冷却方式对热轧铌微合金钢微观组织和力学性能的影响.docx
《冷却方式对热轧铌微合金钢微观组织和力学性能的影响.docx》由会员分享,可在线阅读,更多相关《冷却方式对热轧铌微合金钢微观组织和力学性能的影响.docx(12页珍藏版)》请在冰豆网上搜索。
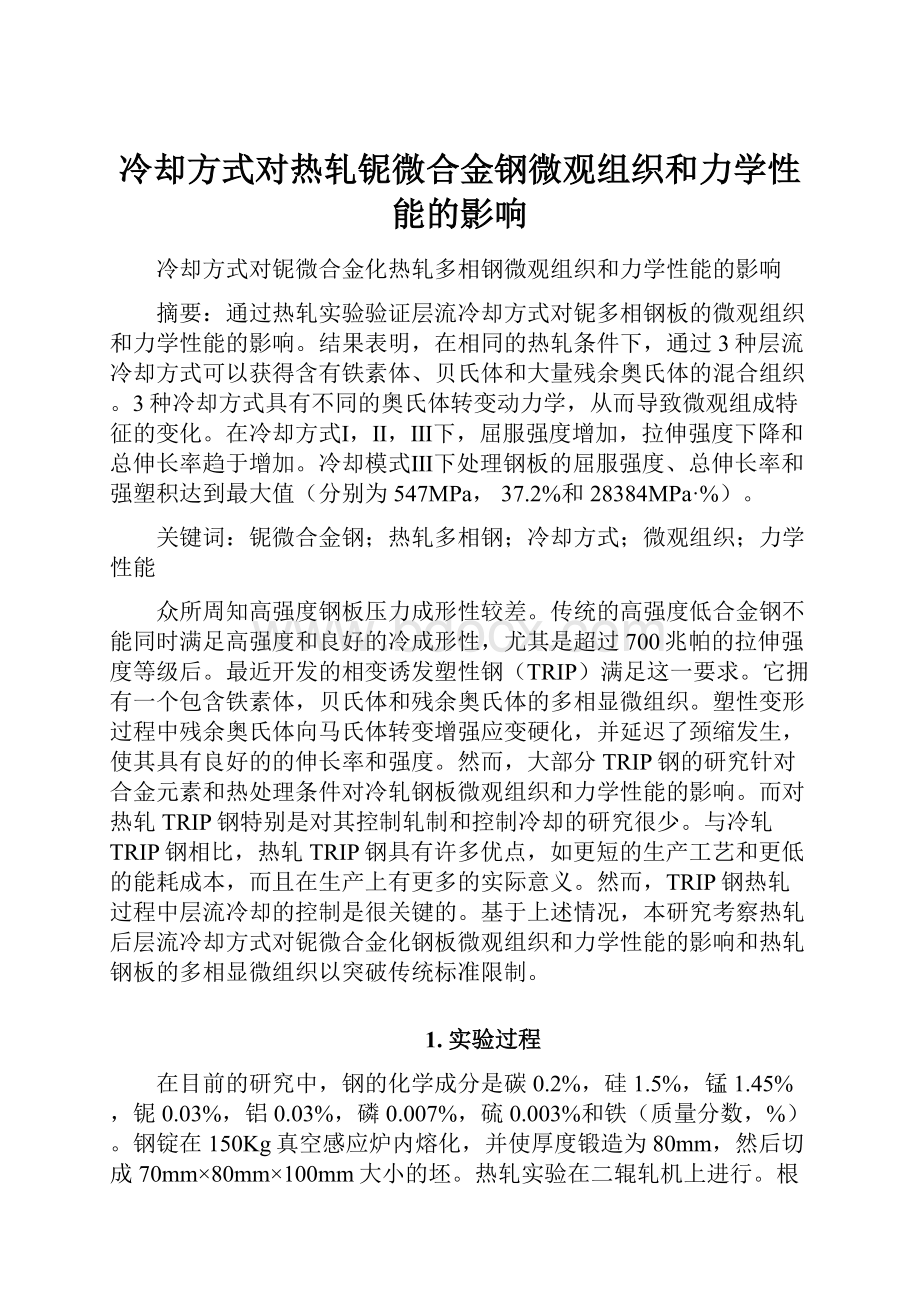
冷却方式对热轧铌微合金钢微观组织和力学性能的影响
冷却方式对铌微合金化热轧多相钢微观组织和力学性能的影响
摘要:
通过热轧实验验证层流冷却方式对铌多相钢板的微观组织和力学性能的影响。
结果表明,在相同的热轧条件下,通过3种层流冷却方式可以获得含有铁素体、贝氏体和大量残余奥氏体的混合组织。
3种冷却方式具有不同的奥氏体转变动力学,从而导致微观组成特征的变化。
在冷却方式Ⅰ,Ⅱ,Ⅲ下,屈服强度增加,拉伸强度下降和总伸长率趋于增加。
冷却模式Ⅲ下处理钢板的屈服强度、总伸长率和强塑积达到最大值(分别为547MPa,37.2%和28384MPa·%)。
关键词:
铌微合金钢;热轧多相钢;冷却方式;微观组织;力学性能
众所周知高强度钢板压力成形性较差。
传统的高强度低合金钢不能同时满足高强度和良好的冷成形性,尤其是超过700兆帕的拉伸强度等级后。
最近开发的相变诱发塑性钢(TRIP)满足这一要求。
它拥有一个包含铁素体,贝氏体和残余奥氏体的多相显微组织。
塑性变形过程中残余奥氏体向马氏体转变增强应变硬化,并延迟了颈缩发生,使其具有良好的的伸长率和强度。
然而,大部分TRIP钢的研究针对合金元素和热处理条件对冷轧钢板微观组织和力学性能的影响。
而对热轧TRIP钢特别是对其控制轧制和控制冷却的研究很少。
与冷轧TRIP钢相比,热轧TRIP钢具有许多优点,如更短的生产工艺和更低的能耗成本,而且在生产上有更多的实际意义。
然而,TRIP钢热轧过程中层流冷却的控制是很关键的。
基于上述情况,本研究考察热轧后层流冷却方式对铌微合金化钢板微观组织和力学性能的影响和热轧钢板的多相显微组织以突破传统标准限制。
1.实验过程
在目前的研究中,钢的化学成分是碳0.2%,硅1.5%,锰1.45%,铌0.03%,铝0.03%,磷0.007%,硫0.003%和铁(质量分数,%)。
钢锭在150Kg真空感应炉内熔化,并使厚度锻造为80mm,然后切成70mm×80mm×100mm大小的坯。
热轧实验在二辊轧机上进行。
根据铌在碳,氮中的溶解度,将坯料在加热炉内以1200℃奥氏体化2小时,以保证铌完全固溶为奥氏体。
之后,在再结晶和非再结晶奥氏体区轧制9道次,使钢板最终厚度为14mm。
终轧温度在820℃左右。
终轧之后,钢板通过3种冷却方式冷却到预定的温度,如图1所示。
不同冷却方式通过在不同的冷却区域调整水流量进行控制。
冷却模式Ⅰ分两步冷却,即空气冷却(AC)和随后的超快速冷却(UFC)。
冷却方式Ⅱ和Ⅲ都分三步冷却,即层流冷却(LC)和UFC的中间空气冷却,以及UFC早期和晚期的中间空气冷却。
最终冷却温度为440℃至460℃。
其次是利用石棉网冷却至室温而发生等温贝氏体转变,来模拟工业生产中材料堆冷过程中的热变化。
Fig·1 Schematicdiagramofcoolingpatterns
图1冷却方式示意图
整个实验过程中,用红外测温仪测量钢板表面温度。
根据GB/T228-2002拉伸试样沿纵向方向切开。
力学性能在5105-SANS的万能试验机上以转速为5mm/min的十字头测定。
微观组织通过4%硝酸酒精溶液腐蚀后在LeicaQ550IW光学显微镜(LOM)和Quanta600扫描电子显微镜(SEM)上进行观察。
TEM研究用的薄采用双喷电解以观察微量成分、位错和析出物。
X射线衍射分析使用了衍射和CoKα辐射,以确认在微观组织中残余奥氏体量。
2.实验结果
2.1冷却方式对力学性能的影响
表1显示了试验钢的力学性能。
试样的屈服强度(YS),极限抗拉强度(UTS),屈服率(YR),总伸长率(TEL)和强塑积(UTS×TEL)如图2所示。
试样1,2和3分别对应冷却方式Ⅰ,Ⅱ,Ⅲ。
试样1具有最小屈服强度和最大抗拉强度,试样3显示了最大屈服强度和最小抗拉强度。
试样2与试样1相比,具有较高的屈服强度和相对较低的抗拉强度。
就总伸长率而言,试样1和2几乎具有相同的值(分别是31.1%和30.8%),而试样3具有最大的伸长率37.2%。
在图2(c)中强塑积(UTS×TEL)与图2(b)总伸长率呈现出类似的趋势。
试样3强的塑积最大,为28384Mpa·%。
如图2(d)所示,试样经冷却方式Ⅰ,Ⅱ,Ⅲ冷却后屈服率增加。
然而,这些值小于0.75。
表1各试验钢的力学性能
Fig·2 Tensilepropertiesofthreespecimens
图2三个试样的拉伸性能
2.2冷却方式对微观的影响
在各种冷却模式下试样的LOM显微照片如图3所示,三个试样的显微组织均由铁素体和贝氏体组成。
在冷却方式Ⅱ,Ⅲ下获得的铁素体晶粒的微观组织比较细并且分布均匀,相应的晶粒大小分别约为6.3μm和5.6μm。
与冷却方式Ⅱ,Ⅲ相比,冷却模式Ⅰ下的铁素体晶粒比较粗大,其大小约7.5μm。
在三个试样的微观组织中铁素体量分别达到40.7%,41.5%和43.4%。
在图3中也可以看出,有两种形式的铁素体,多角形铁素体或等轴铁素体。
后者在微观组织中的量从试样1至试样3逐渐增加。
通过X-射线衍射可以证实残余奥氏体存在。
残余奥氏体量分别是13.5%,11.3%和13.2%。
图4显示了拉伸试验前试样3的X射线衍射图样。
残余奥氏体也可通过透射显微镜观察。
图5展示了残余奥氏体透射图样及试样3的衍射图样。
可以看出,残余奥氏体在贝氏体与铁素体板条之间,或在铁素体/贝氏体界面上。
(a)CoolingpatternⅠ; (b)CoolingpatternⅡ; (c)CoolingpatternⅢ.
Fig·3 Opticalmicrostructuresofspecimensunderdifferentcoolingpatterns
图3不同冷却方式下试样的金相组织
Fig·4 XRDpatternofspecimen3beforetensiletest
图4拉伸试验前试样3的X射线衍射图样
Fig·5 TEMmicrographsofretainedausteniteanditsdiffractionpatternofspecimen3
图5残余奥氏体的透射图样和试样3的衍射图样
2.3位错和析出物分析
不同冷却方式下的铁素体晶粒内的位错如图6所示。
可以看出,试样的位错密度在冷却模式Ⅰ,Ⅱ,Ⅲ下逐步增加。
在冷却模式Ⅰ中,精轧后试样先在空气中冷却到一定温度,然后进行超快速冷却。
然而,冷却模式Ⅱ、Ⅲ通过三步冷却,即早期和晚期水冷,中间空气冷却。
因为在三种冷却方式弛豫终止温度相同,冷却模式Ⅰ下空气冷却的时间比较长,形成先共析铁素体的弛豫度高,导致铁素体基体上位错密度较低。
相反,在冷却模式Ⅱ、Ⅲ下的铁素体基体位错弛豫程度较低。
在冷却模式Ⅱ、Ⅲ下,冷却水在第一阶段分别为层流冷却和超快速冷却。
由于相同的中间空气冷却时间,后者在变形奥氏体中有更多的储存能,导致在铁素体基体上有较高的位错密度。
图7显示不同的冷却模式下三个试样基体上的析出物。
析出量随不同的冷却方式而变化。
采用冷却方式ⅠⅡ,Ⅲ,铁素体晶粒内析出物逐步增加。
此外,由于沉淀硬化,基体析出物均匀分布并且析出物很细小(约5nm)。
相对于基体位错有较高的自由能,因此在空气中冷却时,基体析出物优先在位错处形核。
高的位错密度降低碳氮化物析出的临界形核半径,并提高其核率。
因此,铁素体晶粒内的位错密度显著影响着碳氮化物的析出量。
(a)CoolingpatternⅠ; (b)CoolingpatternⅡ; (c)CoolingpatternⅢ.
Fig·6 Dislocationswithinferritegrainsofspecimenssubjectedtovariouscoolingpatterns
图6不同冷却方式下试样的铁素体晶粒内的位错
(a)CoolingpatternⅠ; (b)CoolingpatternⅡ; (c)CoolingpatternⅢ.
Fig·7 Precipitatesofspecimensunderdifferentcoolingpatterns
图7不同冷却方式下试样的析出物
2.4贝氏体结构
在不同的冷却方式下三个试样的贝氏体结构如图8所示。
在贝氏体与铁素体亚晶平行带可以清楚地看到小角度亚晶界。
此外,在贝氏体铁素体板条内发现存在大量位错。
通过冷却模式Ⅰ冷却下的试样1,位错密度相对较低,板条内位错网络稀疏。
通过冷却模式Ⅱ冷却的试样2贝氏体铁素体亚晶内位错高密度缠结。
在冷却模式Ⅲ下冷却的试样3中可观察到贝氏体铁素体亚晶内具有更高的位错密度。
(a)CoolingpatternⅠ; (b)CoolingpatternⅡ; (c)CoolingpatternⅢ.
Fig·8 Bainiticsubstructureinthreespecimens
图8三个试样的贝氏体亚结构
3.讨论
3.1铁素体生长动力学
在三种冷却方式空气冷却阶段,当过冷奥氏体从
温度慢慢地冷却时,铁素体形成并且碳在奥氏体/铁素体界面扩散。
根据物理冶金学的基本原理,在α/γ相界面向晶内推进前铁素体的增长是由扩散过程控制的。
当
组成的试样在空气冷却控制冷却过程中的温度冷却至T1,部分的Fe-
的相图如图9(a)在温度T1,
和
,分别表示在α/γ相界面的α和γ碳浓度。
图9(b)显示了沿α相析出物的组成。
在图9(b)中,Z是α析出物增长距离,A1的面积与从α相析出的溶质的质量成正比。
该溶质直接堆积在界面前,使9(b)标示的A2区域面积等于A1的面积。
在这不断增长的α-γ界面上的溶质通量可以写成:
(1)
(2)
是通量进入界面的量和
是通量从界面进入的量。
这两个通量维持着界面的平衡,这个流量平衡是:
(3)
其中v是α析出物的增长速度,Dγ是碳在奥氏体中的扩散系数,是碳在α/γ界面上在γ里的浓度梯度。
从图9(b)结构可以看出界面的浓度梯度,可以认定为参数L函数,并且其生长速度为:
(4)
由式(4)得出,随着α析出物的进一步长大,A2越大,因而L越大,而增长速度v越慢。
如果A2面积近似为:
A2=L·(Cγ-C0)/2,并且v=dZ/dt同时认为A1=Z·(C0-Cα),那么A1、A2相等并将其带入公式(4),可以得到下面公式:
(5)
将这个方程积分,得到下式:
(6)
其中
(7)
如上所述,这些析出物生长需要远距离扩散。
因为铁的晶格重组和铁原子与碳原子的相互迁移需要时间,所以增长将是相对缓慢的。
生长率和铁素体晶粒尺寸大小具有时间依赖性。
因此,在冷却模式中应存在空气冷却阶段。
这使得奥氏体相变和铁素体相变两个阶段分开,并且使微观组织中铁素体的量增加。
Fig·9 AportionofFe-Fe3Cphasediagram(a)andcompositionprofilealongαprecipitate(b)
图9(a)Fe-Fe3C相图的一部分;(b)沿α析出物组成剖面图
3.2冷却方式对相变过程的影响
由于轧机上执行相同的热轧过程,控制轧制后三个试样的奥氏体条件是相同的。
各种冷却方式产生不同的奥氏体转变动力学,从而影响过冷奥氏体的相变过程。
在冷却模式Ⅰ下,精轧后空气冷却阶段奥氏体变形使应变能释放并且应变诱导相变的影响被削弱。
除了奥氏体边界锯齿或凸起,奥氏体晶粒内变形带是有效的成核点,而这些区域的特点是由位错缠结构成的高密度单元格。
在空气冷却阶段,变形奥氏体弛豫时间较长时,奥氏体位错弛豫程度高,变形带的数量减少。
因此,从冷却方式Ⅰ至冷却方式Ⅱ冷却方式Ⅲ,铁素体形核点依次增加。
此外,从冷却方式Ⅰ,Ⅱ,Ⅲ,过冷奥氏体逐渐增加,导致铁素体转变开始温度Ar3逐渐降低。
基于形核点的整体考虑和铁素体转变开始温度,采用的冷却方式Ⅰ,Ⅱ,Ⅲ,铁素体形核的数目和铁素体晶粒细化的程度依次增加。
三种冷却方式都有空气冷却阶段,其目的是使奥氏体和铁素体两相独立。
同时,位错密度和碳氮铁素体基体颗粒析出量也在不断变化。
虽然高温空气冷却停止温度(或弛豫终止温度)是相同的,但它们的Ar3温度彼此不同,它们之间的差异值是铁素体弛豫温度区间。
通过运用冷却模式Ⅰ,Ⅱ,Ⅲ,试样的Ar3温度下降,铁素体晶粒的弛豫时间减少。
相应地,铁素体晶粒内的位错密度增加。
在空气冷却阶段随着气温的下降,铌在铁素体中的固溶度降低,析出的Nb(C,N)成为可能。
位错为微合金碳氮化物形核提供平台。
晶粒间位错密度越高,铁素体基体上的析出量越多。
因此,高的位错密度的铁素体基体有利于微合金碳氮化物在适当的析出温度范围的析出。
根据平衡条件,并在铁素体转变的过程中,碳在奥氏体中浓度增加,在3种冷却方式的空气冷却阶段,碳在奥氏体中富集。
在随后的超快速冷却,部分未转换的奥氏体经历弛豫过程转变为贝氏体,贝氏体铁素体包含原奥氏体的位错密度。
根据不同的冷却方式,未转换的奥氏体弛豫程度是不同的,从而导致贝氏体板条内位错密度的差异。
在贝氏体相变过程中碳从贝氏体铁素体中析出。
同时,珠光体转变被超快速冷却抑制,未转变的奥氏体有第二次碳的富集。
因此,残余奥氏体因碳浓度的增加而稳定。
在三种冷却方式下,最终得到多相微观结构包含有铁素体,贝氏体和显着的残余奥氏体。
4结论
1)热轧钢板精轧后通过适当的微合金化和各种冷却方式,形成包含残余奥氏体,铁素体,贝氏体的多相微观组织。
当试样分别通过冷却方式Ⅰ,Ⅱ,Ⅲ冷却时,其微观组织中铁素体晶粒变得更细,铁素体含量略有增加,部分残余奥氏体变化,从13.5%,11.3%到13.2%。
同时,铁素体基体上位错密度和碳氮化物的析出量,以及板条贝氏体铁素体内位错密度逐步增加。
2)在三个冷却方式中空气冷却阶段,奥氏体和铁素体两相分离分开,微观组织中铁素体的量和在未转换奥氏体里的碳浓度增加。
基于适当的铁素体含量,空气冷却的时间应缩短,尽可能减少铁素体晶粒和未转换奥氏体的弛豫程度。
3)在冷却模式Ⅰ,Ⅱ,Ⅲ下,屈服强度增加,拉伸强度下降和总伸长率趋于增加。
由冷却模式Ⅲ处理的试样,屈服强度,伸长率和强塑积达到最大值(分别为547MPa,37.2%和28384MPa·%)。