数字化装配.docx
《数字化装配.docx》由会员分享,可在线阅读,更多相关《数字化装配.docx(23页珍藏版)》请在冰豆网上搜索。
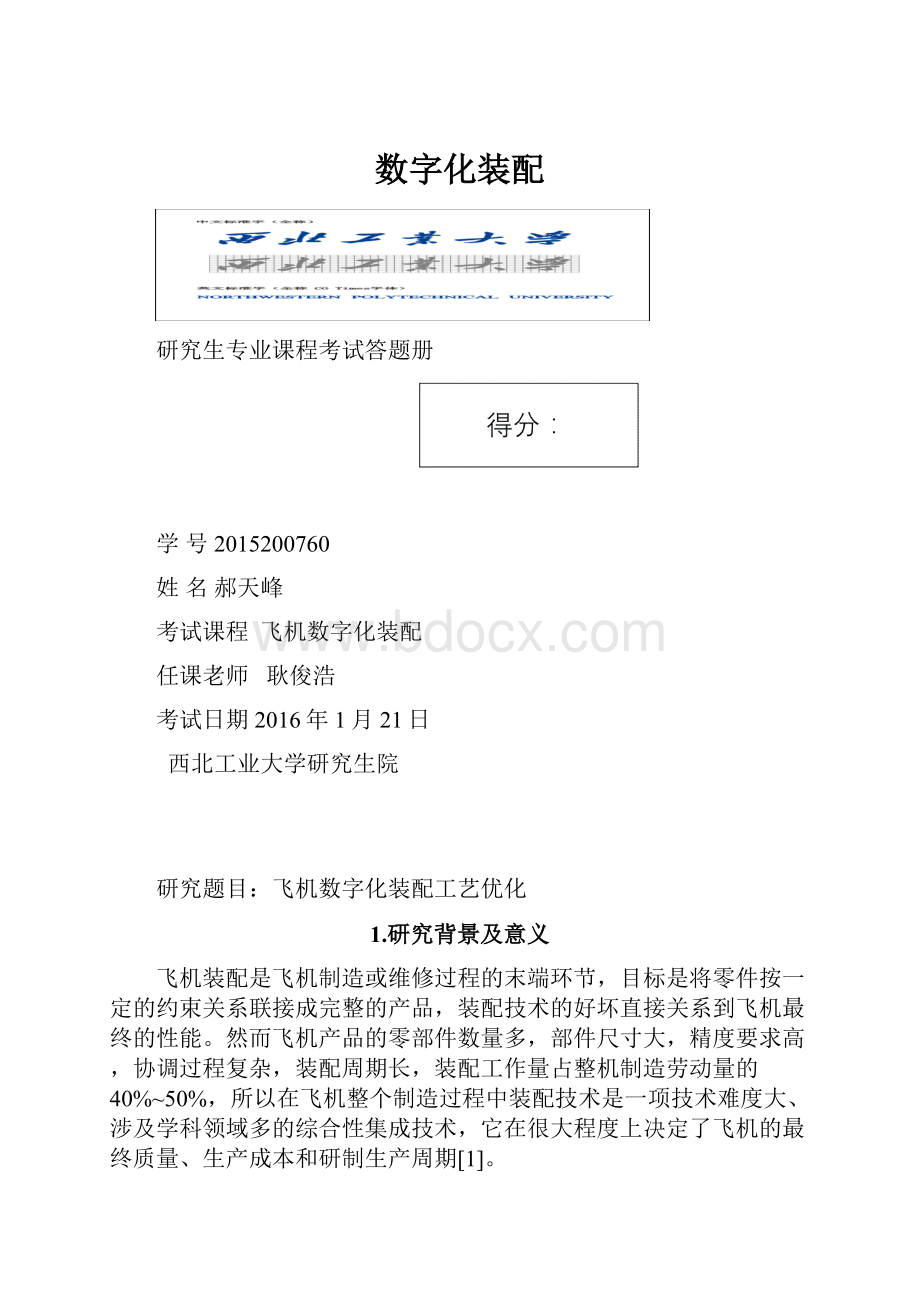
数字化装配
研究生专业课程考试答题册
学号2015200760
姓名郝天峰
考试课程飞机数字化装配
任课老师耿俊浩
考试日期2016年1月21日
西北工业大学研究生院
研究题目:
飞机数字化装配工艺优化
1.研究背景及意义
飞机装配是飞机制造或维修过程的末端环节,目标是将零件按一定的约束关系联接成完整的产品,装配技术的好坏直接关系到飞机最终的性能。
然而飞机产品的零部件数量多,部件尺寸大,精度要求高,协调过程复杂,装配周期长,装配工作量占整机制造劳动量的40%~50%,所以在飞机整个制造过程中装配技术是一项技术难度大、涉及学科领域多的综合性集成技术,它在很大程度上决定了飞机的最终质量、生产成本和研制生产周期[1]。
虽然国内外目前的CAD/CAM软件发展己经口益成熟,然而其飞机装配工艺设计分析能力尚不足以应付快速发展的生产实际需要。
传统的装配分析需要耗费大量的物力、人力和时间来生产物理样机进行实验,而这不仅导致装配工艺设计严重滞后于飞机设计工作,相较于并行设计,耗费过多时间,而且无法及时发现并弥补飞机装配设计中的缺陷,更无法保证工人的安全舒适性,这种传统的装配分析方法受物理样机限制存在诸多弊端,因此需要采用新的技术方法来满足产品并行设计的要求,使设计人员在产品设计阶段就能进行装配设计与验证工作。
在这样的背景环境下数字化装配技术应运而生,为飞机设计和装配性能评价提供了一个新途径[2]。
数字化装配的定义为:
利用数字化现实技术、计算机图形学、人工智能技术和仿真技术等构造数字化现实环境和产品数字模型,从而在产品装配过程中通过交互分析,仿真装配过程和装配结果。
数字化装配的主要研究内容包括:
数字化环境下零件、产品建模及装配过程建模,装配序列和装配路径规划,装配中物理特性的分析研究,装配过程的人机工程学分析,装配系统与其它相关系统(如设计系统)的集成。
与传统CAD装配相比,数字化装配的重点在于直观的人机交互,通过直接操作和自然命令完成装配操作。
它不仅能检验、评价以及预测产品的可装配性,并且能够面向装配过程提供直观经济的规划方法[3]。
随着数字样机、虚拟现实等技术的发展以及各种算法的成熟研究,在数字化环境下模拟装配工作,进而结合各种算法对装配问题进行优化已成为一种重要设计和分析手段。
在构建的数字化仿真环境中,导入产品数字样机和人体模型,并根据产品特征制定装配工艺,完全可以实现“虚拟人装配虚拟产品”的数字化装配仿真,而且可以在装配仿真基础上进行装配工艺分析和人机工效分析等,从而及时发现和修改产品装配中存在的问题,从而实现产品的并行设计,辅助现实产品装配过程[4];进而针对具体的装配问题结合已知算法进行优化,从而提高飞机的装配性,缩短飞机装配周期,节约飞机装配成本,提高飞机装配精度,具有广阔的应用前景。
2.国内外研究现状
2.1飞机数字化装配现状
国外:
美国波音公司在研制波音777的过程中,运用并行工程的思想,实现三维数字化装配过程仿真,同时结合装配自动化技术、先进定位技术和简易型架装配技术,使产品开发周期缩短了40%~60%,制造成本也降低30%~40%[5]。
飞机的设计过程中没有使用一张图纸,全部都在计算机中模拟完成。
波音777通过飞机数字化装配仿真和自动装配,提高了零部件的装配准确度,使用预装配技术,使波音777的地板梁装配时间由19周减少到3周,减少了设计变更,缩短了工艺规划时间,装配周期缩短50%,工艺设计周期缩短30%~50%[6]。
洛克希德马丁公司在研制JSF战斗机X-35过程中明确提出采用数字化装配技术,要使JSF飞机装配制造过程的周期缩短67%,工装减少95%,制造成本降低50%。
空客公司在飞机研制过程中通过实施数字化设计与制造技术,把产品的试制周期从4年缩短为2.5年[7]。
葡萄牙波尔图大学创建基于感知的虚拟装配系统(Haptic-basedVirtualAssemblySystem,HVAS),基于物理建模和触觉反馈进行模拟现实的装配作业[8]。
图2-1基于感知的虚拟装配系统组成[8]
国内:
沈飞公司研究了基于CATIA的装配工装设计及数字化安装技术,并在飞机装配工装的制造中采用了激光跟踪仪;西北工业大学、南京航空航天大学及北京航空航天大学在飞机数字化预装配技术、基于激光跟踪定位的部件对接柔性装配技术、飞机数字化协调、飞机数字化装配定位、飞机数字化装配定位自动控制技术等方面做了一定研究,并不同程度的应用到飞机装配中[9]。
浙江大学万华根等开发的VDVAS(virtualdesignandvirtualassemblysystem)集成了虚拟设计与数字化装配过程,使用者能在统一的虚拟环境中运用三维操作和语音命令建立零件及其装配模型,并通过交互拆装得到装配的顺序和路径[10]。
2.2飞机数字化装配工艺优化现状
数字化装配工艺优化主要包括:
装配零部件建模及装配过程建模、装配序列优化、装配路径规划、装配容差优化、装配生产线调度优化等等方面。
国外:
MichelleBezdecny等人通过建立三维偏差分析模型对飞机装配容差进行仿真预测,并通过分析各个影响因素的敏感度,优化装配容差,改进飞机设计方案[11];Tonshoff等提出了知识求解法,该方法将典型工艺过程、零部件属性、联接方法和技术功能对装配优先关系的影响以规则的形式存储在知识库中,利用知识库中的规则确定零件的装配序列。
J.Butterfield、S.Crosby等人运用数字化飞机装配仿真技术对飞机机身装配进行了优化,对装配中的干涉进行了改进,使得车间绩效增加了一倍,机身装配所需的实际工作时间低于预期水平[12]。
图2-2飞机机身装配干涉[12]
国内:
张卫红等提出基于遗传算法的飞机工装结构优化方法;江善元等提出基于遗传算法的飞机装配工装多模型、多工况、多离散变量的优化设计方法。
2012年华中科技大学华菲菲、朱海平等建立了飞机装配作业的多级网络计划模型,利用粒子群算法对飞机尾翼装配和襟副翼装配作业调度进行了优化,求解得到一个有限资源条件下的工期最短的较合理的车间作业计划[13]。
图2-5飞机尾翼和襟副翼装配任务及相关参数[13]
图2-6并行装配网络计划图[13]
图2-7最优装配车间调度方案[13]
2010年西工大邱晞、魏生民等提出了一种基于空间扫略的飞机产品装配路径规划方法,并且通过对装配干涉阈值的定义和优化调整,完成对飞机装配路径的优化。
并以某型飞机前缘襟翼架装配为实例,针对其蒙皮装配进行路径规划与优化[14]。
图2-8某型飞机外襟翼前缘架装配[14]
图2-9蒙皮装配规划及优化路径[14]
3.研究内容
进行飞机维修装配的优化,可以对工装、装配容差、拆装序列、路径等等许多问题进行优化,本文则是对以下总结出来三个主要的拆装子问题进行优化:
装配序列规划(AssemblySequencePlanning)、装配生产线调度规划(AssemblyLineBalancing)、装配路径规划(AssemblyPathPlanning)。
图3-1飞机维修装配优化子问题[15]
(1)飞机装配序列优化
飞机产品装配序列优化很重要,直接影响到飞机装配时间和成本。
装配序列规划问题就是在装配飞机时,探索合理可行的装配序列,并从中选取最优或次最优的序列,以指导飞机产品的装配,达到预期的装配目标,装配序列规划问题实际上是一个组合优化问题。
要研究装配序列进行优化,首先要研究装配序列的生成及表达。
装配序列的生成,通常根据装配建模推理来生成装配序列,而装配序列模型表达方式大致分为三种:
基于语言的表达;基于图表的表达;基于数据结构的表达。
在这三种表达方式中,基于图的表达方法比较普遍。
最后装配序列在生成以后,根据实际需要结合相关优化算法对装配序列进行优化以满足工程的需求。
通常利用目标函数的值来量化的评价装配序列的合理性,装配序列优化过程中目标函数有:
最小装配成本和最小装配工具更换次数、最小装配方向的改变次数等[16]。
(2)飞机装配生产线调度优化
飞机装配过程是一个复杂的过程,作业数量多,工作量大,不仅存在由作业优先关系产生的作业顺序约束,还存在由于共享资源产生的资源约束以及作业空间限制带来的空间约束。
研究飞机装配生产线作业调度优化问题,对飞机装配作业进行调度安排,合理安排每项作业的开始时间和结束时间,分配工作人员、装配工装工具等装配资源具有重要的现实意义[17]。
要研究飞机装配生产线调度优化,首先要研究装配生产线调度建模,比较常用的有基于数学公式建模和基于图形建模,然后根据实际需要结合相关优化算法对装配生产线调度进行优化以满足工程的需求。
通常利用目标函数的值来量化的评价装配生产线调度的合理性,装配生产线调度优化过程中目标函数有:
最小装配时间、最小装配工位等。
(3)飞机装配拆卸路径优化
装配路径规划与优化是在产品装配建模、工装建模和装配序列规划的基础上,通过对装配过程进行分析和求解,生成零部件从初始位置装配到目标位置所经过的无干涉碰撞且相对最优的路径。
对于飞机产品而言,由于其零件的数量大,结构复杂,相互间存在协调关系,为保证其装配要求,在装配过程中必须大量地使用装配工装、夹具等装配资源,完成对零件的装夹、定位、连接等操作工装夹具的大量引入,占据大量的装配空间,无形中提高了装配路径规划的复杂度,飞机产品装配路径规划已成为装配工艺规划中的主要难点之一
飞机装配路径生成规划方法主要有:
人工势场法,该方法将装配零部件在装配空间中的运动抽象成在引力场中的运动,障碍物对装配零部件有斥力,目标位置对装配零部件有引力,最终促使装配零部件绕过障碍物到达目标位置;可视图法,该方法是从球面图法中总结出的空间方位求解方法,把零部件通过装配空间中的障碍物的问题转化为等价的点通过放大的空间障碍物问题;虚拟装配法,该方法是基于虛拟现实技术的装配路径规划技术,它可通过参数化CAD系统与虚拟装配环境进行交互操作、信息交换和共享等[18]。
4.拟采取的研究方案及可行性分析
上述三个飞机装配子问题优化具体的研究方案可以分为飞机装配建模,然后根据建立的模型结合算法或结合一些规划方法进行优化,进行可行性分析往往是将优化后的结果与优化前的结果进行比较得出结论。
4.1飞机装配建模
图4-1飞机装配优化问题[15]
飞机装配问题本身具有以下的性质:
1)装配零部件的个数;2)规模:
总体装配还是特定某部件装配;3)单调性:
装配串行还是并行进行;4)顺序性:
装配过程中是否有一定的顺序性;5)线性:
零部件一个个依次地从其他装配体中拆除或装上则是具有线性。
根据飞机装配性质进行建模,要考虑以下几点:
1)维度:
飞机装配模型是2D的数学模型、图形模型等,还是3D模型;2)装配约束:
包括几何约束、物理约束、机械约束等;3)运动方式:
平移、旋转、螺旋等;4)零部件几何参数:
装配容差、变形等;5)装配资源:
装配工装工具、装配人员等(考虑人的因素,往往可以进行人因工效分析);6)优化目标函数:
最短时间、最短路径、最小代价花费等。
4.2常见的飞机装配模型
(1)数学模型
数学模型往往是根据一些数学公式,或是装配问题之间存在的数学关系来构建数学模型,可以用于装配生产线调度的优化。
如2014年中国人民解放军4724工厂的孙东余等以最短时间为优化目标函数,根据约束条件建立了大修总装的维修模型[19]。
仅仅已知高级工和初级工数量,以及大修每步消耗的准备和实施时间,可以表示出大修每步的约束条件和目标函数,完成飞机大修总装模型的构建。
图4-2飞机大修总装模型[19]
(2)图形模型
产品装配模型构建最常见的便是图形模型,主要有无向图、有向图、混合图、拆卸Petri网、拆卸矩阵、与或图等方法,这些建模方法中无向图、有向图、与或图是最基本的方法,它们是基于图论的,而混合图是无向图与有向图的结合,其中拆卸矩阵和拆卸Petri网一般是在无向图、有向图和与或图为基础上发展起来的方法。
1)与或图
装配过程建模方法中最为常用方法就是建立产品的拆卸AND/OR图,然后通过相应的算法来求解。
每一级的零件个数依级数递减,同级之间是相与的关系,上一级可以分解为下一级和最后一级中某个组合。
然而,一旦零部件过多,会形成与或图爆炸[20]。
图4-3装配与或图的直接生成示例[20]
2)装配约束图
装配约束图是一种结合有向图和无向图的混合图,节点代表零件或对于装配来说是不能再被分解的子装配体也被称为最小装配单元。
识别阻止最小拆卸单元之间被拆除的几何约束,用无向边连接两个相应节点来代表零部件之间的接触约束;接着识别节点之间的装配优先级信息,通过前驱节点指向后续节点的有向边来表示非接触约束[21]。
图4-4某飞机起落架及其装配约束图
3)Petri网
Petri网因具有完整的数学描述和强大的推理过程建模能力而在维修装配建模领域得到广泛应用。
例如Petri网能表达系统的结构和动态行为,且能将知识的表示和推理融于一体,可以用于维修知识表达和推理;Petri网用于分解与装配序列规划一般可分为几何优先关系的建模和分解装配序列的生成与优化;Petri网是基于状态的建模方法,其演进过程受状态驱动,在描述能力上优于基于事件的建模方法,且Petri网具有强大的分析技术和手段可以辅助工作流的验证;Petri网除具有并发、动态、直观等优点外,还能够准确快速的反映制造系统实时调度的离散性与随机性等,所以与其他方法相结合在调度问题中得到了广泛的应用。
哈尔滨工业大学的唐新民等针对飞机发动机涡轮转子维修过程,进行基于自由选择Petri网的分解装配序列规划等研究[22]。
图4-5飞机发动机涡轮转子装配工艺系统图[22]
图4-6发动机涡轮转子装配Petri网[22]
(3)3维装配优化模型
3D优化模型并不是很常见,但是更加立体形象,例如在用快速扩展随机树来优化装配路径时,确定目标的起始位置与目标位置,通过在三维空间中的随机采样过程,确定搜索树的伸展方向。
在树的生长过程中,通过限制生长的步长以及与环境中障碍物的碰撞干涉检测,逐步接近目标位置[23]。
图4-7齿轮拆卸快速扩展随机树[23]
4.3飞机维修装配优化仿真软件
(1)Tecnomatix
由Siemens公司开发的Tecnomatix是一套数字化仿真软件,主要模块:
工艺过程设计(ProcessDesigner),可以管理仿真所需数据,建立产品树、资源树、操作树等;工艺过程仿真(ProcessSimulate)维修过程仿真、人机工程分析评价等操作;数字化工厂(PlantSimulation),可以进行装配生产线布局等[24]。
图4-8Tecnomatix中进行装配路径规划[24]
(2) 3DVIAComposer
3DVIAComposer是由达索公司开发的图形软件,可读取SolidWorks、CATIA、Pro/E和其他CAD格式的三维CAD数据,还能创建高度压缩的以SMG为格式的轻量化文件,侧重于拆卸/装配设计、拆卸/装配仿真动画的制作、面向文档的发布[25]。
图4-93DVIAComposer中可操作的三维工艺附图[25]
(3)Virtools
Virtools是一种虚拟现实软件,是法国达索公司开发的一个强大的实时可视化的三维引擎平台。
是一套具备多种互动行为模块的编辑软件,而且它能将3D模型、2D图形和音像等相结合,制作出符合不同客户需求的三维虚拟产品[26]。
图4-10Virtools中进行飞机装配线仿真[26]
图4-11Virtools中进行飞机舱座椅维修[26]
(4)Flexsim
Flexsim是一种在图形的模型环境中应用C++IDE和编译程序的仿真软件(定义模型逻辑时,可直接使用C++而且可立刻编译到Flexsim中),一种面向对象的可视化3D仿真软件,可以方便地建立生产线模型并通过仿真进行效能评价。
目前多用在车间调度优化,生产线仿真、物流系统建模、维修故障仿真方面的研究[27]。
图4-12Flexsim中B747客舱安装仿真[27]
图4-13Flexsim中B747安装作业布局调度[27]
(5)Delmia
DELMIA是在法国达索公司开发的,在航空制造领域广泛应用的一款仿真软件,该系统以“数字化制造技术”为核心,重点解决制造过程的仿真问题,并为此提供了定义和模拟数字化制造流程的各项功能。
其具有多个功能模块,在下面的机翼的维修装配仿真中,主要应用PlantLayout(工厂的规划设计仿真)、DPM-AssemblyProcessSimulation(装配流程的仿真)和ErgonomicsDesign&Analysis(人机工效分析)[28]。
图4-14Delmia中某通用飞机机翼装配仿真[28]
4.4飞机维修装配优化算法及可行性分析
基于上述构建的装配模型进行进一步优化常常要利用一些算法并结合实例验证,而优化时往往要针对具体不同的实际问题对基本算法进行改进,将改进前和改进后算法的结果进行比较,验证优化的可行性,这也是一点创新之处。
(1)遗传算法(GeneticAlgorithm)
2011年南京航空航天大学孙有朝、陆中等对飞机起落架构建了产品部件联接图,提出基于有序搜索的部件模块装配序列规划,并利用基因成对交叉变异改进基本遗传算法来求解完整装配序列遗传算法进行优化[29]。
可以看到改进后遗传算法在300代左右得到最优值,而改进算法前需要1500多代,明显得到优化。
图4-15某飞机起落架及部件连接图
图4-16算法改进前后求得最优解的迭代次数
(2)蚁群算法(AntColonyOptimizationAlgorithm)
2013年上海商飞设计研究院的夏坚构建了拆卸Petri网可达图,并且以拆卸代价最小为目标函数,提出改进局部信息素更新方式的改进蚁群算法,并以飞机前机身电子设备舱设备作为典型实例,进行维修拆卸优化[30]。
由图4-16见,改进后蚁群算法的迭代次数和迭代时间都少于改进算法之前,得到了优化。
图4-17飞机前机身电子设备舱及其拆卸序列[30]
图4-18改进算法前后的迭代次数和时间[30]
(3)模拟退火算法(SimulatedAnnealingAlgorithm)
2011年BurcinCakir等人,以最小平滑指数和最小成本为目标函数,改进模拟退火算法,对随机装配生产线生产调度进行优化,得到帕累托最优解(Pareto-OptimalSolution资源分配的一种理想状态),并与原算法进行比较[31]。
由图4-17可见,改进后的模拟退火算法,成本明显小于算法改进之前,得到了优化。
图4-19算法改进前后最小成本比较[31]
(4)粒子群算法(ParticleSwarmOptimizationAlgorithm)
2014年SyedHassan等人,以最短路径和最短时间为目标函数,通过引入人工势场的概念,运用人工势场法,同时改进粒子群算法,并且对飞机装配路径进行优化,并与原粒子群算法比较。
由图4-19可知,改进后的粒子群算法,在同样的迭代次数下,其适应度值明显高于改进之前,问题得到了优化。
图4-20用改进粒子群算法飞机装配路径仿真
图4-21改进前后粒子群算法比较
5.总结
本文明确了研究飞机数字化装配优化的意义,装配作为飞机制造及维修中重要环境,为了缩短飞机装配周期,节约飞机装配成本,提高飞机装配精度,进而减少装配差错和飞行事故发生,必须进行飞机装配的优化;而结合国内外飞机数字化装配、飞机数字化装配工艺优化的国内外研究现状,对国内外飞机数字化装配近来发展动态有了一定的了解;接着总结出本文主要研究的三个子问题:
装配序列规划、装配生产线调度规划和装配路径规划;具体优化方法往往分为飞机装配相关模型的建立和结合相关改进算法进行优化两部分,需要运用相关的仿真软件作为平台进行。
References:
[1].唐健钧,基于精度控制的飞机装配工艺设计与优化技术研究,2014,西北工业大学.第137页.
[2].尹良,基于虚拟装配仿真的人机工效分析,2012,华中科技大学.第63页.
[3].乔勃,面向并行设计的产品装配建模及仿真技术研究,2007,南京航空航天大学.第69页.
[4].王建,人机工程在复杂产品装配规划中的应用,2013,西安电子科技大学.第86页.
[5].吴晓叶,装配仿真技术在飞机翼身对接中的应用.上海电力学院学报,2012(03):
第277-280页.
[6].石炳坤等,复杂产品数字化装配工艺规划与仿真优化技术研究.航空精密制造技术,2014(01):
第46-48+60页.
[7].冯廷廷,基于MBD的飞机装配工艺规划与仿真,2011,南京航空航天大学.第80页.
[8].Xia,P.,etal.,Anewtypehaptics-basedvirtualenvironmentsystemforassemblytrainingofcomplexproducts.TheInternationalJournalofAdvancedManufacturingTechnology,2012.58(1-4):
p.379-396.
[9].靳思源,飞机壁板件装配偏差的刚柔结合建模与工艺优化方法,2013,上海交通大学.第106页.
[10].周栋等,虚拟维修技术研究与应用.北京航空航天大学学报,2011(02):
第231-236页.
[11].Zhao,Z.,etal.PredictionofAssemblyVariationDuringEarlyDesign.inASME2007InternationalDesignEngineeringTechnicalConferencesandComputersandInformationinEngineeringConference.2007.
[12].Butterfield,J.,etal.,OptimizationofAircraftFuselageAssemblyProcessUsingDigitalManufacturing.JournalofComputing&InformationScienceinEngineering,2007.7(3):
p.269-275.
[13].华菲菲,飞机装配的生产计划优化及执行过程监控,2012,华中科技大学.第68页.
[14].邱晞,魏生民与程晖,基于空间扫略的飞机产品装配路径规划技术.北京航空航天大学学报,2010(06):
第676-680+685页.
[15].Ghandi,S.andE.Masehian,Reviewandtaxonomiesofassemblyanddisassemblypathplanningproblemsandapproaches.Computer-AidedDesign,2015.67-68:
p.58-86.
[16].李娜,面向维修的装配序列规划方法研究,2012,南京航空航天大学.第79页.
[