四种工艺原理及影响.docx
《四种工艺原理及影响.docx》由会员分享,可在线阅读,更多相关《四种工艺原理及影响.docx(11页珍藏版)》请在冰豆网上搜索。
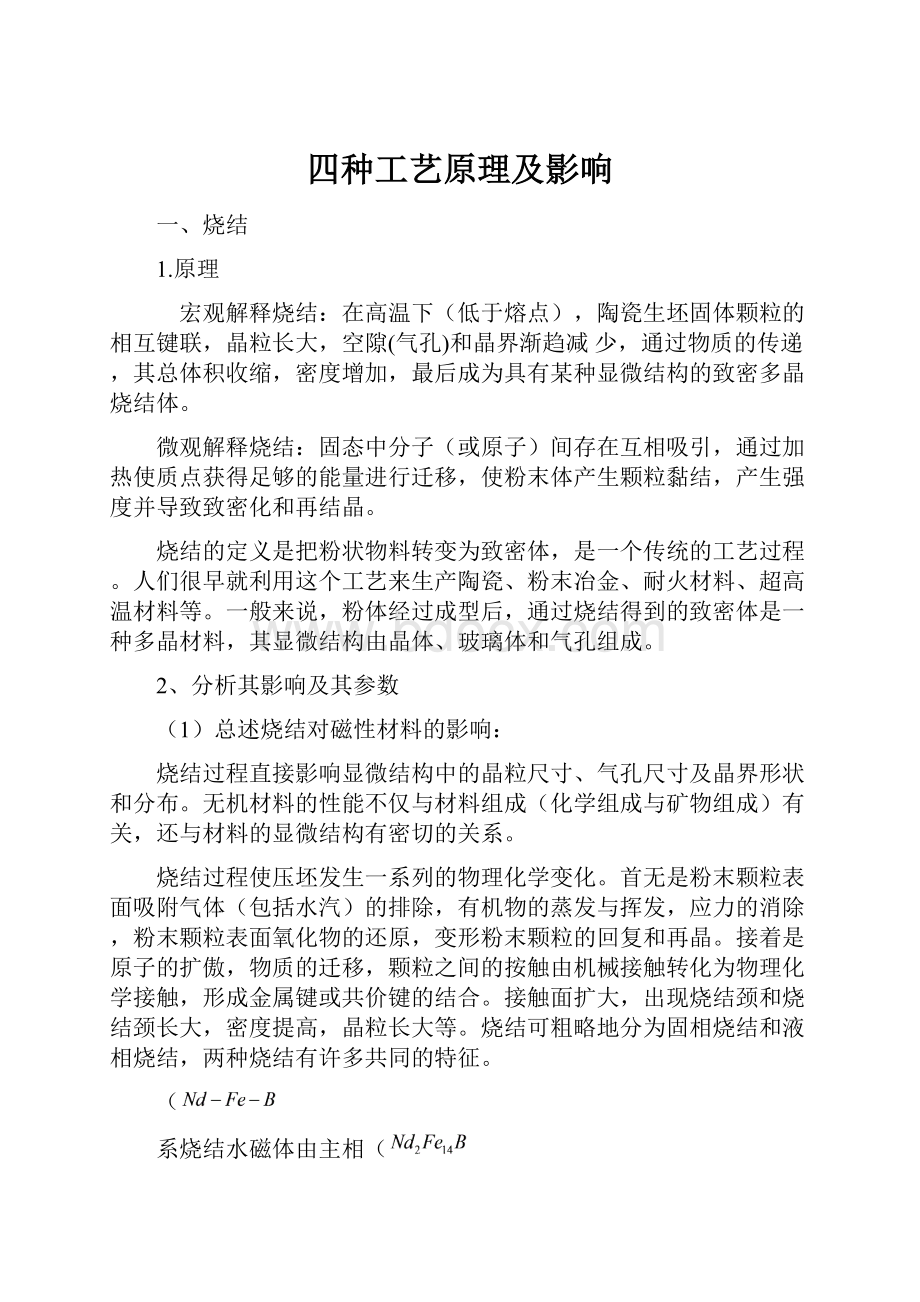
四种工艺原理及影响
一、烧结
1.原理
宏观解释烧结:
在高温下(低于熔点),陶瓷生坯固体颗粒的相互键联,晶粒长大,空隙(气孔)和晶界渐趋减少,通过物质的传递,其总体积收缩,密度增加,最后成为具有某种显微结构的致密多晶烧结体。
微观解释烧结:
固态中分子(或原子)间存在互相吸引,通过加热使质点获得足够的能量进行迁移,使粉末体产生颗粒黏结,产生强度并导致致密化和再结晶。
烧结的定义是把粉状物料转变为致密体,是一个传统的工艺过程。
人们很早就利用这个工艺来生产陶瓷、粉末冶金、耐火材料、超高温材料等。
一般来说,粉体经过成型后,通过烧结得到的致密体是一种多晶材料,其显微结构由晶体、玻璃体和气孔组成。
2、分析其影响及其参数
(1)总述烧结对磁性材料的影响:
烧结过程直接影响显微结构中的晶粒尺寸、气孔尺寸及晶界形状和分布。
无机材料的性能不仅与材料组成(化学组成与矿物组成)有关,还与材料的显微结构有密切的关系。
烧结过程使压坯发生一系列的物理化学变化。
首无是粉末颗粒表面吸附气体(包括水汽)的排除,有机物的蒸发与挥发,应力的消除,粉末颗粒表面氧化物的还原,变形粉末颗粒的回复和再晶。
接着是原子的扩傲,物质的迁移,颗粒之间的按触由机械接触转化为物理化学接触,形成金属键或共价键的结合。
接触面扩大,出现烧结颈和烧结颈长大,密度提高,晶粒长大等。
烧结可粗略地分为固相烧结和液相烧结,两种烧结有许多共同的特征。
(
系烧结水磁体由主相(
)、富Nd相和富B相组成的(
)。
主相熔点约为1185℃,而富Nd相的熔点为655℃(平衡态),
系磁体的烧结温度一般为1080℃左右。
在烧结温度下,合金系由固态的主相和熔化了的富Nd相组成。
在某一温度下,同时存在固相和液相的烧结称为液相烧结。
Nd-Fe-B系永磁体固相之间的烧结即是固相烧结。
)
(2)烧结导致的收缩和致密化的起因:
粉末压结体的孔隙率大,表面积大,表面能大,同时有晶格畸变能,使粉末压结体处于高能状态。
从能量牧态来看,它是不稳定的,具有自发地烧结与粘结成一个致密体的倾向和驱动力。
因此在一定温度条件下,即动力学条件允许的情况下,粉末颗粒之间的接触将由点到面,以便减少表面积和表面能,并随接触面积的扩大其结果是烧结体的收缩和致密化。
(3)就液相烧结过程影响的分析
三个阶段:
<1>液相生成与液相的流动;<2>溶解与析出;<3>固相烧结。
这三个阶段役有明显的界限,而是相互重叠交叉的。
在液相烧结时,当液相数量不足时,部分的固态粉末颗粒之间直接触,而成为固相烧结。
固相烧结过程可用双球模型作定性描述。
在烧结过程中,固相晶粒要逐步地长大,其长大机制为:
一方面是细小的颗粒溶解于液相中.尔后通过液相扩散、析出,在大颗粒表面上沉淀.使颗粒长大。
另一方面是通过固相晶粒边界迁移使烧结体致密化可用致密化系数a描述,a=(
)x100%其中
、
、
表烧结体、压结体、致密体理论密度。
液相烧结三个阶段致密化系
数的变化如图下图:
l一液相流动;2-溶解-析出;3-固相烧结
(4)烧结温度影响的分析
586K的吸热峰和
相的居点相对应,在该温度(TC)
相的原子磁矩由磁有序(铁磁性)转变为无序(顺磁性),困此吸收热量。
938K吸热峰是
三相共晶物熔化而吸收热
量。
1368K的吸热峰对应的是
两相共晶物熔化的温度。
1428K的吸热峰对应的是
相的熔点,即在该温度
相由固相转变为液相.烧结温度应低于该温度55~75K。
N35烧结永磁体在不同温度下烧结时,粉末烧结体的
。
和密度d随烧结时间的变化。
可见在1040℃烧结3h样品的Hit和凤均很低,接近零。
在1040℃到1080℃之间烧结,样品
均直线上升。
可见最佳烧结温度为1070一1080℃之间,在1100℃温度以上烧结,虽然样品密度继续提高,但Br、(BH)max没有明显的提高,而Hci反而降低。
估计它与晶粒长大有关。
粉末压结体分别在1030℃和1080℃烧结后的显微组织1030℃烧结的平均晶粒尺寸为4.6
,矫顽力为875.6。
在1080℃烧结3h后,平均晶粒尺寸为23
,矫顽力已降低到103。
总之,烧结温度过高,晶粒尺寸增加,矫顽力降低。
烧结温度的选摔与合金成分有关,当Nd含量校高时,或含育一定数量的轻稀土元索,如
等,烧结温度应适当降低。
磁体烧结后一般应快淬冷却,以保证获得高
所需的显微组织和为以后的回火处理准备良好显微组织条件。
二、氢破
1.原理:
是利用稀土材料具有吸氢特性,吸氢后发生膨胀,在膨胀的过程中,沿晶界断裂,从而达到破碎的目的。
钕铁硼氢破碎技术(HD):
HD法是一种在一定条件下物理化学破碎的方法。
2、分析其影响及其参数
(1)氢破的说明:
HD氢化粉碎法只适用于能氢化的金属或合金的粗破碎和中磨,进料尺寸100—0.1mm,出粉粒度:
10-1000
,对于储氢合金Ni-
电池负极材料所需粉末,此粒度已满足实用要求。
钕铁硼永磁体的粉末粒度应为3-5
,须气流磨细磨处理。
氢化破碎(HD)法是吸氢晶格膨胀及脱氢还原细化粒径,且吸氢或脱氢是可逆的化学反应过程,物理化学反应存在其化学成分及磁性的改变。
(2)氢破的过程对磁性物质的影响
NdFeB吸氢,生成的氢化物晶格膨胀,并生成热,化学过程;胀的内应力使NdFeB晶体产生裂纹变成疏松体为物理现象,两都同时进行;加温脱氢处理,大部分主相氢化物变回原来的Nd2Fe14B粉体,部份残留富Nd相氢化物需深度处理。
NdFeB的吸氢过程,最先吸氢的是露在表面的富Nd相,其次是主相Nd2Fe14B与H2发生反应,主相氢化物的形成伴随着放热反应,总的热量可以使反应物温度升高到300度。
晶格常数变大和热膨胀过程产生粉态炸裂,钕铁硼的HD粉末已经发生质变。
脱氢使
hy变成
,即将氢化物分解。
温度与压力的影响,650℃时,富Nd相变软熔化,继续升温发生HDDE反应,现在采用最佳脱氢温度是500℃,在此条件下,主相氢化物的氢全部放出,富钕相氢化物NdH3在500℃之后,脱了部份氢变成NdH2,1040℃可将氢从主相
完全排出。
<1>HD+JM(气流磨)的制粉效率提高2-3倍,达到90-100KG/HR(原来仅30KG/HR);接近NDFEB主相成分(RE=11.76at%)就力学性能而论,又硬又韧(Hv=530,抗弯强度24-26KG/mm2);
<2>有效降低磁粉的氧含量,HD氢化粉碎法有效地降低了磨粉工段的氧化程度((200-800)×10-O2 ),在烧结过程中有氢存在,可以还原钕的氧化物,净化晶界促进致密化,实现了部分的活化烧结。
<3>HD粉多沿晶界相开裂:
HD+JM粉末多呈单晶粒子,接近最佳粒子尺寸2-3UM,晶粒边沿均有富钕相,有效地提高IHC,实际上可以提高500-5000Oe.
<4>HD磁粉性能略有变异:
HD+JM粉末由于部分粉末以氧化物形态存在(Nd2Fe14BHxNdHy),其磁性变异呈现:
4πJs高,Br和IHC低的现象,磁性弱,脱模容易,外观整齐,堆放方便;
<5>HD粉末具有良好的抗氧化性:
HD+JM粉末具有较好的抗氧化性,保存时间较长,实践表明≥4UM的粉末在空气中不易燃烧;
<6>HD氧化粉碎法的负面作用和效果(主要对磁性材料):
HD+HM粉末表面楞角很多,在磁场取向和盛开过程中摩擦系数增大,使取向度降低导致Br降低,剩余磁感应强度Br降低;与同成分NDFEB合金机械制粉相比,HD+HM粉末减少了氧化,相对而言Nd(R)成分比同等的合金要高,非磁性相的增加也导致Br的降低;
烧结中脱氢和晶粒反常增大(AGG),HD+JM粉末中含氢量不同,最终在烧结过程中才能脱尽。
在升温过程中还会出现开裂,真空度不高而出现氧化,氮化等现象,原因在于混料烧结,设备不适应,升温不正确所至。
HD+JM粉末中含氢而且粉末细(~3μm)在一般制度下很容易发生晶粒超常增大的问题(矫顽力HC大幅度降低),解决方法:
降低烧结温度由1060度降到960度,添加晶粒抵制剂。
如果采用HD+JM粉末制作磁体与相同成分机械粉末磁体相比较,结果Br,Hk/Hci都化用机械制粉的磁体低。
原因在于Pr-Fe-B合金的氢化物PrFeBHx的易磁化轴由C轴变成A面,在磁取向时发生错位,当完成烧结后,易磁化轴由A面变成C轴了,这就出现Br,Hk/Hci都低的,只要不含Pr的Nd-Fe-B磁体都不会出现这种现象。
尾粉是大颗粒出现的原因,导出尾粉的唯一方式,即停止分级轮的转动,让粉碎室的摒弃将尾粉吹出,从旋风集粉器收集的尾粉粒度不同,批量不大,不好处理,是有存放待以后集中处理。
尾粉收集并不完全,其中许多大颗粒会阻留在所经过的管道中,待到下一次磨粉机运行时,新的强大粉流可能把以前阻留在管道中的大颗粒尾粉卷入到旋风集粉器中,新粉料中混入了大颗粒,这就是大颗粒的污染问题,导致下次制备磁性材料性能下降,当然还有超细粉带来危害。
三、等静压
1、原理
等静压工作原理为帕斯卡定律:
“在密闭容器内的介质(液体或气体)压强,可以向各个方向均等地传递。
”等静压技术已有70多年的历史,初期主要应用于粉末冶金的粉体成型;近20年来,等静压技术已广泛应用于陶瓷铸造、原子能、工具制造、塑料、超高压食品灭菌和石墨、陶瓷、永磁体、高压电磁瓷瓶、生物药物制备、食品保鲜、高性能材料、军工等领域。
等领域。
等静压技术是一种利用密闭高压容器内制品在各向均等的超高压压力状态下成型的超高压液压先进设备。
2、分析等静压技术对材料影响
等静压技术按成型和固结时的温度高低,分为冷等静压、温等静压、热等静压三种不同类型。
(1)三种技术的影响或参数:
冷等静压技术
冷等静压技术,(ColdIsostaticPressing,简称CIP)
是在常温下,通常用橡胶或塑料作包套模具材料,以液体为压力介质主要用于粉体材料成型,为进一步烧结,煅造或热等静压工序提供坯体。
一般使用压力为100~630MPa。
温等静压技术
温等静压技术,压制温度一般在80~120℃下.也有在250~450℃下,使用特殊的液体或气体传递压力,使用压力为300MPa左右。
主要用于粉体物料在室温条件下不能成型的石墨、聚酰胺橡胶材料等。
以使能在升高的温度下获得坚实的坯体。
热等静压技术
热等静压技术(hotisostaticpressing,简称HIP)
HIP,是一种在高温和高压同时作用下,使物料经受等静压的工艺技术,它不仅用于粉末体的固结.睫传统粉末冶金工艺成型与烧结两步作业一并完成.而且还用于工件的扩散粘结,铸件缺陷的消除,复杂形状零件的制作等。
在热等静压中,一般采用氩、氨等惰性气体作压力传递介质,包套材料通常用金属或玻璃。
工作温度一般为1000~2200℃,工作压力常为100~200MPa。
与常规成型技术相比特点
等静压技术作为一种成型工艺,与常规成型技术相比,具有以下特点:
a.等静压成型的制品密度高,一般要比单向和双向模压成型高5~l5%,热等静压制品相对密度可达98%~99.09%。
b.压坯的密度均匀一致。
在摸压成型中,无论是单向、还是双向压制,都会出现压坯密度分布不均现象。
这种密度的变化在压制复杂形状制品时,往往可达到10%以上。
这是由于粉料与钢模之间的摩擦阻力造成的。
等静压流体介质传递压力,在各方向上相等。
包套与粉料受压缩大体一致,粉料与包套无相对运动,它们之间的摩擦阻力很少,压力只有轻微地下降,这种密度下降梯度一般只有1%以下,因此,可认为坯体密度是均匀的。
c.所以制作长径比可不受限制,这就有利于生产棒状、管状细而长的产品。
d.等静压成型工艺,一般不需要在粉料中添加润滑剂,这样既减少了对制品的污染,又简化了制造工序。
四、速凝
1.原理
熔体快淬法制备NdFeB薄带有双辊法和单辊法两种。
单辊法真空快淬法的生产设备如图4—16所示。
感应困将在石英坩埚内的NdFeB母合金加热熔化成为熔体,通过气阀调节氮气压力将熔体从坩埚下端的窄缝直接喷射到高速转动的紫铜辊的表面。
紫铜辊可通冷却液冷却,或利用其自身的良导热性质,将喷射到其表面的合金液体以
一
℃/s速度冷却。
在紫铜辊直径和温度为一定的条件下,紫铜辊的转速(r/min)或表面线速度(m/s)与其冷却速度(℃/s)成正比。
用单辊法制备的NdFeB薄带的厚度为30一80
,宽度为1—3mm,长度取决于坩埚的熔量。
在传统的金属模铸锭工艺中,减薄铸锭厚度可有效地细化晶粒尺寸。
但由于铸锭心部与表面的冷却条件有很大差别,对于NdFeB合金仍难以消除
Fe的析出。
而消除合金中的
Fe是获得高性能烧结NdFeB磁体的重要手段。
为此,1995年Yanmamoto等人开发了所谓的速凝铸造工艺。
速凝铸造工艺的基本原理与快淬法相似,它是将合金熔体浇铸到具有一定转速的水冷铜辊
℃/s的冷速下形成厚度在0.03—10mm范围内的合金薄片。
2、分析其影响及参数
(1)两种铸锭的显微组织来总结速凝的一般影响:
Hirose等人比较了质量分数为30.5%Nd-68.5%Fe-1.0%B的合金铸锭与鳞片铸锭的显微组织。
图中a是水冷铜模铸锭(冷却方向的厚度为30mm)的SEM的背散射电子像,黑色相为树枝状
Fe,白色相团块状的富钕相,基体是
相,显微组织十分均匀。
经1050℃退火4h后,
Fe的数量有所减少,但富钕相聚集长大,如图中b所示。
图中c是相同成分的合金用速凝法制备的鳞片铸锭的显微组织,可见仅有少量的
Fe,富钕相沿2:
14:
1相的片状晶界分布均匀。
2:
14:
1相片状晶厚度约为5—8
,图中d表明,2:
14:
1相的校状晶内部有若干个片状晶,柱状晶短轴方向的尺寸约20一30
。
工艺的基本参数为:
水冷纯钢辊轮直径为400mm,辊表面线速度为1m/s,合金在
坩埚中熔化,合金液温度达到1450℃并在中间包中也保持该温度进行浇铸,冷却速度约为2.5×
℃/s,获得厚约0.3mm、宽几十毫米的鳞片。
鳞片离开辊面的温度约750一600℃,随后的冷却速度约0.5℃/s。
速凝工艺制备的鳞片铸锭,经过HD处理和气流磨制粉,已用于制备向性能NdFeB烧结磁体。
金相观察表明,用速凝鳞片制备的烧结磁体晶粒细小均匀.主相晶粒小于10
的占96%,而大于13
的仅占1%;而常规烷结磁体的品粒则大得多,主相晶粒小于10
的占64%,大于13
的占17%。
但速凝鳞片需在900℃左右热处理,以使主相成分和富钕相成分接近正分成分,才能提高烧结磁体的磁性能。
此外,速凝鳞片中存在2—3
以下的磁晶,应先采用氢爆工艺使这些碎晶分离成单晶颗粒,在随后的制粉过程中
才容易得到粒度均匀的粉末,提高磁粉的取向度。
(2)现在速凝的基本影响和一些参数:
目前,国外工业化生产水平的速凝工艺磁体,
已超过414
,实验室水平
已达到45l
。
当铸锭冷却速度足够快对,例如当铸锭的冷却速度为1000℃/时,
初次晶被抑制,包晶转变也被抑制,而直接从合金液中结晶出
。
随后的结晶过程与前者相同。
铸锭冷却是一个形核长大的过程,在结晶过程中,形核率越大,将有更多的晶核同时增长,这样得到的片状晶尺寸会更细小。
凝固过程的形核率I可有表达式中有临界尺寸晶胚的自由能;有液态原子扩散激活能,有玻耳兹曼常数;有绝热温度。
对某一特定的合金来说,是一个常数。
表达式表明,形核率由两个指数项来决定,第一项与晶胚数有关,第二项与原子扩散有关,因此它们随温度而变化。
所示中Tin为合金的熔点。
当过冷度较小时,需要的形核功较高,形核速率较小,当过冷度增加形核率随之增加;但当过冷度太大时,由于原子扩散困难,而使形核率减小。
中I。
为最大的形核率,相应的温度为TC。
可见获得最大形核率的过冷度为
C=I0一TC。
为获得Nd,Fe,B合金铸锭组织的细小片状晶,应控制浇注时的过冷度,并与该
C相对应。