注塑制品易出现的缺陷原因和解决方法Mold flow.docx
《注塑制品易出现的缺陷原因和解决方法Mold flow.docx》由会员分享,可在线阅读,更多相关《注塑制品易出现的缺陷原因和解决方法Mold flow.docx(14页珍藏版)》请在冰豆网上搜索。
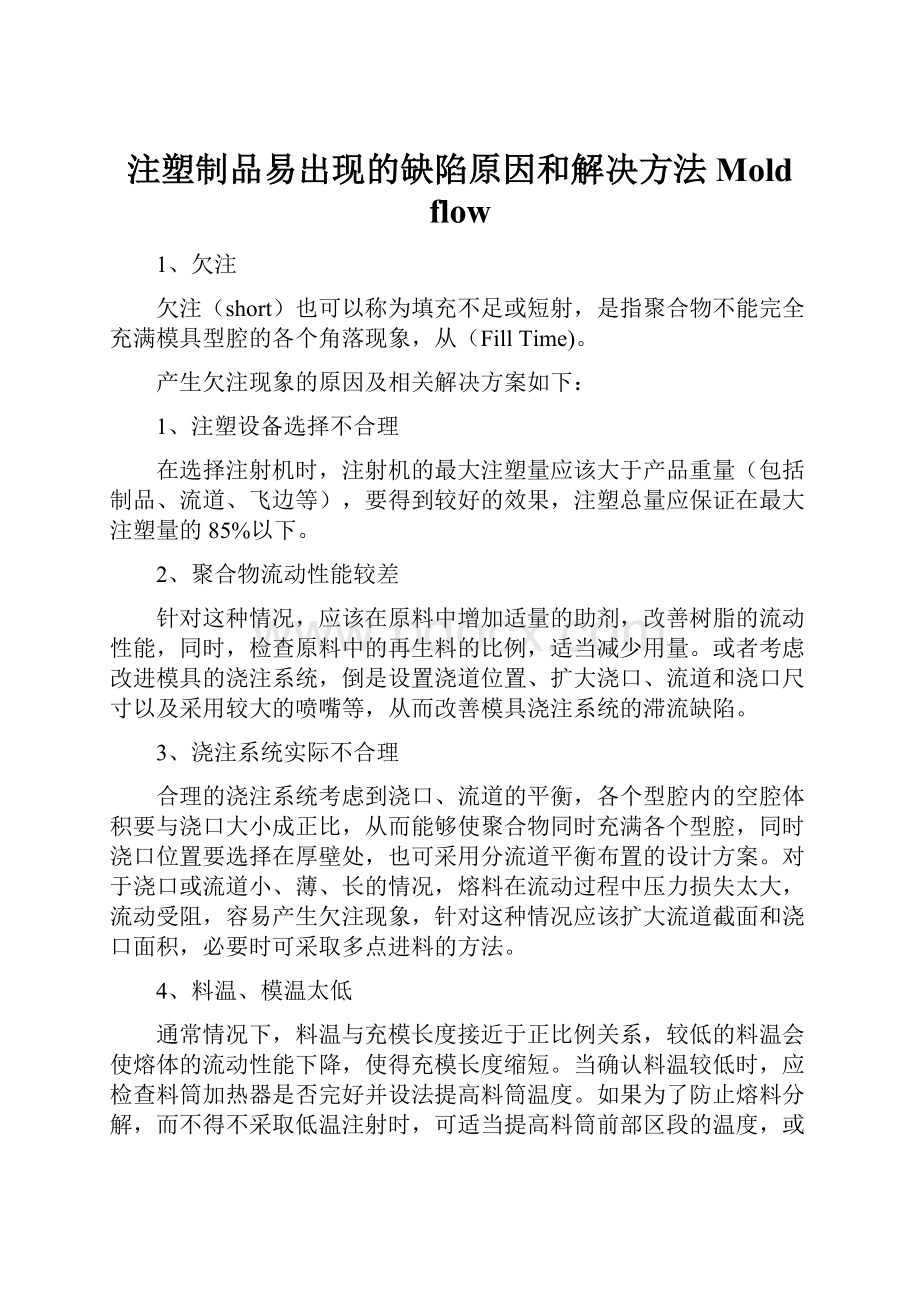
注塑制品易出现的缺陷原因和解决方法Moldflow
1、欠注
欠注(short)也可以称为填充不足或短射,是指聚合物不能完全充满模具型腔的各个角落现象,从(FillTime)。
产生欠注现象的原因及相关解决方案如下:
1、注塑设备选择不合理
在选择注射机时,注射机的最大注塑量应该大于产品重量(包括制品、流道、飞边等),要得到较好的效果,注塑总量应保证在最大注塑量的85%以下。
2、聚合物流动性能较差
针对这种情况,应该在原料中增加适量的助剂,改善树脂的流动性能,同时,检查原料中的再生料的比例,适当减少用量。
或者考虑改进模具的浇注系统,倒是设置浇道位置、扩大浇口、流道和浇口尺寸以及采用较大的喷嘴等,从而改善模具浇注系统的滞流缺陷。
3、浇注系统实际不合理
合理的浇注系统考虑到浇口、流道的平衡,各个型腔内的空腔体积要与浇口大小成正比,从而能够使聚合物同时充满各个型腔,同时浇口位置要选择在厚壁处,也可采用分流道平衡布置的设计方案。
对于浇口或流道小、薄、长的情况,熔料在流动过程中压力损失太大,流动受阻,容易产生欠注现象,针对这种情况应该扩大流道截面和浇口面积,必要时可采取多点进料的方法。
4、料温、模温太低
通常情况下,料温与充模长度接近于正比例关系,较低的料温会使熔体的流动性能下降,使得充模长度缩短。
当确认料温较低时,应检查料筒加热器是否完好并设法提高料筒温度。
如果为了防止熔料分解,而不得不采取低温注射时,可适当提高料筒前部区段的温度,或者加快注塑的速度,减少聚合物冷却的时间,但是同时应该注意,注射速度过快可能引起熔体破裂而形成皱纹缺陷。
较低的模温会导致熔融聚合物过早地冷却,从而无法填充整个型腔。
针对这种情况,应该将模具加热到满足工艺要求的温度,并且在注塑初期,应减少冷却介质的流量。
如果模具温度始终较低,应该改变冷却系统的设计方案。
5、注塑喷嘴温度低
在注射过程中,喷嘴与模具直接接触,由于模具温度一般低于喷嘴温度,且温差较大,两者频繁接触后使喷嘴温度下降,导致熔料在喷嘴处冷凝(又称干尖)。
为防止冷料进入型腔后立即凝固,阻塞后面的热熔料无法充满型腔,可以考虑在流道上开冷料穴,同时在开模时保证喷嘴与模具分开,减少模温对喷嘴温度的影响。
6、注塑压力、保压不足
注塑压力与充模长度也接近于正比的关系,注塑压力小会造成充模长度短,出现欠注现象。
在这种情况下,可通过减慢射料杆前进速度,适当延长注射时间等办法,来提高注射压力。
在注射压力无法进一步提高的情况下,也可通过适当提高料温(这时的料温不至于使熔料分解)以降低熔料黏度,从而提高熔体流动性能来补救。
此外,如果保压时间太短,也会出现欠注现象。
因此,选择适当的保压时间(一般控制在30~120s,对于厚壁制品可适当提高)可以防止欠注现象。
与此同时,也应该注意到,过长的保压时间还会引起制品的自动脱落的困难。
7、制品结构设计不合理
当制品在整体尺寸方面比例失调(例如厚度与长度不成比例),或者是制品形状复杂且成型面积较大时,熔体很容易出现在塑件的薄壁处流动受阻,出现填充不足的现象。
因此在设计塑件的形体结构时,应注意塑件的厚度与熔体充模时的极限流动长度有关。
有关资料显示,熔体的极限流动长度与塑件壁厚的比值如表2-1所示。
表2-1充模过程中熔体极限流动长度与塑件厚度的比值
树脂类别
极限流动长度/厚度
树脂类别
极限流动长度/厚度
LDPE
280:
1
PA
150:
1
PP
250:
1
POM
145:
1
HKPE
230:
1
PMMA
130:
1
PS
200:
1
PVC
100:
1
ABS
190:
1
PC
90:
1
在注塑中,塑件的厚度一般为1~3mm,大型塑件的为3~6mm,通常塑件厚度超过8mm或者小于0.5mm都是对注塑成型不利的。
此外,在复杂结构塑件成型时,在工艺上也需要采用必要的措施,例如适当调整流道布局,合理确定浇口位置,提高注射速度,提高模温、料温,选用流动性能较好的树脂等。
8、排气不良
排气不良会造成大量气体残留在模具型腔内,从而受到流料的挤压,产生较大的压力,当压力大于注射压力时,就会阻碍熔体的充模,导致欠注现象的发生。
针对这种现象,应检查冷料穴是否设置或者位置是否合理,对于深型腔模具,应在发生欠注的部位设置排气槽或排气孔;排气槽可以开在模具的分型面上,深度一般为0.02~0.04mm,宽度为5~10mm,而排气孔应设置在型腔的最终充模处。
对于易挥发或者是含水量较大聚合物,应该在注塑前清除易挥发成分或进行干燥处理。
利用改变模具系统工艺参数的方法,也可以改善排气不良的现象。
例如提高模温、降低射速、减小合模力及加大模具间隙等措施。
2、溢料
溢料(Flashing)也称飞边,当熔体进入模具的分型面,或者进入与滑块相接触的面及模具其他零件的空隙内时,就会发生溢料现象。
溢料产生的原因和相关的解决方法如下。
1、锁模力较低
如果锁模力低于或接近注射压力,会造成模具分型面的密闭不良,从而产生溢料飞边的现象。
对于产生飞边的情况,应该首先校验锁模力与模具型腔内的成型力,成型力的计算为分型面的投影面积与注射压力的乘积,如果锁模力小于腔内成型力,则表明锁模力不足或注射压力太高。
对此,应该降低注射压力或减小浇口截面积,也可以缩短保压及增压时间,缩短推料杆,行程,减少型腔数及选用锁模力更大的注塑设备。
2、模具问题
产生溢料的基本原因除了锁模力低之外,多数情况是模具存在问题。
当较多的溢料飞边出现时,应检查模具的装配精度和分型面是否紧密贴合(有无粘附物或落入异物),使动模与定模对中,型腔及隙芯部分的滑动件磨损间隙是否超差,各模板是否平行,有无弯曲,模板的开距是否按模具厚度调节到正确位置,导合销表面是否损伤,拉杆是否变形不均匀,排气槽孔是否太大、太深,等待。
根据检查结果,可以采用机械方法排除误差。
3、注塑工艺不当
注塑工艺控制不当也会造成溢料飞边的出现,例如注射速度太快,注射时间过长,注射压力在型腔中分布不均,充模速率不均衡,以及加料过多,润滑剂使用过量都会导致溢料飞边。
除此之外,熔融聚合物的温度太高,黏度小,流动性能加强,都可能使熔体注入模具内的零件间隙产生溢料飞边。
排除溢料飞边应该先从排除模具故障着手,如果溢料飞边而改变成型条件或原料配方,往往对其他方面产生不良影响,容易引发其他成型故障。
3、凹陷及缩痕
凹陷及缩痕(SinkMark)是注塑制品表面产生凹坑、陷窝或者是收缩痕迹的现象。
凹陷及缩痕是熔体冷却固化时体积收缩而产生的,它容易发生在制品厚壁的部分或加强筋和凸台的背面,以及直浇口的背面等壁厚不同的部分。
凹陷及缩痕产生的原因和相关的解决方法如下。
1、模具缺陷
产生凹陷及缩痕的情况很多是由于模具设计不合理导致的,例如模具的流道及浇口截面太小,充模阻力太大;浇口设置不对称,充模速度不均衡;进料口位置不合理,以及模具排气不良影响进料、补缩和冷却或模具磨损引起释压等。
对此,应该适当扩大浇口及浇道截面,浇口位置尽量设置在对称处,进料口设置应设置在塑件厚壁部位。
如果凹陷及缩痕远离浇口,其原因很可能是由于模具结构尺寸,特别是对于阻碍熔体流动的“瓶颈”处可以增加流道截面或者直接将流产延伸到产生缺陷的部位。
对于厚壁制品,可以采用扇形浇口或是平缝浇口,从而将塑件的凹陷及缩痕等缺陷转移到浇口上。
2、注塑工艺不当
注射压力过低、注射及保压时间过短、注射速度过慢、料温及模温过高、制品冷却不足、脱模时温度太高、嵌件处温度太低或供料不足,都会引起塑件表面出现凹陷。
对此,应适当提高注射压力及注射速度,增加熔料的压缩密度,延长注射和保压时间,补偿熔体的收缩。
同时保压不能太高,否则会引起凸痕。
对于浇口附近的凹陷,可以通过延长保压时间来解决。
对于塑件壁厚处的凹陷,应适当延长塑件在模内的冷却时间。
对于模具嵌件周围的凹陷及缩痕,应设法提高嵌件温度,减小嵌件与熔体的温差。
对于由于供料不足引起的表面凹陷。
可以通过调节料筒温度,适当降低冷却水温度,以及在保持模具表面及各部位均匀冷却的前提下,对凹陷部位适当强化冷却的方法来实现。
3、注塑原料不符合要求
成型原料的收缩率太大或流动性能太差,或者是原料内润滑剂不足及原料潮湿,都会引起凹陷及缩痕缺陷。
对于表面要求比较高的制品,应尽量选用低收缩率的树脂。
对于原料流动不畅引起欠注凹陷,可在原料中增加扣量的润滑剂改善熔体的流动特性,或加大浇注系统结构尺寸。
对于潮湿的原料应进行预干燥处理。
4、注塑制品结构设计不合理
壁厚相差很大的注塑制品,在厚壁处很容易出现凹陷及缩痕,对此,设计塑件形体尺寸结构时,应尽量保证壁厚的一致性。
4、气穴
气穴(AirTrap)也称作气泡或气孔,它是在成型制品内部所形成的空隙。
根据气穴形成的原因,可以把它分成两类:
●由于排气不良等原因造成熔体中的水分或挥发成分被封闭在成型材料中所形成的气泡;
●由于熔体冷却固化时体积收缩而产生在制品厚壁或加强筋、凸台等壁厚不均匀处的气泡。
下面介绍气穴产生的原因和相关的解决方法。
1、注塑工艺不当
注塑工艺参数对气穴的产生有直接的影响。
例如,注射速度快、注射时间和周期短、注射压力低、加料过多或过少、保压不够、冷却不均匀或冷却不足,以及料温和模温控制不当,都会引起塑件内产生气穴。
尤其是高速注塑过程中,气体来不及排出模具型腔,会导致熔体内残留较多的气体。
对此,应适当降低注射速度,保持型腔内合理的压力,从而在保证排气通畅和不发生欠注的基础上,消除气穴现象。
此外,针对上面其他情况,可以通过调整注射和保压时间、加强冷却效果、控制进料量等方法来避免气穴。
在调整模温和料温的时候,为防止熔体降聚分解,产生大量气泡,应注意温度不要太高;但是温度太低又会造成充模困难,塑料制品中易形成空隙和气泡。
因此,应将熔体温度控制得低一些,而模温控制得高一些,在这样的条件下,既不会产生大量气体,又不会产生缩孔。
2、模具缺陷
模具方面存在的缺陷会造成气穴现象,例如浇口位置不正确、浇口截面太小、流道狭长、流道内有驻气死角和不良。
对此,应该主要考虑调整模具结构,将浇口位置放在塑件厚壁处;加大浇口截面,在一模多腔,且成型制品形状不同时,应注意浇口截面与各形状塑件重量成比例,否则,较大的塑件易产生气泡;减少狭长的流道;消除流道中的驻气死角;改善模具排气情况。
3、注塑原料不符合要求
在气泡产生的情况下,应该充分干燥原料,消除水分,适当降低料温防止熔体热分解,减少原料中的挥发成分。
5、熔接痕
熔接痕(WeldLine)属于产品表观质量缺陷,它是产品注塑过程中两股以上的熔融树脂流相汇合所产生的细线状缺陷。
其产生原因及相关解决方法如下。
1、熔体流动性不足,料温较低
在低温的情况下,聚合物熔体的流动、汇合性能降低,容易发生熔接痕现象。
对此,可以适当提高料筒和注塑喷嘴的温度,同时降低冷却介质的流速、流量,保证一定的模温。
一般情况下,熔接痕部位强度较差,通常可以通过局部加热的方法提高制品发生熔接痕部位的温度,从而保证塑件的整体强度。
对于必须采用低温成型的情况,可以适当提高注塑压力和速度,从而增加熔体流动性能和汇合能力,也可以采用增加润滑剂的方法,提高熔体流动性能。
2、模具缺陷
由于熔接痕主要产生于熔体的分流汇合,因此,模具的浇注系统对于熔接痕的产生有很大的影响。
对此,在模具设计的过程中,应该尽量减少浇口的数量,合理设置浇口位置,加大浇口截面积,设置辅助流道及分流流道。
在模具设计中,应该注意设计冷料穴,防止低温熔体注入,产生熔接痕。
在熔接痕的产生的位置,由于冲模压力高往往会产生飞边的情况,可以很好地利用飞边,在飞边处开一很浅的沟槽,将熔接痕转移到飞边上,并在注塑结束后,将飞边去除。
3、塑料制品结构设计不合理
塑件薄壁、厚薄悬殊或是嵌件过多都有可能产生熔接痕。
在熔体冲过程中,由于薄壁位置充模阻力较大,因此熔体分流总是在薄壁处汇合,并产生熔接痕。
而且,熔接痕部位强度降低,会导致塑件在薄壁处出现断裂。
对此,在设计过程中,要保证塑件的一定壁厚,并尽量保持塑件壁厚的一致性。
4、模具排气不良
熔接痕的位置与合模线或嵌件缝隙相距较远,并且排气孔设置不当,这时多股熔体流汇聚赶压的空气无法排出,气体在高压下释放大量热能,导致熔体分解,从而出现黄色或黑色的碳化点。
这种情况下,塑件表面熔接痕附近总是会反复出现这类斑点。
产生的原因就是模具的排气不良。
对此,应该首先检查排气孔情况,如果排气孔无阻塞物,则应在熔接痕出现位置处,增加排气孔,可者是重新定位浇口或适当降低合模力,以方便排气。
5、脱模剂使用不当
注塑过程中,一般仅在螺纹等不易脱模的部位才少量使用脱模剂,脱模剂用量不合理,会引起塑件表面产生熔接痕。
6、翘曲及扭曲
翘曲和扭曲(Warpage)都是脱模后产生的制品变形。
沿边缘平行方向的变形称之为翘曲,沿对角线方向上的变形称之为扭曲,
下面介绍翘曲和扭曲产生的原因和解决方法
1、冷却不当
塑料制品由于模具的冷却系统设计不合理或模具温度控制不当而造成的冷却不足,都会导致制品的翘曲变形。
壁厚差异较大的塑料制品,由于各部分的冷却收缩不一致,尤其容易翘曲。
对此,塑件的设计应尽量保证壁厚的均匀性。
另外,对于材料热传导性能较差的材料,一定要在模具内保持足够的冷却定型时间,从而保证塑件中心的完全冷却。
在模温控制方面,可以合理地调整阳模与阴模、型芯和模壁等零件之间的温差,来实现对制品各部位收缩速度的控制,从而抵消分子取向收缩,避免制品的翘曲变形。
2、分子取向不均衡
塑料制品的翘曲变形在很大程度上是由聚合物分子取向程度不同造成的。
在充模过程中,大多数聚合物分子将沿着充模流动方向排列,这样就会造成沿熔体流动方向上的分子取向大于垂直流动方向上的分子取向。
在充模完成后,分子试图恢复卷曲的状态,导致塑件有在该方向上缩短的趋势。
因此,在两个方向上的收缩不均衡,导致了塑料制品的翘曲变型。
对此,可以采用降低熔体温度和模温的方法来减少流动取向并缓和取向应力在经过一段时间后释放出来,还会造成翘曲变形。
热处理的方法可以是将成型的塑件立即放入37~43度的温水中缓慢冷却。
3、模具浇注系统设计有缺陷
模具浇注系统的设计会影响熔体的流动性、塑件内应力和热收缩变形,因此合理地设计浇口位置和类型可以较大程度地减少塑件变形,在设计中应该注意以几点:
●为使型芯两侧均匀受力,浇口位置不能使熔体直接冲击型芯;
●对于面积较大的矩形扁平塑件,如果材料的分子取向和收缩较大,应采用薄膜式浇口或多点侧浇口,而尽量不要采用直浇口或分布在一条线上的点浇口;
●对于圆片形制品,应采用中心直浇口或多点式浇口,不要采用侧浇口;
●对于壳形制品,要采用直浇口,不要采用侧浇口。
4、脱模系统不合理
脱模过程中,不合理的、较大的不均衡外力会造成塑件的翘曲变形,对此,要保证制品足够冷却固化之后,再进行脱模。
5、成型条件设置不当
在注塑过程中,注射压力太低、注射速度太慢、保压时间不够、熔体塑化不均匀都会造成塑件的翘曲变形。
7、波流痕
波流痕(FlowMark)是指熔体流的痕迹以浇口为中心呈现出条纹花样。
根据其产生的原因和不同的外观特点,可以将波流痕分为3类。
1、以浇口为中心的年轮状波流痕
这种类型的波流痕主要是由于熔体流动不良引起的。
由于温度低、黏度高,当流动性能较差的熔料在浇口及流道中以半固化波动状态注入型腔后,熔体沿型腔表面流动并被不断注入的后续熔体挤压形成回流及滞流,从而在塑件表面产生以浇口为中心的年轮状波流痕。
对此,可通过提高模温及喷嘴温度,提高注射速率,增加注射压力及保压和增压时间,或者在浇口处设置加热器增加浇口部位的局部温度等方法来解决波流痕。
浇口及流道截面最好采用圆形,这种截面能够获得最佳充模效果。
但是,如果在塑件强度相对薄弱的区域设置浇口,应采用边浇口。
此外,还可以在浇口底部及分流道端部设置较大的冷料穴,料温对熔料的流动性能影响越大,越要注意冷料穴尺寸的大小,冷料穴的位置必须设置在熔料沿注料口流动方向的端部。
2、塑件表面的螺旋状波流痕
这种类型的波流痕主要是熔体在流道中流动不畅所导致的。
当熔体从狭小的流道截面流入较大截面的型腔或者是流道狭窄、光洁度很差时,熔体很容易形成湍流,导致塑件表面形成螺旋状波流痕、
对此,可适当降低注射速度或对注射速度采取慢、快、慢分级控制。
模具的浇口应设置在厚壁部位或直接在壁侧设置浇口,浇口形式最好采用护耳式、扇形或薄片式。
也可适当扩大流道及浇口截面,减少流料的流动阻力。
此外,也可以通过调节模具内冷却水的流量,保持较高的模温,或者是工艺操作温度范围内适当提高料筒及喷嘴温度,来改善熔体的流动性能。
3、塑件表面的云雾状波流痕
这种类型的波流痕主要是由挥发性气体导致的。
当采用ABS或其他共聚型树脂原料时,若加工温度较高,树脂及润滑剂产生的挥发性气体会使塑件表面产生云雾状波流痕。
对此,可以适当降低模具及机筒温度,改善模具的排气条件降低料温及充模速率,适当扩大浇口截面,或者考虑更换润滑剂。
8、裂纹
裂纹(Cracking)是指在成型制品表面出现的头发丝状的小裂纹和小裂痕。
其产生原因及相关解决方法如下。
1、残余应力太高
当塑件内的残余应力高于树脂的弹性极限时,塑件表面就会产生裂纹及破裂。
一般情况下,浇口附近最容易发生由残余应力引起的裂纹,因为浇口处的成型压力相对其他部位要高一些,特别是主流道为直浇口的情况。
此外,当塑件的壁厚不均匀、熔体的冷却速度不一致时,会造成厚薄部位的收缩量不同,从而产生相互拉伸,也会出现残余应力。
由于残余应力是影响塑件裂纹的主要原因,因而可以通过减少残余应力来防止塑件产生裂纹及破裂。
减少残余应力的主要方法是改进浇注系统的结构形式和调整好塑件的成型条件。
在浇注系统设计中,可采用压力损失最小,而且可承受较高注射压力的直浇口,可将正向浇口改为多个针形点浇口或侧浇口,并减小浇口直径。
设计侧浇口时,可以采用凸片式浇口,将裂纹转移到成型后要去除的部位。
此外,在浇口周围合理采用环状加强筋也可减少浇口处的裂纹。
在成型条件方面,减少残余应力的最简便的方法就是降低注射压力,因为注射压力与残余应力呈正比例关系。
如果塑件表面产生的裂纹四周发黑,即表明注射压力太高或加料量太少,应当降低注射压力或增加供料量。
对于低料温、低模温、高注射压力的成型条件,应适当提高料筒及模具温度,减少熔体与模具的温差,控制模内型胚的冷却时间和速度,使取向的分子链有较长的恢复时间。
此外,在保证补料充足,不使塑件产生收缩凹陷的前提下,可适当缩短保压时间,因为过长的保压时间也容易产生残余应力引起裂纹。
2、外力导致残余应力集中
塑件在脱模过程中,由于顶杆及模具脱模斜度设计不合理,都会由于外力作用导致应力集中,使塑件表面产生裂纹。
对于裂纹发生在顶杆周围的现象,应认真检查和校调顶出装置,顶杆应设置在脱模阻力最大的部位,如凸台、加强筋等处。
如果模具型腔的脱模斜度不够,塑件表面也会出现擦伤形成的褶皱花纹。
一般情况下,脱模斜度应大于0.85%,小型塑件的脱模斜度为0.1%~0.5%,大型塑件的脱模斜度可达2.5%。
3、塑件结构设计不合理
制品结构中的尖角及缺口处最容易产生应力集中,从而导致塑件表面产生裂纹。
对此,塑件形体结构中的外角及内角都都应尽可能做成圆角。
实验表明,最佳的过渡圆弧半径与转角处壁厚的比值为1:
1.7,即转角处的圆弧半径为壁厚的0.6倍。
在设计中,对于必须设计成尖角和锐边的部位仍然要采用0.5mm的最小过渡圆角,这样可以延长模具的寿命。
9、银丝纹
银丝纹(Splay)是在塑件表面或表面附近,沿着熔体流动方向出现的闪闪发光的银白色条纹,它是树脂中的气体移动到成型表面,并被压碎所产生的现象。
熔体中含有的挥发物质是产生银丝纹的主要原因。
排除银丝纹应从以下几个方面着手。
●对于降解银丝,要尽量选用粒径均匀的树脂,筛除原料中的粉屑,减少再生料的用量,清除料筒中的残存异料;对于水气银丝,要按照要求,充分干燥原料。
●在成型工艺方面,对于降解银丝纹,应降低料筒及喷嘴温度,缩短熔体在料筒中的滞留时间防止熔体局部过热,也可降低射料杆转速及前进速度,缩短增压时间;对于水气银丝,应调高背压,加大螺杆压缩比,降低螺杆转速或使用排气型螺杆。
●在模具设计和操盘方面,对于降解银丝纹,应加大浇口、主流道及分流道截面,扩大冷料穴,改善模具的排气条件;对于水气银丝,应增加模具排气孔或采用真空排气装置,尽量排清熔料中存留的气体,并检查模具冷却水道是否渗漏,防止模具表面过冷结霜以及表面潮湿,如果模具的型腔表面有水分,塑件表面就会出现白色的银丝痕迹。
Moldflow分析结果
较为均衡的填充过程在Filltime结果中主要体现在两个方面:
●熔体基本上在同一时刻到达型腔各端部;
●以等值线形式显示的结果中,等值线间距比较均匀,因为同一结果中稀疏的等值线表示流速缓和,密集的等值线表示流速湍急。
通过Bulktemperature(endoffilling)的显示结果,可以发现产品在注塑过程中温度较高的区域,如果最高平均温度接近或超过聚合物材料的降解温度,或者是出现局部过热Hotspot的情况,都需要重新设计浇注、冷却系统,或者改变工艺参数。
产品经过冷却的最高温度应该低于设定的产品顶出温度。
在过程参数设置中。
回路中的冷却介质的升温应该小于2~3度。