方垫片冲压成形工艺及模具设计.docx
《方垫片冲压成形工艺及模具设计.docx》由会员分享,可在线阅读,更多相关《方垫片冲压成形工艺及模具设计.docx(23页珍藏版)》请在冰豆网上搜索。
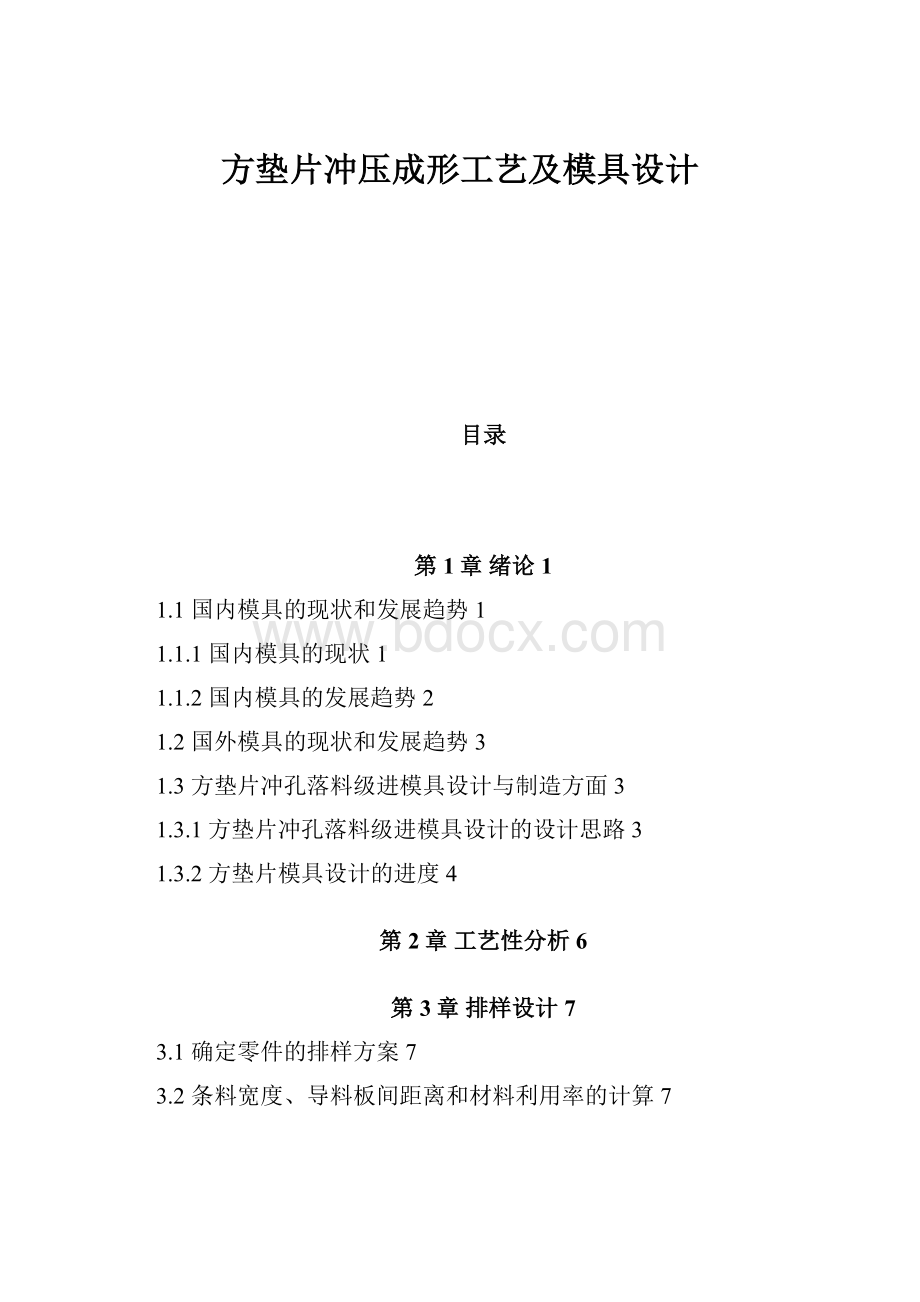
方垫片冲压成形工艺及模具设计
目录
第1章绪论1
1.1国内模具的现状和发展趋势1
1.1.1国内模具的现状1
1.1.2国内模具的发展趋势2
1.2国外模具的现状和发展趋势3
1.3方垫片冲孔落料级进模具设计与制造方面3
1.3.1方垫片冲孔落料级进模具设计的设计思路3
1.3.2方垫片模具设计的进度4
第2章工艺性分析6
第3章排样设计7
3.1确定零件的排样方案7
3.2条料宽度、导料板间距离和材料利用率的计算7
第4章冲压工艺方案的确定9
第5章模具结构形式的选择与确定10
第6章冲压力与压力中心的计算11
6.1冲裁工序总力的计算11
6.2初选压力机12
6.3压力中心的计算12
第7章模具主要零件13
7.1工作零部件的设计与标准化(尺寸、位置、标准与示意图)13
7.2定位装置的设计与标准化18
7.3标准模架的选用20
7.4卸料部件的设计与标准化21
第8章方垫片冲孔落料连续模总装图22
第9章压力机的校核23
结论
参考文献
致谢
第1章绪论
就目前的技术发展水平来看,我国冲压技术与工业发达国家相比还相当的落后,其主要原因是因为我国在冲压基础理论及成形工艺、模具标准化、模具设计、模具制造工艺及设备等方面与工业发达的国家还有相当大的差距,这些导致我国模具在寿命、效率、加工精度、生产周期等方面与工业发达国家的模具相比差距相当大。
1.1国内模具的现状和发展趋势
1.1.1国内模具的现状
我国模具近年来发展很快,根据不完全的统计,在2003年我国模具生产厂点约有2万多家,从业人员约50多万人,2004年模具行业的发展保持良好势头,模具企业总体上订单充足,任务饱满,2004年模具产值530亿元。
进口模具18.13亿 美元,出口模具4.91亿美元,分别比2003年增长18%、32.4%和45.9%。
进出口之比2004年为3.69:
1,进出口相抵后的进净口达13.2亿美元,为净进口量较大的国家,情况不容乐观。
在2万多家生产厂点中,就有一半以上的工厂是自产自用的。
在模具企业中,产值过亿元的模具企业只有20多家,中型企业几十家,其余都是小型企业。
近年来, 模具行业结构调整和体制改革步伐加快,主要表现为:
大型、精密、复杂、长寿命中高档模具及模具标准件发展速度快于一般模具产品;专业模具厂数量增加,能力提高较快;"三资"及私营企业发展迅速;国企股份制改造步伐加快等。
虽然说我国模具业在近年发展迅速,但远远不能适应国民经济发展的需要。
我国尚存在着以下几方面的不足:
第一,体制不顺,基础薄弱。
“三资”企业虽然已经对中国模具工业的发展起了积极的推动作用,近年来私营企业的发展较快,国企改革也在进行之中,但总体来看,体制和机制尚不适应市场经济,再加上国内模具工业基础薄弱,因此,行业发展还不尽如人意,特别是总体水平和高新技术方面的不足。
第二,工厂开发能力比较差,经济效益欠佳.我国模具企业技术人员比例低,水平较低,且不重视产品开发,在市场中经常处于被动地位。
我国每个模具职工平均年创造产值约合1万美元,国外模具工业发达国家大多是15~20万美元,有的高达25~30万美元,与之相对的是我国相当一部分模具企业还沿用过去作坊式管理,才能真正实现现代化企业管理的企业较少。
第三,在工艺装备水平上属于低水准,而且配套性不好,利用率也低。
虽然我国许多企业采用了先进的加工设备,但总的来说装备水平仍比国外企业落后许多,特别是设备数控化率和CAD/CAM应用覆盖率要比国外企业低得多。
由于体制和资金等原因,导致引进设备不配套,设备与附配件不配套现象十分普遍,设备利用率低的问题长期得不到较好解决。
装备水平低,带来中国模具企业钳工比例过高等问题。
第四,国内模具材料及模具相关技术落后。
模具材料性能、质量和品种往往会影响模具质量、寿命及成本,国产模具钢与国外进口钢相比,无论是质量还是品种规格,都有较大差距。
塑料、板材、设备等性能差,也直接影响模具水平的提高。
1.1.2国内模具的发展趋势
巨大的市场需求即将推动着中国模具的工业调整发展。
虽然我国的模具工业和技术在过去的十多年得到了快速发展,但与国外工业发达国家相比仍存在较大差距,尚且不能完全满足国民经济高速发展的需求。
在未来的十年,中国模具工业和技术的主要发展方向主要包括以下几方面:
1)模具正朝着大型化方向发展;
2)CAD/CAE/CAM技术广泛应用于模具设计制造行业中;
3)模具扫描及数字化系统;
4)塑料模具推广应用热流道技术、气辅注射成型和高压注射成型技术;
5)提高模具标准化水平和使用率;
6)发展优质模具材料和先进的表面处理技术;
7)模具的各方面的精度要求都越来越高;
8)模具的运行维护要求高;
9)生产模具的人工技术也在提高。
1.2国外模具的现状和发展趋势
无论在那个国家的工业发展,模具都是工业生产关键的工艺装备,在电子、建材、汽车、电机、电器、仪器仪表、家电和通讯器材等产品中,60%-80%的零部件都要依靠模具成型。
其他加工制造方法所无法替代模具生产制作表现出的高效率、低成本、高精度、高一致性和清洁环保的特性。
模具生产技术水平的高低,已经成为衡量一个国家制造业水平高低的重要标志,并在很大程度上决定着产品的质量、效益和新产品的开发能力。
近几年,据统计全球模具市场呈现供不应求的局面,全世界的模具市场年交易总额为600~650亿美元左右。
欧美等国家年出口模具量约占本国模具年总产值的三分之一。
国外模具企业的组织形式是"大而专"、"大而精",大型、精密、复杂、长寿命模具的比例占到50%以上。
2004年中国模协在德国访问时,从德国工、模具行业组织--德国机械制造商联合会(VDMA)工模具协会了解到,德国大约有5000多家模具企业。
2003年德国模具产值达48亿欧元。
其中(VDMA)会员模具企业有90家,这90家骨干模具企业的产值就占德国模具产值的90%,可见其规模效益很大。
随着时代的进步和技术的快速发展,国外的一些掌握和能运用新技术的人才如模具结构设计、模具工艺设计、高级钳工及企业管理人才等,他们的技术水平比较高。
故人均产值也较高。
而我国每个职工平均每年创造模具产值只有大约合计1万美元左右,而国外模具工业发达国家大多15~20万美元,有的达到25~30万美元。
国外先进国家模具标准件使用覆盖率达70%以上,而我国才达到45%。
1.3方垫片冲孔落料级进模具设计与制造方面
1.3.1方垫片冲孔落料级进模具设计的设计思路
冲裁是冲压工艺的最基本工序之一,它是利用模具使板料沿着一定的轮廓形状产生分离的一种冲压工序。
它包括落料、冲孔、切边、修边、切舌、剖切等工序,其中落料和冲孔是最常见的两种工序。
冲裁在冲压加工中应用极广。
它既可直接冲出成品零件,还可以对已成形的工件进行再加工。
而普通冲裁加工出来的制件的精度不高,一般情况下,冲裁件的尺寸精度应在IT12级以下,不宜高于IT10级。
只有我们不断的加强冲裁变形基础理论的研究,才能准确提供更加准确、实用、方便的计算方法,才能正确地确定冲裁工艺参数和模具工作部分的几何形状与尺寸,解决冲裁变形中出现的各种实际问题,进一步提高制件质量。
方垫片是冲裁模典型的冲压件,该模具工作过程很简单就是冲孔和落料,根据零件图的结构和尺寸精度以及材料的性能确定完成该冲件所需要的模具类型。
因此,综合考虑各种因素后采用复合模。
根据计算的结果和选用的标准模架,判断此次冲裁能不能采用标准的模架。
为了保证制件的顺利加工和顺利取件,模具必须有足够高度。
要改变模具的高度,只有从改变导柱和导套的高度,改变导柱和导套的高度的同时,还要注意保证导柱和导套的强度。
导柱和导套的高度可根据冲裁凸凹模与落料凹模工作配合长度决定。
设计时可能高度出现误差,应该反复多次验证。
1.3.2方垫片模具设计的进度
1.通过网络书籍等方式了解目前国内外冲压模具的发展现状,所用时间8天;
2.查看书本最终确定加工方案,所用时间6天;
3.整体模具的设计,大约用了一个月的时间;
4.模具的最后反复检查验证更正。
冲孔落料级进模设计
工件名称:
方垫片
生产批量:
大批量生产
材料:
A3
厚度:
1mm
工件简图:
见图1
图1方垫片
第2章工艺性分析
图示方垫片零件材料为A3(即Q235碳素结构钢),适合一般的冲压加工。
此工件只有落料和冲孔两个工序,结构相对比较简单,只有一个φ8.0与四个φ3.2的孔。
图示方垫片零件的尺寸全部为未注公差的一般尺寸,但是一般按IT14级取,尺寸精度较低,普通冲裁完全可以满足要求。
由以上各方面综合分析可知,图示零件具有比较好的冲压工艺性,适合冲压生产。
第3章排样设计
3.1确定零件的排样方案
在开始设计模具的时侯,首先要设计条料排样图。
方垫片零件外形是矩形只有冲孔,所以结构比较简单,只需要直排就可以了。
直排(图2所示)的排样方案材料的利用率已经很高。
图2
3.2条料宽度、导料板间距离和材料利用率的计算
查表取得侧搭边值为1.8mm,工件见搭边值为1.5mm
条料宽度的计算:
拟采用无侧压装置的送料方式,由图2条料的排样
b-0Δ=〔Dmax+2a+C〕0-Δ
Dmax————条料宽度方向冲裁件的最大尺寸
a———侧搭边值
△———条料宽度的单向偏差由表查得△=0.10
c———导料板与最宽条料之间的间隙由表查得C=0.5
代入数据计算,取得条料宽度为38.1mm。
导料板间距离的计算:
由A=B+C,代入数据计算得导料板间距离为38.6mm。
根据设计可得送料步距为S=23.5mm
材料利用率的计算:
据大量市场供应调查情况可得,原材料应选用1500mm×750mm×1mm的冷轧薄钢板。
每块可剪38.1mm×1500mm规格条料19条,材料剪切利用率达96.52%。
由文献﹝2﹞材料利用率通用计算公式
冲裁件的面积:
A=34×22-4.252π-4×1.62π=659mm
得
=(1×659)/(38.1×23.5)×100%=73.6%
第4章冲压工艺方案的确定
该工件包括落料和冲孔两个基本工序,可有以下三种工艺方案:
第一个方案:
先落料,后冲孔。
采用单工序模生产。
第二个方案:
落料—冲孔复合冲压。
采用复合模生产。
第三个方案:
冲孔—落料级进冲压。
采用级进模生产。
第一个方案的模具结构比较简单,但需要两道工序两套模具来完成,成本较高而且生产效率低,难以满足大批量生产的要求。
第二个方案只需要一副模具,工件的精度及生产效率都高,由于查表2.9.6可知材料厚度为1mm时凸、凹模的许用的最小壁厚为2.7mm,由图形可知孔边距小于凸、凹模许用最小壁厚,用方案二模具强度较差,制造难度大,并且冲压后成品留在模具上,在清理模具上的物料时会影响冲压的速度,操作不方便。
第三个方案也只需要一副模具,生产效率高,操作方便,工件精度也能满足要求。
通过对比以上方案可知,该工件的冲压生产采用方案三较好。
第5章模具结构形式的选择与确定
1)正倒装结构:
根据上述综合分析,本零件的冲压包括冲孔和落料两个工序,为方便小孔废料和成形工件的落下,采用正装结构,即冲孔凹模和落料凹模都安排在下模。
2)送料方式:
由于这是大批量生产,但是工件简单,所以可以采用手动送料方式,能使模具制造简单。
3)定位装置:
本工件在级进模中尺寸是比较小的,又是大批量生产,冲第一个工位采用始用挡料销定位,而冲第二个工位采用固定挡料销定位。
送料时始用挡料销与固定挡料销作为粗定距,在凸模上安装一个导正销,利用条料上φ8.0mm的孔做导正销孔进行导正,依此作为条料送进的精确定距。
4)导向方式:
为了进一步提高模具寿命和工作质量,便于模具安装调整,该级进模采用中间导柱模架。
5)卸料方式:
由于本模具采用正装结构加工,冲孔废料和工件留在凹模孔洞中,为了简化模具结构,可以在下模座中开有通槽,使废料和工件从孔洞中落下。
工件厚度为1mm,料厚比较厚,为了简化模具结构和达到可靠的卸料力,选用刚性卸料板来卸下条料废料。
第6章冲压力与压力中心的计算
6.1冲裁工序总力的计算
冲裁工序总力的计算,由于工件结构和前面所定的冲压方案可知,本工件的冲裁力包括以下部分。
冲φ8.0mm与φ3.2mm孔的力P1、落外型料的力P2,向下推出φ6.5mm冲孔废料的力P3,向下推出工件的力P4。
由刚性卸料板卸条料的废料的力不是压力机提供的,故不用计算在内。
考虑到模具刃部被磨损、凸凹模间隙不均匀和波动、材料力学性能及材料厚度偏差等因素的影响,实际计算冲裁力时按下面公式:
P=KLtτ﹝3﹞
K—系数,一般取1.3
由上式可知抗剪强度τ与材料种类和坯料的原始状态有关,可在手册中查询得到。
为方便计算,可按下式估算冲裁力表达式又可表示为:
P=1.3Ltτ≈Ltσb式中σb—被冲材料抗拉强度(MPa)。
查手册﹝1﹞表8—7得A3的抗拉强度为440-470Mpa,在这里取σb=450Mpa
L1=[2×(33+21)+2πR]mm=111.14mm
L2=(4π×3.2+π×8.0)=65.31mm
P1=111.14×1×450×1.3=50.13kN
P2=65.31×1×450×1.3=30.1kN
P=P1+P2=80.23kN
推件力Pt=nKtP(3)
Kt—推件力系数,由手册查得Kt=0.055
查手册﹝2﹞表2—40可得h=6mm,故n=6
P3=6×0.055×80.23=26.476kN
卸料力Px=KxF(3)
卸料—卸料力系数,由手册查得Kx=0.0455
P4=0.0455×80.23=3.61kN
工序总力P总=P1+P2+P3+P4=50.13+30.1+26.476+3.61
=110.316kN
6.2初选压力机
查看文献[4]可知压力机参数初选压力机型号为JG23-16,见表一。
表一所选择压力机的相关参数
型号
公称压力/kN
滑块行程/mm
最大闭和高度/mm
工作台尺寸/mm
垫板尺寸(厚度)
可倾斜角/·
封闭高度调节量/mm
JG23-16
160
55
220
300×450
40
35
45
6.3压力中心的计算
根据整体的综合考虑可知,模具的压力中心就是冲压力合力的作用点,为了保证压力机和模具的正常工作,应该使模具的压力中心与压力机的压力中心滑块中心线重合。
否则冲压时滑块就会承受偏心载荷,导致滑块导轨与模具的导向部分不正常的磨损,还会保证不了合理的间隙,从而影响制件的质量和降低模具的寿命,严重的时候还可能损坏模具。
该模具的结构的制造压力中心与模柄中心线重合,故压力中心点就是几何对称点。
若选用坐标系XOY,即xc=0,yc=0。
由以上计算可以得出模具的压力中心以便装模时与压力机滑块的中心线相重合。
第7章模具主要零件
7.1工作零部件的设计与标准化(尺寸、位置、标准与示意图)
7.1.1凸、凹模刃口尺寸的计算
由于方垫片制件结构简单和精度要求不高,所以选择凸模和凹模分开加工的方法制作凸凹模。
这时需要分别计算和标注凸模和凹模的尺寸和公差。
由于零件未标注公差在此均按IT13级算。
根据零件的结构特点,刃口尺寸采用配作法加工。
冲孔时,以凸模为基准,间隙则取在凹模上。
由表2-23得Zmin=0.100mmZmax=0.140mm。
①第二类尺寸:
磨损后减小的尺寸:
φ3.2mm与φ8.0mm。
按IT13级由手册表2-10查得公差分别为△1=0.18mm,△2=0.22mm。
由手册﹝1﹞查表2-30得:
x1=0.75,x2=0.5
B1=(Bmin+x△)0-0.25×△=(3.2+0.75×0.18)0-0.25×0.18=3.340-0.045mm
B2=(Bmin+x△)0-0.25×△=(8.0+0.5×0.22)0-0.25×0.22=8.110-0.055mm
②第三类尺寸:
磨损后不变的尺寸:
16mm与28mm。
按IT13级由手册表2-10查得公差分别为△1=0.27mm,△2=0.33mm。
C1=(Cmin+0.5△)±0.125△=(16+0.5×5.27)±0.125×0.27=16.14±0.0337mm
C2=(Cmin+0.5△)±0.125△=(24+0.5×0.33)±0.125×0.33=28.17±0.0413mm
由计算落料凹模的基本尺寸与凸模相同,分别是3.34mm,8.61mm,16.14mm,28.17,保证最小双面合理间隙值Zmin=0.10mm。
由表2-23得Zmin=0.100mmZmax=0.140mm。
按IT13级由手册表2-10查得公差分别为△1=0.33mm,△2=0.39mm,△3=0.14mm
由手册﹝1﹞查表2-30得:
x1=0.75,x2=0.75,x3=1
A1=(Amax-x△)0+0.25△=(02-0.75×0.33)0+0.555×0.545=21.750+0.0825mm
A2=(Amax-x△)0+0.25△=(354-0.75×0.39)0+0.25×0.39=33.710+0.0975mm
A3=(Amax-x△)0+0.25△=(055-1×0.14)0+0.25×0.14=0.360+0.035mm
落料凸模的基本尺寸与凹模相同,分别是21.75mm,33.71mm,0.36mm,不必标注公差,但要在技术条件中要注明:
凸模实际刃口尺寸与落料凹模配制,保证最小双面合理间隙值Zmin=0.01mm。
7.1.2卸料橡胶的设计
卸料橡胶的设计计算参照下表。
选用的4块橡胶板的厚度必须要一致,不然会造成受力不均匀,运动产生歪斜,影响模具的正常工作。
表二
项目
公式
结果
备注
卸料板工作行程h工
h工=h1+t+h2
4mm
h1为凸、凹模凹进卸料板的高度1mm
h2为凸、凹模冲裁后进入凹模的深度2mm
橡胶工作行程H工
H工=h工+h修
9mm
h修为凸、凹模修模量,取5mm
橡胶自由高度H自由
H自由=4H工
36mm
取H工为H自由的25﹪
橡胶的预压缩量H预
H预=15﹪H自由
5.4mm
一般H预=10﹪~15﹪H自由
每个橡胶承受的载荷F1
F卸/4
1184.5N
选用四个圆筒形橡胶
橡胶的外径D
D=
48mm
D为圆筒橡胶的内径,取d=12mm;p=0.5Mpa
校核橡胶的自由高度H自由
0.5≤H自由/D=0.75≤1.5
满足要求
橡胶的安装高度H安
H安=H自由-H预
30mm
7.1.3工作零部件的设计与标准化
①落料凸模
综合考虑工件外形和加工,将落料凸模设计为直通式,采用线切割机床加工,2个M6的螺钉固定在垫板上,与凸模固定板的配合按H7/m6。
其总长L可按下列公式计算:
L=h1+h2+t+h=(15+12+1+30)=58mm
式中:
h1—凸模固定板厚度(mm);
h2—卸料板厚度(mm);
t—材料厚度(mm);
h—自由高度(mm)。
具体结构图如下所示:
②冲孔凸模
由于要冲的孔都为圆形,而且都不属于需要特别保护的小凸模,所以冲孔凸模采用台阶式,一方面加工简单,另一方面又便于装配与更换。
其中4个冲φ3.2mm的圆形标准件BⅡ型式。
冲φ8.5mm的孔的凸模结构如图3所示:
图3
小凸模强度校核(凸模用T10钢)
要使凸模正常工作,必须使凸模最小断面的压应力小于凸模材料的许用压应力,即对于圆形凸模
dmin≥
=4×1×350/450=3.11mm承压能力足够大。
—冲裁材料的抗剪强度,310~380Mpa
—凸模材料许用强度,取440~470Mpa
抗纵向弯曲力校核:
对于圆形凸模(有导向装置)
Lmax≤270d2/
=270×3.22/√(4521.2)1/2=44.8mm长度刚好。
式中Lmax——允许的凸模最大自由长度,mm
F——冲模力,N
d——凸模最小截面的直径,mm
凸模固定端面压力的计算:
q=
<
=4521.2/(1.652π)=528.2Mpa
式中 q—凸模固定端面的压力,Mpa
F—落料或冲孔的冲裁力,N
—模座材料许用压应力,Mpa
凸模固定板端面压力超过了80~90MPa,为此应在凸模顶端与模座之间加一个淬硬的垫板。
矩形垫板材料可用45钢,结构形式和尺寸规格见手册﹝2﹞表查得100×100×6
③凹模
凹模采用整体式凹模,在安排凹模在模架上的位置时,要依据计算压力中心的数据,将压力中心与模柄重合。
其轮廓尺寸计算如下:
凹模高度H=Kb=0.40×34=13.6mm
按表取标准值15mm
凹模壁厚c=(1.5~2)H=22.5~30mm
取凹模厚度为30mm,
凹模宽度B=b+2c=(34+2×30)=94mm,
凹模长度L取45mm,
式中b---凹模刃口的最大尺寸(mm)
c---凹模壁厚(mm)指刃口至凹模外形边缘的距离;
K=系数,取0.40
故凹模轮廓尺寸为:
45×94×30
凹模上螺孔到凹模外缘的距离一般取(1.7~2.0)d
图4整体式凹模的局部结构图5凹模上的螺孔设计与选用
d为螺孔的距离由于凹模厚度为10mm,所以根据表2.4﹝2)查得螺孔选用4×M5的螺钉固定在下模座。
故选用如图5:
螺孔到凹模外缘的最小距离a2=1.5d=1.5×5=7.5mm
a3=1.13d≈5.65mm
凹模上螺孔间距由表2.47查得最小间距为15mm
最大间距为50mm
螺孔到销孔的距离一般取b>2d
所以b应大于10
通过计算和上述的方法确定凹模外形尺寸应该选用矩形凹模板100×100×15(JB/T7643.1)
7.2定位装置的设计与标准化
(1)始用挡料块的设计与标准化(尺寸、位置、标准与示意图)
挡料块标记:
456GB/T2866.1—81(图6)
材料:
45钢GB/699—88
热处理:
硬度43~48HRC
技术条件:
按GB2870—81
(2)固定挡料销的设计与标准化图6始用挡料销的设计
固定挡料销的设计要求根据标准件,选用此挡料销如图7
图7固定挡料销的结构
根据分析选用废料孔前端定位时挡料销位置如图8其确定如下:
=C-D/2+d/2+0.1=17.9-6.68/2+8/2+0.1=18.66mm
图8固定挡料销的位置
(3)导正销的设计与标准化
导正销主要运用于级进模上,消除挡料销的定位误差,以获得较精确的工件。
导正销的结构形式,结构设计,尺寸精度,材料的热处理等可参照JB/T7647.1—94和JB/T7647.2—94选定。
导正销的结构形式查手册[2]选用如图9
图9导正销的结构形式
冲裁φ6.5mm孔的导正销查表得
h=0.6t2a=0.06mm
D=d-2a=6.68-0.06=6.62mm
h=0.6×1.5=1.32mm
(4)导料板的设计与标准化
导料板的内侧与条料接触,外侧与凹模平齐,导料板与条料之间的间隙取1mm,这样就可以确定导料板的宽度,导料板的厚度查表取6~8mm。
导料板