武钢7号高炉.docx
《武钢7号高炉.docx》由会员分享,可在线阅读,更多相关《武钢7号高炉.docx(8页珍藏版)》请在冰豆网上搜索。
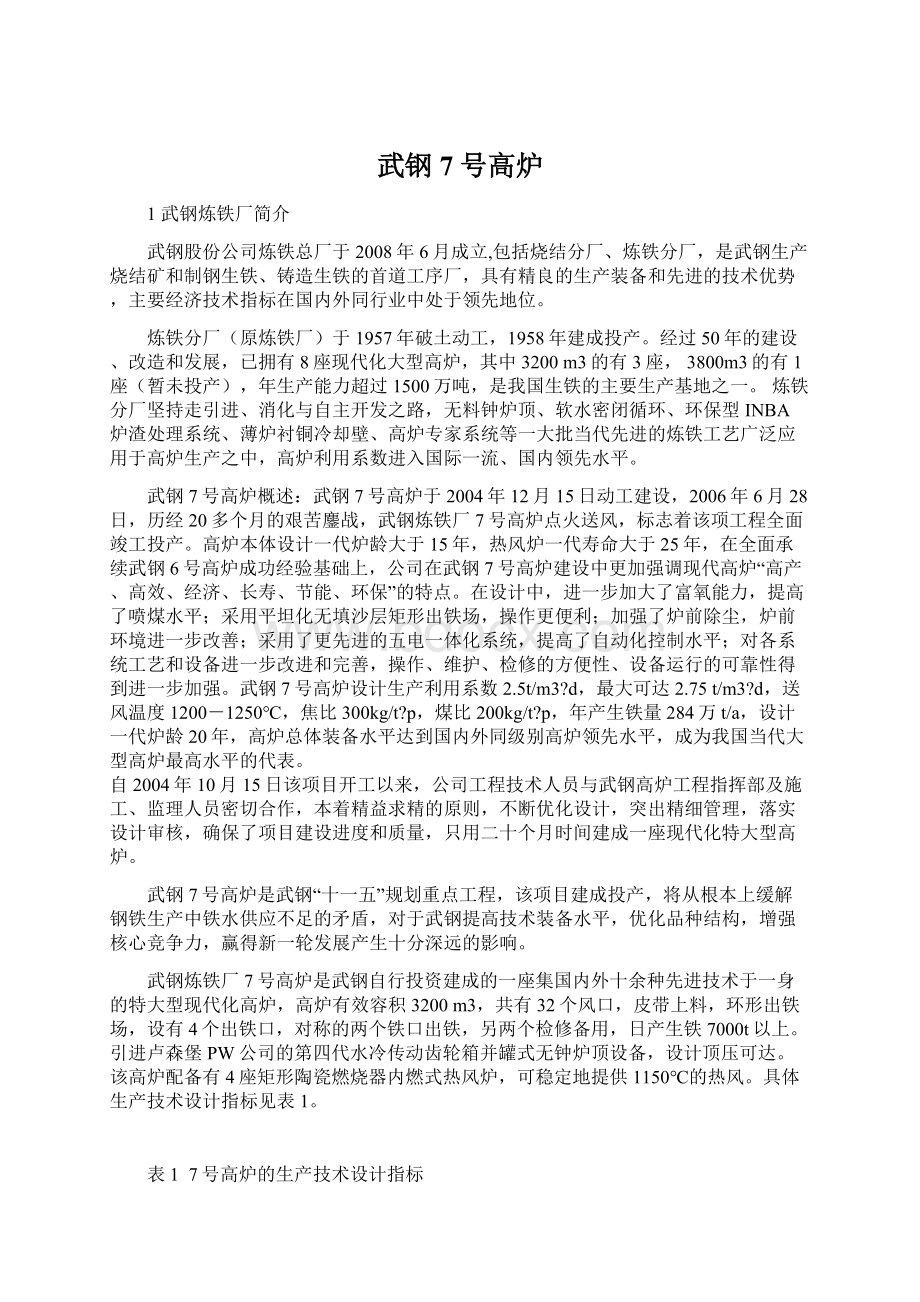
武钢7号高炉
1武钢炼铁厂简介
武钢股份公司炼铁总厂于2008年6月成立,包括烧结分厂、炼铁分厂,是武钢生产烧结矿和制钢生铁、铸造生铁的首道工序厂,具有精良的生产装备和先进的技术优势,主要经济技术指标在国内外同行业中处于领先地位。
炼铁分厂(原炼铁厂)于1957年破土动工,1958年建成投产。
经过50年的建设、改造和发展,已拥有8座现代化大型高炉,其中3200m3的有3座,3800m3的有1座(暂未投产),年生产能力超过1500万吨,是我国生铁的主要生产基地之一。
炼铁分厂坚持走引进、消化与自主开发之路,无料钟炉顶、软水密闭循环、环保型INBA炉渣处理系统、薄炉衬铜冷却壁、高炉专家系统等一大批当代先进的炼铁工艺广泛应用于高炉生产之中,高炉利用系数进入国际一流、国内领先水平。
武钢7号高炉概述:
武钢7号高炉于2004年12月15日动工建设,2006年6月28日,历经20多个月的艰苦鏖战,武钢炼铁厂7号高炉点火送风,标志着该项工程全面竣工投产。
高炉本体设计一代炉龄大于15年,热风炉一代寿命大于25年,在全面承续武钢6号高炉成功经验基础上,公司在武钢7号高炉建设中更加强调现代高炉“高产、高效、经济、长寿、节能、环保”的特点。
在设计中,进一步加大了富氧能力,提高了喷煤水平;采用平坦化无填沙层矩形出铁场,操作更便利;加强了炉前除尘,炉前环境进一步改善;采用了更先进的五电一体化系统,提高了自动化控制水平;对各系统工艺和设备进一步改进和完善,操作、维护、检修的方便性、设备运行的可靠性得到进一步加强。
武钢7号高炉设计生产利用系数2.5t/m3?
d,最大可达2.75t/m3?
d,送风温度1200-1250℃,焦比300kg/t?
p,煤比200kg/t?
p,年产生铁量284万t/a,设计一代炉龄20年,高炉总体装备水平达到国内外同级别高炉领先水平,成为我国当代大型高炉最高水平的代表。
自2004年10月15日该项目开工以来,公司工程技术人员与武钢高炉工程指挥部及施工、监理人员密切合作,本着精益求精的原则,不断优化设计,突出精细管理,落实设计审核,确保了项目建设进度和质量,只用二十个月时间建成一座现代化特大型高炉。
武钢7号高炉是武钢“十一五”规划重点工程,该项目建成投产,将从根本上缓解钢铁生产中铁水供应不足的矛盾,对于武钢提高技术装备水平,优化品种结构,增强核心竞争力,赢得新一轮发展产生十分深远的影响。
武钢炼铁厂7号高炉是武钢自行投资建成的一座集国内外十余种先进技术于一身的特大型现代化高炉,高炉有效容积3200m3,共有32个风口,皮带上料,环形出铁场,设有4个出铁口,对称的两个铁口出铁,另两个检修备用,日产生铁7000t以上。
引进卢森堡PW公司的第四代水冷传动齿轮箱并罐式无钟炉顶设备,设计顶压可达。
该高炉配备有4座矩形陶瓷燃烧器内燃式热风炉,可稳定地提供1150℃的热风。
具体生产技术设计指标见表1。
表1 7号高炉的生产技术设计指标
有效容积
3200m3
炉缸直径
12000mm
炉缸有效高度
4800mm
风口数
32个
铁口数
4个(互成90°)
年产量
324万吨
利用系数
2.0—2.6
入炉焦比
450kg/t
煤比
100—120kg/t
热风温度
1200℃
烧结矿率
80%—85%
渣比
<470kg/t
炉顶压力
利用系数是高炉生产的重要指标之一。
2007年4月,武钢的7号高炉利用系数达2.887吨/立方米·天,这一指标被国家权威部门认定为世界之最;11月,7号高炉利用系数为2.940吨/立方米·天,再次刷新了这一记录。
高炉炼铁过程技术含量极高,其中炉顶布料是核心技术,号称开启高炉高产低耗的“金钥匙”。
由于矿石与焦炭等化学成分不稳定,很难通过准确数据模型测算何时添料与布料,只能以生产经验控制工艺。
武钢在生产全过程导入精细化管理,研发与武钢原燃料条件匹配的高煤比、高风温、大富氧等操作制度与技术,2005年,炼铁厂平均高炉利用系数为2.293,今年上半年达到2.496。
利用系数上涨,说明原材料充分燃烧,同时消耗下降。
2006年,炼铁厂吨铁焦炭消耗量为325.3千克,比上年度下降43.2千克,全年降低炼铁制造成本15亿元。
2.1开炉料的用料结构、装料方式及炉料分布的调整和优化
高炉开炉料的计算、装料方式与分布是整个开炉过程的基础和核心技术,是快速达产的关键。
武钢开炉料的计算一直沿用高度上分成6段的习惯,7号高炉借鉴了武钢其他高炉开炉经验,在各段焦比、碱度、装料顺序、径向的矿焦比、纵向净焦和空料位置进行调整和优化,使经验参数取值更趋合理,理论计算准确性越来越高。
7号高炉开炉料总焦比为3.12t/t,不计净焦碱度0.96,MgO含量10.74%,Al2O3含量14.1%。
炉料结构:
烧结矿+块矿+石灰石+白云石。
开炉焦炭全部采用干熄焦,烧结矿选择13mm以上的大粒度烧结矿。
7号高炉采用炉缸填充枕木开炉,填充方法为“井”字法排列,上下两层采用密排方式装填,其他各层均采用疏排方式充填,风口及炉墙保护用木斜靠炉墙密排列。
2.2装料参数的确定
装料过程中进行料罐最大能力、无料钟炉顶功能测试,炉料的下落轨迹和料面形状测定,观察周向、径向矿石、焦炭分布情况,观测焦炭在高炉中心的堆积情况。
料面测量目的7确定物性参数,校验无料钟设备性能,确定节流阀开度和料流量的关系,校验料流轨迹,测定料面形状,确定开炉布料矩阵。
7号高炉开炉装料轨迹如图1所示。
2.3送风参数的选择
风口布局及进风率是高炉开炉的重要参数。
武钢炼铁厂以前高炉开炉时,一般采用部分风口全开、部分风口堵竹筒及部分风口用泥堵死的方法。
此次7号高炉为实现开炉后迅速恢复炉况并快速达产,改变了堵部分风口的办法,改为全风口送风,进风面积0.4247㎡。
同时,在确定开炉后的布料矩阵时,7号高炉打破了原来的保守思想,果断地将炉料布向9号角位,料线1.3米。
2.4加风曲线的确定
加风曲线是通过装料计算时的热制度、造渣制度和送风后的装料制度、送风制度以及包括炉身静压、煤气成分等参数综合确定的,理论与实际加风曲线如图2所示。
开炉加风曲线的特点主要体现在大风量、高风压点火,点火后控制一定风压操作,在软熔带形成时期和渣铁排出前及下料不畅等引起的透气性变差期间,保持适当的热风压力,采取适当减风控制风压的措施。
当煤气成分趋于稳定软熔带形成后可适当加风,送煤气后加快恢复速度,加风幅度较大,同时配合上、下制度调整,降低软熔带高度,快速降硅增产。
#
。
高炉炉顶采用并罐式无钟炉顶设备,可以使炉顶压力相应提高,有利于高压操作。
并罐式无钟炉顶由受料漏斗、称量料罐、中心喉管、气密箱、旋转溜槽等五部分组成。
旋转溜槽可以完成两个动作:
①绕高炉中心线的旋转运动;
②在垂直面内可以改变溜槽的倾角。
该设备具有以下优点:
①布料理想,调剂灵活;
②设备总高度较低;
③密封性好,能承受高压操作;
④两个称量料罐交替工作。
但其缺点也是很明显的:
①中心喉管磨损较快;
②存在并罐效应。
由于称量料罐中心线和高炉中心线有较大的间距,会在布料时产生料流偏析现象,称之为并罐效应。
3高炉开炉快速恢复及达产措施:
3.1 烧结矿分级入炉新工艺的使用
7号高炉投产初期只使用大粒度烧结矿,投产后的第三天便开始使用小粒度烧结矿。
烧结矿分级人炉技术有如下优越性:
(1)改善了大粒度烧结矿层的透气性,有效控制了装料过程的粒度偏析,同时利用小粒度烧结矿对煤气流阻力大的特点,控制高炉煤气流分布。
既保护炉衬及炉体冷却设备,有利于高炉长寿,又节约能耗,优化指标。
(2)缓解了武钢炼铁原燃料条件波动大的矛盾。
通过调剂大、小粒度烧结矿的比例、用量和小粒度烧结矿的落点,控制煤气流分布,减小炉况波动。
(3)烧结矿分级人炉技术使上部调剂更加灵活。
大粒度烧结矿和小粒度烧结矿可单独使用,也
可以配合使用Ε小粒度烧结矿使用配比可以调整;有利于扩大批重。
并罐无料钟炉顶比串罐无料钟炉顶更具优势。
3.2 上、下部装料制度的调整
砖壁合一薄内衬结构的高炉,设计炉型即是正常操作炉型,因此,在上部调剂中,布料矩阵及用料结构从一开始就接近正常生产水平,大粒度烧结矿从9号角位逐步过渡到9,10号角位,小粒度烧结矿布在边缘区域。
开炉送风时,全部采用加长风口,风量6000m3/min左右。
7月6日在休风处理富氧环管时,对风口布局进行调整,在适当部位扩大.个风口,进风面积扩0.4417㎡时。
在下部进风面积扩大之后,增加大粒度烧结矿边缘区域的份数和小粒度烧结矿使用量,提高球团矿的配比,扩大矿石、焦炭的批重,控制小粒度烧结矿的落点及份数,风量逐步
达到6400m3/min左右,最高日产达8500t/d,7月份实际风量曲线如图3所示。
通过上、下部制度的摸索、调整,煤气流分布更加合理,煤气利用率迅速提高(如图4所示),炉况稳定顺行,为快速达产、高产创造了有利条件。
3.3 大喷吹等降焦技术的快速使用
7号高炉投产后,铁厂原燃料组织非常困难,特别是焦炭的供应,全厂每天缺焦炭3000多吨,特别是影响6号高炉焦炭供应。
为保证整个铁厂原燃料平衡,7号高炉投产后第33h开始喷煤
、用小块焦和球团矿,第3天开始使用小粒度烧结矿,高炉焦比明显下降,大大缓解了铁厂焦炭的需求,同时使高炉生产快速进人正常秩序。
7月份焦比、煤比如图5所示。
3.4 高炉长寿与快速降硅
7号高炉共有15段冷却壁,其中炉缸第2、3段为铸铜冷却壁,炉腹、炉腰、炉身下部共4段轧制铜冷却壁,第10、11段为铸钢冷却壁。
采用带陶瓷杯的综合炉底,炉底自上而下为高导热石墨砖、国产超微孔炭砖、进口微孔炭砖。
另外,7号高炉还采用了模压微孔小炭块,以改善炉缸部位的传热条件。
炉缸以上区域没有专门砌筑耐火材料,只有冷却壁的内表面镶一层大约150mm厚的耐火材料,以保护冷却壁体,避免直接与高温煤气流接触,并利于挂渣,延长一代薄炉衬高炉的使用寿命。
此次高炉开炉降硅速度相对较快。
由于未知原因,开炉后前两次铁炉温偏低,之后【si】迅速上升到2.8%,与设定的3.0%相近。
开炉后【si】的变化趋势如图6所示。
3.5 炉前技术进步
在以前高炉大修投产初期,往往会出现铁口“散喷”现象,有的甚至持续1个月以上,铁口工作的不正常,严重制约了高炉炉况的恢复。
此次7号高炉吸取了以前的经验教训,在开炉前制作铁口泥包时,改过去一次筑制的方法为多次分层筑制,因而泥包致密,强度高,同时在炉缸砌砖时,严格控制砖缝大小。
因此在开炉后,没有出现铁口“散喷”现象,为高炉及时加风提压创造了条件。
在生产过程中,为便于炉前管理,控制合理的铁口深度,在炉前液压炮操作室加装打泥记时器,使打泥量的控制数字化,使铁口一直处于良好的工作状态,为高炉的快速达产并持续高产提供了有力的保障。