农林大学本科毕业设计说明书地沟油加氢催化裂解法生产生物柴油工厂设计.docx
《农林大学本科毕业设计说明书地沟油加氢催化裂解法生产生物柴油工厂设计.docx》由会员分享,可在线阅读,更多相关《农林大学本科毕业设计说明书地沟油加氢催化裂解法生产生物柴油工厂设计.docx(24页珍藏版)》请在冰豆网上搜索。
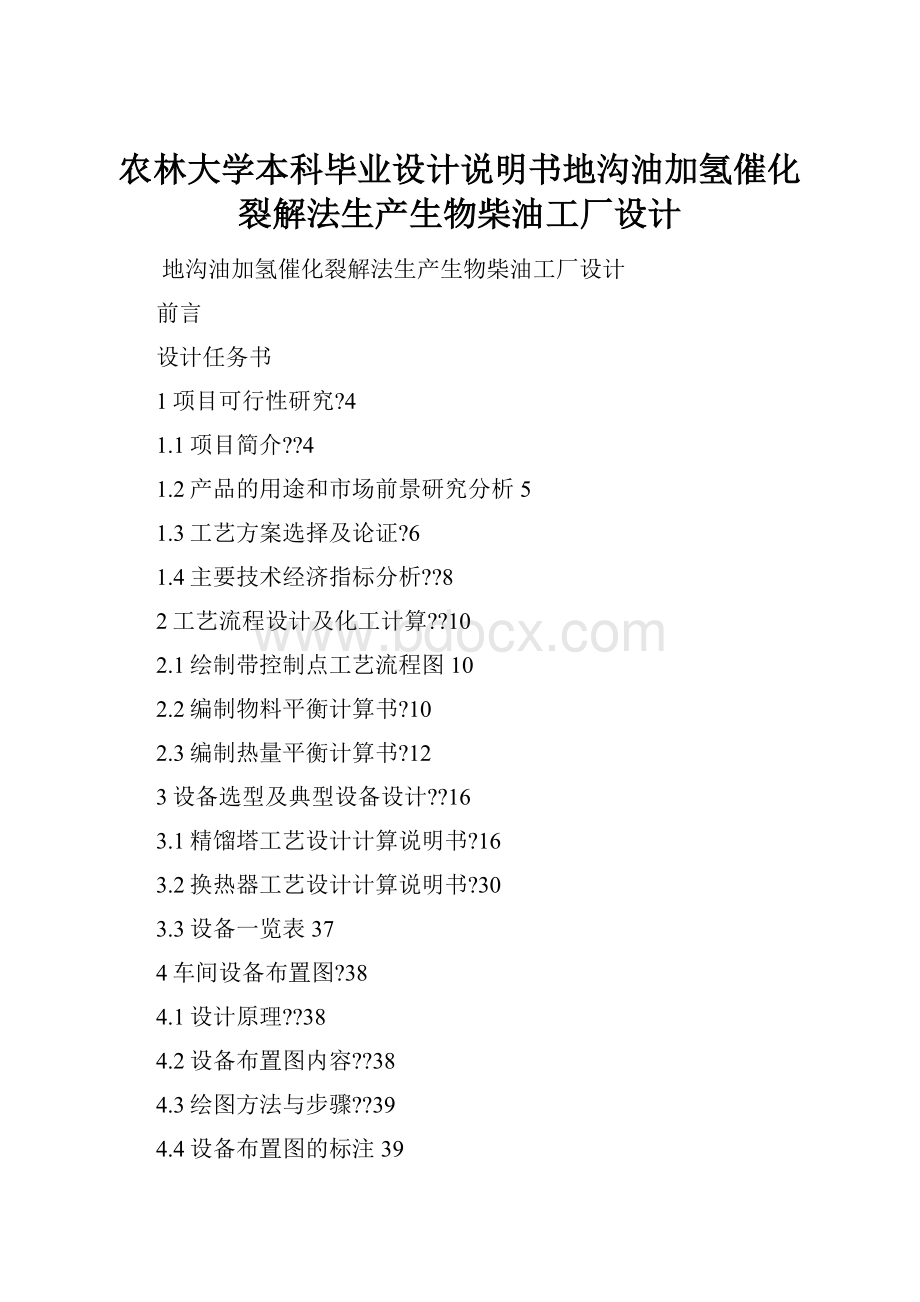
农林大学本科毕业设计说明书地沟油加氢催化裂解法生产生物柴油工厂设计
地沟油加氢催化裂解法生产生物柴油工厂设计
前言
设计任务书
1项目可行性研究?
4
1.1项目简介?
?
4
1.2产品的用途和市场前景研究分析5
1.3工艺方案选择及论证?
6
1.4主要技术经济指标分析?
?
8
2工艺流程设计及化工计算?
?
10
2.1绘制带控制点工艺流程图10
2.2编制物料平衡计算书?
10
2.3编制热量平衡计算书?
12
3设备选型及典型设备设计?
?
16
3.1精馏塔工艺设计计算说明书?
16
3.2换热器工艺设计计算说明书?
30
3.3设备一览表37
4车间设备布置图?
38
4.1设计原理?
?
38
4.2设备布置图内容?
?
38
4.3绘图方法与步骤?
?
39
4.4设备布置图的标注39
5工厂总平面布置设计?
41
5.1总平面设计的原则?
41
5.2设计思路说明?
?
41
参考文献
附图及心得
前言随着社会的发展和进步,物质、能源的消耗愈来愈多,渐渐处于供不应求的状况,这就需要我们创造更多的资源和可能,如能实现原料-废料-原料的最大限度循环利用,如此就能节省大量的原料资源,又可以减轻废弃物对环境的污染。
特别是,在交通工具发达的现在,单单紧靠不可再生的石油来维持是远远不够的,所以急切需要生物质能源来制造生物柴油、汽油等。
而能够利用各种废弃油脂,尤其是大量废弃食用油。
废弃油脂是近期可依赖的重要资源,依据我国人民的饮食习惯,每年需要大量的食用油。
我国目前食用油消费量约为2500万吨/年包括动物油脂,并且每年还在不断增加,估计每年废弃食用油的数量大约在375~625万吨。
因此利用可用资源废油脂设计生产工艺,我们运用《化工厂设计》这门知识能较好地完成任务。
课程设计是本课程教学中综合性和实践性很强的环节,是理论联系实际的桥梁。
通过课程设计,要求学生能综合运用本课程和前修课程的基本知识,进行融会贯通、独立思考,在规定的时间内完成指定的化工单元操作的设计任务,从而得到化工工程设计的初步训练。
通过课程设计,要求学生了解工程设计的基本内容,掌握化工设计的程序和方法,培养学生分析和决工程实际问题的能力。
此次设计主要完成设计方案的设计工艺流程的选择、物料和热量衡算、生产车间各设备的工艺计算、各设备和换热器的主要尺寸的计算、辅助设备的设计,绘制工艺流程图,固定床反应器,高、低压分离器,精馏塔等主要设备的设计。
研究生物柴油生产的开车、停车、生产等操作。
设计任务书
一设计项目:
地沟油加氢催化裂解法生产生物柴油工厂设计
二设计条件
1.原料规格:
原料为选定城市生产的废油脂,先期采用过滤、漂白和脱臭等处理措施,含水量低于3%,氧化值低于5,酸值为88mgKOH/g。
日处理量:
350吨,产率约90%。
废油的组成:
成分棕榈酸硬脂酸油酸亚油酸亚麻酸其他
质量分数16.14%7.55%35.19%32.04%3.42%5.66%
2.产品组成:
组成含量
汽油
燃料气含CO225%
富气5%
粗汽油20%
柴油轻柴油25%
重柴油15%
未转化油油浆5%
焦炭5%
3.排污要求:
含固体有机废渣送至总厂锅炉房焚烧处理;工艺废水含有机物总量0.002,用专用管路送至污水处理车间。
4.公用工程:
供电、供水、供惰性气、机修等公用工程由统一安排、配套提供。
5.厂址地形条件:
一侧靠河,另一侧靠国道公路的狭长平地,宽度80cm等。
全年主风向为东南风。
1项目可行性研究
1.1项目简介本项目通过回收“地沟油”来制得生物柴油,厂址选择武汉市,工厂生物柴油年产量为20万吨,原料来源于武汉市本地以及周边城市。
1.1.1当前利用情况本项目利用各种废弃油脂和含油脚料制造生物柴油。
这些资源包括炒菜和煎炸食品过程产生的废油、烤制食品过程中产生的动物性油脂、动物制品常温加工过程中产生的下脚料经过处理得到的动物性油脂、餐饮废油也称泔水油,主要指从剩余饭菜中经过油水分离得到的油脂、地沟油、厨房抽油烟机泠凝的油脂、含油脚料如皮革、橡胶等工业废油等。
废弃油脂是近期可依赖的重要资源,棕榈油作为补充原料,而中国食用油需要大量进口,因此菜籽油、棉籽油以及大豆油不可能作为生物柴油的原料[1]。
依据我国人民的饮食习惯,每年需要大量的食用油。
我国目前食用油消费量约为2500万吨/年包括动物油脂,并且每年还在不断增加,估计每年废弃食用油的数量大约在375~625万吨。
从这些油脂是一种可再利用的资源被人们认识以后,它便成了抢手货,一支捞油回收队伍便应运而生。
仅在上海无证捞油人员达1000人之多,无固定场所、无营业执照、无管理的“三无”废油脂处理加工点上百个,这其中有相当一部分加工点把这些废油经简单处理后,作为精制食用油又重新回到了市场,对居民健康构成了潜在的严重威胁。
这种现象已经发展成全国性的问题,中央电视台及各省市媒体对这种现象都作了跟踪报道,引起了各地政府的高度重视。
近年来,我国部分城市相继出台了“禁止地沟油非法加工”等相关管理条例。
因此地沟油的再利用技术也成为一个新的研究项目,引起了科研工作者的极大关注[2]。
1.1.2产品研发价值方向我国早在十多年前就开始了生物柴油的研究和推广工作。
科技部在“八五”、“九五”、“十五”分别从开发能源作物、生物柴油生产实验、生物柴油车辆实验等层面支持了可再生液体油品的发展,如2004年,科技部高新技术和产业化司启动“十五”国家科技攻关计划项目“生物燃料油技术开发”。
“863计划”支持了生物酶为基础的生物柴油合成新技术,同时支持隔油池垃圾生产生物柴油。
国家发展与改革委员会组织实施“节能和新能源关键技术”国家重大产业技术开发专项,利用油脂类废料和野生植物生产生物柴油关键技术作为节约和替代石油关键技术予以支持,并将生物柴油生产及过程控制关键技术工业化;国家自然科学基金委在生物柴油燃烧实验方面做了一些支持,中国石油化工集团总公司在生物柴油储备技术方面做了一些支持,支持酶技术与高温高压和超临界生物柴油合成方法。
1.1.3厂址选择选择武汉市郊区为厂址,原因如下:
1产量多。
目前武汉市一天的泔水产量在2500吨左右,全年的泔水产量约80~90万吨,这些泔水可产8万吨地沟油。
2交通便利。
由于武汉作为华中地区的交通和运输枢纽,这就给地沟油的流通创造了有利的条件。
目前,湖北省内的地沟油大多数都由省内各市集中到武汉,再由武汉统一往其它省市发货。
泔水产量主要来源于营业面积在80-200?
含、200-800?
含、800-5000?
三个档次的餐饮企业,它们提供的泔水日产量占到武汉市所有餐饮企业日泔水产量总额的比例分别为31.86%、26.36%、30.76%,合计达到88.98%。
根据调查,武汉市的餐饮企业普遍不关心它们的泔水流向问题,有相当部分的前台经理根本就不知道自己餐馆的泔水情况,让厨房自行处理。
大部分连锁餐饮企业各分店的泔水由各店自行处理,如三国英雄、三镇民生甜食馆等;也有连锁餐饮企业总店统一管理的,如亢龙太子等。
只要泔水转运人员能够及时帮餐饮企业运走泔水,处理价格弹性很大。
1.2产品的用途和市场前景研究分析我国生物柴油工业生产比国外晚几年,在2001年之后才陆续有工业装置投产,这主要包括海南正和、福建卓越、四川古衫等,都建立1~2万吨/年左右的生物柴油厂,原料基本都是采用地沟油、酸化油等。
技术上,中石化开发的生物柴油生产技术在石家庄完成中试,并即将工业应用;中石油在南充建立研发基地,大力研究生物柴油,并将建立中试装置;中海油也在积极运作,与各方联系、合作。
我国生物柴油产业逐渐进入推广阶段,目前已达到100kt生物柴油的产能,并且在原料供应和技术应用方面已经逐渐形成自己的特色。
海南正和公司在河北已开发了11万亩黄连木种植基地1亩666.67m2,下同,每年可产果实20-30kt,可获得生物柴油原料8000-10000t,该公司计划在此基础上建立年产生物柴油50-200kt的炼油化工厂。
目前该公司在河北邯郸建成年产10kt的生物柴油工厂。
四川古杉集团建成年产30kt生物柴油工厂。
北京等省市也已经建成一定规模的生产线。
上述这些生产线目前均是利用垃圾油或植物油脚、餐饮废油等为原料生产生物柴油。
在今后5年内,我国将建成年产20-50kt规模的生物柴油产业化示范工程。
1.3工艺方案选择及论证
工艺流程图:
a.原料预处理
注:
1废食用油加入口;2贮存罐;3闸阀;4过滤器;5废食用油计量泵;6多管热交换器;7蒸汽锅炉;8真空脱水、脱臭塔;9冷凝器;10真空表;11真空装置废食用油首先经过前处理部分1~4,通过在贮存,罐2中经120~140h的静置沉淀后进入滤芯式过滤器4,将油中的杂质除去。
脱水脱臭部分5~11将除去杂质后的废食用油通过多管热交换器6和真空脱水脱臭塔8将油中的水分和臭气除去[3]。
b.催化剂选择随着石油资源的日益短缺,由植物油生产生物柴油的研究日益受到重视。
通常生物柴油是由植物油在碱性或酸性催化剂作用下与甲醇进行酯交换得到的,此反应由于存在环境污染问题或需要高温高压设备,且所得生物柴油凝点较高,所以使用受到限制[4]。
目前比较有代表性的催化剂有加拿大SaskatchewanResearchCouncil大学的负载型CoMoNi硫化态催化剂,柴油收率可达80%以上,十六烷值为90~100,但催化剂容易因硫的流失而失活,所得柴油凝点高于25℃,耗氢量大[5-7]。
Herskowitz采用Pt/SAPO-11催化剂,对植物油进行单段加氢脱氧生成C14~C18的烷烃,同时进一步异构生成异构烷烃,冷滤点从17℃下降为-4℃,但由于发生环化和芳构化反应,造成柴油的十六烷值降为65,且氢耗高。
Murzin等使用Al2O3、SiO2或活性炭负载的Pt、Pd等贵金属,负载量为2%~8%,转化率为62%,正构烷烃选择性为93%。
与加氢脱氧反应相比,氢气消耗量下降了70%~90%,但是催化剂价格昂贵[8]。
运用过渡金属碳化物具有与贵金属Pt和Pd类似的表面性质和吸附特性,对石油馏分的加氢处理、烃的异构化以及碳氧化物的加氢等都具有较高的催化活性.本次采用新型催化剂β沸石负载的碳化钼催化剂具有优良的低碳正构烷烃异构化活性与选择性[9-11]。
对常规的沸石进行改性,调变其表面结构和酸性,有利于植物油大分子的扩散,以及植物油加氢脱羧后长链烷烃的异构化。
本项目采用Mo2C负载量为21.25%的Mo2C/β沸石为催化剂,在压力为3.5MPa、液时空速0.5h-1、氢油体积比500、反应温度280、320℃的条件下,大豆油经过加氢后,凝点下降到-5~-10℃,十六烷值保持在70以上[12]。
c.反应阶段第一代生物柴油主要是脂肪酸低碳醇酯,其中尤以甲酯为主。
在使用过程中有以下缺点:
倘如饱和度高,如棕榈油、牛羊油等生产出来的甲酯其凝固点高,在寒冷季节使用时容易析出并堵塞输送管路;倘如饱和度低,例如用菜籽油、棉籽油等生产出来的甲酯,因为不饱和键含量高,容易氧化变质,不易储存,并影响使用性能。
第二代生物燃料的主要成分是液态脂肪烃,在结构和性能方面更接近石油基燃料,加工和使用都比甲酯类燃料方便,因此,尤其受到石油炼制企业的欢迎。
本项目采用第二代生物燃料的生产方式。
注:
1催化反应器;2气液分离器;3精馏塔油脂直接加氢脱氧是指在高温高压下油脂的深度加氢过程。
此时,羧基中的氧原子和氢结合成水分子,而自身还原成烃。
在该工艺中,不锈钢管式反应器长度为174cm,内径2.28cm,油脂原料和氢气从顶部通过一个导流装置进入到反应器,整个过程模拟喷淋床反应器。
反应器中离中心位置约12.7cm处安放催化剂,用六点电热偶测试催化剂床的温度,反应器外面用环绕加热器加热。
加氢产物从反应器底部流出,通过管道流入气液分离器。
分离出的气体或者作为部分氢气进料循环利用,或者作为加热器的燃料,分离出的液体组分经管道进入分馏柱,分馏成为3部分:
石脑油、柴油和残余馏分。
残余馏分从分馏柱底部流出,可作为加热器的燃料。
加氢反应制备出的柴油馏分中,C15~C18的饱和直链烷烃含量可达到95%,其十六烷值为100甚至更高,密度和黏度都能够达到柴油的质量标准,可以为高十六烷值柴油添加组分与石化柴油进行调配,加入比例可以为5%~30%。
调和物的十六烷值增量与烷烃组分加入量呈线性关系,随着加入量的增加而增加。
1.4主要技术经济指标分析废弃油脂价格随市场变化波动较大,主要是受国内食用油和原油价格波动的共同影响。
目前,废弃油脂收购价已涨至4200~4600/吨左右。
地沟油从当地收集到生物柴油厂之间储运费用约为360~560元/吨,估计到厂价在4560~4760元/吨。
废弃油脂采购存在的主要问题是,废弃油脂的收集和初加工多为地方个体企业,规模较小且分散,无法提供相关票据主要是税票,增值税由原料收购方承担,使生物柴油原料成本增加。
要确保提供价量稳定的废弃油脂,国家必须出台强制性措施。
进口棕榈油在国际市场价格合适的情况下可以作为生物柴油原料的补充。
2工艺流程设计及化工计算
2.1带控制点工艺流程图附图一
2.2物料计算本项目拟定年生产能力10万吨,需废油脂11.2万吨,产率约90%。
按年开工320天计,每天工作24小时。
故日处理约350吨废油脂,每日经过处理后的产量约315吨。
以下计算以每小时的产量为基准。
原料进厂前,先期采用过滤、漂白和脱臭等处理。
2.2.1基本条件
反应式:
RCH2COOHH2RCH3+CO2
废油脂密度0.8g/cm3氢气密度0.9g/L
氢油比:
1000:
1,即每日需氢气量为
350t×1000÷0.8kg/L×1000×0.9g/L4.375×105m3×0.9g/L393.75t
催化剂Mo2Cβ?
沸石的量:
占原料用量2.6%,为350×2.6%9.1t
2.2.2反应前主要成分处理后原料油主要成分有:
棕榈酸十六烷酸16.14%×350t56.49t硬脂酸十八烷酸7.55%×350t26.425t油酸十八碳-顺-9-烯酸35.19%×350t123.165t亚油酸十八碳-顺-9-烯酸32.04%×350t112.14t亚麻酸十八碳-9,12-二烯酸3.42%×350t11.97t其他5.66%×350t19.81t
2.2.3进入反应器
组成含量质量/t相对分子质量物质的量/mol氢气消耗量/mol产物质量/t
棕榈酸16.14%56.49256.43220294.0374220294.03739.74765
硬脂酸7.55%26.425284.4892888.7795392888.779519.36545
油酸35.19%123.165282.47436028.6048872057.2190.02683
亚油酸32.04%112.14280.45399857.37211599429.4981.75084
亚麻酸3.42%11.97278.4442989.513257937.0788.702797
其他物质5.66%19.8119.81计算出日总氢气消耗量为3042606.593mol6.085213t,为0.25355t/h。
故氢气日循环量为16.4-0.2535516.14645t/h,为98.45%
得到的二氧化碳量为52.45t,故进入低压分离器产物总质量为259.4036t+52.45t311.854t故回流的氢气及其他物质为350t-311.854
2.2.4进入低压反应器后
最后产物主要有:
组成含量质量/t
汽油
燃料气
含CO225%78.75
富气5%15.75
粗汽油20%60.00
柴油轻柴油25%78.75
重柴油15%47.25
未转化油油浆5%15.75
焦炭5%15.75
2.2.5单位产品消耗
序号名称消耗指标备注
单位指标
1废油脂t/h14.6
2氢气t/h16.4纯氢气
3催化剂kg/h379.2Mo2Cβ?
沸石
主要原辅材料消耗情况一览表
序号名称年需用量备注
单位数量
1废油脂万t11.2
2氢气万t12.6
3催化剂t2912Mo2Cβ?
沸石
2.3热量计算
2.3.1已知数据
1、生产中以25OC为基准温度
2、原料预处理量为350t/d,即为14.58t/h.查得,废油比热容为2.30KJ/kg?
OC,取原料油密度0.8×10kg/m3,
3、水热容4.18kJ/kg?
0C,冷凝水初始温度为25℃,升温后温度变为40℃,
4、氢气的比热容为7.243KJ/kg?
OC
5、气态二氧化碳比热容为5.904KJ/Kg?
OC
2.3.2计算过程
由生产能力和工艺要求可知,混合的反应物中原料油为14.58t/h.,氢气量中,有循环气的20%以及加入的新氢,依据物料衡算可知该氢气量为m216.15×1000×20%+16.4-16.153480kg
原料油与氢混合后以25OC进入换热器,以170OC离开换热器,所消耗的能量Q需油1m1C1Δt114.58×1000×2.30×170-254862.43MJQ需氢1m2C2Δt13480×7.243×170-253654.8178MJQ需14862.43+3654.81788517.2478MJ
2加氢加热炉中,进入温度为170OC,出来温度为280OC,所需提供能量为Q需2Q需油2+Q需氢2m1C1Δt2+m2C2Δt214.58×1000×2.30×280-170+3480×7.243×280-1706461.36MJ
3反应器中,通入280OC的氢油混合物以及循环氢气占总循环氢气的80%,温度为45OC,又由物料衡算可知,循环氢气为16.15t/h。
Q需油3m1C1Δt314.58×1000×2.30×400-2804024.08MJQ需氢3m2C2Δt33480×7.243×400-2803024.677MJQ氢3m3C2Δt316.15×80%×1000×7.243×400-28011229.547MJ反应器所需提供的总热量为Q需34024.08+3024.677+11229.54718278.304MJ
4换热器中,根据热量守恒原理,由计算1可知,原料油与氢混合从25OC升至170OC所需能量Q需1等于反应后的混合物由物料衡算可知,含CO2量为52.45t,氢气量为16.14t,生成油259.40t,将其从400OC降至t产生的热量,即Q需1Q需油4+Q需氢4+Q需C4m油C1Δt4+m氢C2Δt4+mCO2C3Δt416.4
带入数据,得:
259.40×103×2.30×400-t+16.14×103×7.243×400-t+52.45×103×5.904×400-t8517.2478×103
求得:
t391.7OC
5第一台冷凝器,物料进去的温度为391.7OC,出来的温度为45OC,所需带走的热量为Q需5Q需油5+Q需氢5+Q需C5m油C1Δt5+m氢C2Δt5+mCO2C3Δt5
259.40×103×2.30×391.7-45+16.14×103×7.243×391.7-45+52.45×103×5.904×391.7-45354738.8636MJ
设冷凝水初始温度为25℃,经冷凝器升温后温度变为40℃,
所以,冷凝器所需用水量为WQ需5/C水Δt354738.8636×103÷4.18÷40-255657.7×103kg
6由物料衡算可知,由低压分离器底部出来的物料量为M311.854-78.75233.104t,温度为40℃,与分馏塔底部出来物料以及汽提塔出来的物料进行热交换。
由物料衡算表以及反应工艺可知未转化油31.5t,温度为120℃;轻柴油78.75t,温度为90℃;重柴油47.25t,温度为190℃。
这三种物料的最终温度即为室温25℃.根据能量守恒定律可知:
MCΔt6m未CΔt未+m轻CΔt轻+m重CΔt重
带入数据,得:
233.104×103×2.30×t6-4031.5×103×2.30×120-25+78.75×103×2.30×90-25+47.25×103×2.30×190-25
求得t6111.3℃
7对于分馏加热炉,物料进去的温度为111.3OC,出来的温度为120OC,因此需要的热量Q7MCΔt7233.104×103×2.30×120-111.34664.41MJ
2.3.3能量衡算表
设备入口物料/h入口温度OC出口物料/h出口温度OC设备内
换热器一内管原料油14.58t
氢气3480kg25同入口处170交换热8517.2478MJ
外管CO252.45t
氢气16.14t
油259.40t400同入口处391.7
加氢加热炉一原料油14.58t
氢气3480kg170同入口处280提供热量6461.36MJ
反应器原料油14.58t
氢气16.4t280CO252.45t
氢气16.14t
油259.40t400温度400OC,
压强7.85Mpa,
液时空速0.5h-1,
氢油体积比1000
冷凝器CO252.45t
氢气16.14t
油259.40t391.7同入口处45带走热量354738.8636MJ,用水5657.7×103kg
高压分离器CO252.45t
氢气16.14t
油259.40t温度45OC,
压强8.0Mpa
低压分离器CO252.45t
油259.40t温度40OC,
压强2.5Mpa
换热器二
内管油259.40t40同入口处111.3外管轻柴油78.75t,90OC;重柴油47.25t,190OC,未反应油31.5t,120OC25
分馏加热炉油259.40t111.3同入口处120供热4664.41MJ
分馏塔油259.40t120塔顶:
燃料气、富气、粗汽油;塔底:
油浆、焦炭塔顶温度70OC,塔底温度120OC,压强0.3MP
汽提塔塔顶:
轻柴油;塔底:
重柴油塔顶温度90OC,塔底温度190OC,压强0.8MP
3设备选型及典型设备设计
3.1精馏塔工艺设计计算说明书
3.1.1设计任务
1设计题目:
辛烷-十六烷体系板精馏塔设计
2已知条件:
5500kg/h原料,xF20%,xD≥95%,xW≤2%,单板压降≤0.7kPa
3设计要求
能满足工艺条件,达到指定的产量和质量。
操作平稳,易于调节。
经济合理
生产安全
4化工生产对塔设备的要求
1生产能力大。
2高的传质传热效率。
3操作稳定,操作弹性大。
3.1.2设计方案选定
3.1.2.1精馏方式:
本设计采用连续精馏方式。
原料液连续加入精馏塔中,并连续收集产物和排出残液。
其优点是集成度高,可控性好,产品质量稳定。
3.1.2.2操作压力:
本设计选择常压,常压操作对设备要求低,操作费用低,适用于辛烷-十六烷这类非热敏沸点在常温工业低温段物系分离。
3.1.2.3塔板形式:
根据生产要求,选择结构简单,易于加工,造价低廉的筛板塔