170KA的铝电解槽的设计.docx
《170KA的铝电解槽的设计.docx》由会员分享,可在线阅读,更多相关《170KA的铝电解槽的设计.docx(24页珍藏版)》请在冰豆网上搜索。
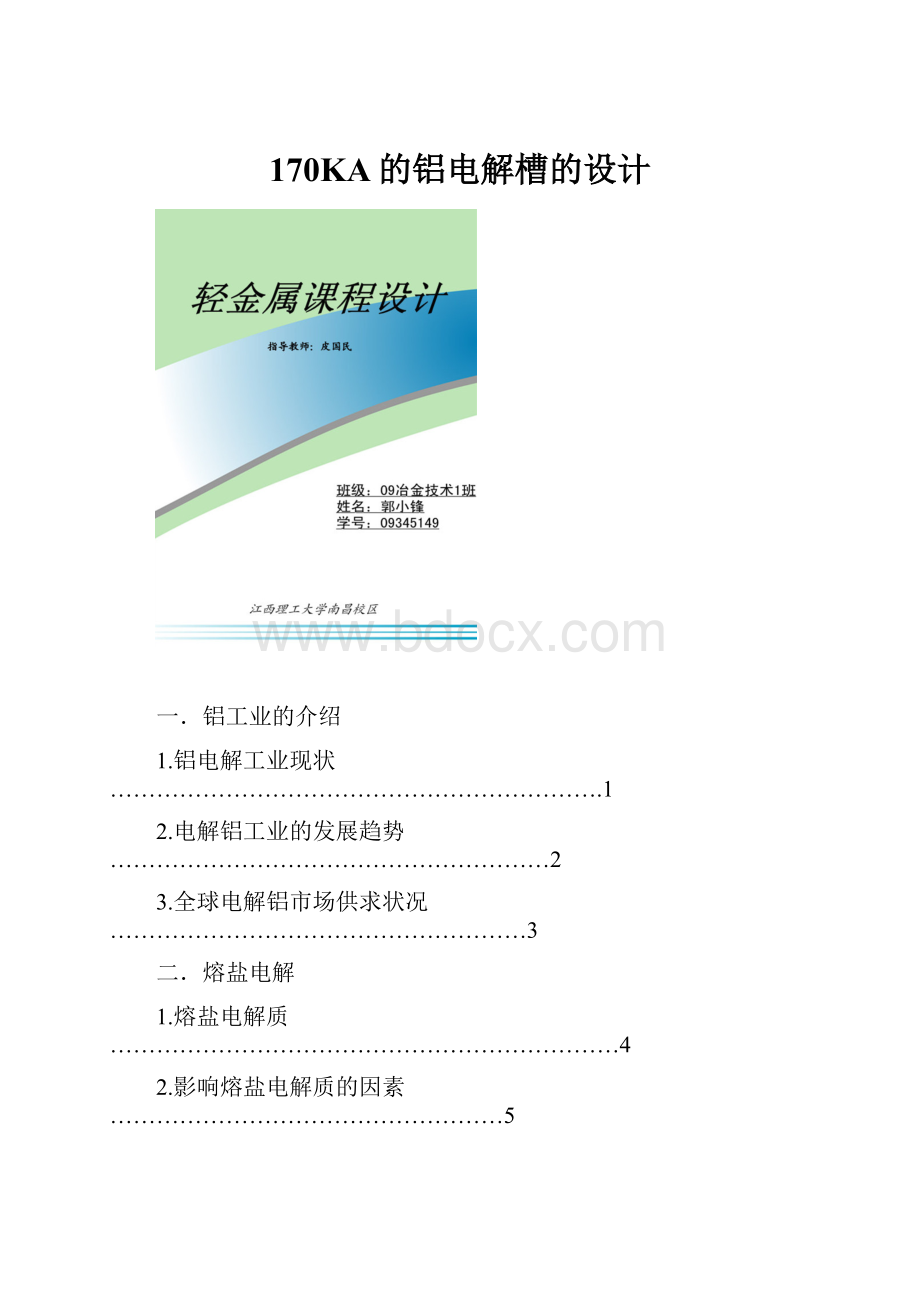
170KA的铝电解槽的设计
一.铝工业的介绍
1.铝电解工业现状……………………………………………………….1
2.电解铝工业的发展趋势…………………………………………………2
3.全球电解铝市场供求状况………………………………………………3
二.熔盐电解
1.熔盐电解质…………………………………………………………4
2.影响熔盐电解质的因素……………………………………………5
三.电解生产工艺流程…………………………………………………6
四.铝电解槽的设计计算
1.阳极结构参数的选择与计算………………………………………….…7
2.电解槽槽体结构选择计算………………….…………….….……….…8
3.阴极结构参数的选择及计算……………………………….………….…9
五.铝电解槽导电部件的选择计算
1.阳极部分导电部件的选择与计算…………………………….….………10
2.阴极部分导电部件的选择与计算…………………………………….…11
六.铝电解槽电压平衡计算
1.阳极部分…………………………………………………………..…12
2.电解质电压降…………………………………………………………13
3.阴极部分电压降………………………………………………………14
4.阳极效应分摊电压……………………………………………………15
5.连接母线压降…………………………………………………………16
七.电解槽电压平衡表………………………………………………17
八.铝电解槽工作制度………………………………………………18
九.设计心得…………………………………………………………19
十.附图………………………………………………………………20
170KA的铝电解槽的设计
一.铝工业的介绍
由于铝电解生产需要大量的电能,故降低单位铝产量的电能消耗量是历来追求的目标。
在铝工业生产初期,每千克铝电耗量高达30~40kwh-1。
以后,随着供电设备的更新,电解槽生产能力的增大,阳极和导电母线电流密度的减小,电解槽结构的改进和生产操作的改善,电耗率亦相应地有所降低,现在一般电耗率为13~15kwh-1/kg,有的甚至降低到12.5kwh-1/kg。
1.铝电解工业现状
本世纪八十年代以来,国外新增电解系列已普遍采用大型预焙阳极电解槽,系列电流强度普遍达到180~350kA,吨铝直流电耗降至12900~14000kw.h.t-1。
目前,西方国家用于生产的电解槽最大电流强度为350kA,且绝大多数企业为280~320kA的超大型预焙槽,电流效率平均达到了94%~96%。
近年来,我国新建槽多采用180~300kA的大型槽,改造旧槽因投资等方面的原因,多采用75kA或160~240kA之间的槽型,其技术与世界先进水平比仍有一定的差距,到目前为止,国内仅有少数企业采用技术上与世界一流企业基本同步的280~320kA之间的槽型。
目前,我国生产使用的铝电解槽,最大的槽型是电流强度为350kA的槽型(应用于平果铝业公司),还有电流强度仅24kA的槽型,我国电解槽电流效率平均仅为86%~90%。
2003年底全国833.82万t产能中,280kA以上特大型预焙槽产能为152.6万t,占总产能的18.3%;160~240kA大型预焙槽产能为387.1万t,占总产能的46.5%;小型预焙槽产能为190.24万t,占总产能的22.8%;还有103.88万t产能仍然是使用落后的自焙槽,占总产能的12.5%。
可见,虽然通过引进、消化、吸收国外先进技术和装备,我国电解铝行业整体装备水平有显著提高,但是,我国还有约100万t的自焙槽和约200万t的小型预焙槽,约占全国总产能的35%,这些低档次的生产技术设备,虽然具有生产工艺简单、投资省、见效快等优点,但技术装备水平较低,能耗、原材料消耗高,环境污染严重,技术经济指标较差。
表1—32000—2006全球电解铝市场供求状况
项目
2000
2001
2002
2003
2004
2005
2006
产量(万吨)
2442
2445
2609
2801
2925
3081
3280
消费量(万吨)
2484
2408
2550
2748
2915
3050
3300
供求(“-”号表示消费缺口)
-421
367
587
536
91
31
-12
表1—42005年底我国按电流强度区分的电解槽数量、产量和能力
电流强度
实有槽数
2005年底开工数
生产能力
产量
个
个
万t
万t
合计
21740
17816
1020
777.8
其中
320—350kA
596
556
53.5
47.9
280—300kA
3554
2774
265.7
159.0
115—240kA
10220
8976
526.4
460.5
10—90kA
7100
5512
174.4
110.4
电解铝工业的发展趋势
(1)世界铝工业的组织结构日趋规模化、集团化、国际化
此外,目前世界上新建铝企业的规模都比较大。
西方新建或改造电解铝的起步规模平均在25-50万吨之间。
如加拿大铝业公司投资19亿美元正在建设的阿尔玛(Alma)铝厂,年产能40万吨;2001年6月,由比利顿(Billiton)矿业公司控股的莫桑比克铝冶炼公司,投资10亿美元建设与一期相同的原铝能力25.3万吨;法国普基铝业公司计划在委内瑞拉建设一个年产能达46万吨的电解铝厂;几内亚拟在未来4-5年内投资25亿美元新建一个年产能达30万吨的电解铝厂及相关项目。
年产50万吨电解铝的海湾巴林铝厂拟扩产到70万吨规模。
扩大产能的目的是节约成本,提高劳动生产率,加强竞争力。
(2)铝电解槽日趋大型化或超大型化,其科技含量、智能化程度越来越高
冰晶石-氧化铝电解法发明110多年来,电解槽设计逐渐合理,容量大幅度增加,其科技含量、智能化程度越来越高,发展大型或超大型高效率、智能化的铝电解槽已经成为当今电解铝企业技术进步的标志和趋势,世界铝电解工业的技术及装备水平已经有了很大提高,在生产规模、电解槽容量、计算机应用、机械化和自动化程度以及烟气治理等方面都有了较大的进步变化。
(3)电解铝生产的技术经济指标向着高产、优质、低耗、长寿和低污染的方向加快进步
西方国家先进电解铝技术的发展,体现在技术经济指标的先进性上:
1)槽型大,电流强度达到300kA以上;2)电流效率高,一般达到94%-95%,个别企业已经提高到96%;3)吨铝直流电耗低,一般为13200-13400kWh,个别企业已经降低到13000kWh。
(4)世界铝工业向电力充裕廉价、铝土矿资源丰富的地区转移
目前,世界原铝生产成本中电费占据相当大的比重,因此,如何降低发电成本和电价,降低原铝生产电耗,是绿工业生存和发展的重要研究课题。
虽然日本是铝的消费大国,但铝产量却一直下降。
日本现在主要靠在海外投资来获取金属铝,仍保持人均年耗铝28kg的高水平。
日本铝工业的衰落,除资源贫乏之外,最主要的是能源短缺,铝用石油电价高达7.5美分/kWh,超过国际铝业平均用电价格2.0-2.1美分/kWh数倍。
日本铝工业的兴衰发人深思,电价渐渐变成左右铝工业发展的制约因素。
当今世界铝工业被迫向电力充裕廉价的地区转移,向铝土矿资源丰富区域和发展中国家转移。
二.熔盐电解
在电化顺序中,极为活泼的金属不能从盐类的水溶液中获得。
因为在水溶液中,该金属将与水作用而析出氢,并生成该金属的氢氧化物。
抽取此类金属,当以热还原法有困难时,经常采用电解该金属的熔融盐或溶于熔盐的氧化物。
有时熔盐电解是某些金属惟一的制备方法。
如铝钙铍锂钠等均以熔盐电解法制备。
许多稀有金属也可用熔盐电解法制得,如钍铌锆钽等
利用电能加热并转换为化学能,将某些金属的盐类熔融并作为电解质进行电解,以提取和提纯金属的过程。
熔盐电解在19世纪初已开始应用,随着熔盐电化学的迅速发展,至19世纪末期就以工业规模生产铝、镁等轻金属。
以后,又用于稀有金属的生产。
酸只有在水溶液中才可以电解
1.熔盐电解质
熔盐是熔融状态的盐类,其中主要是卤化物。
熔盐是离子熔体,有较高的电导率;在比熔点稍高的温度时,晶体结构虽然由于热运动而松散、溃乱,但在一定的距离内仍保持一定的有序性,称为近程序结构。
在电解中使用的熔盐电解质应该具有较低的熔点,适当的粘度、密度、表面张力,足够高的电导率,以及相当低的挥发性和不溶解被电解出来的金属熔体等性质。
为了达到这些要求,常常使用由几种盐类组成的混合物。
它们常具有比纯组分更低的熔点,但也有不少例外。
所以,必须通过实验来选择适当的混合盐组成。
通常,电解镁用NaCl-KCl-MgCl2混合熔盐;电解铝用Na3AlF6-Al2O3混合熔盐。
电解钽则用K2TaF7-Ta2O5混合熔盐;电解铍用BeF2·NaF-BaF2或NaCl-BeCl2混合熔盐。
2.影响熔盐电解的因素
和水溶液电解质一样,当熔融电解质与金属接触时,两者之间将产生一定的电势差,即电极电势。
在同一熔盐中插入两个电极,并利用外加电压通过直流电,当电压达到一定的数值时,熔盐中的某些组分将分解,平衡状态下化合物开始分解的电压称为分解电压(表1)。
常见金属的电化当量见表2。
熔盐的性质和它的组成、金属离子和阴离子的性质都会影响电化顺序中各金属的相对位置。
在大多数情况下,熔盐电解的电流效率低于水溶液电解。
影响电流效率的因素有:
温度、电流密度、极间距离和电解质的性质。
其中电解质对金属的溶解是降低电流效率的主要因素之一。
某些金属可与其高价化合物作用,生成低价化合物,例如:
CaCl2+Ca─→2CaCl
AlCl3+2Al─→3AlCl
低价化合物重溶于熔盐中,并易被空气或阳极析出的气体氧化而成为高价化合物,因而引起更多的金属被溶解,降低电流效率。
此外,析出的金属也可从熔盐中置换出其他金属,而溶解于熔盐中。
阴极反应熔盐电解时阴极上进行的反应为:
Men++ne─→Me
式中Me为金属,n为得失电子数。
当熔盐温度高于金属的熔点时,所得金属为液态。
在工业生产中,有时液态金属即成为阴极表面,如电解铝;由于工艺要求及电解槽构造的不同,有时生成的液态金属迅速自金属阴极离开,如电解镁、锂、钠等。
若熔盐温度低于金属熔点时,所得金属为固态。
随着条件的不同,可以得到金属粉末、片状晶体或薄层覆盖物。
由于高熔点金属的广泛应用,熔盐电解法在这些金属的制备中也获得更大的进展。
如铍、锆、钽、铌、钍等都可用此法制备。
阳极反应在电沉积时常使用碳电极作为阳极,而在电解精炼时则使用粗金属电极。
使用碳电极时,如MgCl2的电解,阳极反应可以使氯离子放电而析出氯气:
2Cl-─→Cl2↑+2e
也可以是碳与氧的化合,如Al2O3在冰晶石熔体中的电解,生成CO或CO2:
2O2-+C─→CO2↑+4e
在电解精炼中,粗金属作为阳极,其反应为:
Me─→Men++ne
电极电势较被提取金属为正的杂质将不溶解,而电极电势较被提取金属为负的杂质,虽溶解于熔盐内,但不能在阴极析出,从而起到提纯的作用。
三.电解生产工艺流程
1.电解原理
工业生产铝,主要采用冰晶石—氧化铝熔盐电解发。
主要设备是电解槽,电解法原理为:
直流电流通入电解槽,在阳极和阴极上起电化学反应,电解产物在阴极上析出率,阳极上是co2(约75%~80%)和co(约20%~25%).电解槽内,电解质通常有冰晶石。
氧化铝和添加剂组成,电解温度为940~950,密度为2.1g|cm3,铝液密度为2.3g、cm3,二者因密度差而分我上下层,铅液用真空抬包抽出,经过净化。
澄清和配料之后,浇铸成商品铝锭。
其纯度课达含铝量99.5%~99.8%.阳极气体中含有少量有害的氟化物和沥青烟气,经净化后,废气排入大气,收回的载氟氧化氯返回电解槽。
铝电解工艺流程如图所示
工业铝电解槽槽型有侧插棒自焙阳极铝电解槽(见电解槽)、上插棒自焙铝电解槽(图1)和预焙阳极铝电解槽(图2),三者各有特点。
自焙阳极铝电解槽按其阳极消耗情况定期地从上部添加阳极糊,利用电解槽运行产生的热量,将新加入的阳极糊焙烧成为坚实的固体阳极。
阳极因此能连续使用,正好与电解的连续过程相适应。
但自焙阳极铝电解槽在铝电解运行中焙烧阳极时散发出有害的沥青烟气,污染生产厂房和外部环境,回收烟气并加以净化较为困难,回收净化费用也较高。
预焙阳极铝电解槽使用预先焙烧过的阳极,待阳极消耗到一定的高度时就要更换。
把旧阳极取出,换上新阳极,不能连续使用。
由此产生了残极,而且在更换阳极时会影响铝电解生产。
预焙阳极铝电解槽由于其阳极事先已在专用的焙烧炉中焙烧好,焙烧过程中产生的烟气可用作为焙烧炉的燃料,因此产出的是无沥青烟气,回收净化较为容易,净化费用较低,厂房内外环境较好。
就机械化和自动化程度而论,以预焙阳极铝电解槽最高,特别是中部下料的预焙阳极铝电解槽;上插棒自焙阳极铝电解槽次之;侧插棒自焙阳极铝电解槽最低。
电极电压降高低的顺序为:
上插棒自焙阳极铝电解槽最高,侧插棒自焙阳极铝电解槽居中,预焙阳极铝电解槽最低。
从投资来看,预焙阳极铝电解槽的上部结构和阳极装置比较简单,电解槽本身造价较低,但制造预焙阳极需要额外的阳极成型、阳极焙烧和阳极组装等一整套设备,增加投资较多,一般适用于大型铝电解厂。
上插棒自焙阳极铝电解槽上部结构比较复杂,投资较高。
侧插棒自焙阳极铝电解槽投资则相对较低。
按电解槽容量而言,预焙阳极铝电解槽容量最大,上插棒自焙阳极铝电解槽次之,侧插棒自焙阳极铝电解槽最小。
近年来,由于预焙阳极铝电解槽,特别是中部加料的预焙阳极铝电解槽在铝电解过程中无沥青烟害,密闭程度高,烟气收集和净化效率好,阳极电压降低,操作运行机械化、自动化程度高,适于电子计算机控制管理,因而为世界上大多新建的大型铝厂所采用。
而中小型铝厂则一般采用自焙阳极铝电解槽。
基本结构工业铝电解槽的基本结构主要包括阴极装置、阳极装置、母线装置和气体回收装置等。
阴极装置由槽壳、阴极碳块、侧部碳块、耐火砖和保温材料组成。
通常采用长方形槽壳,槽壳型式有框架式、臂撑式和摇篮式三种。
槽壳用型钢和钢板焊成。
铝电解槽的槽膛深度一般为450~600mm。
槽膛底部是一层阴极碳块,其下面依次是炭素垫、耐火砖层和保温砖层,有的用氧化铝或其他保温材料取代保温砖层或部分保温砖层。
阴极碳块以碳块组型式砌筑于电解槽内。
阴极碳块组由阴极碳块同埋设其中的导电钢棒(阴极棒)组成。
阴极棒与碳块之间浇铸磷生铁或用碳糊捣固。
阴极碳块组在槽壳内排成两行,碳块组与碳块组间用碳糊捣固或用碳糊浆液灌注。
但纵向中缝一般要用碳糊捣固。
有些电解槽为提高炉底导电性和减去纵向中缝,特意采用通长阴极碳块,其中放置一根通长阴极棒。
阴极棒通过槽壳侧壁上的洞口(窗口)伸出槽壳,其末端与阴极母线连接。
槽膛侧壁有一层或两层阴极碳块。
侧部碳块与槽壳之间用一层耐火砖或颗粒状耐火材料填充。
近年来,大型铝电解槽,特别是中部加料预焙阳极铝电解槽的侧部保温层有所减薄,.以利于凝结固体电解质作为保护层。
有的电解槽还在侧部碳块下部用碳糊捣固成斜坡状,构成人造伸腿,用来保护侧部碳块并收缩铝液镜面。
阳极装置视槽型而异,有三种形式。
(1)侧插棒自焙阳极铝电解槽的阳极装置。
由阳极框架、碳阳极糊、阳极导电棒、氧化铝料仓及阳极升降机构组成。
阳极框架由钢板和型钢焊接而成。
框架内周为厚1mm左右的铝板(铝壳),中间填充阳极糊,阳极棒从阳极框架外部与水平方向成15°角度插入阳极糊内。
阳极棒作为导电体及悬挂阳极用。
阳极棒一般有4排,排向距离200mm,其中下面的两排棒通电,上面的两排作为后备。
随着阳极消耗,取出最下面的一排阳极棒,在上方插入一排新的阳极棒。
阳极棒用铜质导电片来与阳极大母线联接。
阳极框架借助滑轮组或螺旋机构悬吊在电解槽的上部金属结构上,因此阳极可以上下升降。
(2)上插棒自焙阳极铝电解槽的阳极装置。
由阳极框套、阳极糊和组合阳极棒及阳极升降机构组成。
阳极框套由钢板和型钢焊接而成,框套内填充阳极糊。
阳极钢棒为组合式,它由钢质导电棒与上端的铝导杆联接而成,一般采用爆炸焊接。
钢质导电棒由上部垂直插入阳极糊内,分4排插入,高度分若干层次。
组合阳极棒用夹具直接连接到阳极母线上。
阳极有两套提升机构。
随着阳极的消耗,用主升降机构降低阳极母线大梁,亦即阳极本身的高度。
与此同时靠辅助升降机构以精确的相等速度提升阳极框套的位置,其结果是阳极框套的位置移动等于零,它相对于槽壳并未作任何移动,但阳极可以下降,补偿其消耗。
(3)预焙阳极铝电解槽的阳极装置。
由阳极碳块组和阳极升降机构组成。
现代大容量中部下料铝电解槽还配备定时打壳下料装置和氧化铝、氟化铝料仓。
阳极碳块组由阳极碳块、钢爪和铝导杆三部分组成。
依据槽容量大小及碳块规格不同可有单块组、双块组和三块组。
铝导杆与钢爪通常采用爆炸焊联接,钢爪置入碳块上的洼穴(碳碗)中,钢爪和碳碗间浇注磷生铁。
也有用碳糊捣固的。
阳极碳块表面喷一层铝液以防止其氧化,也有不喷铝液的。
铝导杆用夹具紧固于阳极母线梁上。
下料机构包括4~6个打壳锤头和相同数量的定量加料仓。
加料点位于铝电解槽的中心部位自成一列。
打洞加料自动进行,间隔时间短的不过3min,长者为1~2h。
现代化铝电解槽的下料已采用自动控制方式,保持电解质中氧化铝浓度波动在一个很小的范围(2%~3%)内。
大容量铝电解槽的阳极升降,一般选用蜗轮丝杠或滚珠丝杠摇板式机构。
母线装置由阳极母线、阴极母线和立柱母线组成。
母线为铝质压延母线或铝质铸造母线。
铝母线的配置方式,视电解槽的排列方式和容量的不同而异。
配置母线需经过精心设计,以求减弱磁场对电解运行的有害影响并节省母线用量。
现代化大容量预焙阳极铝电解槽一般采用横向排列,母线配置采用多端(4端或5端)进电方式。
中小型铝电解槽一般采取纵向排列,母线配置采取双端或单端进电方式。
气体回收装置侧插棒自焙阳极铝电解槽带有钢质卷帘或吊门,将电解槽加以密闭,由排烟管将烟气导出。
上插棒自焙阳极铝电解槽由安装在阳极框套下部的集气罩将烟气收集于燃烧气中,经燃烧后的烟气排入烟道。
预焙阳极铝电解槽用带有筋板的铝板构成多片单槽罩或整体槽罩,将电解槽密封。
使用寿命 铝电解槽的阴极内衬在使用一段时期后就会破损,这时候便需停槽大修。
现代铝电解槽的平均使用寿命可达4~5a,长者可达7~8a。
铝电解槽破损停槽的主要标志为槽内铝液中铁含量连续不断的增加以至于超过1%,表明碳阴极已发生破损,钢质阴极棒已被铝液侵蚀,此时需停槽大修。
铝电解槽破损主要发生在碳阴极本体中。
同时碳阴极下部的耐火砖和保温材料中也发生严重变化,钢质槽壳也伴有严重变形或破裂。
根据现场观察,破损现象有:
(1)碳阴极中出现大而深的裂纹;
(2)碳阴极出现冲蚀深坑;(3)碳阴极呈层状剥落;(4)碳阴极向上隆起并开裂;(5)阴极棒受铝液侵蚀并熔化,阴极棒发生变形,向上隆起;(6)槽底耐火砖和保温材料受电解质侵蚀,其中间部位存在棱镜状灰白层;(7)侧部碳块受电解质和铝液冲刷磨蚀产生孑L洞;(8)钢质槽壳向外膨胀呈椭圆形,底部钢板向下鼓出甚至开裂。
这些破损现象彼此相互联系,可能会同时出现。
大多数人认为铝电解槽破损主要是由于钠对碳阴极的侵蚀。
在铝电解过程中,钠始终向碳阴极渗透。
钠是由两种反应产生的,一种是钠离子在阴极上放电生成的,另一种是铝和电解质中氟化钠起反应置换出钠。
钠渗透到炭素材料中导致炭素材料体积膨胀并产生裂纹,铝和电解质沿裂缝侵入阴极,最终导致停槽大修。
为了延长铝电解槽的使用寿命,要从多方面采取措旎。
在设计时通过精确计算,设计出强度高的槽壳,并使槽内的热场和磁场分布合理。
建造时要采用高质量的砌筑材料和进行精确的施工。
操作上要采用合适的焙烧和启动方式,并建立平稳的正常运行制度等。
展望 铝电解槽的主要发展方向有:
(1)采用惰性电极代替碳电极,例如采用氧化锡基或氧化镍基阳极,以及采用硼化钛基阴极,以减少电能量消耗;
(2)通过加大现有铝电解槽的电流容量,提高单槽的生产能力并减少能量消耗的办法,来达到降低生产成本的目的;(3)实现连续下料作业,使铝电解槽的各项技术参数,如氧化铝浓度,冰晶石比、电解温度等基本达到稳定,把铝电解电流效率提高到95%以上,吨铝能量消耗降低到12000kW•h。
四.铝电解槽的设计计算
基础数据:
产量:
10万吨/年铝锭
容量:
170KA
阳极电流密度:
0.7A/cm2
效应系数:
<0.2次/槽••••日
电流效率:
94%
阳极炭块尺寸:
1450*660*550
单槽原铝产量:
日产170*0.94*0.3355*24=1286.7Kg
年产1286.7*365*0.001=496t
1.阳极结构参数的选择与计算:
S阳=170000/0.7=242857.1cm2
需阳极炭块数为:
n=242857/(145x66)=25.4
取26块阳极,分两行排列,每行13组炭块
阳极实际面积校核值为:
S阳=26*145*66=248820cm2
D阳=170000/248820=0.683A/cm2
槽膛尺寸取阳极到槽膛侧壁尺寸为380mm,到槽膛端壁之间的距离为460mm,阳极炭块组之间距离取45mm,阳极行间距取250mm,由此计算:
槽膛长度=2*460+13*660+12*45=10040mm
槽膛宽度=2×380+2×1450+250=3910mm
槽膛深度=560mm
2.电解槽槽体结构选择计算
槽内衬选择与计算
5.1槽侧部内衬选择侧壁用一层炭块,通常用炭糊再打一层斜坡,但“伸腿”不易扎固,采用梯形侧部炭块就不用打炭糊“伸腿”.炭块与槽壳之间留有25mm伸缩缝,用耐火颗粒填充
5.2槽底内衬选择侧部为散热性结构,一般底部和上部要加强保温。
在阴极炭块下面有炭素底垫(30mm),三层耐火砖(3×65mm),一层氧化铝粉(100mm),三层保温砖(3×65mm),硅酸盐保温砖一层(65mm)。
由此可计算;
底部厚度=450(底部炭块)+30+3×65+100+3×65+65=1035mm
槽深=1035+560(槽膛深)=1595mm
5.3槽底
槽底部阴极炭块的选择可采用1680×545×450mm,分两行排列,亦可采用通常阴极炭块,其规格3370×515×450mm,单行排列共17组,炭块间用炭糊扎缝(30mm),由此可计算阴极炭块侧部到槽膛侧壁与端壁之距离分别为;
炭块到端壁边缘尺寸=
=145mm
炭块到侧壁边缘尺寸=(3910-3370)/2=270mm
5.4槽壳结构及尺寸
槽壳结构有臂撑式和摇篮式两大类。
摇篮架是弹性变形体,这种槽壳受力不产生应力集中,在电解槽的端角部位,不能发生断裂现象,这是摇篮式槽壳最大优点。
摇篮支架选用360mm工字钢,厚钢板焊制而成,槽侧壁及端臂都没有一些摇篮架。
根据槽膛及槽内衬尺寸可以算出槽壳尺寸:
槽壳宽度=3910+2×150(内衬)+2×13(钢板)+2×27(伸缩缝)
=4290mm
槽壳长度=10040+2×150(内衬)+2×13(钢板)+2×27(伸缩缝)
=10420mm
槽壳深度=560+1035(底部内衬厚度)+13(钢板)+40(槽沿板)
=1648mm
3.阴极结构参数的选择及计算
阴极电流密度一般取0.18~0.25A/mm