斗轮机电气使用说明书.docx
《斗轮机电气使用说明书.docx》由会员分享,可在线阅读,更多相关《斗轮机电气使用说明书.docx(23页珍藏版)》请在冰豆网上搜索。
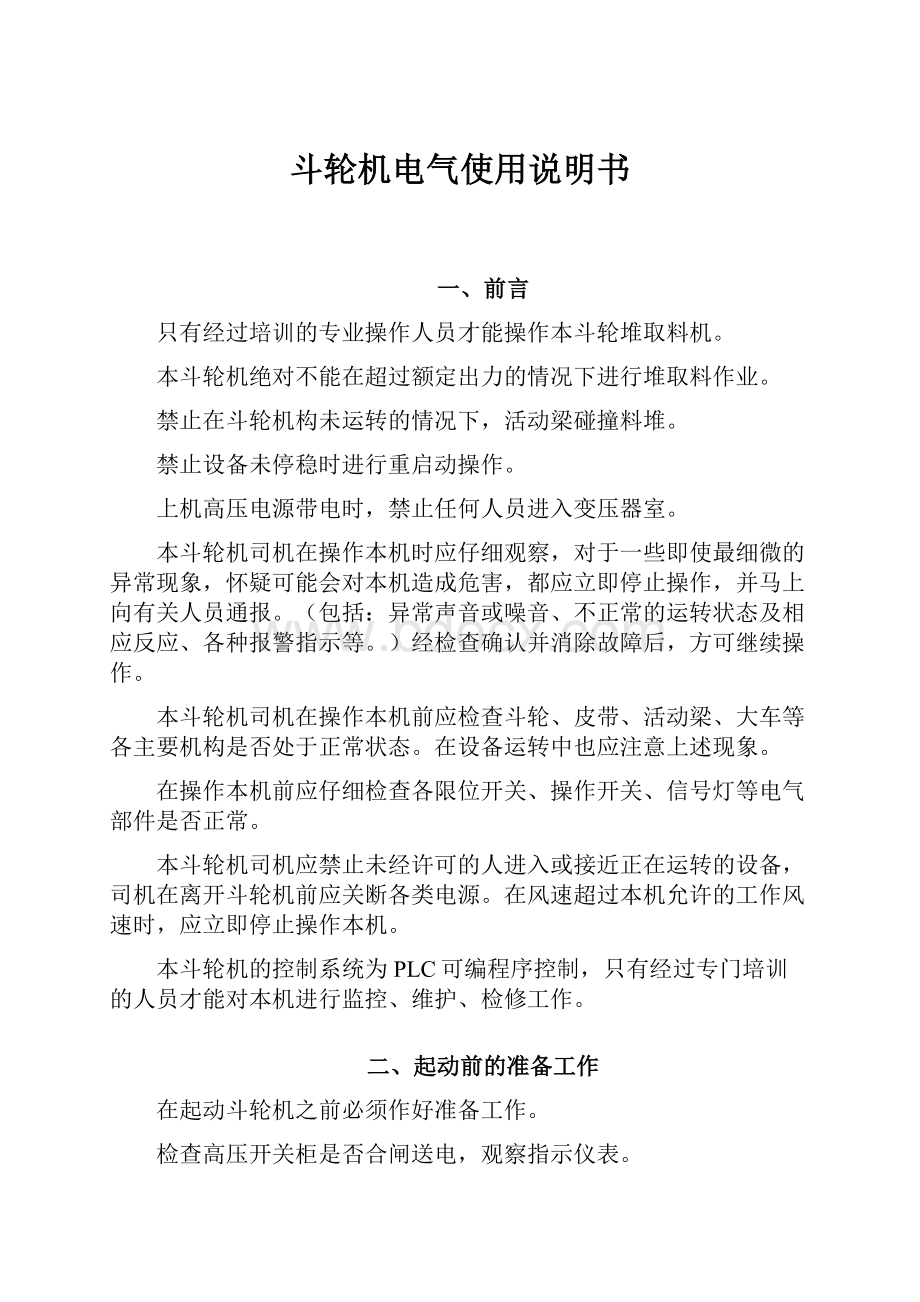
斗轮机电气使用说明书
一、前言
只有经过培训的专业操作人员才能操作本斗轮堆取料机。
本斗轮机绝对不能在超过额定出力的情况下进行堆取料作业。
禁止在斗轮机构未运转的情况下,活动梁碰撞料堆。
禁止设备未停稳时进行重启动操作。
上机高压电源带电时,禁止任何人员进入变压器室。
本斗轮机司机在操作本机时应仔细观察,对于一些即使最细微的异常现象,怀疑可能会对本机造成危害,都应立即停止操作,并马上向有关人员通报。
(包括:
异常声音或噪音、不正常的运转状态及相应反应、各种报警指示等。
)经检查确认并消除故障后,方可继续操作。
本斗轮机司机在操作本机前应检查斗轮、皮带、活动梁、大车等各主要机构是否处于正常状态。
在设备运转中也应注意上述现象。
在操作本机前应仔细检查各限位开关、操作开关、信号灯等电气部件是否正常。
本斗轮机司机应禁止未经许可的人进入或接近正在运转的设备,司机在离开斗轮机前应关断各类电源。
在风速超过本机允许的工作风速时,应立即停止操作本机。
本斗轮机的控制系统为PLC可编程序控制,只有经过专门培训的人员才能对本机进行监控、维护、检修工作。
二、起动前的准备工作
在起动斗轮机之前必须作好准备工作。
检查高压开关柜是否合闸送电,观察指示仪表。
检查全部紧急按钮是否复位。
这里需要说明的是:
各现场机侧控制站在控制操作结束后,要检查现场机侧控制站中所有的开关、按钮等是否复位,这些工作全部结束后,现场操作人员才能离开操作现场。
当有紧急情况发生时,可按下现场及其它各处的紧急按钮、急停拉线开关,待故障排除后应将该紧急按钮、急停拉线开关复位。
其余的开关、按钮多集中在电气室和司机室内,方便检查。
检查司机室联动台上的各主令控制器和开关是否在停止位,没有在停止位的要打到停止位(没有停止位的开关除外)。
检查地面中控室是否发出斗轮机工作信号。
如对某些工作信号指示有疑问,应立即与地面中控室联系进行必要的确认。
三、斗轮机电源
本机采用6kV、50Hz高压上机,电缆卷筒供电。
1、动力电源
6kV高压上机后,通过动力变压器变压后输出的AC380V低压电源经过1×1低压电源柜内的断路器后作为低压动力电源,分配给各电动机柜以驱动各机构运行。
同时,在电气室的1×0A高压电源柜上端、司机室的2×1左联动台上分别设置了显示6kV总电压表,以便操作人员在就地以及司机室内对上机高压电源进行监视。
2、控制电源
6kV高压上机后,经过控制变压器输出的AC380V三相电源,经过1×1低压电源柜内的断路器后作为总控制电源,从AC380V三相总控制电源中取出两相经过变压器变为AC220V电压作为机上的控制电源。
该控制电源经过开关电源(1A01T01)输出DC24V电压作为PLC模块电源及光电编码器电源;经开关电源(1A09T01)输出DC12V电压作为火灾报警电源。
3、其它电源
总控制电源经过1×1低压电源柜内的断路器(1V22Q01)后作为照明电源;经过1×1低压电源柜内的断路器(1V24Q01)后作为检修电源。
同时在大车行走机构、活动梁机构分别设置了检修电源箱,提供AC380V、AC220V电压以便机上各个机构的维修用电。
四、电气系统的布置
电气系统的电气设备主要分布于电气室和司机室。
1、电气室
主要设有1×0高压电源柜、1×1低压电源柜,1×2PLC控制柜、1×3、1×4、1×5低压控制柜。
1×0高压电源柜:
高压电源控制回路;
1×1低压电源柜:
低压电源控制回路;
1×2PLC控制柜:
PLC控制柜及启车报警、与输煤程控系统联锁、电话系统等控制回路。
1×3低压控制柜:
大车行走、电缆卷筒、夹轨器、尾车变换控制回路;
1×4低压控制柜:
活动梁升降、斗轮小车行走、斗轮控制回路;
1×5低压控制柜:
堆取料胶带、取料胶带、移动胶带、移动胶带小车行走、除尘系统控制回路;
2、司机室
主要设有2×1左联动台、2×2右联动台、2×3司机室低压控制柜及可编程终端。
2.1、2×1左联动台设有按钮、指示灯、电压表、转换开关,可实现如下功能:
电压指示
高压电源合分闸指示
动力电源合分闸及指示
控制电源合分闸及指示
照明电源合分闸
移动胶带小车控制(左行、右行、停止)
大车行走控制(前进、停止、后退)
2.2、2×2右联动台设有钥匙开关、按钮、转换开关、选择开关,可实现如下功能:
故障急停
钥匙开关
信号复位
启车报警
夹轨器放松与夹紧
与系统联锁(联锁、解除)
大车速度选择(满速、快速)
控制方式的选择(单动、联动、半自动)
堆取料控制(堆料、停止、取料)
斗轮小车行走(左行、停止、右行)
活动梁升降控制(上升、停止、下降)
尾车变换控制(尾车堆料、停止、尾车取料)
蜂鸣器报警:
各个机构发生故障,有声光报警,以便操作人员及时发现与处理。
事故处理后按下2×2右联动台上的信号复位按钮,将故障显示恢复正常。
2.3、2×3司机室低压控制柜:
PLC从站控制系统、风速显示。
2.4、可编程终端可实现如下功能:
本机选用AB公司生产的可编程终端。
可编程终端系统由以下几个基本屏幕组成:
状态指示屏幕:
指示斗轮机运行过程中各机构的运行状态。
限位指示屏幕:
指示斗轮机运行过程中各机构限位的动作。
故障指示屏幕:
指示斗轮机运行过程中各机构的故障情况。
数据设定屏幕:
半自动堆料过程中活动梁起升次数设定。
单动控制屏幕:
斗轮、堆取料胶带、取料胶带、移动胶带、喷水控制单动操作及半自动过程中的手动干预控制。
五、工作准备
运行人员在登机工作前,应首先抬起锚锭,然后检查电气室各控制柜内的断路器是否全部闭合,再将控制电源、动力电源合闸、放松夹轨器、选择控制方式。
1、锚锭抬起
运行人员在登机工作前,首先将设备两侧台车处的锚锭抬起,使两侧锚锭抬起限位闭合;然后进入电气室将各控制柜内的断路器全部闭合;检查各控制柜内电器元件是否有异常;关闭各控制柜柜门离开电气室。
2、控制电源合闸
进入司机室后,检查左联动台电压显示仪表是否有6kV高压上机电源。
如果上机6kV电源正常,首先将控制电源合闸。
在控制电源合闸之前,用钥匙将右联动台上“钥匙开关”闭合,再按动左联动台上“控制电源合闸”按钮,“控制合闸指示”灯亮,“控制分闸指示”灯灭,此时控制电源合闸完成。
3、动力电源合闸
控制电源合闸后才可以进行动力电源合闸。
按动左联动台上“动力电源合闸”按钮,“动力合闸指示”灯亮,“动力分闸指示”灯灭,此时动力电源合闸完成。
4、夹轨器放松
按动右联动台上“夹轨器放松”按钮,在可编程序终端的“状态指示”画面上,相应的“夹轨器放松”指示灯亮,表示夹轨器已经放松。
5、控制方式选择
门式斗轮堆取料机的控制方式分为单动控制、联动控制、半自动控制三种控制方式,三种控制方式之间可以灵活切换。
设备运行之前必须先确定一种控制方式,在设备运行的过程中,三种方式之间不允许相互切换。
通过右联动台上“控制方式选择”转换开关的转换可以选择三种方式中的一种。
按照上述顺序进行完斗轮机工作准备之后,就可以进行斗轮机正常运行的操作。
六、斗轮机各机构控制
1、单动控制
将右联动台上“控制方式选择”转换开关转至“单动”位置,整机处于单动控制状态。
单动控制方式下的操作是斗轮机的各机构均可以单独的启动和停止。
此方式仅在各机构的调试和检修时使用,必须经过生产调度人员的允许并且设备运行过程中各机构必须有运行人员进行监视和维护。
1.1、大车行走单动控制
(1)通过右联动台上“大车速度控制”旋钮可以实现大车快速、慢速的选择,大车行走前必须选择一种速度。
大车慢速行走为大车工作速度;大车快速行走为非工作速度或调车时使用,正常工作时禁止使用大车快速运行。
(2)通过左联动台上“大车行走控制”主令控制器的前、后转换可以实现大车前进、后退和停止,在可编程终端的“状态指示”画面上,相应的“大车前进”、“大车后退”指示灯亮。
(3)主令控制器在大车前进与大车后退的切换中必须待大车停稳后再向相反的方向切换。
(4)当大车行走至大车前进限位、极限或大车后退限位、极限时,大车将停止运行,在可编程终端的“限位指示”画面上,相应的“大车前进限位”、“大车前进极限”、“大车后退限位”、“大车后退极限”指示灯亮,同时,右操作台上的“故障报警”有声光报警提示。
此时,大车行走只能向相反的方向运行。
(5)大车行走的过程中,进入可编程终端的“电流指示”画面,通过屏幕上的“大车行走电机电流”监视大车行走过程中电机的电流大小。
1.2、电缆卷筒单动控制
电缆卷筒的运行没有单独的开关控制,它随着大车行走同时启动运行及延时停止运行。
1.3、喷水单动控制
(1)喷水系统的控制通过可编程终端完成。
(2)在可编程终端的“状态指示”画面上,“水箱缺水”指示灯灭时才可以进行喷水。
(3)进入可编程终端“单动控制”画面,触摸屏幕上喷水水泵“运行”按钮和“停止”按钮可以实现喷水水泵电机运行和停止。
在可编程终端“状态指示”画面上,相应的“喷水水泵运行”指示灯亮,此时方可操作水泵的堆料运行喷水和取料运行喷水。
(4)斗轮机堆料运行喷水时,进入可编程终端“单动控制”画面,触摸喷水控制“堆料”按钮,斗轮机进行堆料喷水。
堆料喷水结束时,进入可编程终端“单动控制”画面,触摸喷水控制“停止”按钮,斗轮机堆料喷水结束。
(5)斗轮机取料运行喷水时,进入可编程终端“单动控制”画面,触摸喷水控制“取料”按钮,斗轮机进行取料喷水。
取料喷水结束时,进入可编程终端“单动控制”画面,触摸喷水控制“停止”按钮,斗轮机取料喷水结束。
(6)在可编程终端“状态指示”画面上,“水箱缺水”指示灯亮时必须停止喷水,以免损坏水泵、电机。
此时,须向水箱内注水,直至可编程终端上的“状态指示”画面的“水箱水满”指示灯亮,停止向水箱内注水,可以进行斗轮机的喷水运行。
1.4、活动梁单动控制
(1)通过右联动台上“活动梁控制”主令控制器的前、后转换可以实现活动梁下降、上升和停止,在可编程终端“状态指示”画面上,相应的“活动梁上升”或“活动梁下降”指示灯亮。
(2)当活动梁动作至活动梁上升限位、极限或活动梁下降限位、极限时,活动梁将停止运行,在可编程终端“限位指示”画面上,相应的“活动梁上升限位”、“活动梁上升极限”、“活动梁下降限位”“活动梁下降极限”指示灯亮,同时,右联动台上的“故障报警”有报警提示。
此时活动梁只能向相反方向运行。
(3)活动梁升降过程中,活动梁平衡轮偏移限位、活动梁松绳保护动作时,活动梁将停止运行,在可编程终端“故障指示”画面上,相应的“活动梁平衡轮偏移”、“活动梁松绳保护”指示灯亮,同时,右联动台上的“故障报警”有报警提示。
此时,必须人为将故障排除后活动梁才能向相应的方向运行。
故障处理后按下右联动台上的信号复位按钮,将故障显示恢复正常。
(4)活动梁升降过程中,在可编程终端上可以看到“柔性腿侧活动梁”、“刚性腿侧活动梁”电机电流。
1.5、移动胶带小车单动控制
(1)通过左联动台上“移动小车控制”主令控制器的左、右转换可以实现移动小车左行、移动小车右行和停止,在可编程终端“状态指示”画面上,相应的“移动小车左行”、“移动小车右行”指示灯亮。
(2)取料过程中,移动胶带小车停止在移动胶带取料限位处不动。
在可编程终端“状态指示”画面上,相应的“移动小车取料位”指示灯亮。
(3)堆料过程中,移动胶带小车在移动胶带左转堆料左、右限位或移动胶带右转堆料左、右限位之间移动。
1.6、尾车变换单动控制
在进行尾车变换之前,其他转换开关必须处在停止位!
(1)根据堆取料工艺原则,尾车状态分为堆料和取料两种工作位。
工作时尾车所处位置与要求工况不符时,应先将尾车变换到所要求的工况,否则不能工作。
(2)尾车变换的单动控制可在司机室内完成,也可以进行尾车变换就地操作。
在进行尾车变换之前,其他转换开关必须处在停止位。
(3)通过右联动台上“尾车变换控制”转换开关的左、右转换可以实现尾车堆料变换、尾车取料变换和停止,当尾车变换堆料到位限位、尾车变换取料到位限位动作时,尾车变换将停止,在可编程终端“状态指示”画面上,相应的“尾车堆料位”、“尾车取料位”指示灯亮。
(4)尾车变换超限(主令控制器)动作时,尾车变换将停止运行,在可编程终端“故障指示”画面上,相应的“尾车变换超限”指示灯亮,同时,右联动台上“故障报警”有报警提示。
此时,必须人为将故障排除后尾车变换才能向相应方向运行。
故障处理后按下右联动台上的信号复位按钮,将故障显示恢复正常。
(5)通过尾车变换就地操作箱上“尾车变换控制”转换开关的左、右转换可以实现就地尾车堆料变换、尾车取料变换和停止,当尾车变换堆料到位限位、尾车变换取料到位限位动作时,尾车变换将停止,在可编程终端“状态指示”画面上,相应的“尾车堆料位”、“尾车取料位”指示灯亮。
此时,尾车变换就地操作完成。
注意:
在尾车变换过程中,不允许操作其他机构,否则,后果自负!
1.7、斗轮小车单动控制
(1)通过右联动台上“斗轮小车控制”主令控制器的左、右转换可以实现斗轮小车左行、斗轮小车右行和停止,在可编程终端“状态指示”画面上,相应的“斗轮小车左行”、“斗轮小车右行”指示灯亮。
(2)当斗轮小车行走至斗轮小车左行限位、极限或斗轮小车右行限位、极限时,斗轮小车将停止运行,在可编程终端“限位指示”画面上,相应的“斗轮小车左行限位”、“斗轮小车左行极限”、“斗轮小车右行限位”、“斗轮小车右行极限”指示灯亮,同时,右联动台上的“故障报警”有报警提示。
此时斗轮小车只能向相反的方向运行。
(3)斗轮小车行走过程中,斗轮小车防掉轨限位动作时,斗轮小车将停止运行,在可编程终端“故障指示”画面上,相应的“斗轮小车防掉轨限位”指示灯亮,同时,右联动台上的“故障报警”有报警提示。
此时,必须人为将故障排除后斗轮小车才能向相应的方向运行。
故障处理后按下右联动台上的信号复位按钮,将故障显示恢复正常。
(4)斗轮小车行走的过程中,进入可编程终端的“电流指示”画面,通过屏幕上的“斗轮小车行走电机电流”监视斗轮小车行走过程中电机的电流大小。
1.8、斗轮单动控制
(1)斗轮的单动控制通过可编程终端完成。
(2)进入可编程终端“单动控制”画面,触摸斗轮控制“运行”和“停止”按钮可以实现斗轮的运行和停止。
在可编程终端“状态指示”画面上,相应的“斗轮运行”指示灯亮。
(3)斗轮运行过程中,在可编程终端上可以看到“斗轮电机”电流大小。
1.9、堆取料胶带机单动控制
(1)堆取料胶带机的单动控制通过可编程终端完成。
(2)进入可编程终端“单动控制”画面,触摸堆取料胶带控制“运行”按钮和“停止”按钮可以实现堆取料胶带的运行和停止。
在可编程终端“状态指示”画面上,相应的“堆取料胶带运行”指示灯亮。
(3)在堆取料胶带运行过程中,胶带一级跑偏限位动作时,将正常运行,在可编程终端“故障指示”画面上,相应的“堆取料胶带一级跑偏”指示灯亮,同时,右联动台上的“故障报警”有报警提示。
胶带二级跑偏限位动作时,将停止运行,在可编程终端“故障指示”画面上,相应的“堆取料胶带二级跑偏”指示灯亮,同时,右联动台上的“故障报警”有报警提示。
此时,必须将故障排除后才能继续正常运行。
故障处理后按下右联动台上的信号复位按钮,将故障显示恢复正常。
(4)在堆取料胶带运行过程中,速度监控保护开关动作时,堆取料胶带将停止运行,在可编程终端的“故障指示”画面上,相应的“堆取料胶带打滑”指示灯亮,同时,右联动台上的“故障报警”有声光报警提示。
此时,必须将故障排除后才能继续正常运行。
故障处理后按下右联动台上的“故障复位”按钮,将故障显示恢复正常。
(5)在堆取料胶带运行过程中,纵向撕裂保护开关动作时,堆取料胶带将停止运行,在可编程终端的“故障指示”画面上,相应的“堆取料胶带纵向撕裂”指示灯亮,同时,右联动台上的“故障报警”有声光报警提示。
此时,必须将故障排除后才能继续正常运行。
故障处理后按下右联动台上的“故障复位”按钮,将故障显示恢复正常。
(6)胶带运行的过程中,在可编程终端上可以看到“堆取料胶带电机”电流。
1.10、取料胶带机单动控制
(1)取料胶带机的单动控制通过可编程终端完成。
(2)进入可编程终端“单动控制”画面,触摸取料胶带控制“运行”按钮和“停止”按钮可以实现取料胶带的运行和停止。
在可编程终端“状态指示”画面上,相应的“取料胶带运行”指示灯亮。
(3)在取料胶带运行过程中,胶带一级跑偏限位动作时,将正常运行,在可编程终端“故障指示”画面上,相应的“取料胶带一级跑偏”指示灯亮,同时,右联动台上的“故障报警”有报警提示。
胶带二级跑偏限位动作时,将停止运行,在可编程终端“故障指示”画面上,相应的“取料胶带二级跑偏”指示灯亮,同时,右联动台上的“故障报警”有报警提示。
此时,必须将故障排除后才能继续正常运行。
故障处理后按下右联动台上的信号复位按钮,将故障显示恢复正常。
(4)在取料胶带运行过程中,速度监控保护开关动作时,取料胶带将停止运行,在可编程终端的“故障指示”画面上,相应的“取料胶带打滑”指示灯亮,同时,右联动台上的“故障报警”有声光报警提示。
此时,必须将故障排除后才能继续正常运行。
故障处理后按下右联动台上的“故障复位”按钮,将故障显示恢复正常。
(5)在取料胶带运行过程中,纵向撕裂保护开关动作时,取料胶带将停止运行,在可编程终端的“故障指示”画面上,相应的“取料胶带纵向撕裂”指示灯亮,同时,右联动台上的“故障报警”有声光报警提示。
此时,必须将故障排除后才能继续正常运行。
故障处理后按下右联动台上的“故障复位”按钮,将故障显示恢复正常。
(6)胶带运行的过程中,在可编程终端上可以看到“取料胶带电机”电流。
1.11、移动胶带机单动控制
(1)移动胶带机的单动控制通过可编程终端完成。
(2)进入可编程终端“单动控制”画面,触摸移动胶带控制“左转”、“右转”和“停止”按钮可以实现移动胶带左转、移动胶带右转和停止。
在可编程终端“状态指示”画面上,相应的“移动胶带左转”、“移动胶带右转”指示灯亮。
(3)在移动胶带运行过程中,胶带一级跑偏限位动作时,将正常运行,在可编程终端“故障指示”画面上,相应的“移动胶带一级跑偏”指示灯亮,同时,右联动台上的“故障报警”有报警提示。
胶带二级跑偏限位动作时,将停止运行,在可编程终端“故障指示”画面上,相应的“移动胶带二级跑偏”指示灯亮,同时,右联动台上的“故障报警”有报警提示。
此时,必须将故障排除后才能继续正常运行。
故障处理后按下右联动台上的信号复位按钮,将故障显示恢复正常。
(4)在移动胶带运行过程中,速度监控保护开关动作时,移动胶带将停止运行,在可编程终端的“故障指示”画面上,相应的“移动胶带打滑”指示灯亮,同时,右联动台上的“故障报警”有声光报警提示。
此时,必须将故障排除后才能继续正常运行。
故障处理后按下右联动台上的“故障复位”按钮,将故障显示恢复正常。
(5)在移动胶带运行过程中,纵向撕裂保护开关动作时,移动胶带将停止运行,在可编程终端的“故障指示”画面上,相应的“移动胶带纵向撕裂”指示灯亮,同时,右联动台上的“故障报警”有声光报警提示。
此时,必须将故障排除后才能继续正常运行。
故障处理后按下右联动台上的“故障复位”按钮,将故障显示恢复正常。
(6)胶带运行的过程中,在可编程终端上可以看到“移动胶带电机”电流。
2、联动控制
联动控制方式为单动控制方式的联锁运行,即斗轮堆取料机的相应机构进行联锁运行。
联动控制方式下各机构的保护与单动控制方式的保护完全相同。
2.1、大车行走、卷筒、洒水、斗轮小车、活动梁升降、移动胶带小车、尾车变换机构在联动控制方式下的操作与单动控制方式下的操作完全相同。
2.2、堆料联动控制
(1)将尾车变换至堆料位置,在可编程终端“状态指示”画面上,“尾车堆料位”指示灯亮。
此时可进行联动堆料操作。
(2)移动胶带小车开至移动胶带左转堆料左、右限位或移动胶带右转堆料左、右限位,将右联动台上“堆取料控制”转换开关转至“堆料”的位置,相应机构按如下顺序启动:
a、移动胶带按相应的方向启动;
b、经过一定延时后,堆取料胶带运行。
(3)完成上述操作后,在可编程终端“状态指示”画面上,相应的机构的运行指示灯亮。
同时有“斗轮机堆料运行”指示灯亮。
(4)按照单动控制的操作方式控制其他机构的相应运行,就可以完成斗轮堆取料机的堆料作业。
2.3、取料联动控制
(1)将尾车变换至取料位置,在可编程终端的状态指示”画面上,“尾车取料位”指示灯亮。
此时可进行联动取料操作。
(2)将移动胶带小车开至移动胶带取料限位,将右联动台上“堆取料控制”转换开关转至“取料”的位置,相应机构按如下顺序启动:
a、移动胶带右转运行;
b、经过一定延时后,堆取料胶带运行;
c、经过一定延时后,取料胶带运行;
d、经过一定延时后,斗轮运行。
(3)完成上述操作后,在可编程终端“状态指示”画面上,相应机构的运行指示灯亮。
同时有“斗轮机取料运行”指示灯亮。
(4)按照单动控制的操作方式控制其他机构的相应运行,就可以完成斗轮堆取料机的取料作业。
3、半自动控制
本机单动、联动、半自动控制部分均采用AB公司生产的1756系列可编程序控制器完成。
其系统配置和原理详见电气原理图。
半自动控制操作分为半自动堆料和半自动取料两部分,并且允许在半自动运行的情况下,进行手动干预。
3.1、取料半自动
(1)将尾车变换至取料位之后,大车开至预定位置,当具备取煤条件时,即各机构无故障、锚锭抬起、夹轨器放松,便可投入半自动取料运行。
(2)将右联动台上“控制方式选择”转换开关转至“半自动”的位置。
然后将右联动台上“堆取料控制”转换开关转至“取料”的位置,斗轮机将按取料程序顺序移动胶带右转、堆取料胶带、取料胶带、斗轮启动。
当斗轮启动后,用右联动台上“斗轮小车控制”主令控制器的右(左)行档启动斗轮小车右(左)行,同时自动传入第一反向点的位置(取料起始点),然后用停止档设定第二反向点的位置(取料终止点)。
设定后,斗轮小车停止右(左)行,大车开始前进一段距离(程序内部设定),接着斗轮小车开始反方向运行(第二反向点→第一反向点),待行走至第一反向点处停止,大车又前进一段距离,又反方向行走(第一反向点→第二反向点),至第二反向点,前进,然后反向运行,再前进....重复工作下去,直至停机。
(3)在半自动取料投入前,如果煤场煤堆形状不规则,可用联动方式清理工作面,使其形状规则,然后进行半自动操作。
(4)进入可编程终端的“单动控制”画面,触摸手动干预“运行”按钮可以实现半自动取料过程中如下参数的调整:
a、第一反向点角度:
通过斗轮小车控制主令控制器记忆新的起始位置;
b、第二反向点角度:
通过斗轮小车控制主令控制器记忆新的终止位置;
c、通过左联动台上“大车行走控制”主令控制器调整取料位置;
d、通过右联动台上“活动梁控制”主令控制器调整活动梁高度。
确认后,进入可编程终端“单动控制”画面,触摸手动干预“停止”按钮可以实现半自动按新的参数执行。
半自动取料的工艺流程图见附图一。
3.2、堆料半自动
(1)将尾车变换至堆料位,将大车开至预定堆煤位置,将移动胶带
小车开至移动胶带左转堆料左限位或移动胶带右转堆料右限位处。
进入可编程终端“数据设定”画面,设定活动梁起升次数。
(2)将右联动台上“控制方式选择”转换开关转至“半自动”的位置。
然后将右联动台上“堆取料控制”转换开关转至“堆料”的位置,斗轮机将按堆料程序顺序移动胶带、堆取料胶带启动。
(3)移动胶带小车在移动胶带左转堆料左限位处,则启动后移动胶带左转,移动胶带小车右行。
移动胶带小车行至移动胶带左转堆料右限位处,反向开始左行,行至移动胶带左转堆料左限位处再次反向,开始右