水煤浆和粉煤气化变换事故案例.docx
《水煤浆和粉煤气化变换事故案例.docx》由会员分享,可在线阅读,更多相关《水煤浆和粉煤气化变换事故案例.docx(12页珍藏版)》请在冰豆网上搜索。
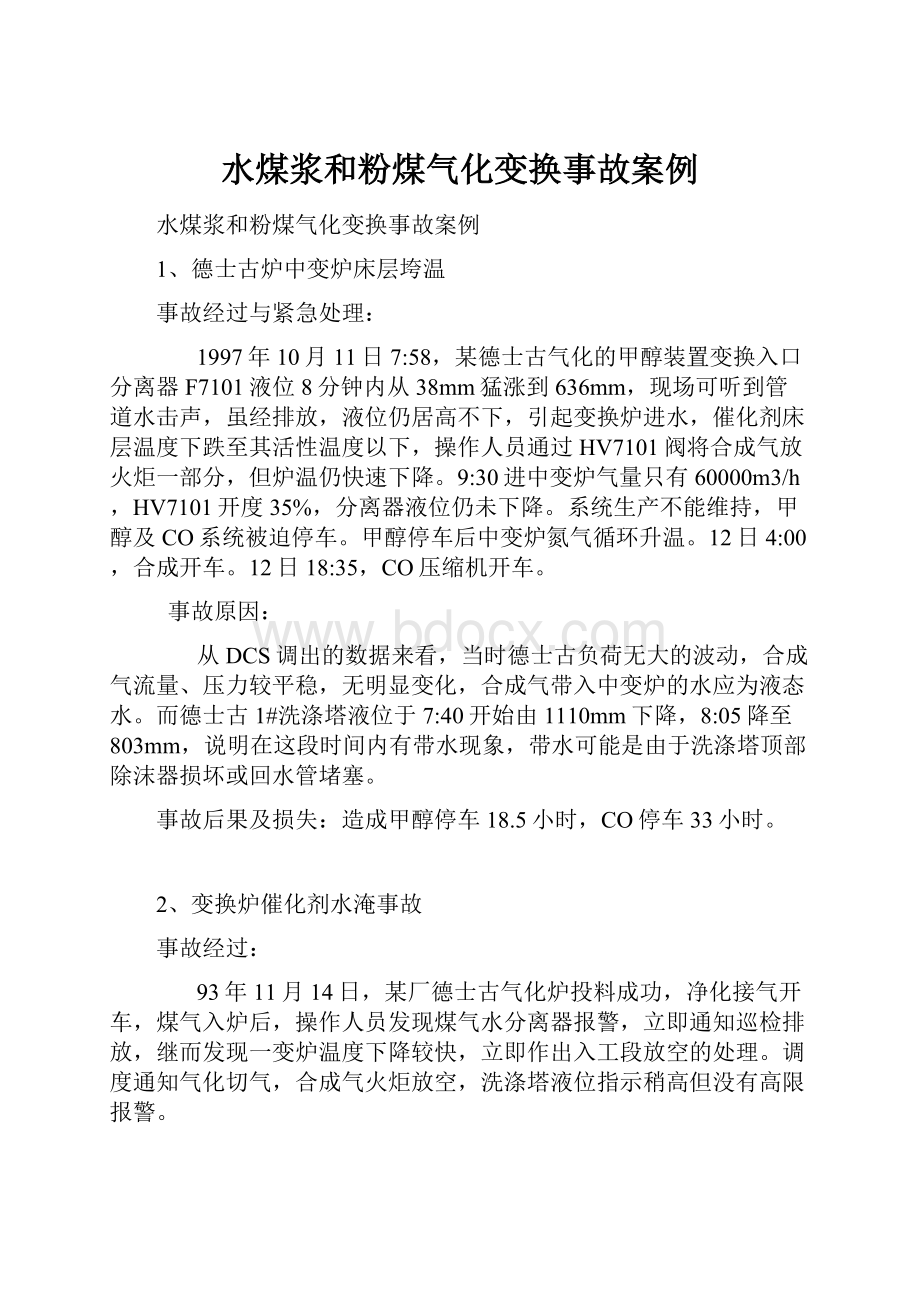
水煤浆和粉煤气化变换事故案例
水煤浆和粉煤气化变换事故案例
1、德士古炉中变炉床层垮温
事故经过与紧急处理:
1997年10月11日7:
58,某德士古气化的甲醇装置变换入口分离器F7101液位8分钟内从38mm猛涨到636mm,现场可听到管道水击声,虽经排放,液位仍居高不下,引起变换炉进水,催化剂床层温度下跌至其活性温度以下,操作人员通过HV7101阀将合成气放火炬一部分,但炉温仍快速下降。
9:
30进中变炉气量只有60000m3/h,HV7101开度35%,分离器液位仍未下降。
系统生产不能维持,甲醇及CO系统被迫停车。
甲醇停车后中变炉氮气循环升温。
12日4:
00,合成开车。
12日18:
35,CO压缩机开车。
事故原因:
从DCS调出的数据来看,当时德士古负荷无大的波动,合成气流量、压力较平稳,无明显变化,合成气带入中变炉的水应为液态水。
而德士古1#洗涤塔液位于7:
40开始由1110mm下降,8:
05降至803mm,说明在这段时间内有带水现象,带水可能是由于洗涤塔顶部除沫器损坏或回水管堵塞。
事故后果及损失:
造成甲醇停车18.5小时,CO停车33小时。
2、变换炉催化剂水淹事故
事故经过:
93年11月14日,某厂德士古气化炉投料成功,净化接气开车,煤气入炉后,操作人员发现煤气水分离器报警,立即通知巡检排放,继而发现一变炉温度下降较快,立即作出入工段放空的处理。
调度通知气化切气,合成气火炬放空,洗涤塔液位指示稍高但没有高限报警。
净化重新对变换系统升温后,接气生产。
15日14:
00再次发现煤汽水分离器报警,一变炉温度下降57℃。
立即进行紧急停车,气化切断了文丘里灰水及洗涤塔塔盘给水,洗涤塔液位仍无下降趋势,判定洗涤塔液位计误指示,后计算机重新组态洗涤塔压差,靠压差值判断塔的液位维持系统运行。
事故损失:
造成净化预变和一变催化剂被淹,活性下降,系统阻力增加,被迫停车三天。
事故原因:
①洗涤塔玻璃板液位计被黑水污染,无法现场判断液位高低;
②气化炉激冷环垢堵严重,激冷水无法加量,造成灰水补充联锁阀打开,洗涤塔循环泵打量很小;
③洗涤塔入高压闪蒸罐黑水管线堵,二次疏通后再次被堵,流量计取压管堵后得不到正确判断,造成洗涤塔无法排水;
④净化操作人员无处理该类事故的经验,未能及时切气停车,造成大量积水带入预变炉、一变炉,致使炉温较低。
事故教训和防范:
①德士古炉有停车机会时,需对其进行检查,重点检查水洗塔顶除沫器及回流管。
②杜绝气化车间洗涤塔液位高限操作,发现液位指示不准或不灵敏及时联系仪表进行调校处理;现场和中控定期校对液位计等仪表,最少每班一次。
③加强管理,提高操作人员责任心和业务水平及判断处理事故能力;
④气化和净化操作人员应精心操作,相互加强联系,遇到异常情况应及时向调度汇报。
⑤对气化车间“黑水管堵24小时停车的规定”重新修正;加强净化入工段分离器的排放,发现高限报警立即切气,入工段放空,待查明原因方可接气生产。
3、管道开裂事故
事故经过与紧急处理:
1995年9月11日17:
05,某厂德士古2#炉投料。
18:
30左右,合成气引入甲醇变换系统充压捉漏。
19:
00,发现变换废锅2进口合成气管线上焊缝泄漏。
19:
10,合成气退出变换系统。
9月12日1:
39,2#德士古炉也被迫停车。
9月16日,开启2.0MPa氮压机对变换系统充压查漏,发现PG7111、PG7112及PG7122三处管道焊缝漏。
事故原因:
设计的管道选材不对,在德士古合成气中温、中压、强还原气氛以及气液两相流条件下,304型不锈钢是不合适的。
事故后果及损失:
使德士古炉从9月11日至11月26日无法试车,并推延了甲醇开车时间。
经验教训及防范措施:
①变换管道材质更换为普通20#碳钢。
②对已更换的管道加强监测,定期侧壁厚。
镇海炼化公司化肥厂、乌鲁木齐石化总厂化肥厂和宁夏化工厂,分别于80 年代陆续从日本宇部兴产株式会社引进渣油为原料的1000 吨/ 日的合成氨生产装置。
在三个厂分别建成开车后的几年里,在4114(一氧化碳变换)工号管道先后多处发生应力腐蚀开裂,严重时因裂纹贯穿工艺气外泄而着火。
当时为了继续生产,对裂纹处进行了补焊加强,但不久即出现更严重的裂纹,最终都被迫停车更换管道。
经检查,发现三个厂发生开裂的管道都是材质为SUS321TP 的奥氏体不锈钢管道,后各厂陆续将变换管道换成15CrMo才避免了这种突发性管道焊缝开裂事件。
河南龙宇煤化工变换装置从2008年3月开始投运试生产,在试运行期间经过15次开停车,实际运行约10个月。
在2008年10月份的运行过程中,发现大量的焊接部位出现了严重的裂纹,开始出现煤气泄漏现象。
出现开裂的部位主要集中在可产生工艺液冷凝的焊缝附近,管子裂纹开裂长度约100mm,且裂纹平行于环焊缝,离环焊缝熔合线3~10mm,裂缝较为平直。
外裂纹两边无任何腐蚀现象,而内裂纹的四周则出现暗黑色,将裂纹打开以后,断口粗糙度呈冰糖状,断面呈黑暗色,靠内壁颜色深,外壁显现深褐色,表明开裂的时间不同,第一次裂纹扩展的厚度几乎占裂纹总厚度的一半左右。
由于变换304不锈钢管道开裂事件频发,该公司已将部分工艺气管道更换为15CrMo钢管道。
中原大化变换装置在出热交换器的变换气管线与AV管线相接以后的管线上,操作温度在300℃以上的弯头同样出现过开裂泄漏现象。
中原大化相关技术人员认为造成弯头开裂的原因主要是弯头质量问题,所以在对弯头检修更换时仍使用了304材质的弯头。
通过对304管线弯头开裂时间段的了解,在系统进行催化剂更换以后,由于不需要向煤气中补加过热蒸汽,变换炉的操作水汽比为0.3左右,这以后管线弯头才未再次发生开裂。
4、变换气提单元的腐蚀
新能凤凰变换汽提塔T2003材质为304,塔内件为304L,塔顶冷凝器E-21017材质为316L。
使用不到1年时间,发现塔顶上部有6层塔盘共计104个泡罩腐蚀较为严重,且上部的塔盘比下部的腐蚀严重,剩余14层塔盘完好无损;塔盘支承圈与塔内壁的焊缝有不同程度的开裂。
T2003与E2017中间部位约1500mm高的鲍尔环填料已逐步腐蚀粉化。
E2017管板与换热管的环向焊缝已被腐蚀,管头大部已经损坏,同时管口内壁出现分层现象。
从金属被破坏的特征分析,T2003与E2017的物料组分均没有强腐蚀性物质,是典型的局部腐蚀。
专家认为,湿H2S环境下,对于碳钢,主要腐蚀形式为腐蚀减薄、点蚀、坑蚀。
对于部分碳钢(含碳量高、沸腾钢、钢内杂质含量高等)、低合金钢、不锈钢主要腐蚀形式为腐蚀开裂。
5、CL-1、H2S湿环境下的管道腐蚀
开裂形式有4种:
a.氢鼓泡(HB)
b.氢致开裂(HIC)
c.硫化物应力腐蚀开裂(SSCC)
d.应力导向氢致开裂(SOHIC)
而在壳牌粉煤气化装置合成气中氯化物含量多于德士古,从而造成不锈钢管道氯化物应力腐蚀开裂(CISCC)。
其特点是管道内壁出现发散状裂纹,并沿晶间腐蚀,最终管道在毫无征兆的情况下开裂,造成合成气外泄。
6、变换废锅1列管漏,合成气串入0.8MPa蒸汽管网事故
时间:
1996.10.04
地点:
变换废锅1
事故性质:
设备事故
事故经过与紧急处理:
10月1日低压氮压机跳车后,2#德士古合成气走变换副线去一煤气新掺混。
10月4日,甲醇对界区内0.8MPa,0.45MPa蒸气管道进行捉漏。
当拆开合成界区0.8MPa至0.45MPa蒸汽减压阀法兰后发现0.8MPa蒸汽中混有煤气,经过检查,发现变换废锅1出口蒸汽中CO浓度很高,确认其列管内漏。
17:
10合成气退至德士古放空,17:
25德士古2#炉停车。
对废锅1进行检修。
事故原因:
变换废锅1有46根列管漏
事故后果及损失:
甲醇停车10天
经验教训及防范措施:
⑴对废锅1的46根列管进行补焊,试压合格后于10月9日复位
⑵变换开车进合成气后每个小时对废锅1出口蒸汽进行CO现场测试。
7、气换热器结垢,中变炉炉温提不上去,合成气大量放空事故
事故时间:
1996.09.15
事故地点:
变换中变气换热器
事故性质:
设备事故
事故经过与紧急处理:
随着变换系统运行时间的增加,其系统阻力也日益增大。
特别是从96年4月30日德士古开两台气化炉,甲醇满负荷运行后,变换阻力大的问题更加突出。
4月30日18:
20,二台德士古气化炉气量进入变换系统,变换系统阻力达到了0.56MPa,进中变炉合成气温度提不上去,炉温不能维持。
8月初,为配合醋酸厂试车,不得已打开HV7101,放散一部分煤气,约5000~10000m3/h。
这种情况一直持续到9月份,开二台德士古炉时,HV7101总有20%左右的开度。
9月15日,00:
25,35吨锅炉炉排轧死,联合循环压缩机停车。
停车后对中变气换热器进行了疏通清洗。
事故原因:
对中变气换热器拆检后发现,其列管结垢严重,影响了换热效果。
据计算,该换热器的K值已由设计的250降至40左右。
事故后果及损失:
造成在相当长的时间内,大量煤气放空。
经验教训及防范措施:
⑴用高压水清通中变气换热器。
⑵在日常操作过程中,德士古务必做到使合成气不带水,严格控制好分离罐液位。
甲醇操作人员也必须严格控制好入口分离器液位,不能使冷凝液带进中变气换热器和中变炉中。
⑶除尘过滤器F7102原来用的玻璃纤维过滤网长期在高温及酸性介质作用下严重粉化,随煤气带入中变气换热器中,以致使列管堵塞。
在9月份停车检修中,已换上了不锈钢丝网滤芯。
⑷除尘过滤器底部排水口增加分离罐。
⑸在进变换炉的煤气管道上增加若干排水装置。
8、15万甲醇变换爆燃烫伤事故
事故时间:
2005年8月23日
事故地点:
15万合成现场
事情经过:
2005年8月23日,上午8:
30左右经测爆合格后,作业区XXX通知三化建施工人员开始在15万变换废锅1上封头法兰管道打磨准备焊接,至12:
30因变换现场CS2要进行卸装,故作业区通知三化建人员停止打磨工作,CS2装好后,在16:
45左右经再次测爆合格后,XXX通知三化建人员继续打磨作业,17:
05打磨处管道突然发生爆燃,致使打磨人员张某烫伤。
事故主要原因:
因大修进度紧张,变换动火管道在工艺上未能用盲板做到有效的隔离。
事故直接原因:
大修现场统一指挥欠缺,400#净化系统冲氮升压时未考虑变换系统检修进度,变换动火在不知情的情况下继续作业,致使可燃气体从净化慢慢渗透至变换,积聚到一定浓度后遇明火发生爆燃。
防范措施:
⑴制定及完善系统检修规程,对于临时增设检修项目,必须按规定制定检修方案,检修项目负责人必须依照方案进行措施确认。
⑵检修现场设立指挥小组,统一组织指挥现场检修工作。
⑶在今后的检修、动火作业必须做到安全有效的隔离,“阀门不是有效切断的措施”形成制度执行。
⑷举一反三,在分公司内部组织学习,提高员工事故防范意识。
9、壳牌气化造成袋除尘器S1103B发生严重安全事故
事故描述
1.时间:
Dec.2009
2.地点:
SCGPLicensee 某客户
3.事故:
开车后3小时S1103B发生爆炸
4.当即措施:
紧急手动停车。
5.事故后果:
①布袋除尘器S1103B完全损坏
②大量煤粉抛向地面
③幸好现场无人,否则会发生伤亡。
6. 初步查证
①全场低压氮气与变换及制粉系统联通。
因为低压氮气与变换系统隔离不当,合成气导入变换系统后,合成气流入低压氮气系统,然后进入磨煤系统而导致布袋除尘器爆炸。
②低压氮气和变换系统之间未加盲板,仅靠单一阀门隔离。
③合成气进入布袋除尘器后,合成气里的氢、一氧化碳与煤粉及系统内的氧气形成爆炸物。
氢气易燃,其混和物的爆炸下限很低,煤粉输送系统很容易形成静电,很可能是静电火花点燃了可燃粉尘/气体爆炸物。
事故分类和分析
1.事故类别:
爆炸及资产损坏
2. 事故分级–高风险潜在风险:
人员4D,环境2D, 资产3C,声誉4D;实际:
无伤亡,环境1,资产3,声誉4
3. 直接原因:
①S1103B 变换装置里的合成气进入低压氮气系统后,又进入S1103B,与煤粉形成爆炸粉尘/气体混和物。
②固体输送形成的静电点燃了S1103B里的爆炸混和物。
4. 间接原因:
①低压氮气与变换系统的隔离未采用盲板或断开的方式,而仅仅依靠单一阀门。
②氮气消防系统根据测量到的布袋内的氧含量和一氧化碳含量的高低来决定氮气消防流量。
此次事故中,一氧化碳含量高,氮气消防流量增加,但此时消防系统送入的恰恰是导致火灾和爆炸事故的合成气,而非纯氮,导致事故升级。
主要教训
1. 所有阀门都存在内漏。
如果高压系统与低压系统相连,而仅用阀门隔离,高压介质会流向低压系统。
所以不能依靠阀门担当系统隔离。
建议采用断开的隔离方式。
2. 需要建立管理程序,当装置开车时,不用的系统需要可靠隔离,比如对于低压氮气系统,应拿掉短节,以确保与变换系统可靠隔离。
3. 防爆片的定值和安装非常重要,布袋除尘器气密要合格,根据不同煤种,氧量保持在8%或6%以下。
该系统也应考虑设置泻压阀。
4. 布袋除尘器区域是高风险区域,需要区域隔离。
需要考虑长期解决放案。
系统隔离标准参见下表:
隔离方式
示例
优点
缺点
1
断开
拆掉阀门或管段,敞口处加盲法兰
可靠
①工作量大,花费时间长
②因为可能损坏法兰面,投用前需要作气密试验
③每次需要更换垫片
2
盲板
①在隔离阀后加一块盲板
②在法兰之间加堵板
③八字盲板转到关闭位置
可靠
①工作量大,花费时间长
②因为可能损坏法兰面,投用前需要作气密试验
③每次需要更换垫片
3
双隔离阀
+排放阀
双截止阀关闭,中间导淋或排空阀开启,阀门上锁。
容易实施,
不会损坏法
兰面和垫片
①如果人员需要进入容器,而需隔离的介质是液态碳氢化合物/可燃气体/氮气/其他窒息性气体/有毒材料或腐蚀性化学品等,不可使用此种隔离方法
②如果任一个截止阀存在漏泄,这种隔离方法不得使用。
4
单阀
不推荐使用
如果存在火灾、爆炸、中毒和窒息等风险,一般要求使用物理断开或盲板隔离的系统隔离方式。
请勿忘记隔离马达和射源!
10、变换炉超温事故
2000年5月,某德士古气化的变换在原始开车的摸索过程中,曾经出现过一次由于将入变换炉水气控制太低,造成发生急剧的甲烷化反应,床层超温至802℃,系统被迫停车。
甲烷化反应是CO变换工序的副反应之一,该反应是强放热反应,每生成1%的CH4就会使床层产生60-70℃的温升!
引起床层温度暴涨,烧坏设备和催化剂。
该厂在2001年9月22日变换系统开车时,由于管网压力不稳,蒸汽压力在0.6MPa至0.3MPa之间波动,自调阀无法调节,造成入炉水气比随之波动,致使炉温超至700℃。
研究结果表明:
甲烷化副反应与床层热点温度、反应压力和原料气中CO含量密切有关,床层温度和反应压力越高,原料气中CO含量越高,水/气越小,发生甲烷化副反应的可能性就越大。
11、变换水冷器铵盐结晶堵塞
一、事故经过
2002年2月21日,某厂甲醇净化变换系统阻力突然上涨,阻力达到1.4MPa,系统被迫切气。
经停车检修发现变换气水冷器内部出现结晶物堵塞管路造成阻力增大。
后来将气体温度由25℃提到100℃使结晶物溶解、熔化后,阻力消失:
2004年3月同样因铵盐结晶造成变换阻力增大而被迫切气。
二、分析原因
水煤气中有NH3和N2的存在,同时变换炉内由于金属催化剂对N2和H2起催化剂作用,也会合成部分NH3,造成变换气体中氨含量较高,同时由于醇净化的部分变换工艺的主要特点是汽气比偏低冷凝液较少,所以冷凝液中铵盐浓度偏高,在温度较低时,铵盐结晶析出。
三、结晶部位
除变换气水冷器容易出现铵盐结晶导致系统停车外,开车后不久,还出现过汽提塔出口管道结晶堵塞,导致汽提塔超压至0.42MPa(设计0.2MPa,正常0.08Mpa)的现象,且居高不下,甚至开塔顶放空也无效,并时常因超压导致汽提塔顶部垫子漏气。
变换气分离器出口溶液自调阀及前后切断阀、导淋阀出现铵盐结晶,在冬季经常出现变换气分离器液位高限、出口自调卡没法调节的现象,严重时导淋也无法疏通。
四、处理对策:
增加冲洗线,定期对变换气水冷器及变换气水分离器进行清洗,在开停车时,变换气水冷器循环关死,将温度提至90℃维持1小时左右,基本上再没有出现此类问题。
对易结晶堵塞的部位、管线增加伴热,提高局部温度,减少碳铵的形成。