毕业论文分油机的工作原理及故障分析.docx
《毕业论文分油机的工作原理及故障分析.docx》由会员分享,可在线阅读,更多相关《毕业论文分油机的工作原理及故障分析.docx(15页珍藏版)》请在冰豆网上搜索。
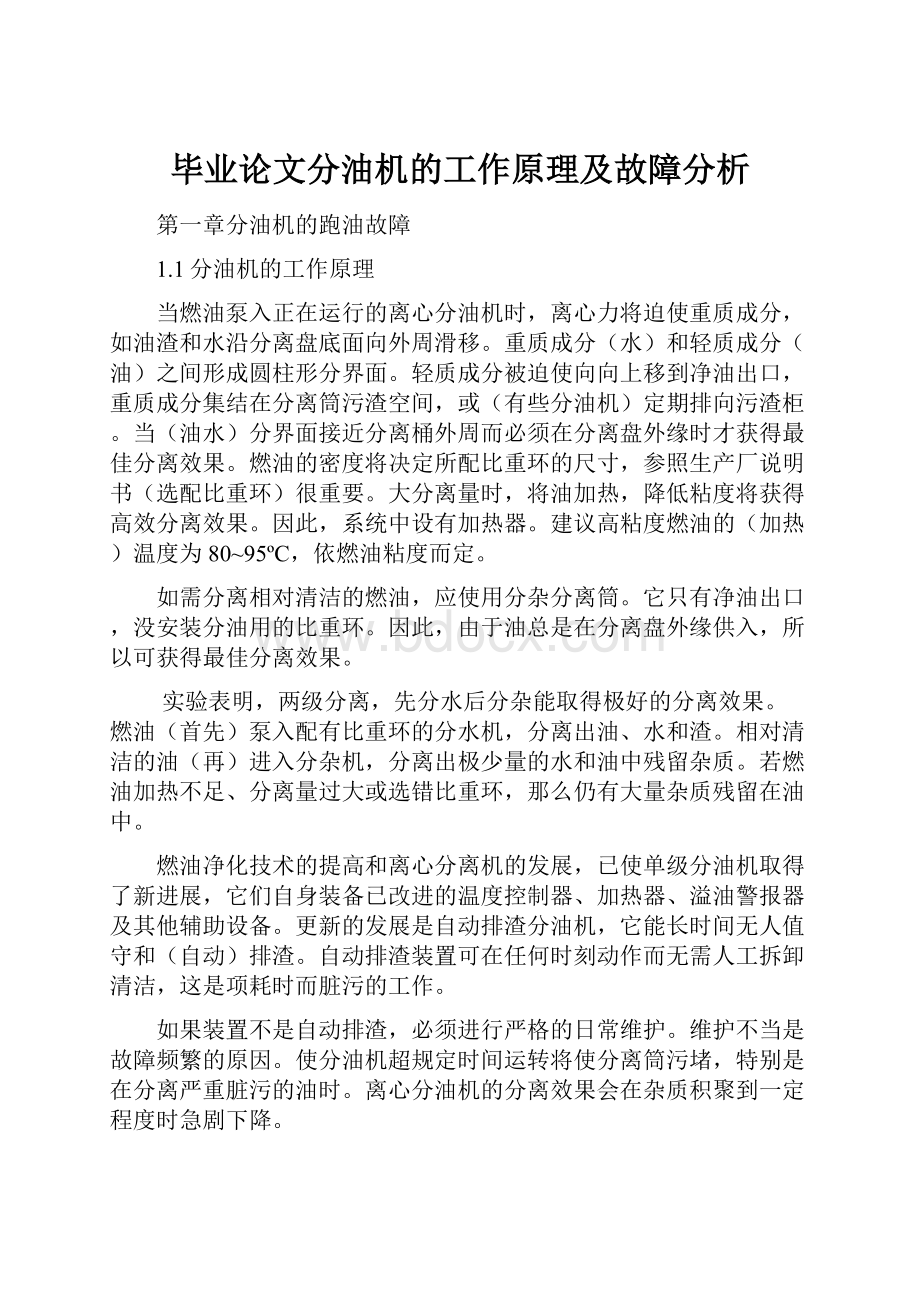
毕业论文分油机的工作原理及故障分析
第一章分油机的跑油故障
1.1分油机的工作原理
当燃油泵入正在运行的离心分油机时,离心力将迫使重质成分,如油渣和水沿分离盘底面向外周滑移。
重质成分(水)和轻质成分(油)之间形成圆柱形分界面。
轻质成分被迫使向向上移到净油出口,重质成分集结在分离筒污渣空间,或(有些分油机)定期排向污渣柜。
当(油水)分界面接近分离桶外周而必须在分离盘外缘时才获得最佳分离效果。
燃油的密度将决定所配比重环的尺寸,参照生产厂说明书(选配比重环)很重要。
大分离量时,将油加热,降低粘度将获得高效分离效果。
因此,系统中设有加热器。
建议高粘度燃油的(加热)温度为80~95ºC,依燃油粘度而定。
如需分离相对清洁的燃油,应使用分杂分离筒。
它只有净油出口,没安装分油用的比重环。
因此,由于油总是在分离盘外缘供入,所以可获得最佳分离效果。
实验表明,两级分离,先分水后分杂能取得极好的分离效果。
燃油(首先)泵入配有比重环的分水机,分离出油、水和渣。
相对清洁的油(再)进入分杂机,分离出极少量的水和油中残留杂质。
若燃油加热不足、分离量过大或选错比重环,那么仍有大量杂质残留在油中。
燃油净化技术的提高和离心分离机的发展,已使单级分油机取得了新进展,它们自身装备已改进的温度控制器、加热器、溢油警报器及其他辅助设备。
更新的发展是自动排渣分油机,它能长时间无人值守和(自动)排渣。
自动排渣装置可在任何时刻动作而无需人工拆卸清洁,这是项耗时而脏污的工作。
如果装置不是自动排渣,必须进行严格的日常维护。
维护不当是故障频繁的原因。
使分油机超规定时间运转将使分离筒污堵,特别是在分离严重脏污的油时。
离心分油机的分离效果会在杂质积聚到一定程度时急剧下降。
对安装在无人机舱的自动排渣分油机,控制的设置是这样的:
一台分油机故障时,另一台备用机自动投入运行。
分油机装有电动计时器用于控制分离筒的排渣周期,程序控制装置控制各种排渣操作。
分油机必须配有声光警报器,以便运转不正常时报警。
当在报警状态时,分油机应停止运转或燃油循环阀打开,油在外围循环而不致跑油。
为控制分离筒的油水分界面,净油出口安装了定压控制阀。
当施加高背压时,油水分界面外移,反之移。
当油中有大量水时,必须特别注意,(加热)温度应在水的沸点以下,否则油就会起泡且混浊。
在这种情况下必须在小分离量下工作以获得合理的分离效果。
a油的处理
燃油和滑油在进入主机之前都要经过处理。
油的处理包括储存,为使油中的水分离而进行的加热;为除去固体颗粒而进行的粗细过滤以及离心分离。
离心式分离机用来分离两种液体,如油和水;或者用来分离液体和固体,如污油。
使用分离机可加快分离速度,且可将分离安排成一个连续的过程。
当分油机用来分离两种液体时,叫做“分水机”。
当分油机用来分离油中的杂质和少量水时,叫做“分杂机”。
从燃油中分离出杂质和水,对良好燃烧是极为重要的。
从滑油中除去污染杂质将会减少机器磨损和可能的损坏。
b离心分离
离心分油机由驱动立轴的电动机和在此立轴上端安装的分离筒组件组成。
分离筒组件外是机壳,机壳上带有各种供给和排放接头。
分离筒可以是整体式的,它将分离出来的油渣保留在其中,并以不连续的方式运行。
分离筒也可以制成上、下分开式的,在离心机不间断地运行时,油渣可以排出。
脏油从分离筒中心进入,向上通过一叠分离盘,并从顶部排出。
c分水过程
两种液体的离心分离,如水和油的离心分离导致在两种液体之间形成分界面。
离心机油水分界面的位置对机器的正常运行相当重要。
油水分界面的确定或定位可以通过在分油机出口处使用阻水环,即比重环来实现。
为了便于分离不同密度的油,每台分离机都配有多种直径的比重环。
d分杂过程
含极少水和不含水的油的净化由分杂机分离筒来完成。
在分离筒里杂质和水积聚在筒的周边。
分杂机分离筒只有一个出口。
由于无油水分界面形成,所以无须比重环。
由于油受到最大离心力的作用,所以分离筒以最高得分离效率运转。
e分离盘
水机和分杂机都带有一叠锥形分离盘。
盘数可多达150个,各分离盘之间都有小的间隔。
将水和杂质从油中分离,是在这些分离盘之间进行的。
在分离盘外缘附近一系列对中的孔可以让脏油进入。
离心力使较轻的成分(净油)向流动,而使水和杂质向外流动。
水和杂质形成的油渣沿分离盘下表面向外移动到筒的边缘。
f比重环的选择
密封液体(水)和油之间的分界面应尽可能靠近分离筒边缘。
然而,分界面一定不能离分离筒中心太远,以至油流过顶部分离盘的外边缘,破坏水封,并同水一起排出。
影响分界面位置的因素有:
油的粘度和密度——高密度的油和低密度的油相比,会使分界面更靠近分离筒边缘。
分油量和背压——一般来说,大分油量会使分界面比小分油量更靠近分离筒边缘,净油出口背压的高低会相应地产生同样的效果。
比重环——油水分界面的位置可通过改变出水口即更换比重环来调节。
更换大口径的比重环将使分界面移向分离筒边缘,相反,小口径比重环将使分界面移向分离筒中心。
在给定温度下已知油的密度时,诺谟图可以帮助选择一个试验性的比重环,第一个试用的比重环的孔径直接从诺谟图查找,然而,在实际运转中,最好的结果是在不引起分离筒中水封破坏,或在出水孔外乳化情况下使用最大孔径的比重环。
g排渣
现代分油机能在相当长的时间连续运转。
这是通过周期性定时排渣程序实现的。
在连续运转时,油渣积聚在分离筒边缘,在他们开始影响分油过程之前,排渣程序定时地清除这些油渣。
为了开始排渣,首先停止向分油机供油,用冲洗水将分离筒残油赶出,然后,将水送入分离筒底部的液压系统,打开多个弹簧阀,此“工作水”引起滑动底盘下移,打开分离筒边缘的排渣孔,油渣在离心力的作用下通过这些孔排出。
接着关闭“工作水”供入,滑动底盘再次上移,关闭排渣孔。
水供入分离筒,重新形成水封,再次供油,分离过程继续进行。
h维护
不论运转中是否有排渣过程,分离筒和分离盘均需定期清洁。
在拆卸分离筒时应小心,只能使用提供的专用工具,并注意某些左旋螺纹。
分油机是一个完全平衡的设备,以高速运转,因此所有的零件都应当小心地操作和处理。
1.2分油机的操作
a起动前
分离筒应清理干净并组装完毕。
特别应检查:
刹车已松开,各封盖(对应的框架锁紧环)已由活页销卡紧。
齿轮箱油位应稍高于观察镜中位,工作水箱应充满,控制阀关闭(工作水关闭,分离筒打开)。
注意:
油位决不允许低于观察镜低线。
若观察镜带棱,它们应当直立。
保持观察镜清洁,否则在玻璃面,就会形成一条线而影响油位观察。
若分油机停用(如在夜间),将放残旋塞旋松几圈,防掉残水。
b起动电机
若欲处理的油液要加热,则使其流经预热器循环直到合适的温度。
刚起动不久,分离筒可能开始发生比正常运行是更强烈的振动。
原因通常是因清洁不良造成的(运转部件)失衡。
若振动十分强烈,应停机并清洁分离筒。
在运转期间,摩擦离合器总是发热,特别是放置在摩擦筒上的摩擦片是新的情况下,可通过烧焦产生的烟和气味觉察到。
若是打滑声,则十分正常,并无大碍。
在加速过程中,能耗比正常运转时高。
加速过程时,可能有少许变化,这依摩擦离合器的摩擦片的情况而有所不同。
c密封分离筒
达到合适的转速后,应密封分离筒。
在开始密封操作前,转速指示器的指示转速应对照说明书中的转速表核实。
加速过程时间可变化少许,以摩擦片的磨损程度而定。
开启相应的控制阀,密封分离筒。
待分离筒密封后注液体。
d充注(液体)
充注操作随分水、分杂和浓缩分离,即对带分杂、分水和浓缩分离筒的分油机的操作各不相同。
分杂(分杂分离筒)操作——将流量调节器调定在欲分离流量位置之后打开供油阀。
分水(分水分离筒)操作——供液,通常是水形成液封。
这种液体最好与欲分离的液体温度相同,且必须快速注入。
当从观察镜看到密封液流出使,切断密封液。
将液流调节器调至欲分离的流量。
缓慢打开供油阀。
部分密封液会流出直至达到平衡。
若供油阀开启太快,可能破坏液封而致使轻质液体(油)以错误的路径排出(跑油)。
即从重质液体排出口(出水口)排出。
若出现这种情况,应重新进行充液操作。
将轻质液体排出管调至适当背压(对带油水分界调节设备的分油机,见比重环的选用)。
浓缩(浓缩分离筒)操作——液封自动建立。
。
调至欲分离的流量(见分水操作)。
e运行
特别检查:
分离流量及工作温度恒定,没从传动齿轮箱(油位在运行油位)跑油;若是分水操作,没从出水口跑油;若有该种情况发生,则表明分离筒已堵塞或水封已破坏;若是这样,应立即排渣,而且必须缩短排渣周期;若分离盘已被污渣堵塞,应停机,手工清洗分离筒。
第二章MOPX-205型分油机工作原理及系统概述
在日常工作中,维护管理MOPX-205型分油机,轮机人员需要了解其工作原理及概况,以便出现故障时能快速准确地排除,现叙述如下:
2.1MOPX-205型分油机工作原理
MOPX-205型分油机工作原理是基于油、水分和机械杂质的密度各不相同,密度越大受到的离心力也就越大。
MOPX-205型分油机分离筒和进排装置构造如图2.1所示:
图2.1
1-污油进口;4-净油出口;5-水出口;10-水封水/置换水进口;15-开启水进口;16-密封和补偿水进口;a-水腔;AA-比重环;aa-油腔;B-小锁紧圈;C-液位环;D-配油器;E-顶盖;F-筒盖;G-分离盘组;H-大锁紧环;I-排渣口;ii-渣空间;J-筒本体;K-滑动底盘;L-滑动圈;M-外泄孔;O-弹簧;T-向心水泵;U-向心油泵;VV-配油锥体;Y-开启水腔;Z-配水盘;ZZ-弹簧座
分离筒由分离筒本体J、滑动底盘K、分离筒盖F、配油器D、配油锥体VV和分离盘组G等组成。
油净化发生在分离筒本体中,它依靠分离筒的高速旋转净油、排渣。
筒本体的高速旋转是电动马达经弹性联轴器、摩擦离合器、蜗轮机构传动给立轴,再由立轴带动分离筒本体高速旋转。
待净化的油经污油进口1进入,流过配油器D、配油锥体VV,在分离盘组G进行分离。
净油由顶盖E与液位环C形成的油腔aa,经向心油泵U从净油出口4泵出。
因密度大而被甩在外围的水沿分离盘组外缘上升,经顶盘流至油腔上部的水腔a,溢过比重环AA由向心水泵泵出至水出口5.分出的渣因为密度最大,所以汇集在分离盘组外缘的渣空间ii,通过EPC-41控制单元定时开启排渣口排出。
2.2MOPX-205型分油机系统概况
MOPX-205型分油机滑油净化系统由分油机、检测机构(热电阻、压力开关、温度传感器)、微机处理系统EPC-41、执行机构(电热加温装置、电磁阀、起动控制箱)组成,如图2.2所示:
图2.2
1-分油机;2-组合电磁水阀;3-应急停止按钮;4-EPC-41控制单元;5-电磁阀;6-柔性管;7-流量表;8-高压继电器;9-低压继电器;10-压力表;11-调节阀;12-三通阀;13-温度传感器;14-起动控制箱;15-高置水箱;16-供油泵;17-流量开关;18-电加热
供油泵16将污滑油经电加热装置18、气动三通阀12(电磁阀5控制,当高低油压警报、高低油温警报、振动等故障时污油经C口流回主机循环柜)进入分油机,经过分油机净化,干净的油经流量计7、高压继电器8、低压继电器9从B口流回主机滑油循环柜。
分油机的密封工作水是由高置水箱15提供的,水封水/置换水和开启工作水是由日用热水压力柜提供的压力热水。
EPC-41控制在一定间隔周期(一般30分钟,根据油脏的程度可以自行调节时间间隔)后,产生一个排渣程序,置换水经由组合电磁阀2中一个电磁阀MV10进入分离筒,约二十秒钟后开启工作水经组合电磁阀中的MV15进入开启水腔,活动底盘下移排渣口打开,开始排渣,约三秒钟后密封水经组合电磁阀中的MV16将活动底盘紧压在分离筒盖上,然后水封水进入约三十秒(本船为30S,可调),三通阀停止循环开始进油,分油机开始运行。
MOPX-205型分油机系统的各个电磁阀的通电、电加热装置、分油机的起动、正常分离、排渣、停止都是由EPC-41控制单元控制,它根据检测机构中各个传感器传来的信息、外部指令和部预设的程序来控制整个系统的自动运行。
第三章分油机的跑油故障
某主机型号为Sulzer6RTA52主副机滑油净化系统配以由EPC-41控制单元控制的2台AlfaLavalMOPX-205型分油机,原则上一台分主机滑油,另一台分副机滑油,但通常都只用状态好的2#分油机。
根据船舶正常定速航行期间计算日平均消耗滑油约33KG,但长期以来主机滑油日消耗达到了40-60KG。
停止分油机运行时,滑油日消耗量恢复到正常值30KG左右。
分油机运行期间,警报系统没有声光报警从而自动停止分油工作。
主机滑油系统属于干油底壳式滑油系统,主机滑油循环舱位于油底壳下方,其滑油净化系统如图1所示:
图3.1
1-滑油循环柜;2-污油吸管;3-泵;4-加热器;5-分油机;6-净油;7-滑油泵;8-滤器;9-冷却器;10-冷却水出口;11-柴油机;12-冷水;13-工作水箱;14-水出口;15-污油出口;16-污油箱;17-加热管;18-污油泵出口
此净化系统在柴油机运转中可连续对滑油循环舱1中滑油进行净化处理。
它的工作流程:
污油从吸入管2经泵和加热器4预热后进入分油机5进行净化处理,净油6从分油机出口返回到滑油循环柜中。
滑油中分离出的水和污渣分别由14和15出口排出。
我们检查了净油系统整个管系,没有发现任何泄漏。
但是分油机运转期间看不见有跑油的痕迹,看似正常的运行使得主机滑油日消耗量大幅增加,所以问题根源还是在分油机跑油。
第四章分油机跑油的故障分析
在分油机的管理维护中,分油机难免出现跑油现象,此类故障原因一般有出水口跑油、排渣口跑油以及系统程序设定有误等从而使油料损失。
当跑油故障出现后,应及时推断产生故障的原因,确定故障确切部位,进而采取针对性措施。
为避免或延缓再次发生相同故障,对于提高工作效率,对于跑油现象,轮机员应该熟知可能产生此类故障的原因,这些具有重要意义。
4.1跑油故障原因的分析
分油机跑油故障的出现并没有报警的出现,而只是根据分油机分滑油时主机消耗大幅增加,而且检查了其净油系统相关的管路没有发现泄漏,推断出分油机跑油。
但是从分油机运行过程中发现排渣口没有跑油现象,出水口也无明显跑油现象。
我们对低压继电器PS42(对净油出口低流量监控)进行检查,发现正常,说明水封没有被破坏,没有跑油造成出口低油压现象。
我们推测应该是排渣时出现大量跑油。
随后观察分油机自动排渣过程,分油机正常运转时面板上仅MV1(进油电磁阀)绿灯亮显示净油进行中,显示窗显示着排污倒计时。
排污程序如图3.1所示,正常的排污程序为图中实体部分,而本船分油机排渣时有时为实体部分,有时却多了一个虚线过程。
显然PS42红灯亮,说明出口低流量报警,因排渣后重新进油2秒是正常的,但超过2秒EPC-41控制单元仍接收到低流量信号,说明分油机在此过程跑油。
为此轮机员查阅AlfaLaval公司推荐的故障表,如下表:
表4.1低流量故障原因及排除(PS42)
原因
纠正措施
进水滤器堵、水压低
清洗滤器,保证水压2-6KP
分油机托盘密封圈损坏
更换密封圈
MV15电磁阀(开启水)未动作
检查电路及元件
进油量少、油泵停
检查油泵
电磁阀MV1(进油)与分油机见通道堵
清通管路,检查MV1动作
MV1不动作,油路处于A-C循环
检查MV1阀背压空气,检查阀动作是否正常
油背压太低
调整手动背压阀,保证背压1.5bar
分油机托盘泄漏
拆检分油机
分油机正常运转,突然排渣
检查开启水电磁阀,检查分油机排污部件
根据表所推荐逐一排除,未查出问题。
我们再分析图3.1,EPC-41控制单元第一次接收到低流量信号并未给出声光报警,仅以二极管红灯显示(PS42红灯亮),然后MV1动作切断进油追加一个水封程序进行自我补偿,这就是该单元—自矫正功能。
只有当EPC-41单元第二次接收到低流量报警信号时单元才发出声光报警信号,同时切断进油。
而本船分油机没有报警出现,凭白多了一个水封程序,在表3.1中列出的可能原因我们已经排除,那原因应该就是水封的进水时间不够,使得水封没有完全建立而引发跑油。
本船分油机装船至今所有的时间参数皆按AlfaLaval公司推荐的时间设定,并未根据实际情况做出调整。
分油机说明书中多处提到水封水的时间,推荐30秒但应根据实际情况进行调整。
我们试着调整水封进水时间,当调整到35秒时,运行结果中自矫正现象消失,分油机按图3.1实线部分正常工作,主机滑油日消耗也降至30KG左右。
1PS42灯2秒暗程序执行
实体,超时程序执行虚体
2
10秒
PS422秒不暗
PS422秒暗
图4.1
4.2日常管理工作中分油机跑油的一些原因分析
4.2.1分油机出水口跑油故障
出水口跑油是分油机最常见的故障,原因很多,主要有:
转速不够;比重盘口径不当;进油量过大;分离筒积聚污物太多,分离盘片脏堵;配水盘故障,水封建立不起来;加热不够,进口油温太低;高置水箱水位过低导致托盘没有托起等等。
虽然原因很多,但大多是由排渣口脏堵引起的,只需将分油机进油阀关闭,手动排渣一到两次,故障多能排除。
其它原因,如分油机出油阀没有打开或没有全部打开引起跑油,不属于机械故障,就不再讨论了。
按故障表逐一排查,不仅费时费力,而且可能使问题复杂化甚至根本找不到毛病。
不妨采用这样的思考方式加以分析,例如:
上午分油机正常,下午就跑油了,显然可以排除比重盘径太小;若进油量太大,只需将进油阀关小一点(注意,这时要手动排渣一次,否则,跑油现象未必会停止)。
至于是不是分离筒污物太多,可以查看轮机日志,看是不是到该拆洗分油机的时间了。
根据师傅们的经验,自动排渣式分油机一般一到二个月洗一次就可以了;但若是重油太脏,则应增加排渣次数(调小排渣间隔时间,含渣量低于0.3%的重油,每分离1000升排渣一次)。
配水盘故障,一般是橡皮圈老化,弹性不足,密封性降低所致,应该按照橡皮圈的寿命定期更换;另一种可能是工作水不干净,配水盘脏赌,应该清洗配水盘,更换橡皮圈。
至于“进口油温太低”和“高置水箱水位过低”等原因,目测就能确定。
经上面分析可知,尽管一件事物纷繁复杂,经过条理的分析,就会变得简单清晰。
这种思考方法很重要,可以运用到其它各项工作中去。
4.2.2分油机排渣口跑油故障
发生排渣口漏油(下漏油)是由于排渣口未能封闭,或滑动底盘与排渣胶圈密封不良导致. 具体来讲有以下几种原因:
1)操作水压力不足
软水系统恒压装置的压缩空气泄露而没有及时补充,水系统关闭时压力正常,但开阀后压力不足,操作水管路泄流、脏堵或滤网堵塞,使操作水压力不足而导致滑动活塞下方的关闭水量不足。
处理措施是充加压缩空气和清洗水路滤网。
2)操作水电磁阀失灵或复位不良
操作水电磁阀一直处于进水排渣状态,致使滑动底盘下移处于常开位置,发生从排渣口漏油现象。
处理措施是修理或清洗操作水电磁阀。
3)滑动圈不能上移堵死密封水腔泄水口
分离筒上的小孔M堵死,不能泄水;滑动圈下方弹簧失效;滑动圈上方塑料堵头失严。
4)滑动底盘与分离筒盖不能贴紧
滑动底盘上端面密封环失效;传动齿轮和轴承过度磨损使立轴下沉。
结论:
分油机出现跑油的原因很多,总的来说通常表现为出水口跑油、排渣口跑油。
本例事故的发生是忽视水封进水时间应根据实际情况做出相应的调整,使得分油机在排渣后水封重新建立不起来导致跑油,然而ALFALAVALMOPX-205型分油机的EPC-41控制单元的“自矫正功能”在第一次接收低流量信号时没有声光报警,只是追加一个水封程序重新建立水封,从而使得轮机管理人员忽视了初次水封没有建立而造成跑油现象的存在。
所以,管理人员应注意:
水封水时间参数应根据实际情况具体调试。
常观察二极管面板,注意排渣程序;选定正确、稳定的进机温度;对可能造成跑油的故障源应定期检测。
致
值此论文完成之际,首先衷心地感导师对我的培养和关心。
在导师的精心指导和深切的关怀下,我最终顺利完成了本文的写作。
本文从初稿、修改到定稿,都得到了导师的细心指导,一次次问题的探讨和论证,导师一直都孜孜不倦的指导。
在四年的大学生活中,导师严谨的教学作风、敏捷的思维都使我受益匪浅。
而且,导师在我们的学习生活中平易近人、和蔼可亲都令学生深深景仰。
对我今后的学习、工作和生活都将产生深远的影响,使我铭记一生。
借此机会特向导师表达我最诚挚的意和最真诚的感!
参考文献
[1]AlfaLavalMOPX205InstructionManual.AlfaLavalMarine&PowerCO.LTD
[2]杜荣铭.船舶柴油机[M].海事大学,1999
[3]周明顺.船舶柴油机[M].海事大学,2006.2
[4]白德富,黄连中,福伟.阿法拉伐船用知识竞赛(决赛)题解
(二).航海技术.2000,2:
65-67.
[5]吕凤明,动力设备拆装与操作,:
海事大学,1999.9
[6]满一新,船机维修技术[M].:
海事,1999
[7]詹玉龙,启陆,船舶分油机故障分析和防措施.航海技术.2002.2:
55-57.
[8]谭子良,船用分油机典型故障及其维修注意事项.航海技术.2004.4