机械制造工艺实习报告.docx
《机械制造工艺实习报告.docx》由会员分享,可在线阅读,更多相关《机械制造工艺实习报告.docx(40页珍藏版)》请在冰豆网上搜索。
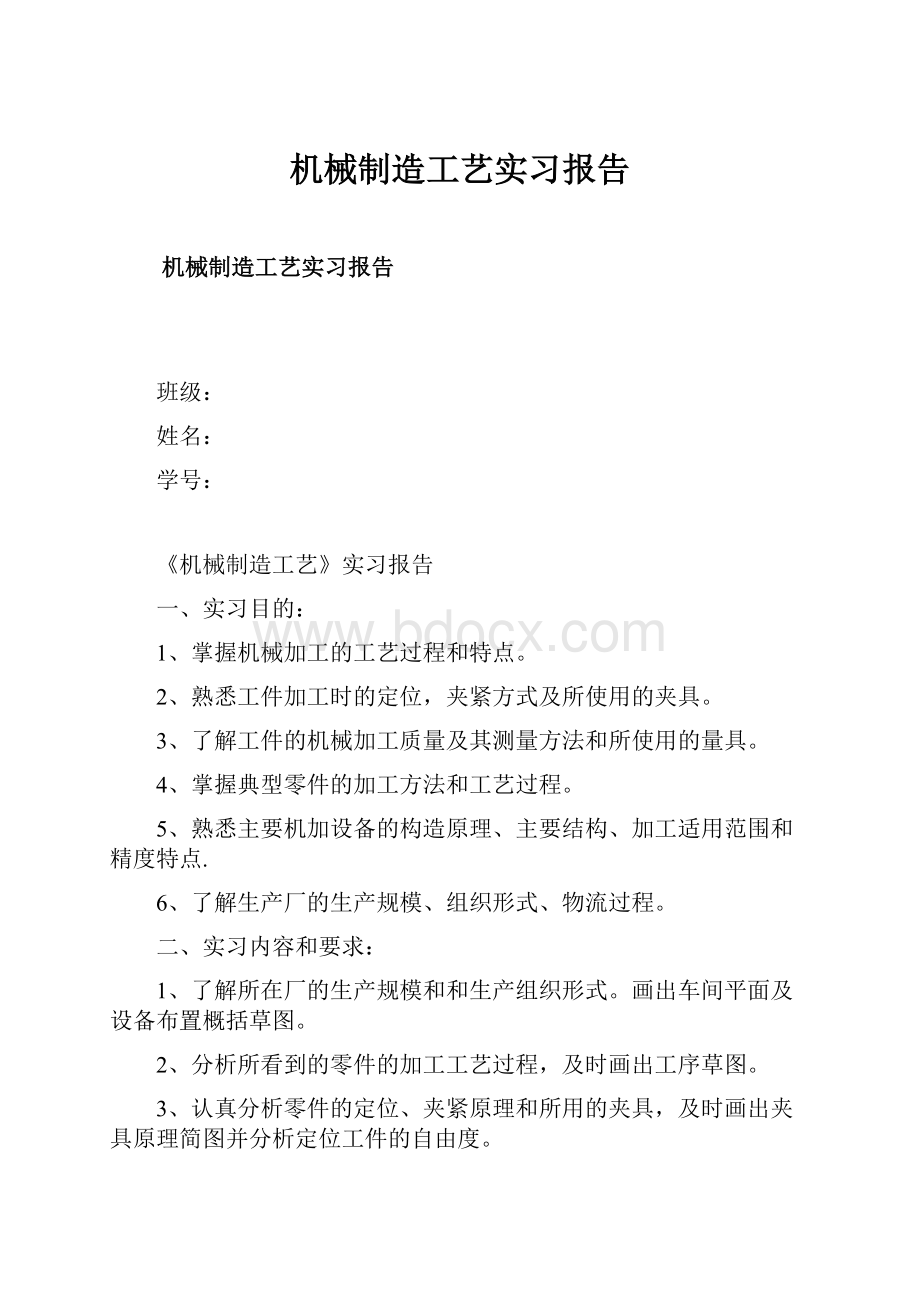
机械制造工艺实习报告
机械制造工艺实习报告
班级:
姓名:
学号:
《机械制造工艺》实习报告
一、实习目的:
1、掌握机械加工的工艺过程和特点。
2、熟悉工件加工时的定位,夹紧方式及所使用的夹具。
3、了解工件的机械加工质量及其测量方法和所使用的量具。
4、掌握典型零件的加工方法和工艺过程。
5、熟悉主要机加设备的构造原理、主要结构、加工适用范围和精度特点.
6、了解生产厂的生产规模、组织形式、物流过程。
二、实习内容和要求:
1、了解所在厂的生产规模和和生产组织形式。
画出车间平面及设备布置概括草图。
2、分析所看到的零件的加工工艺过程,及时画出工序草图。
3、认真分析零件的定位、夹紧原理和所用的夹具,及时画出夹具原理简图并分析定位工件的自由度。
4、认真分析轴类、齿轮、箱体类等典型零件的技术要求,典型表面的工艺过程和方法。
了解工件的材料、毛坯的结构形式及时效处理、热处理工艺安排,分析各加工工序的定位、夹紧和所使用的夹具,了解典型工艺过程,并掌握工件的检验方法和所使用量具的测量原理。
5、掌握车、铣、刨、镗、齿轮加工的典型机床的主要性能、规格、结构特点,精度和表面粗糙度。
画出机床结构简图,标出运动形式。
6、了解机器的装配过程,熟悉装配的工作方法;掌握典型零件的装配工艺。
了解装配时所用的设备、工具等。
7、分析零件的结构工艺性,结合其它技术要求,能制订简单的加工工艺路线。
认真分析现场工艺并能提出合理的改进意见。
三、具体实习过程
实习地点:
包钢集团设备制造有限公司(二机修车间)
实习日期:
2010年06月23日到25日。
包钢集团机械设备制造有限公司
包钢集团机械设备制造有限公司的前身是包钢机械总厂,始建于1957年,于1999年4月改制为包钢集团机械设备制造有限公司。
它是西部地区最大的冶金机械设备制造企业,具有年产钢水41000吨、异型铸件10000吨的配套能力和25000吨机加工及装配能力,是我国重型冶矿专业设备制造行业的大型骨干企业。
机制公司拥有铸钢、铸铁、锻造、铆焊、机加工、木型、工具、检修、轧钢等十余个生产车间和辅助车间。
现有在职职工1400余人,各类专业技术人员150余人,其中高级职称15人,中级职称43人,初级职称23人。
公司具有生产大型机械设备的综合能力,可以生产冶金机械产品及其它非标产品。
此外,我公司还具有制造一、二类压力容器和中压容器的资质,制造50吨以下桥(门)式起重机械资质。
公司拥有现代化的管理手段和完善的质量保证体系,技术力量雄厚工艺水平先进、员工素质较高,装备实力强。
公司通过ISO9001-2000质量体系认证。
我公司具有科研、开发、设计、制造矿山、选烧、冶金、轧钢、化工等部分和成套设备。
主要产品有:
连续铸钢机系列;各类冶金车辆及不同规格的盛钢罐、盛铁罐、盛渣罐;各类轧机系列;破碎机系列;球磨机系列;烧结机系列及化工设备等。
用户的需求就是我们的目标,敏捷优质、追求卓越是我们的行动口号,我公司立足技术创新、管理创新、服务创新、竭诚为新老用户服务.
一、重要设备
1、插床,型号B5032最大插削长度320mm,抚顺新生机床厂1972年制造。
2、万能升降台铣床,型号x63w,最大工作面宽度400mm,最大工作面长度1600mm。
北京第一机床厂1971年7月制造。
3、立式车床,型号C5110A,最大车削直径1000mm,齐齐哈尔第一机床厂1987年1月制造。
4、普通车床,型号CY6140,车削最大工件回转直径400mm,最大长度1500mm。
云南机床厂制造。
5、龙门刨床,型号B2010A,最大切削宽度1000mm,最大切削长度3000mm,1971年9月制造。
6、卧式镗铣床,型号TX8113.最大镗削直径130mm。
苏联制造。
7、龙门铣刨床:
型号B228A,最大切削宽度2800mm,最大切削长度8000mm。
滑枕行程460mm,改造日期2009年2月。
8、单臂刨床:
型号CB1016EX60最大切削宽度1600mm,最大切削长度6000mm。
9、牛头刨床:
型号BC6063,最大刨削长度630mm。
二、如加工如下零件
工艺过程分析如下:
1、定位基准的选择:
对实心的轴类零件,精基准面就是顶尖孔,满足基准重合和基准统一.所以选择中心孔作为定位基准.
2、定位原理:
采用双顶尖和三抓卡盘。
用三抓卡盘夹紧轴的一端,此时限制5个自由度,沿轴线方向的旋转自由度没有被限制。
3、热处理的选择:
预备热处理,安排在毛坯和粗加工之间,有正火和退火目的是提高切削性能。
中间热处理,消除内应力,调质提高综合力学性能。
最终热处理,淬火,提高材料的力学性能。
4、加工阶段的划分
(1)、粗加工阶段
1)毛坯处理毛坯备料、锻造和正火
2)粗加工车去多余部分,铣端面、钻中心孔和荒车外圆等
(2)、半精加工阶段
1)半精加工前热处理对于45钢一般采用调质处理以达到220~240HBS。
2)半精加工车工艺倒角(定位锥孔)半精车外圆和端面。
(3)、精加工阶段
1)精加工前热处理局部高频淬火
2)精加工前各种加工粗磨定位锥面、粗磨外圆
3)精加工精磨外圆保证最重要表面的精度。
5、工顺序的安排和工序的确定
1)车端面见平,钻中心孔;调头车另一端面保证总长120mm,钻中心孔。
2)粗车右边三个台阶,调头粗车左边一个台阶,直径留3mm余量。
3)调质220~240HBS.
4)修研两端心孔。
5)半精车右边三个台阶和调头左边一个台阶;Φ32mm加工到图纸规定要求,其余直径留0.5mm加工余量。
6)粗磨定位锥面、粗磨外圆
7)高频淬火
8)精磨外圆和端面达到图纸规定的要求
3爪卡盘夹紧原理
3爪卡盘又称自定心卡盘,原理是这样的,在一个圆锥形齿轮的背面加工有平面螺纹。
当使用钥匙转动卡盘时,带动圆锥齿轮转动,平面螺纹和活动卡爪相啮合,这样就使三个卡爪同时向中心移动。
过
道
卧式镗床
过
道
镗床T612
插床BA5063
铣床
立式车床
X53K
钻床Z3040
插床B5032
插床B5050A
入
口
镗床T-6
牛头刨床BC6063
钻床
插床B5032
插齿5B150
齿轮(滚)5355
锯床
X6140
单臂刨床
龙门铣刨床B228A
M6025A
插齿Y54
M2120
M7130
普通车床CW6110
普通车床
X62W
M1432
三、车间布置草图
实习地点:
包钢集团设备制造有限公司(检修车间)
三、重要设备
1、插床,型号B5032最大插削长度320mm,抚顺新生机床厂1972年制造。
2、万能升降台铣床,型号x63w,最大工作面宽度400mm,最大工作面长度1600mm。
北京第一机床厂1971年7月制造。
3、立式车床,型号C5110A,最大车削直径1000mm,齐齐哈尔第一机床厂1987年1月制造。
4、普通车床,型号CY6140,车削最大工件回转直径400mm,最大长度1500mm。
云南机床厂制造。
5、龙门刨床,型号B2010A,最大切削宽度1000mm,最大切削长度3000mm,1971年9月制造。
6、卧式镗铣床,型号TX8113.最大镗削直径130mm。
苏联制造。
龙门
刨床
立式车床
镗床
普通车床
镗床
普通车床
镗床
普通车床
拉床
普通车床
镗床
普通车床
钻床
牛头刨床
普通车床
普通车床
锯床
普通车床
普通车床
数控车床
普通车床
万能升降台铣床
铣床
万能升降台铣床
铣床
插齿机
入口
入口
三、车间布置图
四.典型零件的技术要求
典型零件加工工艺(轴类,箱体类,齿轮类等)
一.轴类零件的分类、技术要求
轴是机械加工中常见的典型零件之一。
它在机械中主要用于支承齿轮、带轮、凸轮以及连杆等传动件,以传递扭矩。
按结构形式不同,轴可以分为阶梯轴、锥度心轴、光轴、空心轴、曲轴、凸轮轴、偏心轴、各种丝杠等.
根据轴类零件的功用和工作条件,其技术要求主要在以下方面:
⑴尺寸精度 轴类零件的主要表面常为两类:
一类是与轴承的内圈配合的外圆轴颈,即支承轴颈,用于确定轴的位置并支承轴,尺寸精度要求较高,通常为IT5~IT7;另一类为与各类传动件配合的轴颈,即配合轴颈,其精度稍低,常为IT6~IT9。
⑵几何形状精度 主要指轴颈表面、外圆锥面、锥孔等重要表面的圆度、圆柱度。
其误差一般应限制在尺寸公差范围内,对于精密轴,需在零件图上另行规定其几何形状精度。
⑶相互位置精度 包括内、外表面、重要轴面的同轴度、圆的径向跳动、重要端面对轴心线的垂直度、端面间的平行度等。
⑷表面粗糙度 轴的加工表面都有粗糙度的要求,一般根据加工的可能性和经济性来确定。
支承轴颈常为0.2~1.6μm,传动件配合轴颈为0.4~3.2μm。
⑸其他 热处理、倒角、倒棱及外观修饰等要求。
二、轴类零件的材料、毛坯及热处理
1.轴类零件的材料
⑴轴类零件材料 常用45钢,精度较高的轴可选用40Cr、轴承钢GCr15、弹簧钢65Mn,也可选用球墨铸铁;对高速、重载的轴,选用20CrMnTi、20Mn2B、20Cr等低碳合金钢或38CrMoAl氮化钢。
⑵轴类毛坯 常用圆棒料和锻件;大型轴或结构复杂的轴采用铸件。
毛坯经过加热锻造后,可使金属内部纤维组织沿表面均匀分布,获得较高的抗拉、抗弯及抗扭强度。
2.轴类零件的热处理
锻造毛坯在加工前,均需安排正火或退火处理,使钢材内部晶粒细化,消除锻造应力,降低材料硬度,改善切削加工性能。
调质一般安排在粗车之后、半精车之前,以获得良好的物理力学性能。
表面淬火一般安排在精加工之前,这样可以纠正因淬火引起的局部变形。
精度要求高的轴,在局部淬火或粗磨之后,还需进行低温时效处理。
三、轴类零件的安装方式
轴类零件的安装方式主要有以下三种。
1.采用两中心孔定位装夹
一般以重要的外圆面作为粗基准定位,加工出中心孔,再以轴两端的中心孔为定位精基准;尽可能做到基准统一、基准重合、互为基准,并实现一次安装加工多个表面。
中心孔是工件加工统一的定位基准和检验基准,它自身质量非常重要,其准备工作也相对复杂,常常以支承轴颈定位,车(钻)中心锥孔;再以中心孔定位,精车外圆;以外圆定位,粗磨锥孔;以中心孔定位,精磨外圆;最后以支承轴颈外圆定位,精磨(刮研或研磨)锥孔,使锥孔的各项精度达到要求。
2.用外圆表面定位装夹
对于空心轴或短小轴等不可能用中心孔定位的情况,可用轴的外圆面定位、夹紧并传递扭矩。
一般采用三爪卡盘、四爪卡盘等通用夹具,或各种高精度的自动定心专用夹具,如液性塑料薄壁定心夹具、膜片卡盘等。
3.用各种堵头或拉杆心轴定位装夹
加工空心轴的外圆表面时,常用带中心孔的各种堵头或拉杆心轴来安装工件。
小锥孔时常用堵头;大锥孔时常用带堵头的拉杆心轴,
3.CA6140车床主轴加工定位基准的选择
主轴加工中,为了保证各主要表面的相互位置精度,选择定位基准时,应遵循基准重合、基准统一和互为基准等重要原则,并能在一次装夹中尽可能加工出较多的表面。
由于主轴外圆表面的设计基准是主轴轴心线,根据基准重合的原则考虑应选择主轴两端的顶尖孔作为精基准面。
用顶尖孔定位,还能在一次装夹中将许多外圆表面及其端面加工出来,有利于保证加工面间的位置精度。
所以主轴在粗车之前应先加工顶尖孔。
为了保证支承轴颈与主轴内锥面的同轴度要求,宜按互为基准的原则选择基准面。
如车小端1∶20锥孔和大端莫氏6号内锥孔时,以与前支承轴颈相邻而它们又是用同一基准加工出来的外圆柱面为定位基准面(因支承轴颈系外锥面不便装夹);在精车各外圆(包括两个支承轴颈)时,以前、后锥孔内所配锥堵的顶尖孔为定位基面;在粗磨莫氏6号内锥孔时,又以两圆柱面为定位基准面;粗、精磨两个支承轴颈的1∶12锥面时,再次用锥堵顶尖孔定位;最后精磨莫氏6号锥孔时,直接以精磨后的前支承轴颈和另一圆柱面定位。
定位基准每转换一次,都使主轴的加工精度提高一步。
4.CA6140车床主轴主要加工表面加工工序安排
主轴加工工艺过程可划分为三个加工阶段,即粗加工阶段(包括铣端面、加工顶尖孔、粗车外圆等);半精加工阶段(半精车外圆,钻通孔,车锥面、锥孔,钻大头端面各孔,精车外圆等);精加工阶段(包括精铣键槽,粗、精磨外圆、锥面、锥孔等)。
在机械加工工序中间尚需插入必要的热处理工序,这就决定了主轴加工各主要表面总是循着以下顺序的进行,即粗车→调质(预备热处理)→半精车→精车→淬火-回火(最终热处理)→粗磨→精磨。
如:
轴类零件机械加工工艺文件的制订
一、零件的工艺分析
传动轴零件图
图示零件是减速器中的传动轴,该零件小批生产。
它属于台阶轴类零件,由圆柱面、轴肩、螺纹、螺尾退刀槽、砂轮越程槽和键槽等组成。
轴肩一般用来确定安装在轴上零件的轴向位置,各环槽的作用是使零件装配时有一个正确的位置,并使加工中磨削外圆或车螺纹时退刀方便;键槽用于安装键,以传递转矩;螺纹用于安装各种锁紧螺母和调整螺母。
根据工作性能与条件,该传动轴图样规定了主要轴颈M,N,外圆P、Q以及轴肩G、H、I有较高的尺寸、位置精度和较小的表面粗糙度值,并有热处理要求。
这些技术要求必须在加工中给予保证。
因此,该传动轴的关键工序是轴颈M、N和外圆P、Q的加工。
二、毛坯的选择
该传动轴材料为45钢,因其属于一般传动轴,故选45钢可满足其要求。
本例传动轴属于中、小传动轴,并且各外圆直径尺寸相差不大,故选择φ60mm的热轧圆钢作毛坯。
三、定位基准的选择
合理地选择定位基准,对于保证零件的尺寸和位置精度有着决定性的作用。
由于该传动轴的几个主要配合表面(Q、P、N、M)及轴肩面(H、G)对基准轴线A-B均有径向圆跳动和端面圆跳动的要求,它又是实心轴,所以应选择两端中心孔为基准,采用双顶尖装夹方法,以保证零件的技术要求。
粗基准采用热轧圆钢的毛坯外圆。
中心孔加工采用三爪自定心卡盘装夹热轧圆钢的毛坯外圆,车端面、钻中心孔。
但必须注意,一般不能用毛坯外圆装夹两次钻两端中心孔,而应该以毛坯外圆作粗基准,先加工一个端面,钻中心孔,车出一端外圆;然后以已车过的外圆作基准,用三爪自定心卡盘装夹(有时在上工步已车外圆处搭中心架),车另一端面,钻中心孔。
如此加工中心孔,才能保证两中心孔同轴。
四、工艺路线的拟定
1.各表面加工方法的选择传动轴大都是回转表面,主要采用车削与外圆磨削成形。
由于该传动轴的主要表面M、N、P、Q的公差等级(IT6)较高,表面粗糙度Ra值(Ra=0.8um)较小,故车削后还需磨削。
外圆表面的加工方案可为:
粗车→半精车→磨削。
2.加工顺序的确定
对精度要求较高的零件,其粗、精加工应分开,以保证零件的质量。
该传动轴加工划分为三个阶段:
粗车(粗车外圆、钻中心孔等),半精车(半精车各处外圆、台阶和修研中心孔及次要表面等),粗、精磨(粗、精磨各处外圆)。
各阶段划分大致以热处理为界。
轴的热处理要根据其材料和使用要求确定。
对于传动轴,正火、调质和表面淬火用得较多。
该轴要求调质处理,并安排在粗车各外圆之后,半精车各外圆之前。
综合上述分析,传动轴的工艺路线如下:
下料→车两端面,钻中心孔→粗车各外圆→调质→修研中心孔→半精车各外圆,车槽,倒角→车螺纹→划键槽加工线→铣键槽→修研中心孔→磨削→检验。
定位精基准面中心孔应在粗加工之前加工,在调质之后和磨削之前各需安排一次修研中心孔的工序。
调质之后修研中心孔为消除中心孔的热处理变形和氧化皮,磨削之前修研中心孔是为提高定位精基准面的精度和减小锥面的表面粗糙度值。
拟定传动轴的工艺过程时,在考虑主要表面加工的同时,还要考虑次要表面的加工。
在半精加工φ52mm、φ44mm及M24mm外圆时,应车到图样规定的尺寸,同时加工出各退刀槽、倒角和螺纹;三个键槽应在半精车后以及磨削之前铣削加工出来,这样可保证铣键槽时有较精确的定位基准,又可避免在精磨后铣键槽时破坏已精加工的外圆表面。
在拟定工艺过程时,应考虑检验工序的安排、检查项目及检验方法的确定。
综上所述,所确定的该传动轴加工工艺过程如下:
传动轴机械加工工艺过程卡
内蒙古科技大学机械工程学院
机械加工工艺过程卡
产品名称
减速器
图号
零件名称
传动轴
共1页
第1页
毛坯种类
圆钢
材料牌号
45钢
毛坯尺寸
¢60mm×265mm
序号
工种
工步
工序内容
设备
工具
夹具
刃具
量具
1
下料
φ60mm×265mm
2
车
三爪自定心卡盘夹持工件毛坯外圆
1
车端面见平
2
钻中心孔
用尾座顶尖顶住中心孔
3
粗车φ46mm外圆至φ48mm,长118mm
4
粗车φ35mm外圆至φ37mm,长66mm
5
粗车M24mm外圆至φ26mm,长14mm
调头,三爪自定心卡盘夹持φ48mm处
(φ44mm外圆)
6
车另一端面,保证总长250mm
7
钻中心孔
用尾座顶尖顶住中心孔
8
粗车φ52mm外圆至φ54mm
9
粗车φ35mm外圆至φ37mm,长93mm
10
粗车φ30mm外圆至φ32mm,长36mm
11
粗车M24mm外圆至φ26mm,长16mm
12
检验
3
热
调质处理220~240HBS
4
钳
修研两端中心孔
5
车
双顶尖装夹
1
半精车φ46mm外圆至φ46.5mm,长120mm
2
半精车φ35mm外圆至φ35.5mm,长68mm
3
半精车M24mm外圆至
,长16mm
4
半精车2-3mm×0.5mm环槽
5
半精车3mm×l.5mm环槽
6
倒外角1mm×45°,3处
调头,双顶尖装夹
7
半精车φ35mm外圆至φ35.5mm,长95mm
8
半精车φ30mm外圆至φ35.5mm长38mm
9
半精M24mm外圆至
长18mm
10
半精车φ44mm至尺寸,长4mm
11
车2~3mm×0.5mm环槽
12
半精车3mm×l.5mm环槽
13
倒外角lmm×45°,4处
14
检验
6
车
双顶尖装夹
1
M24mm×l.5mm-6g至尺寸
调头,双顶尖装夹
2
车M24mm×1.5mm-6g至尺寸
3
检验
7
钳
划两个键槽及一个止动垫圈槽加工线
8
铣
用V形虎钳装夹,按线找正
1
铣键槽12mm×36mm,保证尺寸41~41.25mm
2
铣键槽8mm×l6mm,保证尺寸26~26.25mm
3
铣止动垫圈槽6mm×l6mm,保证20.5mm至尺寸
4
检验
9
钳
修研两端中心孔
10
磨
1
磨外圆M至尺寸
2
磨轴肩面I
3
磨外圆Q至尺寸
4
磨轴肩面H
调头,双顶尖装夹
5
磨外圆P至尺寸
6
磨轴肩面G
7
磨外圆N至尺寸
8
磨轴肩面F
9
检验
五、轴类零件的检验
1.加工中的检验
自动测量装置,作为辅助装置安装在机床上。
这种检验方式能在不影响加工的情况下,根据测量结果,主动地控制机床的工作过程,如改变进给量,自动补偿刀具磨损,自动退刀、停车等,使之适应加工条件的变化,防止产生废品,故又称为主动检验。
主动检验属在线检测,即在设备运行,生产不停顿的情况下,根据信号处理的基本原理,掌握设备运行状况,对生产过程进行预测预报及必要调整。
在线检测在机械制造中的应用越来越广。
2.加工后的检验
单件小批生产中,尺寸精度一般用外径千分尺检验;大批大量生产时,常采用光滑极限量规检验,长度大而精度高的工件可用比较仪检验。
表面粗糙度可用粗糙度样板进行检验;要求较高时则用光学显微镜或轮廓仪检验。
圆度误差可用千分尺测出的工件同一截面内直径的最大差值之半来确定,也可用千分表借助V形铁来测量,若条件许可,可用圆度仪检验。
圆柱度误差通常用千分尺测出同一轴向剖面内最大与最小值之差的方法来确定。
主轴相互位置精度检验一般以轴两端顶尖孔或工艺锥堵上的顶尖孔为定位基准,在两支承轴颈上方分别用千分表测量。
二.箱体类零件的加工
一、箱体零件概述
箱体类零件通常作为箱体部件装配时的基准零件。
它将一些轴、套、轴承和齿轮等零件装配起来,使其保持正确的相互位置关系,以传递转矩或改变转速来完成规定的运动。
因此,箱体类零件的加工质量对机器的工作精度、使用性能和寿命都有直接的影响。
箱体零件结构特点:
多为铸造件,结构复杂,多平面和孔,内部呈腔形,壁薄且不均匀,刚度较低,加工部位多,加工精度要求较高,加工难度大。
箱体零件的主要技术要求:
轴颈支承孔孔径精度及相互之间的位置精度,定位销孔的精度与孔距精度;主要平面的精度;表面粗糙度等。
箱体零件材料及毛坯:
箱体零件常选用灰铸铁,其毛坯一般采用铸件,因曲轴箱是大批大量生产,且毛坯的形状复杂,故采用压铸毛坯,镶套与箱体在压铸时铸成一体。
压铸的毛坯精度高,加工余量小,有利于机械加工。
为减少毛坯铸造时产生的残余应力,箱体铸造后应安排人工时效。
箱体类零件加工
箱体零件加工工艺分析
下面表A为上图所示某车床主轴箱小批生产的工艺过程;下面表B为该车床主轴箱大批生产的工艺过程。
从这二个表所列的箱体加工工艺过程可以看出,不同批量