冷精轧机操作规程完全版.docx
《冷精轧机操作规程完全版.docx》由会员分享,可在线阅读,更多相关《冷精轧机操作规程完全版.docx(17页珍藏版)》请在冰豆网上搜索。
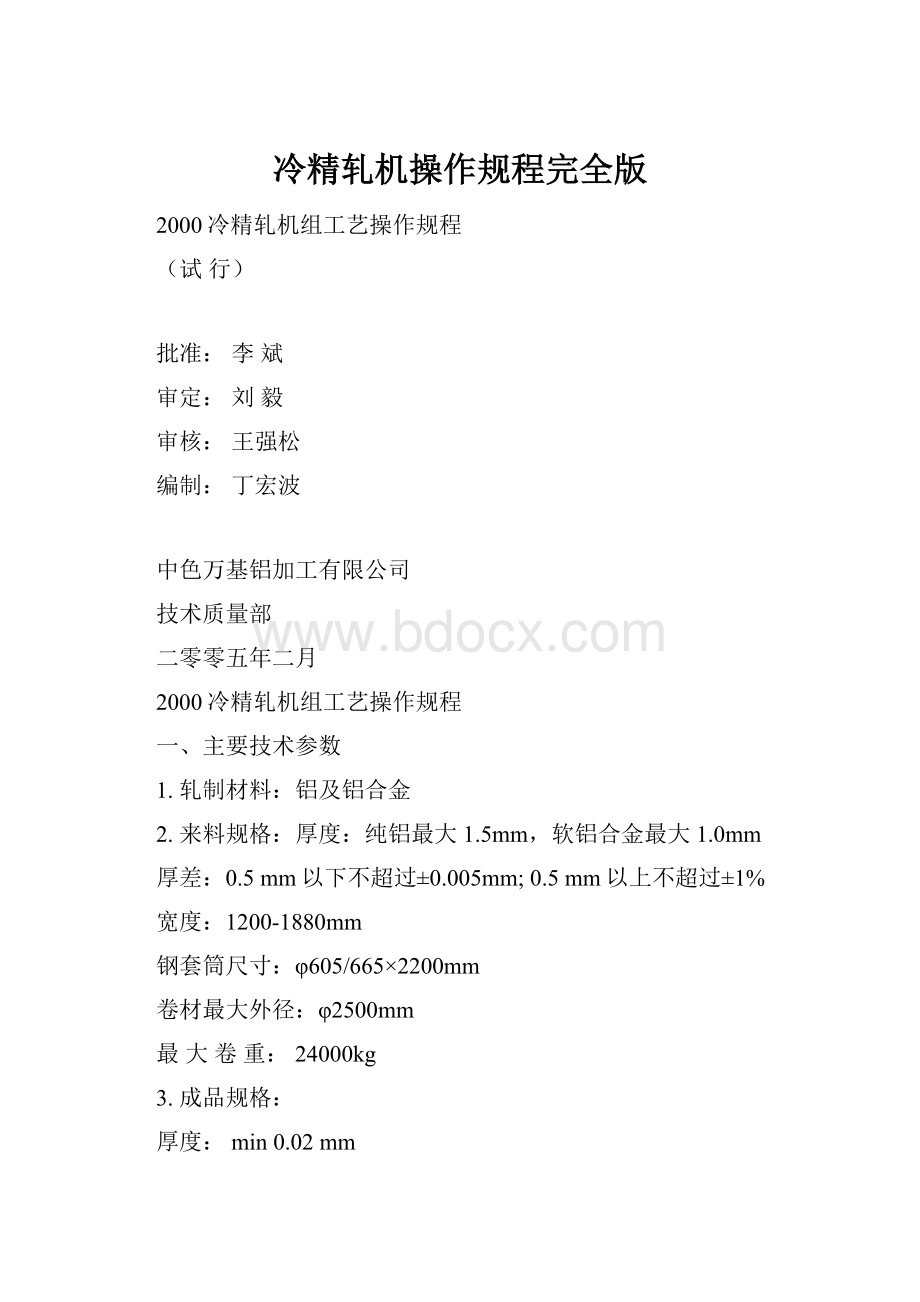
冷精轧机操作规程完全版
2000冷精轧机组工艺操作规程
(试行)
批准:
李斌
审定:
刘毅
审核:
王强松
编制:
丁宏波
中色万基铝加工有限公司
技术质量部
二零零五年二月
2000冷精轧机组工艺操作规程
一、主要技术参数
1.轧制材料:
铝及铝合金
2.来料规格:
厚度:
纯铝最大1.5mm,软铝合金最大1.0mm
厚差:
0.5mm以下不超过±0.005mm;0.5mm以上不超过±1%
宽度:
1200-1880mm
钢套筒尺寸:
φ605/665×2200mm
卷材最大外径:
φ2500mm
最大卷重:
24000kg
3.成品规格:
厚度:
min0.02mm
卷材宽度:
1200~1880mm
卷材最大外径:
φ2500mm
最大卷重:
24000kg
4.轧机参数
1)支承辊规格:
φ860/φ810×2000mm
2)工作辊规格:
φ300/φ275×2100mm
3)最大轧制压力:
10000kN
4)最大输出额定力矩:
50kN.m
5)开卷张力、速度:
低速档双电机:
5.6~56kN
低速档单电机:
2.8~28kN
低速档速度:
Vmax=500m/min
高速档双电机:
2.4~24kN
高速档单电机:
1.2~12kN
高速档速度:
Vmax=1200m/min
张力精度:
动态±3%额定张力
稳态±1.5%额定张力
6)卷取张力、速度:
低速档三电机:
4.7~47kN
低速档单电机:
1.57-15.7kN
低速档速度:
Vmax=875m/min
高速档三电机:
2.2-22kN
高速档单电机:
0.73-7.3kN
高速档速度:
Vmax=1900m/min
张力精度:
动态±3%额定张力
稳态±1.5%额定张力
7)穿带速度:
8-12m/min
8)轧制速度:
低速档0-366/700m/min
高速档0-750/1500m/min
速度精度:
动态±0.4%额定速度
稳态±0.1%额定速度
9)总装机容量:
约DC3164kW
约AC500kW
二、生产工艺过程
首先将冷轧过的卷材(带套筒),用吊车吊到入口卷材存放装置的料架上(可存放2个料卷),然后将上卷车移到卷材存放装置料架端头的卷材下面。
上卷车上的升降油缸升起套筒,将卷材托起,移动上卷车至开卷机。
使小车准确停至开卷机锥头中心线线上,锥头传动键准确停在垂直位置。
对准钢套筒的键槽,夹紧套筒,托板下降,开动锥头对中装置,使带材对准机列中心线,然后人工(厚度1.0以上的来料采用刮板直头)将带材打开,以穿带速度送向轧机,此时张紧辊处于升起位置,带材喂入轧辊后,张紧辊落下,张紧带材,此时机后的活动导板处于升起位置,轧机以穿带速度送料,人工将带材接过,缠绕在卷取机套筒上,带材缠绕几圈后,形成一定张力,压下包角辊(活动导板跟着下落),张紧带材,测厚仪进入工作位置,调整张力、工艺润滑油量,当板形、厚度合适后开始加速,速度上升到该道次设定的轧制速度则自动保持,恒速进行轧制。
轧制过程中,可根据带材板形及厚度调节压下、正负弯辊、轧制速度、前后张力及冷却液喷射量和区段,保证良好的板形,合格的厚度。
当开卷机套筒上的带材接近轧完时,开始减速,速度降到穿带速度则自动保持低速轧完剩余的带材,轧完后抬起机前的张紧辊,抬起机后的测厚仪、包角辊,人工将带卷捆好,并将卸卷小车升起,托住钢套筒两端,打开卷取机锥头,移动小车至卷材存放装置卸料架。
将卷材放到料架上,小车移出。
开卷机上的套筒通过上卷小车和套筒返回装置送到卷取机下方,以备使用,整个轧制过程完结,开卷机再上一个卷材,卷取机通过套筒返回装置再上一个套筒,进行下一道轧制道。
三、机组组成
机组主要由生产设备、辅助系统、电控系统及主要工具组成。
(一)生产设备
1.入口卷材存放装置
2.上卷车
3.开卷机
4.机前装置
5.Φ300/Φ860×2000四辊不可逆轧机
6.机后装置
7.卷取机
8.套筒返回装置
9.换辊装置
10.卸卷车
11.出口卷材存放装置
(二)辅助系统
1.稀油润滑系统2.油气润滑系统
3.工艺润滑系统
4.液压压下(上)与弯辊、平衡液压系统
5.辅助液压系统
6.压缩空气系统
7.CO2灭火系统
(三)电控系统
1.直流传动系统
2.辅助传动系统
3.油泵站控制系统
4.板式过滤机控制系统
5.AGC和AFC控制系统(用户自备)
(四)主要生产工具
1.支承辊换辊架
2.Φ605/Φ665×2200套筒
3.压上油缸拆卸装置
四、机组的结构特点及说明
(一)机械设备
1.入口卷材存放装置
存放装置有两个工位,可同时贮存二个料卷,每个工位由一对托架组成,安装在地面上,上卷时由上卷小车将卷材从托架上取走。
2.上卷小车
上卷小车由交流变频电机驱动,车体用钢板和型钢焊接而成,用来运输送卷料和卸套筒。
水平移动由液压马达驱动;垂直升降由两个液压缸实现,采用同步阀保持同步。
小车行走速度:
0.1m/s~0.5m/s
最大提升重量:
24000kg
3.开卷机
开卷机为双锥头式,两侧锥头可通过两侧的油缸夹紧或打开。
传动侧设有对中调节机构,轴向调节量为±50mm。
传动侧的锥头、轴通过齿形联轴器、传动轴、减速箱,联轴器与传动电机相联。
传动电动机:
2X270kW360/1200r/min400V/768A
减速箱速比:
i=4.65/2.1
开卷张力:
低速档双电机:
5600-56000N
低速档单电机:
2800-28000N
Vlsmax=500m/min
高速档双电机:
2400-24000N
高速档单电机:
1200-10500N
VHsmax=1300m/min
4.机前装置
由事故剪、刮板直头装置、下导辊和张紧辊等组成。
事故剪根据带材的宽度不同可左右移动,刀片固定在气缸的端部,刀片横梁沿两个导柱可上、下移动。
张紧辊在上部位置时进行穿带、喂料、到下部位置使带材张紧,起到部分张紧和展平作用。
刮板直头用于厚料开卷(厚度大于1.0mm)
5.φ300/φ860×2000mm四辊不可逆轧机
四辊铝带箔轧机由轧机本体、排烟罩、挡油门、废料箱、集油槽及主传动等部分组成。
1)轧机本体
①轧辊装置
轧辊装置由工作辊及轴承座,支承辊和轴承座及弯辊平衡装置等组成。
弯辊及平衡缸安装在牌坊凸块上,共四块,每块上有一个支承辊平衡缸,四个弯辊缸、所有缸均为活塞缸,用来实现支承辊平衡及工作辊的弯辊。
工作辊直径:
φ300/φ275mm
辊身长度:
2100mm
辊面硬度:
HS100~102
支承辊直径:
φ860/φ800mm
辊身长度:
2000mm
辊面硬度:
HS70~75
工作辊和支承辊轴承均采用四列短圆柱滚子轴承。
支承辊轴承尺寸:
500X680X420
在支承辊轴承座中设置温度检测元件,当轴承温度达到100℃时报警。
轴承的润滑采用油气润滑。
换辊:
工作辊更换时,设有专门的换辊小车,实现快速换辊。
支承辊换辊时,用特制的支架将上、下辊架起,然后用液压缸一起推出。
②机架
机架是由两个闭式牌坊、上横梁、换辊导轨及底座组成。
牌坊的上部用上横梁联接,下端用螺栓固定在底座上,底座固定在基础上,机架用来支承四辊轧机的所有部件,牌坊用铸钢制成。
立柱断面尺寸:
430X520=2236cm2
③轧线调整装置
轧制线调整机构,位于上支承辊轴承座上方,它由两对上下斜楔、蜗轮、蜗杆、丝杠及液压马达组成。
可使上支承辊轴承座上、下移动,调整轧线正确位置。
④液压压上油缸
压上油缸为八角形,底面有凹形卡槽,靠凹形槽卡在机架窗口的垫板上,两侧卡在机架两侧壁上,每个压上油缸外壁上装有两个位置传感器、一个压力传感器。
⑤空气清辊装置
空气清辊装置的喷嘴通过对准上工作棍和上支承辊间的辊缝,吹掉挤过的部分轧制油,以防落到板面上。
⑥支承辊清辊装置
清辊装置由框架和耐油橡胶组成,安装在牌坊上,通过汽缸驱动使其靠上轧辊或离开轧辊,框架用钢板焊成,用以擦掉辊身上的污物。
⑦排烟罩、挡油门及集油槽为焊接构件。
用来防溅和排烟。
2)主传动装置
主传动由二台直流电机经齿形联轴节、齿轮机座及万向接轴等组成。
抱轴装置移动距离可调整,在卸轧辊时通过油缸可抱紧万向接轴轴套,使轴套位置固定,便于换辊。
主传动电机:
2X907kW,Z560-4,529/1200r/min,660V/1466A
Vmax=1508m/minVls=610m/min
减速箱速比:
高速档0.7474,低速档1.5306
最大输出扭矩:
50kN.m
3)废料箱
废料箱放置在轧机底座之间的轨道上,用来收集轧制中的碎铝箔,用钢板及型钢焊制而成。
6.机后装置
机后装置由包角辊、板形辊(仪)、熨平辊、及导板所组成。
偏导辊辊、包角辊及熨平辊均为双层套辊结构。
包角辊靠液压上下移动,熨平辊靠气缸上下摆动,导板可以随包角辊摆起。
当包角辊、熨平辊在上部位置及导板升起时进行穿带,带材靠导板可顺利导入套筒。
熨平辊随着卷径增大而升高,但压紧点始终保持在距切点一定距离处。
板形辊及板形系统用户自备。
7.卷取机
卷取机采用双锥式夹紧机构,其结构形式与开卷机相同。
传动电机采用三台直流电机:
3X270kW360/1200r/min
减速箱速比:
低速档:
i=2.8235
高速档:
i=1.3084
卷取张力:
低速档三电机:
4700-47000N
低速档单电机:
1570-15700NVLsmax=875m/min
高速档双电机:
2200-22000N
高速档单电机:
730-7300NVHsmax=1900m/min
8.卸卷小车
卸卷小车的主要技术性能及结构与上卷小车相同,安装方向相差1800。
9.卷材存放装置
卸料架与上料架相同,可同时贮存两卷料。
10.套筒返回装置
套筒返回装置在主轧机下,开卷、卷取机之间,通过提升装置使套筒上升或下降,实现上卸套筒工序,套筒通过导轨滚动传递。
11.X射线测厚装置
测厚装置由测厚仪及底座组成。
测厚仪(买方引进)
(二)工艺润滑冷却系统
1.用途:
工艺润滑冷却系统用于对轧辊的辊面进行润滑和冷却,是机组的重要组成部分。
该系统除供轧辊工艺润滑、冷却外,还用来控制轧辊辊形,与弯辊系统配合达到改善带材表面质量和板形的目的。
2.系统组成
1)工艺润滑冷却泵站
2)喷嘴梁系统
3)板式过滤机
3.主要技术参数
供油能力:
3600l/min
供油压力:
0.2-0.6MPa
过滤机流量:
4200l/min
4.系统主要工作特点
1)工艺润滑冷却泵站
工艺润滑冷却泵站配置在一号地下室,其内配有污油箱、净油箱、过滤泵、冷却器、加热器、防火闸门及温度、压力、液位、流量等检测仪表。
(1)工艺流程:
从轧机集油槽收集的污油经回油管、防火闸门回至污油箱内,再由过滤泵供给板式过滤机进行过滤,经过滤的净油返回地下净油箱,再由供油泵通过给油管路送给轧机,经喷嘴喷射至轧机表面达到润滑和冷却的作用。
(2)油箱的液位控制:
污油箱及净油箱上装有浮球液位计用来控制两油箱的最高点及最低点液位,以达到控制供油泵、过滤泵起动停止的目的,使油箱液位平衡,确保供油。
所有控制液位点都有音响、灯光信号,供轧机操作人员观测。
地上还设有油箱液位观测二次仪表,可随时检查油箱的液位高低、油面变化速度,供操作人员掌握供油及回油情况。
(3)系统温度控制:
一号地下室设有两台加热器、一台冷却器、油箱、管路温度检测仪表。
当轧制油低于设定的温度时,检测元件发出信号,加热泵、加热器工作,将油箱中轧制油循环加热,当达到所设定温度,加热系统自动停止工作。
正常供油过程中,当温度高于或低于供油温度时,在线冷却器、在线加热器可工作补偿油温的变化,达到控制油温的目的。
(4)系统压力控制:
系统中设有压力调节阀及管路压力、流量检测元件。
根据这些检测元件来控制管路压力的大小。
(5)系统连锁保护:
整个系统是在PLC控制下工作的,所有泵、加热器、冷却器、阀都有连锁保护。
系统分为手动状态和自动状态。
当在手动状态时,各执行元件可单动;当在自动状态时系统各部分发生连锁保护作用,并各执行元件在自动工作状态,部分元件手动不起作用。
(6)防火闸门:
防火闸门位于地沟内,回油管内污油经防火闸门返回污油箱,其主要作用是隔断火源。
另外油箱加油可从防火闸门注入。
2)喷嘴梁系统
喷嘴梁系统由电磁阀控制柜及喷嘴横梁组成。
电磁阀控制柜控制横梁上的喷嘴工作,以达到喷射轧制油的目的。
电磁阀柜内设有电磁阀,一个电磁阀控制两个喷嘴,每个喷嘴的开闭是由气动薄膜阀来控制的,工艺润滑油经过气动薄膜阀向轧机供油。
电磁阀由PLC控制。
在机前装置上装有三根喷嘴梁,形成上下五排喷咀,每排设置36个喷嘴,通过对工作辊喷嘴梁成排成对喷嘴的打开和关闭,来调节流量,从而调节轧辊辊型,达到控制板形的目的。
换辊时喷嘴梁随机前装置一起移开。
正常轧制时,电磁阀全部断电,喷嘴梁全部打开,根据板形控制要求可随时关闭一对或几段喷嘴,上、下工作辊可组成七种不同流量。
另外根据支承辊三段控制与工作辊喷咀控制仍能组合成若干种流量,根据生产操作实际需要可随时控制和调节。
3)板式过滤机
精密板式过滤机是由过滤箱、过滤箱压紧机构、提升装置、混合箱、运纸机构、纸卷架及气动系统等组成。
过滤泵将污油箱内的轧制油送往过滤机,经过过滤后的净油进入净油箱。
为了保证要求的过滤精度,在每层过滤箱间铺设一层过滤纸。
在过滤前需要在过滤纸上沉积一层一定厚度的助滤剂,在过滤过程中还要根据油的脏污程度,通过进给阀不断供给助滤剂,当过滤纸脏污需要换纸时,通过气动系统把滤箱内的工艺润滑油吹回污油箱,并将助滤剂吹干成滤饼,然后提升过滤箱,通过运纸机构将废纸拉出,新滤纸拉入,最后压紧滤箱,重新开始上述过程。
整个过滤机的操作有三种工况要求:
1)手动方式
a.在调试、维修以及过滤过程中出现故障时采用手动方式。
包括:
过滤机的提升及压紧,电磁阀的接通。
b.运纸机构的电机采用手动启动、停止。
c.混合箱的搅拌电机采用手动操作。
2)换纸程序控制
当过滤箱脏污时,连接在滤箱进油侧的电接点压力表被接通,这时轧机主操作台和滤油机操作箱上显示滤箱脏污信号,轧机操作手将视工作情况决定是否停止生产,以便滤油机更换滤纸。
整个过程是以时间进行控制的,每一动作过程所需的时间以及所占整个控制时间的比例按程序执行。
当程序控制进行到提升过滤箱,达到提升高速后接近开关动作,程序控制停止,此时需要手动启动换纸机构,将滤纸拉出,置入新纸,此后再按一下程序控制按钮,程序重新开始运行。
3)中断程序控制
虽然过滤箱尚未脏污,但轧机需要较长时间停机或者发生意外事故,这时要求滤油机停止工作。
为了不使过滤箱中的工艺油外渗,需要吹扫滤箱中的存油,当需要重新工作时,程序控制从中断处开始运行。
(三)机械润滑系统
轧机机械润滑系统包括稀油润滑系统及油雾润滑系统。
1.稀油润滑系统采用标准稀油站分别供给主传动、开卷机、合卷开卷机、卷取机传动齿轮箱齿轮及轴承润滑。
润滑油由油泵从油箱吸出后,经单向阀、过滤器、换热器等送往设备润滑用点,经润滑用点通过磁过滤器后返回油箱,以便循环使用。
稀油站配备有加热器和冷却器,根据油温变化和季节变化加热或冷却。
所有轴承润滑点都配有给油指示器以便观察和调节轴承的润滑油流。
在供油管路中配有油流指示器并带有干簧管,以便观察给油油流情况和发出讯号,保证机械设备运行正常。
2.油气润滑系统:
主要用来润滑支承辊四列圆柱轴承及机前、机后辊子的轴承以及开卷、合卷、卷取机的轴承润滑。
(四)压缩空气系统
压缩空气主要用来驱动气缸及吹扫,有以下用气点:
1.上下支承辊清辊器摆动缸及压紧清刷缸;
2.工艺润滑空气电磁阀柜;
3.油气润滑用气;
4.空气清带用气(喷嘴在防溅板及出口导板上);
5.空气清辊喷嘴用气(喷嘴在防溅板上);
6.测厚仪探头吹刷用气;
7.操作台吹扫用气;
8.板式过滤机吹扫及混合箱用气;
9.工艺润滑系统气动薄膜阀用气;
(五)液压系统
轧机的液压系统包括:
液压压上系统、弯辊平衡及辅助操作液压系统。
轧机的液压系统由泵站及控制阀台组成,泵站为一带有高位油箱、集油盘的整体结构,控制阀台全部采用叠加阀式集成小阀台,放置在机械设备附近。
1.液压压上系统:
该系统用来供给轧机压上油缸压力油源,并根据压力,带材厚度和位置反馈信号对其进行伺服控制以保证产品厚度精度。
该系统包括液压压上泵站及伺服阀台。
该泵站设置在地下室内,二个伺服阀台分别装在靠近油缸的操作侧和传动侧机架上。
叶片泵用来过滤循环冷却油液并给油缸活塞杆腔以背压。
主泵供高压油流通过伺服阀供给油缸,通过厚度自动控制系统完成辊缝的调整,实现辊缝的设定和厚度自动控制。
2.弯辊、平衡及辅助液压系统
该系统为机组弯辊、平衡液压系统,按需要控制弯辊力和弯辊状态从而控制辊型,达到控制板形的目的。
该系统由泵站、管路和阀台组成。
液压泵站置于地下室,弯辊阀台置于地面附近。
系统中设有电液比例减压阀用于调整正负弯辊力,在出口侧操作台上有弯辊力大小显示。
弯辊平衡系统有以下几种工作状态:
①工作辊正弯;
②工作辊负弯;
③工作辊负弯加平衡;
④工作辊平衡;
⑤负弯加进退(换辊状态);
⑥全退;
⑦支承辊平衡.
2)辅助液压系统
该系统用来做全机组传动液压缸和液压马达的动力源,由油泵和阀台两部分组成,泵站置于地下室,阀台置于设备附近。
3.轧机液压系统具有以下结构特点:
1)定量泵系统采用电磁溢流阀与泵的连锁控制,实现无载起动及无载停泵,提高了泵的寿命;
2)根据辅助操作的特点,采用蓄能器工作制,通过压力继电器、电磁溢流阀控制泵的运转,由蓄能器保持系统压力,节省了能源,减少了系统的发热;
3)为保护机械设备及液压泵,系统中采用了完备的超压保护环节;
4)系统中采用了吸油口、主油路、旁路等多级过滤,保证系统的清洁度;
5)具有手动及自动两种加热冷却系统,高温灯光报警;
6)除目测的液位计外,另有液位控制器,低液位声光报警;
7)弯辊系统中同时采用了背压系统,实现了正负弯辊状态的快速切换。
4.轧机液压系统的装机水平:
1)压上系统、弯辊系统采用恒压变量泵。
辅助操作、对中系统采用高性能叶片泵。
2)控制阀件采用VICKERS公司产品,为叠加阀式集成,结构紧凑,方便了维护检修;
3)压上系统采用609所生产航空用伺服阀。
4)弯辊系统采用比例控制,操作简便,弯辊力控制精确。
(六)CO2灭火系统
该系统用于探测和扑灭在生产过程中轧机本体及附近、地沟、地下室等部位因某些原因而发生的火灾,以确保设备和操作生产人员安全。
灭火区域的划分:
1.轧机本体及附近烟道;
2.轧机辊缝;
3.集油槽;
4.地沟;
5.地下室;
6.板式过滤机区域;
灭火系统由探测报警系统,自动和电动手控灭火系统,CO2瓶组及CO2释放系统三部分组成。
轧机本体、烟道、地下室及灭火地沟、板式过滤机区域为自动灭火和电动手控灭火区域;轧机二次灭火及辊缝、集油槽为电动手控灭火区域。
该系统探测报警器、灭火控制器、CO2释放控制箱等均布置在机组传动侧柱子之间的地坪上。
轧机本体、地下室、地沟均为独立的探测区域;轧机排烟罩中布置有二组定温和差定温热探测器;地下室布置有二组定温和差定温热探测器。
(七)电控系统
主要包括直流传动控制系统、辅助传动系统、油泵站控制系统和板式过滤器控制系统。
1.直流传动控制系统
轧机、开卷机和卷取机的直流传动系统均采用ABB公司生产的DCS500系列晶闸管变流装置供电,该装置为全数字式,四象限或三象限运行,具有电机测速反馈丢失、轴承过温、过载、超速、堵转、电枢过流、电枢电流波动、电枢过压、电枢电流波动、电枢过压、磁场欠磁、磁场过流、变流器晶闸管温度过高、供电电源主电路欠压、辅助供电欠压、相序错误等监控和保护措施,同时还包含紧急停车和防止意外起动等基本保护功能,故障信息可以存储和显示,并能方便地与PLC通讯。
该装置还可以实现速度控制和转矩控制,包括设定加减速和张力运算及补偿功能,它可以在Windows环境下方便地进行调试及维修。
对开卷和卷取直流传动系统设置断带保护功能,包括紧急停车、测厚仪的C形架移出,由AGC系统使轧辊抬起。
2.辅助交流传动系统
辅助交流传动电机的起动装置为马达控制中心。
3.机列的操作
机列的操作控制系统采用OMRONCS1可编程控制器通过PPI、I/O远传和CONTRLLER-LINK通讯可实现对整个机列的直流传动、工艺润滑泵站、压上泵站、弯辊泵站、稀油泵站等交流辅助传动进行操作和连锁。
该程控器可通过HOST-LINK实现对上位机的通讯。
4.上位监测
上位监测用计算机采用奔腾III(主频500MHZ,10GB硬盘等),用于工作参数、报表和故障信号监测、显示、存储和打印。
该计算机通过HOST-LINK与OMRONCS1程控制器相连,可以对CS1编程调试或监视。
五、生产中设备出现故障,应及时停车,通知维修人员处理。
六、工作后处理
1.生产结束后,按《1450mm分卷机机械说明书》的要求,做好停车后的设备调整工作。
2.当班生产结束后,将所有控制旋钮和手把恢复到零位,切断电源。
3.认真清擦设备,清扫现场。
4.认真填写交接班记录和生产记录。