钢材控轧和控冷技术的发展.docx
《钢材控轧和控冷技术的发展.docx》由会员分享,可在线阅读,更多相关《钢材控轧和控冷技术的发展.docx(7页珍藏版)》请在冰豆网上搜索。
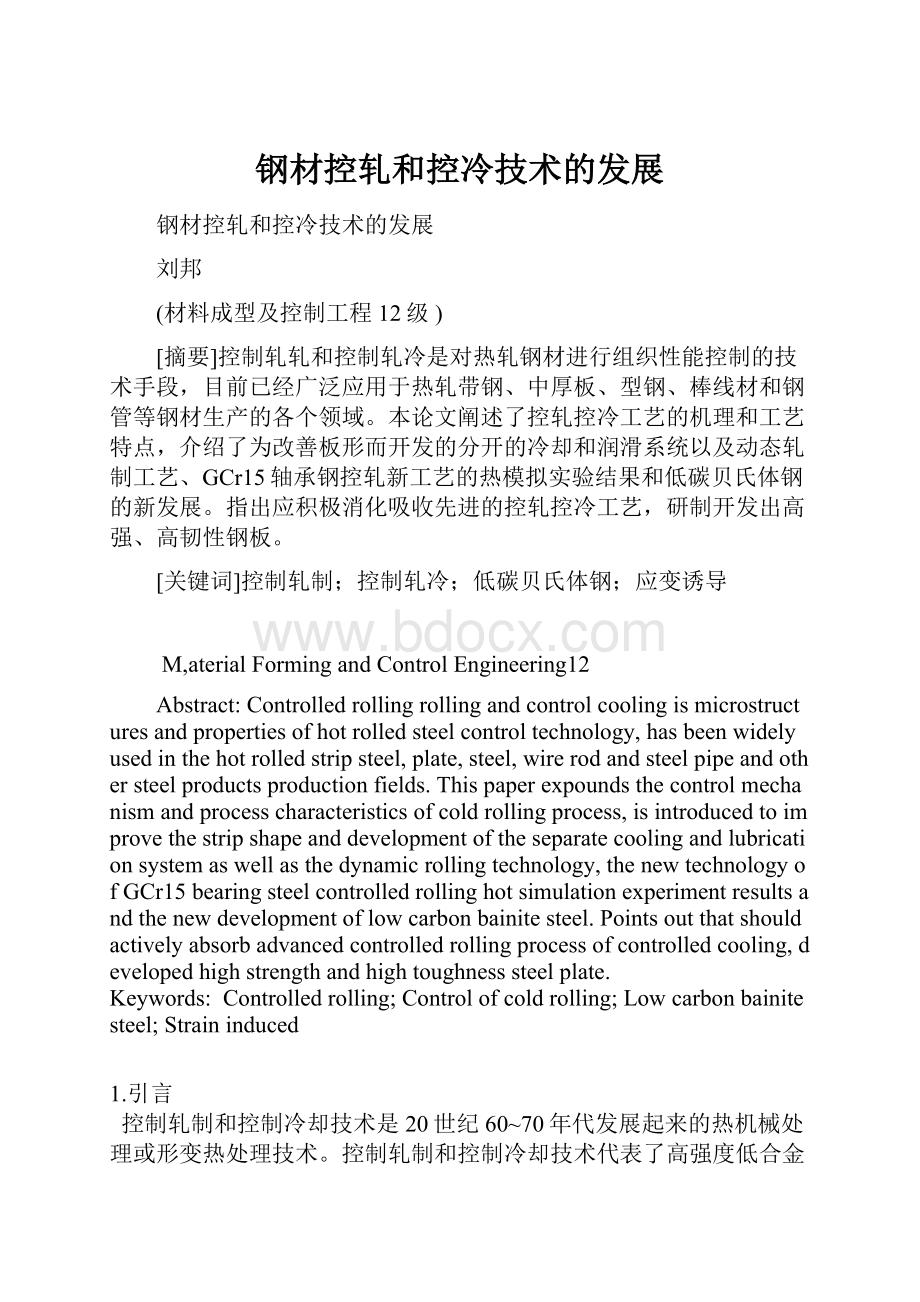
钢材控轧和控冷技术的发展
钢材控轧和控冷技术的发展
刘邦
(材料成型及控制工程12级)
[摘要]控制轧轧和控制轧冷是对热轧钢材进行组织性能控制的技术手段,目前已经广泛应用于热轧带钢、中厚板、型钢、棒线材和钢管等钢材生产的各个领域。
本论文阐述了控轧控冷工艺的机理和工艺特点,介绍了为改善板形而开发的分开的冷却和润滑系统以及动态轧制工艺、GCr15轴承钢控轧新工艺的热模拟实验结果和低碳贝氏体钢的新发展。
指出应积极消化吸收先进的控轧控冷工艺,研制开发出高强、高韧性钢板。
[关键词]控制轧制;控制轧冷;低碳贝氏体钢;应变诱导
M,aterial Forming and Control Engineering12
Abstract:
Controlled rolling rolling and control cooling is microstructures and properties of hot rolled steel control technology, has been widely used in the hot rolled strip steel, plate, steel, wire rod and steel pipe and other steel products production fields. This paper expounds the control mechanism and process characteristics of cold rolling process, is introduced to improve the strip shape and development of the separate cooling and lubrication system as well as the dynamic rolling technology, the new technology of GCr15 bearing steel controlled rolling hot simulation experiment results and the new development of low carbon bainite steel. Points out that should actively absorb advanced controlled rolling process of controlled cooling, developed high strength and high toughness steel plate.Keywords:
Controlled rolling; Control of cold rolling; Low carbon bainite steel; Strain induced
1.引言
控制轧制和控制冷却技术是20世纪60~70年代发展起来的热机械处理或形变热处理技术。
控制轧制和控制冷却技术代表了高强度低合金钢的发展方向。
控轧控冷是一种定量的按预定程序控制热轧钢形变温度、压下量(形变量)、形变道次、形变间歇停留时间、终轧温度以及终轧后的冷却速率、终冷温度、卷取温度等参数的轧制工艺。
通过降低终轧温度的方法来改善钢的力学性能,早在20世纪30年代已为人注意。
1925年H.Hanemann和F.Lucke发现,通过降低最终热加工的变形温度可使晶粒细化,从而提高轧制产品的力学性能。
然而,由于低温轧制的较大轧制负荷使一般轧机难以承受,因而这项技术很长时间并未在工业上得到实际应用。
20世纪50年代,采用控制轧制生产出352MPa级别的C-Mn钢,是世界上首次采用TMCP工艺进行的商业性生产。
直至60年代,人们认识到Nb对奥氏体再结晶的强烈阻止作用,可使钢在相对高的温度下控轧,这项技术才开始得到广泛的注意和应用。
60年代中期英国的钢铁研究人员对控制轧制开始进行了系统的研究,之后日本和法国的科研人员也相继进行了深入的探索和开发。
他们的研究成果为开发现有的控轧控冷状态的高强度钢种提供了基础。
2.我国控制轧制、控制冷却技术的发展
我国有丰富的铌、钒、钛和稀土资源,具有发展微合金控制轧制、控制冷却技术的广阔前途。
近十年来,尤其是第六个五年计划期间以来,控制轧制、控制冷却技术在我国取得了不小的进展。
目前每年采用控制轧制、控制冷却工艺生产的刚才已经超过100万吨,涉及到20多个钢种,已经应用到造船、石油、天然气输送管线、锅炉及压力容器、钢板桩、汽车大量、螺纹钢筋、钢丝绳、轴承及地质管等方面。
其中板材占40%左右,棒、线材占60%左右,管材和型材所占比例较小。
目前控制轧制、控制冷却技术在工业试验和生产上的应用如表1-1所示。
国内各厂采用控制轧制和控制冷却工艺在提纲产品综合性能方面所获得的效果。
上钢2350mm二辊-四辊中板轧机与武钢2800mm二辊-四辊中板轧机,采用两阶段控轧工艺,生产了合乎劳氏船规要求的09MnNb、16MnNb钢DH360N级船板;上钢三厂的2300mm三辊-四辊中板轧机采用混合型控制轧制工艺与轧后控冷相结合,生产出了性能达到国外同类产品实物水品的容器钢板。
武钢热轧厂1700mm热连轧机采用Ⅰ型和Ⅱ型控轧工艺,或配合使用轧后控冷,研制出7~12mm厚的合乎API-5L标准要求的X60和X65级含铌微合金钢板卷。
太钢五轧厂中板轧机采用控制轧制工艺,解决了20g钢时效冲击值及16Mng钢屈服强度偏低的问题,使热轧性能合格率提高15%以上;武钢轧板厂采用控轧工艺,提高了4C船板热轧性能合格率38%以上,邯郸钢铁厂2300mm三辊劳特式中板轧机采用IB型控制轧制工艺,轧以后水幕冷却,提高了A2F、20g中板综合性能合格率。
3.控制轧制工艺的机理和特点
控制轧制工艺是指钢坯在稳定的奥氏体区域(Ar3)或在亚稳定区域(Ar3~Ar1)内进行轧制,然后空冷或控制冷却速度,以获得铁素体与珠光体组织,某些情况下可获得贝氏体组织。
现代控制轧制工艺应用了奥氏体的再结晶和未再结晶两方面的理论,通过降低板坯的加热温度、控制变形量和终轧温度,充分利用固溶强化、沉淀强化、位错强化和晶粒细化机理,使钢板内部晶粒达到最大细化从而改变低温韧性,增加强度,提高焊接性能和成型性能。
所以说,控制轧制工艺实际上是将形变与相变结合起来的一种综合强化工艺。
3.1控制轧制的主要工艺参数
控制轧制的主要工艺参数有:
加热温度、加热时间、开轧温度、轧钢的变形量、精轧开轧温度、中间坯厚度和终轧温度。
3.1.1加热温度
加热温度对Nb、V在奥氏体中的固溶量有很大的影响,在Nb、V能固溶的范围内尽量采用低温加热,使高温奥氏体晶粒不致于粗化,从而改善韧性。
若加热温度过低,将存在部分未溶微合金碳氮化物,由于颗粒大于1000,不可能产生抑制奥氏体再结晶的作用。
适当提高再加热温度,使微合金元素的固溶量增加从而提高钢的强度和有效提高奥氏体的再结晶终止温度。
若再加热温度过高,则会使原始奥氏体晶粒粗化,从而使相变后的铁素体晶粒更粗大,不利于钢的韧性。
另外,板坯在炉加热时间对管线钢的探伤合格率有一定的影响。
3.1.2轧钢的变形量
轧钢过程中存在再结晶区域、部分再结晶区域和未再结晶区域。
为了细化铁素体晶粒,在γ再结晶区进行多道次大变形量(每道次变形量必须大于再结晶临界变形量)高温粗轧,通过形变/再结晶反复进行使奥氏体晶粒充分细化;同时还须保证粗轧结束时处于完全再结晶区,不能进入部分再结晶区,以免产生混晶组织。
根据变形温度可知,此时变形处在部分再结晶区,奥氏体再结晶数量急剧增加。
同时变形量的增加使晶粒变形加剧,晶粒因发生畸变增加了储存能,发生再结晶时形核的驱动力增加,促进了再结晶的发生,使奥氏体晶粒更加细小,并最终获得细小的铁素体晶粒。
在γ未再结晶区精轧时必须保证较大的累积变形量,这样才可使奥氏体晶粒充分压扁,在拉长的奥氏体晶粒内产生高密度的形变孪晶和形变带,同时微合金元素的碳氮化物因应变诱导析出,从而为铁素体转变提供更多的有利形核位置。
因此,在γ未再结晶区轧制时累积变形量越大,轧后铁素体晶粒的细化效果越好,改善钢综合性能的效果越显著。
3.1.3中间坯厚度
γ再结晶区轧制结束后板坯待温时的厚度称为中间坯厚度。
适当增加中间坯厚度,可增大γ再结晶温度以下时的累积变形量(即精轧累积变形量),使变形奥氏体晶粒内部的形变能和形变缺陷增多,从而有利于提高相变驱动力,减少带状区域相变温度差,减小相变的不同时性,有利于铁素体均匀形核,最终使晶粒细化并减少带状组织,进一步改善钢的综合性能。
适当地增加中厚板轧件的中间坯厚度,致使表层奥氏体组织在低温时发生大变形,加上机架间除鳞高压水冷却、轧件与传送辊、轧辊的接触导热可快速降低表层组织的温度,促使表层组织发生应变诱导相变,在适当条件下可实现表层组织的超细晶化。
在轧制过程中轧件表层组织硬化使其变形抗力逐渐增大,有利于变形向心部渗透,从而细化表层以下材料的晶粒,进而实现内部组织的细晶化。
4.控制轧制、控制冷却工艺参数控制特点
4.1控制轧制和控制冷却的工艺参数控制与普通轧制工艺相比具有如下特点:
1.控制钢坯加热温度
2.控制最后几个轧制道次的轧制温度。
3.要求在奥氏体末再结晶区域内给予足够的变形量。
4.要求轧制后的钢材冷却速度、开始快冷温度、快冷终了温度或卷取温度,以便获得必要的显微组织。
5.控轧和控冷工艺的优点和缺点
5.1控制轧制的优点如下:
1.可以在提高钢材强度的同时提高钢材的低温韧性。
2.可以充分发挥铌、钒、钛等微量元素的作用。
5.2控制冷却的优点:
1.节约能源、降低生产成本。
2.可以降低奥氏体相变温度,细化室温组织。
3.可以降低钢的碳当量。
5.道次间控制冷却可以减少待温时间,提高轧机的小时产量。
6.板带材控轧工艺过程的新方法
板带材的质量很大程度上取决于对轧制工艺过程的控制。
常规方法有许多不足之处,原始凸度的设定无法对不同规格、不同材质的轧件进行跟踪控制;不均匀冷却方法具有响应太慢的缺点。
戴维.麦基公司对板形自动控制系统及冷却液的喷射装置进行了独特的设计,其中彼此分隔开的冷却和润滑系统(SLC)和动态轧制工艺系统(DSS)收到了很好的效果。
6.1分隔开的冷却和润滑系统(SLC)
板带材轧制大多数采用乳液来实现冷却润滑。
在采用乳液冷却润滑的过程中,普遍存在乳液稳定性差、使用寿命短,尤其是轧后板带材表面质量达不到最佳程度等问题。
利用分隔开的冷却和润滑系统可避免常规乳液冷却润滑给制品带来的缺陷。
该系统有两个连在一起的钢质冷却箱。
每个冷却箱分别封住上工作辊和支承辊的辊面及下工作辊和支承辊的辊面,从而使每一个对轧辊和冷却箱构成一个隔离系统。
上下两个冷却箱之间有一道缝,需轧制的带材由此通向辊缝,实现轧制。
在轧制过程中把冷却系统和润滑系统分隔开,这就意味着在具备冷却润滑综合功能的基础上,还可以分别按各自独特的功能去进行配制。
SLC系统可最大限度地发挥冷却和润滑的功能,从而使轧机的功率密度大大提高。
6.2动态轧制工艺系统(DSS)
戴维.麦基公司利用计算机预测了全带材轧制的主要过程。
充分利用计算机来建立轧制过程中的数学模型,本质上就是在线的模型参数估计。
其中最为典型的例子是动态轧制工艺系统。
该系统主要安装在热轧机组上,用于板形和断面形状的控制。
由建立的数学模型和程序,根据预测的结果,连续地由轧机自适应功能进行控制。
与通常的反馈式AGC系统不同之处,在于这个系统采用两个基本自适应等级。
第一级为轧机控制的自适应,即包括轧辊的弯辊力、压下量的方式、运行速度和轧辊冷却液的分布等,使产品质量达到始终稳定一致。
第二级是预测模型所用系数的自适应,即利用在轧制过程中测得的参数经过趋势回归分析来实现。
接着按实测值与模型预测值的误差值作为一个函数来调整模型的系数。
应用DSS的主要目的是要生产出横向厚度均匀一致的产品。
6.3GCr15控轧新工艺的模拟研究
近年来,一些工作者研究了轴承钢的热加工性能以及形变球化和再结晶,定量地确定了流变应力和破断应变与变形过程中的变量(应变、应变率、温度和相变)之间的关系;研究奥氏体加渗碳体的双相区形变球化,确定了变形温度和变形量是控制球化的主要因素,奥氏体化后变形有利于双相区形变球化;借助于热扭转实验机用停顿变形方法,研究了轴承钢热轧过程中的再结晶行为,确定了静态和动态再结晶,与变形温度、道次应变和道次间隔时间等之间的关系,以及在双相区发生的动态软化现象。
这一系列的工作为正确制定轴承钢控制轧制工艺提供了科学的依据。
轴承钢的各种生产工艺中,在900℃以上奥氏体单相区轧制后快冷至850~800℃的双相区内再次轧制是最有前途的新工艺。
该工艺对控制轧制的推广应用、改善轴承钢的质量及提高其疲劳寿命、节省能源等方面均有重要意义。
7.提高控制轧制的途径和方法
7.1交叉轧制
各个轧制阶段都有一定的开轧温度和终轧温度。
因此,各阶段之间都有一个.中间冷却待温的问题。
中伪冷却时间的长短主要取决于轧件的中间厚度,中间厚度愈大,轧件在辊道上放置的时间就愈长。
轧机只轧制一块板坯时,轧件的中间
冷却待温会造成轧机产量较大的下降。
如果在轧件中间冷却期间,让轧机轧制其它轧件,那显然会提高轧机的产量。
根据鞍钢厚板厂轧制线条件和板坯的情况,提出三种交叉轧制方案。
总之,采用交叉轧制,就在于充分地利用轧件的中间冷却时间,让轧机轧制另外的轧件,达到提高轧机产量的目的。
7.2缩短中间冷却时间
为了缩短轧件中间冷却时间,结合二期工程还要增设精轧机的条件,在粗轧机后设置一喷淋冷却装置,由于轧机后设置喷淋冷却装置,同样的待冷轧件,轧件在轧机前和轧机后的中间冷却时间会有所不同。
据此,我们给出了两块钢板的两阶段交叉轧制方法。
这种方法的要点是要使轧件在轧机前的中间冷却时间大于精轧时间。
这种方法适合于较厚产品的生产,轧件在轧机后,可根据实际需要确定轧件的喷水时间,以保证轧制节奏协调,从而达到提高产量的目的。
待将来安装精轧机后,实现多块钢板的控制轧制,喷淋冷却在缩短轧件中间冷却时间方面就会显示出其重要作用。
7.3控轧控冷
控制冷却是一种利用钢材轧后余热进行热处理的操作。
分为直接淬火和加速冷却两种。
在中厚板轧制线上可设置直接淬火和加速冷却两种装置,或设置多功能冷却装置,由于它们具有不同的冷却速度和冷却能力,便可生产出所要求机械性能的轧材。
前面已指出,控制轧制与控制冷却都是细化铁素体晶粒的重要方法。
但控制轧制,特别是三阶段轧制,由于轧制温度低,再加上两次中间冷却,对轧机产量影响很大。
如果采用两阶段轧制,配以加速冷却,同样可以生产出满足性能要求的钢材,这既减轻了轧机负荷,又提高了产量。
用加速冷却方法处理钢板时,一定要控制钢板冷却开始温度、冷却速度和冷却终止温度,使之形成铁素体和岛状贝氏体复合组织,同时要防止生成不利于韧性的马氏体组织。
还要保证处理的钢板冷却均匀,以免造成瓢曲,只有钢板在宽度、长度和厚度方向上达到均匀冷却,才能保证钢板的性能均匀。
总之,控制轧制与控制冷却对轧材组织各有不同作用,两者可以互为条件。
相互补充,达到提高产品性能的目的。
控制轧制与控制冷却相结合,可以减轻轧机负荷,提高产量。
提高终轧变形率,可使第二阶段轧件开轧厚度减小,达到提高产量的目的。
在保证总压缩比的条件下,还可用较薄板坯,减小总的压下量,以便提高轧机的产量。
8.结语
采用控轧控冷工艺技术是生产强度高、韧性好、可焊性优良且成本低的钢板的最好办法,将应变诱导轧制技术与常规控轧工艺相结合可获得更为理想的超细晶组织。
可以借鉴国内外先进的轧制工艺控制方法,消化、吸收这些新技术,充分发挥控制轧制工艺的优势,在我国现有资源的条件下,研制开发出高强、高韧性钢板,特别是低温韧性好的钢板。
[参考文献]
[1]高惠临《钢的控轧控冷技术及其研究进展》
[2]《钢铁研究学报》1999年第三期38-43页
[3]张展文;钢的控制轧制【J】;兵器材料科学与工程;1985年Z1期
[4]王有铭《钢材的控制轧制和控制冷却》第2版
[5]石凯管线钢控制轧制与控制冷却技术的应用和进展【J】;焊管;1995年03期
[6]韩维坤;控制轧制的影响因素【J】鞍钢技术;1980年04期