变频器控制功能的参数选择与典型应用.docx
《变频器控制功能的参数选择与典型应用.docx》由会员分享,可在线阅读,更多相关《变频器控制功能的参数选择与典型应用.docx(16页珍藏版)》请在冰豆网上搜索。
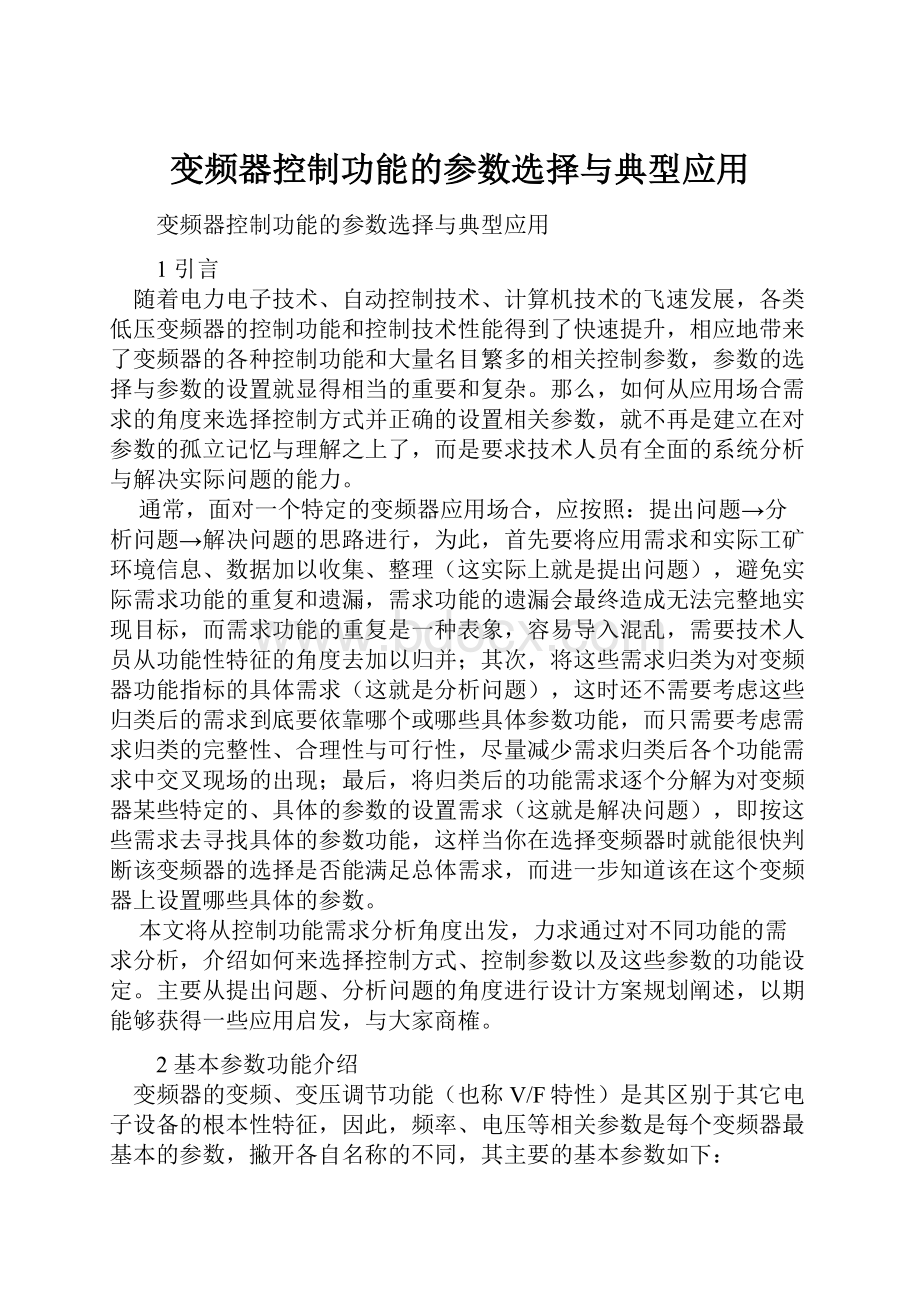
变频器控制功能的参数选择与典型应用
变频器控制功能的参数选择与典型应用
1引言
随着电力电子技术、自动控制技术、计算机技术的飞速发展,各类低压变频器的控制功能和控制技术性能得到了快速提升,相应地带来了变频器的各种控制功能和大量名目繁多的相关控制参数,参数的选择与参数的设置就显得相当的重要和复杂。
那么,如何从应用场合需求的角度来选择控制方式并正确的设置相关参数,就不再是建立在对参数的孤立记忆与理解之上了,而是要求技术人员有全面的系统分析与解决实际问题的能力。
通常,面对一个特定的变频器应用场合,应按照:
提出问题→分析问题→解决问题的思路进行,为此,首先要将应用需求和实际工矿环境信息、数据加以收集、整理(这实际上就是提出问题),避免实际需求功能的重复和遗漏,需求功能的遗漏会最终造成无法完整地实现目标,而需求功能的重复是一种表象,容易导入混乱,需要技术人员从功能性特征的角度去加以归并;其次,将这些需求归类为对变频器功能指标的具体需求(这就是分析问题),这时还不需要考虑这些归类后的需求到底要依靠哪个或哪些具体参数功能,而只需要考虑需求归类的完整性、合理性与可行性,尽量减少需求归类后各个功能需求中交叉现场的出现;最后,将归类后的功能需求逐个分解为对变频器某些特定的、具体的参数的设置需求(这就是解决问题),即按这些需求去寻找具体的参数功能,这样当你在选择变频器时就能很快判断该变频器的选择是否能满足总体需求,而进一步知道该在这个变频器上设置哪些具体的参数。
本文将从控制功能需求分析角度出发,力求通过对不同功能的需求分析,介绍如何来选择控制方式、控制参数以及这些参数的功能设定。
主要从提出问题、分析问题的角度进行设计方案规划阐述,以期能够获得一些应用启发,与大家商榷。
2基本参数功能介绍
变频器的变频、变压调节功能(也称V/F特性)是其区别于其它电子设备的根本性特征,因此,频率、电压等相关参数是每个变频器最基本的参数,撇开各自名称的不同,其主要的基本参数如下:
(1)基本频率
是指变频器输出额定电压时所对应的频率值,有时也称为额定频率。
通常按照图1(a)所示的设置就可以满足V/F特性需求,即将电机的额定数据(额定电压380V、额定频率50Hz)作为该参数的值,这时斜线①的斜率K=380/50=7.6,它的V/F关系相当于直线方程V=7.6F。
但也有例外,比如:
当我们试图使用一个变频器去驱动1台3相50HzAC220V的电机时,就需要按图1(b)中的斜线②来设置而不能再按斜线①设置参数。
(2)转折频率
是指变频器在该转折点的输出电压已经达到额定电压参数所设置的电压数值,在这点以后的输出频率运行段都不再增加其输出电压,即输出电压将维持在这个电压值不变。
在图1(b)中,对于斜线①来说,其V/F的转折频率点是A点;对于斜线②来说,其V/F的转折频率点是C点。
通常,我们将转折频率值设置与基本频率值相同,以便在变频器输出频率达到基本频率后,使变频器的输出电压维持在额定电压不变。
如图1(a)所示。
图1变频器部分基本参数特性图
(3)启动频率
是指变频器开始有电压输出时所对应的频率。
在变频器启动过程中,当变频器的输出频率还没达到启动频率设定值时,变频器就不会输出电压。
通常,为确保电机的启动转矩,可通过设定合适的启动频率来实现。
(4)上下限频率
上限频率、下限频率有时也被分别称为输出频率上限、输出频率下限。
顾名思义,这个参数是对变频器运行时输出频率的一种限制。
需要注意的是,在变频器启动过程中,输出频率下限是不起作用的。
例如:
在图1(a)中当变频器正处于从E点到A点的启动过程中时,尽管设置了输出频率下限D点,但ED段仍然有频率和电压输出。
只有当变频器已经在DA段运行时,就再也不能进入DE段运行了。
在图1(c)中的H点就更直观地反映了这种情况。
输出频率上限值的设定将使变频器的实际运行频率输出值永远小于该设定值,哪怕是给定频率值超越了上限输出频率,变频器也不会出现实际输出频率超越上限输出频率限制的情况。
通常情况下,我们设定“上限输出频率值≥额定频率值”,如图1(a)所示,这样就可以实现电机在超越额定速度的状态下运行。
但,在图1(d)中却发现了“上限输出频率值≤额定频率值”的相反情况。
那么,在什么情形下才要这样的参数设置应用呢?
例如:
对于一个轻负载和低启动转矩的“小马拉大车”变转矩负载应用系统或者对于扬程、流量等有输出限定的节能控制应用场合。
对于前者,只要“小马”(变频器标称额定输出功率小于电机的额定功率)能够让电机得以顺利启动,那么,就可以通过这种方法来使电机始终运行在其输出功率小于等于变频器标称额定功率范围内,从而达到“小马拉大车”的应用实现。
对于后者,可以作为“1+1≤1”的节能优化控制判断点(控制器通过对上限输出频率到达点的判断,来决定此时是选择继续以单台泵提升输出频率方式变频运行,还是以2台泵同时变频运行),假定:
有这样的2套完全一样的水泵电机,其电机额定功率为45kW,水泵额定流量320m3/h。
若当前系统实际仅需要流量256m3/h,那么只需要1套水泵电机以40Hz的频率运行就可以满足需求,此时,电机实际消耗功率约需要24kW。
若此时系统实际需求流量需要增加到305m3/h时,那么该电机必须以约48Hz的频率运行来满足此时的流量需求,那么,此时该电机实际消耗功率约为40kW。
现在让我们同样在系统实际需求流量为305m3/h时,改变仅1#泵变频运行的这种习惯,让系统在需求流量大于288m3/h时就转换为2套电机水泵系统同时变频运行状态,为了同样达到305m3/h的实际系统流量需求,那么2套电机水泵系统就必须同时按输出频率约24Hz的频率运行,那么,此时2套水泵电机各自仅需要消耗约6kW的输出功率,即累计消耗功率小于12kW。
可见此时2套泵同时变频运行要远比单套水泵电机运行时所消耗的功率40kW要小很多。
此就是“1+1≤1”的节能优化运行控制。
关于详细的功率计算对比,请参阅本人发表在2005年05月的《变频器世界》的“中央空调系统变频节能改造控制技术的分析与实现”一文相关章节的内容。
除以上几个与频率相关的基本参数外,还有一个最大、最小频率的概念,它是对应最大、最小频率给定值的一个范畴参数,通常我们将以上几个频率参数都设定在这两个参数的范围内,如图1(d)所示。
图2典型应用案例图
(5)转矩补偿
变频器将电机在一定时间内从静止状态驱动到一定的运转速度,需要克服机械装置的静态转矩阻力和运行加速度转矩阻力。
由于电机在低速时激磁电压降低,为此,需要补偿电机的欠激磁状态,使电机低速运行时转矩增强(V/F特性增强,也即V/F在低频段的斜率增大),以此来克服这2种转矩阻力。
图1(b)中的斜线③是对斜线①的转矩补偿作用后的结果。
需要指出,转矩补偿值较大时,容易导致低速时电机发生过激磁状态,按这种状态连续运行时,电机可能会发生快速发热现象,危害电机的安全运行;同时,转矩补偿值过大时,也容易产生启动阶段过压甚至过流故障发生。
转矩补偿值的大小应该以满足电机启动需求的最小值为较好。
(6)加减速时间
变频器加速时间、减速时间分别对应电机在启动过程从0Hz到最大输出频率所需要的时间、停止过程中从最大输出频率到0Hz所需要的时间。
如图1(c)所示。
加减速时间的大小将直接影响频率给定跃变到实际最终输出频率响应时间的长短。
对于诸如风机类大惯量平方特性负载,时间值的过长或过短都将容易引发变频器在启动、停止过程中的过压、过流故障的发生。
需要在实际调试中通过不断的启停操作的尝试来寻找合理的时间设定值。
另外,与加减速时间相关的参数还有加减速曲线类型选择问题,图1(c)中的斜线①、斜线②、斜线③是针对3种不同负载特性在加减速过程中而设置的,可参考LG公司《IS5系列变频器用户手册》来了解这个问题,这里不再赘述。
(7)与电机保护直接相关的参数
变频器不仅是一个变频、变压装置,更是一个电机综合保护装置,通常都有以下保护功能参数:
输入/输出缺相保护、电子热保护、热敏保护、过载保护、过流保护、堵转保护等。
除输入缺相保护是对进线电源因素的保护外,后5种保护都是针对电机的直接保护,区别在于热敏保护是一种直接的电机温度信号检测结果的保护,而其它保护则是一种基于电机铭牌数据(包括额定功率、电流、电压、频率、转速,以及定子电阻与电抗)而进行的电流热效应计算的理论保护。
电机的铭牌数据可以手动设置,在大多数主流变频器中,也可以利用一个被称为“自动马达适配”(AMA:
AutoMotorAdapter)的参数帮助我们自动设置电机的部分特征参数。
另外,需要指出的是堵转保护功能的使能作用,经常会导致电机启动过程中实际加减速时间将不再严格按照加减速时间参数的设定值进行,通常会导致实际启停过程的时间延长。
(8)与启停操作和频率给定方式相关的参数
撇开RS-485串行通讯方式,变频器的启停操作方式和频率给定方式一般都各自有2种:
操作面板和端子。
因此,我们可以得出变频器如表1所述的4种组合运行方式:
表1启停操作与频率给定方式的组合
其中,“0”代表该方式无效,“1”代表该方式有效。
它们各代表的意义是,编号0:
全端子操作与频率给定方式;编号1:
端子启停+面板频率给定方式;编号2:
面板启停+端子频率给定方式;编号3:
全面板操作与频率给定方式。
在集中控制系统应用中以编号0方式(下文会常用到)使用的最多。
在对变频器的主要基本参数做出介绍后,下面让我们来介绍一下变频器中都有哪些常用的控制方式,针对这些控制方式都应用在哪些比较典型的应用场合,以及相应需要设置哪些相关参数。
本文把以下将要介绍的开环与闭环控制方式、工艺过程控制方式、开环转矩控制方式、速度反馈转矩控制方式统称为常规控制方式,而把专用变频器或通过选件卡实现的为某个特定行业应用而 采用的控制方式称为特殊控制方式。
3开环与闭环速度控制方式
对变频器控制而言,所谓开环就是变频器的运行输出频率只受频率给定值大小变化的影响,而没有与外部反馈信号作用建立数学关系或根本就不存在外部反馈信号。
可见开环控制方式在概念上是一种只顾“命令”而不顾“实际结果”的控制方式(之所以说是概念上,是因为现在有些变频器产品,诸如通过滑差补偿等参数的设定可以达到命令与结果之间有一定程度的关联),因此,开环速度控制方式的速度精度不够精确,对需要追求高精度速度准确性或实际速度追踪调节的控制应用场合,就需要采用闭环速度控制方式。
需要申明的是,我们在这里讲的开环与闭环都是站在变频器设备的角度而不是控制系统角度进行判定的。
比如,在我们经常看到的变频恒压供水系统中,那些通过数字PID仪表来设定压力给定值和接收现场压力变送器的实际压力反馈信号的控制方式,若站在控制系统角度,这个系统就是闭环控制方式,但若站在变频器角度看,在这里仍然被称为开环控制方式,因为对变频器而言它的运行频率给定来自PID仪表的输出,整个给定、反馈、调节等功能全部又PID仪表来完成的,变频器只是被作为一个驱动执行设备在使用。
3.1开环速度控制方式
●问题1的提出
假设有这样一个印刷业务用户,如图2(a)所示,希望通过变频驱动实现对收卷过程的恒定线速度控制,具体要求如下:
(1)启停操作和调速都在现场操作箱上进行,并可通过电位器在控制箱上调节收卷的线速度;
(2)收卷电机的线速度要始终与牵引电机的线速度保持一致(放卷由刹车片控制,张力由张力架调节);
(3)限定速度调节范围。
针对用户的机械设备和提出的这个需求,我们将其控制驱动对象分为2个部分:
牵引辊道电机驱动和收卷筒电机的驱动。
●问题1的分析
首先,让我们看看用户对牵引电机控制的要求,针对用户的需求,可以把其中对牵引电机的需求收集为表2所示的具体子项,并将这些子项对应给出所需求的变频器功能。
很显然,按照表2中的参数,在牵引电机上只需要采用开环速度控制方式就可以满足用户对牵引电机变频驱动的要求。
同时,按照表2中的各项“需求对应的变频器功能”,我们也很容易去寻找到具备这样功能的变频器,那么,我们也就能相当轻松地完成用户对牵引电机的控制需求了。
当然,除了表2中的需要功能外,变频器的一些基本参数功能,诸如:
电机参数、频率参数、加减速时间参数等(如第2节内容所提到的一些基本参数),无论在什么样的控制方式应用系统中都是必不可少需要设置的,这里不再赘述(以下类同,略)。
表2开环速度控制方式的功能需求与参数选择
通过以上分析,可以得出如表2所示的分析结果。
再按照表2中的归类后的功能需求,逐个分解为对变频器某些特定的、具体的参数的设置,这样就可以得到如图2(a)中的1#变频器所示的设计结构图了。
图2(a)中的1#变频器采用的控制方式就是开环控制、编号0方式。
在本文中,对于常规控制方式的案例分析中,不准备将诸如表2中的对应的变频器功能再进一步转化为某个特定品牌的变频器参数,以免给读者造成品牌依赖性误导(以下常规控制方式的案例同),只想表达一种思维过程,供读者参考。
而对于特殊应用场合的控制方式,将以具体品牌为例加以说明。
3.2闭环速度控制方式
●问题2的提出
同问题1的提出,如图2(a),略。
●问题2的分析
首先,由于用户需要收卷电机的运行线速度与牵引电机保持一致,为达到这个目的,我们只要将牵引电机与收卷电机用同一个速度给定就可以实现这2台电机角速度的一致(当然,也可以将牵引电机实际运行速度的输出信号DC4~20mA或DC0~5V/10V作为收卷电机的速度给定信号,这2种方式的差异在于:
前者为同步速率给定方式;而后者为主从随动给定方式,存在一定的响应延迟,具体差异分析,略);其次,由于收卷滚筒在运行过程中,随着纸张等物体被不断地缠绕在滚筒上,导致滚筒的半径在不断地增大,如果收卷电机的角速度保持不变,那么,收卷过程中的线速度也同样在不断地加快,为满足用户对收卷过程中线速度恒定的需求,必须想办法让收卷电机的角速度随滚筒半径的增长而降低,以实现线速度恒定的目的。
为此,需要一个检测线速度的传感器信号,以此来作为变频器的速度反馈,告诉变频器要做出角速度的实时调整。
在本例中,我们在夹送导向辊上安装了编码器(不能安装在电机轴或收卷滚筒轴上,否则,编码器测出的信号就不是线速度反馈信号而是角速度反馈信号),以编码器的脉冲率来表示实际线速度的快慢。
如图2(a)中所示,这样对于2#变频器而言,它既有一个用电位器表示的给定速度,又有一个用编码器的脉冲来表示的实际速度反馈信号,因此,2#变频器就应该是一个闭环速度控制方式的应用案例。
通过以上对用户需求的分析,我们可以得出如表3所示的结果。
表3闭环速度控制方式的功能需求与参数选择
在表3中,我们略去了与闭环速度控制非直接相关的其它一些功能的列举,在实际应用中就像对基本参数的需求一样,同样需要对这些功能进行选择与相应参数的设置。
4工艺过程闭环控制方式
传统的V/F控制实际上是一种角速度的控制模式,而闭环速度控制是通过对实际角速度的检测的一种调节控制。
但是,在现实的许多应用场合,显然,我们并不只关心电机的速度,而可能更多地要关注生产工艺过程中的某些被控对象的参数测量值,这些参数包括:
温度、压力、流量、液位等信号。
比如,在混配料系统中,我们可能需要关心某种配料的质量或流量,而这个量却并不直接与电机的速度成正比例或反比例关系,这是工艺闭环过程控制与上面所叙述的闭环速度控制的根本差别,当然,工艺过程闭环控制也是一种闭环控制,它关注的不是速度而是工艺过程的参数变量。
在诸如这样的一些应用场合,就需要我们采用工艺过程闭环控制方式。
●问题3的提出
假定有一个需要进行混配料比例控制的用户,他的配料A和配料B由各自的配料电机送入配料搅拌筒中进行混合均匀搅拌,其中,配料B有生产过程决定其送料的多少,而配料A需要根据配料B的变化始终保持在搅拌筒混合料中的比例恒定,如图2(b)所示。
现要求对配料A的电机进行变频控制,以实现如下具体需求:
(1)配料A的比例可以自由设定;
(2)既使在配料B的量是变化的时候,配料A在混料搅拌筒中的比例也要维持在设定比例。
●问题3的分析
首先,用户对配料电机A的控制需求是要根据配料B的变化始终维持恒定的配料A所占比例的一种闭环控制方式,这个反馈信号是混料筒中的配料A所占的比例信号,它与电机的速度无关,因此,可以准确地定位这种控制需求为工艺过程闭环控制方式。
其次,用户要求配料比可以在生产过程中根据需要进行设定,为此,需要提供配料A所占比例的设定手段—电位器给定配料比方式。
椐此可以得到如表4所示的需求与对应功能。
表4工艺过程闭环控制方式的功能需求与参数选择
对比表4与表3,可以看见,他们之间的差异除了控制方式的选择区别外,还有一个最为明显的差异,那就是表4中作为控制对象的参考量与反馈值都是生产工艺过程中的参数(这样设定的参数与反馈的参数都更直接表达了生产过程状态,也更加直观明了),而不再是速度参数。
撇开这些表面上的差异,几乎完全可以用一个虚拟的闭环“速度”控制来实现。
从这个意义上讲,工艺过程闭环控制方式与闭环速度控制方式在本质上是没有差异的,它是闭环速度控制方式的延伸形式与变种应用。
5开环转矩控制方式
上面介绍的无论是开环与闭环速度控制,还是工艺过程闭环控制,其实质都还是变频器的矢量控制技术的一种应用。
矢量控制实现的基本原理是通过测量和控制异步电动机定子电流矢量,根据磁场定向原理分别对异步电动机的励磁电流和转矩电流进行控制,从而达到控制异步电动机转矩的目的。
具体是将异步电动机的定子电流矢量分解为产生磁场的励磁电流分量和产生转矩的转矩电流分量分别加以控制,并同时控制两分量间的幅值和相位,即控制定子电流矢量,所以,称这种控制方式称为矢量控制方式。
矢量控制方式又有基于转差频率控制的矢量控制方式、无速度传感器矢量控制方式和有速度传感器的矢量控制方式等。
而转矩控制则是以转矩为中心来进行磁链、转矩的综合控制。
和矢量控制不同,直接转矩控制不采用解耦的方式,从而在算法上不存在旋转坐标变换,简单地通过检测电机定子电压和电流,借助瞬时空间矢量理论计算电机的磁链和转矩,并根据与给定值比较所得差值,实现磁链和转矩的直接控制。
对交流电机的直接转矩控制(DTC)技术的引入,使得交流电机转矩特性像直流电机一样在应用中表现的“硬”起来了,因此,DTC可以说是变频器技术发展史上的又一个里程碑。
目前,在丹佛斯VLT2800/5000、ABBACS6000、爱默生TD2000等产品中都有直接转矩控制功能。
开环转矩控制方式就是利用变频器本身对电机的转矩的控制来实现输出轴转矩的稳定控制,这种控制方式可广泛地应用在那些在运行过程中需要保持转矩恒定,不需要改变运行方向的场合,诸如:
卷绕、挤压、皮带输送等相关行业应用。
●问题4的提出
假定有一个石料厂的皮带输送机用户,皮带输送机需要不断地将从料斗中卸下的片石块送到破碎机中进行破碎,如图2(c)所示,用户想对这个皮带输送机进行变频驱动改造,具体要求如下:
(1)由于料斗下料的大小、快慢不均匀,致使落在皮带上的石块总量不一致,希望即使在皮带上的石块较多时,皮带也能够拖的动;
(2)皮带上的石料多时,速度可慢些,在皮带上的石料较少时,希望皮带能尽可能快些;
(3)现场无法提供检测石块在皮带上数量多少的信号。
●问题4的分析
首先,应用现场无法提供被控对象的检测信号,可以说只能采用开环控制方式;其次,用户的第②个需求,实质上就是转矩控制的运行特点,而要保证一个始终稳定的输出转矩(用户的第①个要求)就只有采用转矩控制方式,至此,我们可以肯定地说这个案例需要采用开环转矩控制方式。
椐此可以得到如表5所示的需求与对应功能。
表5开环转矩控制方式的功能需求与参数选择
用以上的方法在给一个90kW电机调试后,其表现出以下运行特征现象:
(1)当皮带上的石块量较少时,皮带以较快的速度在运转(但不会超越输出频率上限的限定50Hz);
(2)当皮带上的石块量较多时(接近给定转矩),皮带运行在32Hz~38Hz;
(3)当皮带上的石块量很多时(超越给定转矩),皮带停止输送。
尽管此时电机停止运转,即相当于堵转表现的状态,但与通常的堵转有本质区别,在转矩控制方式下,此时电机不会在短时间内烧坏。
6速度反馈转矩控制方式
在开环转矩控制案例中,了解到转矩控制的一些特点,那么,如果应用场合在既需要保持控制转矩稳定输出的同时又需要根据速度反馈信号进行相应调节,此时,就要选择带速度反馈的转矩控制方式。
速度反馈转矩控制方式最适合应用在卷绕、抽丝等纺织行业。
在图2(a)中,如果没有张力架,收卷的张力需要依靠在变频器上进行设定,并且要根据收卷筒半径的变化作为反馈来适时自动调整电机输出转矩和角速度调整,来保持卷取切线力的恒定和线速度恒定,而将编码器信号作为速度反馈信号,来保持角速度的恒定。
在图2(d)中给出了控制结构。
按照图2(d)的构造,得到表6所示的参数:
表6速度反馈转矩控制方式的参数选择
以上介绍常规控制方式是变频器应用领域使用最为普遍的方式,约占整个变频器应用需求市场的70%以上,准确掌握这些基本控制方式的内涵与应用技巧,基本上可以胜任变频器的售前或售后技术服务支持工作。
但对于一些特殊应用需求的场合,还需要掌握一些专用变频器的应用技术和相关的控制概念以及生产工艺需求。
这些比较特殊的应用场合一般都需要借助于变频器厂家针对各个行业生产的“选件卡”或专用变频器。
当前,由于变频器行业的激烈竞争,各变频器生产厂家几乎都在努力寻找自己在相关行业上的专用功能产品的研发与定位。
下面,简要介绍几种在市场上使用比较广泛的特殊控制方式的概念,详细的应用方法还需要用户进一步参考相应的选件手册或说明书。
7其它特殊应用场合的控制方式
在这里之所以将以下的应用场合称为特殊应用场合,是因为变频器的这些衍生的控制方式是针对某个特定的行业应用开发的。
撇开行业的特殊性,这些具有特殊控制功能的变频器本身就是一个内在的、多变量输入与反馈的闭环控制系统,只不过这些变量可能不仅有电流参数,还可能有转矩参数、计算速度参数、计算功率以及甚至有时间参数和空间位置参数等。
7.1曳引拖动控制方式
传统的放卷筒的控制都是采用诸如力矩电机、刹车片、磁粉离合器等方式,LGIS5变频器的应用组参数APP-33(标准配置,无须选件)可以实现对诸如需要在正常运行过程中处于力矩控制方式下的发电运行状态。
当收卷电机仅以一个恒定的线速度运行时,若系统需要控制张力,可以通过参数APP-34来设定放卷张力的大小,由放卷电机来控制张力。
曳引拖动控制方式与前面介绍的开环力矩控制方式的区别在于:
(1)曳引拖动控制方式正常运行在发电状态,而开环力矩控制方式则运行在电动状态;
(2)曳引拖动控制方式在受到的外界牵引力小于设定值时,它将正向运转;反之,反向运转;而开环力矩控制方式要么正向运转,要么停止运转。
在一个收卷与放卷的应用中,如果将放卷使用曳引拖动控制方式,收卷使用速度闭环控制,通过收卷和放卷变频器的直流母线共享技术,不仅可以实现线速度恒定的恒张力控制目的,而且可以达到最大限度的节能效益。
系统成本低、安装调试容易。
7.2三角波控制方式与摆频控制方式
7.2.1LG公司的IS5系列变频器三角波控制方式介绍
由于纺织过程对纺锤绕线形状的特殊要求,LG公司的IS5系列变频器三角波控制功能可以满足这个需求,它的应用组参数APP-02~APP-07(标准配置,无须选件)是用来设置三角波控制方式的参数,如表7所示。
表7三角波控制方式的参数的设置
在图3(a)中给出了纺锤绕线工艺结构,在图3(b)中给出了三角波控制方式的参数APP-02~APP-07与变频器设定频率、实际输出运行频率之间的关系。
无论在