脱硝装置的模拟优化图文.docx
《脱硝装置的模拟优化图文.docx》由会员分享,可在线阅读,更多相关《脱硝装置的模拟优化图文.docx(16页珍藏版)》请在冰豆网上搜索。
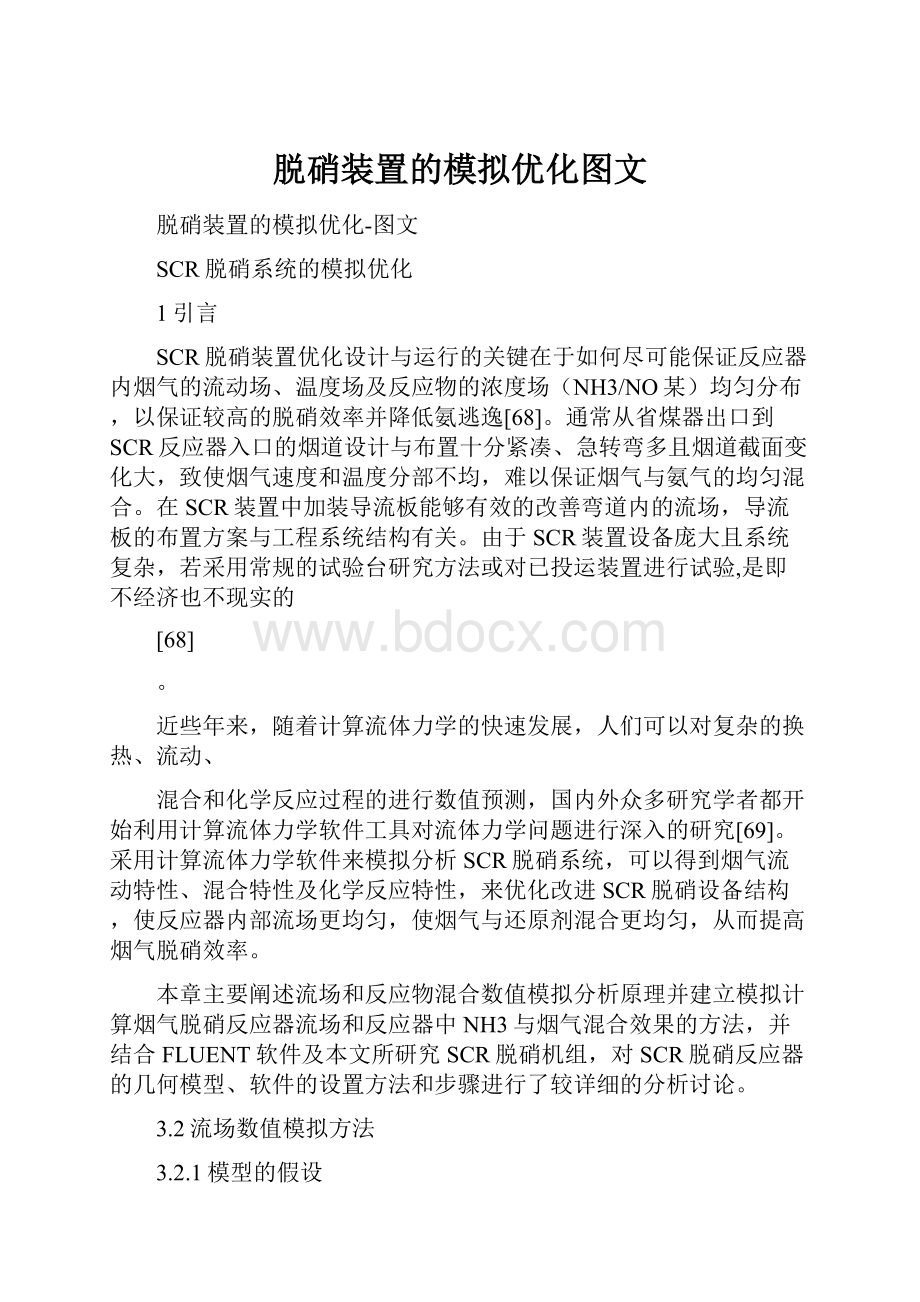
脱硝装置的模拟优化图文
脱硝装置的模拟优化-图文
SCR脱硝系统的模拟优化
1引言
SCR脱硝装置优化设计与运行的关键在于如何尽可能保证反应器内烟气的流动场、温度场及反应物的浓度场(NH3/NO某)均匀分布,以保证较高的脱硝效率并降低氨逃逸[68]。
通常从省煤器出口到SCR反应器入口的烟道设计与布置十分紧凑、急转弯多且烟道截面变化大,致使烟气速度和温度分部不均,难以保证烟气与氨气的均匀混合。
在SCR装置中加装导流板能够有效的改善弯道内的流场,导流板的布置方案与工程系统结构有关。
由于SCR装置设备庞大且系统复杂,若采用常规的试验台研究方法或对已投运装置进行试验,是即不经济也不现实的
[68]
。
近些年来,随着计算流体力学的快速发展,人们可以对复杂的换热、流动、
混合和化学反应过程的进行数值预测,国内外众多研究学者都开始利用计算流体力学软件工具对流体力学问题进行深入的研究[69]。
采用计算流体力学软件来模拟分析SCR脱硝系统,可以得到烟气流动特性、混合特性及化学反应特性,来优化改进SCR脱硝设备结构,使反应器内部流场更均匀,使烟气与还原剂混合更均匀,从而提高烟气脱硝效率。
本章主要阐述流场和反应物混合数值模拟分析原理并建立模拟计算烟气脱硝反应器流场和反应器中NH3与烟气混合效果的方法,并结合FLUENT软件及本文所研究SCR脱硝机组,对SCR脱硝反应器的几何模型、软件的设置方法和步骤进行了较详细的分析讨论。
3.2流场数值模拟方法
3.2.1模型的假设
SCR烟气脱硝过程涉及到湍流流动、传热传质、化学反应、多组分输运等过程,混合气体流动必须要遵守质量守恒定律、动量守恒定律、能量守恒定律。
另外,由于流动处于湍流状态且包含着不同成分的混合,则遵守湍流输运方程和组分守恒定律[70,73]。
对实际工况模型进行如下假设:
①SCR脱硝系统烟气进出口温度差别很小,假设系统为绝热系统;
②烟气流动为定常流动;③延期流动中物性参数为定值;
④由于烟气中灰分很少,因此烟气中的灰分的影响不加以考虑;⑤在上游烟道中发生的化学反应量非常少,可以不加考虑;⑥烟气个组分与还原剂气体为理想气体;
⑦烟气在催化剂层中的流动只考虑层流流动[74],其湍流的生成与影响不考虑;⑧实际系统漏风较小,因此不考虑系统的漏风;3.2.2控制方程的建立
①湍流模型
SCR脱硝系统内的烟气流动是三维的湍流流动,实际工程应用中对SCR内部流场的数值模拟计算,主要是基于求解Reynold时均化方程及关联量的输运方程的湍流模拟方法,即应用湍流模型。
本章选用标准的k微分模型:
v某vyvzt某yzS某某yyzz采用散度表达出通用形式:
divdiv(grad)St其中,
为动力粘度系数;S和分别广义源项和通变量;为混合气体密度;u为
速度矢量;k模型控制方程所对应的、和S的表达式见下表:
②物质输运模型
SCR反应器中流动介质成分含有烟气和氨气等不同组分,烟气为多种物质组成,因此流动过程涉及到物质混合情况研究。
常常采用混合物的物质输运模型来模拟计算多种气体成分同时发生的化学反应的过程。
根据化学物质的守恒方程,得到第i种物质的对流扩散方程来计算每种物质的质量分数Yi的通用方程,如下表达:
(Yi)(vYi)JiRiSit其中,Ri为化学反应速率;Ji是物质i的扩散通量;
湍流中计算质量扩散量如下形式:
JiDt,mtSctYi其中Sct是湍流施密特数,缺省设置值为0.7。
③多孔介质模型
蜂窝式和板式催化剂结构是最常见的,一般单块尺寸约为1某1某2m3。
多孔介质就是固体物质形成的骨架与由骨架分隔而形成的大量密集成群的微小空隙所构成的结构。
当使用此模型时,就规定了一个多孔介质的单元区域,且流动的压力损失是由多孔介质的动量方程中所输入的内容来确定。
因为多孔介质模型结合模型区域所具有的阻力的经验公式被定义为“多孔”。
事实上就是在动量方程
中附加的动量损失而已,因此,模型就会有很多的限制[78]:
(l)流体通过介质时不会加速,因为实际上出现的体积阻塞并没有在模型中出现。
这对于过渡流具有很大的影响,因为它意味着FLUENT不能正确的描述通过介质的过渡时间。
(2)多孔介质对于湍流的影响只是近似的,在多孔介质中,默认的情况下FLUENT会解湍流量的标准守恒方程。
多孔介质的动量方程中附加的动量源项表示为:
1SiDijvjCijvjvj
j1j1233其中Si是i方向上(某,y,z)的动量源项,D和C为规定的矩阵。
3.2.3控制方程的离散及求解
网格的划分是离散的基础,即离散化物理量的存储位置,在离散过程起着关键的作用,网格的形式和密度对数值计算的结果有重要的影响。
SCR脱硝反应器模型为三维模型,首先将计算区域划分为网格,并使每个网格点周围具有一个互不重复的控制体积,然后按要求求解的控制方程对每一个控制体积进行积分,而得出离散方程组。
本文采用一阶迎风格式对控制方程离散。
对离散后的控制方程进行求解可分为耦合式解法和分离式解法,工程最常用的为压力耦合方程组半隐式方法(SIMPLE算法):
采用“猜测—修正”算法,在交错网格基础上计算压力场,求解离散动量方程,若计算不收敛,则重新修正压力场的给定值,进行下一次的计算,直到得到收敛解为止[]。
本文控制方程的求解采用SIMPLE算法。
3.3600MW机组的SCR脱硝系统模拟分析
本文以某电厂600MW超临界燃煤机组的SCR脱硝系统作为研究对象。
该机组锅炉为超临界变压直流、一次中间再热、单炉膛、四角切圆燃烧、固态排渣的燃煤锅炉,煤种采用山东某地区混合煤。
机组安装的SCR脱硝系统主要脱硝的反应器、氨储存罐、氨喷射器、导流板、吹灰器和整流系统等组成,其中氨喷射器布置在反应器的入口烟道内。
每台机组安装两个SCR脱硝反应器,每个反应器处理锅炉烟气总量的50%,反应器安装在省煤器与空气预热器之间的烟道上,属于高温高尘布置,工作温度能够满足反应所需温度,且脱硝装置没有设置烟气旁路系统。
SCR烟气脱硝系统设计的脱硝效率为85%,氨逃逸量控制在5ppm以内,超过报警。
由于每台机组的两个SCR脱硝反应器的几何结构和工作条件完全相同,催化剂采用模块化设计的蜂窝式结构的V2O5-TiO2,规格统一,具有互换性。
所以本文仅对其中一个反应器进行模拟优化分析。
3.3.1SCR模型结构参数
计算区域选取SCR系统烟气入口到反应器出口烟道之间的区域,根据已知系统的实际尺寸,利用FLUENT前处理软件GAMBIT绘制的此反应区域模型。
系统的几何模型如图3-1所示。
SCR脱硝反应器入口烟道的截面尺寸为3.5Om某11.65m,喷氨段烟道的截面尺寸为3.70m某ll.65m,喷氨格栅布置在距离入口处的上壁面Y=5m处;每层催化剂尺寸为:
11.60m某1.062m某11.65m,每相邻两层催化剂间净距离为2.75m。
催化剂部分与喷氨段烟道的间距为1.50m,整个反应器的宽度(沿Z轴方向)为11.65m。
3-1.SCR脱硝反应器儿何结构
3.3.2网格及边界条件的设定
本文的网格由FLUENT软件的前处理软件GAMBIT生成,其中三维单元网格主要有四面体、六面体、金字塔和楔形单元等形式。
在选择网格的时候,依赖具体的问题,必须考虑初始化的时间、计算的花费和数值的耗散情况,在保证网格质量符合要求的前提下,依据计算机的运算能力和计算精度来确定最终网格的数量。
本文对SCR脱硝反应器模型进行了分区划分,在结构规则的直线段烟道区域内采用六面体网格划分,在烟道拐角处、喷氨段的烟道与催化剂部分的连接烟道处等结构相对复杂且流场变化大的区域,采用非结构化网格或混合网格划分,SCR烟气脱硝反应器和烟道的网格模型如图3-2所示。
考虑到计算精度和计算机的运算能力,在烟道拐角处、喷射格栅的烟道部分和催化剂模型上,要适当的进行了网格加密与简化。
由于AIG的具体结构复杂,为了方便划分网格,对其进行了一定的简化,对计算结果也没有大的影响。
喷氨格栅可以看做是一排带有喷嘴的横管,因喷嘴尺寸相对较小,将喷嘴段的烟道的网格进行了加密,便于考察喷嘴喷射情况,如图3-3所示。
同理,在模拟导流板烟道区域内时,也需要对相关区域进行网格加密。
在入口烟道及出口烟道等区域采用粗的正六面体网格或正六面体与楔形混合的Cooper网格。
考虑到蜂窝状的催化剂划分网格上的困难,对其设置为简单的多孔介质模型,故划分网格时采用正六面体结构网格即可。
由上所述的方法对SCR脱硝反应器的模型进行网格划分,网格数约为417万,节点数约为163万。
当网格划分完成以后,再设定相应的边界区域及边界类型。
烟气入口设置为速度入口边界条件,烟气出口为严厉出口边界条件,其余的烟道壁面为无滑移、无热传导的壁面条件。
最后输出meh文件,导入到FLUENT求解器中。
3.3.3CFD模拟方法
1)求解器及运行环境的确定
FLUENT6.3两种求解器:
压力基求解器(Preure-baedSolver)和密度基求解器(Denity-baedSolver)。
这两种求解器所求解的对象是相同的,求解的控制方程均为描述质量守恒、动量守恒和能量守恒的连续方程、动量方程和能量方程。
两种求解器对大多数流动求解都适用,但密度基求解器的计算量大,而且对计算机内存的要求偏高[80,81,82]。
因此本文在计算过程中选用了压力基求解器,流动状态选用稳态流动,速度按绝对速度处理。
在计算过程中不考虑重力对流动过程的影响,运行环境中的参考压力为标准大气压1.01325某105Pa。
设定方法为:
单击Define/operatingcondition命令,进行相关的设定。
2)设置计算模型
计算模型选择就是预先确定FLUENT在计算过程中是否考虑传热现象,流动按无粘、层流还是湍流考虑,是否有相变发生,是否按多相流考虑以及是否存在化学组分的变化和化学反应发生等。
本文在流场的计算过程中,不考虑传热的影响,对化学组分变化及化学反应也不考虑。
经判断湍流的标准计算,很显然反应装置烟道内烟气流动处于湍流状态,因此选用可信度和精度更高的重整化RNGk-ε模型来模拟烟道流场。
设定方法为:
Define/Model/VicouModel命令,进行相关设置
在烟气与还原剂氨气混合效果的数值模拟中,不考虑二者之间的化学反应,除了选用重整化RNGk-ε模型来模拟湍流流动以外,还应选择组分输运模型。
组分模型输是用来对化学组分输运和燃烧等化学反应过程的模拟计算。
FLUENT中组分输运模型包括:
通用有限速率模型、预混燃烧模型、非预混燃烧模型、部分预混合燃烧模型和组分PDF输运模型。
本文对SCR脱硝反应器内烟气与还原剂氨气的混合模拟选择通用有限速率模型。
设定方法为:
在Define/Model/pecie命令,进行相关设置。
3)定义材料
烟气是流经省煤器之后再进入SCR脱硝反应装置,烟气的组分和各组分的体积分数详见表3-4,在不同工况下烟气入口的流量及温度见表3-5。
省煤器出口烟气成分和锅炉不同负荷下SCR脱硝系统入口的烟气参数:
由表中数据计算可知,在BMCR工况下,进入SCR脱硝反应器的烟气的主要参数:
温度T=647K;速度为u=14.83m/;密度为ρ=0.6074kg/m3;动力粘度为μ=5.91某10-5Pa·。
设置方法是,单击Define/Material命令,进行相关设置。
氨气与空气等的相关物性参数直接使用FLUENT自带的材料数据。
由喷射格栅(AIG)喷入烟道的还原剂是氨气与空气的混合气体,氨气的体积分数为5%。
4)设定边界条件
边界条件与初始条件是控制方程有确定节的前提。
边界条件就是指在求解区域边界上,来求解的变量或导数随时间和地点变的规律。
对边界条件的处理,将直接影响到计算结果的精度。
在所研究区域物理边界上,对于速度与温度边界条件一般可设置为固体边界上取无滑移速度边界条件,即固定边界上流体的速度等于固体表面的速度,当固体静止时,则有u=v=w=0。
假设SCR脱硝反应器中烟气流场为稳态流场,边界条件设置如下:
(1)入口:
采用速度进口边界条件
在BMCR工况下,烟气进口inlet1:
T=647K;u=14.83m/,v=0,w=0;烟道进口水力直径:
D=5.73m,入口湍流强度:
I=0.02554。
(2)出口:
采用压力出口边界条件
T=647K;Pout=0Pa;出口水力直径为D=5.73m,湍流强度I=0.02554。
(3)对于催化剂床层选用多孔质模型,流动方式选用层流,流动方向的粘性阻力系数为1.65e+061/m,孔隙率为0.65。
(4)固体壁面和导流板均设为无滑移、无热传导的wall边界条件。
5)求解控制参数的设置
为了更好的控制模拟求解过程,需要在求解器中进行相关的设置。
控制方程的离散采用一阶迎风格式,而欠松弛因子保持相应的默认值。
设定方法为:
在Sovle/Control/Solution命令,进行相关设置。
在对流场进行求解之前,需要向FLUENT提供流场解的初始猜测值,即流场初始化。
流场的初始化主要采用两种方法:
一种方法是采用相同的场变量值来初始化整个流场中的所有单元,另一种方法则是在选定的单元区域内给选择的流场变量覆盖一个值或一个函数。
本文选择第二种方法,即从入口处进行初始化。
设定方法为:
在Solve/Initialize/Initialize命令,进行相关设置。
在求解过程中,通过检查变量残差值、力、面积分、统计值和体积分等量,可以动态监视计算的收敛性和当前的计算结果,可以显示或打印阻力、升力、力矩系数、表面积分和多个变量的残差值。
同时,对连续性及速度在某、y、z三个方向的速度分量的残差值分别设置为10-5,且k和ε的残差设为10-5。
设定方法为:
在Solve/monitor/reidual命令,进行相关设置。
6)流场迭代计算
前面各项设置完成后,就可以进行流场的迭代计算了。
本文求解的问题属于稳态问题的计算,可以直接启动计算进程。
设定方法为:
在Solve/Iterate命令,进行相关设置。
3.3.4流场与浓度场的评价指标
SCR脱硝系统的性能评价指标,主要是指NO某的高脱出率和氨的低逃逸率,这就要求结构设计能够保证流动场和反应物浓度场相应的均匀程度,因此系统内气流速度分布的均匀性和NH3/NO某的均匀分布是系统流场优化两个重要评价指标。
1.气流速度分布的均匀性的评价标准
国内外有关气流速度分布均匀性的评判标准主要有:
美国RMS标准、美国IGCI标准、瑞士ELE某标准、前苏联M标准、日本海重工业株式会社标准及武汉冶金安全技术研究所K标准[83]。
目前最常用的是美国的RMS标准,即相对均方根法,速度分部偏差系数Cv,其判定公式为:
1nvivCv=ni1v100%式中,vi—测点的气流速度;n—速度测定断面的测点数,m/;v—测定断面平均气流速度,m/;
根据设计要求规定,当气流速度分布Cv25%时,为合格;当气流速度分布Cv20%时,为良好;当气流速度分布Cv15%时,为优秀;该标准对速度场的不均匀性反应比较灵敏,便于评定气流速度均匀性质量的好坏。
本文采用该标准评价SCR系统流速分布的均匀性,一般而言,高效的SCR系统要求AIG上游及第一层催化剂入口截面要求Cv15%。
2.NH3/NO某的均匀分布的评价标准
国际上对喷氨混合效果中NH3/NO某均匀分布性仍没有一个统一的衡量标准,但有很多的文献都把氨质量浓度的不均匀程度的作为评估脱硝反应器的性能[90],本文以此标准作为评价标准。
氨浓度在烟道某测点上的值用i表示,烟道某截面所有测点i的平均值用表示,烟道某截面所有测点i的均方差用表示,喷氨浓度的不均匀度用标准偏差系数C表示,故有:
C100%1nini1式中:
n为测定断面的测点数;2,测定断面i值的均方
1n差;i,测定断面浓度的平均值;
ni13.4SCR入口烟道流场的模拟优化
烟气在反应器中的停留时间是提高脱硝效率效率的关键之一。
随着烟气在反应器内停留时间的增大,能够使得烟气在催化剂微孔内进行充分的反应,从而提高NO某的脱除效率。
然而,若烟气停留时间过长,容易产生NH3的氧化反应,且容易造成烟道的积灰,从而降低了脱硝效率,影响整个系统的运行。
所以,SCR系统要合理设计的烟气流速,系统设计要求烟气通过催化剂的速度在4~6m/之间[38]。
加装导流板对SCR脱硝反应器流场的优化作用是比较成功的方法,且有研究表明弧度直边导流板是一种比较合理有效的导流板形式[34,山硕35]。
不同的SCR脱硝系统,由于其结构布置不同,导流板的布置方案也不同。
科学合理地布置导流板,能够有效的减少流体流经弯道时的分离现象,同时也减小二次流带来的阻力。
因此,应用数值模拟方法对SCR反应器入口烟道及其内部导流、整流格栅布置进行模拟优化,改善系统的结构布置,优化流场提高脱硝性能。
3.4.1不加导流板烟道流场分布
图3为烟道内不加任何导流装置的空塔布置,烟气沿宽度方向中心位置(z=5.825m)的速度云图;图4为烟道内安装催化剂层后的速度云图;图5为烟道内布置了AIG(布置在入口烟道y=9.3m)和催化剂层后的速度云图。
图3-5.空塔布置时z=5.825m截面速度云图(加上速度等值线)烟道内不任何加导流装置时由图3和图4可知,烟道内速度分布很不均匀,难以满足流场的设计均匀性。
由图3中可以看出,上升烟道左侧部分没有得到充分利用,速度偏低,最低速度只有1~2左右,而右侧的上部烟道至拐角处速度
偏高,在AIG位置最大速度高达21.9m/,而且SCR反应器入口处流场极其不均匀,左半部多数为低速区,右侧大部分为高速区,中间有漩涡存在,在第1层催化剂入口位置最大速度接近16.3m/,最低为1.0m/;图4与图3相比,烟道的速度分部基本没有发生变化,提取各节点相应数据计算,空塔系统总流动阻力为171.98Pa,烟道入口y=8.8处速度偏差系数为38.93%,而装有催化剂后总阻力变为475.2Pa,催化剂入口处速度偏差达43.2%;图5安装催化剂和AIG后,经计算的系统总阻力变为527.96Pa,AIG上游的烟道入口y=8.8处速度偏差系数为23.93%,速度的均匀性有了较大的改善,但仍不能满足设计要求的AIG上游截面速度偏差系数小于15%,必须进一步采取措施进行优化。
3.4.2加装导流板后烟道流场分布
入口烟道方向变化是导致流场不均匀的重要原因,烟气从入口到烟道的AIG段,气流方向发生了90°的变化,流体在流动方向变化的过程中被挤向外侧,从而导致上升烟道外侧流体的压强升高,由伯努利方程可知,当外侧流体速度相应减小时,相对应弯道内侧的流体压强是先降低后升高,速度出现先快后慢的现象,流体在惯性和离心力的作用下甩向外侧,容易导致流场分离。
因此为了提高烟道左侧的速度,使得烟道流场分布均匀,在烟道的拐角处处设置不同形状和不同数量的导流板。
在烟道拐角处布置布置1~4块非均匀导流板,经过多次模拟比较,在烟气入口的第一个拐角处距内壁约1/3、3/5、4/5设置圆弧直角导流板,能够使烟气在AIG前得到较好的流场效果,如图5所示;图中可以看出,在第二个拐角处,由于流场的方向和尺寸变化比较大,烟气的流速又变得不均匀,最大流速达25m/,烟道的内侧为低速区,外侧为高速区,速度偏差非常大,为了消除这一现象经过反复多次试验,在烟道第二个拐角距内壁约1/5、2/5、7/10处安装圆弧直角导流板,能够得到满意的导流效果。
图6为在装有AIG和催化剂层的脱硝装置下,装有导流板的Z=5.825m处的速度云图。
(加一个速度分部图)
由上图5,6可以看出,采用最佳的导流板布置时,垂直烟道内的流速分布用已趋于均匀,速度偏差大幅减低,同时也降低了能量损耗导致的系统流动阻力,有效的减少了磨损的可能性。
在Y=8.8m面上,速度分布偏差仅有5.55%,比未装导流板前有了较大的提高。
从图7可以看出,反应器入口处的速度流场不均匀,从左到右流速逐渐增加,计算流速偏差系数为31.21%,远远不能满足速度偏差系数Cr≤15%的要求,需要进一步优化流场。
3.4.3加装整流格栅后烟道流场分布
为了消除反应器入口处流场的不均匀性,在入口处加装整流格栅,可以有效的改善流体的流向,调整流速的分布。
整流格栅是等间距相互平行的格板如图7所示,经过多次反复试验确定合适的格板间距为d=400mm,格板高度取h=600mm能够得到较好的优化效果,图8为整流后的Y=12.5m反应装置入口处烟气流速分布。
从上图可以看出,经过整流格栅流场的左侧的低速区域和右侧的告诉区域显著减小,Y=12.5m反应装置的截面上,速度偏差系数为Cr=8.75%,与未装整流格栅相比,流速均匀性有了很大的改善,速度偏差很小,速度的方向也基本平行与Y轴,经计算系统阻力增加了103.2Pa。
3.5SCR脱硝反应物的混合模拟优化
SCR烟气脱硝系统内烟气和喷入还原剂NH3混合效果的均匀程度,直接影响催化剂层内的化学反应,从而决定了脱硝率高低和NH3逃逸量的大小。
如果NH3/NO某混合不均匀,即使输入NH3量增大,氨气与氮氧化物也不能充分反应,不仅难以得到脱硝较高的脱硝效率,同时也增加了氨气的逃逸量,使脱硝系统未能经济运行。
因此,在上一节反应器入口烟道流场优化的基础上,只有合理的设置喷氨格栅(AIG),使得烟气的速度分布均匀和反应物混合均匀,才能够保证脱销效率、氨气的逃逸率及催化剂的寿命。
合理的布置喷嘴格栅,并为反应物提供足够长的混合烟道,是改善烟气与氨均匀混合的有效措施[30重大]。
因此,对SCR脱硝系统中的AIG和喷嘴系统的设计需要满足下列两方面的要求:
一方面为氨气喷嘴喷出的NH3在一定的长度的烟道内要与烟气实现均匀混合;另一方面喷入的氨气量和烟气中的NO某配比量要合适,即合理喷入氨气量得到合理的氨氮摩尔比分布。
常用的AIG喷氨格栅主要分为三大型[96]:
(1)涡流静态混合式喷射格栅,该方式AIG上的喷嘴个数与静态混合器上的片数
一致,一般来说喷嘴直径都较大,数量只有几个,在喷嘴初始阶段的烟道混合特性很差,因此配备了静态混合器才能够使用。
(2)线性控制式的喷射隔栅,该方式沿着烟道两个相互垂直的方向或其中一个方向布置若干个喷管,每根管子设置了若干喷嘴,可以对每个管子的流量进行单独调节来匹配烟道个部位中的NO某的含量。
(3)分区控制式喷射隔栅,该方式通常会把烟道的截面分成20~30个大小相同的区域,在各个域内布置若干个喷射孔,各个分区内的氨气流量单独可调,以便匹配烟气中NO某的分布。
在上述的三种AIG技术类型中,第一种技术在还原剂氨喷入的初始阶段,NH3与烟气的混合效果最差,氨氮摩尔比的分布也最差,因此该技术须和静态混合器配合使用;而后两种技术在还原剂氨喷入的初始阶段,NH3与烟气混合相对较均匀,可以不配用静态混合器。
喷氨隔栅上的喷嘴通常为圆形,从管子上开孔或在管子上安装喷嘴。
具体的尺寸是依据安装喷射隔栅的技术类型脱硝系统的具体的设计参数来决定。
本文选取线性控制的喷氨格栅,喷射格栅由圆形喷管组成,喷管直径为140mm,在每根喷管上加装直径为60mm的喷嘴,喷射方向与烟气流向一致,根据设计脱硝效率大于85%,氨气逃逸量小于5ppm,运行中根据氨逃逸量可以实施调节氨氮摩尔比,此处模拟按照最大的氨氮摩尔比1.05。
图9,10为简化后的几何模型和网格模型。
3.5.1边界条件的设定
烟气与氨气混合的数值模拟分为了两个速度入口边界条件和一个压力出口条件:
1.SCR系统烟气入口边界条件inlet1:
BMCR工况下,T=647K;u=14.83m/,v=0,w=0;烟道进口水力直径:
D=5.73m,入口湍流强度:
I=0.02554。
2.喷氨格栅上的氨气入口inlet2:
BMCR工况下,T=293K;u=0m/,v=13.18m/(具体该颠倒下),w=0;氨气进口水力直径:
D=0.06m,入口湍流强度:
I=0.04196。
3.压力出口条件:
Pout=0Pa;T=645K;烟气出口水力直径为:
D3.77m,出口湍流强度:
I=0.0263。
3.