化工原理实验设计资料.docx
《化工原理实验设计资料.docx》由会员分享,可在线阅读,更多相关《化工原理实验设计资料.docx(20页珍藏版)》请在冰豆网上搜索。
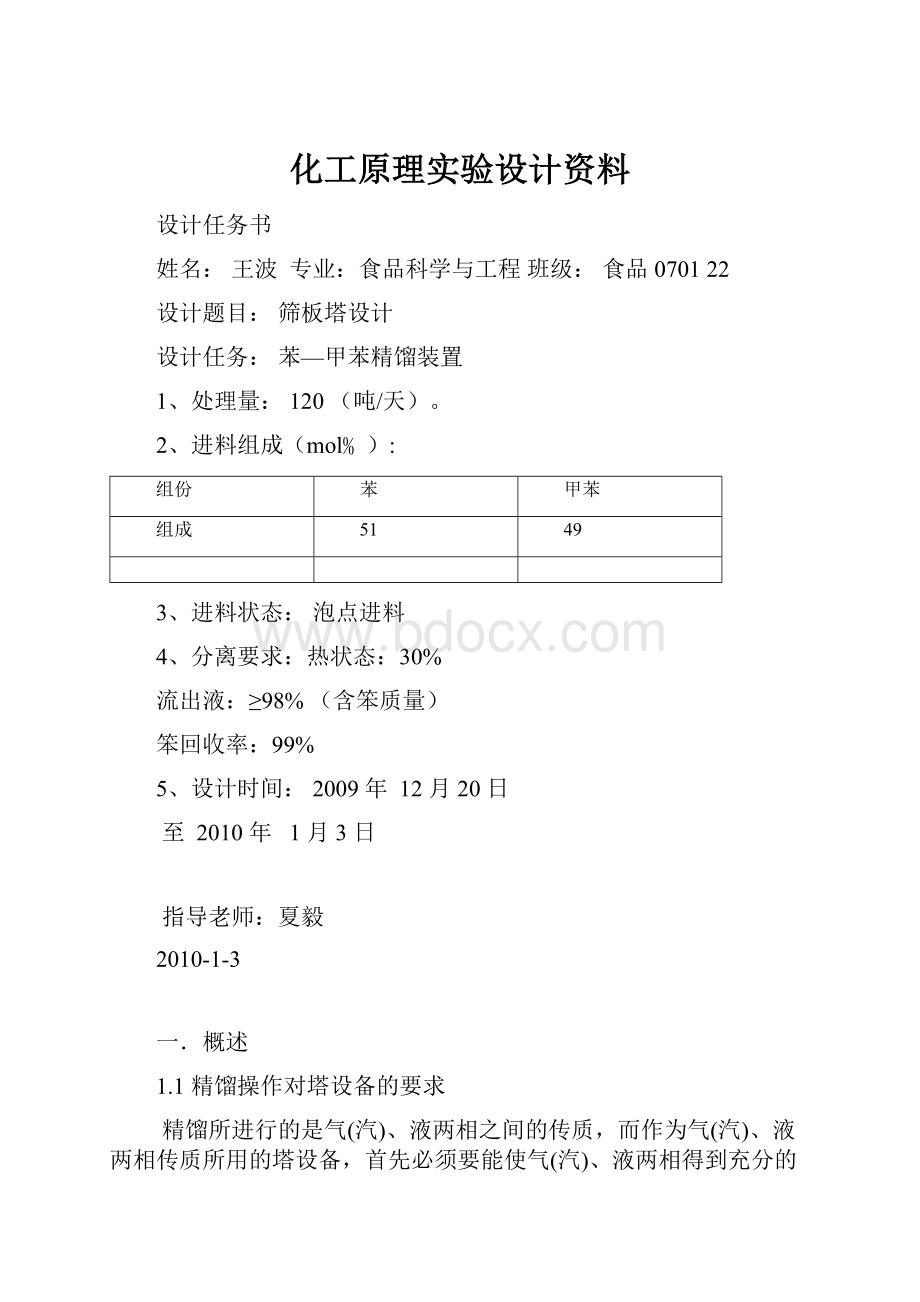
化工原理实验设计资料
设计任务书
姓名:
王波专业:
食品科学与工程班级:
食品070122
设计题目:
筛板塔设计
设计任务:
苯—甲苯精馏装置
1、处理量:
120(吨/天)。
2、进料组成(mol﹪):
组份
苯
甲苯
组成
51
49
3、进料状态:
泡点进料
4、分离要求:
热状态:
30%
流出液:
≥98%(含笨质量)
笨回收率:
99%
5、设计时间:
2009年12月20日
至2010年1月3日
指导老师:
夏毅
2010-1-3
一.概述
1.1精馏操作对塔设备的要求
精馏所进行的是气(汽)、液两相之间的传质,而作为气(汽)、液两相传质所用的塔设备,首先必须要能使气(汽)、液两相得到充分的接触,以达到较高的传质效率。
但是,为了满足工业生产和需要,塔设备还得具备下列各种基本要求:
(1)气(汽)、液处理量大,即生产能力大时,仍不致发生大量的雾沫夹带、拦液或液泛等破坏操作的现象。
(2)操作稳定,弹性大,即当塔设备的气(汽)、液负荷有较大范围的变动时,仍能在较高的传质效率下进行稳定的操作并应保证长期连续操作所必须具有的可靠性。
(3)流体流动的阻力小,即流体流经塔设备的压力降小,这将大大节省动力消耗,从而降低操作费用。
对于减压精馏操作,过大的压力降还将使整个系统无法维持必要的真空度,最终破坏物系的操作。
(4)结构简单,材料耗用量小,制造和安装容易。
(5)耐腐蚀和不易堵塞,方便操作、调节和检修。
(6)塔内的滞留量要小。
实际上,任何塔设备都难以满足上述所有要求,况且上述要求中有些也是互相矛盾的。
不同的塔型各有某些独特的优点,设计时应根据物系性质和具体要求,抓住主要矛盾,进行选型。
1.2设计题目
苯—甲苯精馏装置
1.3设计要求
原谅处理量:
12吨/天
原谅浓度:
51%
热状态:
30%
流出液:
≥98%(含笨质量)
笨回收率:
99%
回流比是最小回流比的1.6
1.4设计步骤
1.收集基础数据
2.工艺流程选择
3.全塔物料衡算
4.确定操作条件
5.确定回流比
6.理论板数与实际板数
7.冷凝器和再沸器的热负荷
8.初估冷凝器和再沸器的传热面积
9.塔径计算及板间距确定
10.堰及降液管设计
11.塔板布置及筛板塔的主要结构参数
12.筛板塔的水力学计算
13.塔盘结构
14.塔高的计算
二具体步骤
2.1基础数据
原谅处理量:
12吨/天
原谅浓度:
51%
热状态:
30%
流出液:
>=98%(含笨质量)
苯回收率:
99%
冷却介质及其温度、加热介质及温度:
冷却介质:
水30℃
加热介质:
蒸汽100℃
2.2工艺流程的选择
精馏装置一般包括塔顶冷凝器,塔釜再沸器,原料预热器及流体输送泵等。
流程选择应结合实际进行,考虑经济性、稳定性。
如进料是否需要预热、冷凝器的型式及布置、及再沸器的型号等。
当塔顶需汽相出料时,采用分凝器,除此之外,一般均采用全凝器。
对于小塔,通常将冷凝器放于塔顶,采用重力回流。
对于大塔,冷凝器可放至适当位置,用泵进行强制回流。
再沸器的型式有立式与卧式、热虹吸式与强制循环式之外。
当传热量较小时,选用立式热式再沸器较为有利。
传热量较大时,采用卧式热虹吸式再沸器。
当塔釜物料粘度很大,或易受热分解时,宜采用泵强制循环型再沸器。
几种再沸器型式如图1所示。
精馏装置中,塔顶蒸汽的潜热和塔釜残液的显热可以被用于预热进料。
塔顶蒸汽潜热大,而温度较低,塔釜残液温度高,而显热的热量少。
在考虑这些热量的利用时要注意经济上的合理性及操作上的稳定性。
2.3全塔物料衡算
2.4确定操作条件(压力、温度)
精馏操作最好在常压下进行,不能在常压下进行时,可根据下述因素考虑加压或减压操作。
(1)、对热敏性物质,为降低操作温度,可考虑减压操作。
(2)、若常压下塔釜残液的泡点超过或接近200℃时,可考虑减压操作。
因为加热蒸汽温度一般低于200℃。
(1)立式热虹吸型
(2)泵强制循环型
(a)(b)
(3)卧式再沸器
(3)、最方便最经济的冷却介质为水。
若常压下塔顶蒸汽全凝时的温度低于冷却介质的温度时可考虑加压操作。
还应该指出压力增大时,操作温度随之升高,轻、重组分相对挥发度减少,分离所需的理论板数增加。
在确定操作压力时,除了上面所述诸因素之外,尚需考虑设备的结构、材料等。
(1)、选择冷却介质,确定冷却介质温度。
最为方便、来源最广的冷却介质为水。
设计时应了解本地区水的资源情况及水温。
(2)确定冷却器及回流罐系统压力
。
塔顶蒸汽全部冷凝时的温度一般比冷却介质温度高10~20℃。
冷却器和回流罐系统压力即为该温度下的蒸汽压(平衡压力),可由泡点方程式得。
式中
—平衡指数。
(3)、确定塔顶和塔釜压力。
塔顶压力
等于冷凝器压力
加上蒸汽从塔顶至冷凝器的流动阻力
,即
塔釜压力
等于塔顶压力加上全塔板阻力
塔。
全塔阻力
塔等于塔板阻力乘实际板数,即
2.8初估冷凝器和再沸器的传热面积
传热面积A可由传热方程计算,即
(15)
式中:
Q—热负荷。
K—传热系数。
—冷热流体平均温度差。
对于低沸点烃类,冷凝介质为水时,传热系数为390~980(千卡/
·时·℃)。
加热介质为水蒸汽时,再沸器的传热系数为390~880(千卡/
·时·℃)。
⑴再沸器
因为蒸汽温度 ts(℃)=130,釜液进口温度 t1'(℃)=100,釜液出口温度 t2'(℃)=110,
所以传质温差Δtm(℃)=[(ts-t1')-(ts-t2')]/ln[(ts-t1')/(ts-t2')]= 24.66,
因为传质系数 K1(W/m^2/K)=300,
所以传质面积 A(m^2)=Qr/K/Δtm=157.64。
⑵冷凝器
因为蒸汽进口温度 T1(℃)=100,蒸汽出口温度 T2(℃)=80,冷却水的进口温度t1=25℃, 冷却水的出口温度 t2=70℃,
所以传质温差Δtm'(℃)=(Δt1-Δt2)/ln(Δt1/Δt2)= 41.24,
因为 K2(W/m^2/K)=250,
所以,传质面积 A'(m^2)=Qc/K2/Δtm'=118.68。
1.9塔径的计算及板间距的确定
因为液流量不大,所以选取单流型,因为提馏段液相流量较大,所以以提馏段的数据确定全塔数据更为安全可靠。
查表得,液态苯的泡点密度ρa(Kg/m^3)=792.5,
液态甲苯的泡点密度ρb(Kg/m^3)=790.5,
根据公式 1/ρl=x1/ρa+(1-x1)/ρb 得,
液相密度ρl(Kg/m^3)=791.1
根据公式 苯的摩尔分率=(y1'/78)/[yi'/78+(1-yi')/92]
M’=苯的摩尔分率*M 苯+甲苯的摩尔分率*M 甲苯
ρv=M’/22.4*273/(273+120)*P/P0 得
气相密度ρv(Kg/m^3)=2.74。
气液流动参数,Flv=Lh/Vh*(ρl/ρv)^0.5=0.13,
根据试差法,设塔径 D(m)=1.2,根据经验关系:
可设板间距 Ht=0.45m,
清液层高度 Hl取为50mm,
所以液体沉降高度 Ht-hl=0.4m。
根据下图
可查得,气相负荷因子 C20= 0.065,
液体表面张力δ(mN/m),100℃时, 查表 苯 18.85 甲苯 19.49
所以,平均液体表面张力为 19.26,
根据公式:
C=C20×[(δ/20)^0.2]得,C= 0.0645.
所以,液泛气速 u=C×[(ρl-ρv)^0.5]/[ρv^0.5]=1.09m/s。
设计气速 u'=u=(0.6~0.8)×u=0.766m/s,
设计塔径 D'=(Vs/0.785/u)^0.5=1.19m,根据标准圆整为1.2m,
空塔气速 u=0.785*Vs/D/D=0.469m/s.
10、堰及降液管的设计
⑴确定降液管结构
塔径 D(mm) 1200
塔截面积 At(m^2) 查表 1.31
Ad/At (Ad/At)/% 查表 10.2
lw/D lw/D 查表 0.73
降液管堰长 lw(mm) 查表 876
降液管截面积的宽度 bd(mm) 查表 290
降液管截面积 Ad(m^2) 查表 0.115
底隙 hb(mm), 一般取为 30~40mm,而且小于 hw,本设计取为30mm,
溢流堰高度 hw(mm), 常压和加压时,一般取 50~80mm.本设计取为60mm,
⑵降液管的校核
单位堰长的液体流量,(Lh/lw) (m^3/(m.h))=27.48,
不大于100~130,符合要求
堰 上 方 的 液 头 高 度
how(mm) = 2.84*0.001*E*[(Lh/lw)^0.66667] =25.86,
式中,E 近似取1, how=25.86mm,符合要求。
底隙流速,ub(m/s) =Ls/lw/hb=0.254,而且不大于 0.3~ 0.5,符合要求。
液体在塔板上的流动型式单溢流、双溢流和多溢流。
当塔径小于2米时,通常采用单溢流,塔径在2米~4米时采用双溢流,塔径大于4米时,一般应考虑采用多溢流。
(如下图)
a.单溢流b.四溢流c.双溢流
2.12、筛板塔的水力学计算
12-1塔板阻力
(1)气相通过塔板的阻力为干板阻力与液层阻力之和。
即
(41)
式中:
hP—气体通过每一层塔板的阻力,m液柱;
hC—干板阻力,m液柱;
h1—塔板上的液层阻力,m液柱。
筛孔塔板的干板可用下式计算。
(a)
由于do/﹠=51s=1.67查图得
=0.772
将数据带入a式求得hC=0.0353m液柱
(2)雾沫夹带
雾沫夹带量的计算有两类,一类直接用板上参数表,如下式:
(b)
hf=2.5hL=2.5×0.06=0.15m
将hf=0.15m带入b式求得ev=0.009kg液/kg气<0.1
故本设计中液沫夹带是在允许范围内的
(3)液泛的校核
降液管内液面的高度按下式计算。
式中:
—降液管液面的高,m;
—液体在降液管出口阻力,按式(49)计算;
=0.0009m液柱
为了避免液泛,降液管中液面高不得超过(0.4~0.6)倍的(
),即
≤(0.4~0.6)(
)
因此设计的是符合要求的,不会发生液泛现象
(4)液体在降液管的停留时间
为使降液管中液体的气泡能够脱除,液体在降液管的停留时间不得少于3~5秒,即
≥3~5(51)
(5)负荷性能图
对于一个结构已定的塔板,将有一个适宜操作区。
它综合地反映了塔板的操作性能,把不同的气、液流率下塔板上出现的各种流体力学的界限综合地表达出来。
上述反映气、液负荷和塔板性能的关系图称为负荷性能图。
负荷性能图的作法如下:
(1)、按式
作漏液线①;
(2)、按式
取泛点率为(65~82﹪)时作雾液夹带线②;
(3)、按式
取Hd=(0.4~0.6)(HT+Hw)时作液泛线③;
(4)、按式
≥3~5作最大液量线④;
(5)、按式
作量小液量线⑤。
(式中:
L—液体流率,m3/h;
—堰长,m;E—液流收缩系数,取1。
)
13、塔盘结构
直径为1.2m的塔,采用分块式塔板,以便于从入孔进入塔内。
(1)、塔板型式
理想的塔板应在满足工艺操作的条件下,要求结构简单、有足够的刚性、便于加工、安装和检修。
根据上述要求,选择自身梁式塔板,塔板的结构尺寸见下图。
其厚度S对于碳钢可取2~4mm,不锈钢为2~3mm。
压弯半径R=(1~1.5)S,R1=S。
塔板宽度应能从Φ450mm入孔进出。
塔板梁高h见下表。
自身梁式塔板梁高(mm)
塔板长度
小于1000
1000~1400
梁高h
60
80
图11自身梁式塔板
(2)、塔板固定件
受液盘有平形受液盘和凹形受液盘。
凹形受液盘在低液量时仍能造成液封,且有改变液体流向的绶冲作用和便于液体的侧线采出。
塔径大于800毫米时常采用凹形受液盘。
若物料易聚合或含有悬浮固体时,凹形受液盘易造成死角而堵塞,应采用平形受液盘。
用平形受液盘时,为使上一层流入的液体在板上均匀分布,常设进口堰。
用凹形受液盘时一般不设进口堰。
受液盘一般为50mm。
塔板固定件由以下部件组成:
固定的受液盘和降液管、支持圈、支持板、支持角钢。
(3)、为便于安装、检修或检查塔板腐蚀、堵塞等,须设置内部通道板。
内部通道板最好位于塔盘中央同一垂直位置上,并能上、下均匀可拆。
其最小尺寸为300×400mm,最重不应超过30kg,其长度一般不得大于1m。
(4)、塔板紧固件
a、塔板与支持圈的连接采用卡子,卡子由下卡(包括卡板下螺柱)、椭圆垫板及M10螺母等零件组成。
b、塔板紧固件的间距
用于塔板与支持圈(或支持板)连接的紧固件(包括卡子、双面可拆连接件),其间距为150mm左右。
用于自身梁式塔板之间连接的紧固件(包括螺栓、双面可拆连接),其间距为150~200mm。
2.14、塔高
(1)塔的有效高度
板式塔的有效高度是指安装塔板部分的高度,可按下式计算:
(a)
式中Z——塔的有效高度=1.2m;
ET——全塔总板效率=0.54
NT——塔内所需的理论板层数=14.16
HT——塔板间距=0.45m。
把数据带入a式解得Z=11.35m
(2)塔体总高度
板式塔的塔高如图5-2所示,塔体总高度(不包括裙座)由下式决定:
(b)
式中HD——塔顶空间,m;
HB——塔底空间,m;
HT——塔板间距,m;
HT’——开有人孔的塔板间距,m;
HF——进料段高度,m;
Np——实际塔板数;
S——人孔数目(不包括塔顶空间和塔底空间的人孔)。
a、塔顶空间HD
塔顶空间(见图5-2)指塔内最上层塔板与塔顶空间的距离。
为利于出塔气体夹带的液滴沉降,其高度应大于板间距,通常取HD为(1.5~2.0)HT。
取HD=1.8HT=0.81m
b、人孔数目
人孔数目根据塔板安装方便和物料的清洗程度而定。
对于处理不需要经常清洗的物料,可隔8~10块塔板设置一个人孔;对于易结垢、结焦的物系需经常清洗,则每隔4~6块塔板开一个人孔。
人孔直径通常为450mm。
取人孔数目为4
c、塔底空间HB
塔底空间指塔内最下层塔板到塔底间距。
其值视具体情况而定:
当进料有15分钟缓冲时间的容量时,塔底产品的停留时间可取3~5分钟,否则需有10~15分钟的储量,以保证塔底料液不致流空。
塔底产品量大时,塔底容量可取小些,停留时间可取3~5分钟;对易结焦的物料,停留时间应短些,一般取1~1.5分钟。
d、总高度计算
取HF=1.5m,HB=1.2m,则
=0.81+(27-2-4)×0.45+4×0.45+1.5+1.2
=14.76m
2.15
物理量
符号
单位
结果
原料液流量
F
Kmol/h
59.24
流出液流量
D
Kmol/h
32.88
釜残液流量
W
Kmol/h
26.36
回收率
η
——————
99%
原料液苯摩尔分数
xf
0.551
流出液苯摩尔分数
xD
0.983
釜残液苯摩尔分数
xW
0.012
加热蒸汽温度
T
℃
100
冷却水温度
t
℃
30
压强
P
kPa
101
最小回流比
Rmin
1.15
回流比
R
1.84
理论板数
NT
块
14.16
实际板数
N
块
27
总板效率
ET
0.54
q值
q
1
相对挥发度
α
2.47
塔顶温度
tD
℃
81.7
塔釜温度
tW
℃
109.8
进料液温度
tF
℃
96.9
冷凝器热负荷
Qc
Kj
3,5×108
再沸器热负荷
Qr
Kj
4.16×108
冷凝器传热面积
A
m2
118.68
再沸器传热面积
A
m2
157.64
再沸器平均温度差
⊿tm
℃
24.66
冷凝器平均温度差
⊿tm
℃
41.24
板间距
Ht
m
0.45
塔径
D
m
1.2
开孔率
φ
10.98%
干板阻力
hc
m液柱
0.0353
塔有效高度
Z
m
11.35
塔总高度
H
m
14.76
15参考文献
[1]《浮阀塔》,燃料化学工业出版社,1972。
[2]《化工原理》,管国锋赵汝溥主编化学工业出版社,2009。
[3]《化工原理实验》,夏毅等编燃料化学工业出版社,1972。
[4]《化工单元过程及设备课程教材》匡国柱,史启才主编 ,化学工业出版社,2005.1
[5]《化工原理》,杨祖荣著,化学工业出版社,2004。
[6]《化工设备结构图册》,上海科技出版社
[7]天津大学华工学院柴诚敬主编《化工原理》下册,高等教育出版社,2006.1
[8]大连理工大学主编《化工原理》下册,高等教育出版社,2002.12