液压系统基本原理.docx
《液压系统基本原理.docx》由会员分享,可在线阅读,更多相关《液压系统基本原理.docx(45页珍藏版)》请在冰豆网上搜索。
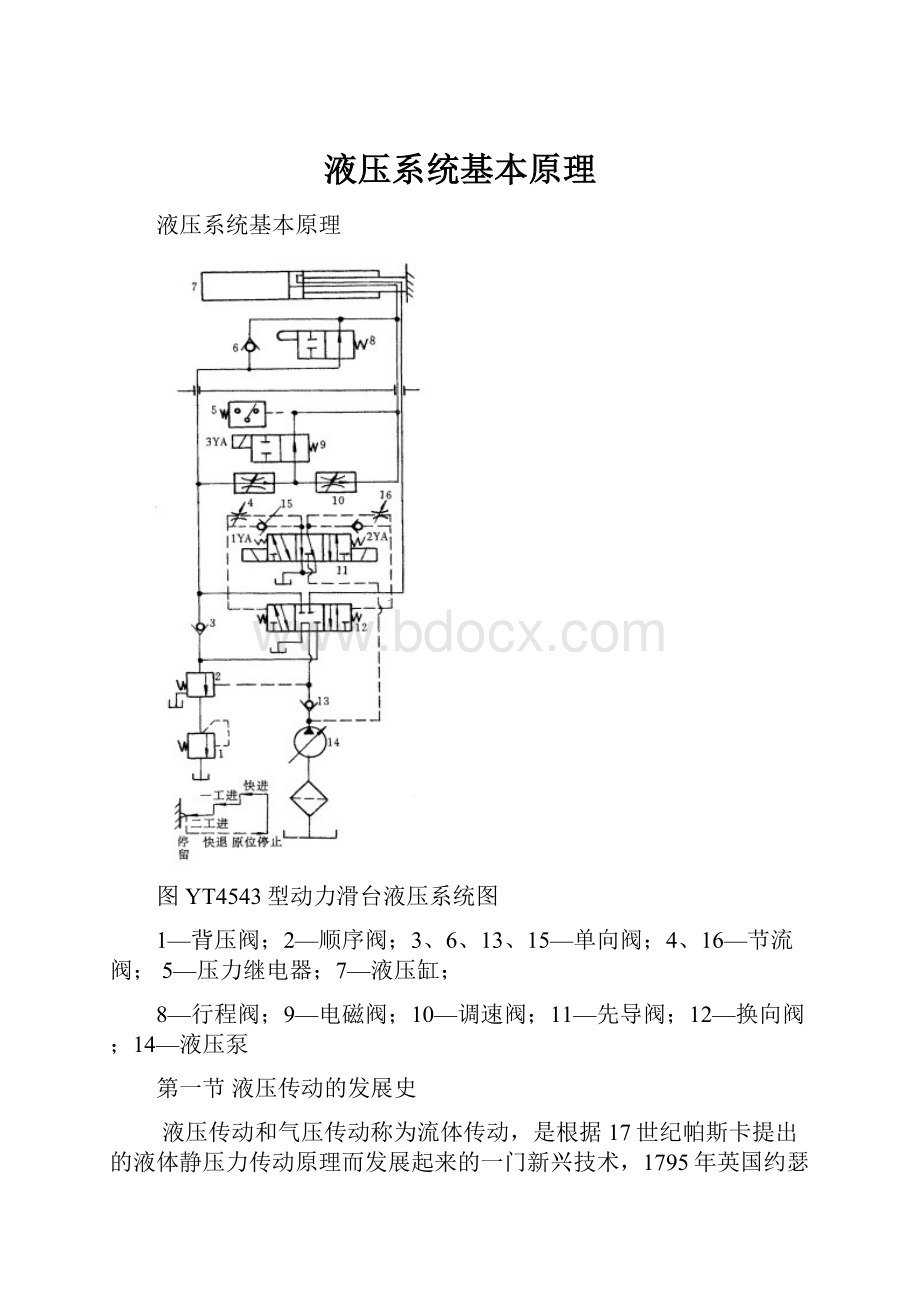
液压系统基本原理
液压系统基本原理
图YT4543型动力滑台液压系统图
1—背压阀;2—顺序阀;3、6、13、15—单向阀;4、16—节流阀;5—压力继电器;7—液压缸;
8—行程阀;9—电磁阀;10—调速阀;11—先导阀;12—换向阀;14—液压泵
第一节液压传动的发展史
液压传动和气压传动称为流体传动,是根据17世纪帕斯卡提出的液体静压力传动原理而发展起来的一门新兴技术,1795年英国约瑟夫?
布拉曼(JosephBraman,1749-1814),在伦敦用水作为工作介以水压机的形式将其应用于工业上,诞生了世界上第一台水压机。
1905年将工作介质水改为油,又进一步得到改善。
第一次世界大战(1914-1918)后液压传动广泛应用,特别是1920年以后,发展更为迅速。
液压元件大约在19世纪末20世纪初的20年间,才开始进入正规的工业生产阶段。
1925年维克斯发明了压力平衡式叶片泵,为近代液压元件工业或液压传动的逐步建立奠定了基础。
20世纪初康斯坦丁?
尼斯克(G?
Constantimsco)对能量波动传递所进行的理论及实际研究;1910年对液力传动(液力联轴节、液力变矩器等)方面的贡献,使这两方面领域得到了发展。
第二次世界大战(1941-1945)期间,在美国机床中有30%应用了液压传动。
应该指出,日本液压传动的发展较欧美等国家晚了近20多年。
在1955年前后,日本迅速发展液压传动,1956年成立了“液压工业会”。
近20~30年间,日本液压传动发展之快,居世界领先地位。
液压传动有许多突出的优点,因此它的应用非常广泛,如一般工。
业用的塑料加工机械、压力机械、机床等;行走机械中的工程机械、建筑机械、农业机械、汽车等;钢铁工业用的冶金机械、提升装置、轧辊调整装置等;土木水利工程用的防洪闸门及堤坝装置、河床升降装置、桥梁操纵机构等;发电厂涡轮机调速装置、核发电厂等等;船舶用的甲板起重机械(绞车)、船头门、舱壁阀、船尾推进器等;特殊技术用的巨型天线控制装置、测量浮标、升降旋转舞台等;军事工业用的火炮操纵装置、船舶减摇装置、飞行器仿真、飞机起落架的收放装置和方向舵控制装置等。
第二节液压系统地组成
一个完整的液压系统由五个部分组成,即动力元件、执行元件、控制元件、辅助元件和液压油。
一、动力元件的作用是将原动机的机械能转换成液体的压力能,指液压系统中的油泵,它向整个液压系统提供动力。
液压泵的结构形式一般有齿轮泵、叶片泵和柱塞泵。
二、执行元件(如液压缸和液压马达)的作用是将液体的压力能转换为机械能,驱动负载作直线往复运动或回转运动。
三、控制元件(即各种液压阀)在液压系统中控制和调节液体的压力、流量和方向。
根据控制功能的不同,液压阀可分为压力控制阀、流量控制阀和方向控制阀。
压力控制阀又分为溢流阀(安全阀)、减压阀、顺序阀、压力继电器等;流量控制阀包括节流阀、调速阀、分流集流阀等;方向控制阀包括单向阀、液控单向阀、梭阀、换向阀等。
根据控制方式不同,液压阀可分为开关式控制阀、定值控制阀和比例控制阀。
四、辅助元件包括油箱、滤油器、油管及管接头、密封圈、压力表、油位油温计等。
五、液压油是液压系统中传递能量的工作介质,有各种矿物油、乳化液和合成型液压油等几大类。
第三节液压的原理
一、它是由两个大小不同的液缸组成的,在液缸里充满水或油。
充水的叫“水压机”;充油的称“油压机”。
两个液缸里各有一个可以滑动的活塞,如果在小活塞上加一定值的压力,根据帕斯卡定律,小活塞将这一压力通过液体的压强传递给大活塞,将大活塞顶上去。
设小活塞的横截面积是S1,加在小活塞上的向下的压力是F1。
于是,小活塞对液体的压强为P=F1/SI,能够大小不变地被液体向各个方向传递”。
大活塞所受到的压强必然也等于P。
若大活塞的横截面积是S2,压强P在大活塞上所产生的向上的压力F2=PxS2截面积是小活塞横截面积的倍数。
从上式知,在小活塞上加一较小的力,则在大活塞上会得到很大的力,为此用液压机来压制胶合板、榨油、提取重物、锻压钢材等。
二、液压的优缺点
与机械传动、电气传动相比,液压传动具有以下优点:
1、液压传动的各种元件,可以根据需要方便、灵活地来布置。
2、重量轻、体积小、运动惯性小、反应速度快。
3、操纵控制方便,可实现大范围的无级调速(调速范围达2000:
1)。
4、可自动实现过载保护。
5、一般采用矿物油作为工作介质,相对运动面可自行润滑,使用寿命长;
6、很容易实现直线运动。
7、很容易实现机器的自动化,当采用电液联合控制后,不仅可实现更高程度的自动控制过程,而且可以实现遥控。
液压传动也存在着一些缺点:
1、由于流体流动的阻力和泄露较大,所以效率较低。
如果处理不当,泄露不仅污染场地,而且还可能引起火灾和爆炸事故。
2、由于工作性能易受到温度变化的影响,因此不宜在很高或
低的温度条件下工作。
3、液压元件的制造精度要求较高,因而价格较贵。
4、由于液体介质的泄漏及可压缩性影响,不能得到严格的传动比。
5、液压传动出故障时不易找出原因;使用和维修要求有较高的技术水平。
第四节液压系统的三大顽疾
一、发热由于传力介质(液压油)在流动过程中存在各部位流速的不同,导致液体内部存在一定的内摩擦,同时液体和管路内壁之间也存在摩擦,这些都是导致液压油温度升高的原因。
温度升高将导致内外泄漏增大,降低其机械效率。
同时由于较高的温度,液压油会发生膨胀,导致压缩性增大,使控制动作无法很好的传递。
解决办法:
发热是液压系统的固有特征,无法根除只能尽量减轻。
使用质量好的液压油、液压管路的布置中应尽量避免弯头的出现、使用高质量的管路以及管接头、液压阀等。
二、振动液压系统的振动也是其痼疾之一。
由于液压油在管路中的高速流动而产生的冲击以及控制阀打开关闭过程中产生的冲击都是系统发生振动的原因。
强的振动会导致系统控制动作发生错误,也会使系统中一些较为精密的仪器发生错误,导致系统故障。
解决办法:
液压管路应尽量固定,避免出现急弯。
避免频繁改变液流方向,无法避免时应做好减振措施。
整个液压系统应有良好的减振措施,同时还要避免外来振源对系统的影响。
三、泄漏液压系统的泄漏分为内泄漏和外泄漏。
内泄漏指泄漏过程发生在系统内部,例如液压缸活塞两边的泄漏、控制阀阀芯与阀体之间的泄漏等。
内泄漏虽然不会产生液压油的损失,但是由于发生泄漏,既定的控制动作可能会受到影响,直至引起系统故障。
外泄漏是指发生在系统和外部环境之间的泄漏。
液压油直接泄漏到环境中,除了会影响系统的工作环境外,还会导致系统压力不够引发故障。
泄漏到环境中的液压油还有发生火灾的危险。
解决办法:
采用质量较好的密封件,提高设备的加工精度。
另:
对于液压系统这三大顽疾,有人进行了总结:
“发烧、拉稀带得瑟”。
YT4543型组合机床动力滑台液压传动系统
(应用举例)
组合机床是由通用部件和部分专用部件组成的高效、专用、自动化程度较高的机床。
它能完成钻、扩、铰、镗、铣、攻丝等工序和工作台转位、定位、夹紧、输送等辅助动作,可用来组成自动线。
这里只介绍组合机床动力滑台液压系统。
动力滑台上常安装着各种旋转着的刀具,其液压系统的功能是使这些刀具作轴向进给运动,并完成一定的动作循环。
图和表分别表示YT4543型组合机床动力滑台液压系统原理图和动作循环表。
这个系统用限压式变量叶片泵供油,用电液换向阀换向,用行程阀实现快进和工进速度的切换,用电磁阀实现两种工进速度的切换,用调速阀使进给速度稳定。
在机械和电气的配合下,能够实现“快进→一工进→二工进→死挡铁停留→快退→原位停止”的半自动循环。
其工作情况如下所述。
1.快进
按下起动按钮,电磁铁1YA通电吸合,控制油路由泵14经电磁先导阀11左位、单向阀15,进入液动阀12的左端油腔,液动阀12左位接系统,液动阀12的右端油腔回油经节流器16和阀11的左位回油箱,液动阀处于左位。
主油路:
泵14→单向阀13→液动阀12左位→行程阀8(常态位)→液压缸左腔(无杆腔)。
回油路:
液压缸右腔→阀12左位→单向阀3→阀8→液压缸左腔。
由于动力滑台空载,系统压力低,液控顺序阀关闭,液压缸成差动连接,且变量泵14有最大的输出流量,滑台向左快进(活塞杆固定,滑台随缸体向左运动)。
表 YT4543型动力滑台液压系统的动作循环表
元件
动作
1YA
2YA
3YA
压力继电器
行程阀
快进(差动)
+
-
-
-
导通
一工进
+
-
-
-
切断
二工进
+
-
+
-
切断
死挡铁停留
+
-
+
+
切断
快退
-
+
?
-
切断→导通
原位停止
-
-
-
-
导通
2.一工进
快进到一定位置,滑台上的行程挡块压下行程阀8,使原来通过阀8进入液压缸无杆腔的油路切断。
此时阀9的电磁铁3YA处于断电状态,调速阀4接入系统进油路,系统压力升高。
压力的升高,一方面使液控顺序阀2打开,另一方面使限压式变量泵的流量减小,直到与经过调速阀4后的流量相同为止。
这时进入液压缸无杆腔的流量由调速阀4的开口大小决定。
液压缸有杆腔的油液则通过液动阀12后经液控顺序阀2和背压阀1回油箱(两侧的压力差使单向阀3关闭)。
液压缸以第一种工进速度向左运动。
3.二工进
当滑台以一工进速度行进到一定位置时,挡块压下行程开关,使电磁铁3YA通电,经阀9的通路被切断。
此时油液需经调速阀4与10才能进入液压缸无杆腔。
由于阀10的开口比阀4小,滑台的速度减小,速度大小由调速阀10的开口决定。
3.死挡铁停留
当滑台以二工进速度行进到碰上死挡铁后,滑台停止运动。
液压缸无杆腔压力升高,压力继电器5发出信号给时间继电器(图中未表示),使滑台在死挡铁上停留一定时间后再开始下一动作。
滑台在死挡铁上停留,主要是为了满足加工端面或台肩孔的需要,使其轴向尺寸精度和表面粗糙度达到一定要求。
当滑台在死挡铁上停留时,泵的供油压力升高,流量减少,直到限压式变量泵流量减小到仅能满足补偿泵和系统的泄漏量为止,系统这时处于需要保压的流量卸荷状态。
3.快退
当滑台在死挡铁上停留一定时间(由时间继电器调整)后,时间继电器发出使滑台快退的信号。
此时电磁铁1YA断电,2YA通电,阀11和阀12处于右位。
进油路:
泵14→阀13→液动阀12右位→液压缸右腔;回油路:
液压缸左腔→单向阀6→阀12右位→油箱。
由于此时为空载,系统压力很低,泵14输出的流量最大,滑台向右快退。
3.原位停止
当滑台快退到原位时,挡块压下原位行程开关,使电磁铁1YA、2YA和3YA都断电,阀11和阀12处于中位,滑台停止运动,泵14通过阀12的中位卸荷(这时系统处于压力卸荷状态)。
YT4543型组合机床动力滑台液压系统包括以下一些基本回路:
由限压式变量叶片泵和进油路调速阀组成的容积节流调速回路,差动连接快速运动回路,电液换向阀的换向回路,由行程阀、电磁阀和液控顺序阀等联合控制的速度切换回路以及中位为M型机能的电液换向阀的卸荷回路等。
液压系统的性能就由这些基本回路所决定。
该系统有以下几个特点:
1采用了由限压式变量叶片泵和进油路调速阀组成的容积节流调速回路。
它既能满足系统调速范围大,低速稳定性好的要求,又提高了系统的效率。
进给时,在回油路上增加了一个背压阀,这样一方面可改善速度稳定性,另一方面可使滑台能承受一定的与运动方向一致的切削力(负值负载)。
2采用限压式变量泵和差动连接两个措施实现快进,既能得到较高的快进速度,又不致使系统效率过低。
动力滑台快进和快退均为最大工作进给速度的倍,泵的流量自动变化,系统无溢流损失,效率高。
3采用行程阀和液控顺序阀使快进转换为工进时,动作平稳可靠,转换的位置精度比较高。
至于两个工进之间的换接则由于两者速度都较低,采用电磁阀完全能保证换接精度。
第五节动力元件常见故障与排除
一、齿轮泵常见故障
(1)故障现象:
泵不能排料
故障原因:
a、旋转方向相反;b、吸入或排出阀关闭;c、入口无料或压力过低;d、粘度过高,泵无法咬料
对策:
a、确认旋转方向;b、确认阀门是否关闭;c、检查阀门和压力表;d、检查液体粘度,以低速运转时按转速比例的流量是否出现,若有流量,则流入不足、
(2)故障现象:
泵流量不足
故障原因:
a、吸入或排出阀关闭;b、入口压力低;c、出口管线堵塞;d、填料箱泄漏;e、转速过低
对策:
a、确认阀门是否关闭;b、检查阀门是否打开;c、确认排出量是否正常;d、紧固;大量泄露漏影响生产时,应停止运转,拆卸检查;e、检查泵轴实际转速;
(3)故障现象:
声音异常
故障原因:
a、联轴节偏心大或润滑不良b、电动机故障;c、减速机异常;d、轴封处安装不良;e、轴变形或磨损
对策:
a、找正或充填润滑脂;b、检查电动机;c、检查轴承和齿轮;d、检查轴封;e、停车解体检查
(4)故障现象:
电流过大
故障原因:
a、出口压力过高;b、熔体粘度过大;c、轴封装配不良;d、轴或轴承磨损;e、电动机故障
对策:
a、检查下游设备及管线;b、检验粘度;c、检查轴封,适当调整;d、停车后检查,用手盘车是否过重;e、检查电动机
(5)故障现象:
泵突然停止
故障原因:
a、停电;b、电机过载保护;c、联轴器损坏;d、出口压力过高,联锁反应;e、泵内咬入异常;f、轴与轴承粘着卡死
对策:
a、检查电源;b、检查电动机;c、打开安全罩,盘车检查;d、检查仪表联锁系统;e、停车后,正反转盘车确认;f、盘车确认
二、叶片泵常见故障排除
1.电动机转向不对;
纠正转向
2.油箱液面过低;
补油至油标线
3.吸油管路或过滤器堵塞;
疏通吸油管路,清洗过滤器
4.电动机转速过低;
使转速达到液压泵的最低转速以上
5.油粘度过大;
检查油质,更换粘度适合的液压油或提高油温
6.配油盘端面磨损;
修磨端面或更换配油盘
7.叶片于定子内表面接触不良;
修磨接触面或更换叶片
8.叶片在叶片槽内卡死或移动不灵活;
逐个检查,对移动不灵活的叶片重新研配
9.连接螺钉松动;
适当拧紧
10.溢流阀失灵;
调整、拆卸、清洗溢流阀
三、柱塞泵故障诊断及排除方法
液压泵是液压系统的动力元件,也是液压系统的心脏部位,一旦
泵发生故障系统就不能正常工作。
而液压系统大量使用柱塞泵,因此掌握柱塞泵的故障对以后液压维护是很必要的。
柱塞泵故障的表现形式有以下几种:
?
?
?
一、柱塞泵工作噪声过大的原因及排除方法
?
?
?
(1)油泵内存有空气。
这个故障一般是在安装了一台新泵的时候出现,在开起一台新泵时,应先向泵内加入油液,对泵的轴承、柱塞与缸体起到润滑作用。
?
?
?
处理方法:
在泵运转时打开油泵加油口,使泵内的空气从加油口排放出去。
?
?
?
(2)油箱的油面过低,吸油管堵塞使得泵吸油阻力变大造成泵吸空或进油管段有漏气,泵吸入了空气。
?
?
?
处理方法:
按规定加足油液;清洗滤清器,疏通进气管道;检查并紧固进油管段的连接螺丝。
?
?
?
(3)油泵与电机安装不当,也就是说泵轴与电机轴同心度不一致,使油泵轴承受径向力产生噪声。
?
?
?
处理方法:
检查调整油泵与电机安装的同心度。
?
?
?
(4)液压油的粘度过大,使得泵的自吸能力降低,容积效率下降。
?
?
?
处理方法:
选用适当粘度的液压油,如果油温过低应开启加热器。
?
?
?
二、轴向柱塞泵工作时压力表指针不稳定的原因及排除
?
?
?
(1)配油盘与缸体或柱塞与缸体之间磨损严重,使其内泄漏和外泄漏过大。
处理方法:
检查、修复配油盘与缸体的配合面;单缸研配,更换柱塞;紧固各连接处螺钉,排除漏损。
?
?
?
(2)如果是轴向柱塞变量泵,可能是由于变量机构的变量角过小,造成流量过小,内泄漏相对增大。
因此,不能连续供油而使压力不稳。
?
?
?
处理方法:
适当加大变量机构的变量角,并排除内部泄漏。
?
?
?
(3)进油管堵塞,吸油阻力变大及漏气等都有可能造成压力表指针不稳定。
?
?
?
处理方法:
进油管堵塞,液流阻力大,可疏通油路管道洗进口滤清器,检查并紧固进油管段的连接螺钉,排除漏气。
?
?
?
三、轴向柱塞泵流量不足的原因及排除方法
?
?
?
表现为执行元件动作缓慢,压力上不去。
?
?
?
(1)油箱油面过低,油管、滤油器堵塞或阻力过大及漏气等。
?
?
?
处理方法:
检查油箱油面高度。
不足时应添加。
油管、滤清器堵塞应疏通和清洗。
检查并紧固各连接处的螺钉,排除漏气。
?
?
?
(2)油泵内运转前未充满油液,留有空气。
?
?
?
处理方法:
从油泵回油口灌满油液,排除油泵内的空气。
?
?
?
(3)油泵中心弹簧折断,使柱塞不能回程,缸体和配油盘密封不良。
?
?
?
处理方法:
油泵中心弹簧弹力不足或折断。
?
?
?
(4)油泵连接不当,使泵轴承受轴向力,导致缸体和配油盘产生间隙,高低油腔串通。
?
?
?
处理方法:
改变连接方法,消除轴向力。
?
?
?
(5)如果是变量轴向柱塞泵,可能是变量角太小。
?
?
?
处理方法:
如果变量轴向柱塞泵变量角过小时,应适当调大。
?
?
?
(6)液压油不清洁,缸体与配油盘或缸体与柱塞磨损,使漏油过多。
?
?
?
处理方法:
检查缸体与配油盘和柱塞的磨损情况,视情况进行修配,更换柱塞。
?
?
?
(7)油温过低,油液粘度下降,造成泵的内泄漏增大,泵并伴有发热的症状。
?
?
?
处理方法:
根据油泵的温升情况,选用合适粘度的液压油。
找出油温过高或过低的原因,并及时排除。
?
?
?
四、轴向柱塞泵油液漏损严重的原因及排除方法
?
?
?
(1)油泵各结合处密封不良,如密封圈损坏。
?
?
?
处理方法:
检查油泵各结合处的密封,更换密封圈。
?
?
?
(2)配油盘与缸体或柱塞与合同工体之间磨损过大,引起回油管外泄漏增加,也会杨起油泵没低压油腔之间的内泄漏。
?
?
?
处理方法:
修磨配油盘和缸体的接触面;研配缸体与柱塞副。
?
?
?
根据经验,泵的故障一般是因为系统油液不清洁引起泵的损坏,泵内进入空气也是造成泵使用寿命降低的原因之一。
要对油液做好维护。
第六节执行元件常见故障与排除
一、液压油缸常见故障及排除方法
今天给大家详细介绍一下液压油缸在日常中常见故障及其排除的方法,希望能够对大家有所帮助。
1)由于经常用工作行程的某一段,造成液压油缸内径直线性不良(局部有腰鼓形),致使液压油缸的高、低压油互通。
应镗磨修复液压油缸内径,单配活塞。
2)缸内有空气侵入,应增设排气装置或使液压油缸以最大行程快速运动,强迫排除空气。
3)液压油缸内油液温升太高、粘度下降,使泄漏增加;或是由于杂质过多,卡死活塞和活塞杆。
应采取散热降温等措施,更换油液。
4)液压油缸的端盖处密封圈压得太紧或太松,应调整密封圈使之有适当的松紧度,保证活塞杆能用手来回平稳地拉动而无泄漏。
5)活塞与活塞杆同轴度不好,应校正、调整。
6)活塞配合间隙过大或密封装置损坏,造成内泄漏。
应减小配合间隙,更换密封件。
7)活塞配合间隙过小,密封过紧,增大运动阻力。
应增大配合间隙,调整密封件的松紧度。
8)活塞杆弯曲,引起剧烈磨擦。
应校直活塞杆。
9)液压油缸安装后与导轨不平行,应进行调整或重新安装。
10)活塞杆弯曲,应校直活塞杆。
11)活塞杆刚性差,加大活塞杆直径。
12)液压油缸运动零件之间间隙过大,应减小配合间隙。
13)液压油缸的安装位置偏移,应检查液压油缸与导轨的平行度,并校正。
14)液压油缸内径直线性差(鼓形、锥形等),应修复,重配活塞。
15)缸内腐蚀、拉毛,应去锈蚀和毛刺,严重时应镗磨。
16)缸筒拉伤,造成内泄漏。
应更换缸筒。
17)双出杆活塞缸的活塞杆两端螺帽摒得太紧,使其同心不良,应略松螺帽,使活塞处于自然状态。
二、液压马达使用中常出现的故障以及处理办法?
三、?
?
?
?
?
1.马达漏油?
?
?
原因:
(1)轴端漏油:
由于马达在日常时间的使用中油封与输出轴处于不停的摩擦状态下,必然导致油封与轴接触面的磨损,超过一定限度将使油封失去密封效果,导致漏油。
处理办法:
需更换油封,如果输出轴磨损严重的话需同时更换输出轴。
?
?
?
?
?
?
(2)封盖处漏油:
封盖下面的“O”型圈压坏或者老化而失去密封效果,该情况发生的机率很低,如果发生只需更换该“O”型圈即可。
?
?
?
?
?
?
(3)马达夹缝漏油:
位于马达壳体与前侧板,或前侧板与定子体,或定子体与后侧板之间的“O”型圈发生老化或者压坏的情况,如果发生该情况只需更换该“O”型圈即可。
?
?
?
?
?
?
2.马达运行无力?
?
?
?
?
?
?
?
?
原因:
(1)定子体配对太松:
由于马达在运行中,马达内各零部件都处于相互摩擦的状态下,如果系统中的液压油油质过差,则会加速马达内部零件的磨损。
当定子体内针柱磨损超过一定限度后,将会使定子体配对内部间隙变大,无法达到正常的封油效果,就会造成马达内泄过大。
表现出的症状就是马达在无负载情况下运行正常,但是声音会比正常的稍大,在负载下则会无力或者运行缓慢。
。
。
解决办法就是更换针柱。
?
?
?
?
?
?
(2)输出轴跟壳体之间磨损:
造成该故障的主要原因是液压油不纯,含杂质,导致壳体内部磨出凹槽,导致马达内泄增大,从而导致马达无力。
解决的办法是更换壳体或者整个配对。
。
。
?
?
?
?
?
?
3.马达外泄漏大?
?
?
?
?
?
原因:
(1)定子体配对平面配合间隙过大:
BMR系列马达的定子体平面间隙应大致控制在的范围内(根据排量不同略有差别),如果间隙超过,将会发现马达的外泄明显增大,这也会影响马达的输出扭距?
?
?
?
?
?
?
?
?
?
?
?
?
?
?
?
?
?
?
?
?
?
。
另外,由于一般客户在使用BMR系列马达时都会将外泄油口堵住,当外泄压力大于1MPa时,将会对油封造成巨大的压力从而导致油封也漏油。
处理办法:
磨定子体平面,使其跟摆线轮的配合间隙控制在标准范围内。
?
?
?
?
?
?
(2)输出轴与壳体配合间隙过大:
输出轴与壳体配合间隙大与标准时,将会发现马达的外泄显着增加(比原因1中所述更为明显)。
解决办法:
更换新的输出轴与壳体配对。
?
?
?
?
?
?
(3)使用了直径过大的“O”型圈:
过粗的“O”型圈将会时零件平面无法正常贴合,存在较大间隙,导致马达泄漏增大。
这种情况一般很少见,解决办法是更换符合规格的“O”型圈。
?
?
?
?
?
?
(4)紧固螺丝未拧紧:
紧固螺丝未拧紧会导致零件平面无法正常贴合,存在一定间隙,会使马达泄漏大。
解决办法是在规定的力矩范围内拧紧螺丝。
。
?
?
?
?
?
?
4.马达不转或者爬行?
?
?
?
?
?
?
?
?
原因:
(1)定子体配对平面配合间隙过小:
如之前所述,BMR系列马达的定子体平面间隙应大致控制在的范围内,这时如果间隙小于,就可能发生摆线轮与前侧板或后侧板咬的情况发生,这时会发现马达运转是不均匀的,或者是一卡一卡的,情况严重的会使马达直接咬死,导致不转。
处理方法:
磨摆线轮平面,使其跟定子体的平面间隙控制在标准范围内。
?
?
?
?
?
?
(2)紧固螺丝拧得太紧:
紧固螺丝拧得太紧会导致零件平面贴合过紧,从而引起马达运转不顺或者直接卡死不转。
解决办法是在规定的力矩范围内拧紧螺丝。
。
?
?
?
?
?
?
(3)输出轴与壳体之间咬坏:
当输出轴与壳体之间的配合间隙过小时,将会导致马达咬死或者爬行,当液压油内含有杂质也会发生这种情况。
。
。
。
。
处理办法只有更换输出轴与壳体配对。
?
?
?
?
?
?
5.其他一些常见的故障:
?
?
?
?
?
?
(1)输出轴断掉:
由于BMR系列马达的输出轴是由露在外部的轴与内部的配油部分焊接起来的,因此该焊接部分的好坏以及外力的作用将直接影响轴的寿命,该故障也是经常发生的,如发生只有更换输出轴。
?