第一章 磨削加工的基本知识.docx
《第一章 磨削加工的基本知识.docx》由会员分享,可在线阅读,更多相关《第一章 磨削加工的基本知识.docx(15页珍藏版)》请在冰豆网上搜索。
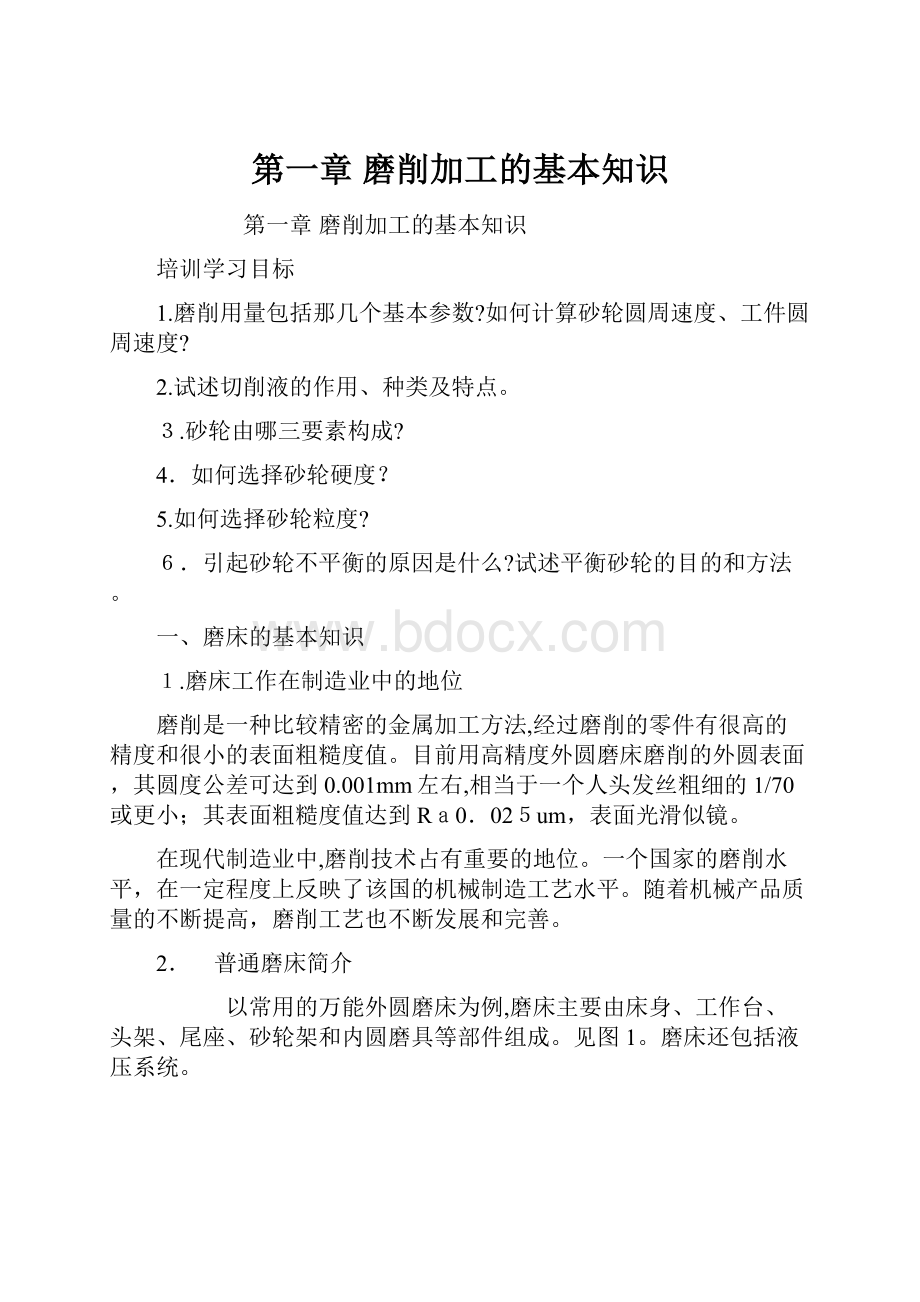
第一章磨削加工的基本知识
第一章磨削加工的基本知识
培训学习目标
1.磨削用量包括那几个基本参数?
如何计算砂轮圆周速度、工件圆周速度?
2.试述切削液的作用、种类及特点。
3.砂轮由哪三要素构成?
4.如何选择砂轮硬度?
5.如何选择砂轮粒度?
6.引起砂轮不平衡的原因是什么?
试述平衡砂轮的目的和方法。
一、磨床的基本知识
1.磨床工作在制造业中的地位
磨削是一种比较精密的金属加工方法,经过磨削的零件有很高的精度和很小的表面粗糙度值。
目前用高精度外圆磨床磨削的外圆表面,其圆度公差可达到0.001mm左右,相当于一个人头发丝粗细的1/70或更小;其表面粗糙度值达到Ra0.025um,表面光滑似镜。
在现代制造业中,磨削技术占有重要的地位。
一个国家的磨削水平,在一定程度上反映了该国的机械制造工艺水平。
随着机械产品质量的不断提高,磨削工艺也不断发展和完善。
2. 普通磨床简介
以常用的万能外圆磨床为例,磨床主要由床身、工作台、头架、尾座、砂轮架和内圆磨具等部件组成。
见图1。
磨床还包括液压系统。
(1)床身:
磨床的支承。
(2)头架:
安装与夹持工件,带动工件旋转,可在水平面内逆时针转90°;
(3)内圆磨具:
支承磨内孔的砂轮主轴。
(4)砂轮架:
支承并传动砂轮主轴旋转,可在水平面±30°范围内转动;
(5)尾坐:
与头架一起支承工件;
(6)滑鞍与横进给机构:
通过进给机构带动滑鞍上的砂轮架实现横向进给;
(7)横向进给手轮
(8)工作台:
a.上工作台:
上面装有头架与尾坐;b.下工作台:
上工作台可绕下工作台在水平面转±10°角度。
3.磨床的型号
磨床的种类很多,按GB/T15375-1994磨床的类、组、系划分表,将我国的磨床品种分为三个分类。
一般磨床为第一类,用字母M表示,读作“磨”。
超精加工机床、抛光机床、砂带抛光机为第二类,用2M表示。
轴承套圈、滚球、叶片磨床为第三类,用3M表示。
齿轮磨床和螺纹磨床分别用Y和S表示,读作“牙”和“丝”。
第一类磨床按加工不同分为一下几组:
0—仪表磨床;1—外圆磨床(如M1432A、MBS1332A、MM1420、M1020、MG10200等);2--内圆磨床(如M2110A、MGD2110等);3—砂轮机;4—研磨机、珩磨机;5—导轨磨床;6—刀具刃磨床(M6025A、M6110等);7—平面及端面磨床(如M7120A、MG7132、M7332A、M7475B等);8—曲轴、凸轮轴、花键轴及轧辊轴磨床(如M8240A、M8312、M8612A、MG8425等);9—工具磨床(如MK9017、MG9019等)。
型号还指明机床主要规格参数。
一般以内、外圆磨床上加工的最大直径尺寸或平面磨床工作台面宽度(或直径)的1/10表示;曲轴磨床则表示最大回转直径的1/10;无心磨床则表示基本参数本身(如M1080表示最大磨削直径为80mm)。
应当注意,外圆磨床的主要参数代号与无心外圆磨床不同。
磨床的通用特性代号位于型号第二位(如表1-1),如型号MB1432A中的B表示半自动万能外圆磨床。
磨床结构性能的重大改进用顺序A、B、C……表示,加在型号的末尾。
现以一数控高精度外圆磨床的型号说明磨床型号的表示方法。
其最大磨削直径为200mm,经第一次改进设计。
常用的磨床型号含义如下:
M1432B表示万能外圆磨床,最大磨削直径为320mm,经第二次重大结构改进;
MM1420表示精密万能外圆磨床,最大磨削直径为200mm;
MBS1332A表示半自动高速外圆磨床,最大磨削直径为320mm,经第一次重大结构改进。
MG1432A表示高精度万能外圆磨床,最大磨削直径为320mm,经第一次结构改进。
MB1632表示半自动端面外圆磨床最大回转直径为320mm;
M1080表示无心外圆磨床,最大磨削直径为80mm;
M2110表示内圆磨床,最大磨削孔径为110mm;
M7120A表示卧轴矩台平面磨床,工作台宽度为200mm,经第一次重大结构改进;
M7475B表示立轴圆台平面磨床,工作台直径为750mm,经第二次重大结构改进;
M6025A表示万能工具磨床,最大回转直径为250mm,经第一次重大结构改进;
S7332表示螺纹磨床,最大工件直径为320mm。
4.磨床的润滑和保养
1.磨床的润滑
良好的保养和润滑有利于延长磨床的使用寿命,保持磨床的精度和可靠性。
润滑的目的是减小磨床摩擦面和机构传动副的磨损,并提高机构工作的灵敏度。
如磨床主轴的动压轴承,其砂轮架油池每三个月更换一次精密主轴油,常用的润滑油为N2主轴油、N5主轴油两种。
主轴的油膜对润滑油有很高的要求,故不能用错油,有些高精度磨床的主轴动压轴承采用汽轮机油与煤油配置而成。
磨床工作台纵向导轨、砂轮架横向导轨用润滑油是全损耗系统用油,如L-AN46、l-AN32、L-AN68。
内圆磨具滚动轴承,500h更换一次润滑油,如3号锂基润滑脂,3号钙基润滑脂。
其它需采用滴油润滑的各润滑点如尾座套筒注油孔、横向进给手轮润滑油杯、工作台纵向手轮润滑杯等都需注入全损耗系统用油。
2.磨床的保养
磨床的日常保养很重要,要正常操作磨床,防止产生磨床故障或损害机床,降低机床精度。
机床保养九项要点:
1)合理操作磨床,不损害磨床部件、机械结构。
2)工作前后须清理机床,检查磨床部件、机械结构、液压系统、冷却系统是否正常,并及时修理排除磨床故障。
3)在工作台上调整头架、尾座位置时,须擦净其联接面,并涂润滑油后移动头架或尾座。
保护工作台、头架、尾座
联接间的有关机床精度。
4)人工润滑的部位应按规定的油类加注,并保证一定的油面高度。
5)定期冲洗冷却系统,合理更换切削液。
处理废切削液应符合环保要求。
6)高速滚动轴承的温升应低于60℃。
7)不同精度等级和参数的磨床与加工工件的精度和尺寸参数相对应,以保护机床精度。
8)磨床敞开的滑动面和机械机构须涂油防锈。
9)不碰撞或拉毛机床工作面的部件。
磨床运转500h后,需进行一次一级保养,一级保养工作以操作人员为主,维修人员配合进行。
一级保养常用工具有一字槽螺钉旋具、十字槽螺钉旋具、活扳手、呆扳手、内六角扳手、整体扳手、成套套筒扳手、锁紧扳手等。
一级保养的操作步骤:
1)切断电源,摇动手轮使砂轮架退后至较后位置,推动头架、尾座至工作台两端。
2)清扫机床铁屑较多的部位,如水槽、切屑液箱、防护罩壳等。
3)用柴油清洗头架主轴、尾座套筒、液压泵过滤器等。
4)在机修人员配合指导下,,检查砂轮架及床身油池内的油质情况,油路工作情况等,并根据实际情况调换或补充润滑油和液压油。
5)在维修电工的配合指导下,进行电气检查和保养。
6)进行机床油漆表面的保养,按从上到下,从后到前,从左到右的顺序进行,如有油痕可以用去污粉或碱水清洗。
7)进行附件的清洁保养。
8)补齐所缺少的零部件。
9)调整机床,如调整砂轮架主轴,头架主轴的间隙等。
10)装好防护罩壳、盖板。
二、磨削加工的特点及磨削过程
1磨削加工的特点
1)砂轮是由磨料和结合剂粘结而成的的磨料工具(磨具)。
磨粒材料(简称磨料)时一种具有极高硬度的非金属晶体,其硬度大于经热处理后的钢材的硬度,具有极高的可加工性。
因此砂轮不但可以磨削铜、铝、钢、铸铁等材料,而且还可以磨削硬度很高的材料。
2)砂轮是一种特殊的多刃磨削工具。
砂轮在磨削时,除了切除极细的小金属外,磨粒还对工件表面挤压和摩擦,在磨削区域的磨削温度高达400-1000℃。
3)磨削加工能获得极高的加工精度和极低的表面粗糙度值。
每颗磨粒切去切削厚度很薄,一般只有几微米,一般精度可达IT6级~IT7级,表面粗糙度可达Ra0.08μm~Ra0.05μm,精度磨削可达到更高,故磨削常用在精加工工序。
4)磨削作为机械加工的精加工工艺,是工件经过粗加工后,只切除工件表层极薄的金属层,最终达到工件的加工精度和表面粗糙度要求。
磨削时吃刀量是很小的。
5)一般磨削加工的金属切除效率较低,生产效率较低,高速磨削,强力磨削则有较高的金属切除率,特别是高速磨削的推广具有重要意义。
6)砂轮在磨削时还具有自锐性。
磨粒具有一定的脆性。
在磨削力的作用下会破裂,从而更新其切削力,称为砂轮的“自锐作用”。
7)砂轮的工作表面须经过修整,才能形成合适的微刃进行磨削加工。
2.磨削过程及磨削力、磨削热
(1)磨削过程
磨削加工的实质是工件被磨削的金属表层在无数磨粒的瞬间挤压、刻划、切削、摩擦抛光作用下进行的。
磨削瞬间起切削作用的磨粒的磨削过程可分为四个阶段:
砂轮表面的磨粒与工件材料接触为弹性变形的第一阶段;磨粒继续切入工件,工件进入塑性变形的第二阶段;材料的晶粒发生滑移,使塑性变形不断增大,当磨削力达到工件的强度极限时被磨削层材料产生挤裂,进入第三阶段;最后被切离。
磨削过程表现为力和热的作用。
(2)磨削力
磨削力时磨削加工时,工件材料抵抗砂轮磨削所产生的阻力。
磨削力在空间可分为三个分力:
1)切削力Fc总切削力在主运动方向上的正投影。
2)被方向力Fp 总切削力在垂直于进给运动方向上的分力。
磨削时要特别注意被向力对加工精度的影响。
3)进给力Ff 总切削力在进给运动方向上的正投影。
(3)磨削热
磨削热是在磨削过程中,由于被磨削材料层的变形、分离及砂轮与被加工材料间的摩擦而产生的热。
磨削热较大,热量传入砂轮、磨削、工件或被切削液带走。
然而砂轮是热的不良导体,因此几乎80%的热量传入工件和磨屑,并使磨屑燃烧。
磨削区域的高温会引起工件的热变形,从而影响加工精度。
严重的会产生工件表面灼伤、裂纹等弊病,因此磨削时应特别注意对工件的冷却和减小磨削热,以减小工件的热变形,防止产生工件表面灼伤和裂纹。
三、磨削用量的概念
1.磨削的基本运动
磨削的运动分主运动和进给运动两种。
1)外圆磨削的进给运动为工件的圆周进给运动、工件的纵向进给运动和砂轮的横向吃刀运动。
2)内圆磨削的进给运动与外圆磨削相同。
3)平面磨削的进给运动为工件的纵向(往复)进给运动,砂轮或工件的横向进给运动和砂轮的垂直吃刀运动。
2.磨削用量
磨削用量来表示磨削加工中主运动及进给运动参数的速度或数量。
磨削主运动的磨削用量为砂轮圆周速度,磨削进给量有些区别。
外圆磨削的磨削用量包括:
砂轮圆周速度Vs、工件圆周速度Vw、纵向进给量f、被吃刀量ap。
四、砂轮
1.砂轮的结构
磨具(abrasivegrinding tools):
分砂轮、油石、磨头、砂瓦、砂布、砂纸、砂带、研磨膏等6类。
砂轮是特殊的刀具,又称磨具,其制造过程也较复杂。
他是由一种用结合剂把磨粒粘结起来,经压坯、干燥、焙烧及修整而成的,具有很多气孔、用磨粒进行切削的固结磨具。
磨粒以其露在表面部分的尖角作为切削刃。
砂轮的特性主要由磨料、粒度、结合剂、硬度、组织及形状尺寸等因素所决定。
1).磨料
磨料是制造磨具的主要原料,直接担负着切削工作。
目前常用的磨料有棕刚玉(A)、白刚玉(WA)、黑碳化硅(C)和绿碳化硅(GC)等。
棕刚玉:
用于加工硬度较低的塑性材料,如中、低碳钢和低合金钢等;
白刚玉:
用于加工硬度较高的塑性材料,如高碳钢、高速钢和淬硬钢等;
黑碳化硅:
用于加工硬度较低的脆性材料,如铸铁、铸铜等;
绿碳化硅:
用于加工高硬度的脆性材料,如硬质合金、宝石、陶瓷和玻璃等。
2).粒度
粒度是指磨料颗粒的尺寸,其大小用粒度号表示。
国标规定了磨料和微粉两种粒度号。
一般说,粗磨选用较粗的磨料(粒度号较小),精磨选用较细的磨料(粒度号较大);微粉多用于研磨等精密加工和超精密加工。
3).结合剂
结合剂的作用是将磨料粘合成具有一定强度和形状的砂轮。
砂轮的强度、抗冲击性、耐热性及抗腐蚀能力,主要取决于结合剂的性能。
常用的结合剂有陶瓷结合剂(V)、树脂结合剂(B)、橡胶结合剂(R)和金属结合剂(M)等。
陶瓷结合剂:
应用最广,适用于外圆、内圆、平面、无心磨削和成形磨削的砂轮等;
树脂结合剂:
适用于切断和开槽的薄片砂轮及高速磨削砂轮;
橡胶结合剂:
适用于无心磨削导轮、抛光砂轮;
金属结合剂:
适用于金刚石砂轮等。
4).硬度
磨具的硬度是指磨具在外力作用下磨粒脱落的难易程度(又称结合度)。
磨具的硬度反映结合剂固结磨粒的牢固程度,磨粒难脱落叫硬度高,反之叫硬度低。
国标中对磨具硬度规定了16个级别:
D,E,F(超软);G,H,J(软) ;K,L(中软);M,N(中);P,Q,R(中硬);S,T(硬);Y(超硬)。
普通磨削常用G~N级硬度的砂轮。
5).组织
磨具的组织指磨具中磨粒、结合剂、气孔三者体积的比例关系,以磨粒率(磨粒占磨具体积的百分率)表示磨具的组织号。
磨料所占的体积比例越大,砂轮的组织越紧密;反之,组织越疏松。
国标中规定了15个组织号:
0,1,2,…,13,14。
0号组织最紧密,磨粒率最高;14号组织最疏松,磨粒率最低。
普通磨削常用4~7号组织的砂轮。
6).形状与尺寸
根据机床类型和加工需要,将磨具制成各种标准的形状和尺寸。
7).最高工作速度
砂轮高速旋转时,砂轮上任意一部分都受到很大的离心作用,如果砂轮没有足够的回转强度,砂轮就会爆裂而引起严重事故。
砂轮上的离心力与砂轮的线速度的平方成正比,所以当砂轮的线速度增大到一定数值时,离心力就会超过砂轮回转速度所允许的范围,砂轮就要爆裂。
砂轮的最大工作线速度,必须标注在砂轮上,以防止使用时发生事故。
(3)砂轮的代号
根据普通磨具标准GB/T2485--1994规定,砂轮(普通磨具)各特性参数以代号形式表示,依次序是:
砂轮形状、尺寸、磨料、粒度、硬度、组织、结合剂、最高工作速度。
(4)砂轮的选择
1).磨料的选择
按工件材料及其热处理的方法选择,使磨料本身的硬度与工件材料的硬度相对应。
一般的选择原则是:
工件材料为一般钢材,可选用棕刚玉;工件材料为淬火钢、高速工具钢,可选用白刚玉或烙刚玉;工件材料为硬质合金,则可选用人造金刚石或绿色碳化硅;工件材料为铸铁、黄铜则选用黑色碳化硅。
2).粒度的选择
按工件表面粗糙度和加工精度选择。
细粒度的砂轮可磨出细的表面;粗粒度则相反,但由于其颗粒粗大,砂轮的磨削效率高,一般常用的粒度是F46-F80。
粗磨时选用粗粒度砂轮,精磨时选用精粒度砂轮。
3).砂轮硬度的选择
砂轮硬度时衡量砂轮“自锐性”的指标。
磨削过程中,磨粒逐渐由锐利而变钝。
磨硬材料时,砂轮容易钝化,应选用软砂轮,以使砂轮锐利;磨软材料时,砂轮不易钝化,应选用硬砂轮,以避免磨粒过早脱落损耗;磨削特别软而韧的材料时,砂轮易堵塞,可使用较软的砂轮。
(5)砂轮的安装
砂轮安装前首先要鉴别其外观,常用的陶瓷砂轮是脆性体,受损伤的砂轮不能使用。
砂轮的裂纹可用响声法检测。
砂轮一般用法兰盘安装。
法兰盘主要由法兰底盘1、法兰盘2、衬垫3,内六角螺钉4等组成。
砂轮的孔径与法兰盘轴颈部分应有0.1-0.2mm的安装间隙。
如砂轮孔径与法兰盘轴颈配合过紧,可用刮刀均匀修刮砂轮内孔;如配合间隙太大则砂轮盘的中心与法兰盘的中心会产生安装偏心,增大砂轮的不平衡量。
为此,可在法兰轴颈的的周围垫上一层纸片,以减小安装偏心;如果砂轮孔径与法兰轴径相差太多,就应从新配置法兰盘。
法兰盘的支撑平面应平整且外径尺寸相等,安装时在法兰盘端面和砂轮之间,应垫上1-2mm厚的塑性材料制成的衬垫,衬垫的直径比法兰盘外径稍微大一些。
安装以后,砂轮应作两次平衡,在精平衡前砂轮需作整形修整。
从磨床主轴上拆卸法轮盘时使用套筒扳手和拨头。
(6)砂轮的平衡
砂轮的平衡程度是磨削主要性能指标之一,砂轮的不平衡是指砂轮的重心与旋转重心不合,即由不平衡质量偏离旋转中心所致。
例如不平衡量为1500g·cm的砂轮在转速达到1670g·cm时,其离心力可达460N。
巨大的离心力将迫使砂轮震动,使工件表面产生多角形的波纹,同时附加压力会加速主轴磨损。
当离心力大于砂轮强度时则会引起砂轮爆裂。
砂轮不平衡的原因是砂轮本身不平衡和砂轮安装所造成的不平衡所致。
静平衡的步骤如下:
1)调整平衡架导柱面水平位置。
2)安装平衡心轴。
3)找出不平衡位置。
4)装平衡块。
5)求各点的平衡位置。
(7)砂轮的修整
砂轮磨钝的形式有以下三种:
1)磨粒的钝化
2)磨粒急剧且且不均匀的脱落
3)砂轮的粘嵌和堵塞
砂轮在工作一段时间以后,砂轮的工作表面会发生钝化。
若继续磨削,将加剧砂轮与工件表面之间的摩擦,工件会产生烧伤或震动波纹,是磨削效率降低,也影响加工的表面粗糙度,因此应选择适当的时间及时修整砂轮。
砂轮磨钝的过程:
磨削过程中,可将砂轮表面微刃的钝化过程划分为初期、正常、急剧三个阶段。
在初级阶段,微刃表面残留的毛刺不断脱落划伤工件表面;正常阶段,微刃表面的毛刺已消失,微刃为正常的切削状态且逐步钝化,这是最佳的磨削阶段,工件的精磨应在此阶段内完成;当微刃锐角已完全消失,磨削时发出噪声,即为急剧钝化阶段。
除磨粒磨钝外,通常磨削时还伴有砂轮的堵塞,特别是在磨削铸铁材料时,磨屑堵满砂轮的网状空隙中,使砂轮磨钝。
(8)修整砂轮的方法
1)金刚钻笔车削法
金刚钻笔是将大颗粒的金刚钻镶焊在特制刀杆上制成的,金刚钻的尖端研成
φ=70°-80°的尖角。
修整时将金刚钻笔安装在修整座上,车削砂轮表面。
2)其它工具介绍,金刚石笔是由颗粒较小的碎粒金刚石或金刚粉用结合力强的合金结合而成的。
金刚石笔分层状、链状、粉状三种。
滚轮式割刀是由多片渗碳淬火钢的金属圆片装在刀柄上制成,常用于整形粗修整。
金刚石滚轮磨削法修整装置主要由传动装置和金刚石滚轮组成。
金刚石滚轮一般用电镀法制造而成。
五、切削液
1.切削液的作用
切削液主要用来降低磨削热和减少磨削过程中工件与砂轮之间的摩擦。
切削液主要有以下作用:
(1)冷却作用
(2)润滑作用
(3)清洗作用
(4)防锈作用
2.切削液的种类
切削液分为水溶液和油类两大类。
常用的水溶性液有乳化液和合成液两种。
常用的油类为全损耗系统用油和煤油。
水溶液以水为主要成分,水的冷却作用很好,但以使机床和工件锈蚀。
油类的润滑和防锈作用好,常用于螺纹及齿轮磨床的加工中,油类的冷却性较差,会产生油雾。
3.切削液的正确使用
1)切削液应该直接浇注在砂轮与工件接触的部位。
2)切削液流量应充足,并应均匀地喷射到整个砂轮磨削宽度上,并能达到冷却效果。
3)切削液应有一定的压力注入磨削区域,以达到良好的清洗作用,防止磨屑在磨削区域堵塞砂轮表面。
4)合理配置挡水板,防止切削液飞溅出磨床。
5)水箱中切削液要保持一定的液面高度。
6)切削液应经常保持清洁,尽量减少切削液中磨屑和磨粒碎粒的含量,变质的切削液要及时更换,超精密磨削时可以采用专门的过滤装置。
7)切削液的液流要保持通畅,防止液流在通道中被磨削堵塞。
堵塞的磨削要及时清除。
8)不要把其他杂物带入水箱中。
9)在夏天特别要注意防止乳化液锈蚀工件和磨床工作台表面,乳化液的质量分数可取高些。
10)防止切削液溅入眼中,特别要防止切削液中的亚硝酸钠入口中或吸入肺中,保护身体健康。
11)树立环保意识。
习题解答:
1、磨削用量包括四个参数:
砂轮圆周速度、工件圆周速度、纵向进给量、背吃刀量。
砂轮圆周速度(Vs)计算:
式中:
Vs--砂轮圆周速度(m/s)
Ds--砂轮直径(mm)
n--砂轮转速(r/min)
工件圆周速度(Vw)计算:
式中:
Vw--工件的圆周速度(m/min)
dw--工件外圆直径(mm)。
Nw--工件转速(r/min)
2、
(1)切削液的作用
切削液主要用来降低磨削热和减少磨削过程中工件与砂轮之间的摩擦。
切削液主要有以下作用:
(1)冷却作用
(2)润滑作用
(3)清洗作用
(4)防锈作用
(2)切削液的种类
ﻩ切削液分为水溶液和油类两大类。
常用的水溶性液有乳化液和合成液两种。
常用的油类为全损耗系统用油和煤油。
水溶液以水为主要成分,水的冷却作用很好,但以使机床和工件锈蚀。
油类的润滑和防锈作用好,常用于螺纹及齿轮磨床的加工中,油类的冷却性较差,会产生油雾。
3、磨粒、结合剂、空隙构成砂轮结构的三要素。
4、砂轮硬度时衡量砂轮“自锐性”的指标。
磨削过程中,磨粒逐渐由锐利而变钝。
磨硬材料时,砂轮容易钝化,应选用软砂轮,以使砂轮锐利;磨软材料时,砂轮不易钝化,应选用硬砂轮,以避免磨粒过早脱落损耗;磨削特别软而韧的材料时,砂轮易堵塞,可使用较软的砂轮。
5、粒度的选择:
按工件表面粗糙度和加工精度选择。
细粒度的砂轮可磨出细的表面;粗粒度则相反,但由于其颗粒粗大,砂轮的磨削效率高,一般常用的粒度是F46-F80。
粗磨时选用粗粒度砂轮,精磨时选用精粒度砂轮。
6、砂轮不平衡的原因是砂轮本身不平衡和砂轮安装所造成的不平衡。