甲醛储气罐焊接课程设计 焊接.docx
《甲醛储气罐焊接课程设计 焊接.docx》由会员分享,可在线阅读,更多相关《甲醛储气罐焊接课程设计 焊接.docx(21页珍藏版)》请在冰豆网上搜索。
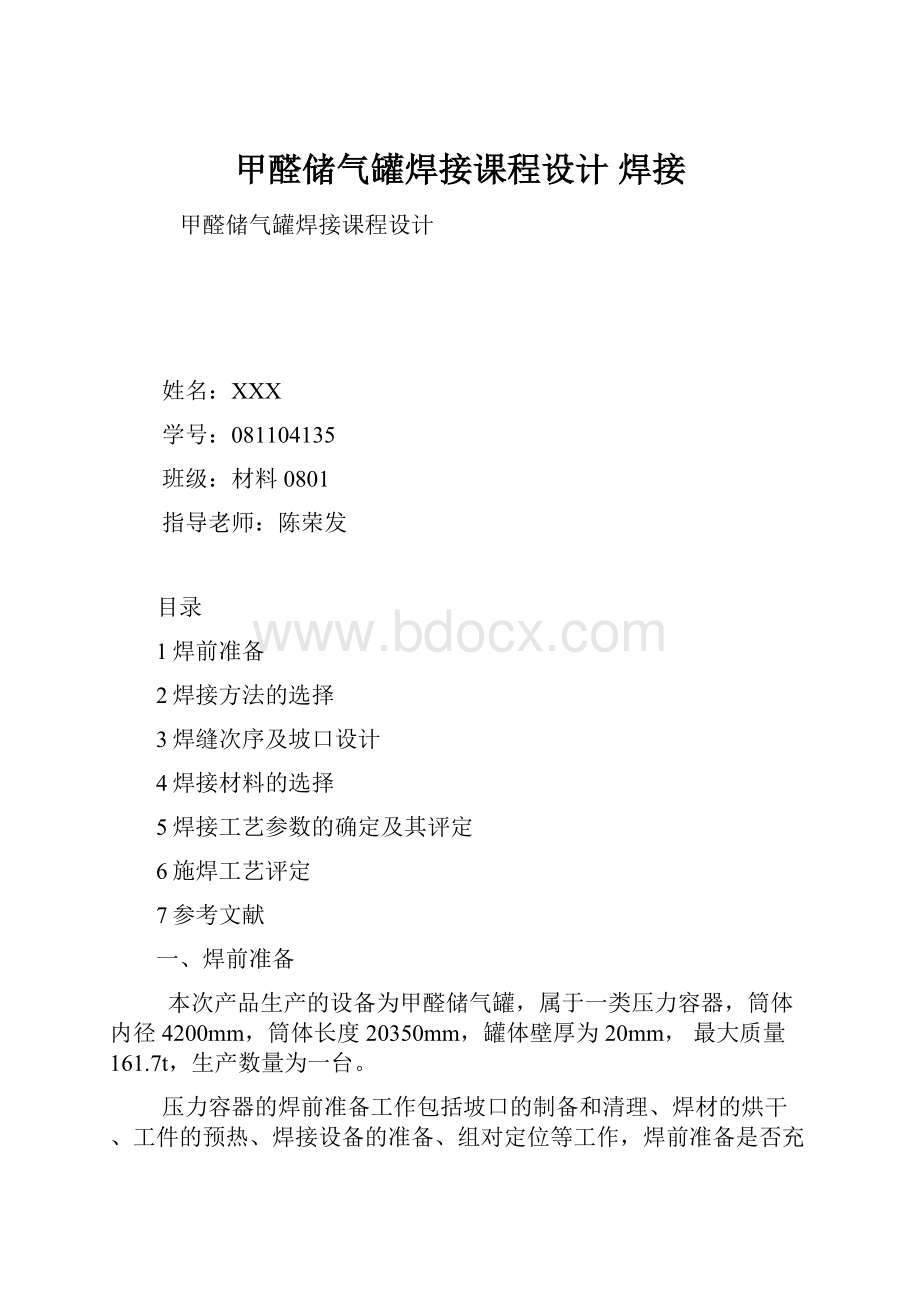
甲醛储气罐焊接课程设计焊接
甲醛储气罐焊接课程设计
姓名:
XXX
学号:
081104135
班级:
材料0801
指导老师:
陈荣发
目录
1焊前准备
2焊接方法的选择
3焊缝次序及坡口设计
4焊接材料的选择
5焊接工艺参数的确定及其评定
6施焊工艺评定
7参考文献
一、焊前准备
本次产品生产的设备为甲醛储气罐,属于一类压力容器,筒体内径4200mm,筒体长度20350mm,罐体壁厚为20mm,最大质量161.7t,生产数量为一台。
压力容器的焊前准备工作包括坡口的制备和清理、焊材的烘干、工件的预热、焊接设备的准备、组对定位等工作,焊前准备是否充分,直接影响到压力容器的焊接质量。
1、清理
焊前表面清理:
a、机械清理:
采用旋转钢丝刷、金刚砂毡轮抛光等,或者采用喷丸、喷砂处理。
b、化学清理:
包括去油、酸洗、钝化等。
化学清理是,零件不应有搭接缝或其他缝隙,以免因腐蚀液冲洗不干净而受腐蚀。
电解抛光可用于板厚<0.5mm的不锈钢件、质量稳定。
清理后的焊件存放时间不可太长。
化学清理腐蚀液成分及工艺见下表:
焊件
溶液成分及温度
中和溶液
热轧低合金钢、不锈钢、耐热钢及高温合金钢
(酸洗用)
先在60-70°C质量分数为10%的Na2CO3 溶液中,后在冷水中冲净
硫酸 H2SO4
盐酸 HCl
硝酸 HNO3
温度 50-60°C
2、预温
焊前预热的有利作用还在于:
①改变了焊接过程的热循环,降低焊接接头各区高温转变和低温转变温度区间的冷却速度,避免或减少了淬硬组织的形成;②减少焊接区的温度梯度,降低了焊接接头的内应力,并使之较均匀分布;③扩大了焊接区的温度场,使焊接接头在较宽的区域内处于塑性状态,减少了焊接应力的不利影响;④延长了焊接区在100℃以上温度的停留时间,有利于氢从焊缝金属中逸出。
根据母材的化学成分、焊接性能、厚度、焊接接头的拘束程度、焊接方法和焊接环境等综合考虑是否预热,必要时通过试验确定。
常用钢号推荐的预热温度见表1。
不同钢号相焊时,预热温度按预热温度要求较高的钢号选取。
采取局部预热时,应防止局部应力过大。
预热的范围为焊缝两侧各不小于焊件厚度的3倍,且不小于100mm。
需要预热的焊件在整个焊接过程中应不低于预热温度。
当用热加工法下料、开坡口、清根、开槽或施焊临时焊缝时,亦需考虑预热要求。
常用钢号推荐的预热温度
钢号
厚度,mm
预热温度,℃
20R
20~50
≥100
>50
≥150
根据上表,本设计规定的材料为20R,压力容器厚度约为20mm,因此,选择预热温度为120℃。
二、焊接方法的选择
在压力容器制造中,生产中常用的焊接方法有二氧化碳气体保护焊、埋弧焊、乌极氩弧焊等。
拟采用的焊接方法主要根据被焊钢种、接头厚度、焊缝位置和坡口形式以及对接头的质量要求等来选择,同时还应考虑到该种焊接方法的效率和生产成本。
1、二氧化碳气体保护焊
氧化碳气体保护焊的各种参数
a、焊丝直径
焊丝的直径通常是根据焊件的厚薄、施焊的位置和效率等要求选择。
焊接薄板或中厚板的全位置焊缝时,多采用1.6mm以下的焊丝(称为细丝CO2气保焊)。
焊丝直径的选择参照下表:
焊丝直径(mm)
熔滴过渡形式
可焊板厚(mm)
施焊位置
0.5~0.8
短路过渡
0.4~3
各种位置
细颗粒过渡
2~4
平焊、横角
1.0~1.2
短路过渡
2~8
各种位置
细颗粒过渡
2~12
平焊、横角
1.6
短路过渡
2~12
平焊、横角
细颗粒过渡
〉8
平焊、横角
2.0~2.5
细颗粒过渡
〉10
平焊、横角
b、焊接电流焊接电流的大小主要取决于送丝速度。
送丝的速度越快,则焊接的电流就越大。
焊接电流对焊缝的熔深的影响最大。
当焊接电流为60~250A,即以短路过渡形式焊接时,焊缝熔深一般为1mm~2mm;只有在300A以上时,熔深才明显的增大。
c、电弧电压短路过渡时,则电弧电压可用下式计算:
U=0.04I+16±2(V) 此时,焊接电流一般在200A以下,焊接电流和电弧电压的最佳配合值见表2。
当电流在200A以上时,则电弧电压的计算公式如下:
U=0.04I+20±2(V)
d、焊接速度
半自动焊接时,熟练的焊工的焊接速度为18m/h~36m/h;自动焊时,焊接速度可高达150m/h。
e、焊丝的伸出长度
一般的焊丝的伸出长度约为焊丝的直径的10倍左右,并随焊接电流的增加而增加。
f、气体的流量正常的焊接时,200A已下薄板焊接,CO2的流量为10L/min~25L/min.200A以上厚板焊接,CO2的流量为15L/min~25L/min.粗丝大规范自动焊为25L/min~50L/min。
2、埋弧焊
埋弧焊的工艺参数
埋弧焊的焊接参数主要有:
焊接电流、电弧电压、焊接速度、焊丝直径和伸出长度等。
a、焊接电流
当其他参数不变时,焊接电流对焊缝形状和尺寸的影响如图所示。
电流对焊缝的影响,一般焊接条件下,焊缝熔深与焊接电流成正比。
随着焊接电流的增加,熔深和焊缝余高都有显著增加,而焊缝的宽度变化不大。
同时,焊丝的熔化量也相应增加,这就使焊缝的余高增加。
随着焊接电流的减小,熔深和余高都减小。
b、电弧电压
电弧电压的增加,焊接宽度明显增加,而熔深和焊缝余高则有所下降。
但是电弧电压太大时,不仅使熔深变小,产生未焊透,而且会导致焊缝成形差、脱渣困难,甚至产生咬边等缺陷。
所以在增加电弧电压的同时,还应适当增加焊接电流。
c、焊接速度
当其他焊接参数不变而焊接速度增加时,焊接热输入量相应减小,从而使焊缝的熔深也减小。
焊接速度太大会造成未焊透等缺陷。
为保证焊接质量必须保证一定的焊接热输入量,即为了提高生产率而提高焊接速度的同时,应相应提高焊接电流和电弧电压。
d、焊丝直径与伸出长度
当其他焊接参数不变而焊丝直径增加时,弧柱直径随之增加,即电流密度减小,会造成焊缝宽度增加,熔深减小。
反之,则熔深增加及焊缝宽度减小。
当其他焊接参数不变而焊丝长度增加时,电阻也随之增大,伸出部分焊丝所受到的预热作用增加,焊丝熔化速度加快,结果使熔深变浅,焊缝余高增加,因此须控制焊丝伸出长度,不宜过长。
e、焊丝倾角
焊丝的倾斜方向分为前倾和后倾。
倾角的方向和大小不同,电弧对熔池的力和热作用也不同,从而影响焊缝成形。
当焊丝后倾一定角度时,由于电弧指向焊接方向,使熔池前面的焊件受到了预热作用,电弧对熔池的液态金属排出作用减弱,而导致焊缝宽而熔深变浅。
反之,焊缝宽度较小而熔深较大,但易使焊缝边缘产生未熔合和咬边,并且使焊缝成形变差。
3、乌极氩弧焊
钨极氩弧焊工艺参数
a、焊接电流种类及大小,一般根据工件材料选择电流种类,焊接电流大小是决定焊缝熔深的最主要参数,它主要根据工件材料、厚度、接头形式、焊接位置,有时还考虑焊工技术水平(钨极氩弧时)等因素选择。
b、钨极直径及端部形状,钨极直径根据焊接电流大小、电流种类选择。
钨极端部形状是一个重要工艺参数。
根据所用焊接电流种类,选用不同的端部形状。
尖端角度α的大小会影响钨极的许用电流、引弧及稳弧性能。
表1列出了钨极不同尖端尺寸推荐的电流范围。
小电流焊接时,选用小直径钨极和小的锥角,可使电弧容易引燃和稳定;在大电流焊接时,增大锥角可避免尖端过热熔化,减少损耗,并防止电弧往上扩展而影响阴极斑点的稳定性。
钨极尖端角度对焊缝熔深和熔宽也有一定影响。
减小锥角,焊缝熔深减小,熔宽增大,反之则熔深增大,熔宽减小。
c、气体流量和喷嘴直径
在一定条件下,气体流量和喷嘴直径有一个最佳范围,此时,气体保护效果最佳,有效保护区最大。
如气体流量过低,气流挺度差,排除周围空气的能力弱,保护效果不佳:
流量太大,容易变成紊流,使空气卷入,也会降低保护效果。
同样,在流量子定时,喷嘴直径过小,保护范围小,且因气流速度过高而形成紊流;喷嘴过大,不仅妨碍焊工观察,而且气流流速过低,挺度小,保护效果也不好。
所以,气体流量和喷嘴直径要有一定配合。
d、焊接速度焊接速度的选择主要根据工件厚度决定并和焊接电流、预热温度等配合以保证获得所需的熔深和熔宽。
在高速自动焊时。
还要考虑焊接速度对气体、保护效果的影响。
焊接速度过大,保护气流严重偏后,可能使钨极端部、弧柱、熔池暴露在空气中。
因此必须采用相应措施如加大保护气体流量或将焊炬前倾一定角度,以保持良好的保护作用。
e、喷嘴与工件的距离距离越大,气体保护效果越差,但距离太近会影响焊工视线,且容易使钨极与熔池接触而短路,产生夹钨,一般喷嘴端部与工件的距离在8~14mm之间。
综上,基层用埋弧自动焊,过渡层用二氧化碳气体保护焊,复层用乌极氩弧焊。
3、焊缝次序及坡口设计
1、焊接次序如图所示:
2、坡口设计:
合理的坡口应满足如下条件:
⑴焊接坡口形式的设计应避免采用焊不透或局部焊透的坡口,还要尽量减少焊缝的横截面积,以降低接头的残余应力,同时也可以减少焊接材料的消耗量。
⑵坡口加工采用热切割时应注意防止母材边缘会形成一定深度的淬硬层,这种低塑性的淬硬层往往成为冷加工的开裂源。
⑶适应所采取的焊接方法及其工艺规范,使焊接接头的内在质量和力学性能满足无损探伤和其他技术标准。
⑷残余变形和残余应力最小
⑸有利于焊工操作和保护,焊接接头的合格率高,耗资少,经济效益高。
为了达到此要求,在设计或选定坡口形式及其几何尺寸时,必须同时考虑所采用的焊接方法及其工艺规范参数能够达到的熔深和可焊到性。
根据熔深确定钝边尺寸;为了达到良好的可焊到性,应综合考虑坡口角度,根部圆角R值和间隙大小。
为保证接头部位熔合良好,焊接前应对焊接部位开坡口。
尽量选择Y形和V形坡口。
为对口错边量、热处理、无损检测、焊缝尺寸等方面有针对性地提出不同的要求,GB150根据位置,根据该接头所连接两元件的结构类型以及应力水平,把接头分成A、B、C、D四类,如图。
A类:
圆筒部分的纵向接头(多层包扎容器层板层纵向接头除外)、球形封头与圆筒连接的环向接头、各类凸形封头中的所有拼焊接头以及嵌入式接管与壳体对接连接的接头。
B类:
壳体部分的环向接头、锥形封头小端与接管连接的接头、长颈法兰与接管连接的接头。
但已规定为A、C、D类的焊接接头除外。
C类:
平盖、管板与圆筒非对接连接的接头,法兰与壳体、接管连接的接头,内封头与圆筒的搭接接头以及多层包扎容器层板层纵向接头。
D类:
接管、人孔、凸缘、补强圈等与壳体连接的接头。
但已规定为A、B类的焊接接头除外。
注意:
焊接接头分类的原则仅根据焊接接头在容器所处的位置而不是按焊接接头的结构形式分类,所以,在设计焊接接头形式时,应由容器的重要性、设计条件以及施焊条件等确定焊接结构。
这样,同一类别的焊接接头在不同的容器条件下,就可能有不同的焊接接头形式。
焊接时应选择合适的焊缝坡口,方便焊材(焊条或焊丝)伸入坡口根部,以保证全熔透。
坡口选择因素:
①尽量减少填充金属量;②保证熔透,避免产生各种焊接缺陷;③便于施焊,改善劳动条件;④减少焊接变形和残余变形量,对较厚元件焊接应尽量选用沿厚度对称的坡口形式,如X形坡口等。
1.筒体、封头及其相互间连接的焊接结构纵、环焊缝必须采用对接接头。
对接接头的坡口形式可分为不开坡口(又称齐边坡口)、V形坡口、X形坡口、单U形坡口和双U形坡口等数种,应根据筒体或封头厚度、压力高低、介质特性及操作工况选择合适的坡口形式。
2.接管与壳体及补强圈间的焊接结构一般只能采用角接焊和搭接焊,具体的焊接结构还与容器的强度和安全性要求有关。
有多种接头形式,涉及是否开坡口、单面焊与双面焊、熔透与不熔透等问题。
设计时,应根据压力高低、介质特性、是否低温、是否需要考虑交变载荷与疲劳问题等来选择合理的焊接结构。
不带补强圈的插入式接管焊接结构
中低压容器不需另作补强的小直径接管用得最多的焊接结构,接管与壳体间隙应小于3mm,否则易产生裂纹或其它焊接缺陷。
(a)图:
单面焊接结构,适用于内径小于600mm、盛装无腐蚀性介质的接管与壳体之间的焊接,接管厚度应小6mm;(b)图:
最常用的插入式接管焊接结构之一,为全熔透结构。
适用于具备从内部清根及施焊条件、壳体厚度在4~25mm、接管厚度大于等于0.5倍壳体厚度的情况;(c)图:
在(b)的基础上,将接管内径边角处倒圆,可用于疲劳、低温及有较大温度梯度的操作工况。
带补强圈的接管焊接结构
要求:
尽量与补强处的壳体贴合紧密,焊接结构力求完善合理。
但只能采用塔接和角接,难于保证全熔透,也无法进行无损检测,因而焊接质量不易保证。
坡口:
大间隙小角度,利于焊条伸入到底,减少焊接工作量。
图(a):
一般要求的容器,即非低温、无交变载荷的容器图(b):
承受低温、疲劳及温度梯度较大工况的容器,保证接管根部及补强圈内侧焊缝熔透。
四、焊接材料的选择
焊接材料,选用与母材成分基本相同的同类焊材。
焊材的合金(尤其是Cr、Mo)含量必须与母材相同,一保证焊接接头与母材有相同的高温强度、高温蠕变性能与抗氧化性能。
同时也要控制合金成分,改善钢的焊接性。
如Nb、V都是强碳化物形成元素,对改善钢的转变特性、细化晶粒、提高焊缝金属的韧性和抗冷裂纹性能具有重要作用,但是当Nb、V含量过高时,也会提高中合金耐热钢焊缝金属的热裂纹和再热裂纹倾向。
首先要考虑焊材质量。
生产厂家和焊条、焊剂的高清洁度,可以避免污染和回火脆性。
为提高焊接金属的再结晶温度并降低回火脆性的灵敏度,焊材的生产厂家在生产中往往要加入一些微量合金元素,但不同元素需要控制在一定范围内以获得优良的硬度和蠕变特性。
这些元素的影响如下:
控制硅元素含量以降低冲击硬度,硅含量最好控制在0.19%~0.26%之间。
如果锰和镍含量高,则AC1温度降低得到奥氏体的可能性升高。
锰含量一般在0.5%~0.8%之间。
镍元素可以提高蠕变性能,其最好的控制范围在0.04%~0.05%。
Ni含量0.04%为最佳。
铬含量在8%~10%之间,其范围变化没有什么太大影响。
另外,选择焊接材料时必须考虑两方面的问题:
一是不能有裂纹等焊接缺陷产生;二是能满足使用性能要求。
选择焊接材料的依据是保证焊缝金属的强度、塑性和韧性等力学性能与母材匹配。
5、焊接工艺参数的确定
在制定埋弧焊工艺时,首先要保证的是焊接接头的质量完全符合焊接技术要求或标准规定;其次是最大限度的降低生产成本,即以最高的焊接速度,最低的电能与焊材消耗以及最少的焊接工时完成整个焊接过程,以求获得最好的经济效益。
当其它工艺条件确定后,焊接工艺参数的合理选择将直接影响到焊接生产效率、焊接质量、焊产成本。
通常,我们将埋弧焊焊接工艺参数分为焊接参数(主要参数)和焊接因数(次要参数)。
焊接参数是指那些直接影响焊接质量和生产效率的参数,它们是焊接电流大小、电流种类与极性、焊件预热及预热温度、电弧电压、焊接速度、焊丝和焊剂的成分与配合等。
焊接因数是指对焊接质量和生产效率影响有限或无多大影响的参数,它们是焊丝直径与焊丝伸出长度、焊丝倾角、焊丝与焊件的相对位置、焊剂粒度、焊剂堆撒高度和多丝焊的焊丝间距等。
1、焊接电流大小及电流种类与极性
接电流过大,易使焊件产生咬边、焊穿,增加焊件变形和金属飞溅量,还会使焊接接头的组织由于过热而发生变化,导致力学性能下降。
焊接电流过小,又会使电弧不稳,造成焊件未焊透、夹渣及焊缝成形不良等缺陷。
当其他参数不变时,一般焊接条件下,焊缝熔深与焊接电流大小成正比,而焊缝的宽度受电流变化的影响不大。
随着焊接电流的增加,电能和焊剂消耗增加,焊丝的熔化量也相应增加,会使焊缝的余高显著增加。
随着焊接电流的减小,熔深和余高都减小。
采用直流正接时,熔敷速度比反接高,但熔深较浅(埋弧焊时阴极温度>阳极温度),降低了熔敷金属中母材的百分比。
特别适合于堆焊,当母材的热裂纹倾向较大时,为了防止热裂,也可采用直流正接。
采用直流反接时,熔敷速度比正接低30%一50%,熔深较大。
因此,埋弧焊时一般情况下都采用直流反接。
2、电弧电压
电弧电压主要由电弧长度来决定:
电弧长度越长,电弧电压越高,电弧保护效果降低,易产生电弧偏吹等。
在焊接过程中,应尽量使用短弧焊接。
埋弧焊采用自动送丝(等速或变速),其电弧电压在调整好后其变化量一般能自动稳定在一个较小的动态范围内。
电弧电压影响焊缝成形,电弧电压增加,焊接宽度明显增加,电弧电压对熔深的影响很小,随着电弧电压的增大,熔宽增大,而熔深及余高略有减小。
电弧电压还会改变熔敷金属的化学成分。
当电弧电压增加时,焊剂的熔化量增加,熔渣和液态金属重量间的比值增大,过渡到熔敷金属中的合金元素会有所增加。
电弧电压太大时,不仅使电能消耗增大,使熔深变小,产生未焊透,而且会导致焊缝成形差甚至产生咬边等缺陷,同时焊剂消耗量也会显著增加,而且脱渣困难。
为保证电弧的稳定燃烧及合适的焊缝成形系数,电弧电压应与焊接电流保持适当的匹配关系,在增加电弧电压的同时,还要适当增加焊接电流与之相匹配,这样会进一步增加电能和焊剂的消耗量,所以采用较高的电弧电压相对经济性较差。
3、焊接速度及焊接热输入量
焊接速度对熔深及熔宽及埋弧焊的经济性均有明显的影响。
当其它焊接参数不变而焊接速度增加时,焊接效率提高(电能、焊材消耗等都会相应降低),单位焊缝长度上由电弧提供的焊接热能输入量(线能量输入)相应减小,从而使焊缝的熔深、熔
宽均减小。
焊接速度过快,熔化温度不够,会造成未焊透、未熔合、焊缝成形不良等缺陷。
为保证焊接质量必须保证一定的焊接线能量输入,即为了提高生产率而提高焊接速度的同时,应相应提高焊接电流和电弧电压。
若焊接速度太慢,高温停留时间增长,热影响区宽度增加,不仅使焊接接头的晶粒变粗,力学性能降低,焊件变形量会增大,而且会使电能及焊剂的消耗量显著增加。
当焊接较薄焊件时,还易形成烧穿。
4、焊丝直径与焊丝伸出长度
当其他焊接参数不变而焊丝直径增加时,弧柱直径随之增加,即电流密度减小,会造成焊缝宽度增加,熔深减小。
反之,则熔深增加及焊缝宽度减小。
为获得良好的焊缝成型,当焊丝直径增大时,焊接电流必须随之增大。
电能消耗、焊剂消耗量
也会随之增加。
当其他焊接参数不变而焊丝伸出长度增加时,伸出部分焊丝电阻也随之增大,其所受到的预热作用增加,焊丝熔化速度加快,结果使熔深变浅,焊缝余高增加,电能消耗、焊剂消耗量会增加,经济性会变差,因此须控制焊丝伸出长度,不宜过长。
综上,焊机选择为MZ-1000,DCRP(直流反极性接)
焊接工艺参数
板厚/mm
坡口
形式
焊丝直径/mm
焊接电流/A
焊接电压/V
焊丝
焊接速度
m/h
电流极性
第一层
其余层
20
V型
4.0
620
750
36
H08MnA
35
直流反接
6、施焊工艺评定
1、焊后处理
a、后热
对冷裂纹敏感性较大的低合金钢和拘束度较大的焊件应采取后热措施。
后热应在焊后立即进行。
后热温度一般为200~350℃,保温时间与焊缝厚度无关,一般不低于0.5h。
④若焊后立即进行热处理则可不做后热。
b、焊后热处理
根据母材的化学成分、焊接性能、厚度、焊接接头的拘束程度、容器使用条件和有关标准综合确定是否需要进行焊后热处理。
压力容器或受压元件焊后热处理厚度δPWHT按如下规定选取。
等厚度全焊透对接接头的焊后热处理厚度δPWHT为其焊缝厚度,也即容器或其受压元件钢材厚度δ。
焊缝厚度是指焊缝横截面中,从焊缝正面到焊缝背面的距离(余离不计)。
表3常用钢号焊后热处理规范
钢号
焊后热处理温度,℃
最短保温时间
电弧焊
电渣焊
10
Q235-A,20
Q235-B,20R
Q235-C,20G
20g
600~640
—
当焊后热处理厚度50mm时,(PWHT/25)h,但最短时间不低于1/4h
当焊后热处理厚度PWHT>50mm时,为
09MnD
580~620
—
16MnR
600~640
900~930正火后
600~640回火
16Mn,16MnD,16MnDR
—
15MnVR,15MnNbR
540~580
—
20MnMo,20MnMoD
580~620
—
18MnMoNbR
13MnNiMoNbR
600~640
950~980正火后
600~640回火
根据表3,工件焊后热处理方式选用640℃保温50min。
2、焊后探伤
低碳钢的焊后无损检测一般有两种作法,一种是在基层、过渡层、复层都焊完后一起拍片;另一种是当设计厚度裕度较大,基层焊接后能够保证基层焊缝处的厚度不小于设计厚度,射线检测可在过渡层焊接之前进行,但焊缝全部焊完后。
必须再次进行射线检测,检查无裂纹即可。
因为产品用不锈钢复合钢厚度不厚,即使有缺陷也比较容易定位、清除,我们选择基层、过渡层和复层都焊完后一起拍片,这样可以降低成本。
一般缺陷清除。
返修焊接从基层侧进行。
基层焊接工作完毕后,应先进行外观检查(焊缝不得存在裂纹、气孔和夹渣等缺陷),然后进行X射线探伤。
无损探伤合格后,应将基层焊缝表面打磨平整,使其表面略低于基层金属表面。
过渡层焊接完毕后,应采用超声波或渗透法进行无损检验。
3、焊后接头强度
a、产品焊接试板试样的制备
试板尺寸和试样毛坯的截取试板焊缝应进行外观检查和无损检测(按JB4730),然后在合格部位截取试样试板的长度和宽度以满足试验所需的试样类别和数量的截取为宜。
试样的截取如图1(对接接头试板)和图2(堆焊试板)所示。
图2堆焊试板
试板两端舍弃部分长度随焊接方法和板厚而异,一般手工焊不小于30mm;自动焊和电渣焊不小于40mm。
如有引弧板和引出板时,也可以少舍弃或不舍弃。
试样毛坯的截取一般采用机械切割法,也可用激光或线切割的方法,但应去除热影响区。
必要时,也可直接从焊件上截取试样。
根据不同项目的试验要求,对试样进行加工,经检验合格后,打上钢印或其它永久性的标志。
b、拉伸试验
拉伸试验的试样尺寸如图3所示。
试样宽度b≥25mm。
图3拉伸试样
试样的分割:
当因试验机能力限制而不能进行全板厚的拉伸试验时,则沿试板厚度方向,分割成近似相等的若干等分,以此作为试样厚度,该试样厚度应较接近于试验机所能试验的最大厚度。
因切口损耗造成的厚度减薄应属正常,即分割后若干试样叠加的厚度可以小于原试板的全板厚。
试样的加工:
拉伸试样表面焊缝的余高应采用机械方法去除,使之与母材齐平。
对具有复合层的材料,当复层计人设计厚度时,拉伸试样包括基层及复层;当复层不计人设计厚度时,拉伸试样可去除复层后制取。
采用多种方法施焊时,试样的受拉面应包括每一种焊接方法(或焊接工艺)的焊缝金属。
试验方法:
拉伸试验按GB/r228的有关规定进行,在确认已读出拉伸试样的最大载荷后,允许不拉断试样,以避免噪声和对机器的损伤。
合格指标:
拉伸试样的抗拉强度应大于或等于下列规定之一:
产品图样的规定值;
钢材标准抗拉强度下限值;
对不同强度等级的钢材组成的焊接接头,则为两种钢材标准抗拉强度下限值中的较小者;
若采用分割后的多片试样,则将该多片试样组成一组,并对每片进行试验。
同时,焊接试板全厚度焊接接头的拉伸试验结果为该组试样的平均值,其平