杨柳煤矿梳状钻孔现场试验报告.docx
《杨柳煤矿梳状钻孔现场试验报告.docx》由会员分享,可在线阅读,更多相关《杨柳煤矿梳状钻孔现场试验报告.docx(20页珍藏版)》请在冰豆网上搜索。
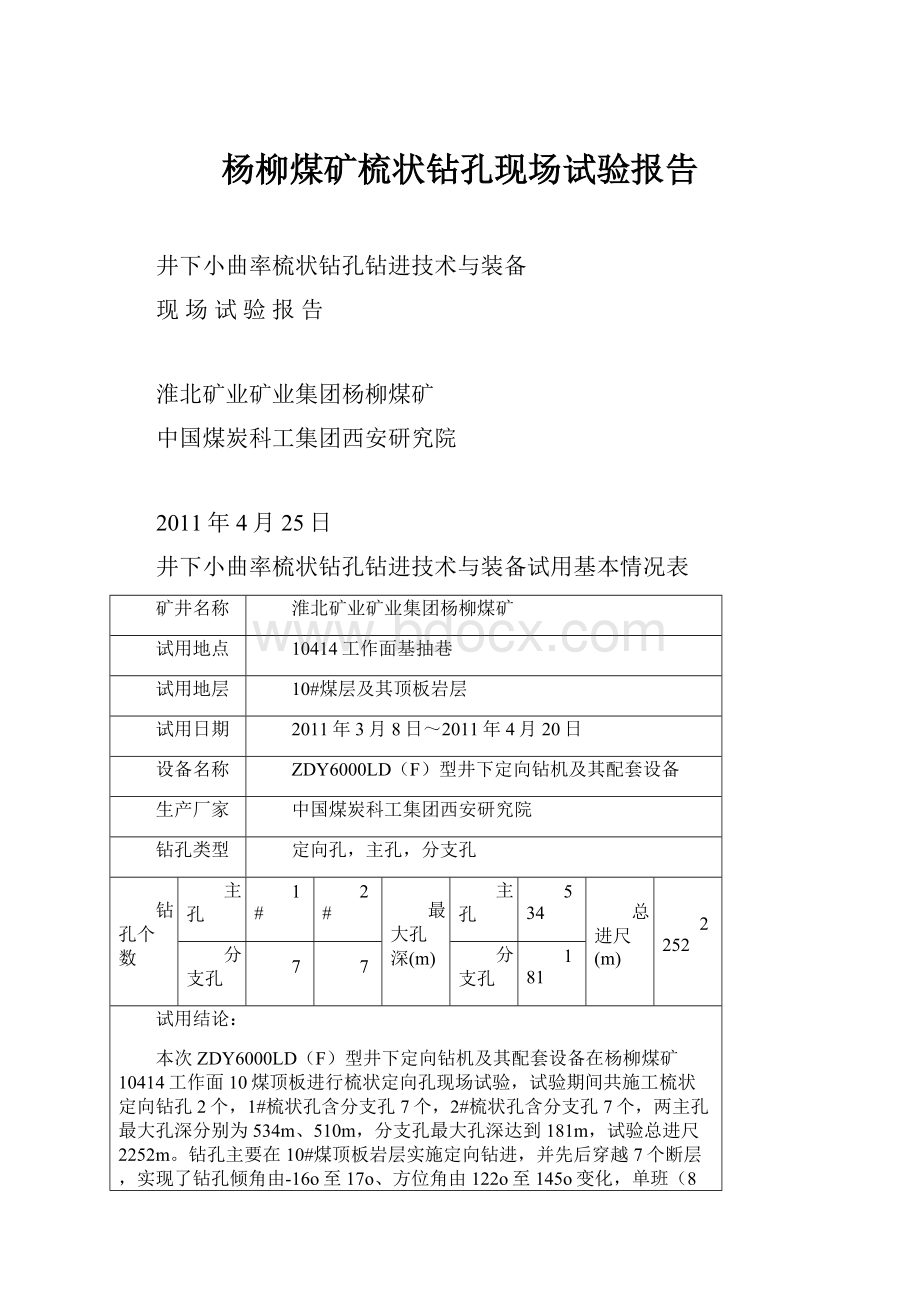
杨柳煤矿梳状钻孔现场试验报告
井下小曲率梳状钻孔钻进技术与装备
现场试验报告
淮北矿业矿业集团杨柳煤矿
中国煤炭科工集团西安研究院
2011年4月25日
井下小曲率梳状钻孔钻进技术与装备试用基本情况表
矿井名称
淮北矿业矿业集团杨柳煤矿
试用地点
10414工作面基抽巷
试用地层
10#煤层及其顶板岩层
试用日期
2011年3月8日~2011年4月20日
设备名称
ZDY6000LD(F)型井下定向钻机及其配套设备
生产厂家
中国煤炭科工集团西安研究院
钻孔类型
定向孔,主孔,分支孔
钻孔个数
主孔
1#
2#
最大孔深(m)
主孔
534
总进尺(m)
2252
分支孔
7
7
分支孔
181
试用结论:
本次ZDY6000LD(F)型井下定向钻机及其配套设备在杨柳煤矿10414工作面10煤顶板进行梳状定向孔现场试验,试验期间共施工梳状定向钻孔2个,1#梳状孔含分支孔7个,2#梳状孔含分支孔7个,两主孔最大孔深分别为534m、510m,分支孔最大孔深达到181m,试验总进尺2252m。
钻孔主要在10#煤顶板岩层实施定向钻进,并先后穿越7个断层,实现了钻孔倾角由-16o至17o、方位角由122o至145o变化,单班(8小时)最大进尺达到78m,在细砂岩中纯钻进时效达到15m/h以上,通过本次试验说明该定向钻设备在杨柳煤矿10414工作面岩层中施工近水平长钻孔是可行的,为解决杨柳煤矿瓦斯抽采提供一有效新途径,具有较好应用前景。
此外试验期间为淮北矿业集团工程处钻探公司培训了一批梳状定向钻设计与施工人员,为今后梳状定向孔技术在淮北矿业应用奠定了技术基础。
杨柳煤矿
2011年4月20日
1概述
本次试验根据杨柳煤矿瓦斯治理要求,采用井下小曲率梳状钻孔钻进技术进行梳状定向孔试验。
该技术解决松软煤层长距离瓦斯抽采与钻孔轨迹控制问题,拟使用先进的随钻测量定向钻进技术在煤层顶板中施工长距离瓦斯抽采主钻孔,再在主孔四周施工梳状多分支钻孔增加钻孔抽采区域,以达到长距离控制和预抽瓦斯的目的。
2011年3月8日至4月20日中国煤炭科工集团西安研究院在杨柳煤矿10414工作面进行梳状孔现场试验。
本次试验共施工梳状钻孔2个、1#梳状孔含分支孔7个、2#梳状孔含分支孔6个,两主孔最大孔深分别为534m、510m,分支孔最大孔深达到181m,试验总进尺2252m。
完成了试验要求各项技术指标,为解决松软煤层瓦斯抽采长钻孔成孔难题提供一有效途径,并为淮北矿业集团工程处钻探公司培训了一批梳状定向孔钻孔设计与施工人员,为今后梳状定向孔技术在淮北矿业应用奠定了技术基础,取得了较好的应用效果。
2试验目的及内容
本次现场试验的目的:
通过在10414工作面10煤顶板施工一水平长钻孔,并从该长钻孔向上或向下开若干分支孔,以便在钻孔底部10煤开采完后,抽采10煤顶板裂隙中瓦斯,并验证中煤科工西安研究院ZDY6000LD(F)定向钻机在杨柳煤矿施工长水平定向孔可行性。
试验主要内容及指标包括:
施工两个梳状孔,主孔孔深不小于500m水平长钻孔,主孔主体位于在10煤上方20m~40m。
3试验钻场地质条件
杨柳煤矿位于童亭背斜东翼北端。
地层走向在浅部为近于南北向,向东倾斜的单斜构造,地层倾角15°~20°;深部次一级褶曲较发育,主体上呈向东延深,地层倾角5°~10°,较平缓。
矿内断层较发育,查出落差大于或等于20m的断层20条,正断层19条,逆断层1条;按落差分:
大于或等于20m,小于30m的断层2条;大于或等于30m,小于50m的断层3条;大于或等于50m,小于100m的断层6条;大于100m的断层9条。
见图3201。
岩浆活动较剧烈,几乎普布全矿井,其中对72、81煤层影响最大。
钻孔所在区域基本为一东高西低的单斜构造,断层发育。
钻孔轨迹需进过七个断层:
F106(∠65°H=20-25m)、F104-33(322°∠56°H=1.3m)、F104-34(135°∠71°H=2.1m)、F104-20(120°∠16-25°H=8m)、F104-32(100°∠15-20°H=1.8m)、F104-21(110°∠60-70°H=5-6m)、F104-31(322°∠78°H=0.6m),钻孔试验主要地层为10煤顶板(即8煤底板),钻孔开孔所处岩层为10煤顶板的粉砂岩,其中9-4钻孔煤层柱状图详见图2-1,10煤层及顶底板情况:
10煤(高程-582.67~-585.73m):
黑色,条痕黑褐色,块状、沫状、鳞片状结构、玻璃光泽、以亮煤为主。
泥岩(高程-579.43~-582.67m)
细粒砂岩(高程-574.93~-582.67m):
灰白色,中-细粒,石英为主,绿色矿物及黑云母;下部含炭质泥岩包体,黑色。
泥岩(高程-530.03-574.93m)
4钻孔设计与施工工艺
4.1钻孔设计
为了达到较好的瓦斯抽放效果,在设计10414工作面顶板瓦斯预抽钻孔时,需尽量保证设计布置的钻孔为上斜孔,以免钻孔内的积水影响钻孔瓦斯抽放。
根据10414工作面地质特征,选用10煤及其顶板为试验岩层,首先利用长水平定向钻技术在10煤的顶板施工孔深不低于500m水平主孔,然后在主孔内向上(或向下)开5个以上分支孔。
其中1#梳状孔开孔方位角选取127°,开孔倾角选取5°,2#梳状孔开孔方位角选取135°,开孔倾角选取5°,施工完主孔后,采用后退式开分支技术,在主孔合适位置向上或向下开4~5个分支孔。
钻孔主孔设计轨迹见图4-1。
2#
1#
图4-1钻孔主孔设计轨迹
4.2施工工艺
4.2.1施工顺序
用螺杆钻具进行煤矿井下定向主孔及分支孔施工时,根据施钻地层状况、设计要求和目的等不同,施工顺序可分为“前进式”和“后退式”两种。
不管采用何种方式,都存在从主孔中定向开分支孔(即侧钻)问题,还会涉及分支孔重入技术。
根据钻孔设计与地层条件,本次试验钻孔施工顺序:
首先采用“前进式”开分支工艺施工右上方分支孔,钻至设计孔深后,采用“后退式”开分支工艺施工左下方分支孔。
1)前进式分支孔工艺
也称从外向内开分支孔,即在主孔钻孔的同时进行分支孔施工。
此种分支孔工艺主要用于探测煤层产状、采空区等地质构造,为后续工作做前期准备。
其工艺流程见图4-2。
图4-2前进式开分支孔施工工艺流程
2)后退式分支孔工艺
也称从内往外分支孔,即完成超过600m的主孔指标后,在起钻的同时进行分支孔施工。
其工艺流程见图4-3。
图4-3后退式开分支孔施工工艺流程
4.2.2钻进工艺与钻进参数
1)钻孔开孔、扩孔段
根据钻孔开孔设计参数(倾角、方位角)稳固钻机,采用回转钻进工艺钻进15m开孔。
钻具组合:
Φ96mmPDC平底钻头(窄保防反切)+Φ73mm通缆钻杆。
扩孔8m:
Φ153mm扩孔钻头+Φ73mm通缆钻杆。
安装孔口管、联接孔口气液分离器。
2)主孔段及分支孔段
主孔段、分支孔段都采用定向钻进技术,即利用随钻测斜技术指导调螺杆马达工具面向角来控制钻孔钻进轨迹。
钻具组合:
Φ96mmPDC平底钻头(窄保防反切)+Φ73mm无磁螺杆马达(1.25°或1.5°)+Φ73mm无磁测量短节+Φ73mm通缆钻杆。
钻进参数:
泥浆泵排量为200L/min;泵压为1~4.MPa,钻孔液:
清水。
5试验设备概况
5.1钻机
试验所用的ZDY6000LD(F)履带式全液压定向钻机是中煤科工集团西安研究院针对“井下小曲率梳状钻孔钻进技术与装备”项目最新研制的。
该钻机具有搬迁方便、转速调节范围宽、扭矩大、结构合理、技术性能先进、工艺适应性强、操作省力、安全可靠等优点。
主要用于煤矿井下地质勘探孔、抽放瓦斯孔、注水孔等钻孔施工。
钻机主要分两部分,包括采用履带式结构的钻车(图5-1右)和采用胶轮式结构的泵车(图5-1左),两车体通过车体连接架(图5-1中)连接起来。
钻车是钻机的操纵和执行机构,包括主机、操纵装置、稳固装置、履带总成、钻车车体等部件,泵车是钻机的动力源,包括电机泵组、油箱、泵车车体、泥浆泵、电磁启动器等部件;当需要移动钻机时,用车体连接架将两车体连接起来,用带快速接头的液压胶管通过两车体的油管连接板将钻机液压系统连接起来,就可以操作钻车的履带手柄来控制钻机的行走。
图5-1ZDY6000LD(F)履带式全液压定向钻机
其主要技术参数见表5-1。
表5-1ZDY6000LD(F)型钻机主要技术参数一览表
钻孔倾角(°)
-10~30
钻机质量(kg)
钻车
5930
泵车
3500
回转速度(rpm)
50~190
最大回转扭矩(Nm)
6000~1600
主轴额定制动转矩(Nm)
1000
给进能力(kN)
180
起拔能力(kN)
180
行走速度(m/s)
0-2.5
给进/起拔行程(mm)
1000
最大爬坡能力(°)
10
液压系统额定压力(MPa)
25(Ⅰ泵)
21(Ⅱ泵)
21(Ⅲ泵)
电机功率(kW)
90
运输状态外行尺寸(mm)
钻车
3230×1360×1867
泵车
2870×1410×1500
泵车上泥浆泵为BWY-200/9型泥浆泵,是一种卧式三缸单作用往复式活塞泵。
由定量液压马达驱动,可实现流量的无级调速,主要与近水平长钻孔定向钻机配套。
该泵具有高冲次、无级变量、结构先进、性能可靠、较市场上现有同档次的泥浆泵体积小、重量轻、装拆方便等特点。
其主要作用是作为动力为孔底马达提供高压钻井液,直接驱动钻头回转破碎岩石。
其次冲洗液(主要为清水)进入钻孔内,冲洗并带走孔内岩粉,冷却、润滑钻头和钻具、保护孔壁等,以保证正常钻进。
其主要技术参数见表5-2。
表5-2BWY-200/9型泥浆泵主要技术参数
型式
数值
行程(mm)
82
缸径(mm)
57
泵速(min-1)
370
流量(L/min)
200
压力(MPa)
9
容积效率(%)
93
总效率(%)
84.5
输入速度(r/min)
1406
进水管直径(mm)
Φ79.2
排水管直径(mm)
Φ38
液压马达型号
A2F80W2Z2定量马达
外形尺寸(mm)(长×宽×高)
1040×820×720
质量(kg)
470
减速比
3.8
5.2钻具
5.2.1钻杆
试验中使用了两种钻杆:
第一种是Φ73mm中心通缆钻杆(见图5-2),该钻杆具有以下特点:
1)钻杆接头采用内加厚方式局部增加壁厚,通过摩擦焊与钻杆相连,钻杆外径为73mm,内径为59mm,钻杆强度较高。
2)在测量钻孔轨迹的过程中,有缆钻杆与YHD1-1000型随钻测量系统配合使用能够实现孔底钻孔参数的即时随钻测量。
3)该钻杆刚性好、抗弯扭能力强,该钻杆设计强度既可满足孔底马达钻进要求也可以可满足孔口动力回转钻进要求。
图5-2Φ73mm中心通缆钻杆
第二种是Φ73mm无磁钻杆,材料选用无磁性的铍铜。
主要用于钻孔测斜时放置测量仪器,以避免普通钢性钻杆对测量方位角造成的干扰,保证测量数据准确。
无磁钻杆分上无磁钻杆(见图5-3下)、探管外管(见图5-3中)、下无磁钻杆(见图5-3上)三种,其中上无磁钻杆与通缆钻杆一样都含中心通缆,探管外管用于安装固定“探管+探管电池筒”。
图5-3Φ73mm无磁钻杆
5.2.2螺杆马达
本次试验采用进口螺杆钻具,主要由螺杆马达(定子、转子)总成、万向轴总成、传动轴总成四大部分组成,见图5-4。
图5-4螺杆马达
5.2.3通缆式送水器
在定向钻进过程中,通缆式送水器有三方面的作用:
1)输送高压水,驱动螺杆钻具转子旋转,带动钻头转动,完成钻孔作业;
2)向孔口监视器传输孔底测斜单元的输出信号,方便施工人员随时掌握钻具姿态;
3)在回转钻进过程中,向孔底输送冲洗介质,便于孔内煤粉和岩粉的排出,同时能冷却钻头的作用。
因此,通缆式送水器在结构设计过程中,既要考虑其能够灵活转动和耐高压,也要保障信号的正常传输。
见图5-5。
图5-5通缆式送水器
5.3钻头
此次试验共选用两种钻头:
第一种是Φ96mm平底钻头(窄保防反切),该钻头利用粉末冶金原理烧结而成,其耐磨性强,钻头保径效果好,碎岩能力强、通水排渣流畅,此外由于在钻头四翼镶焊反切削硬质合金,增强其钻探事故处理能力。
试验中该钻头配合螺杆钻具钻进取得了很好的效果,如图5-6
(1)所示。
第二种是Φ94mm/Φ153mm扩孔钻头,由于试验区煤层瓦斯大,瓦斯喷孔严重,所以在钻进过程中必须安装封孔装置,以便钻进的同时进行抽放瓦斯,此钻头主要用于在开孔时扩孔,以便安装孔口装置,如图5-6
(2)所示。
(1)Φ96mm平底钻头(窄保防反切)
(2)Φ94mm/Φ153mm扩孔钻头
图5-6试验用钻头
5.4YHD1-1000随钻测量系统
YHD1-1000随钻测量系统由下无磁钻杆、测量探管、上无磁钻杆、通缆式钻杆、通缆式送水器、通讯电缆、孔口监视器等组成。
该系统与定向钻机、孔底马达和钻头配套在一起,用于水平定向钻进的测量和控制,形成定向钻进系统。
系统的连接示意图如图5-7所示。
图5-7YHD1-1000随钻测量系统连接示意图
YHD1-1000型随钻测量系统主要用于近水平定向钻孔施工过程中的随钻监测,其硬件部分主要包括测量短节及电池筒(见图5-8)、无磁钻杆(见图5-4)、孔口监视器及匹配电源(见图5-9)、通缆钻杆(见图5-2)、通缆式送水器(见图5-5)及信号线,软件包括井上用定向钻进设计软件和井下用随钻测量系统。
该系统可随钻测量钻孔倾角、方位、工具面等主要参数,同时可实现钻孔参数、轨迹的即时孔口显示,便于施工人员随时了解钻孔施工情况,并及时调整工具面方向和工艺参数,使钻孔尽可能的按照设计轨迹延伸。
图5-8测量短节(下)及电池筒(上)
图5-9孔口监视器及匹配电源
6现场试用情况
2011年3月8日至4月20日在杨柳煤矿10414工作面基抽巷进行了梳状定向钻孔现场试验,本次试验共施工梳状钻孔2个、1#梳状孔含分支孔7个、2#梳状孔含分支孔7个,两主孔最大孔深分别534m、510m,分支孔最大孔深达到181m,试验总进尺2252m。
6.11#梳状孔施工情况
1#梳状孔自2011年3月8日中班开孔,由于在设备搬迁过程中保护不当、设备出现故障,经过检修和维护,3月24日开始正常施工。
1#梳状孔至4月7日早班终孔,共施工主孔一个,分支孔7个,试验总进尺1144m(见表6-1)。
表6-1钻孔施工情况
孔号
孔起始深度(m)
孔深(m)
终孔原因
主孔(1-1-3#)
0~528
534
施工安全
1#
39~96
57
遇断层塌孔
1-1#
75~129
54
遇断层塌孔
1-1-1#
57~238
181
遇断层塌孔
1-2#
312~393
81
设计深度
1-4#
45~153
108
见煤瓦斯超限
1-5#
33~45
12
遇断层塌孔
1-6#
18~135
117
设计深度
合计
1144
本次试验在钻进时主要采用后退式分支孔施工工艺,其工艺流程见图4-3。
具体钻孔施工情况如下:
首先以倾角5°、方位角127°稳固钻机开孔,施工主孔段1#,钻至96m处钻遇断层塌孔,后多次尝试无法穿过断层,提钻至39m开分支继续施工主孔,并将原主孔段39m~96m作为分支孔1#。
然后施工主孔段39m~129m,钻至129m处钻遇断层塌孔,后多次尝试无法穿过断层,提钻至75m开分支继续施工主孔,并将原主孔段75m~129m作为分支孔1-1#。
之后施工主孔段75m~238m,钻至238m处钻遇断层塌孔,后多次尝试无法穿过断层,提钻至57m开分支继续施工主孔,并将原主孔段57m~238m作为分支孔1-1-1#。
之后施工主孔段57m~534m,钻至534m处钻遇塌孔,为施工安全而终止主孔施工。
之后提钻至主孔312m处开分支1-2#,钻至设计孔深393m而终止1-2#分支孔施工。
之后提钻至主孔45m处向下开分支1-4#,钻至孔深153m处见煤,孔口瓦斯超限而终止1-4#分支孔施工。
之后提钻至主孔33m处向下开分支1-5#,钻至孔深45m处钻遇断层塌孔,后多次尝试无法穿过断层而终止1-5#分支施工。
最后提钻至主孔18m处向下开分支1-6#,钻至设计孔深135m而终止1-6#分支孔施工。
1#梳状孔实钻轨迹见图6-1、图6-2。
蓝线—设计轨迹,粉红线—实钻轨迹
图6-11#梳状孔实钻轨迹在10414瓦斯抽排钻孔层位预想剖面图分布
蓝线—设计轨迹,粉红线—实钻轨迹
图6-21#梳状孔实钻轨迹平面图(上)与剖面图(下)
6.22#梳状孔施工情况
2#梳状孔自2011年4月7日中班开孔,至4月20日夜班,共施工主孔一个,分支孔7个,试验总进尺1108m(见表6-2)。
表5-2钻孔施工情况
孔号
孔起始深度(m)
孔深(m)
终孔原因
主孔(2-5#)
0~510
510
施工安全
2#
33~48
15
塌孔卡钻
2-1#
180~285
105
设计孔深
2-2#
384~453
69
塌孔卡钻
2-6#
303~384
81
设计孔深
2-7#
123~288
165
见煤
2-8#
78~138
60
遇断层不返水
2-9#
66~169
103
合计
1108
本次试验在钻进时采用后退式分支孔工艺施工工艺。
具体钻孔施工情况如下:
首先以倾角5°、方位角135°稳固钻机开孔,施工第一段主孔0m~48m,钻至48m处遇断层塌孔,后多次尝试无法穿过断层,提钻至33m开分支继续施工主孔,并将原主孔段33m~48m作为分支孔2#。
施工主孔段33m~180m,并在180m处采用前进式开分支施工2-1#分支孔,钻至设计深度285m,终止2-1#分支孔施工。
施工完2-1#分支孔后提钻至主孔180m开分支继续主孔段180m~453m施工,钻至453m处遇断层塌孔,后多次尝试无法穿过断层,提钻至384m开分支继续施工主孔,并将原主孔段384m~453m作为分支孔2-2#。
施工主孔段384m~510m,钻至510m处钻遇塌孔,为施工安全而终止主孔施工。
提钻至主孔303m处开分支2-6#,钻至设计深度384m,终止2-6#分支孔施工。
之后提钻至主孔123m处向下开分支2-7#,钻至孔深288m处见煤,并遇断层不返水,因达到设计要求而终止2-7#分支孔施工。
之后提钻至主孔78m处向下开分支2-8#,钻至孔深138m处因遇断层,使水从断层裂隙流失而钻孔不返水,终止2-8#分支孔施工。
最后提钻至主孔66m处向下开分支2-9#,钻至设计孔深169m处,终止2-8#分支孔施工,提钻终孔。
2#梳状孔实钻轨迹见图6-3、图6-4,1#、2#梳状孔在10414采掘平面图实钻轨迹分布见图6-5。
蓝线—设计轨迹,粉红线—实钻轨迹
图6-32#梳状孔实钻轨迹在10414瓦斯抽排钻孔层位预想剖面图分布
图6-42#梳状孔实钻轨迹平面图(上)与剖面图(下)
蓝线(上)—2#钻孔,粉红线(下)—1#钻孔
图6-51#、2#梳状孔实钻轨迹在10414工作面的采掘平面图分布
7结论
通过本次杨柳煤矿10414工作面10煤顶板梳状孔现场试验,得出如下结论:
1)本次试验共施工梳状钻孔2个、1#梳状孔含分支孔7个,2#梳状孔含分支孔7个,两主孔最大孔深分别为534m、510m,分支孔最大孔深达到181m,试验总进尺2252m。
2)ZDY6000LD(F)履带式全液压定向钻机,试验期间该钻机运行稳定而高效、事故处理能力强、搬迁方便,具有较强穿越断层能力,能够满足杨柳煤矿孔深500m岩层梳状定向孔施工。
3)螺杆马达性能稳定、钻进效率高,满足梳状定向孔施工要求,在试验中单班(8小时)最大进尺达到78m,在细砂岩中纯钻进时效达到15m/h以上,此外可在岩层可进行开分支施工。
4)主孔位于在10煤上方20m~40m”。
施工过程中钻孔共穿过7个断层,在施工中常出现塌孔卡钻现象,
本次试验完成了主要技术指标:
“施工两个梳状孔,主孔孔深不小于500m水平长钻孔,班最大进尺78m,此外最大孔深达534m,总进尺2252m,两钻孔抽采覆盖区域面积近两万多平方米,主体钻孔轨迹精确控制精度在10煤上方20m~40m,预测待钻孔下方10煤开采过后,两梳状孔将有较好瓦斯抽采效果。
通过本次试验说明该定向钻设备在杨柳煤矿10414工作面岩层中施工近水平长钻孔是可行的,为解决杨柳煤矿瓦斯抽采提供一有效新途径,具有较好应用前景。
此外试验期间为淮北矿业集团工程处钻探公司培训了一批梳状定向钻设计与施工人员,为今后梳状定向孔技术在淮北矿业应用奠定了技术基础。