,体积增加97.9%,导致转炉渣严重膨胀而影响了其稳定性。
转炉渣中的f-CaO主要有两个来源。
一是炼钢造渣过程中,有一部分CaO经高温锻烧未化合,形成了f-CaO,结构比较致密,水化很慢;二是缓冷过程中,热渣中的C3S(3CaO·SiO2)极不稳定,在1250~1100℃时由稳定相转变为亚稳相,从而发生矿物的相变,C3S易析出C2S和f-CaO,C2S在675℃再次发生相变,由β一C2S相变成γ一C2S[7]。
f-CaO和C2S滞留在转炉渣中,如果发生水化或相变将会严重影响转炉渣的稳定性。
另外,缓冷过程中生成的f-CaO会包裹住C3S使得渣的胶凝性偏低。
钢渣的一些指标
压碎值、磨耗值、磨光值等指标是钢渣的基本指标。
在表1.2显示的是各个钢厂生产的钢渣中的物理力学性质,表1.3显示的是几种岩石的物理力学性质。
从表1.2、表1.3中可以看出,钢渣的稳定性能和强度值等基本指标都能够满足在冶金工业、城市建筑、道路交通中使用要求。
和这几种岩石比较之后,钢渣的视密度较大,然而其他的各项指标都和岩石相似,因此可以使用钢渣来代替岩石在各种路面中使用[8-9]。
表1.2钢渣基本的物理力学性质
表1.3几种岩石的物理力学性质
2.4转炉渣的处理方法
为解决上述转炉渣利用问题,人们认识到:
转炉渣组成与物性的不合理,使其无法直接利用,只有将转炉渣出炉后先进行预处理,预处理好的渣一方面利于其中含铁组分的回收,另一方面要保证其组成与结构的基本稳定。
具体包括:
首先将出炉渣进行预处理,或“稳定化”处理,其主旨是预先消除或消解以自由及f-CaO为主的亚稳相,使转炉渣在被利用前组成与结构基本稳定,并利于渣、铁分离【10】。
其次,将预处理好的转炉渣依据需要,进行资源化利用。
为此,相继开发出转炉渣的多种预处理技术。
这类可称之为两步法的转炉渣利用技术,一直延续到今天,并仍起着主导作用。
这类渣处理技术的出现及发展,是转炉渣利用第二阶段的本质标志。
目前,国内转炉渣的生产主要是采用热泼法、水淬法、风淬法、闷罐法、滚筒法、粒化法、转碟法等[11-12]。
转炉渣的处理一般遵循“一破、两选、三筛”的工艺,由于转炉渣的粒径尺寸差异较大,一般情况下需要破碎到一定的粒径再进行分选。
转炉渣中含铁15%~25%,利用价值高,因此首先要选出转炉渣中的铁。
常用分选方法有磁选(强磁和弱磁)、浮选等,然后对转炉渣进行筛分。
经过初步处理,再根据利用方式的不同进行精细加工,可以通过球磨等方式,将转炉渣进一步磨细。
转炉渣活化和碳化后,可制备水泥等材料。
激发活化包括机械激发、化学激发、热力激发等方法。
碳化是利用转炉渣将CO2以碳酸盐的形式永久储存,即CO2矿物固定。
碳化是处理转炉渣、固定CO2气体的有效方法,是大量利用转炉渣、缓解CO2排放压力的有效措施。
在转炉渣利用过程中,单一的转炉渣不能完全发挥利用价值,就需要和其他副产品(如转炉污泥、高炉渣等)混合后再利用【13】。
几种常见的转炉渣处理方法:
1.热闷法
此法是较早开发的转炉渣预处理技术,也是国内钢企最早采用及引进的处理工艺。
原理是将出炉渣置于可封闭罐内,利用出炉渣自身的显热与潜热,喷水对其作用,产生带压蒸汽,从而对钢渣强行“消解”。
对欲处理钢渣没有特殊要求,钢渣消解较彻底,渣铁易于分离,回收铁组分后的尾渣矿物组织比较稳定、均匀,利于后续粗放式利用。
缺点是:
间歇性处理,处理效率很低,占用处理场地大,处理时间偏长,综合处理成本偏高,安全性控制要求也较高。
待熔渣温度自然冷却至300~800℃时,将热态钢渣倾翻至热闷罐中,盖上罐盖密封,待其均热半小时后对钢渣进行间歇式喷水。
急冷产生的热应力使钢渣龟裂破碎,同时大量的饱和蒸汽渗入渣中与f-CaO、f-MgO发生水化反应使钢渣局部体积增大从而令其自解粉化。
此工艺的优点在于渣平均温度大于300℃均适用,处理时间短(10~12h),粉化率高(粒径20mm以下者达85%),渣铁分离好,渣性能稳定,f-CaO、f-MgO含量小于2%,可用于建材和道路基层材料。
其缺点为需要建固定的封闭式内嵌钢坯的热闷箱及天车厂房、建设投入大、操作程序要求较严格、冬季厂房内会产生少量蒸汽【14-15】。
2.水淬法
液态高温渣在流出、下降过程中,被压力水分割、击碎、速凝,在水幕中进行粒化。
水淬工艺会因炼钢设备工艺布置、排渣特点不同而不同。
水淬法有多种处理方法如盘泼一水淬法,滚筒一水淬法等。
盘泼法优点是:
用水强制快速冷却,处理时间短,生产能力大;处理过程粉尘少;钢渣粒度小,可减少破碎、筛分的工作量,便于金属料回收;钢渣游离氧化钙含量较低,改善了钢渣的稳定性,有利于综合利用。
缺点是:
设备投资比较大;处理过程蒸汽直接排放量较大,对厂房和设备寿命有一定影响;操作工艺比较复杂;对钢渣的流动性有一定要求,粘度高、流动性差的钢渣不能用该方法处理【16】。
滚筒水淬法是将熔渣以适宜流速进入滚筒,在离心力和喷淋水作用下,熔渣被水激散并凝成小块而被收集。
在滚筒内同时完成冷凝、破碎及渣、钢分离。
该类方法优点是:
处理量大、效率较高,处理后的钢渣游离氧化钙较低、粒化较为均匀且粒度分布较为理想,自由氧化钙消解也较为理想,渣中铁较少氧化,多以二价铁或金属铁存在,利于后续磁选分离。
缺点是:
对渣流动性要求较高,因冷却速度快,凝渣的相析出经历淬冷的非平衡演化完成,因此其结构内应力较大,化学活性相对较高,并存在时效相变的潜在机制。
3.风碎法(钢渣风碎粒化技术)
风碎法即用压缩气体冲击高温液渣使其碎粒化,此法尚处于完善阶段[17]。
将出炉熔渣倒入中间罐,运到风淬装置处进行处理。
处理时,熔渣流被高速喷出气流打碎并呈抛物线运动,最终落入水池并被捕集。
用于风碎的气体可以是空气、惰性气体或高压蒸汽等,被加热的气体可通过另外热交换装置进行热量回收。
该法处理获得的渣粒粒径较小、粒径分布范围较窄,此法处理的渣冷凝速度最快,自由氧化钙消解也最为彻底,各晶相分布均匀,晶粒非常细小。
颗粒硬度较大,相对其他处理方式,凝渣的结构内应力最大,往往会在一周内或稍长时间出现时效相变与结构重组,重组后的主晶相主要是硅酸二钙,且晶粒变大。
用该法处理转炉熔渣,如采用不同的气体做风碎介质,得到的凝渣微粒在性能上存在较大差异。
采用风碎工艺处理时,同样要求钢渣有良好的流动性与低粘度。
2.5转炉渣的利用
1.循环利用方式
循环利用方式又可以分为大循环和小循环。
循环利用方式是指转炉渣依旧用于烧结、炼铁、炼钢等冶金内部流程,主要用做添加剂。
大循环利用方式是将转炉渣中的CaO、MgO、MnO等成分,使其充当烧结、高炉炼铁的溶剂,也可称为长流程循环利用。
经过处理的转炉渣再加入转炉中充当造渣剂和脱磷剂等,是小循环利用方式,也称为短流程循环利用。
钢铁生产主要是以铁元素为核心的物理和化学反应过程。
随着铁矿石等生产原料的不断加入,除铁元素以外的副产品会越来越多。
无论采取何种循环利用方式,转炉渣的利用量是有限的,而高炉渣、转炉渣等固体副产品会越来越多,企业内循环的利用量有限,却是利用效果好、效益高、可持续的【18-19】。
2.非循环利用方式
(1)转炉渣在筑路方面的应用
将转炉渣用于除冶金过程以外的途径,都可以称为非循环利用方式。
目前,水泥、公路、建筑材料、农业生产、水处理、海洋等都有了利用转炉渣的实践。
另外,利用转炉渣制备塑料橡胶无机填料、硫酸钙晶须等添加剂也取得了成功。
转炉渣生产的新产品用于人居建筑时,应该考虑这些新材料的放射性。
实践表明高炉渣生产仿大理石没有放射性。
(2)转炉渣作为钢渣微粉的应用
将转炉渣磨细为符合应用规定的钢渣微粉并掺和在水泥中应用,已成为国内外研究与应用的一个热点。
国内一般认为转炉渣在生料中的掺量以10%~15%为宜,但也有专家认为掺量可达20%~30%。
与用作筑路材料相比,转炉渣微粉的附加值相对较高,但仍属大宗量低附加值利用的范畴。
随着转炉渣处理技术的发展,我国主要钢铁企业均将转炉渣微粉作为转炉渣大宗量利用的方向之一【20】。
然而,目前转炉渣微粉的规模化利用受到两大因素制约:
①以介质冷却为主导的转炉渣稳定化处理技术无法彻底解决组织稳定性差以及组分不合理问题,所以其只适合于工程质量要求较低的项目,发展空间因此受到制约;②转炉渣自身成分波动较大,加之采用的是非平衡变化处理过程,其组织与结构性能波动也很大。
因冶炼时间、地点不同,所炼钢种不同,入炉原料组成波动或种类、配料不同等诸多影响因素的不确定,而很难实现对转炉渣成分、组织性能实现稳定化、均匀化的有效控制,进而在对其进行大量利用时就很难实现对其质量实现稳定化、标准化控制。
所以,转炉钢渣微粉作为水泥掺和料加以利用,同样存在其资源多样化利用不理想的问题。
(3)转炉渣制备微晶玻璃
利用废渣制备微晶玻璃起于高炉渣。
与国外相比,我国转炉渣微晶玻璃应用研究起步较晚,利用高炉渣、矿渣和尾矿制备微晶玻璃也取得了一定的成绩。
但与高炉渣、矿渣和尾矿相比,转炉渣应用性能更差,制备微晶玻璃难度更大,国内外报道不多。
但是,转炉渣具有化学成分复杂(尤其铁的含量很高)、熔化温度高和晶化时间长等特点,用其制备微晶玻璃的工艺相对复杂,成本高,制成的微晶玻璃颜色较深,应用范围较窄,因此目前转炉渣在制备微晶玻璃中的利用比例一直很低。
但是,转炉渣用来替代现有原料制备微晶玻璃的市场前景是巨大的。
关键是如何低成本解决转炉渣中铁分离、降低熔化温度、控制晶化时间问题【21】。
3.转炉渣高附加值利用
转炉渣的高附加值利用是这些年来转炉渣利用研究新出现的热点。
该类研究针对转炉渣具有多种有价组分的特点,或将其材料化制备具有特定功能的材料,如利用其制备锂离子电池阳极材料、制备水处理剂。
这类研究将有效拓展转炉渣高附加值利用的途径,大大提升其利用的附加值,但困难依然是如何解决转炉渣低资源禀赋的瓶颈问题。
综上,在两步法主导的现行转炉钢渣利用模式下,开拓了转炉渣很多利用途径,也取得了很多瞩目的成果,在一定规模上实现了转炉渣的有效利用。
但是,现行的预处理技术无论如何先进,仍无法、也不可能使转炉渣在低成本、大宗量、多途径利用技术上出现根本性的突破。
从这个意义上讲,革新现有转炉渣利用模式的局限,是实现未来转炉渣利用技术突破的关键。
2.6转炉渣处理利用展望
炼钢生产过程中产生的固体副产品和废弃物主要有:
转炉粉尘和污泥、转炉渣以及废弃耐材[22]。
如果对各种废弃物进行综合利用,将具有显著的社会效益、环境效益和经济效益。
建议在冶金废弃物的处理和利用过程中,结合当地的实际情况,建立具有不同适应性的阶梯利用方式。
除了现有的利用方式外,将固体废弃物做无害化处理后,用于填充矿井、堆山造田、填海造田也是值得研究的[23]。
总体而言,中国钢渣的利用率仍然较低,这源于钢渣应用的众多制约因素。
根据中国目前钢渣的利用情况,应对以下几个方面进行更为深化的研究:
1)对钢渣成分和性能进行深入了解,为钢渣的开发利用提供理论依据。
2)加强钢渣处理技术的研究,以解决钢渣内所含的游离氧化钙(f-CaO)和氧化镁(MgO)遇水后易膨胀的问题,还有由于钢渣中的Ca、Si、Al三大元素相对偏低,所形成的硅酸盐总量与水泥熟料相差过大(近45%)的问题【24】。
3)通过推广钢渣作冶炼(烧结、高炉、炼钢)熔剂的应用技术,充分利用其中所含的铁、钙、镁、锰等成分的同时,还可以节省大量能源。
加强钢渣作回填和筑路材料的研究。
4)由于钢渣中的硅酸二钙和硅酸三钙矿物结晶完整,晶粒粗大致密,粉磨的细度难以达到要求。
所以,制造高性能钢渣微粉的难点在于开发针对钢渣的特殊磨粉工艺和设备。
钢渣是一种“放错了地方的资源”【25-26】。
钢渣的综合利用不但可以消除环境污染,还能够变废为宝创造巨大的经济效益,是可持续发展的有效途径,对国家、对社会都具有十分重要的意义。
3.消解钢渣中游离氧化钙的实验研究
实验1游离氧化钙与CO2和水蒸气反应
3.1.1研究目的
利用转炉炼钢废渣含有游离氧化钙与CO2和水蒸汽反应生成碳酸钙,以达到消除f-CaO的目的。
以此来解决由于转炉炼钢废渣中含有一定量的游离氧化钙,其水化后体积膨胀导致难以作为铺路材料或者建筑原料等进行再生资源综合利用的问题。
3.1.2实验原理
实验原理就是游离氧化钙的碳酸化反应,将CO2、水和钢渣中的f-CaO在一定温度下发生化学反应,生成碳酸钙物质,同时达到固定CO2和快速消解钢渣中f-CaO的目的。
利用CO2对钢渣微粉进行化学改性,降低f-CaO的含量,提高钢渣微粉的化学稳定性,达到国家标准的技术要求,此项技术不但可以改善钢渣微粉的稳定性,而且还可以固定CO2,降低温室气体排放,实现环境友好的可持续发展的低碳循环经济模式。
通过热力学分析,来确定碳酸化反应的可行性及反应时所需的温度。
本课题使用热力学软件HSC对碳酸化反应进行热力学分析。
测得化学反应所需的温度如图3.1所示。
图3.1碳酸化反应的热分析
由HSC热力学软件得出的化学反应温度范围如下:
CaO+CO2(g)=CaCO3298~1159K;(3.1)
CaO+H2O(g)=Ca(OH)2298~788K;(3.2)
Ca(OH)2+CO2(g)=CaCO3+H2O298~1015K;(3.3)
根据热力学分析之后的结果,确定消解实验的温度为600℃、720℃、850℃,运用三种温度进行实验,确定温度与消解率之间的关系。
3.1.3实验材料与实验装置
1.实验材料
实验的原材料选用的是鞍钢的转炉渣。
将其破碎、筛选之后得到0~0.1mm、0.1~0.22mm、0.22~0.5mm三种颗粒大小的钢渣。
经过检验得出,渣样的主要化学成分分析见表3.1。
钢渣的X光衍射测试结果见图3.2所示。
钢渣中的主要矿物为MgO,Fe3O4、CaSiO4和Ca2Fe2O5。
表3.1转炉钢渣中各种成分的质量分数%
图3.2钢渣的X光衍射测试结果
2.实验装置
选用图3.3所示的实验装置进行f-CaO消解实验,主要的目的是通过CO2和水蒸气消解其中的f-CaO,使其转化成为CaCO3,使钢渣在使用过程中不再遇水膨胀。
图3.3实验装置
1-二氧化碳钢瓶;2-针形阀;3-流量计;4-水蒸气发生器;5-精密温度控制装置;6-反应性实验炉;7-石英管;
3.1.4实验方法
本实验的目的就是使用二氧化碳气体和水蒸气与钢渣中的f-CaO发生碳酸化学反应,使f-CaO转化成为Ca(OH)2或者CaCO3,从而消解钢渣中的f-CaO,使其含量降至3%以下,使钢渣在使用过程中不再粉化。
本实验以石英管作为反应器,将其水平放置,并绕中心轴线旋转。
将钢渣放入中间加热段的位置。
控制反应性试验炉的温度(600℃、720℃、850℃),将流量为2L/min的CO2通过缓冲瓶和流量计后,与水蒸气汇合,进入反应性试验炉。
从常温开始,5℃/min升温直至最终温度,恒温5min,使钢渣在反应性管式炉中消解时间分别控制在30、60min。
反应结束之后,将钢渣进行检测,测量f-CaO的含量,比较之后,确定最佳的反应条件。
3.1.5实验步骤和实验方案
1实验步骤
a.破碎,将转炉炼钢废渣放入颚式粉碎机中破碎,破碎粒度≦0.5mm;
b.筛分,将破碎后的钢渣分别按0~0.1mm、0.1~0.22mm、0.22~0.5mm以下三种不同粒径进行筛分,分别放置;
c.混料,不同粒度的钢渣0~0.1mm、0.1~0.22mm、0.22~0.5mm,按照比例混合,料混合比例如表3.2:
表3.2物料混合比例
表中骨料即为经粉碎的不同粒径的钢渣。
d.实验消解:
将混合好的物料放入内径为30mm,长度为400mm的石英管中,将石英管放入反应性试验炉中,启动程序,持续加热至所需恒定温度,并在其一端通入二氧化碳气体并旋转0.5~2h,择优选择1h。
e.反应完全后,冷却至室温,待检测其消解情况。
2实验方案
a.在720℃,100%CO2下,七种配比进行实验以确定最佳的配比;
b.在不同温度下,100%CO2,以S2为例,确定温度对消解情况的影响;
c.在相同的温度下,以S2为例,确定水蒸汽对消解情况的影响;
d.不同温度下,80%CO2、20%H2O,以S2、S3为例,确定水蒸气在不同温度下对消解情况的影响;
3.1.6实验结果数据分析
a.在720℃,100%CO2的条件下,七种配比进行实验,测得实验结果以及消解率见表3.3。
表3.3实验结果及其消解率
由此可见,在同温度和二氧化碳含量下,S6对游离氧化钙消解量最大,其消解率也最高。
b.在不同温度下,100%CO2,以S2为例,确定温度对消解的影响,检测结果以及消解率见表3.4:
表3.4实验结果及其消解率
本次实验以S2为例,由此可见在颗粒配比和二氧化碳含量一定的条