诊断处理印刷品.docx
《诊断处理印刷品.docx》由会员分享,可在线阅读,更多相关《诊断处理印刷品.docx(19页珍藏版)》请在冰豆网上搜索。
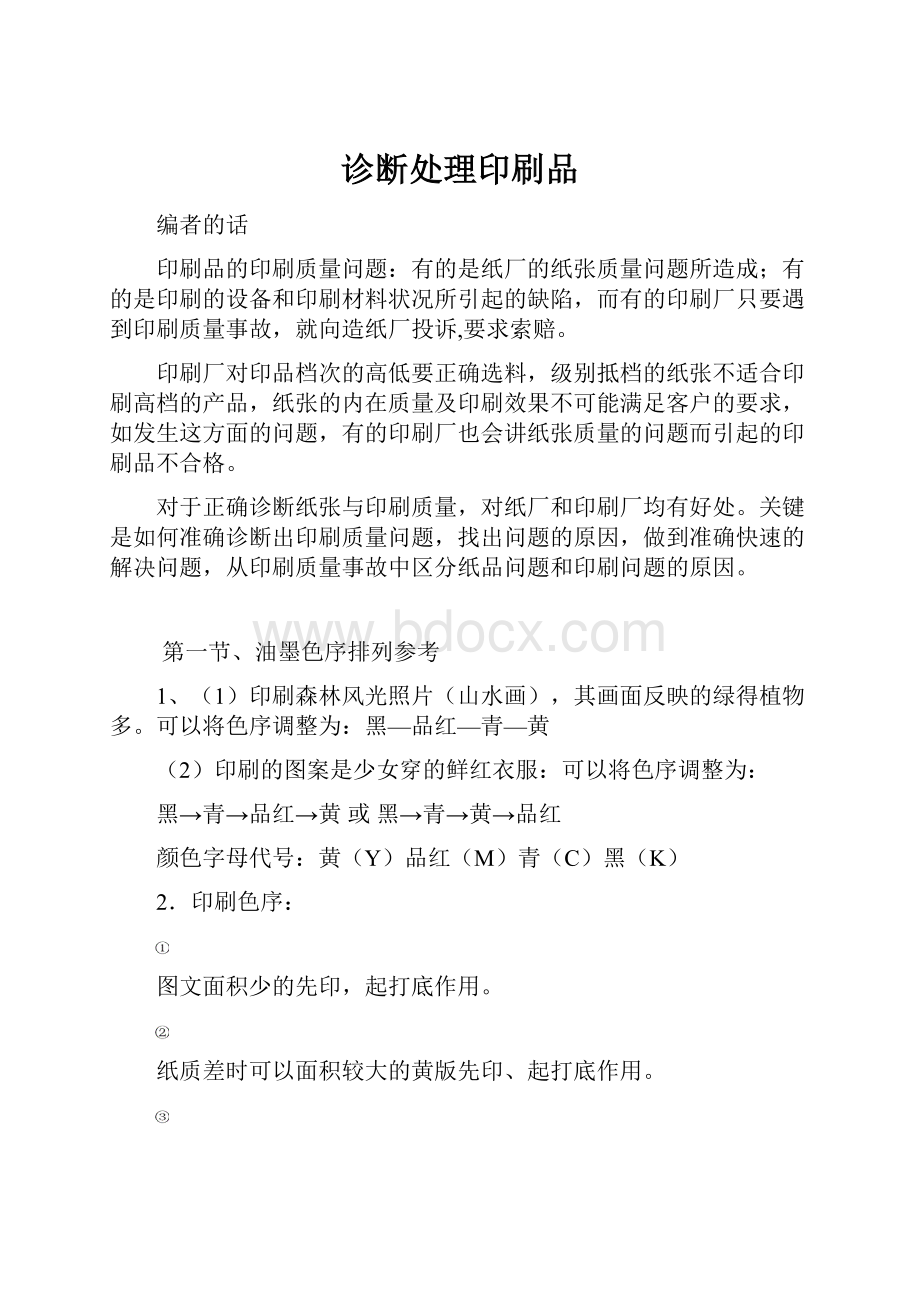
诊断处理印刷品
编者的话
印刷品的印刷质量问题:
有的是纸厂的纸张质量问题所造成;有的是印刷的设备和印刷材料状况所引起的缺陷,而有的印刷厂只要遇到印刷质量事故,就向造纸厂投诉,要求索赔。
印刷厂对印品档次的高低要正确选料,级别抵档的纸张不适合印刷高档的产品,纸张的内在质量及印刷效果不可能满足客户的要求,如发生这方面的问题,有的印刷厂也会讲纸张质量的问题而引起的印刷品不合格。
对于正确诊断纸张与印刷质量,对纸厂和印刷厂均有好处。
关键是如何准确诊断出印刷质量问题,找出问题的原因,做到准确快速的解决问题,从印刷质量事故中区分纸品问题和印刷问题的原因。
第一节、油墨色序排列参考
1、
(1)印刷森林风光照片(山水画),其画面反映的绿得植物多。
可以将色序调整为:
黑—品红—青—黄
(2)印刷的图案是少女穿的鲜红衣服:
可以将色序调整为:
黑→青→品红→黄或黑→青→黄→品红
颜色字母代号:
黄(Y)品红(M)青(C)黑(K)
2.印刷色序:
图文面积少的先印,起打底作用。
纸质差时可以面积较大的黄版先印、起打底作用。
油墨透明度差、遮盖力大的油墨先印{反之}油墨透明度低的先印、高的后印、油墨干燥慢的先印、快的后印。
一般地平网文先印、实地后印
单、双色机上面,采用亮色先印;暗色后印。
第二节、各类印刷机的印刷色序
1.单色机印刷:
黄、品红、青、黑。
2.四色机印刷:
黑、青、品红、黄(或)黑、品红、青、黄从逆叠印的角度分析:
青、品红、黄、黑的印刷色序较好。
3.双色机印刷:
黑、黄、品红、青(或)黑、黄、青、品红
品红(青)、黄、黑、青(品红)或青(品红)、黑
品红、青(或)青、品红、黑、黄
总之,墨量大的放在第二组。
第三节、实地版印不实的解决放法
在实地印刷中遇到实地版印不平实,借调整压力是无法解决问题的,应该调整印刷工艺的方法来解决根本问题。
在生产中常常遇到
%→
%的品红版与
%的青版、叠印的蓝色实地,常出现红网发花现象需要通过工艺的调整。
印刷常规色序是:
黑、青、品红、黄;品红网需要叠在刚印好的青色实地上,为防止反剥,于是降低了品红墨的粘性;加大了青墨的粘性。
问题仍没有得到解决。
由于四色机是湿湿叠印,在湿的实地上叠印另一色墨时,转印效果差,油墨转移率低、可将品红和青的色序调换。
先印品红网,这样品红网可100%向低张转印。
而青板实地有一半以上的面积也可以直接转印在纸张上。
这样的印刷非常平服,即使换用质量差一点的纸张也能印实。
其次:
如果版面上有大面积青版实地,发花现象严重。
即使加大印刷压力也无效。
因为由于青色在第二组纸张亲墨性差、与油墨结合不牢固,印上的青墨含在后两组橡皮布上反驳下来一部分。
这时可将机器其余几色离压,只印青色。
印出的实地应该是平服的。
这时就应该调整色序,将青版放在第一组,印刷发花的故障即可排除。
印刷色序对油墨转移影响很大,特别是多色印刷湿湿叠印。
应根据不同的活件,灵活调整印刷色序是非常必要的。
第四节、印金掉色的解决方法
印刷一种大面的实地金墨,印完后产品表面金色耐磨力差,一擦就掉色,出现轻微的粉化状太。
根据出现的掉色的问题:
1、纸张的纸质紧密,表面平滑度高,纸张表面细小空对金墨的吸墨性,吸附性,渗透性造成的掉色现象。
2、金墨是调金油和金属铜粉调和而成的,铜粉的比重大、颗粒粗、粘度低。
印刷到纸面后,金墨中的连接料首先渗透在纸张的毛细孔中,将纸张毛细孔填满,使金粉颗粒渗透不到纸张的毛细孔中,造成金墨中的金粉颗粒在纸面聚合固着性差,出现粉化状态而掉色。
解决办法:
1、在原金墨的基础上加放8%的调金油,0.7%的干燥油,4%的酚醛清漆,增加金墨中的粘度,加快墨层在纸张表面的氧化结膜干燥,和聚合固着有一定的效果。
2、在原金墨中的基础上加放0.8%的干燥油,20%—25%的亮光桨。
不仅色相基本不变,而且还增加了墨层光面的光泽度。
加放这两种原料能减少金墨中连接料在纸张表面毛细空的快速渗透,增加了金墨中的粘度、光泽度和油墨的聚合固着作用;使金墨颗粒在纸张毛细孔中有较多的渗透,墨层表面氧化膜干燥加快。
第五节、印刷纸张打皱的原因及对策
印刷纸张打皱原因有:
1、机器调整不当
2、纸张不平整(因水量不均)在实际工作中可按下述原则判断是机器原因还是纸张原因:
同一台机器印这一种纸打皱,印另一种纸则不打皱,多数是纸张方面的原因。
把切好纸张前后左右调换上机。
如果是在机器的某一位置打皱则说明是机器调整不当;如果固定于纸的部位打皱则说明是纸张方面的原因。
相同的两台(或几台)机器印同一种纸,有的机器打皱,有的机器不打皱,则说明打皱的机器调整不当。
一、印刷方面的原因:
1、印刷机输纸装置调整不当,飞达在分纸时两送纸吸嘴不同步,两侧的压纸舌压力不等,容易造成输纸歪斜,是打皱的原因之一。
2、输纸带松紧不一,压纸轮的压力不等,扁毛刷轮太重,方向不妥,易形成纸张歪斜,中间鼓起来。
这也是会造成打皱的原因。
3、压印滚筒叼纸牙力不均,牙排的牙垫不在同一平面,中间叼牙、牙垫太光滑;印刷滚筒表面高低不平,也是纸张打皱的常见原因。
二、纸张方面的原因:
1、纸张含水量不均匀造成纸张不平整(翘曲)。
2、纸张随着环境的温度、湿度的高低,水分会有增减,因而产生“荷叶边”和“紧边”现象。
为了防止和消除纸张变形,一般应采取下列措施:
尽量采用横丝缕纸上机印刷。
遇到纸张失去水分出现“紧边”时可在纸堆和机台周围洒些水或利用湿器喷雾加湿,均有好的效果。
产生“荷叶边”时可采取烘干的办法处理,但要掌握烘干时间,千万不要烘干过头再产生“紧边”的问题。
对变形较大的纸张可把橡皮滚筒内的垫纸撤一部分。
具体方法是把橡皮和垫纸从机器上卸下,平放在桌子上面把印迹以外部分的垫纸用剪刀切除,然后装好橡皮。
这样橡皮滚筒印迹以外部分的直径就小一些,纸张从橡皮滚筒与印滚筒之间挤压穿过时,印迹以外部分挤压很小,平直度差的纸也能过去,可避免减轻打皱。
第六节、初步了解部分印刷基础知识
一、在生产中润湿液的作用是什么?
1、使空白部分不起脏和油腻(不感脂)。
2、通过亲水胶体和有机酸使空白部分保持良好的亲水性能。
3、通过表面活性物质和表面活性剂,使版面空白部分得到保护,有利于水墨平衡。
4、通过缓冲液(同离子效应)使润湿液PH值稳定。
二、生产润湿液中的PH值应控制在什么范围?
对PS版润湿液中PH值一般控制在5-6之间为宜。
三、润湿液中的PH值控制不当对产品质量有何影响?
酸性过强,容易造成印版发花,网点变小降低印版耐印力,油墨容易乳化,造成印迹不容易干,产品背面粘脏等质量弊病。
四、印刷时版面水分大小与产品质量有什么影响?
印刷操作中版面水分控制不当,造成水分偏大容易出现产品墨色过淡,墨色无光泽,颜色色彩不鲜艳,版子容易花,油墨容易乳化;同时会造成纸张伸缩,变形;造成套印不准质量弊病。
而水分偏小容易使版面起脏或起腻及网点出现并连和糊掉等质量弊病。
五、日常生产总要求的“水墨平衡”是什么含义?
水墨平衡是指在一定条件下调节润湿液的供剂量,使油墨的乳化量控制在最小的范围内,用最少量的水和印版图像应有的油墨量相抗衡。
六、什么是理想压力?
使用最小值量的力而获得原稿相符和要求的网点大小的压力,为理想压力。
七、怎样理解理想压力?
理想压力是指被人们认可的将墨量正确转移到承印物上时所使用最小量的力,实际上是在印刷品图像不同的条件下,承印物得到足够结实的基础,均匀使用最小压力。
理想压力是固定不变的而要根据产品的不同要求适当调整。
八、印刷压力使用不当产品质量会出现什么弊病?
压力偏小,印刷效果差,画面网点空虚,无精神,实地和文字化淡,残缺不全,压力偏大,画面层次不清,清晰度差,文字没有笔峰。
第七节、套印不准
造成套印不准的原因很多,常见的有纸张伸缩,输纸歪斜,规矩定位不惟,叼牙咬力不够,叼牙轴磨损,交接不符合要求,递纸牙传动部件磨损等。
另外一些特殊因素也会造成套印不准,比如橡皮布局部变形大,也能使图像局部套印不准,递纸牙轴,牙印滚筒轴轴向窜动,会造成横向套印不准等。
总体概括由三个方面的因素造成的:
1.制版不良造成的原版不准。
2.胶印机出故障或操作调节不当造成的套印不准。
3.纸张伸缩造成的套印不准。
一、纵向套印不准:
1、单边不到位(一只前规档纸舌太低,侧规工作时间太早,近纸定位时间太晚,侧规拉纸压球抬球太慢,输纸板前端铁板太高。
叼纸牙咬力太轻。
拖稍定位毛刷失去作用,毛刷轮太轻或没有压住纸面,侧低于输纸台面)
2、单边走过位(该边一只前规档纸舌太高,前规矩板上有线型凹槽,进纸定位距离太短,毛刷轮太重,输纸歪斜,压球压住拖梢纸边,低速机“千斤”抬起过早。
3、单边无规律套印不准(输纸歪斜,规矩部件同时出现故障)
4、双边对称走不到位(摆动牵手上滚子轴承磨损严重,摆动牵手上的横销轴磨损严重,摆动凸轮送纸部位不准)。
5、双边对称走过位(摆动大拉簧太松,前规抬起过早,摆动凸轮送纸部位磨损压印滚筒纵向位移)。
6、双边无规律套印不准(前规不在一条直线上,咬纸幅度两头悬殊,压印滚筒叼牙轴或轴套磨损,压印滚筒叼纸牙撑簧断裂,低速机输纸铁板前端离前规太远,摆动叼牙静止时间太短,摆动叼纸牙和压印滚筒叼牙轴摆杆上销钉的松动和断裂。
低速机“翻斗”和撞闩方面的故障。
叼纸牙碰“靠山”叼纸牙咬力太松,低点闭牙问题)。
二、横向套印不准:
1、纸张拉不到位(侧规挡纸舌太低,侧规拉纸球压力太小,侧规拉纸球不转,进纸离侧规太远,托梢压纸球压着纸边,高速机扁毛轮太重,高速机弹子压球架歪倒,低速机“千斤”下来过早,纸张表面太光滑,拉不到7厘米的故障)。
2、纸张拉过位(侧规挡纸太高,侧规拉纸压球压力过大,纸边卷曲,侧规短板同纸边不平行,,规矩板翘起,规矩板产生线形凹槽,高速机进纸过侧规)
3、横向无规律套印不准(摆动轴轴向窜动和侧规调节不良,压印滚筒轴向窜动和侧规调节不良,侧规规矩板歪斜和拉纸压球调节不良)除印刷设备故障以外判断纸张伸缩造成的套印不准,只要看靠山的标准“十字”线。
如果靠山“十字”套线准确而外边套印不准,属纸张伸缩的问题。
另外,可根据版面拼版的情况在中间放“十字”标准线,把余量往两边推移,损失会小一点。
第八节、防止纸张伸缩造成套印不准的补救办法
1、垫纸条,拉版改变滚筒包衬厚度,在前两色可在印版内多垫0.05mm厚两色则在橡皮布内多垫0.05mm.。
2、控制版面水分。
3、先套印一次清水使纸张适应印刷要求。
然后再开始印刷,
4、保持车间恒温恒湿,印刷车间不同季节温度湿度范围:
春秋两季温度:
21-25度相对湿度:
53-58%
夏季温度:
26-30度相对湿度:
60-65%
冬季温度:
16-20度相对湿度:
45-50%
5、晒两次印版,采取借版线的办法来弥补图像伸缩。
第九节、油墨的转移率对印刷品发花的影响
油墨的转移率一般情况,从印版转移到橡皮布上位50%。
从橡皮布转移到纸面上为76%,按这两个比例最终从印版转移物到纸面上的油墨约为38%,能保证这个转移率应属正常。
一、压力:
1、印版滚筒和橡皮滚筒之间为0.08-0.15mm
2、橡皮滚筒和压印滚筒之间为0.2-0.25mm
3、橡皮布和压印滚筒之间的压力由于垫衬性质的影响为4.5-15kg/c㎡不等。
二、纸张的平滑度决定了转移率的大小,油墨的转移率几乎同纸张平滑度的对数成比例的增长。
平滑度差的纸张只有用油墨量来弥补缺陷(或适当加入煤油)增加油墨的渗透性。
还应适当增加压力,减少或不使用胶粘以增强着实力。
三、橡皮布的印刷适应性(吸墨、传墨),对油墨的良好转移有着重要的作用(转移率76-80%)橡皮布夹空偏斜,两边不平行,绷的太紧,横竖方向上反,都会使橡皮布局部或整体表面的弹性降低,使表面不平整,从而印刷网线实地产品时就容易发花。
四、橡皮布垫衬的总体硬度大,即面压力增加,油墨的转移率相对提高,(采取中、硬性垫衬)橡皮布垫衬一般指呢子。
呢子使用时间过长,毛绒经长期碾压打结,堆积造成衬垫不平,衬纸,印版滚筒和橡皮滚筒压力不均匀,印品都会发花,其次是晒PS版的真空压力不足,使印版上网点不实造成发花。
五、油墨粘度低转移率高,反之两者成反比关系。
1、降低油墨粘度可在油墨中添加去粘剂,每加入1%,油墨粘性可降低0.2,粘度可减低2.3PA.S左右,流动度不变。
2、若降低油墨粘度,提高油墨的流动度,可以在油墨中添加6号调墨油,每添加1%,粘性可降低0.2-0.3,流动度可增加0.5mm/35℃,但用多了影响油墨的固着性和干燥性。
3、撤粘剂加得过多,都可造成油墨乳化,乳化严重就会造成印品发花。
4、油墨过干,流动性不好,都不利于油墨传递,从而造成印品发花。
六、墨辊与墨辊接触不良,使油墨不能正常传递,从而造成印品发花。
串墨辊老化,表面光滑,不能均匀的传递油墨,产生印品发花。
传墨辊老化严重,表面麻坑,裂口内存留水分,使油墨不能均匀,平实地传递给印版,从而使印品发花。
七、版面水分比例在20-25%最为理想,小于20%印品会带脏;大于25%形成“水包油”的状态,油墨转移率降低,且墨色变淡。
在这种状态下,如果不降低水而增加下墨量,则犯了胶印中最忌讳的“水大墨多”的毛病。
产生背面粘脏,印迹不干,网点毛糙等弊病。
供水量过大印品还会出现水迹或引纸后半部发花,水量不均匀会造成印品局部发花。
第十节、覆膜常见的问题及解决办法
在腹膜工艺过程中,处理好纸张与塑料膜,通过热压合机构成的温度、压力、时间三者关系。
熔合阶段控制好粘合剂稀稠、胶量、烘道温度、热棍温度、机械压力、机械速度等因素。
就能避免腹膜时的起泡,纸塑粘合不牢等方面的问题。
一、粘合牢度:
1、采用树脂型的粘合剂,因为与树脂型的油墨膜面,会很容易粘合,相应来说粘合牢度较好。
2、甲乙两种树脂组成成份的配比混合之后,粘合剂的使用期限都将直接影响粘接粘度。
3、要根据印刷墨层厚度,图文面积,调整粘合剂粘度和胶层厚度。
4、掌握复合温度在70-90°C之间,压力在15-25Mpa范围内,机速为35-45张min(4k以下)。
对开一分钟10-20张,若要机速快,温度要相应提高,压力也要调大一些,有助于纸塑复合的粘度牢度。
5、金银色墨中含有铜、铅等金属粉末,附着力差,容易从连接料中分离,影响粘接牢度。
6、油墨中撤粘剂和防粘剂加入过多,喷粉量过大会严重影响粘接牢度。
7、粗糙的纸张表面印刷大面积满版实地部分,很容易引起粘接不牢。
8、压力偏小,车速较快,温度较低会粘度不牢。
9、印刷品墨层太厚要增加粘合剂的用量,增大压力。
10、塑料薄膜表面处理不够或超过使用期(电子火花冲击),使处理面失效。
11、如果印刷墨层不干就覆膜,容易造成表面膜起皱和橘子皮现象。
一定要墨层干燥后才能覆膜。
二、折皱现象
1、出现纵向或斜向的皱折,多出现在拖梢的部位,主要原因是纸张在通过热压和机构时,不是平整自然的接受热量和压力。
2、薄膜出现斜向,纵向或横向的皱折,主要原因是薄膜在输送过程中,因牵引力不当会使薄膜的张力或大或小、松紧不一或波浪边,胶层过厚,溶剂挥发不彻底,纸张与薄膜之间产生滑动。
电热棍与橡皮棍两端不平,压力不一致;线速度不等,温度过高。
3、纸张与薄膜一起起皱,主要是施压棍压力太大。
4、车间的温度、湿度控制不当,纸张产生“荷叶边”会造成抚膜过程中的起皱。
5、滚筒压力不均匀,胶棍本身不平,胶棍有污物都会造成抚膜过程中的纸张起皱。
6、输纸歪斜造成覆膜时纸张起皱。
三、覆膜起翘
1、张力不平衡,薄膜拉得太紧,调整压力改变纸张运行方向。
2、复合压力过大,减小复合压力。
3、温度过高,适当降低复合温度。
4、纸张含水量多,湿度大。
四、出现起泡
1、施胶棍压力太小。
2、刚落版的印刷品油墨中部分溶剂没有挥发或氧化膜干燥不完全,切忌上机覆膜,易造成薄膜澎润,出现起泡脱层现象。
3、干燥温度过高,粘合剂表面结皮,应降低干燥温度。
4、薄膜表面裹入灰尘杂质。
5、粘合剂涂布不均匀,用量小。
6、粘合剂浓度高,粘度大,用稀释剂降低浓度。
第十节、油墨的干燥和印刷品背面粘脏
印刷的干燥速度对印刷的质量有很大的影响:
干燥过慢会使印刷品背面粘脏。
一、影响印迹干燥速度的因素:
1、纸张的酸碱度对印刷的干燥有较大的影响,当室温保持20℃,相对湿度75%,PH值5.4时,印迹干燥时间为30h,若PH值4.4需80h,在任何湿度的环境中印迹均能迅速干燥。
2、纸张本身的含水高也能影响印迹的干燥。
3、车间的湿度上升,纸张的含水量也相应增加,也防碍了油墨的干燥。
4、加入过多的撤粘剂,调墨油等辅助料,降低了油墨的粘着性,防碍了油墨中连接料的氧化聚合反应,油墨干燥速度不降。
5、印刷好成品堆码较高,印张面积较大,承印物表面光滑,印迹干燥缓慢。
6、版面水大、墨大造成油墨乳化严重。
7、纸张吸收性差。
8、燥油用量太少等,一般燥油用量冬天比夏天多些,后一色比前一色多,冲淡量比未冲淡量多。
二、影响背面粘脏的因素:
1、油墨本身的内聚力,油墨和印刷正面附着力大小有关。
2、油墨的触变性小,转移到印品上的墨膜,粘度的回升就缓慢,即不太容易固着结膜,因而容易发生印刷品背面粘脏。
3、纸张表面过于光滑。
4、油墨太稀薄。
5、印刷压力太轻。
6、版面水大墨大。
三、背面粘脏的预防:
1、使用快干性的油墨
2、通过喷粉加速油墨干燥速度
3、克服胶印中水大墨大的弊病
4、增加油墨的粘稠度
5、油墨内加入玉米粉(还可以适量加入煤油)或防粘剂用量不能超过5%
6、采用快干亮光油墨
7、润湿液中的PH值控制在5-6之间为宜
8、压印滚筒与橡皮滚筒之间的压力略大于印版滚筒与橡皮滚筒之间的压力为好。
第十二节、印刷品上光、压光、纸起皱常见的问题
一、水性上光常见的故障
1、光泽不好亮度不够的原因:
纸质太粗,渗透收性过强,胶水涂布量不足,涂层太薄。
上光油粘度小,固含量不足。
印刷品表面油墨不干,涂布环境温度低,湿度大,上光油内在质量不佳。
解决办法:
适当提高光油的粘度,加大涂布量,上光前应使油墨充分干燥。
如果是纸面粗糙,应先涂一层底胶或上两遍光油,提高环境温度,如烘干温度。
用光泽好的水性光油,可少量加入流平助剂。
2、干燥不好,表面发粘的原因:
上光油涂布过厚粘度偏高,供道温度及热风不足,光油PH值太高,机速过快,压力不匀。
解决办法:
降低上光油的粘度,采用乙醇和水1:
1的混合溶剂和稀释,适当减少涂布量,调整压力均匀,加强烘道温度及热风,上光油PH值应控制走8-9之间,可适量舔加快干性乳液。
3、出现条纹及橘色现象的原因:
主要是光油粘度高,涂布量过大或光油干燥太快,流干性差。
油墨不干,排斥光油,涂布棍表面太粗糙,不光滑。
解决办法:
适当降低光油粘度,减少涂布量,少量加入干助剂或PH值稳定性。
4、上光过程中出现气泡多的情况:
光油的粘度偏高,PH值偏低,循环搅拌过度。
胶桶中光油不足,机速过快等。
解决办法:
降低光油粘度,适量加入稳定剂,提高PH值,加大光油供给量。
降低涂布速度,适量加入水性消泡剂。
要充分混匀且最多加入量不宜超过1%。
5、印品放置时间过长或因在底色墨中加放过量的燥油,以致墨层在纸张表面形成晶化现象。
这样上光油时,光油附着不上墨层,会出现光油层发花不均匀现象。
遇到这种情况可在上光油中加入5%的乳酸,搅拌均匀后即可进行上光。
二、压光膜层光泽差的原因:
1、纸张质地太粗,吸性太强。
光油固含量低,涂布量少,涂层薄,压光温度偏低,压力不够。
解决办法:
纸质差的应先上一次低油,提高光油的固含量,加大涂不量,提高压光温度,适当加大压光压力。
2、印刷品压光后,表面易折裂的原因:
压光中温度偏高,使印刷品含水量降低,纸纤维以及表面涂布变脆,压光中压力大,使印刷品延伸性,柔性变差。
解决办法:
降低压光干燥温度,并采取有效措施,改变印刷品的含水量减少压光压力,调整磨切加工条件。
3、压光后印刷品空白部分呈浅色,浅色部位变色的原因:
油墨没有充分干燥,墨层耐溶剂性能不好,涂料溶剂对油墨层有一定的溶解作用,料层干燥不彻底,溶剂的残留量提高。
解决办法:
待印刷品干燥后再上油压光,减少上光涂料中溶剂的用量,(对油墨有溶解作用的溶剂)条件允许可改变溶剂或更换涂料,提高干燥温度,降低涂层及内部的溶剂残留量。
三、UV上光常见故障及排除方法:
造成亮度不好,光泽度差的原因:
光油的粘度小,涂层太薄,纸张粗糙,平滑度差,吸收性过强。
溶剂稀释过度,印刷品表面油墨不干。
油墨排斥光油,造成发花和不匀,温度低,或温度高。
再就是UV光油质量差,亮度不好光源老化,光油固化不彻底。
解决办法:
适当提高UV光油的粘度,增加涂布量,在不影响涂布量平均光滑度的情况下,尽可能少涂厚些。
对纸质太粗,应先涂一层水性底胶或溶剂型底胶,UV上光前油墨需充分干燥。
如果是排斥光油,影响光油与油墨附着力,造成发花,应先上一层底胶,应尽量减少非反应稀释剂(例如:
乙醇、乙酸乙酯、甲苯)的加入。
以免影响UV光油的彻底固化,最主要的还是选用流动性好、光泽度高的UV油。
第十三节、电化铝烫金的几个问题
一、烫印电化铝的三个基本要素:
烫印电化铝的三个基本要素是:
温度、压力和烫印时间。
烫印的温度过高,产品容易起泡,起砂孔,温度过低,则烫印不上。
一般温度在6-175℃之间,温度的高低同烫印面积成正比。
压力同温度成反比,垫板平整性同压力是否均匀一致有极大关系,压力不均匀一致往往使局部烫印不上或发花,烫金压力约在2.5-3.5mm范围内。
压印速度的快慢,使一个不可忽视的问题,机速较快,烫印时间较短,往往是烫印不上的原因之一。
机速一般控制在18印张/分钟较为合适.
在实际操作中,经常是固定烫金速度,调节烫金压力和温度,使三者处于最佳状态,从烫印效果来看,以较平的压力,较低的温度和稍慢的车速,烫印效果最为理想。
二、胶印产品电化铝烫不上的因素:
1、印刷实地版块,防止背面粘脏,在油墨中加入一些玉米粉或防粘剂,但不可超量,绝对不能超过3%,否则致使电化铝粘结胶成与玉米粉接触面产生烫印不实。
2、喷粉量要控制到最小限度,因国产喷粉以淀粉为主要原料,要严加控制。
3、有些黄和红墨的印品墨层过厚,加之燥油用量过多,印记干燥后容易产生晶化现象,要尽量不用红燥油,即使在温度过的的情况下要放燥油应选用白燥油。
4、不能在油墨中加入去粘剂,亮光浆等辅助剂,因为这些辅助剂中含有石蜡。
5、UV上光后电化铝烫印不上。
三、电化铝烫印不上的补救措施:
1、由于晶化或油墨中含有蜡类物质(亮光浆,去粘剂)发生烫印不上。
可调整烫印温度,适当加大烫印压力。
更换粘合力强的国产15号或德国的338号电化铝,烫印面积较大的可连续两次,印数较少的产品,可用五层纱布绣松香粉,在烫印部位揩擦,数量大而且质量要求高的产品,可用冲淡墨加3%的黏合剂和2%的白燥油先罩印一次,再烫印电化铝。
2、发生烫印不上的故障应对温度、压力、烫印时间多做调整和试验(包括电化铝的品种,牌号)一般规律烫印压力较小,机器速度快,印刷品底色墨层厚,图文面积大线条粗,环境温度低,烫印温度要提高,反之。
(调温范围在70-80度之间为宜)
3、属于UV上光的印品烫印不上的可选用烫印塑料的电化铝,也可用用少量乙醇擦拭去已迁移至光油涂层表面的有机硅或蜡的微量成分,然后再进行烫印。
四、烫印电化铝时产生的拉墨(反拉)故障:
这种故障看上去与烫印不上很相似,但实际并非使烫印不上,如果按烫印不上去处理往往适得其反,其实是底色印迹没有完全干燥、电化铝烫印过程中必须印迹油