液态成型作业答案 完结版.docx
《液态成型作业答案 完结版.docx》由会员分享,可在线阅读,更多相关《液态成型作业答案 完结版.docx(24页珍藏版)》请在冰豆网上搜索。
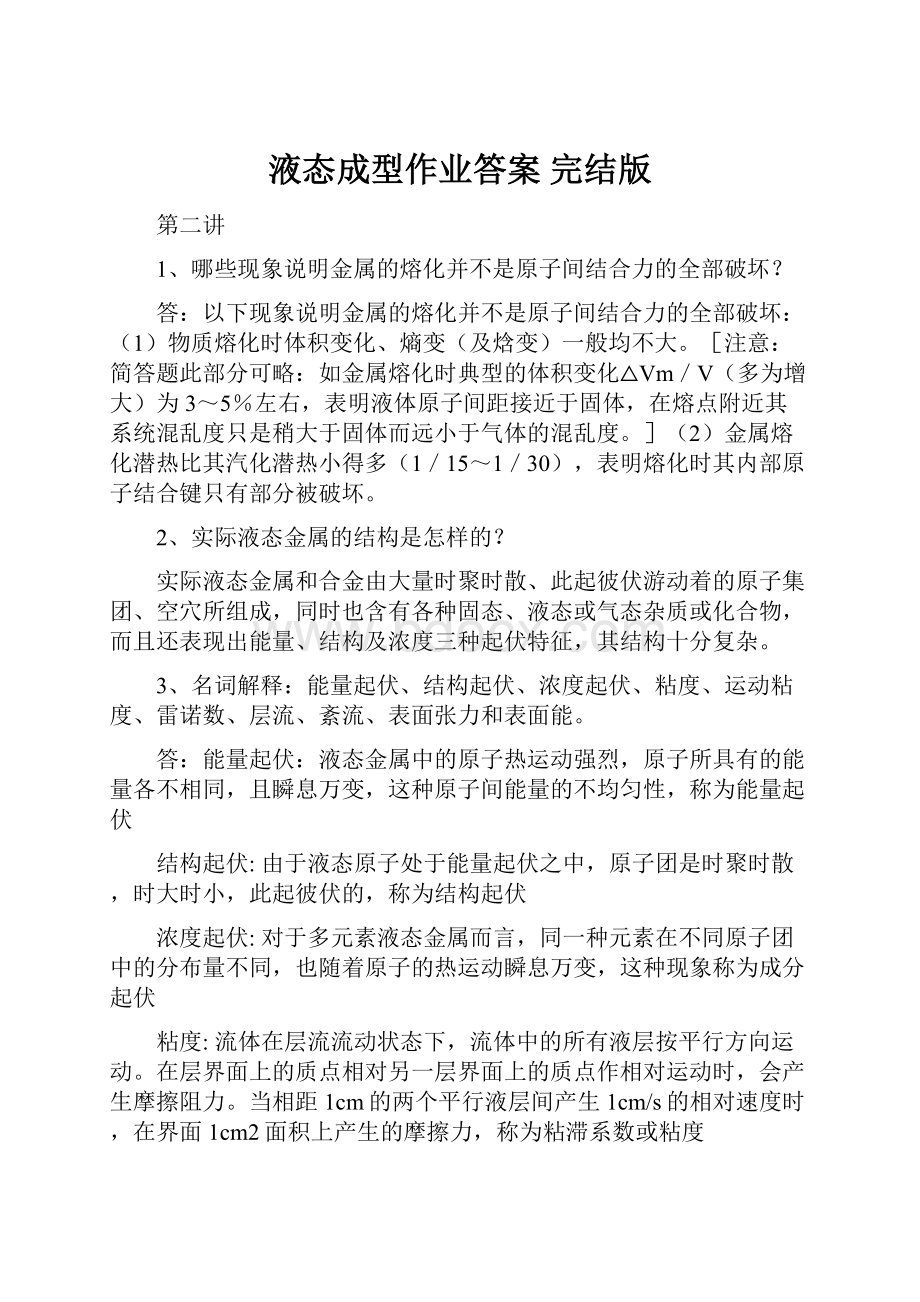
液态成型作业答案完结版
第二讲
1、哪些现象说明金属的熔化并不是原子间结合力的全部破坏?
答:
以下现象说明金属的熔化并不是原子间结合力的全部破坏:
(1)物质熔化时体积变化、熵变(及焓变)一般均不大。
[注意:
简答题此部分可略:
如金属熔化时典型的体积变化△Vm/V(多为增大)为3~5%左右,表明液体原子间距接近于固体,在熔点附近其系统混乱度只是稍大于固体而远小于气体的混乱度。
]
(2)金属熔化潜热比其汽化潜热小得多(1/15~1/30),表明熔化时其内部原子结合键只有部分被破坏。
2、实际液态金属的结构是怎样的?
实际液态金属和合金由大量时聚时散、此起彼伏游动着的原子集团、空穴所组成,同时也含有各种固态、液态或气态杂质或化合物,而且还表现出能量、结构及浓度三种起伏特征,其结构十分复杂。
3、名词解释:
能量起伏、结构起伏、浓度起伏、粘度、运动粘度、雷诺数、层流、紊流、表面张力和表面能。
答:
能量起伏:
液态金属中的原子热运动强烈,原子所具有的能量各不相同,且瞬息万变,这种原子间能量的不均匀性,称为能量起伏
结构起伏:
由于液态原子处于能量起伏之中,原子团是时聚时散,时大时小,此起彼伏的,称为结构起伏
浓度起伏:
对于多元素液态金属而言,同一种元素在不同原子团中的分布量不同,也随着原子的热运动瞬息万变,这种现象称为成分起伏
粘度:
流体在层流流动状态下,流体中的所有液层按平行方向运动。
在层界面上的质点相对另一层界面上的质点作相对运动时,会产生摩擦阻力。
当相距1cm的两个平行液层间产生1cm/s的相对速度时,在界面1cm2面积上产生的摩擦力,称为粘滞系数或粘度
运动粘度:
液体在重力作用下流动时内摩擦力的量度,数值等于γ=η/ρ。
表面张力:
产生新的单位面积表面时系统自由能的增量。
与表面能大小、单位一致,从不同角度描述同一现象。
表面能:
表面自由能(简称表面能)为产生新的单位面积表面时系统自由能的增量。
雷诺数:
流体流动时的惯性力Fg和粘性力(内摩擦力)Fm之比称为雷诺数。
用符号Re表示。
Re是一个无因次量。
层流:
流体流动时,如果流体质点的轨迹(一般说随初始空间坐标x、y、z和时间t而变)是有规则的光滑曲线(最简单的情形是直线),这种流动叫层流。
紊流:
在一定雷诺数下,流体表现在时间和空间上的随机脉动运动,流体中含有大量不同尺度的涡旋(eddy)。
4、分析粘度的影响因素及其对粘度的影响规律。
①温度一般情况下温度提高,液体金属的粘度减小。
②化学成分
杂质的数量、状态和分布情况都能在不同程度上影响到液态金属的粘度。
在液态金属中呈固态杂质常使其粘度增加。
但有些熔点低的杂质在液态属中呈熔融状态,反而会使该液态金属的粘度降低。
酸性钢较碱性钢的粘度小就是因为酸性钢的杂质多是液态的,而碱性钢的杂质常呈粒状固体;共晶成分的合金粘度小;液体金属和合金的粘度与其过热度有关,过热度越大,粘度越小。
5、分析表面张力的影响因素及其对表面张力的影响规律。
(1)表面张力与熔点的关系
熔点越高,或摩尔表面积越大,表面张力越大。
因为熔点越高说明金属原子之间的作用力越大,所以表面张力也越大。
(2)表面张力与温度的关系在高温及低温区,表面张力均随温度的增加而减小,二者几乎成直线关系;对大多数液体金属来说,表面张力与温度呈线性关系。
这是因为随着液体金属温度的升高,原子热振动加剧,振幅变大,原子间的距离增加,相互作用减弱,因此表面张力下降。
但也有反常情况,例如铜,随着铜熔体温度的升高,表面张力也随着增加
(3)表面张力与化学成分的关系
化学成分对表面张力的影响有两种情况,一种是合金元素的加入使液体金属表面张力降低,这种元素对该种金属来说称为液体金属的表面活性物质,具有正吸附作用;另一种是合金元素的加入使液体金属表面张力增加,这种元素对该种金属来说称为液体金属的表面非活性物质,具有负吸附作用。
通常正吸附时溶质元素在表面的浓度大于其在内部的浓度,而负吸附时溶质元素在表面的浓度小于其在内部的浓度。
第三讲
1、流动性与充型能力的联系和区别。
答:
区别:
①二者概念不同。
铸造工艺学中的流动性指液态金属本身的流动能力,常用规定的铸型条件和浇注条件下的试样的长度或薄厚尺寸来衡量;而充型能力是指液态金属充满铸型型腔,并使铸件形状完整、轮廓清晰的能力。
②影响因素有区别。
流动性是液态金属本身的流动能力,与金属的成分、温度、杂质含量,及其物理性质有关;而充型能力除了取决于金属本身的流动能力外,还受外界条件,如铸型性质、浇注条件、铸件结构等因素的影响。
联系:
都是影响成形产品质量的因素。
①流动性好的合金充型能力强;流动性差的合金充型能力亦差,但是,可以通过改善外界条件提高其充型能力。
②可认为合金的流动性是在确定条件(试样结构、铸型性质、浇注条件)下的充型能力。
2、用同一种合金浇注同一批、同一种铸件,其中有一两件出现“浇不足”缺陷,可能是什么原因造成的?
答:
因为是用同一种合金浇注同一批、同一种铸件,所以合金性质、铸件结构相同,但可能由于一两件的铸型温度、浇注温度偏低(后浇的因为温降而温度略低)、或者浇注速度偏高、充型压头小等原因,都会造成“浇不足”缺陷。
3、用螺旋形试样测定合金的流动性时,为了使测得数据稳定和重复性好,应控制那些因素?
答:
应控制的因素包括:
铸型条件、浇注条件恒定,如铸型温度保持不变,浇注温度、速度、充型压头保持恒定。
4、四类影响充型能力的因素中,哪些是可以控制的,哪些是不可控的,提高浇注温度会带来什么负作用?
一般条件下:
合金与铸件结构不可控制,而铸型和浇铸条件可以控制,浇铸温度太高,容易使金属吸气,氧化严重达不到预期效果。
第四讲
1、什么是温度场?
空间中一切点的瞬时温度值的集合
2、温度场的研究方法有哪些?
实测法,数学解析法,数值模拟法。
第五讲
1、铸件温度场的影响因素有哪些、各是如何影响的?
金属性质的影响:
(1)金属的热扩散率a
热扩散率大→铸件内部的温度均匀化能力高→温度梯度小,断面温度分布曲线平坦
例:
a铝合金>a铁碳合金→铝合金断面温度分布曲线相对平坦
a普碳钢>a高合金钢→普碳钢断面温度分布曲线相对平坦
(2)结晶潜热
(3)金属的凝固温度
结晶潜热大→向铸型传热时间长→铸型内表面被加热温度高→温度梯度小→温度场平坦
凝固温度高→铸件表面与中心温差大→温度场梯度高,如:
有色合金铸件比铸钢件和铸铁件的温度场平坦
铸型性质的影响:
铸型吸热速度越大→铸件凝固速度越大→温度梯度
(1)铸型蓄热系数b2
b2越大→对铸件冷却能力越强→温度梯度越大
(2)铸型预热温度T型
T型越高→对铸件冷却作用越小→温度梯度越小
熔模铸造,T型=600~900℃
金属铸造,T型=200~400℃
浇注条件的影响:
(1)金属过热量远远小于结晶潜热。
(2)砂型铸造中,增加过热度,相当于提高铸型温度,从而减小铸件温度梯度。
(3)金属型铸造中,因铸型导热能力强,而过热量比重很小,能迅速传导出去,故浇注温度影响不很明显。
铸件结构的影响:
(1)铸件壁厚
厚壁铸件比薄壁件含有更多热量,会把铸型加热到更高的温度。
铸件越厚,温度梯度越小。
(2)铸件形状
铸型中被液态金属几面包围的突出部分,型芯以及靠近内浇道附近的铸型部分,由于有大量金属液通过,被加热到很高温度,相对应的铸件的温度场较平坦。
2、名词解释:
等温面、倾出边界、补缩边界。
等温面:
瞬时温度场中温度相同的各点相连构成的面
倾出边界:
液固部分与固液部分的边界
称为倾出边界。
补缩边界:
固液部分分为两个带,其中,一个带里,晶体虽已连成骨架,但是液体还能在其间移动。
另一个带中,晶体连接成牢固的骨架,骨架中的液体(小熔池“)不能互相沟通,凝固体积收缩时,熔池得不到液体的补充。
上述两带的边界称为补缩边界。
3、根据凝固区域的宽度不同,凝固方式如何分类?
试述各凝固方式的概念、特点。
根据合金固液相区宽度,可将凝固过程分为三种方式:
逐层凝固:
合金结晶温度范围很小或断面温度梯度很大时,铸件断面的凝固区域很窄,固液体几乎由一条界线分开,随温度下降,固体层不断加厚,逐步到达铸件中心。
体积/糊状凝固:
合金结晶温度范围很宽或断面温度梯度很小时,铸件断面的凝固区域很宽,在凝固的某一段时间内,凝固区域在某时刻贯穿整个铸件断面时,在凝固区域里既有已结晶的晶体也有未凝固的液体。
中间凝固:
合金结晶温度范围较窄或断面温度梯度较大时,铸件断面上的凝固区域界于前二者之间。
4、凝固方式如何影响铸件的质量?
凝固方式分为三种:
①逐层凝固方式对铸件质量的影响:
流动性好,容易获得健全凝固体,液体补缩好,铸件组织致密,形成集中缩孔的倾向大;热裂倾向小,气孔倾向小,应力大,偏析严重。
②体积凝固方式对铸件质量的影响:
流动性差,不容易获得健全的凝固体,液体补缩差,铸件组织不致密,形成集中缩孔的倾向小,热烈倾向大,气孔倾向大,缩松倾向大,应力小,宏观偏析不严重。
③中间凝固方式对铸件质量的影响介于上述二者之间。
第六讲
1、何谓平方根定律和折算厚度法则?
试述二者的区别与联系。
平方根定律:
凝固层厚度与凝固时间的平方根成正比。
“折算厚度”法则:
体积为V1和表面积为S1的铸件,其完全凝固时间t,已由公式给出,将厚度的表达式代入,得
R-铸件的折算厚度。
铸件凝固时间与铸件形状无关,与当量厚度平方成正比。
凝固金属和铸型材料影响凝固时间和凝固速率。
区别:
平方根定律是指凝固层厚度与凝固时间的平方根成正比。
主要适用于大型平板类、结晶间隔小的合金铸件。
折算厚度法则指铸件的凝固时间与其折算厚度的平方成正比。
适用于大平板、球和长的圆柱体。
联系:
二者均可以计算铸件的凝固时间,且折算厚度法则可以直接从平方根定律导出。
由于折算厚度法则考虑了铸件形状这个主要影响因素,所以更加接近实际,是对平方根定律的一个发展。
(补充)用Chvorinov公式计算凝固时间时,误差来源于铸件的形状、铸件结构、热物理参数浇注条件等方面。
半径相同的圆柱和球体比较,前者的误差大;大铸件和小铸件比较,后者误差大;金属型和砂型比较,后者误差大,因为后者的热物性参数随温度变化较快。
第七讲
1、试述均质形核与异质形核之间的联系和区别。
均质形核与异质形核是晶体两种不同的形核方式。
前者是依靠过冷液相中的结构起伏进行形核的方式,而后者则依靠外来质点进行形核。
均质形核需要很大的过冷度和更高的形核功,所以实际金属和合金中很难发生均质形核,而多是异质形核。
二者的临界形核半径相同,异质形核形核功△Ghe*与均质形核形核功△Gho*之间有如下关系:
△Ghe*=f(θ)△Gho*,其中,θ为新生固相与基底的夹角。
θ<180°时,为异质形核;θ=180°时,为均质形核。
2、试推导均质形核临界晶核半径。
懒得打公式。
。
。
书上或者课件上找。
。
。
3、影响异质形核的因素都有哪些?
形核温度T、形核时间、形核基底的数量、接触角θ、形核基底的形状
4、粗糙界面与光滑界面的生长方式各是怎样的?
粗糙界面:
连续长大
光滑界面:
侧面长大,分为二维晶核台阶和晶体缺陷台阶
第八讲
1、何谓结晶过程中的溶质再分配?
何谓平衡结晶?
结晶过程中的溶质再分配:
是指在结晶过程中溶质在液、固两相重新分布的现象。
平衡结晶:
在结晶的每个阶段,固、液两相中的成分均能及时、充分扩散均匀,液、固相溶质成分完全达到平衡状态图对应温度的平衡成分。
2、试推导平衡结晶时的溶质再分配公式。
以下为等截面水平圆棒自左向右单向结晶过程分析。
假设:
合金原始成分为C0,界面前方为正温度梯度,界面以宏观平面形态向前推进。
结晶开始时,
结晶过程中,
平衡结晶下的溶质再分配规律
第九讲
1、A-B二元合金原始成分为C0=CB=2.5%,k0=0.2,mL=5,自左向右单向凝固,固相无扩散而液相仅有有限扩散(DL=3×10-5cm2/s),达到稳定态凝固时,求:
(1)固液界面的CS*和CL*;
(2)固液界面保持平整界面的条件。
(1)CS*=C0=2.5%,CL*=C0/k0=2.5%/0.2=12.5%
(2)固液界面保持平整界面的条件是成分过冷度△TC为0,成分过冷区宽度x0为0,即满足条件:
△TC=0,x0=0
则:
可得:
GL/R=5×2.5%×(1-0.2)/(3×10-5×0.2)
GL/R=1.67×104
2、根据右式分析有效溶质分配系数的三种情况。
①KE=K0(KE最小):
发生在
时,发生在慢生长速度和最大的搅动或对流情况下,这时δN很小,相当“液相充分混合均匀”的情况。
②KE=1(KE最大):
发生在
时,即快生长速度凝固、或没有任何对流,δN很大的情况下,相当于“液相只有有限扩散”的情况。
③K0<KE<1:
相当于液相部分混合(对流)的情况,工程实际中常在这一范围。
3、说明成分过冷与热过冷的联系与区别。
热过冷是仅由熔体实际温度分布所决定的过冷状态,成分过冷则是由溶质再分配导致界面前方熔体成分及其凝固温度发生变化而引起的过冷。
二者之间的根本区别是前者仅受传热过程控制,后者则同时受传热过程和传质过程制约。
如令成分过冷判别式中的C0=0,则成分过冷判据就变为热过冷判据。
因此,在晶体生长中,界面前方的热过冷只不过是成分过冷在C0=0时的一个特例而已,二者本质上是一样的。
成分过冷的本质:
由于固液界面前方溶质富集而引起溶质再分配,界面处溶质含量最高,离界面越远,溶质含量越低。
由结晶相图可知,固液界面前方理论凝固温度降低,实际温度和理论凝固温度之间就产生了一个附加温度差△T,即成分过冷度,这也是凝固的动力。
4、何谓成分过冷判据?
成分过冷的大小受哪些因素的影响?
“成分过冷”判据为:
当“液相只有有限扩散”时,
,代入上式后得
成分过冷的条件为
<
成分过冷的范围为△=
-
上式中,
为不变量,所以影响成分过冷范围的因素只有DL、GL和v。
对于纯金属和一部分单相合金的凝固,凝固的动力主要是热过冷,成分过冷范围对成形产品没什么大的影响;对于大部分合金的凝固来说,成分过冷范围越宽,得到成型产品性能越好。
(其中:
GL—液相中温度梯度,R—晶体生长速度,mL—液相线斜率,C0—原始成分浓度,DL—液相中溶质扩散系数,K0—平衡分配系数K)
5、根据共晶体两组成相的界面结构,共晶组织分为哪三类?
根据共晶体两组成相的界面结构不同,可将共晶合金分为三类;
1)粗糙-粗糙界面(非小晶面-非小晶面);
2)粗糙-光滑界面(非小晶面-小晶面);
3)光滑-光滑界面(小晶面-小晶面),多由不规则化合物组成。
6、根据共晶两相在结晶时的相互关系不同,共晶生长分为哪两种方式?
共生生长和离异生长
第10、11讲铸件的宏观组织
1、铸件典型晶粒组织包括哪几部分?
细小等轴晶柱状晶层粗大的等轴晶
2、如何在铸件中获得细等轴晶组织?
1)合理的浇注工艺
(1)合理降低浇注温度,减少柱状晶、获得细化等轴晶;
(2)设计合理的浇注方式,强化对流对模壁激冷晶的冲刷作用,促进细等轴晶的形成。
2)冷却条件的控制
需控制小的温度梯度和高的冷却速度,但就铸型能力而言,除薄壁铸件外,此二者不可兼得。
(1)对薄壁铸件,采用高蓄热、传导能力强的铸型细化晶粒;
(2)对厚壁铸件,采用冷却能力小的铸型以确保等轴晶的形成,同时辅以其他晶粒细化措施。
(3)采用悬浮铸造法,即在浇注过程中向液态金属中加入一定量的金属粉末,起显微激冷作用,加速液态金属的冷却,促进等轴晶的形成和细化。
3)孕育处理
向液态金属中添加少量物质,以达到细化晶粒、改善宏观组织的目的的工艺方法。
4)动力学细化
采用机械力或电磁力,引起固相和液相的相对运动,导致枝晶的破碎或与铸型分离,在液相中形成大量结晶核心,达到细化晶粒目的。
第12讲砂型铸造
1、试述砂型铸造的特点和应用范围。
1)砂型铸造的特点
①可以制造形状复杂的毛坯或零件;
②加工余量小,金属利用率高;
③适应性强,应用面广,用于制造常用金属及合金的铸铁件;
④铸件的成本低;
⑤铸件的晶粒比较粗大,组织疏松,常存在气孔、夹渣等铸造缺陷,机械性能比锻件差;
⑥铸造生产工序多,铸件质量不够稳定,废品率较高;
⑦铸件表面较粗糙,多用于制造毛坯。
2)适用范围
a、湿型砂(湿型):
单件或批量生产,尤其是大批量生产。
广泛用于铝合金、镁合金和铸铁件
b、干砂型(干型):
单件、小批生产品质要求较高,结构复杂的中、大型铸件
c、表面烘干型:
单件、小批生产中、大型铝合金铸件和铸铁件
d、自硬砂型:
单件或批量生产各类铸件,尤其是大、中型铸件
第13讲特种铸造
1、金属型铸造有何优点?
(1)机加工余量小
(2)冷却速度快,铸件晶粒较细
(3)一型多铸,提高生产率
(4)成本高,不宜大型,形状复杂和薄壁铸件
(5)铸件的精度和表面光洁度比砂型铸件高,而且质量和尺寸稳定
(6)铸件的工艺收得率高,液体金属耗量减少
2、熔模铸造的主要工艺过程包括哪些工序?
该方法有何特点?
工序:
制蜡膜-浸涂料-撒硅砂-硬化-成型壳-脱蜡-烘干-焙砂加固-浇注-去型壳-带浇冒口铸件-清理得铸件
特点:
(1)铸件精度高,表面质量好,属少,无切削工艺
(2)可铸造形状复杂铸件
(3)铸造合金种类不受限制
(4)生产批量不受限制,可单件或成批生产
(5)工序繁杂,生产周期长,原辅材料费用高,生产成本较高,铸件限于25kg
3、试述压力铸造、低压铸造与差压铸造各自的特点。
试分析三者的异同。
(1)压力铸造特点:
1.精度高
2.适应形状复杂、轮廓清晰、薄壁深腔铸件;可组合压铸或镶嵌压铸;
3.生产率高,少切削和零切削
(2)低压铸造特点
1.浇注压力和速度可调,适应各种铸型、合金和铸件大小;
2.平稳充型,无飞溅、气体卷入和型壁冲刷,铸件合格率提高;
3.压力下结晶,组织致密,轮廓清晰,表面光洁,少切削或零切削,机械性能高,对薄壁件铸造尤其有利;
4.节省补缩冒口,金属利用率高
5.劳动强度低,劳动条件好,容易数控自动化。
(3)差压铸造工艺特点
1.可获得最佳充型速度。
同时,型腔内有较高的反压力,不容易引起金属液喷射、飞溅,能平稳充型。
利于生产质量要求高的大型复杂件。
2.可调节压差,从而获得轮廓清晰、尺寸精确的铸件。
这对于生产薄壁铸件有利。
3.金属液在压力下结晶凝固,铸件组织致密,力学性能好。
4.可以实现控制气氛浇注。
可以控制金属液和铸型型腔上部气体分压,如能使有害气体分压趋于零,则可生产出有害气体含量非常低的铸件。
(4)相同点:
A、均是在压力作用下的铸造工艺
B、尺寸精度高
C、均对生产薄壁件有利
(5)不同点:
1)压力铸造可组合压铸或镶嵌压铸
2)低压铸造适应各种铸型、合金和铸件大小,节省补缩冒口且容易数控自动化
3)差压铸造可获得最佳充型速度和可实现控制气氛浇注
4、什么是离心铸造?
它有何优缺点?
它应用在什么场合?
离心铸造是指将熔融金属浇入旋转的铸型中,使液体金属在离心力作用下充填铸型并凝固成形的一种铸造方法。
优点:
(1)不用型芯即可铸出中空铸件,简化了套筒、管类铸件的生产过程。
(2)由于旋转时液体金属所产生的离心力作用,离心铸造可提高金属充填铸型的能力,因此一些流动性较差的合金和薄壁铸件都可用离心铸造法生产。
(3)由于离心力的作用,改善了补缩条件,气体和非金属夹杂物也易于自金属液中排出,产生缩孔、缩松、气孔和夹杂等缺陷的几率较小。
(4)无浇注系统和冒口,节约金属。
缺点:
1)内孔的尺寸不精确,质量也较差
2)铸件易产生成分偏析和密度偏析
应用:
铸铁管、汽缸套、铜套、双金属轴承、特殊钢的无缝管坯、造纸机滚筒等铸件的生产。
5、什么是实型铸造?
该方法有何特点?
又称消失模铸造:
采用聚苯乙烯发泡塑料模样代替普通模样,造好型后不取出模样就浇入金属液,在金属液的作用下,塑料模样燃烧、气化、消失,金属液取代原来塑料模所占据的空间位置,冷却凝固后获得所需铸件的铸造方法。
又称为无型腔铸造、气化模铸造。
实型铸造特点
(1)由于采用了遇金属液即气化的泡沫塑料模样,无需起模,无分型面,无型芯,因而无飞边毛刺,铸件的尺寸精度和表面粗糙度接近熔模铸造,但尺寸却可大于熔模铸造。
(2)各种形状复杂铸件的模样均可采用泡沫塑料模粘合,成形为整体,减少了加工装配时间,可降低铸件成本,也为铸件结构设计提供充分的自由度。
(3)简化了铸件生产工序,缩短了生产周期,使造型效率比砂型铸造提高2~5倍。
缺点:
实型铸造的模样只能使用一次,且泡沫塑料的密度小、强度低,模样易变形,影响铸件尺寸精度。
浇铸时模样产生的气体污染环境。
用途:
实型铸造主要用于不易起模等复杂铸件的批量及单件生产。
第14、15讲铸造工艺设计
1、为什么球磨铸铁的强度和塑性比灰铸铁高,而铸造性能比灰铸铁差?
①灰铸铁中的片状石墨的强度、硬度极低(Rm≤20MPa),塑性接近于零,因此灰铸铁的组织如同在钢的基体中分布着大量裂纹,同时石墨尖角处容易造成应力集中,容易导致铸件断裂。
所以灰铸铁的强度和塑韧性较差。
球墨铸铁通过球化处理使石墨呈球状,它对基体的缩减和割裂作用减至最低限度,基体强度的利用率可达70~90%,因此球墨铸铁具有比灰铸铁高得多的力学性能。
②因为灰铸铁的碳当量接近共晶成分,结晶温度范围小,并呈逐层凝固方式结晶,因而其流动性好,铸造性能好;而球墨铸铁的碳当量较高,一般是过共晶成分,结晶温度范围较宽,倾向于糊状凝固,在结晶后期外壳不坚固,不足以承受本身石墨化的膨胀压力,促使型腔扩大,故它比灰铸铁易于产生缩孔、缩松、皮下气孔、夹渣等缺陷,因而铸造性能比灰铸铁差。
2、铸钢与球墨铸铁的力学性能和铸造性能有哪些不同?
为什么?
①一般而言,铸钢具有较高的强度与塑韧性,其力学性能比铸铁好。
而球墨铸铁中的石墨呈球状,它对基体的缩减和割裂作用减至最低限度,基体强度的利用率可达70~90%,抗拉强度可以和钢媲美(Rm=400-900MPa),塑韧性较好(A=2%~18%)。
②铸钢的铸造性能比球墨铸铁差,因为:
其熔点高,钢液易氧化;流动性不好;收缩较大,体收缩率为10~14%,线收缩率为2.2~2.5%。
球墨铸铁结晶时由于石墨析出发生体积膨胀而可以抵消部分收缩,使总收缩较小。
3、为什么可锻铸铁只适宜生产薄壁小铸件?
壁厚过大易出现什么问题?
可锻铸铁具有较高的力学性能,其碳、硅含量低(WC=2.4~2.8%,WSi=0.4~1.4%),熔点较高,流动性差、收缩大,因为其铸态组织为白口(碳以化合态Fe3C存在),没有石墨化膨胀,极易形成缩孔和缩松缺陷,只适宜生产薄壁小铸件。
如果壁厚过大,易产生冷隔、浇不足、缩孔、缩松、裂纹等缺陷。
4、铸造铝合金和铜合金的熔炼工艺特点是什么?
各采取什么方法除气?
(1)铸造铝合金的熔炼工艺特点:
铝液在高温下极易吸气和氧化,熔炼时关键是除气去杂,以提高铝液的纯净度。
氢是铝合金中气体的主要来源。
在铝液出炉前要进行精炼。
在熔炼铝合金时,为改变其中共晶硅和初晶硅的形貌,提高铸件的力学性能,通常要对其进行变质处理。
常用钠或锶(亚共晶铝硅合金和共晶铝硅合金)或者磷(过共晶铝硅合金)作为变质剂。
铝合金熔炼一般多用坩埚炉。
铝合金熔炼时,除气的方法是向铝液中通入氯气或加入氯化锌、六氯乙烷等,形成大量Cl2、AlCl3等气泡,使铝液中的氢气扩散到气泡内,在其上浮过程中将铝液中的气体H2